
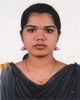
- Open Access
- Authors : Athira K P , Haris Naduthodi
- Paper ID : IJERTV9IS070642
- Volume & Issue : Volume 09, Issue 07 (July 2020)
- Published (First Online): 04-08-2020
- ISSN (Online) : 2278-0181
- Publisher Name : IJERT
- License:
This work is licensed under a Creative Commons Attribution 4.0 International License
Optimization of Scallops on Curved Surface of 3D Printing
Athira K P
M. Tech Student Department of Production Engineering
Government Engineering College Thrissur, India
Haris Naduthodi Professor
Department of production engineering Government Engineering College Thrissur, India
Abstract 3D printing or additive manufacturing is a process of printing three dimensional solid objects from a STL file. Previously the process was just a rapid prototyping compromising part geometry and material on account of reduced processing time. However, the process is evolving to a solution for manufacturing processes with shape flexibility. There exists sufficient research potential for improvements in additive manufacturing due to various errors inherent to the process. For curved surfaces, the surface is irregular due to staircase effect compared with planar surfaces. In the latter case, irregularity is contributed the unevenness across the layers. The layer thickness, being the culprit for this error, needs to be primarily controlled. Adaptively computing the layer heights for 3D printed parts has the potential to achieve high quality results while maintaining a reasonably short printing time. During layered manufacturing, steps are formed, due to staircase effect, at the work piece surface, the primary error, which requires finishing before use. The secondary error is due to unevenness within the slices while freezing the layer. In this paper ball burnishing is proposed as a suitable finishing process to reduce the stair step effect in thin slicing layer to obtain a particular geometry. Workstation is integrated with the 3D printer. The conceptual model of the post processing station and process parameters are identified.
Keywords STL, Stair step error, Adaptive Slicing, Ball burnishing.
-
INTRODUCTION
Applications of additive manufacturing are in increasing trends in industries including medical field. During the early of 1980s rapid prototyping was introduced first. The main advantage of additive manufacturing is the product flexibility at relatively lesser process time. The weight and strength of the solid parts can be controlled by changing the infill percentage. The mechanical properties of the printed products depend on the properties of material used in printing. The product designer can select multiple materials according to the functional requirements. The major disadvantage of the process is the poor surface quality. The surface error is contributed by stair step errors, a systematic error inherent to the process, while developing curved surfaces such as cylindrical, conical, spherical or free form. The surface quality can be improved by using adaptive slicing which states the quality is directly proportional to the number of layers. As the number of layers increased the surface quality of the printed product increased but the processing time is compromised. The surface quality obtained depends on the approximation algorithm used in data exchange to STL(stereo lithography) designing software and specifications of 3D printer. It is impossible to obtain a printed surface represented
exactly as in the CAD file without data loss. This paper also discusses a selective surface treatment method as a post process to the typical additive manufacturing in order to reduce the effect of steps formation on the outside surfaces especially on curved surfaces. The proposed post process is ball burnishing where in no material is removed but is redistributed across the lays. Due to the rolling contact between the roller and printed surface, the surface finish and strength will increase.
Poly lactic acid (PLA) filament with 1.75mm diameter is used as the working material and Creality CR 10S pro 3D printer is used for printing the specimen. This paper focuses on the deviation for printer surface from the intended surface represented in the design. Florens, NJianwei, Z et al. [1] investigated the error measurement for this compared the volumetric surface deviation between the model and 3d printed product with optimum control. According to the implementation of adaptive slicing algorithm the surface quality could be increased and also a focus on the usability of a rather complex concept for users without extensive previous knowledge. Here an efficient computation of adaptive layers by analyzing the model surface over the full layer height and implementations were available as ready-to-use open source software. K. Mani, P. Kulkarni and D. Dutta [2] implemented new methods for region-based adaptive slicing. In this, users can implement adaptive slicing on the surface which need more surface finish. Souvik, B. Hota [3] states in his review paper using ball burnishing process the surface error will be reduced and also strain hardening will happen. Diameter of ball, amount of leveling, layer thickness, and rolling force are considered as the parameters. Heechang, K. et al. [4] used analysis of variance (ANOVA) method for analyzing the relation between optimum parameters and mechanical properties. PLA material with 100% fill rates in x- direction can perform improved mechanical properties. G R E Mrie¹ and A M Abrudan¹ [5] studied the characteristic and behaviors of thermoplastics. These properties help to find the perfect material for product design and production.
From the studies of K. O. LowKing Jye Wong [6] ball burnishing process is favorable as a surface post processing method. A. E. Tontowi [7] et al reported the tensile strength is varying with layer thickness and the dimension error was dominantly depends upon raster angle. They state that, according to current condition it is impossible to print a part having complex geometry and shape with any orientation angles using 3D printer machine with fixed printing movement. Daniel and Chris McCoy [8] studied the relation
of infill and tensile strength. In this work it was found that the specific ultimate tensile strength of the 3D printed product is directly proportional to the infill percentage with hexagonal and rectilinear infill geometries. The strength and stiffness of hexagonal infill geometry is higher than rectilinear geometry. But in the case of deformation, the deformation of rectilinear infill is lower than hexagonal infill when the same load was applied. Deepak and Ravindra [9] have identified significant process variables for ball burnishing as burnishing force, speed and feed. The authors have used aluminum and steel materials as the material for ball in polymers. Surface roughness and hardness values are the important measured variables. The methodologies are based on mathematical modeling and experimental analysis. M. J. Puttock and E. G. Thwaite Nat [10] developed equations for finding the relation between forces and surface penetration of surface in contact. Mechanical properties of different material in different physical thermal conditions are also documented. A data structure for adaptive slicing has reported. Mechanical, Electrical, Chemical properties of plastics are depends upon its thermal properties. E. Alfredo Campo [11] tabulated these relations in his studies. N.H. Lohs, C. Tams, Miyazawa [12] used response surface methodology for preparing model for ball burnishing process. In this case depth of penetration, feed, and burnishing speed are considered. Fitting polynomials of first and second degree of freedoms are used for design and analysis purpose.
The nickel, chromium and iron alloy (Nichrome) is considered as the transducer in the study of R. Sinclair [13]. Good resistance to the oxidation, high resistivity is the main advantages of Nichrome. Review paper of Natasch Andraschek 1,*, Andrea Johanna Wanner 1 [14] gives the information about increasing the demand of Mica with development in electrical industry. It performs best electric insulation. Alan Meier, [15] conducted survey to find the features and working of traditional and modern thermostat. Temperature controlled working condition is possible with electric thermostat.
-
PROBLEMSTATEMENT
In the case of additive manufacturing and 3D printing process in particular the surfaces generated are of inferior quality. This limitation is high while producing curved surface. Identification and elimination of the causes of errors is critical in process control. The literature survey conducted on the methods revealed the fact that adaptive slicing has proposed many authors and found reduced the surface errors up to certain extend. Hence it was decided to set the following objectives for this work
-
OBJECTIVE AND METHODOLOGY
-
To study the adaptive slicing method and propose improvements
-
To design a post processing station for a selective smoothening of curved surfaces.
The methodology adopted in this work is given below : Development of CAD model
Exchange to STL format
Experimentation
Building with constant slice thickness Building the part with adaptive slicing Test of surface
Post process Conceptual design
Create a 3D model with flat and curved surfaces using modeling software so that both surfaces could be compared. The CAD data is exchanged to the stereo Lithography (STL) format. The staircase errors and roughness errors could be evaluated with and without adaptive slicing in both curved and flat surfaces. Similarly the experiment is repeated after burnishing.
A post processing station integrated with the existing 3D printer is also attempted.
-
-
PROBLEM AND SOLUTION
-
Errors in curved and flat surface
3D model with dimensions of 5cm side cube and5 cm diameter hemisphere as shown in figure 1. There are mainly two types of surface errors in the 3d printed surfaces. Stair step or primary error () error and surface roughness error or secondary error (r) as shown in figure 2. Sum of these considered as the total error in this work [1].
Error measurement, = s+ r = (sin/2) * h + Cr * h
So, h ((sin/2) + Cr)/
Cr= empirically determined constant factor which describes the elliptical structure and
= Raster angle
Adaptively computing the layer heights for 3Dprinted parts has the potential to achieve high quality results while maintaining a reasonably short printing time. During adaptive slicing the layer heights are adjusted depending upon the surface variations.
Range of layer heights = [hminhmax] hmax = maximum layer height
hmin = minimum layer height
When, min = Cr *hmin where (sin =0) max = (hmax /2) + Cr *hmax where (sin =1)
Fig. 1 specimen with flat and curved surface
Fig.2 surface errors
Considering quality parameter Q = [0…1] and scale quality parameter Qs,
Qs = Q *(max -min) + min
When Q = 0, minimum layer height Q = 1, maximum layer height
Values in-between select smooth profiles according to the cusp values.
-
EXPERIMENT RESULT
-
Comparison on surface roughness values
For the normal case without adaptive slicing the surface roughness value of flat surface and curved surface is tabulate d below in Table.
Sl. NO.
Surface roughness without adaptive slicing
Surface roughness with adaptive slicing
Curved surface (s)
Flat surface (r)
Curved surface (s)
Flat surface (r)
1
2.787
2.224
1.176
1.732
2
3.441
1.408
1.172
2.04
3
3.529
1.835
3.180
1.836
4
3.800
2.206
3.199
2.024
5
2.217
1.443
2.622
1.732
6
1.083
1.835
1.132
1.626
Average values
2.809
1.820
2.08
1.832
Table.1 Surface roughness for curved and flat surfaces with and without adaptive slicing
For the model surface, roughness value of curved surface is comparatively higher than flat surface. The surface quality of curved surface needed to be improved. The adaptive slicing has improved average surface roughness from 2.809 to 2.08. However, there is no significant change in flat surface. One major disadvantage of adaptive slicing is increased processing time due to high number of layers. In this case maximum and minimum layer height is manually fixed. Minimum layer height is taken as 2mm and minimum layer height is taken as 4mm.
-
Number of layers in adaptive slicing
The number of layers is a controllable parameter in 3D printing. It can use as a tradeoff between surface quality and process time. As the number of layers increases surface quality also increases (Fig.3). Using adaptive slicing time and numbers of layers are optimized with good surface quality.
Fig.3.surface roughness value versus number of layers
-
-
-
Post processing Ball burnishing
Majority of additive manufacturing products are of materials with low melting point such as polymers. This part of the work also discussed the case of Poly lactic acid. It has been found in the previous experiment that the errors are inherent with the process in case of the requirements for smooth surfaces additional process are to be added to the 3D printing machine. The propose post process is ball burnishing. It is a process by which a smooth hard steel ball, using sufficient pressure, is rubbed on the surface. This process flattens the high spots by causing plastic flow and consequent strain hardening. It improves the surface finish, surface hardness and wear-resistance. The typical set up of a burnishing process is shown in figure 4.
Fig.4. Ball burnishing process
The type of tooling and the requirements of motion in burnishing process differs from the tooling of a 3D printer, it is suggested an additional station to the 3D printer. However, the same controller can handle both the stations. The burnishing ball travels in longitudinal direction as shown in figurer 5. The burnishing tool is heated to a temperature of about 75% of its glass transition temperature; we can reduce the requirement of tool force.
Fig.5.Tool movement
The control of tool movement along the lays and its orientation is achieved by numerical methods. The Gcodes (ie coordinates of cloud points) obtained from STL format are used for discrete representation by the slope change notation reported by Ernesto Bribiesca, 1992. The orientation of burnishing tool has to be normal to the profile. This achieved by the tool is oriented perpendicular to the slop of the line joining to corresponding extremities of two consecutive layers. Table 2 shows the sample data.
Sample layers
Coordinates of extremities
Slope (degree)
x
y
z
362
149.16
158.30
72.86
-2.6
363
149.13
158.24
72.92
-2.6
364
149.10
158.12
73.00
5
td> 365
149.12
157.96
73.10
4.7
366
149.15
157.58
73.24
4
Sample layers
Coordinates of extremities
Slope (degree)
x
y
z
362
149.16
158.30
72.86
-2.6
363
149.13
158.24
72.92
-2.6
364
149.10
158.12
73.00
5
365
149.12
157.96
73.10
4.7
366
149.15
157.58
73.24
4
2. EXPERIMENT RESULT Sample set burnishing tool path
General equation for Sphere in contact with a plane [10],
. (1)
Where is in-feed, P is the load in Kg, V1 and V2are material constants in general
Where m is Poisson ratio and E is youngs modulus
The in feed, = 0.08the diameter of burnishing ball , D = 8mm
Using the general equation the sphere in contact with a plane, the total load to be applied is calculated from (1)
P = 412.84 gf
4.04 N
-
Heating of burnishing tool
Poly lactic acid is a thermoplastic material. It can be softened easily by heating and reshaped. Controlled tool heating is required for this ball burnishing process. Glass transition temperature (Tg) of PLA is 60°C. We have set the temperature 75% of the Tg value. The transition will take place from hard and relatively brittle glassy state into a viscous or rubbery state (Fig.6) as the temperature is increased
Table.2.burnishing tool path discrete data
The in-feed in burnishing process is depended by the cusp height. The cusp height is shown as BD and layer thickness is AB in figure 6.
Fig.6. Cusp height geometry
The in-feed is taken as half of the cusp height, the cusp height is a function of slice thickness. These relationships could be implemented in the program controlling the motion. The work done in burnishing is also to be calculated.
Sample load calculation:-
Layer height is 0.2 the cusp height = 0.17 Layer height is 0.4 the cusp height = 0.16
From this the expecting tool penetration, = 0.08 mm.
Working temperature
Fig.7.Change of mechanical property with respect to temperature
For the supply of controlled heat to ball burnishing tool heating coil with thermostat control is used. Transition temperature is 48° Celsius and after this the material state will start to change. This circuit shown figure 8 consist mainly four components.
Fig.8. Circuit for tool heating
-
-
CONCLUSION AND FUTURE WORK
Adaptive slicing is a prominent method used in additive manufacturing for controlling the inherent errors with the process by reducing slice thickness locally. This has drastically reduced the process time and hence productivity. In this study it was found that 25.71 % increase in surface finish is obtained by enhancing 3.4%increment in number of layers, but there is a huge time loss.
A mechanical method of post-processing has been focused to overcome the deficits caused by surface properties, and may bring more suitable tolerances to the end products. Burnishing process can improve the surface quality of the curved or irregular surface. Current practice in industries is to do post process in conventional machines and may take more time than the additive manufacturing process. In this work the post process, that is burnishing is incorporated to the printing machine as a processing station with required tooling under the same controller. The slope calculated from point data from STL file has used for orientation of burnishing tool. The tool orientation is obtained by a single degree of freedom obtained a turning pair. The rotation is governed by the slope variation. The application of heated burnishing tool contributes reduction of load requirements and size of the machine and tooling.
The staircase error or scallop is a common phenomenon in all machining process where the control resolution of the machine is the culprit. In additive manufacturing slice thickness is the smallest controllable length along the axis of filling, that too not in a straight line due to the effect of molten PLA during lying. The slice thickness in additive manufacturing is thousand times larger than the control resolution of conventional CNC machines, thus the errors are predominant in the case of additive manufacturing.
The design of post processing station is only in conceptual level. Motion work piece relative to burnishing tool is to be discussed and integrated with the additive manufacturing machine. The round edged slices contribute r errors. This is to be controlled by research on surface tension on the process parameters.
REFERENCES
-
FlorensWasserfall, Norman Hendrich and Jianwei Zhang, Adaptive Slicing for the FDM Process Revisited. 2017 13th IEEE Conference on Automation Science and Engineering (CASE) Xi'an, China, August 20-23, 2017.
-
K. Mani, P. Kulkarni, D. Dutta, Region based adaptive slicing, Computer-aided Design, Volume 31, Issue 5, 30 April 1999, Pages 317-333.
-
Souvik Brahma Hota. Eliminating the Stair Step Effect of Additive Manufactured Surface-A Review Paper. www.ijraset.com Volume 5 Issue IV, April 2017 IC Value: 45.98 ISSN: 2321-9653
-
Heechang Kim, Eunju Park, Suhyun Kim, Bumsoo Park, Namhun Kim, and Seungchul Lee*. Experimental Study on Mechanical Properties of Single- and Dual-Material 3D Printed Products Heechang Kim45th SME North American Manufacturing Research Conference, NAMRC 45, LA, USA. Procedia Manufacturing 10 ( 2017 ) 887 897.
-
G R E Mrie¹ and A M Abrudan¹, Thermoplastic polymers in product design, IOP Conf. Series: Materials Science and Engineering 393 (2018) 012118 doi:10.1088/1757- 899X/393/1/012118.
-
K. O. LowKing Jye Wong, Tribological effects of polymer surface modification through plastic deformation. Article in bulletin of materials science 34 (7). December 2011.
-
A. E. Tontowi#1, L. Ramdani#2, R. V. Erdizon#3, D. K. Baroroh#4. Optimization of 3D-Printer Process Parameters for Improving Quality of Poly lactic Acid Printed Part. ISSN (Print) : 2319-8613 ISSN (Online) : 0975-4024 A. E. Tontowi et al. / International Journal of Engineering and Technology (IJET)
-
Daniel Farbman, Dr. Chris McCoy, MATERIALS TESTING OF 3D PRINTED ABS AND PLA SAMPLES TO GUIDE MECHANICAL DESIGN, Proceedings of the ASME 2016 International Manufacturing Science and Engineering Conference MSEC2016 June 27-July 1, 2016, Blacksburg, Virginia, USA
-
Deepak Mahajan* , RavindraTajane. A Review on Ball Burnishing Process International Journal of Scientific and Research Publications, Volume 3, Issue 4, April 2013 1 ISSN 2250-3153
-
M. J. Puttock and E. G. Thwaite, Elastic Compression of Spheres and Cylinders at Point and Line Contact, National Standards Laboratory Technical Paper No. 25 Commonwealth Scientific and Industrial Research Organization, Australia Melbourne
-
E. AlfredoCampo, 3- thermal properties of polymeric materials. Selection of polymeric materials, how to select design properties from different standards, plastic design library 2008,pages 103-140.
-
N.H. Lohs, C. Tams, Miyazawa, Application of experimental design in ball burnishing, international journal of machine tools and manufacture. Volume 33, issue 6, December 1993, Pages 841-852.
-
R. Sinclair, Temperature sensors and thermal transducers, sensors and transducers (Third Edition), 2001, page 87-115.
-
Natascha Andraschek 1,*, Andrea Johanna Wanner 1, Catharina Ebner 2, Gisbert Riess 2. Review: Mica/Epoxy composites for insulation, and investigations on failure mechanisms for prospective optimizations. 2016 by the authors; licensee MDPI, Basel, Switzerland. This article is an open access article distributed under the terms and conditions of the Creative Commons Attribution (CC- BY) license (http://creativecommons.org/licenses/by/4.0/).
-
Alan Meier, Cecilia Aragon, Therese Peffer and Marco Pritoni, Thermostat Interface and Usability: A Survey, ERNEST ORLANDO LAWRENCE BERKELEY NATIONAL LABORATORY. Environmental Energy Technologies Division, pages 9-12.
-
R . Stalin John , A. Welsoon Wilson , A. Prasad Bhardwaj , Avinav Abraham , B.K. Vinayagam. An investigation of ball burnishing process on CNC lathe using finite element analysis Simulation Modeling Practice and Theory 62 (2016) 88101
-
Ernesto Bribiesca. A Geometric structure for two-dimensional shapes and three-dimensional surfaces , Pattern recognition,
Volume 25, Issue 5, May 1992, Pages 483-496
-
Bharat ramachandra Baeltur, Adaptive Slicing in Additive Manufacturing using Strip Tree Data Structures, thesis , 2012. Amrita VishwaVidyapeetham, Bangalore, India.
-
A. E., Tekkaya, M., Kleiner, D., Biermann, L., Hiegemann, S., Rausch, V., Franzen, L., Kwiatkowski, P.Kersting, Production Engineering, 7, 601610, (2013).
-
Lars Hiegemann1, Chiranshu Agarwal2, Christian Weddeling and
-
Erman Tekkaya, Reducing the stair step effect of layer manufactured surfaces by ball burnishing process, AIP conference proceedings 1769,190002(2016).
-