
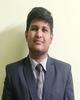
- Open Access
- Authors : Kunal Shashikant Jadhav , Vishal Maruti Dhobale , Shubham Rajendra Mali , Sneha Shirke
- Paper ID : IJERTV11IS060017
- Volume & Issue : Volume 11, Issue 06 (June 2022)
- Published (First Online): 09-06-2022
- ISSN (Online) : 2278-0181
- Publisher Name : IJERT
- License:
This work is licensed under a Creative Commons Attribution 4.0 International License
Oscillating Water Column Well’s Turbine Design & Modification
Kunal Shashikant Jadhav Department of Mechanical Engineering SOET, Sandip University
Nashik, India
Shubham Rajendra Mali
Department of Mechanical Engineering SOET, Sandip University
Nashik, India
Vishal Maruti Dhobale
Department of Mechanical Engineering SOET, Sandip University
Nashik, India
Prof. Sneha Shirke
Professor, Department of Mechanical Engineering SOET, Sandip University
Nashik, India
Abstract: The ocean waves are one of the most important renewable energy resources that if extensively used in energy generation that can contribute significantly amount of the electrical energy supply of countries with coasts facing the sea. Variety of research been conducted and technologies has been developed and studied, in some cases tested at full size in real world conditions. Oscillating-water-column (OWC) turbine technologies of fixed structure or floating, are an important part of wave energy generation devices. Wells turbine is humid air axial-flow turbine, which operates inside tube like wave energy converters under reciprocating bidirectional airflows. A large part of wave energy generator prototypes research, studied and deployed so far into the real-world sea are of OWC type. In an Oscillating-water-column is a fixed or floating hollow structure, open to the sea above the water surface that traps air and allowed to flow it into the turbine housing. This reciprocating Wave action give rise in the alternately compresses and decompresses of the trapped air which is forced to flow through a turbine coupled to a generator. This paper presents a comprehensive review of OWC devices and air blade of turbines. This is followed by a study and analysis Wells turbine theoretically, numerically and development of experimental 3D model techniques of OWC. Reactive control of the air flow and phase control by latching are important issues that are addressed. In addition to this various accessory are added to the turbine to increase the rotational speed. This paper contributes to the increasing the efficiency of the wells turbine.
Keywords Oscillating-water-column, wells turbine, air blade, 3D model.
-
INTRODUCTION
In this paper we have shown working of the wells turbine with different types of the blade that are used in the various energy generation project. This blade are taken from the wind mill blade shape i.e. air foil shape which is used for the wind in the unidirectional flow. The second wind blade is take from the propeller shape blade used in the pushing the ship in the water. The propeller generates the trust that can push the heavy ship under water which is many times denser than the air. The propeller shape turbine is also used in the small-scale river water energy generator project across the globe. The third type of the blade is the symmetrical type. This type of the blade is bidirectional type in the nature. This means that the blade moves in the one direction in air flow which alternate over the
period of the time. Other propeller which are unidirectional move in the one direction in the air flow and reverse in the alternate air flow.
Fig.1 Rising & Falling Water Column showing two direction air-flow
This paper also study the accessory added to the turbine which can help the low efficiency wells turbine to increase its overall efficiency. This include the object that can increase the air velocity of the turbine housing to generate more torque and rpm of the turbine. The additional torque that is been generated by the turbine hence can be used in the two stage gear box in increase the rpm at generator. Optimization works in the area of wells turbines are new and very few turbine have applied optimization techniques at sea structure to improve the turbine performance through study, analysis and design optimization. This article discusses different turbine options along with the performance improvement achieved through design, simulation and testing.
For this we have taken the 3D model of the turbine in the tank filled with water to simulate the operation of the wells turbine.
-
ASSUMPTION AND EXPERIMENTAL SETUP
-
Assumption: –
-
The OWC wells turbine structure is located in the seaside were the high tide and low tides has very less varied. This can be achieved by simulation of the sea in the tank of water were one side is made shallow as in the beach.
-
The simulation of the tide that has a frequency of 20 waves per minute or every wave per 3 sec this can be achieved wave generation throw the motor waver in the water of the tank.
-
Assuming the wave in the tanks occurs every 3 sec hence
-
The water level should rise 60 mm in the slanted portion of the tank.
-
Volume of the water displaced is in ideal condition.
-
The increase in the water level react with air column above it.
-
The air will move out through the hole in the above.
-
Diameter of the hole is 89 mm.
-
Air reacting with water is in ideal condition non-compressible fluid.
-
-
-
Setup of the water tank: –
Tank: The water tank we have taken is in the dimension of the 700x400x400
Fig 2 Design of Tank
In the following tank, the part of the sea is been simulated by the creating the wave manually. by the assumption no. 1 the water rise in the part of the tank by 52 mm in the part were the well of the turbine is been simulated as shown in the above Fig. 2.now considering the displacement of the water in the 52 mm block of water :
Fig.3 displacement of the water by volume
Calculating the following:
Volume of the water displaced (V1) = 5830448.839 cubic millimeters = 0.005830 cubic meters
Flow rate (Q) = Volume (V1) / Time I.e. Q= 0.005830 / 1
Q= 0.005830 m3/s
Now, the velocity of the air passing through the tank is Q=A x v
Here,
Q= flow rate of the air
Q= 0.005830 m3/s
A= area of the upper surface A= 0.050 m2
-
design of the turbine housing: –
Fig. 4 Housing of Turbine
The housing of the turbine is cylinder shape container were the road is attach to the rod holding bearing support at the entrance of the housing as well as at the end of the housing. The also contain the turbine blade join to the rod at the middle of the housing. The rod is connected to the generator which is located at upper side of the turbine. The housing is open from both side allowing the air to pass by. Diameter of the tube = 82 mm
Area = 3.14x 412
Area = 5281.01 mm2 = 0.0052801 m2
Time =3 sec (wave occurs every 3 sec) Displacement =0.00583 m3
NOW DOING SIMULATION OF DISPLACEMENT IN THE SOLIDWORKS
Fig. 5 Flow Simulation
RESULT:
Name |
Value |
GG Minimum Velocity 1 |
0 m/s |
GG Velocity 2 |
3.498 m/s |
GG Bulk Av Velocity 4 |
0.175 m/s |
GG Minimum Velocity (Y) 5 |
-0.738 m/s |
GG Velocity (Y) 6 |
3.481 m/s |
GG Bulk Av Velocity (Y) 7 |
0.148 m/s |
Table 1. Velocity of the air in normal housing
Fig. 6 Chart of GG Velocity (Y) 6
The velocity of the air in the housing as per the simulation is
3.498 m/s when 0.00583 m3 of water Displaced in the tanks well
-
At the entrance of the housing from the well structure
-
At the entrance of the housing from the atmosphere
Introducing the shoot to the assembly and simulating the velocity of the air here is the fig of the shoot placement in the assembly.
Fig. 7 Shoot Placement
NOW DOING SIMULATION OF DISPLACEMENT IN THE SOLIDWORKS
RESULTS:
Fig.6 Simulation of the Air Flow
Name
Value
GG Minimum Velocity 1
0 m/s
GG Velocity 2
6.227 m/s
GG Velocity (Y) 3
6.227 m/s
GG Minimum Velocity (Y) 4
1.462 m/s
Table 2. Velocity of the air in normal housing
Fig. 8 Chart of GG Velocity (Y) 6
This show as the significant increase in the speed of the air in the housing. I.e. from 3.498 m/s to 6.227 m/s
-
This is around 70% increase in the velocity of the housing.
-
This addition speed will increase the torque to be generated
-
-
SELECTION OF THE BLADE:-
increasing the velocity of air flow in housing by introduction of shoot: –
The velocity of the air passing through the housing is 3.498 m/s which pass through the cylindrical housing in the straight direction, with reducing the diameter or more specifically without reducing the area of the housing through which we can increase the speed of the air farther. This can be done by introduction of the part which by decrease the volume of the housing. A cone shaped piece is used in the housing around the rod to decrease volume of the housing. The cone do not turn with the rod it is stationary items, this named as the shoot. There two shoot introduce to the assembly:
The blade of the turbine is the most important part of entire system as it give the require measure to generate the energy. The blade that are to be used into the system should enter act with air flow in bidirectional way so that the maximum energy can generated. The following type of the blade is most used to generate energy.
They are three types of blade that are used in the turbine:
-
WIND BLADE TURBINE
Wind turbine blades are airflow-shaped blades that harness wind energy and drive rotor of a wind turbine. The airflow- shaped shaped which provides lift in a fix wing aircraft and is used to allow the blade to exert lift perpendicular to wind direction. The reverse of it is used in the wind blade of the wind energy program this type of blade is best for the single direction of the wind. Hence this blade is our first choice. The simulation tells more about the blade in two direction wind.
Fig.9 3D Model of Wind Blade
Following are the dimension of the following blade
Fig.10 2D Drawing of the Wind Blade
Considering the speed of the air in the housing is 6.227 m/s And the blade is fixed in the middle of the housing, now doing simulation in the solidworks.
Fig. 11 Simulation of Turbine with 3 Blades
The following simulation is done in two ways i.e. in bidirectional air flow
-
Air flow in upward direction
-
Air flow in downward direction
-
Name |
Value |
SG Torque (Y) 1 |
0.0805N*m |
SG Force (Y) 2 |
0.021 N |
-
in upward follow
-
in downward follow
Name |
Value |
SG Torque (Y) 1 |
0.0021 N*m |
SG Force (Y) 2 |
0.01 |
-
PROPELLER SHAPED TURBINE
The propeller shaped blade are used in the driving the ship in the ocean. The torque created by the propeller is allow the ships to move around in the water. Its edges highlight an angled air foil with its plane of twisted around the central axis
in the plane of revolution and opposite to the air stream. Its efficiency is high than that of a turbine with constant air stream direction however not so in the opposite direction. This type of case is the biggest disadvantage of it.
Fig. 12 3D Model of the Propeller Blade
Following are the dimension of the following blade
Fig. 13 2D Drawing of the Propeller Blade
Considering the speed of the air in the housing is 6.227 m/s And the blade is fixed in the middle of the housing, now doing simulation in the solidworks.
The following simulation is done in two ways i.e. in bidirectional air flow
-
Air flow in upward direction
-
Air flow in downward direction
Fig14. Simulation of Turbine with Propeller Blade
Name
Value
SG Torque (Y) 1
0.02 N*m
SG Force (Y) 2
0.1967 N
-
In upward direction
-
In downward direction
Name
Value
SG Torque (Y) 1
0.0019 N*m
SG Force (Y) 2
0.015 N
The general torque in up wind is 0.02 N*m and the general torque in downwind is 0.0019
-
-
-
SYMMETRICAL SHAPED WIND BLADE
Wells turbine is a low-pressure air turbine that pivots ceaselessly one way autonomous of the heading of the wind stream. Its edges highlight an even air foil with its plane of symmetry in the plane of revolution and opposite to the air stream. Its efficiency is lower than that of a turbine with constant air stream direction and asymmetric air foil.
The modelling of the symmetrical shaped blade is been done on the solidworks software. The blade has 5 symmetrical blades to be used in the process following is the diagram and the model of the wind blade.
Fig.15 Design of 3D Model of Symmetrical Blade
Following are the dimension of the following blade
Fig. 16. Shape of Wind Blade
Considering the speed of the air in the housing is 6.227 m/s And the blade is fixed in the middle of the housing, now doing simulation in the solidworks.
The following simulation is done in two ways i.e. in bidirectional air flow
-
Air flow in upward direction
-
Air flow in downward direction Time =3 sec (wave occurs every 3 sec)
-
Fig. 17 Simulation of Turbine with Blade
-
In upward direction
Name
Value
SG Torque (Y) 1
0.017 N*m
SG Force (Y) 2
0.106 N
-
in downward direction
Name |
Value |
SG Torque (Y) 1 |
0.019 N*m |
SG Force (Y) 2 |
0.13 N |
2.5.3 SYMMETRICAL SHAPED WIND BLADE
The following simulation show as that different torque of this three wind blade in bidirectional way. The blade that can be selected must have average torque in both direction near it value in any one direction.
The following table show the torque generated in the housing with velocity of the 6.227m/s.
Blade |
Flow in forward direction |
Flow in backward direction |
average |
Wind mill shaped |
0.0805 |
0.0021 |
0.0413 |
Propeller shaped |
0.02 |
0.0019 |
0.00595 |
Symmetrical |
0.017 |
0.019 |
0.018 |
Bar graph 1. Graph of Torque of blade
The average of the torque in both direction is given by
Bar graph 2. Graph of Average Torque Selection of the blade are done as below:
-
As it seen in the bar graph 2. Graph of Average Torque, the propeller shaped wind have the average below the other average of the blade hence this blade cannot be taken in the experiment setup.
-
The wind mill shaped have the highest average among the 3 blade however the 2 reading of the blade i.e. upward flow torque and the down ward flow torque should be with +_10% of the average value
-
Upward flow torque=0.0805.
-
Down ward flow= 0.0021.
(3) Average=0.0413.
-
The upward torque is not equal to
+_10% of the average value + average value…
-
The downward torque is not equal to
+_10% of the average value + average value…
Hence cannot be taken as the blade of the turbine
-
-
-
The symmetrical type of they have the second highest average among the 3 blade, however the 2 reading of the blade i.e. upward flow torque and the down ward flow torque should be with +_10% of the average value
-
Upward flow torque=0.017.
-
Down ward flow= 0.019.
-
Average=0.018.
-
The upward torque is equal to +_10% of the average value + average value.
-
The downward torque is equal to +_10% of the average value + average value.
-
The following selection can be explained by following:
-
the upward air flow i.e. when the air is pushed out of the tank generate more torque then when downward i.e. during suction of the air into the tank.
-
Therefore, the upward torque is called as the speed driving torque and downward is called drag torque
-
When the rpm generated by the upward torque during the wind push out of the tank drive the turbine blade at the highest possible rpm.
-
When the wind is sucked into the tank the rpm during that is less then that of the upward torque.
-
the average of the both air flow rpm is around the +- 10% of the average torque, this help when to keep the rpm around the suitable position where it can work smoothly even if the upward air flow comes at the low velocity or late by the time.
-
INTODUCTION OF THE GEAR TRAIN: –
The addition torque that we get from the increasing the velocity of the air in the housing from 3.498 m/s to 6.227 m/s give as that increase in the torque that can be used in the joining the gear box. The gear is added in such a way that the speed of the rotation that we gain from the turbine are gradually increase. The two-stage gear system is used for this system
The specification that we get from the turbine output are as follows:
1. Torque=(T) =0.018N-m= 18 N-mm
2. Force=(P)=0.13 N/m Since 1N/m=1W
Therefore, the force=0.13W
Using the simple relation between power, torque and rpm: – P=
-
Where,
P=force T=torque N=rpm
-
n =
n= 68.96== 69 rpm
-
For the first gear train, we assume that the efficiency of the gear is 85%.
-
Efficiency =
0.85=
G2=0.1105 N/m
-
Now considering the value from the table of the module, pitch diameter and torque.
-
We get,
Module = 4
Pitch diameter = 45mm
No.
Item
Symbol
Formula
Gears
Pinion (1)
Gear (2)
1
Module
m
Set Value
4
2
Reference Pressure Angle
20 deg
3
Number of Teeth
z
18
10
4
Center Distance
a
(z1 + z2) m / 2NOTE1
54.000
5
Pitch Diameter
d
zm
40.00
25.00
6
Addendum
ha
1.00m
4.00
4.000
From that we can calculate all other measurement of the gears
7
Tooth Depth
h
2.25m
9
9
8
Tip Diameter
da
d + 2m
48
33
9
Root Diameter
df
d 2.5m
30
16
Every rotation of the gear 1 turn the gear 2 8 times with the 20 % reduction of the torque.
-
Design of the first gear
-
Parameter to design are
-
Pitch diameter = 45mm
-
Number of Teeth = 18
The design is done in the solidworks: –
Fig.18 3D Model of the 1st Gear
And for the 2nd gear in the gear train
-
-
Parameter to design are
-
Pitch diameter = 25mm
-
Number of Teeth = 10
The design are done in the solidworks:-
Fig.19 3D Model of the 2nd Gear
1. The meshing of the first stage gear is shown in the below drawing
The ratio of the this 2 gear are as follows Gear 1 = 1:1.8 = gear 2
2. The second stage of the gear box.
. The gear are added in such a way that the speed of the rotation that we gain from the turbine are gradually increase. The two stage gear system is used for this system
The specification that we get from the first stage output are as follows:
3. Torque=(T) =0.015N-m= 15 N-mm
4. Force=(P)=0.11 N/m Since 1N/m=1W
Therefore, the force=0.11W
Using the same gear train for the second stage as it optimum level of the torque is reduce by it hence not stopping the process in the middle of the operating turbine.
Therefore the gear system would look like the following:-
Here the gear no 2 and the gear number 3 are connected by axis rod that is the two gear rotates at the same speed.
The gear ratio are as follows Gear1:Gear2: Gear3:Gear4 1:1.8:1.8:3.24
This means that when the gear number 1 completes 1 rotation the last gear i.e. gears no 4 will rotate 3.24 rotation. This means that when the gear 1 rotates 69 times, the gear no 2 will rotate 1.8 times that of gear no1 which comes out to be 124.2 and gear no 4 will rotate 3.24 times that of the gear 1 that comes out to be 223.56 times
Hence the gradually decreasing the torque help as to achieve this speed without rick of being jammed half the process.
-
-
-
INTODUCTION OF GENERATOR FOR THE MODEL:
Now using the known dc generator, we calculate the power generated by the turbine:
-
This generator is the bipolar with the magnetic flux of
-
As the no of the conductor are 2 and the number of the paths are also 2
-
By using the following formula for calculating the power output E=0P N/60
-
The RPM of the turbine is 224 Following are the known value of the motor
3. 3D PRINTING OF THE PARTS
We 3D printed the parts using Ender 3 V2 using Prusa Slicer software (v2.4.0). Software gave us complete information about the time required by the ender 3 v2 to complete each part and also weight of the part.
E=12v
Fig 20 motor/ generator
Information of ENDER 3 v2: –
The firmware version used in ender 3 v2: – Ver 1.0.2. Build size of the machine: – 220*220*250 mm.
Machine Size: – 475*470*620mm. Machine Power: – 350W.
Net Weight: – 8KG.
Material used: -Polylactic Acid
Rpm = 800
-
Operating Voltage(V): 9v
-
Rted Speed (RPM): 600
Rated Torque(kg-cm): 2.2=2.2x 0.980665=2.1N- mm
-
Now considering the equation
Where, E= power output
= magnetic flux P = poles
N = speed in rpm
Now by rearrange the formula
-
E1= , for the known power
-
E2= , for the unknown power
-
Therefore,
E1= = .(1)
E2= = .(2)
-
From (1) and (2)
-
The valve from the known factors substituting value
-
E2= 4.5 V
The output power of the turbine is 4.5 v or 2.25x 10-3 kW The model that is been used is 100 times smaller than the actual working turbine at coast.
After importing STL File into Pursa Slicer software it provided a G-Code file. G-code file through a memory card is inserted into Ender 3 V2 with settings given below: –
TABLE 3.3 3D printer setting before start of Printing
Sr no |
Printer Setting Name |
Setting |
1 |
PLA temp |
200-210°C |
2 |
Bed Temp |
60 |
3 |
1st layer height |
0.4 |
4 |
Next layer height |
0.15 |
5 |
Infill |
30% |
6 |
Speed |
20mm/sec |
7 |
Quantity/Parts |
4 |
Following is image of the 3D printed model
FIG 21 TURBINE GEAR BOX ASSEMBLY
RESULTS AND DISCUSSION
The report describes working of the OWC wells turbine with various aspect of it. The OWC wells turbine is the low efficiency turbine as it torques in the two direction of the wind are different. The torque in the direction of the air pushed out is more powerful, then the wind that is pull inside the turbine housing. This happen due to compression phenomenon of the air, therefore the downward torque is drag torque that work as the running the turbine at the constant speed that the upward torque generated.
The shoot introduces in the housing at the angle of the 100 to 110 so that they give the angle to the air rather than blocking the air flow or create a turbulent flow of the air. The 100 to 110 angles are the point that amplifies the power that we get turbine without shoot. This extra torque is very important for the next step.
The extra power that we get is used in the two-stage gear box that requires that is reverse of the reduction gear. This is a two-stage gear box that multiples the 3.24 times the speed that is produces by the turbine. The two stage is use it can distribute the effort to revolve the gear is reduced greatly. The high armature motor is used to convert this mechanical energy into electricity
Considering the model used for the construction is 100 times small then power that we get much greater than the experiment model, the actual model works in company of 5-8 turbine, this company of the turbine is more than capable to power the small town of the people
The experiment of study and modification of the wells turbine successful
develop our project. Last, but not the least, we would like to thank our friends for providing us the support and contributing in our project work.
REFERENCES
[1] Manabu Takao1 and Toshiaki Setoguchi2, Air Turbines for Wave Energy Conversion in International Journal of Rotating Machinery Volume 2012, Article ID 717398, 10 pages [2] Sunil Kumar Mishra, 1 Bhargav Appasani, 1 S.Amitkumar Vidyakant Jha,1 Izaskun Garrido , 2 and Aitor J. Garrido2, Centralized Airflow Control to Reduce Output Power Variation in a Complex OWC Ocean Energy Network in Hindawi Complexity Volume 2020, Article ID 2625301, 16 pages https://doi.org/10.1155/2020/2625301. [3] Torresi marco 1,Sergio Mario camporeale2, Daniela pranzo, Giuseppe pascazio, improved design of high solidity wells turbine in research gate publication January 2011 [4] Ahmed s. Shehata1, khalid m. saqr2, Qing xiao3, sandy day4, wells turbine for wave energy conversion in International Journal of Energy Research · January 2017 [5] Orrin Lancaster1, Tom Bladock2, Remo Cossu3, Scourprediction around an oscillating water energy converter in research gate publication January 2011
[6] Rameez Badhurshap, Karthikeyan Thandayuutham2, Abdus Samad3, oscillating water column wave energy system in research gate publication January 2011 [7] T. V. HEATH, A review of oscillating water columns in Phil.Trans. R. Soc. A (2012) 370, 235245 doi:10.1098/rsta.2011.0164
[8] Ahad Sedaghat1, Ahmadreza Zamani 2, design of chamber and wells turbine for oscillating of water for extracting wave energy from anzali port in research gate publication December 2012 [9] Y T. V. HEATH, A review of oscillating water columns in research gate publication January 2016 [10] Antonio Falcao1, Joao c. c. henriques oscillating water column wave energy converters and air turbine in research gate publication January 2016ACKNOWLEDGMENT
We would like to express our gratitude and appreciation to all those who helped us in completion of our project. Special thanks to project guide Prof. Sneha Shirke for providing us with the necessary help, suggestions and encouragement during completion of the project. We also sincerely thanks for the time spent proofreading and correcting our many mistakes. We sincerely thank our college for providing us the opportunity to
SPECIAL THANKS TO
Invensys Cad Solution
-
Director: Anil J. Pagar Sir
-
Training Executive: Sushil S. Pote Sir