
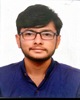
- Open Access
- Authors : Manthan R Pandya , Devansu J Khorasiya , Parth V Patel
- Paper ID : IJERTV9IS080228
- Volume & Issue : Volume 09, Issue 08 (August 2020)
- Published (First Online): 26-08-2020
- ISSN (Online) : 2278-0181
- Publisher Name : IJERT
- License:
This work is licensed under a Creative Commons Attribution 4.0 International License
Modified Propelled Cycle
Devansu J Khorasiya, Manthan R Pandya, Parth V Patel
Research Scholar Gandhinagar Institute of Technology,
Gujarat, India – 382721
-
INTRODUCTION
The following research paper is for details the process we used to generate and evaluate possible iterations for our hand-operated rear wheel drive cycle attachment. Since this process resulted in the final design that we are going to build, the main focus of this research paper is to present an outline for the next phase of development, which is the actual construction and testing of the device.
Worldwide, 100-130 million people need wheelchairs, but less than 10% either own or have means of obtaining one because most of these people live in developing countries where cycles are not available. It is predicted that these figures will rise by 22% over the next ten years for a number of reasons, including but not limited to the aging baby- boomer generation, many ongoing wars, re-habitation of areas infested with land mines from prior conflicts, and other injuries and diseases. Current cycle technology is relatively well- established in that there is not a great deal of variation in the wheel chair market, which can create difficulties for individuals whose needs are not met by currently available model. Cycle design and functionality as a whole has been greatly improved over the past several decades, but there is still a need for new technology and innovative designs. The majority of assistive device users are over age 65, with increases expected as the baby boomers age and the average life expectancy increases. Many of the conditions that restrict an individual to reliance on a Cycle also limit control of the upper extremities to the extent that the user can only operate the chair with one hand. Powered cycles serve this need quite well but are expensive and thus inaccessible for many individuals. They came with many difficulties like hard to transport, hard to use, etc. A person with disability, that person who wishes to remain independent and mobile needs specially adapted vehicle with all necessary functions. If you can see the current scenario of market, Configuration utilizes heavy internally-geared, quirky chain-driven system with quick release fixtures at the head tube connection and the connection to the wheelchair, under the users seat. It breaks by means of a coaster brake, so to stop, you just forwards with your hands. The advantages of such a system are: Increased mobility, Increased efficiency and steering – (a current wheelchair steers by braking on wheel, which continually causes the user increased energy expenditure), Exercise for the upper body, Versatility – (by being able to detach the steering column from the wheelchair, as opposed to a fixed tricycle for exercise), Carrying capacity of the basket.
-
RESEARCH METHODOLOGY
In the lead up to the project proposal, we did extensive research on domestic and international standards for cycle construction; the potential market for such a device; and the existing products and patents that were similar to our design. The results are summarized in the sections that follow. The internationally accepted standard for Cycle design is provided by the International Organization for Standardization (ISO). The German national organization for standardization, the Deutsches Institute für Normung e.V. (DIN; in English, the German Institute for Standardization) is the country's ISO member body and has wheelchair designs that are equivalent to the ISO standards. While both codes provide standards for the design of wheelchairs, these standards do not extend to wheelchair attachments and as such there are not governing standards for the design of wheelchair attachments. However, in order to test the strength of our design and guarantee strength and durability, we will design our wheelchair attachment to comply with ISO standards.
(A ISO 7176/ EISO-ii) The international standard for evaluating cycle is the International Organization for Standardization (ISO) 7176, International Standard for Wheelchairs. In 1996 Whirwind Wheelchair International, an organization that works to promote safety of wheelchairs in developing countries, where such standards do not exist, developed their own Extended ISO (EISO) standards for testing the strength of wheelchairs. Some of these tests are more rigorous than traditional ISO standards such that they specify static and impact tests for active wheelchairs in a variety of environments, terrains, and loading conditions.
EISO standards cover subjects such as basic seating dimensions, ways of determining tipping stability, static and impact strength requirements, and testing methods to ensure long-term durability. The intent of our project is to produce a high-quality prototype specifically for use by Users, but if it results in a commercially viable product, we believe that a global market exists for this type of device. Such a product would appeal to any disabled persons who maintain the complete use of their arms and upper body, but either permanently or temporarily lack the use of their legs and lower body. This could be someone who is a paraplegic, or someone who has been in an accident and is temporarily without
the full use of their legs. Our product is designed for the user who desires the functionality and increased mobility of a hand-cycle, but also requires the versatility and accessibility available in a standard wheelchair configuration.
An estimated 1.6 million Americans residing outside of institutions use wheelchairs, most (1.5 million) use manual devices, with only 155,000 people using electric wheelchairs.iii In March 2003, the German Statistics Office calculated that 1.56 Million German citizens (1.9 % of the population) depended permanently or temporarily on a wheelchair. For Europe as a whole this translates to 7.1 Million people.
Abledata.com, an online resource that provides objective information about assistive technology, states in the document informed Consumer's Guide to Wheelchair Selection, that Wheelchair types vary nearly as much as the types of disabilities for which they are designed. A user who maintains the use of their upper body but has no use of their legs will obviously require a much different chair compared to an individual who lacks the use of both their upper and lower body. Similarly, an individual who has suffered a spinal injury and has lost the use of their legs will require a different arrangement than an individual whose legs have been amputated.
Because there are so many wheelchair designs that are customized for the needs of specific users, our product will have a larger target market as a removable attachment that accommodates the users current wheelchair compared to a permanent hand-cycle wheelchair. Our product will allow users to remain in their customized wheelchairs but still have the added mobility offered by a hand- cycle when necessary. Since our product is an attachment, users dont need to sacrifice the comfort and familiarity of their wheelchair to have a hand-cycle.
Since the project proposal, we have researched a number of new ideas, including (but not limited to) flexible shafts, hydraulic drive systems, belt drive systems, internally-geared cranks, round profile gears (as opposed to the involute profile typically found on gears), differentials, and steering and suspension geometry (camber, caster, slip angle, etc…). Each of these concepts was carefully evaluated and either rejected or added to the list of potential components.
After the many iterations of drives, these methods did not mae it to the final design were the hydraulic drive, the belt drive, the internally-geared cranks, and round profile gears. Reason for the hydraulic drive was found to be too inefficient, Reason for the belt drive not easily standardized, Reason for the internally geared cranks didnt offer enough range of gearing options, and the round profile gears are expensive and not easily standardized.
For the final design, there are four major components that will be incorporated. First, a flexible shaft will transfer power from the cranks to the portion of the device that is under the seat of the wheelchair. This was chosen as the best method, as it allows for the subtle changes in geometry that occur while steering without any sacrifice in efficiency. Second, the attachment of the device to the wheelchair will be accomplished with a latching mechanism that will secure the device and lift the front casters off the ground all in one motion. Third, gearing will be accomplished with an internally-geared hub affixed to the wheelchair frame beneath the user. A chain will go from the hub to the drive wheel of the fourth major component; a differential that will transfer power to the rear wheels. The differential was chosen to maintain the handling characteristics of a wheelchair without an attachment, namely, its ability to turn in place. The differential also prevents slip of the wheels while turning, as one wheel travels a shorter distance through a turn.
-
CONCEPT EVALUATION
Initially in the design phase, we paired up into two teams consisting of two students members each. Each team was assigned one or two subsystems to brainstorm and create sketches for. Ultimately, four or five sketches for each subsystem were developed and selected for analysis in the overall system configuration.
-
Subsystems
Subsystems are the individual parts of the device that contribute to the whole. We identified four subsystems to develop in our teams of two students. The following are the subsystems we chose to sketch and analyze.
-
Steering/Power Transfer
The subsystem for steering and power transfer includes the method of steering to be used and most importantly was the method by which the rotation of the cranks is transferred to our attachment interface.
This is a difficult mechanism to design because we need to transfer power input to the cranks down the head tube and into the attachment, so the rotational motion changes direction two times. We need to keep the current crank function, but we need to find a way to transfer that rotation to the rear wheels.
The steering system will work the same way that the current system does, whereby a shaft connecting the cranks to the front fork is run through the head tube and supported by bearings, similar to the head set on a bicycle
Its very important to combine functions of drives at one place. Modified Steering is the one where user will experience all the functions at one place like Forward drive, Backward drive, Breaking of cycle, Moving towards right or left side, horn system etc. This phenomenon will decrease lots of mechanical effort of user. User can operate steering
with one or both of the hands, depends on user. Mechanism used in steering is to and fro motion converting into rotary motion of rear wheels. All the modification accessories are on steering at right place to make it easy for user..
Some current models of one-hand propelled manual wheelchairs have steering mechanisms which control the position of the front casters. This makes it very difficult or impossible for the cycle to be steered by anyone other than the user, i.e. an attendant cannot have complete control of the cycle. In order for the any cycle to be available to the largest possible population, this problem must be eliminated.
-
Flexible Shaft
Flexible shafts are used for rotary power transmission in a variety of commercial, industrial, and medical applications. Flexible shafts are commonly used for rotary tools and other high torque and high speed of transmission, low torque applications and its majorly made from tightly looped coils. Flexible shafts can transmit both the alternatives: High torque-low speed and Low torque-high speed. Flexible shafts can make bends up to 90degrees without adversely affecting performance and efficiency.
-
Constant Velocity Joint
Forces and torques from the cranks are deflected in a first (upper) gearbox. From this box the transmission is realized by a rigid shaft along the axis of the head tube. Underneath the crank there is a second (lower) driven mechanism which changes the rotation phenomenon along the longitudinal axis of the vehicle. In order to maintain the forks ability to steer, the rigid shaft which leads to shifting is connected with a constant velocity joint to the gearbox output shaft. This joint has to be positioned in a straight line with the turning axis of the steering system.
-
Universal joints
A Universal joint is a joint in a rigid rod that allows transfer of rotary motion of the rod, while allowing the rod to bend at an angle, usually up to 45degrees. Universal joints are used in series to raise the angle that a rigid shaft can bend and still permit transfer of rotary motion. U-joints are commonly used in a variety of light and heavy duty applications including automotive applications. U-joints are strong and readily available and can transmit high-torque and high-speed rotation.
-
Rear Drive Method
The rear drive method subsystems are basically ideas for the mechanism that will transfer power of driving from the steering of cycle to the drive wheels. This mechanism is easy to semi-permanently mount to the wheelchair frame with minimal modification to the wheelchair. Final design is selected from the analysis following configurations because we need to maintain the modified mechanism of steering that the wheelchair utilizes without having any frictions engaged, and still maintain efficient power transfer.
-
Propelled Drive
A tricycle/cycle which may be propelled by the arms of the rider and that is supported thereon in a prone position. The forward or drive wheel is driven by the rider as he grasps a pair of hand-grips which respectively are rotatably attached to a pair of opposing crank members. A typical coaster-brake couples the crank members to the drive wheel to enable the rider to cease turning the crank members for coasting, steering, and braking purposes. A slide-bar is included which is established in part by one of the crank members and enables one of the hand-grips to be shifted from a drive position wherein the hand-grips are radially displaced 180* one from the other to a coaster-steering position wherein the hand-grips are radially aligned one with the other.
-
Braking Solutions
Solutions for stopping the device were not included in the process of concept generation and evaluation because we believed that adding a braking system was something that could be accomplished more easily after we had settled on the best design for transmitting power, attaching the device, and gearing. We have since selected a combination of the coaster brake that is included in the internally-geared hub that we are using to stop the rear wheels with a back- pedaling motion of the cranks; and a standard bicycle v-brake on the front wheel, actuated by hand, using a brake lever attached to the grip part of the crank assembly.
-
Braking andPropulsion
Cycle moves forward and reverses directions by propulsion system and Braked must be able to slow down the cycle in addition to bringing it to a stopping position. As we know the basic function of brakes is to slow or stop moving wheels to prevent loss of control of cycle. In the general practical uses of modified propelled cycle we considered 35 pounds of grip force to actuate.
Individuals with disabilities and the elderly both may have moderate to severely diminished physical strength capabilities comared to able-bodied adults. As such, the actuation force limit was based on grip strength data from elderly men and women. For elderly men, the first, fifth, and tenth percentile.
-
Working Principal
When the user apply his/her efforts on steering in forward and reverse direction crank and cnnecting rod provide the motion to wheel chair by converting the to and fro motion into rotary motion. Simply User make force on steering to move the steering forward and backward. The motion of direction of cycle is controlled by steering. The turning action takes place by turning the steering right and backwar direction, same like any car. This mechanism must allow the cycle to move both forward and reverse, and as such have a means of switching between the two directions within less efforts. In order to propel the chair in a straight line, it must also move three wheels simultaneously. The following mechanism outlines possible ways of accomplishing these goals.
-
Concepts
We tried to standardize the process of generating concepts by using a blank wheelchair template for our sketches. We assigned names for each concept based on the options for each as given by the decision matrix. For Every Concept We considered the Power transfer, rear drive type, coupling, gearshift, braking solutions, etc. Each Concept has their different advantages and disadvantages and All Concepts have their own abilities. From those all concepts we have to choose one which highest affectivity.
-
-
PROJECT METHODOLOGY
The limitations of the projects in the above mentioned research papers are: Irreplaceable components, Complex Handling mechanisms, Complex Components design, Difficult to fabricate, Uneconomical, Unsuitable for all types of arms ,Time-consuming, Heavier in weight
We have tried to overcome the above mentioned limitations by implementing: Replaceable components, Simple mechanisms, Simple design, Easy to fabricate, Economical, Suitable for all types of customers (Disabled Peoples), Timesaving, Lighter in weight
Physically handicapped people have many problems. Assuming little or no use of legs or feet, particularly, since paraplegia springs to mind, very often have difficulties rising from bed, getting into their chair, dressing below the waist, moving from chair to toilet and back (and wiping themselves before returning), reaching for any items on or above standard-height vanities and kitchen cabinets and above centerline in refrigerators, finding and using common furniture such as couches and recliners, getting through house doors (especially closing doors behind them), getting from door to parking lot over curbs, getting from chair to vehicle (sometimes riding in their own chair in a specially- equipped van), driving, exiting their vehicle (usually but not always made easier by a rear-exit ramp), getting from parking lot into many institutions or places of business over curbs and up steps and over thresholds, reaching over standard-height counters, reaching higher grocery-store shelves and cooler cases, fueling their vehicles at self-serve stations, getting around in narrow business aisles (especially when "normally-abled" people have parked their shopping carts in the middle of the aisle and are jabbering to someone on a cell phone), traveling by any form of mass transit (bus, train, airplane), passing through metal detectors.
One of the main problems faced by the disabled peoples in this modern Era is high cost of the equipment used in facilities provided for them which leads to less productivity and more labor work in cultivating workshops. In order to minimize the problems of disabled peoples we have designed an economical and affordable Modified Propelled Cycle which can perform very effectively for them. In order to maximize the benefits of the product we have also planned our design so that normal people can also use the product in place of todays eras costly vehicles. We are planning to use some attractive looks and materials in the fabrication process as well as we are also designing our product that gives highest comfort level to the customer. As the customers aspect view they are always looking for economical and attractive looking model so our product is also designed with respect to these all requirements fulfillment.
This Research leads to: More Affectivity of Cycle, Reduction in Effort with respect to time, Less labor work to manufacturing, Affordable equipments, Flexible in nature, Easy to use and affordable, More economical, All Peoples can Use: Disabled as well as Normal peoples can also use, More Applications from the current scenarios..
Objectives of Research: No consumption of fuel and electricity, thus this will be helpful to poor peoples, This design of wheelchair is made to achieve to travel long distance (more than25km), Provide utmost comfort and ease while operating and travelling, The system is intended to provide easy handling and acceleration compared to conventional available wheelchair, Facility for light, luggage and Brake control, The various attachments can be easily assembled and disassembled. The equipment is light in weight, thus the customer can easily carry it by road, The equipment reduces the labor cost of workers, The vehicle does not cause any kind of pollution, The vehicle is economical and thus affordable by the customers at low-cost, The vehicle is suitable for any kind of peoples, The vehicle is simple and its maintenance cost is low.
This project deals with the solution of basic problems faced by the poor peoples of India like the high equipment cost used in manufacturing and high labor cost which ultimately leads to less productivity of cycles. Moreover this
project combines attachments for various Applications like less mechanical efforts, luggage storage, attractive looking with affordable cost which will bring revolution in India.
-
DESIGN PROCEDURE
Chassis: A chassis comprises of a nternl framework which provide support to an artificial man- made object. It is similar to an animals skeleton. The under part of an automobile which consists of the frame can be considered as an example of the chassis. If the wheels are included in the chassis, then the chassis can be termed as rolling chassis. The chassis is considered as one of the necessary part of an automobile. It holds both the body of power train and the machine. Chassis also acts as a holding device on which several mechanical parts like the drives, gear trains and the engine, the axle assemblies which consists of various suspension parts, brakes, wheels, steering mechanisms and components are bolted.
Specifications:
Maximum Length of Cycle: 1990 mm Maximum Width of Cycle: 935 mm Maximum Height of Cycle: 1300 mm Front Band of Chassis: 138 mm of Diameter (Up Side)
Rear Band of Chassis: 118 mm of Diameter (Down Side)
Maximum Length or Distance for Seat: 602 mm
Maximum width or Distance for Seat: 800 mm
Distance for Footrest: 150 mm
Distance of Steering Upper Point to footrest: 320 mm
1. Geometry |
Width: Seat width 45.7cm (18in.) + armrest + tires Length: Must be about same size as current set up Height: Less than 1.1 m (3.6 ft) Space Requirement: Must be able to fit into trunk of midsized car Front Wheel: 24-28 inches (70cm bicycle standard) Rear Wheel: 24-28 inches (70cm bicycle standard) Connection: Minimal changes to the wheelchair for connection Connecting and releasing without any further tools |
2. Driving Behavior |
Handling: Sporty but still comfortable and suited to daily use Traction assured: Must maintain traction while accelerating, turning, up 20% grade, on wet surfaces Traction limited: Should be limited traction on snow and ice Control: Must not be limited by: bevel surfaces, curves, small steer angle, directional stability should be assured by mechanism |
3. Kinematics |
p>Direction of motion: Translation in x,y,z Rotation around z
Rotation around y should be limited to stop roll over Translation motion: Forward motion only, no reverse Velocities: Regular: 5-7 km/h (3.1mph) Maximum: 25 km/h (15.5mph) Accelerations: Acceleration: 2 m/s2 (6.56 ft/s2) Braking: 10 m/s2 (32.8 ft/s2) |
4. Stress |
Drive train: Average torque: 10 Nm (7.38 ft) Maximum torque: 50 Nm (36.9 ft) Average power: 120 W Maximum power: 500 W Stress type: Part load of about 80 – 90% Peak load 10 -20 % Rotation speeds: Continuous crank speed: 20 – 40 rpm Peak crank speed: 50 rpm Mass inertia: Keep small by weight reduction Load distribution: If possible try to avoid forces on the front axis Dynamic loads: Shocks caused by pavement Force transmission: Manual Not constant (alternating) User weight: Average: 75 kg (165 lbs) Maximum: 120 kg (264 lbs) |
5. Power Transfer |
Efficiency: 70% Approximately (By Calculations in ANSYS) |
6. Ergonomics |
Access of controls: Brake must be easy and quick to use, Best if working without removing hands from cranks, Gearshift should be easy and quick to use, Light should be turned on by one switch. Kind of usage: Usually manual control, exceptions may be tachometer Crank attachment: Must not interfere with user while in use, Must not obstruct view |
1. Geometry |
Width: Seat width 45.7cm (18in.) + armrest + tires Length: Must be about same size as current set up Height: Less than 1.1 m (3.6 ft) Space Requirement: Must be able to fit into trunk of midsized car Front Wheel: 24-28 inches (70cm bicycle standard) Rear Wheel: 24-28 inches (70cm bicycle standard) Connection: Minimal changes to the wheelchair for connection Connecting and releasing without any further tools |
2. Driving Behavior |
Handling: Sporty but still comfortable and suited to daily use Traction assured: Must maintain traction while accelerating, turning, up 20% grade, on wet surfaces Traction limited: Should be limited traction on snow and ice Control: Must not be limited by: bevel surfaces, curves, small steer angle, directional stability should be assured by mechanism |
3. Kinematics |
Direction of motion: Translation in x,y,z Rotation around z Rotation around y should be limited to stop roll over Translation motion: Forward motion only, no reverse Velocities: Regular: 5-7 km/h (3.1mph) Maximum: 25 km/h (15.5mph) Accelerations: Acceleration: 2 m/s2 (6.56 ft/s2) Braking: 10 m/s2 (32.8 ft/s2) |
4. Stress |
Drive train: Average torque: 10 Nm (7.38 ft) Maximum torque: 50 Nm (36.9 ft) Average power: 120 W Maximum power: 500 W Stress type: Part load of about 80 – 90% Peak load 10 -20 % Rotation speeds: Continuous crank speed: 20 – 40 rpm Peak crank speed: 50 rpm Mass inertia: Keep small by weight reduction Load distribution: If possible try to avoid forces on the front axis Dynamic loads: Shocks caused by pavement Force transmission: Manual Not constant (alternating) User weight: Average: 75 kg (165 lbs) Maximum: 120 kg (264 lbs) |
5. Power Transfer |
Efficiency: 70% Approximately (By Calculations in ANSYS) |
6. Ergonomics |
Access of controls: Brake must be easy and quick to use, Best if working without removing hands from cranks, Gearshift should be easy and quick to use, Light should be turned on by one switch. Kind of usage: Usually manual control, exceptions may be tachometer Crank attachment: Must not interfere with user while in use, Must not obstruct view |
Factor of Safety: 4.6 Objective Table:
Figure 1: Design of Chassis in FUSION 360 Software
7. Safety |
Braking: Plan of differential Driving at night: Planning to attach Lighting meets German and American specs in Future. Roll over protection: Wheelchair may not roll over at any time while in use Protection of user: Covering of rotating and moving components |
|
8. Usage |
Types of usage: Daily use: going to work, errands, private contacts Sporty aspect: small tours, fitness Area of use: All over the World. Duration of use: Daily: 1-5 hours Total: 2000 hours without general overhaul Special environments: Dust, small stones, water, humidity, grass, other substances Attachment Time: No more than 30 seconds, single person operation Detachment Time: No more than 30 seconds, single person operation |
|
9. Transport |
No lifting device: two person must be able to lift (15 Kg, 33 lbs) |
|
10. Manufacturing |
Prototype: No fixed concept |
|
11. Assembly |
Prototype: No fixed concept |
|
12. Maintenance |
General: Maintenance free for 2000 hours Break: Visual inspection and change if ware if too large |
|
13. Recycling |
Steel: Material recycling like any other product Aluminum: Material recycling like any other product Rubber and Plastics: Probably thermal utilization Lubricants: Disposal as hazardous substances |
Product Description:
-
Product Name: Modified Propelled Cycle
-
Vehicle configuration: Upright, Semi-recumbent, Prone
-
Frame material: MILD STEEL AISI 4130
-
Fairing material(s): Fiber Reinforced Plastic
-
Number of wheels: 3
-
Vehicle Dimensions (m): Length: 1.995m, Width: 0.935m, Height: 1.32m
-
Weight Distribution (kg): Front: 6.4 kg, Rear: 10.2 kg, Total Weight (kg): 16.6 kg (Based on Software)
-
Wheel Size (m): Front: 0.66m, Rear: 0.66m, Frontal area (m²): 0.64 m²
-
Steering (Front or Rear): Front
-
Braking (Front, Rear, or Both): Rear
-
Estimated Coefficient of Drag: 0.3141
Analysis: Once 3-D models were made in a CAD program, the weight was analyzed to insure that the product would not be too heavy. The components that are permanently fixed to the wheelchair weigh just over 20lbs, and the attachment weighs just over 16lbs. This is a little on the heavy side, but fortunately, the majority of the weight will be carried on the wheelchair, and the lighter of the two halves is the part the user actually has to lift. Furthermore, the rear portion of the wheelchair has some components which may be machined to reduce the weight.
Figure 2: Equivalent Stress Analysis in ANSYS Software
As for the strength of the device, most of the necessary testing will be on the components that we have to manufacture ourselves. This is because the off-the-shelf components are all from the cycling industry, which are tested for the greater loading that results in pedaling with the legs instead of rowing with the arms. We have since done some finite element analysis, which proves that the original design was probably sound, but we are considering a new, adjustable connection, which should be even stronger.
Figure 3: Total Deformation Analysis in ANSYS Software
Figure 4: Side View, Front View, Top View (2D)
Front Body: Front Body is very important part of Cycle as it carries front wheel as well as steering too. Dynamic loads are effect every times on the Front Body as the maximum loads reacts in this area. Front Body contains front wheel, front tyre, front wheel bush, bearing, steering mechanism hooks, bush etc. these all things are very necessary for the cycle. Front Body is designed for the Maximum of 50 Nm of Dynamic Loads in between the running of cycle in the roads. There may be a Road Bumpers also So, we also consider that in this Dynamic loads.
Figure 5: Front/Rear Wheel Tyre Figure 6: Front Body
Specifications: Maximum Length: 990 mm Maximum Width: 45.5 mm
Front & Rear Wheels: Cycle has total three wheels for moving motions. Front wheel is attached to the Front Body and remaining two rear wheels are attached with the chassis with the steering mechanism for drive. Standard size and dimensions wheels are used for the manufacturing. One of the rear wheels is only for support purpose for motion of the cycle. As only one wheel is attached with the driving mechanism of the cycle. Crank transfers to and fro motion into the rotary motion where supporting crank takes major role to transfer this rotary motion to the wheel with the help of the flexible shaft and flywheel. Wheels are mounted on horizontal axis to consider heavy weights transmission. All the necessary tests are done for the proper driven system of the cycle in the ANSYS software to avoid any inconvenience while manufacturing.
Steering Mechanism:
Figure 6: Steering Mechanism Illustration
Final Assembly: After designing rough sketch on paper and designing each and every part in the software, we finally assembled all the parts to obtain our cycle named Modified Propelled Cycle. Each and Every component is designed/modelled in the fusion 360 software with 100 percent dimensions as well as precision and accuracy. Design for assembly can take different forms. Cycle has many components and each component have to assemble first on software for the virtual look and analysis purpose. Its time consuming but it saves much efforts while manufacturing and assembly after the manufacturing. In addition, if the parts are provided with features which make it easier to grasp, move, orient and insert them, this will also reduce assembly time and assembly costs.
Front wheel is attached with the Front body and two rear wheels are attached with the chassis. Steering is connected with both front body and chassis, which is driving component the cycle. Driving mechanism contains shafts, cranks, flywheel, connecting rod etc. In this design we majorly used One Chassis which is heart of our Project.
In chassis there are lots of mountings like Wheels, Seats, Steering, Mechanism of Wheels as well as Mechanism of Steering to rotate the cycle in left or right direction. Moreover there is Bushes, Bearings, Nuts, Bolts etc mounting to give our Product extra power and Strengths. Steering Mechanism is connected with the four bar chain mechanism so both the motion of the cycle are interconnected and User can use that both motion at a time.
Bill of Material: Here is the detailed list of every components or parts used while manufacturing the modified propelled cycle. Each Component or Part have named, Description (Where or how that part is used), Part or components weight in gram and material used to manufacture that part or component. Figure 7 which is two dimensional (2D) Drawing of Modified Propelled Cycle denotes each part or components number wise whose details given in the Bill of Material Table.
-
All Mass are based on Software Data.
BOM Table:
Figure 7: Two Dimensional Drawing of Modified Propelled Cycle
ITEM
PART NAME
QUANTITY
DESCRIPTION
MASS
MATERIAL
1
Chassis
1
Frame/Skeleton of cycle
8256 g
Mild Steel
2
Front Body
1
Face of cycle, Operator
4944 s
Mild Steel
3
Front Wheel
1
Important for Turning
924 g
Steel
4
Front Wheel Tyre
1
For Drive and friction
433g
Rubber
5
Rear Wheel – 1
1
Driving Wheel
924 g
Steel
6
Rear Wheel Tyre – 1
1
For Drive and friction
433g
Rubber
7
Rear Wheel – 2
1
Driving Wheel
924 g
Steel
8
Rear Wheel Tyre – 2
1
For Drive and friction
433g
Rubber
9
Seat
2
Comfortable seat
1371g
Plastic
10
Governor
1
Important Mechanism for Turning
3975 g
Mild Steel
11
Lower Governor
1
Balancing Mechanism for Steering
295 g
Steel
12
Connecting Rod – 1
1
Driving Mechanism
435 g
Mild Steel
13
Connecting Rod – 2
1
Driving Mechanism
1818 g
Mild Steel
14
Steering Mechanism – 1
1
Turning Mechanism
478 g
Mild Steel
15
Steering Mechanism – 2
1
Turning Mechanism
478g
Mild Steel
Figure 8: 3D CAD View of Modified Propelled Cycle
-
TESTING & REFERENCES
-
Manual Testing will be accomplished primarily by four different methods. Visual Inspection: Many of our specifications can be easily measured with standard tools (ruler, scale, etc…) Computer simulation/analysis: We started building cycle with rough sketches on paper. Before construction even begins, a complete model of the device and all of its components are designed and developed in CAD software (Fusion360 and ANSYS). ANSYS software enables a certain amount of geometric, weight and force analysis. Paper Calculations: Mechanical design principals are utilized to theoretically test for yield and fracture strengths, Factor of Safety, handling characteristics, etc. Each and every components stress and strength calculations are done before manufacturing phase of the cycle to avoid any inconvenience during the manufacturing process. Physical Test Drive: After the manufacturing phase, we have to drive what we have built and evaluate its performance. It will then be given to Prof. Expert to drive and evaluate as well. There is no substitute for real world performance analysis
ERGONOMICS TEST
Objective: The objective was to make the vehicle more rider friendly and hence comfortable as well as the safe.
Methodology: Going through various research articles deep study of ergonomics/safety, we decided proper dimensions for our vehicle which included special emphasis on riders position and all sorts of angular adjustments. All sorts of designing were assisted by CAD (FUSION360), taking appropriate human dimensions.
Result: We connected the fork to the front wheel at an angle of 22 Degree with the vertical. We finalized the distance between handle bar and shoulder as 54 cm. After the All Analysis and Ergonomics Test of the Cycle we overcome on the decision that our Product is Safe enough for the customer, Customer can easily travel by our product from one place to another place. In Future we are planning to add more advantages to the customer for that we are thinking about Battery drive with Gears, More sufficient Speed for the over bridges in the City, Less efforts in the driving Mechanism (Still Current effort s also good enough, but for Customers point of view), More Applications as well as Functions of the Cycle.
REFERENCES
-
Machine Design By P.C. Sharma
-
Machine Design By V.B. Bhandari
-
Production Engineering by O.P.Khanna
-
Manual wheelchairs – Requirements and test methods; German version EN 12183/DIN12183. PDF version. Nov 1999.
-
Origins of Whirlwind Test Values (PowerPoint), Whirlwind Wheelchair International Website, created September 2004, accessed October 17, 2008
-
Wheelchair Use in the United States. Kaye, Kang, LaPlante. USCF Disability Statistics Center. . May, 2002. Accessed Oct 2008.
-
MOVEMENT Periodic Activity Report N°: 2. Zagler, Wolfgang. Modular Versatile Mobility Enhancement Technology (MOVEMENT). Aug, 2006.
-
Mohan Kumar R, Lohit H. S, Manas Ranjan Mishra,Md. Basheer Ahamed Design of Multipurpose Wheel Chair for Physically Challenged and Elder People Volume 11, Issue 1, Apr 2012, Department of Design, M. S. Ramaiah School of Advanced Studies, Bangalore 560058.
-
Shikhar Agarwal and Saumya Gautam Analysis and Optimization of All Terrain Wheelchair SAE Technical Paper 2015-01- 1368 Krishna Institute of Engrg & Technology