
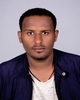
- Open Access
- Authors : Yabebal Kefyalew Abeje
- Paper ID : IJERTV11IS120132
- Volume & Issue : Volume 11, Issue 12 (December 2022)
- Published (First Online): 10-01-2023
- ISSN (Online) : 2278-0181
- Publisher Name : IJERT
- License:
This work is licensed under a Creative Commons Attribution 4.0 International License
Numerical Study to Investigate the Effect of CFRP Sheet on Ductility of Reinforced Concrete Slab
Yabebal Kefyalew Abeje
Department of Civil Engineering, College of Engineering, Assosa University, Assosa, Ethiopia.
Abstract: Carbon fiber reinforced polymer (CFRP) sheets have been used to improve structural behavior of reinforced concrete (RC) buildings and bridges. Due to the great advantages of the CFRPs, such as a high strength to weight ratio, high corrosion resistance and enhanced durability of structure, they have been used as strengthening materials to strengthen RC structures. CFRP result in significant an increase in ductility of member. Ductility of the resulting CFRP strengthened RC member plays an important role in structural performance, especially in earthquake resistant, where ductility plays a vital role in design of structures. This study numerically investigates the effect of strengthening CFRP sheet on ductility of RC. Powerful software in field of engineering, ANSYS was used to perform a structural 3D non-linear finite element analysis (FEA) of RC structures. The accuracy of the FEA method is verified in terms of concrete crack using experimental test results from literature. Effects of parameters on ductility, including sheet layer number, sheet width, sheet spacing and fiber orientation on ductility of RC slab was conducted. The ductility of the slab was expressed in terms of concrete damages and plotted with color regions. The blue, yellow and color ranges show the magnitude and distribution of scalar isotropic damage variable defined in CDP micro-plane model. By observing the color range of regions with blue, yellow and red colors in the concrete damage figures. Using comparison colors region range, a specimen having maximum of blue color regions behaves more ductile. The FEA results indicated that due to CFRP sheets the ductility of RC slab significantly enhanced.
Keywords: RC slab; CFRP sheets; ANSYS; Finite element analysis; parametric study; ductility
-
INTRODUCTION
In recent, fiber reinforced polymers (FRPs) have been increasingly used for retrofitting reinforced concrete (RC) members and carbon fiber reinforced polymer (CFRP) sheets have been widely used for strengthening RC structures. Slabs and beams are among the most commonly used structural members. Repairing or retrofitting of existing structures such as buildings and bridges has been amongst the most important challenges in civil engineering. There are many reasons for strengthening structures but the primary reason for strengthening structures includes upgrading of its resistance to withstand underestimate loads, such as due to increased perceived risk from seismic excitations, eliminating premature failure due to detailing error, restoration of lost load carrying capacity due to corrosion of reinforcing bars or types of degradation of caused by aging (Feng et al., 2018)
Structural elements such as slabs, beams, and columns require strengthening during their period of service life. Factors affect the requirement for strengthening of these elements including design or construction defects, increased load, change of structure operation, or new code requirements. FRP has many advantages, which make it more attractive for the civil engineering industry. They are available in several forms such as laminates and sheets. It has a high strength to- weight ratio, corrosion resistance, fast processing time, and flexibility. The use of FRP composite for strengthening RC element causes significant enhancements to durability, economics, and success (Emarah, 2019). In recent years, the carbon fiber reinforced polymer (CFRP) composites have been widely utilized to rehabilitate and strengthen weak and harmed RC structures (Al-Ghazawi and Al-Rousan, 2020). Teng and Zhang (2017) due to the superior material FRPs in enhancing durability, they have been used to strengthen deteriorated or insufficient concrete structure. Many of research efforts have been made to investigate the structural behavior of FRP strengthened RC slabs and further numerical study has been an effective method.
Feng et al. (2018) conducted both experimental test and FEA to study the effectiveness of the proposed strengthening schemes of the strengthened RC beamslabs in resisting progressive collapse. Among the four specimens, one was the control, two of them were strengthened by externally bonded GFRP laminates of different width, and the remaining was strengthened by GFRP. Vertical loads were applied on the removed column using two hydraulic actuators. Finally, concluded that the progressive collapse resistance, the peak load capacity and the bearing capacity of the sub-assemblage was mainly provided by the slab and beams.
Emarah (2019) conducted a numerical study to investigate the behavior of RC slabs with CFRP sheets. From total of five, one was taken as control and four specimens strengthened with CFRP of width 200, 300, 400 and 600mm. Found that the use of FRP composite for strengthening RC element causes significant enhancements to durability. Fathelbab et al. (2014) studied numerically fifteen real scales of size 6×2.1×0.12m one-way rectangular slabs. One specimen was control; other fourteen were strengthened by CFRP and also parametric study with four variables was done on strengthened specimens. First three of them were CFRP sheet width of 100mm, 200 mm and full length of slab and found that increasing in sheet width increase the slab ductility. The other three were CFRP length with full, 2/3, 1/3 of short span length and it was found that 2/3
of short span gives same results to full span but 1/3 of short span has less ductility than that of full length. The next five were CFRP sheet spacing of 1.5, 1.0, 0.6, 0.5 and 0.3 m and found that decreasing CFRP sheet spacing slightly increases the slab ductility. The remaining were with CFRP number of 1, 2 and 3 and it was found that with increased sheet number the ductility is significantly increased.
Lima et al. (2016) studied RC slab on numerical investigation the effect of loading direction on CFRP orientation. The result indicated that preferred CFRP orientation in slab is perpendicular to the loading direction. Mutlaq et al. (2020) studied the performance enhancement of damaged four two-way RC slabs. The use of CFRP sheets as an external strengthening has a significant effect on the cracking pattern of two-way RC slabs by delaying the occurrence of crack. The ductility of the slab enhanced due to strengthening CFRP. The value of ductility index ranges from 2.49 to 5.29.
Due to the great advantages of the FRPs, such as a high strength to weight ratio, high corrosion resistance and enhanced durability of structure, they have been used as
strengthening materials to strengthen RC structures. Thus, investigating the structural behavior of CFRP-strengthened RC member is essential. To investigate the effectiveness of CFRP sheet, a number of numerical studies of the structural behavior of slabs have been developed.
-
METHODOLOGY
-
Geometrical Specifications
Prototype Structure: is a five- story commercial purpose building with 6×4 bays (Lim, 2017) designed based on Euro code-2. The span length in both directions is 6m. The height of a typical story is 3m, while the ground floor height is 4.5m. The sizes of all the beams and columns are 250x450mm and 450x450mm respectively.
Experimental Test: due to laboratory space constraints,
15 scaled specimen was extracted from prototype structure in experimental test. Rotational restraints from adjacent slab are
represented by thicker slab portions r the thicknesses of extended slab increased by 50% beyond the perimeter beams compared to the main slab.
TABLE II-1 SECTIONAL SIZES AND REINFORCEMENT OF PHAM ET AL. (2017)
Type
Tested Specimens
Beam (mm)
100 × 180
Column
180 × 180
Slab (mm)
2400 × 2400 × 80
Beam Reinforcement
Bottom
2Ø10
Top
3Ø10
Column Reinforcement
–
4Ø10 & 4Ø6
Slab Reinforcement
Main
Bottom
Top
Ø6 c/c 150mm, full length
Extension
Bottom
Ø6 c/c 150mm, full length
Top
Ø6 c/c 100mm, L =720mm
Finite Element Modeling: experimental test specimen was modeled using ANSYS, mechanical. Concrete volume and only reinforcement plot is shown in Figure II-1. Powerful
software in field of engineering; ANSYS FEA software was used to develop 3D models of RC slabs. The general FEA producer is shown in Figure II-2.
(a)
(b)
Figure II-1 Plot of FEM (a) concrete volume; (b) only reinforcement.
Figure II-2 FEA producer in ANSYY mechanical APDL
Parametric Study Variables
The parametric study deals with four variables as follows:
-
The first one is CFRP sheet layer number, SN =1, 2, and 3.
-
The third one is CFRP sheet spacing, SS= 100, 200 and 300mm.
-
The fourth one is fiber orientation of CFRP sheet
2. The second one is CFRP sheet width, SW =100, 300 and 500mm.
composites, FO = 00, 450
and 900
TABLE II-2 PARAMETRIC STUDY MODEL SPECIMENS WITH COMBINATION OF VARIABLES
CFRP Attachment Configurations
Specimen
SN
SW
SS
FO
1
100mm
100mm
450
S-1
2
100mm
100mm
450- 450
S-2
3
100mm
100mm
450- 450 450
S-3
3
300mm
100mm
450- 450 450
S-4
3
500mm
100mm
450- 450 450
S-5
1
300mm
100mm
450
S-6
1
300mm
200mm
450
S-7
1
300mm
300mm
450
S-8
2
500mm
100mm
00- 00
S-9
2
500mm
100mm
450- 450
S-10
2
500mm
100mm
900- 900
S-11
The most common types of fibers typically used in FRPs are glass, carbon and aramid. These fibers are all linear elastic up to failure, with no significant yielding compared to steel. In general, when a RC slab is externally strengthened with CFRP to tension face, ductility of it is greater than their original slab.
FEA models of CFRP sheet strengthened RC slab specimens have been conducted using four parametric variables. Typical plot of sheet layer number, sheet width, sheet spacing and fiber orientation of CFRP sheet composites are shown in Figure II-3.
(a) SN-1 & F0 = 00
(b) SN-2 & F0 = 00 – 00
(c) SN = 3 & F0 = 450 – 450 – 450
(d) SW = 100mm & SS = 100mm
Where:
(e) SW = 500mm & SS = 100mm
-
SN is sheet layer number
-
SW is sheet width
-
SS is sheet spacing
-
FO is fiber orientation
Figure II-3 Plot of CFRP sheet typical sheet number, sheet width, sheet spacing and fiber orientations
-
-
-
Element Idealizations
Concrete: is idealized using CPT215 element. It is 3D-8N solid element (sown in Figure II-5, a) capable of modeling structural implicit regulation using a nonlocal field. It has elasticity, stress stiffening, large deflection, and large strain capabilities.
Reinforcing Steel: is idealized using REINF264 element. It is 3D-8N discrete element (shown in Figure II-4) suitable for
simulating fibers placed sparsely, or fibers with non-uniform properties, such as cross-section area, material, spacing, and orientation. It is uniaxial tension-compression and modeled separately as spar that has only uniaxial stiffness.
CFRP: is idealized using SHELL181 element. It is 2D-4N element (shown in Figure II-5, b) suitable for analyzing thin to moderate thick shell structures.
(a)
(b)
Figure II-4 (a) Geometry of REINF264 element; (b) REINF264 coordinate system
(a)
(b)
Figure II-5 (a) CPT215 structural solid geometry; (b) SHELL181 geometry
-
Material Models
Concrete: coupled damage plasticity, CDP micro-plane is used for concrete modeling. Advantage of this approach is to overcome numerical instability and pathological mesh
sensitivity problem causes due to strain-softening materials, concrete damage plasticity.
TABLE II-3 MATERIAL PROPERTIES FOR OF CONCRETE
Category
Parameters
Elasticity
= 20000
= 0.2
Plasticity
= 30
= 34.5
= 2.9
Steel: Bilinear isotropic hardening, BIH model using Von Misses type of yield criterion is used for modeling reinforcing steel material. The steel in FEM is assumed to be a bilinear
elastic-plastic material and identical intension and compression.
TABLE II-4 STEEL REBAR PROPERTIES USED FOR BIH MODEL
Type
Diameter Ø (mm)
Yield Strength
(MPa)
Elastic Modulus
(GPa)
Tangent Modulus
(MPa)
Poissons Ratio,
Reinf.
10
460
200
500
0.3
Stirrup
6
400
200
500
0.3
CFRP is simulated as elastic-orthotropic material. An elastic behavior is assumed for CFRPs. This means up to a maximum
stress level, the CFRPs have linear elastic behavior and then with zero bearing stress.
TABLE II-5 FRP UNIDIRECTIONAL-SHEET 240/600 (FRP SYSTEM – REV. TECH. SH. FS01/02/15)
p>FRP Elastic Modulus (MPa)
Poissons Ratio
Tensile Strength (MPa)
Shear Modulus (MPa)
Sheet Thickness (mm)
= 240000
= 0.1
= 14000
CFRP
= 16000
= 0.1
3800
= 14000
0.334
= 16000
= 0.1
= 14000
-
Meshing and Boundary Conditions
The model is divided into a number of small elements and the required values are calculated at integration points of these small elements. To get good result the use of rectangular mesh was used. In ANSYS selection of mesh density is very important and fine mesh is recommended, particularly at probable damage-prone regions. But to obtained mesh-
independent results, the mesh size needs to be less than the half of square root of the nonlocal parameter, c. Displacement boundary conditions are needed to constraint the model to get a unique solution for each FEA model.
-
Type of Finite Element Analysis
Newton-Raphson equilibrium iteration was used to solve this nonlinear problem in ANSYS software of incremental load analysis. In order to predict the nonlinear behavior, the load applied to a FEM was subdivided into a series of load increments which can be applied over several load steps. Before each solution, the Newton-Raphson method evaluates the out-of-balance load vector. The program then performs a linear solution, using the out-of-balance loads, and checks for convergence. If convergence criteria are not satisfied, the out- of-balance load vector is reevaluated, the stiffness matrix is updated, and a new solution is obtained. This iterative procedure continues until the problem converges.
-
-
RESULTS AND DISCUSSIONS
-
Validation of Finite Element Analysis
In verification section, to demonstrate the validity of the implemented FEA, the specimen was first simulated and then the obtained crack pattern of numerical result is comparatively presented with the experimental result. The comparison of crack of FEA simulation and experimental test result of the Pham et al. (2017) specimen is shown in Figure III-1. The propagation of cracks observed in the experimental study is comparatively presented with results obtained from this FEA numerical study. There is relatively good agreement between these two figures of crack.
(a) FEA model result
(b) Experimental test result
Figure III-1 Comparison of experimental and FEA crack patterns of specimen bottom surface
Parametric Study
-
Load Displacement Curve
The area under load – displacement curves are used to confirm RC slabs ductility. The most area of the curve indicates that the best in ductility the slab. It can be observed that the ductility of strengthened reinforced concrete slab is enhanced when strengthening CFRP sheet layer number increases. Using the area of load – displacement cure the ductility of RC slab is summarized as follows:
-
Sheet layer number is significant effect in enhancing the ductility of the slab (Figure III-2, a
&b)
-
The ductility of RC slab reduced with an increase in sheet spacing (Figure III-2, c)
-
Fiber orientation of 450 is effective in enhancing ductility than 00 and 900 fiber orientations (Figure III-2 d)
Load, KN
Load, KN
(a) Effect of sheet number
(b) Effect of sheet width
100
80
60
40
20
0
S-1
S-2
S-3
Control
0 100 200 300 400
Displacement, mm
100
80
60
40
20
0
Control S-3
S-5
S-6
0 100 200 300 400
Displacement, mm
Load, KN
Load, KN
(c) Effect of Sheet width
(d) Effect of Fiber Orientations
80
70
60
50
40
30 S-6
20 S-7
S-8
10
0
0 100 200 300 400
Displacement, mm
90
80
70
60
50
40
Control
30 S-9
20 S-10
10 S-11
0
0 100 200 300 400
Displacement, mm
Figure III-2 Effect of CFRP sheet on ductility of RC slab
-
-
Concrete Crack Pattern
In order to assess the effect of parametric variables of study in enhancing the ductility of CFRP sheet strengthened RC slab, FEA simulations were conducted. The ductility of the slab is expressed in terms of concrete crack pattern and it is plotted with color regions. Those color show the magnitude and distribution of scalar isotropic damage variable defined in CDP micro-plane model. By observing the color range of regions with blue, yellow and red colors, A specimen having maximum of blue color regions behaves more ductile behavior.
Effect of CFRP Sheet Layer Number: Three RC slab with sheet number, SN of 1, 2 & 3 were analyzed. From Figure III-3, compare the area of regions with blue, yellow and red colors, it can be seen that specimen strengthened with SN = 3 in comparison to un-strengthened, strengthened with SN = 1 and 2 is more ductile. Therefore, strengthening CFRP sheet layer number significantly enhanced the ductility of slab.
(a) Control Unstrengthen Specimen
(b) S-1 (SN = 1)
(c) S-2 (SN = 2)
(d) S-3 (SN = 3)
Figure III-3 Plot of damage distribution in failure state with sheet number
Effect of CFRP Sheet Width: Three CFRP sheet strengthened RC slab specimens with sheet width, SW of 100, 300 & 500mm were analyzed. From Figure III-4, it is observed that strengthening CFRP sheet width enhanced the ductility of
slab., it can be seen that specimen strengthened with sheet width of 500mm in comparison to un-strengthened, strengthened with sheet width of 100 and 300mm more ductile but the change is invisible between 300 and 500mm of width.
(a) Control specimen
(b) S 3 (SW = 100mm)
(c) S – 4 (SW = 300mm)
(d) S – 5 (SW = 500mm)
Figure III-4 Plot of damage distribution in failure state with sheet width
Effect of CFRP Sheet Spacing: To assess the effect of sheet spacing on ductility of RC slab, three CFRP sheet strengthened RC slab with sheet spacing of 100, 200 & 300mm were analyzed. From Figure III-5, it is observed that strengthening
CFRP sheet enhanced the ductility of the RC slab but its effect is reduced due to increasing sheet spacing and the change is insignificant.
(a) Control Unstrengthen Specimen
(b) S-8 (SS = 300mm)
(c) S-7 (SS = 200mm)
(d) S-6 (SS = 100mm)
Figure III-5 Plot of damage distribution in failure state with sheet spacing.
Effect of CFRP sheet Composite Fiber Orientation: Three CFRP sheet strengthened RC slab specimens with fiber orientation of 00, 450 & 900 were analyzed. From Figure III-6, it is observed that strengthening CFRP sheet enhanced the ductility of the RC slab. By assessing the effect of fiber
orientation on ductility of RC slab, it is observed that slab specimen strengthened with fiber orientation of 450 in comparison to specimen strengthened with fiber orientation of 00 and 900 is more ductile.
table cellspacing=”0″>
(a) Control specimen
(b) S-11 (FO = 900 900)
(c) S-9 (FO = 00 00)
(d) S-10 (FO = 450 450)
Figure III-6 Plot of damage distribution in failure state with sheet fiber orientation.
-
-
-
CONCLUSIONS
The finite element analysis used in the present work is able to simulate the behavior of reinforced concrete RC slab. Results obtained from the presented ANSYS FEA modeling technique was verified using experimental result from literature. The accuracy of proposed modeling procedure was confirmed in terms of concrete crack. This showed good agreement with experimental test results. The use of CFRP
sheets as external strengthening mechanism to enhance ductility of RC slab. In parametric study the effects of sheet layer number, sheet width, sheet spacing and fiber orientation of sheet composite in RC slab were discussed. Finally, based on the limited study in this research work, the following conclusions can be drawn from finite element analysis results:
-
Externally strengthening CFRP sheets to tension faces are effective method in enhancing ductility of RC slab.
-
The increased in pre-crack and post- crack stiffness of external beam missing RC slab, due to CFRP sheet ranges from 6.7 to 21.1% and 36.1 to 92.3% respectively.
-
CFRP sheet layer number and sheet width have significant effect on enhancing ductility of RC slab.
-
CFRP sheet spacing has slight decreasing effect on ductility of RC slab.
-
The effect of CFRP sheet fiber orientation on ductility of RC fiber orientation, FO 450 has more effective than FO 00 and 900
ACKNOWLEDGEMENT
The authors gratefully acknowledge every support from Assosa University.
REFERENCES
[1] AIELLO, M. A., ASCIONE, L., BARATTA, A., BASTIANINI, F., BATTISTA, U., BENEDETTI, A., BERARDI, V. P., BILOTTA, A.,BORRI, A. & BRICCOLI, B. 2014. Guide for the design and construction of externally bonded FRP systems for strengthening existing structures.
[2] AL-GHAZAWI, O. & AL-ROUSAN, R. Z. 2020. Response ofReinforced Concrete Slabs Strengthened with CFRP. Journal of Engineering Science & Technology Review, 13.
[3] EMARAH, D. A. 2019. Numerical study to investigate the behavior of reinforced concrete slabs with CFRP sheets. Water Science, 33, 142- 153. [4] FATHELBAB, F. A., RAMADAN, M. S. & AL-TANTAWY, A.2014. Strengthening of RC bridge slabs using CFRP sheets. Alexandria Engineering Journal, 53, 843-854.
[5] FENG, P., QIANG, H., OU, X., QIN, W. & YANG, J. 2018.Progressive Collapse Resistance of GFRP-Strengthened RC Beam Slab Subassemblages in a Corner ColumnRemoval Scenario. Journal of Composites for Construction, 23, 04018076.
[6] LIM, N. S. 2017. Systematic study on reinforced concrete structures under progressive collapse. [7] MUTLAQ, S. A., RASHEED, L. S. & AL-KHAFAJI, A. G. A.Performance enhancement of damaged two way concrete slabs. IOP Conference Series: Materials Science and Engineering, 2020. IOP Publishing, 022156.
[8] PHAM, A. T., LIM, N. S. & TAN, K. H. 2017. Investigations of tensile membrane action in beam-slab systems under progressive collapse subject to different loading configurations and boundary conditions. Engineering Structures, 150, 520-536. [9] TENG, X. & ZHANG, Y. 2017. Structural behavior FRP-strengthened steel-reinforced concrete slabs under moving-wheel cyclic loads. Australian Journal of Structural Engineering, 18, 86-94.