
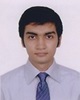
- Open Access
- Authors : Jasem A. Ahmed , Muhammad A. Wahab
- Paper ID : IJERTV10IS120097
- Volume & Issue : Volume 10, Issue 12 (December 2021)
- Published (First Online): 20-12-2021
- ISSN (Online) : 2278-0181
- Publisher Name : IJERT
- License:
This work is licensed under a Creative Commons Attribution 4.0 International License
Multiscale Modeling on the Creep Analysis of Functionally Graded Cylinders under Mechanical and Thermal Loads
Jasem A. Ahmed
Ex-Graduate Student, Department of Mechanical & Industrial Engineering, Louisiana State University and Agricultural & Mechanical College, Engine-ering Lane, 3261 Patrick F. Taylor Hall, Baton Rouge,
LA 70803, USA.
Muhammad A. Wahab
Department of Mechanical & Industrial Engineering, Louisiana State University and Agricultural & Mechanical College, Engineering Lane, 3261 Patrick F. Taylor Hall, Baton Rouge, LA 70803, USA.
Abstract This study attempts to develop a multiscale model to investigate the time-dependent creep behavior of functionally graded cylinders. With Finite Element (FE) simulations the position-dependent parameters associated with creep constitutive law at the microscale are evaluated. A non-linear boundary value problem is solved to determine the time-varying creep stresses and strains using a macroscopic FE model. The proposed work can predict the creep response of functionally graded pressure vessels based on the constitutive behavior of the creeping matrix (Aluminum with SiC (silicon carbide) inclusions), and volume fraction profiles. Three different micromechanical models have been used and the homogenized creep responses have been evaluated and its effect on the macroscopic behavior have been compared. It has been found that for large 3D-finite element models the computational expenses are enormous and the study shows that the simple 2D-axisymmetric model can closely capture the creep behavior of such multiscale methods. It has been found that the radial variations of constituent volume fractions have significant effects on stress distributions and creep strain histories. The models are useful to investigate materials combinations and heterogeneity profiles. The creep strain can be controlled by adjusting the volume fraction profiles.
Keywords Functionally-Graded-Materials (FGM); thick-walled cylinders; primary and secondary creep; creep stress and strain; multiscale modeling; Time-dependent creep analysis, Metal matrix composites.
-
INTRODUCTION
Aerospace and energy production applications require components to withstand high temperature and demonstrate high strength at the same time. This can be achieved by designing advanced composites by utilizing special characteristics of different materials e.g., combining high strength of metals with high temperature resistance of ceramics. Coating of ceramic layers onto a metal surface leads high stress concentration due to abrupt transition of material properties at the interface, resulting in failure of the coating by cracking, spalling, delamination etc. To mitigate these damages, materials with smooth spatial gradient in properties, known as Functionally-Graded-Materials (FGM) were developed in the 1980s by Japanese scientists working on thermal shock in space shuttles.
Hollow cylinders are widely used in engineering applications, often exposed to high stress levels at elevated temperatures. Under these conditions, creep deformations are significant and dictate the useful life of the structures. There is strong need for time-dependent analyses for predicting the performance and lifetime of the cylindrical structures. Experimental creep evaluation of composite materials is time-consuming and expensive, therefore, computational techniques become useful in predicting and assessing service life of structures. Although research is being done in analyzing thermoelastic behaviors, and on the steady-state creep response of FGM thick-walled cylinders, time-dependent creep analysis under various boundary conditions remains an active area of interest. Solving creep constitutive equations for FGMs is complicated, and for this reason, development of analytical and numerical methods for analyzing creep behavior is of utmost importance. It is typical in analytical and semi- analytical methods to make restrictive assumptions for material variation to simplify solutions. The analytical studies are applicable to limited cases only and cannot be used directly for quantitative evaluation in design and decision making. This limitation can be overcome by moving towards advanced multiscale methods by unifying the creep behavior of FGMs at the microstructural level to the stress-strain response at the macroscale.
This study presents a multiscale framework to predict and implement local creep behavior of the FGM of the macro body to obtain numerical solutions for FGM cylinders. This research is expected to significantly extend the current ability to incorporate creep deformations into the design of FG- thick cylinders, which are potential structural components operating under severe conditions. The models are beneficial to investigate the choice of material combinations and heterogeneity profiles, thereby reducing cost of materials, fabrication, and testing associated with experimental trials.
-
GENERAL OVERVIEW OF FUNCTIONALLY- GRADED- MATERIALS
2.1 Functionally Graded Materials
FGMs are advanced composite materials of two or more constituents, tailored to exhibit a smooth variation of composition or microstructure with location. Advances in manufacturing techniques have allowed material ingredients to be combined and its
composition engineered in ways to make the best use of properties unique to each constituent. This means that design engineers have a wider choice of potential materials to meet functional requirements of applications, specifically under severe environments. FGMs take their motivation from natural structures such as bamboo, bone etc. The gradual property variation is formed by varying chemical composition, microstructure etc. with location. Thus, components can be manufactured for applications where different properties are desired at different surfaces, e.g., a metal-rich side can be used in regions where superior mechanical properties are required, while a ceramic-rich side can be used to withstand high temperatures. The gradient can be built up continuously or in stepwise formation, followed by a consolidation process (drying, sintering or solidification). It is possible to optimize the material composition profile to extract maximum benefit of the inhomogeneity by minimizing stress-strain levels in a structure developed during both its processing and service life under extreme temperatures.
-
POTENTIAL APPLICATIONS OF FUNCTIONALLY GRADED MATERIALS
FGMs can effectively reduce thermal mismatch between neighboring materials and can be used to manufacture components for applications where specific properties are favored at different surfaces. They have wide scope of applications in joining dissimilar materials such as ceramics to super alloys for thermal barrier coatings (TBC), gas turbines, turbochargers etc. Plasma divertor designs of the International Thermonuclear Experimental Reactors (ITER) employ tungsten-copper alloy FG components to face high heat flux and efficiently transfer heat to a cooling base. The gradation alleviates high thermal stresses arising due to material property mismatch and reduces temperature of the cooling base to prevent thermal softening. Metal-Matrix-Composites (MMC) have been considered to fabricate pressure vessels and propellant tanks, providing strength against tensile loading at high pressures, and compressive loading without buckling. These multifunctional vessels can potentially reduce the overall weight, and improve efficiencies for propulsions technologies in aerospace, military, and commercial systems.
Hollow cylinders are one the major structural omponents in many engineering applications. Examples are pressure vessels for aerospace vehicles or shuttles used in reentry to earths atmosphere, nuclear reactors, military applications, and storage and transmission of pressurized chemical and fluids, boilers etc. In many cases, they are required to withstand high temperature environments for sustained period of thermal loads causing significant creep damage which may trigger catastrophic failures. For extreme conditions, structures could be designed FGMs to alleviate damaging effects. A gradual property variation is usually formed by varying chemical compositions, mechanical properties, and microstructures, etc. with location.
Fig. 1: Creep curve – strain with time
FGMs can effectively reduce thermal mismatch between neighboring materials and can be used to manufacture components for applications where specific properties are favored at different surfaces to mitigate detrimental effects of severe environments. Temperature and stress solutions of engineering structures are of fundamental importance from a design point of view, as well as in-service fitness assessment. Creep accumulation is a leading cause of crack initiation in components working at high temperatures. Evaluation of creep stresses and strains is essential in design, and as well as fitness analysis of aging structures. Successful implementation of the FGM technology into pressure vessel components necessitates the need for a comprehensive study for structural response. This is relatively new area of research and so far, experimental efforts have been quite limited, and needs innovative thinking, critical analysis, assessment of the materials properties, and design loads understanding.
-
Creep damage in materials
Creep is an important material behavior occurring at elevated temperatures, especially at that higher than 50% of the melting temperature of the material. It is the time-dependent, inelastic deformation taking place when the material is subjected to a load over time. A structure undergoes changes in state of stress and strains, reduction in material strength etc. The deformation is commonly characterized in the form of strain versus time data, known as the creep curve (Fig. 1). There are three regions in the creep curve: (i) primary, (ii) secondary), and (iii) tertiary regions. The primary creep stage is characterized by an initial high creep rate which decreases with time. Eventually a secondary stage is attained at which significant deformation takes place at a constant rate. At the tertiary stage, the creep rate begins to increase leading to rupture due to necking and formation of cavities. Figure- 1 highlights the three regions in a typical creep curve. Primary creep occurs in a short interval of time, and cylinders are mostly subject to secondary creep effects during their useful lifetime. Tertiary creep is usually not considered because it indicates imminent failure.
-
Multiscale analysis of functionally graded structures
FGMs allow spatial customization of material properties in order to derive maximum benefits from constituents with wide variation in properties. Several analytical and semi-analytical solutions FG cylinders have been developed based on restrictive assumptions. A widely used assumption is the usage of separate power-law formulae for thermal, elastic, and creep properties. Correlation between the properties exist, and it becomes impractical to restrict these using such profiles. Current computers are incapable of handling calculations for detailed finite element models generated with microstructural inhomogeneity inside the macroscopic structure. Multiscale numerical techniques become extremely useful to predict the macroscopic behavior of FG
structures, as these can be used to first, evaluate location-dependent properties based on compositions. With limited FGM experimental progress, numerical models provide a driving force in comprehension the fundamentals in the field.
To date, multiscale creep analysis of FGMs have not been investigated fully. A method is proposed in this study is well-suited for analyzing creep behavior of FG cylinders. An objective of this research is to develop a framework for generating two phase unit-cells to estimate creep properties over a range of volume fractions, and thereby using the information to predict the macroscopic time-dependent behavior of FG thick-walled cylinders. Optimization schemes are employed to determine the best spatial variation of material properties that would minimize creep deformation while taking stress constraints into considerations. Metal-Matrix-Composites (MMCs) are widely used as structural components in engineering applications. Titanium-silicon carbide composite pressure vessels and propellant tanks have been designed for spacecraft and satellite applications to attain burst- pressures of more than four times the expected operating pressure [1]. Advances in manufacturing techniques have allowed composition of MMCs to be engineered in ways to make the best use of the properties unique to each constituent. Silicon Carbide (SiC) reinforced Aluminum (Al) composites have been widely considered especially in the aerospace industry due to its low cost, mass production, formability using conventional processes, superior mechanical properties, and retention at high temperatures compared to Aluminum alloys. Al-SiC composites are also frequently considered in the potential high-temperature applications of Functionally Graded (FG)- thick-walled cylinders, and discs. Mathematical solutions of temperature and thermo-mechanical stresses in FGM cylinders have been studied over the last decades. In an extensive review paper, Dai et al. [2] put together research articles published on the coupled-mechanics of FG- cylindrical structures from 2005 to 2015. Owing to the complexities associated with the creep governing equations, analytical solutions are difficult to obtain; and most creep studies have concentrated on semi- analytical solutions for steady-state creep problems [3-9]. Some articles [10-17] are dedicated to time-dependent creep deformations in FGM cylinders. These studies are restricted to the usage of Nortons creep law and assumption of independent power-function profiles for the creep coefficient, and other material properties. Material properties have correlation to the local composition and are not restricted to such profiles. Multiscale techniques employed effective property models, or combined macroscopic-microscopic models such as: asymptotic methods, or nested boundary value homogenization problems [18]. The effective property models can use homogenization techniques of particle-reinforced composites for the determination of material
properties and have been employed in several engineering applications [19-20].
Evaluation of microstructural materials properties have significant interest for the development of MMCs. Behavior of composites have been commonly estimated using Rules of Mixture (Voigt and Reuss estimates), mean-field mechanics (Mori- Tanaka [21], Eshelby, self-consistent scheme [22] etc.), theoretical bounding methods (Hashin-Shtrikman lower and upper bounds [23]), and computational simulations (finite or boundary element methods). Rules of mixture are mathematically simple, and are widely used to determine physical properties such as: Youngs modulus, Poissons ratio, thermal conductivity, coefficient of thermal expansion, density, and specific heat, etc.
Idealized microstructures, known as the Representative-Volume-Elements (RVE) are commonly modeled by two methods: (i). The first one is a single inclusion unit-cell model, which is the smallest repeatable geometry in the RVE. To reduce computational expenses, it may be further simplified into two- dimensional axisymmetric problems. (ii). The second approach is by generating a larger domain – the Statistically- Representative- Volume- Element (SRVE), which includes sufficient microstructural features into the domain and captures the radom arrangement of heterogeneities. Generation of an RVE requires prior determination of spatial arrangement of particles. The modified Random Sequential Adsorption (RSA) algorithm [24-26] is commonly used to generate random, non-overlapping particles, and can include the effect of non-uniform spatial distribution of inclusions.
Aluminum composites have been studied by only a few authors [27-30]. These models do not include the influence of local stress concentrations due to spatial distribution of inclusions in the microstructure and assume that all reinforcements deform simultaneously. As creep deformations are highly sensitive to stress levels, the spatial distributions have a large influence on the overall creep response, although the effect may be small for effective physical properties. 3D-morphologies with random multi- inclusions are expected to give more accurate predictions than the single-inclusion models. While most models developed to predict the creep behavior of MMCs used the single inclusion unit-cell model, but the RSA algorithm motivated researchers [31- 36] to model multi-particle RVEs. A few articles [37-40] also aimed to study the effects of interfaces on material creep behavior. Multiscale methods can address the spatial variation of FGMs [41-42]. The model has been successfully implemented to study the time-histories of creep strains and stress distributions of FG- thick-cylinder using different micromechanical models.
Finally, parametric studies are performed to study the effects of material distribution, maximum volume fraction, and cylinder thickness on the creep response.
-
-
MULTISCALE CREEP ANALYSIS OF FGM CYLINDERS
The creep response of FG cylinders has been an area of interest to the solid mechanics community. The behavior of such structures depends on the underlying simplifications and assumptions. In the last decades, developments have been limited to ideal cases, but not linked to the study of multiscale models required to design high performance pressure vessels for extreme environments. The studies have been successful in representing the idealized macroscopic behavior but are not consistent with the microstructure of FGMs. To bridge the gap between the micro and macro levels a practical
model for the creep behavior of FG cylindrical vessels has been developed. In this chapter, modeling steps and techniques of the proposed multiscale creep analysis of an FG thick- walled cylinder has been described.
-
Typical analysis at the microscale
Consider a FGM composed of two distinct constituents: metal and ceramic. As precise morphological information is not available, the effective properties of the composite can be determined based on properties of the constituents and the volume fraction. At the micro level, the structure is assumed to be composed of spherical ceramic particles of several microns in diameter dispersed within a metal matrix (Fig.2). To account for the functional gradation, the spacing between the particles is gradually changed from one surface to the other.
Fig. 2: Schematic of two phase FGM [43]
Computation of creep properties at the microscale in terms of constituent volume fractions is the first step in understanding the macroscopic response. The method allows to generate ideal microstructures of either periodic (regularly arranged), or random materials accounting for particle interactions to be used for homogenization. Single or multi-particle unit- cells much smaller than the characteristic size of the macroscopic structure are generated and the effective elastic and creep properties are obtained. Three different models have been used at the micro-level: (i) 2D single-inclusion unit-cell, (ii) 3D single- inclusion unit-cell, and (iii) 3D SRVE. Each model employs FEM to compute creep properties for different local compositions to generate a material model. To automate the entire procedure, the models are prepared using scripts developed in MATLAB [44]. The volume fraction Vf of each single-inclusion model is related to the particle radius r and unit-cell length. L using:
2D axisymmetric unit-cell:
= 2
3
3
3
3
33
(1)
3D single-particle unit-cell:
= . (2)
63
For the 3D SRVE model, coordinates of centers, and radii of randomly arranged spheres required to meet a required volume fraction are first generated using modified RSA algorithm.
-
Modified-random sequential adsorption algorithm (RSA)
The modified RSA algorithm can simulate an RVE with a given volume fraction Vf by generating a population of reinforcement particles. Spheres are sequentially added to a cube of length L, not allowing intersection with each other. With identical spheres (monodisperse), a jamming limit exists, and it is not possible to generate volume fractions more than 30%. However, spheres of decreasing sizes can be sequentially added to reach values higher values, up to 60% [45]. Flowchart of the RSA algorithm is given in [46].
Start
Generate random center and radius
Start
Generate random center and radius
Firstly, radii of all incoming particle that satisfies the volume fraction requirement are generated according to desired statistical distribution and arranged in descending manner.
Generate symmetry particles
Generate symmetry particles
YES
YES
Intersects boundary
NO
Intersects boundary
NO
Particle centers are produced using a random number generator and accepted if the distances between its center and previously accepted particles exceed a minimum value of 1.05 (Ri +Rj), where Ri is the radius of the candidate particle, and Rj is the radius of j-th accepted particle. To maintain periodicity, any particle cutting a face of the unit cell is copied to allowed reappear from the opposite face.
Accept particle(s) and update
Accept particle(s) and update
Delete
Delete
YES
YES
Intersect others?
NO
Intersect others?
NO
The particles are also checked to maintain a minimum distance (one-tenth of particle radius) from the cell face and between each other in order to generate an adequate finite element mesh. A particle very close to the RVE surface, edge or corner could result in distorted finite elements.
Target reached?
NO
Target reached?
NO
YES
Stop
YES
Stop
Fig. 3: Flowchart of the modified-RSA algorithm [46]
-
Simulation of creep curves
Once the unit-cell and particle specifications have been generated, an input file readable by ANSYS MAPDL [47] is written and imported to form a cube with spherical inclusions. Elastic and creep material properties are assigned to the matrix and inclusions. The combined time-hardening constitutive equation delivers a good model for the primary and secondary stages of creep. It is described by a total of 7 parameters. The constitutive equation is given in the ANSYS documentation as creep strain
as a function of time , stress , and temperature T:
4
23+1
7
= 1 + 56 , (3)
3+1
where C1 through C7 are the material creep parameters used to fit experimental data, and various values of the constants C1 through C7 are evaluated and explained in great detail in [46,48]. The constants C4 and C7 can be assumed to be zero as temperature dependence is not considered. In a single-inclusion unit-cells, only a quarter (for 2D) or one-eighth (for 3D) of the particle-matrix system is modeled as result of symmetry. The inclusion and matrix regions are meshed using 8-noded 2D quadrilateral elements
(Element type: PLANE-183) for the 2D axisymmetric model, or 10-noded 3D tetrahedral elements (Element type: SOLID-187) of the 3D unit-cell or 3D SRVE models. Elements at the matrix-inclusion interfaces matrix are further refined.
-
Boundary conditions
Te orthogonal mixed-boundary condition (OMBC) is imposed on the micromodels. Symmetry boundary condition are applied to the inner surfaces, and iso-displacement boundary conditions are imposed on the outer. An iso-displacement condition is applied a face by coupling normal displacements of all nodes on it. A uniaxial tensile load is applied in the -direction to simulate creep behavior of the RVE. Figure- 4 illustrates the three-different unit-cell models considered in this study.
The models are implemented using ANSYS Mechanical APDL R16.0-17.2. Owing to the large number of degrees-of-freedom to be solved, High Performance Computer (HPC) Philip at Louisiana State University is used. A node of the supercomputing cluster has two 4-core 2.93 GHz Quad Core Nehalem Xeon 64-bit processors with 24 GB 1333 MHz RAM.
Fig. 4: Mesh and boundary conditions for (a) 2D unit-cell, (b) 3D unit-cell, and (c) 3D SRVE. (Figures have different scales)
Using volume averaging over total elements N, the effective creep strain at current time for a prescribed volume fraction and load is determined by:
= 1
() (), (4)
and the total unit-cell volume is given by:
=1
=
=
=1
(). (5)
-
Estimation of creep properties
A microscale FE creep analysis is performed for different macroscopic loads. For random microstructures, the homogenized behavior depends on the size of the RVE. The RVE size should be significantly larger than the particle radius "" to contain sufficient microstructural features. With increasing size of the RVE, the effective properties tend to become independent of the applied boundary conditions. To study the existence of RVE, a statistical analysis based on mathematical expectation and standard deviation is performed using a series of samples with (i) increasing RVE size, and (ii) multiple realizations i.e., samples from different inclusion locations with the same particle volume fraction. For the SRVE model, numerical averaging is performed over several samples to reduce computational resource requirements. The process is repeated for different tensile load values, and the creep curves obtained are fitted to the parent creep constitutive equation to estimate the creep parameters 1 through 7. The operation is now performed for successively higher volume fractions until creep parameters for the entire range are evaluated. The ability to estimate the creep parameters over a range of volume fractions forms the basis of the multiscale framework. The operation is then performed for successively higher volume fractions until creep parameters for the entire range are evaluated. To establish the accuracy of homogenized material behavior, it is important to check convergence characteristics of finite element solutions. The convergence of numerical results is investigated by successive refinement of mesh density, time-increments each time halving the corresponding values. The ability to estimate the creep parameters over a range of volume fractions forms the basis of the multiscale framework.
-
Analysis at the macroscale
Considering radial symmetry, an axisymmetric domain of the hollow cylinder is modeled in ANSYS MAPDL [47] to reduce computational costs. The dimensions, and loadings, mesh and boundary conditions are shown in Fig.. The cylinder has inner and outer radii and respectively and is exposed to an internal pressure , external pressure , angular speed , and a heat-flux of at the outer wall. The inner wall is held reference temperature of zero. The thermoelastic problem is at first decoupled, and the thermal portion solved to input the temperature solution into the mechanical problem. The user programmable feature USERMATTH is used for the implement the functional gradation. This is done by defining a field variable (local volume fraction of constituent- 2) at several design points in the radial direction.
A volume fraction profile is implemented to the model by assigning the local volume fraction to each node as an initial state value. Spatial variations of material properties are frequently calculated using simple homogenization schemes by assuming constituent volume fractions in the form of power-law, polynomial, exponential and sigmoidal functions. In this study, a power- function profile is used to smoothly vary the volume fraction of constituent 2 in the radial direction:
DOF UY = 0
Axis of symmetry Pressure
Inner radius
Outer radius
Fig. 5: Finite Element model for macroscale
Power function profile:
2 = + ( ) ( ) ,
(6)
where and are the volume fractions at the inner ( = ) and outer ( = ) surfaces respectively, and is the gradation parameter controlling the shape of the profile. At intermediate volume fraction values, the material properties are automatically
calculated by linear interpolation. Initial elastic stress-strain analysis at the macroscopic level is followed by time dependent creep analysis.
-
Methodology
A numerical procedure is presented to determine the optimal material distribution of a functionally graded cylinder undergoing creep deformations. The procedure uses graded finite elements in determining the creep solution and avoids the disadvantage of discretizing the domain into numerous homogeneous layers. Otherwise, the number of design points would be vastly increased, and making the optimization problem difficult to solve. The parallel implementation drastically reduces the total time for completion of the algorithm.
A multiscale approach based on the finite element method is developed to link the microscopic and macroscopic scales to predict the creep behavior of FG pressure vessels. The model is implemented sequentially:
Step 1 characterizes the FG composite by determining the homogenized creep behavior as a function of volume fraction. Finite element models of particle-reinforced composite samples are first constructed to compute their homogenized creep behavior. Creep parameters are estimated by curve-fitting the data obtained from the finite element study to a material model.
Step 2 links the estimated parameters to an axisymmetric finite element model at the macroscale. Functional gradation is defined by assigning the volume fraction as a field-variable to each node. Homogenized material properties are interpolated at the integration points in the elastic and creep computations to determine the time-dependent response of a pressurized FG thick- walled cylinder. The step is computationally efficient because there is no need to model detailed microstructure or solve an entire RVE at each integration point. A schematic representation of the multiscale framework is illustrated in Fig. 6.
-
-
NUMERICAL RESULTS FROM MULTISCALE CREEP ANALYSIS OF FGM CYLINDERS
-
Numerical Results
This section presents a limited collection of important numerical results and observations resulting from the studies. Effects of important material gradient indices are investigated and discussed. Qualitative insights into the creep behavior of FG cylinders, and numerical benchmark data for qualification of numerical solutions are established. Some useful and relevant results from creep analysis can be found in Ref. [46, 48].
Functionally graded hollow- cylinder
Field variable assigned over domain
Functionally graded hollow- cylinder
Field variable assigned over domain
PLANE183
element
Axisymmetric model
PLANE183
element
Axisymmetric model
Volume fraction
Volume fraction
Interpolated Elastic properties E, and Creep parameters C1 to C7
Evaluate elastic properties:
Interpolated Elastic properties E, and Creep parameters C1 to C7
Evauate elastic properties:
Creep parameters for different volume fractions
Evaluate creep properties: FE based
Creep parameters for different volume fractions
Evaluate creep properties: FE based
(a) 2D
(a) 2D
(b) 3D
(c) 3D SRVE
(b) 3D
(c) 3D SRVE
Creep-curve fitting to evaluate parameters
Creep-curve fitting to evaluate parameters
Homogenized creep curve at different stress levels
Homogenized creep curve at different stress levels
Fig. 6: Schematic representation of the multiscale framework
-
Thermoelastic solutions
Thermoelastic and time-dependent creep response of the cylinder having inner radius = 0.5 m and outer radius = 0.75 m have been investigated. Material properties used are 0 = 200 GPa, = 0.3, 0 = 1.2 × 105 K1, and 0 = 7800 kg/m3. Creep data are assumed to be = 3.75, and 0 = 1 × 1011MPap. Gradient indices are varied from 2 to +2 to illustrate the influence of material property distributions on thermoelastic and creep stress-strain behaviors. A positive index value
represents that the physical property at the outer surface is higher than that of the value at the inner surface (with a non-linear radial distribution according to the power-law), and a negative value indicates lower property value.
The formulation includes solutions for combined mechanical and thermal loadings. Typically, studies have performed illustrative examples by taking equal functional grading exponents e.g., 1 = 2 = 3 = 4 = 5 = . Controlling all material distributions using a single parameter fails to demonstrate how responses are influenced by individual material gradations, which becomes a primary motivation in materials selection and tailoring of FG structures. Parametric studies are thus performed by varying each index form 2 to +2, while keeping the others constant at 1. Plots become more revealing when parametric studies are separately performed for applied pressures, rotation, and heat generation in convective environments only. Firstly, stress distributions along the cylinder wall thickness at zero time are calculated; creep strain components are zero.
Figure- 7 shows the effect of Youngs modulus distribution on the stress components due to internal pressure only ( = 50 MPa). For all values of 1, radial stresses are 50 MPa at = , and zero at = , ensuring that mechanical boundary conditions have been satisfied. Hoop and axial stress distributions are tensile due to the application of internal pressure, and with the increase of index 1, hoop and axial stress values at the inner surfaces decrease, and magnitudes at the outer surface increase. Von Mises stress distribution gives an effective representation of the influence of material property inhomogeneity on stress states and will be considered for the latter case illustrations. In this case, von Mises stress takes a homogenized profile throughout the cylinder for 1 = 2. Thus, Youngs modulus variation along the cylinder has significant effect on stress distributions, and an appropriate gradation can be used to attain optimal stresses profiles.
(a) Radial
(b) Circumferential
(c) Axial
(d) von Mises Stress
Fig. 7: Effect of 1 on (a) radial, (b) circumferential, (c) axial, and (d) von Mises stress distributions along the cylinder thickness for pressure loading only ( = 50 MPa)
-
Creep behavior
Evolution of circumferential stress and strain at the inner and outer surfaces are plotted in Figure 8. Strain rate initially decreases and reaches a constant value with time. Strain rate at the inner surface is higher than that at the outer. During the initial period, there is significant increase in circumferential stress at the inner surface, and the value then decays to a steady-state value. The converse holds true at the outer surface. Good agreement is observed between iteratively calculated stress/strain histories and that obtained from FEA using ANSYS MAPDL R16.0 [47], demonstrating accuracy of iterative solutions. It is to be noticed that during the initial redistributions, the cylinder experiences peak stress values much higher than initial or steady state levels which would not be revealed in a steady-state creep analysis. Thus, time-dependent analyses are vital of design of FG thick cylinders.
-
Results of homogenized creep properties from different micro models
The homogenized creep properties are presented for a range of volume fractions using different micromechanical models. Silicon carbide particle reinforced aluminum composite is considered for the FGM. This material combination is chosen since it is widely considered for high temperature applications. SiC typically does not undergo noticeable deformation with time compared to Al. As a result, it can be modeled as a non-creeping, elastic material. As for Aluminum, the combined time-hardening creep constitutive model incorporates primary and secondary deformation stages. The material properties of Al and SiC are tabulated in
Table -1. The creep parameters have been reported by Lee, et al. [49] by fitting experimental data of Al-1.5Mg obtained from work of Krajewski, et al. [50]. A more detailed work with analysis and explanations of approximations have been reported in Ref. [46].
Solid lines Iterative solution
o FEA using ANSYS MAPDL
Solid lines Iterative solution
o FEA using ANSYS MAPDL
Fig. 8: Evolution of circumferential (a) stress, and (b) strain at = and = for 10 h.
Table -1: Elastic and creep properties of Al-6061 and SiC
Material
(GPa)
1
2
3
5
6
Al
68.3
0.345
2.07e-7
0.5
-0.55
1e-22
7.6
SiC
470
0.17
–
–
–
–
–
For a given volume fraction, creep strain versus time curves is obtained for different load values. A commercial package, ANSYS Mechanical APDL R16.0 is used to solve and post-process the creep results for the FEM. To model the particles and matrix, PLANE183 (8- noded quadrilateral) elements are used for 2D simulations, and SOLID187 (10- noded quadratic tetrahedral solid) elements for 3D. The creep curves are fitted to the combined time-hardening equation using the curve-fitting tool in ANSYS MAPDL to estimate the parameters. Figure-9 illustrates the variation of homogenized creep strain versus time curves for different stress values of 40, 50, 60, 70 and 80 MPa obtained using the 2D unit-cell model of 20% SiC composite.
-
Results of macroscopic creep analysis
A 2D axisymmetric finite element model using ANSYS MAPDL is used to analyze the macroscopic creep behavior of the FG thick cylinder for different volume fraction profiles. The finite element is meshed with 8-noded quadrilateral (PLANE183) elements.
Fig. 9: Homogenized creep curves for different load values (2D unit-cell model, = 0.2)
The volume fraction of constituent 2 at each location over the domain are determined from the gradation profile and assigned to each node as an initial state variable 2() [0,1]. The fraction of the two constituents adds up to 1, i.e., 1 + 2 = 1. The homogenized thermoelastic properties are calculated using the Mori-Tanaka [21] schemes. The effective creep properties for range of field-variable values are determined using the homogenization, ensemble averaging and surface fitting procedure. A macroscopic analysis is performed to obtain time-dependent stresses and strains.
<>Fig. 10: Power-function volume fraction profiles for different values of ( = 0, = 0.5)
Fig. illustrates the volume fraction profiles for different values of for power-function (Eq. 6) for = 0 and = 0.5. As exponent increases, the SiC content in the interior region (and the overall SiC content) of the cylinder decrease. The effect of parameter is translated into the macroscopic problem through a change in thermoelastic and creep behavior within the cylinder. Figure-11 shows the macroscopic creep strain histories at inner and outer surfaces, and stress distributions up to 150 h of creeping using the homogenized creep curves from the 2D micromechanical model. The composite is graded linearly ( = 1) in the radial direction with = 0 and = 0.5. The initial stress distribution curves (at = 0) are also shown as dashed lines.
Initially, the radial stress is compressive throughout the cylinder and is equal to 15 MPa on the inner surface, and zero on the
outer boundary surface, satisfying the imposed boundary conditions.
Fig. 11: (a) Stress component distributions along the thickness, (b) Evolution of creep strain components with time at different locations, (dotted lines indicate initial conditions, and the solid lines represent after reaching steady state)
Both tangential and axial stresses are tensile and increases with increasing radius to attain a maximum at the outer surface. The effective stress also increases with increasing radius. With creep accumulation, the radial stress changes little, but the tangential stress is decreases at the inner surface and increases at the outer surface. The axial stress component increases throughout the cylinder. Each section of the cylinder experiences a multiaxial state of time-varying stresses, whereas the creep model is generated from a uniaxial model. Since the maximum creep strain components are located at the inner surface of the cylinder, history of the tangential creep strain at the inner surface and von Mises effective stress distribution throughout the cylinder wall at steady state have been selected to represent the stress and creep strain situation.
-
-
CONCLUSIONS FROM MULTISCALE CREEP ANALYSIS OF FGM CYLINDERS
To determine safety requirements of functionally graded (FG) pressure vessels, time-dependent structural integrity assessment procedures need to be established. Firstly, thermoelastic and time-dependent stress/strain solutions of a heat generating, and rotating FG cylindrical vessel are studied in this research. Individual material property profiles are described using power-functions. Exact solutions are obtained for thermoelastic stress and strain distributions. A numerical procedure based on successive solutions is employed to obtain time-varying stress and strain histories. Results are presented, which are useful for validation purposes of more complicated cases e.g., temperature dependent materials, more general material property distributions etc. The study provides valuable hints to material scientists and engineers in choosing material gradients for minimizing creep damage. Important results and few general observations from this work are summarized as follows:
FGMs are composed of gradually varying composition, with the possibility of hierarchical microstructures. To predict the time-dependent response at the macroscale, effects of microstructural features on the creep behavior need to be quantified. Multiscale techniques are effective in incorporating underlying deformation and failure mechanisms at smaller scales. However, limited work has been reported on the multiscale creep modeling of FGMs. A multiscale model has been developed to incorporate material properties of constituents into the creep study.
Parametric studies have been performed to investigate the effects of volume fraction profiles, maximum particle composition, and cylinder thickness on the maximum creep strain. (i): A higher ceramic content at the outer wall reduces the accumulated creep strain in the inner wall. (ii): The creep strain can also be controlled by adjusting the volume fraction profile. In practice, it is desirable to minimize the creep strain accumulating in the pressure vessel structure.
The framework relates the time-dependent behavior of the matrix into the micromechanical model, and further integrates it to the macroscopic model. At a local scale, the Mori-Tanaka scheme is used to estimate the homogenized elastic properties, and a finite-element based homogenization techniques is used to estimate the creep response. Creep characteristics are described by the combined time-hardening creep model. The model has been successfully implemented to study the time-histories of creep strains and stress distributions of FG thick-cylinder. The model has been further employed to compare the creep response of any internally pressurized cylinder (linearly graded) using three different micromechanical models: (a) 2D axisymmetric unit cell, (b) 3D unit cell, and (c) 3D SRVE. It is found that the macroscopic stress-strain results based on the 2D single-inclusion micromechanical model are close to that obtained from more realistic 3D SRVE model, while providing computational simplicity.
-
ACKNOWLEDGMENTS
The authors gratefully acknowledge the financial support provided by the Louisiana Board of Regents in the form of Louisiana State Universitys Economic Development Assistantship (EDA) award. Supercomputing facilities provided by High Performance Computing (HPC) at the Louisiana State University are also gratefully appreciated.
-
REFERENCES
-
B.D. Dunn, Materials and Processes: for Spacecraft and High Reliability Applications, Springer International Publishing, 2015.
-
H.-L. Dai, Y.-N. Rao, T. Dai, Composite Structures, 152 (2016) 199-225.
-
L.H. You, H. Ou, Z.Y. Zheng, Composite Structures, 78 (2007) 285-291.
-
L.H. You, H. Ou, J Press Vess-T Asme, 130 (2008) 014501.
-
T. Singh, V.K. Gupta, Journal of Composite Materials, 44 (2009) 1317-1333.
-
T. Singh, V.K. Gupta, The Journal of Strain Analysis for Engineering Design, 44 (2009) 583594.
-
T. Singh, V.K. Gupta, Composite Structures, 93 (2011) 747758.
-
J. Chen, K. Yoon, S.-T. Tu, J. Press Vess-T Asme, 133 (2011) 051401.
-
M.Z. Nejad, Z. Hoseini, A. Niknejad, M. Ghannad, Journal of Mechanics, 31 (2014) 16.
-
Y.Y. Yang, International Journal of Solids and Structures, 37 (2000) 7593-7608.
-
J. Chen, S. Tu, F. Xuan, Z. Wang, Journal of Strain Analysis for Engineering Design, 42 (2007) 69-77.
-
A. Loghman, A.G. Arani, S. Amir, A. Vajedi, Int J Pres Ves Pip, 87 (2010) 389-395.
-
A. Loghman, A. Ghorbanpour Arani, S.M.A. Aleayoub, Mech Time-Depend Mat, 15 (2011) 353-365.
-
A. Loghman, M. Moradi, Mech Time-Depend Mat, (2012).
-
J. Jafari Fesharaki, A. Loghman, M. Yazdipoor, S. Golabi, Mech Time-Depend Mat, 18 (2013) 41-53.
-
M.Z. Nejad, M.D. Kashkoli, International Journal of Engineering Science, 82 (2014) 222-237.
-
J.A. Ahmed, M.A. Wahab, World Journal of Engineering, 12 (2015) 517-532.
-
H.W. Zhang, D.S. Yang, S. Zhang, Y.G. Zheng, Finite Elements in Analysis and Design, 88 (2014) 97-117.
-
D.-F. Li, B.J. Golden, N.P. ODowd, Acta Materialia, 80 (2014) 445-456.
-
R.L.J.M. Ubachs, O. van der Sluis, W.D. van Driel, G.Q. Zhang, Microelectronics Reliability, 46 (2006) 1472-1477.
-
T. Mori, K. Tanaka, Acta Metall Mater, 21 (1973) 571-574.
-
R. Hill, J Mech Phys Solids, 13 (1965) 213-222.
-
Z. Hashin, S. Shtrikman, J Mech Phys Solids, 11 (1963) 127-140.
-
J. Llorca, J. Segurado, Materials Science and Engineering: A, 365 (2004) 267-274.
-
S. Kari, H. Berger, R. Rodriguez-Ramos, U. Gabbert, Composite Structures, 77 (2007) 223-231.
-
L. Yang, Y. Yan, Z.G. Ran, Y.J. Liu, ComposSci Technol, 76 (2013) 14-20.
-
M. Mondali, A. Abedian, A. Ghavami, Materials & Design, 30 (2009) 10751084.
-
A. Ghavami, A. Abedian, M. Mondali, Materials & Design, 31 (2010) 2616-2624.
-
V. Monfared, M. Mondali, A. Abedian, J Mech Sci Technol, 27 (2013) 3277-3285.
-
Y.H. Park, J.W. Holmes, Journal of Materials Science, 27 (1992) 6341-6351.
-
W.J. Lee, J.H. Son, I.M. Park, Y.H. Park, Comp Mater Sci, 48 (2010) 802-812.
-
W.J. Lee, S.K. Jo, I.M. Park, Y.H. Park, Materials Science and Engineering: A, 528 (2011) 45644568.
-
W. Lee, Materials transactions, 55 (2014).
-
Y.J. Cho, W.J. Lee, Y.H. Park, Comp Mater Sci, 100 (2015) 67-75.
-
C.H. Yu, M.W. Bird, C.W. Huang, C.S. Chen, Y.F. Gao, K.W. White, C.H. Hsueh, J Eur Ceram Soc, 34 (2014) 4145-4155.
-
K. Kwok, D. Boccaccini, Ã…. Persson, H. Frandsen, Inter. Journal of Solids and Structures, 78 (2016) 38-46.
-
S. Goto, M. McLean, Scripta Metallurgica, 23 (1989) 2073-2078.
-
M. Mondali, A. Abedian, S. Adibnazari, Comp Mater Sci, 34 (2005) 140150.
-
Y. Pan, G.J. Weng, S.A. Meguid, W.S. Bao, Z.H. Zhu, A.M.S. Hamouda, Mech. of Materials, 58 (2013) 111.
-
M.M. Aghdam, S.R. Morsali, Comp Mater Sci, 91 (2014) 62-67.
-
H.M. Yin, G.H. Paulino, W.G. Buttlar, L.Z. Sun, J Appl Phys, 98 (2005) 63704.
-
A.H. Muliana, International Journal of Solids and Structures, 46 (2009) 1911-1924.
-
Vel, S.S. and A.J. Goupee. (2010). Multiscale thermoelastic analysis of random heterogeneous materials Part I: Microstructure characterization and homogenization of material properties. Computational Materials Science, 48(1), 22-38.
-
MATLAB Release 2013b, The MathWorks, Inc., Natick, Massachusetts, United States.
-
Kari, S., H. Berger, R. Rodriguez-Ramos, and U. Gabbert. (2007). Computational evaluation of effective material properties of composites reinforced by randomly distributed spherical particles. Composite Structures, 77(2), 223-231.
-
J.A. Ahmed, Analytical Solutions and Multiscale Creep Analysis of Functionally Graded Cylindrical Pressure Vessels, (2017), Ph.D. Dissertation, Louisiana State University, LSU-Doctoral Disserttaion-4279.
-
ANSYS® Academic Research, Release 16.0-17.2, ANSYS Documentation, ANSYS, Inc.
-
J.A. Ahmed and M.A. Wahab, "Generalized study on time-dependent creep analysis of functionally graded thick-walled cyclinders under thermal and mechanical boundary conditions," Proceeding of the ASME 2021, International Mechbnaical Engineering Congress and Exposition, Paper No. IMECE2021 -71743, IMECE21(Virtual), November 1-5, 2021,USA,
-
Lee, W. (2014). Practical applicability and limitation of representative volume element approach to model creep behaviors of metal matrix composites.
Materials transactions, 55(9).
-
P.E. Krajewski, J.W. Jones, J.E. Allison, Metallurgical and Materials Transactions A, 26 (1995) 3107-3118.