
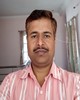
- Open Access
- Authors : K. C. Santhosh , Dr. B. K. Muralidhara
- Paper ID : IJERTV10IS040248
- Volume & Issue : Volume 10, Issue 04 (April 2021)
- Published (First Online): 30-04-2021
- ISSN (Online) : 2278-0181
- Publisher Name : IJERT
- License:
This work is licensed under a Creative Commons Attribution 4.0 International License
Microstructure and Mechanical Properties of Heat Treated Ti8Al1Mo1V Alloy
K. C. Santhosp, Dr. B. K. Muralidhara2
1 Research scholar, Department of Mechanical Engineering, UVCE,
-
Circle, Bangalore University, Bangalore-560001, Karnataka, India
2 Professor and Former Dean, Bangalore University, Bangalore-560001, Karnataka, India
Abstract:- Titanium and its alloys exhibit several unique properties and have been widely used in the field of chemical industry, aviation, aerospace, marine and medical devices since 1950.Titanium and titanium alloys are widely used in aerospace field due to property of high strength to weight ratio as it saves lot of cost spent on fuel due to weight and non reactivity to adverse environmental conditions. The applications of Ti8Al1Mo1V include compressor blades, turbine discs, housing inner skin and frame for nozzle assembly of Jet engines. Literature review indicates that published information not available regarding systematic reporting of structure and properties of this alloy. Hence in this study systematically studies have been carried out on structure and properties of Ti-8Al-1Mo-1V alloy when subjected to solutionising and ageing followed by air cooling and thermal oxidation heat treatments.
In this study Titanium alloy Ti8Al1Mo1V (TA8DV) is subjected to solutionising and ageing followed by air cooling and further subjected to thermal oxidation at 600°C, 750°C and 900°C for 6 hours, 15 hours and 24 Hours time duration in each combination in a resistance furnace in presence of Air. The thermal oxidized samples are subjected to Tensile test, Micro hardness test and the cross sectioned samples are tested for microstructure in an optical microscope. Micro hardness (knoop hardness number) is more at the surface and reduces gradually to core. The maximum number achieved is 548.8 for sample To-24-900; it is revealed that the hardness increases with temperature and time duration. From Microstructure studies the effect of thermal oxidation varies from15 microns at 6 hrs duration 600°C and 150 microns at 24 hours duration 900°C temperature and it is known that the effect of oxidation varies proportional to temperature and time duration. From tensile test the yield strength and ultimate tensile strength decreases from 8% to 15 % as compared to the value of the sample in ASR condition.
Key Words: As received (ASR), Solution treated and Aged (STA), Thermal oxidation, Titanium
-
INTRODUCTION:
Titanium is the 4th abundant structural metal available on earth crust after aluminum, iron and magnesium. Titanium element was discovered in 1791. There are two allotropic forms of titanium: – Ti at 882.5°C or lower, with a closely packed hexagonal (hcp) lattice structure and – Ti at 882.5°C or higher with a body centered cubic (bcc) lattice structure. Depending on the phase structure and the content of stable element, titanium alloy is classified in to three categories: , + and . There are varieties of Titanium alloys available depending on the composition some of the alloys are Ti6Al4V, Ti8Al1Mo1V, Ti6Al2Sn4Zr2Mo, Ti10V3Fe3Al etc. Depending on the phases formed the alloys are classified as , +, titanium alloy. Titanium and its alloys exhibit several unique properties and have been widely used in the field of chemical industry, aviation, aerospace, marine and medical devices since 1950. [1]. Main physical properties of titanium and titanium alloys include: Low density and high specific strength: the density of Ti is 4.51 g/cm3 with tensile strength up to 1300MPa. The specific strength is much higher than that of aluminum and alloying steel. Good heat resistance: some new types of titanium alloys can be used for a long time at 600°C or higher, and are suitable for the aviation and aerospace heat-resistance components; Good low temperature resistance: at temperature of -196 to -253°C, titanium maintains relatively good ductility and toughness. These make Ti to be an ideal material for cryogenic vessels and tank equipments; Good corrosion resistance: Ti is very stable among many media. For example, Ti is corrosion resistant in the medium of oxidation, neutral and weak reduction. However titanium also has some drawbacks along with aforementioned advantages which are Low wear resistance: the low surface hardness of titanium makes the adhesive wear easy to occur. Low oxidation resistance at high temperature: titanium shows a strong tendency of oxidation at a temperature of 350°C or higher. High cost: the price of titanium is 5-10 times higher than that of steel. [1]. Ti8Al1Mo1V is considered which comes under near alloy, which was initially developed as super alloy for engine use principally as forgings. Ti8Al1Mo1V alloy contains a relatively large amount of alpha stabilizer, aluminum and Fairley small amounts of beta stabilizers, molybdenum and vanadium (plus iron as impurity). Although this alloy is metallurgically an alpha-beta alloy, the small amount of beta stabilizer in this grade(1Mo+1V) permits only small amounts of the beta phase to be stabilized, thus the alloy is also known as near alpha alloy. Although this is a near alpha alloy, an increase in tensile strength by almost 25% over that of mill annealed material can be obtained by appropriate choice of heat treatment sequence consisting of quenching followed by an ageing treatment.[9]. The yield strength, the ultimate tensile strength and the elongation depend strongly on the solutionising temperature [10]. Many non metallic elements are used to enhance the titanium alloy surface to improve its Tribological properties, which can form a hardened, interstitially enriched alpha-case layer with or without an outer surface layer of hard compound. [7]. The thermal oxidation process is one of the most important advances in the field of surface engineering of Ti- based materials due to its capability of enhancing the Tribological properties of Ti alloys [1]. Ti-6Al-4V alloy treated using thermal oxidation exhibited low coefficient of friction and low wear rate, which is attributed to both the formation of a useful oxide and hardened diffusion layer. Many non metallic elements are used to enhance the titanium alloy surface to improve its
Tribological properties, which can form a hardened, interstitially enriched alpha-case layer with or without an outer surface layer of hard compound. [2].Thermal oxidation is one of the widely used thermo chemical treatment for titanium alloys. In the process oxygen is incorporated in to the surface layers of titanium base alloys at elevated temperatures and yields various combinations of improved properties. In principle it is possible to improve the surface hardness, wear resistance and fatigue resistance and improve the appearance of the surface of treated parts.
-
EXPERIMENTAL DETAILS:
In this study Titanium alloy Ti8Al1Mo1V (TA8DV) is subjected to solutionising and ageing followed by air cooling and further subjected to thermal oxidation at 600°C, 750°C and 900°C for 6 hours, 15 hours and 24 Hours time duration in each combination in a resistance furnace in presence of Air. Titanium alloy received in the form of Rectangular bar of 45mm*50mm*500mm is cut into required dimensions. The cut alloy sample is analyzed for Chemical Composition via chemical analysis method. The composition results obtained are presented in Table1.
The cut pieces of alloy are cleaned thoroughly using cleaning agent and applied two layers of protective coating before loading to furnace for solutionising heat treatment. The alloy pieces are subjected to solutionising heat treatment at 899 to 1010 ºC for 1 hour followed by stabilizationageing) treatment at temperatures of 595 ºC for 8 hours followed by air cooling in a resistance furnace. Further the solutionised, aged and air cooled specimens (designated as STA) are machined to prepare specimens for Tensile test, wear test, micro hardness test and microstructure studies.
The prepared specimens are subjected to thermal oxidation in presence of air in a resistance furnace at 600°C, 750°C and 900°C temperatures for durations of 6 hours, 15 hours and 24 hours each. The thermally oxidized samples are designated as To-6-600, To-6-750, To-6-900, To-15-600, To-15-750, To-15-900, To-24-600, To-24-750, To-24-900.
-
Microstructure Studies:
The thermally oxidized samples are sectioned and mounted in a thermosetting compound. The mounted samples are grinded using SiC emery papers of grades 80,100,220,320,400,600 to get smooth surface and the samples are polished using 0.05µm alumina polishing medium. The polished surfaces are thoroughly washed and etching was carried out using krolls etchant as per ASTM E0003-01. The samples are studied under leica vertical metallurgical microscope and the images are captured. The Microstructures obtained for different conditions of thermal oxidation heat treatment are presented in Figure 1.
-
Micro hardness Test:
The samples prepared for microstructure studies are polished and Microhardness is measured at different depth from surface at a load of 100gmforce in Buhler Microhardness Tester as per ASTM 0384-9 and the results are presented in Table 2.
A comparitive graph is plotted representing microhardness at different depth from the surface for different duration and time of thermal oxidation heat treatment which are presented in Figure 2.
-
Tensile test:
The thermally oxidized specimens are subjected to Tensile Test in Tinus olsen universal testing machine and the results are presented in table 3. The specimen was prepared as per ASTM standard with diameter of specimen is 4mm, gauge length is 20 mm. The tensile test was carried out as per ASTM E8 standards and yield strength, ultimate tensile strength and percentage elongation of all the titanium alloy samples are determined.
-
-
RESULTS AND DISCUSSION:
The alloy in As Received condition designated as ASR was analyzed using chemical analysis method and the composition percentage values are as per standard alloy composition of Ti8Al1Mo1V alloy.
DESCRIPTION: SAMPLE FROM BAR
CONDITION: SOLID METAL TEST SPECIFICATION/METHOD: TA8DV
TEST RESULTS: CHEMICAL ANALYSIS
Table 1. Chemical composition of Titanium alloy Ti-8Al-1Mo-1V
SL NO
ELEMENTS
VALUES OBTAINED (%)
SPECIFICATION REQUIREMENT
1.
ALUMINIUM
7.39
7.35-8.35
2.
VANADIUM
0.98
0.75-1.25
3.
MOLYBDENUM
1.00
0.75-1.25
4.
IRON
0.04
0.30 MAX
5.
CARBON
0.01
0.08MAX
6.
TITANIUM
REMAINDER
-
Microstructure study:
The microstructures obtained from the microscopic study are presented below. Figure 1(a) is the microstructure of Thermally oxidised sample at 600°C for 6 hrs where in the formation of oxidised surface is up to depth of 15 to 25 microns. Figure 1(b) represents the microstructure of Thermally oxidised sample at 750°C for 6 hrs where in the formation of oxidised surface is up
to depth of 45 to 55 microns from the surface. Figure 1(c) represents the microstructure of Thermally oxidised sample at 900°C for 6 hrs where in the formation of oxidised surface is up to depth of 90 to 100 microns from the surface.
Figure 1(d) represents the microstructure of Thermally oxidised sample at 600°C for 15 hrs where in the formation of oxidised surface is up to depth of 60 to 80 microns from the surface. Figure 1(e) represents the microstructure of Thermally oxidised sample at 750°C for 15 hrs where in the formation of oxidised surface is up to depth of 80 to 100 microns from the surface. Figure 1(f) represents the microstructure of Thermally oxidised sample at 900°C for 15 hrs where in the formation of oxidised surface is up to depth of 100 to 120 microns from the surface.
Figure 1(g) represents the microstructure of Thermally oxidised sample at 600°C for 24 hrs where in the formation of oxidised surface is up to depth of 60 to 80 microns from the surface. Figure 1(h) represents the microstructure of Thermally oxidised sample at 750°C for 24 hrs where in the formation of oxidised surface is up to depth of 100 to 120 microns from the surface. Figure 1(i) represent the microstructure of Thermally oxidised sample at 900°C for 24 hrs where in the formation of oxidised surface is up to depth of 120 to 160 microns from the surface
microstructure of TO-6-600 at 500X(a)
microstructure of TO-6-750 at 500X(b)
microstructure of TO-6-900 at 500X(c)
microstructure of TO-15-600 at 200X(d)
microstructure of TO-15-750 at 500X(e)
microstructure of TO-15-900 at 500X(f)
microstructure of TO-24-600 at 100X(g)
microstructure of TO-24-750at 100X(h)
microstructure of TO-24-900 at 100X(i)
Figure 1.Typical microstructure of Ti-8Al-1Mo-1V alloy subjected to different cycles of heat treatment indication the effect of oxidation from surface.
The higher the temperature and higher the duration of oxidation gives better oxidised surface as it gives better time for the oxygen to get dissolved in to the surface and the maximum depth of oxidised surface obtained is for thermally oxidised sample at 24 hours duration and 900°C. From this it is known that the effect of oxidation varies proportional to temperature and time duration.
-
Microhardness:
Microhardness (knoop hardness number) is more at the surface and reduces gradually to core due to formation of alpha casing on the surface. The maximum number achieved is 548.8 for sample To-24-900; it is revealed that the hardness increases with temperature and time duration. In samples oxidised at 750°C for 6 hour duration the surface microhardness is comparatively less as compared to microhardness at depth of 25 microns and 50 microns from the surface due to formation of brittle surface which peels off. Same is the case with samples oxidised at 900°c for 15 hours duration and samples oxidised at 750°c, 600°c for 24 hours duration. The values obtained from microhardness test for different samples are presented in Table 2.
Table 2. Microhardness of Ti-8Al-1Mo-1V alloy subjected to different cycles of heat treatment at different depth from surface.
Depth in Microns
KHN forTO 900°C for 6 hours
KHN forTO 750°C for 6 hours
KHN forTO 600°C for 6 hours
0
383.1
320.2
445.5
25
316.6
377.9
408.7
50
289.7
536.0
403.0
100
264.0
412.6
390.2
150
247.9
404.9
364.6
200
244.3
328.7
369.3
250
230.6
306.4
346.0
Depth in Microns
KHN forTO 900°C for 15 hours
KHN forTO 750°C for 15hours
KHN forTO 600°C for 15 hours
0
460.2
487.6
475.4
25
489.4
404.9
428.6
50
559.8
363.0
424.5
100
428.6
335.7
410.6
150
376.2
332.9
401.1
200
358.2
326.0
393.8
250
334.3
319.2
362.4
Depth in Microns
KHN forTO 900°C for 24 hours
KHN forTO 750°C for 24 hours
KHN forTO 600°C for 24 hours
0
548.8
457.8
377.6
25
480.2
538.9
445.5
50
393.8
430.6
384.8
100
366.3
349.0
332.9
150
323.2
316.6
316.6
200
297.8
312.7
338.6
250
272.2
319.2
346.0
600
500
400
300
200
100
KHN forTO 900°C for 6 hours
KHN forTO 750°C for 6 hours
KHN forTO 600°C for 6 hours
0
0 25 50 100 150 200 250
Figure 2(a) Microhardness for thermal oxidised specimens at 600,750 and 900°C for 6 hours duration
600
500
400
300
200
TO 900°C for 15 hours
TO 750°C for 15hours TO 600°C for 15 hours
600
500
400
300
200
TO 900°C for 15 hours
TO 750°C for 15hours TO 600°C for 15 hours
100
0
100
0
0 25 50 100 150 200 250
0 25 50 100 150 200 250
Figure 2 (b) Microhardness for thermal oxidised specimens at 600,750 and 900°C for15hoursduration
600
500
400
300
200
TO 900°C for 24 hours
TO 750°C for 24 hours TO 600°C for 24 hours
600
500
400
300
200
TO 900°C for 24 hours
TO 750°C for 24 hours TO 600°C for 24 hours
100
0
100
0
0
25 50 100 150 200 250
0
25 50 100 150 200 250
Figure 2 (c) Microhardness for thermal oxidised specimens at 600,750 and 900°C for 24 hours duration
Graph is plotted for microhardness values for different conditions of thermal oxidation heat treatment against depth from surface is represented in Figure 2. Figure 2 (a) indicates the microhardness number is higher for the alloy sample oxidised at 750°c for 6 hours at depth of 50 microns from surface. For other two temperatures and durations of thermal oxidation the values of microhardness values follows linear path and it decrease from surface to core.
Figure 2 (b) indicates the microhardness number is higher for the alloy sample oxidised at 900°c for 15 hours at depth of 50 microns from surface. For other two temperatures and durations of thermal oxidation the values of microhardness values follows linear path and it decrease from surface to core.
Figure 2 (c) indicates the microhardness number is higher for the alloy sample oxidised at 900°c for 24 hours at surface. For samples oxidised at 750°c and 600°c for 24 hours duration the maximum microhardness value obtained at depth of 50 microns from surface and follows linear path and it decreases from surface to core.
-
Tensile test:
The results obtained from tensile test for the samples subjected to thermal oxidation at different durations and at different temperatures are presented in Table 3. The samples subjected to thermal oxidation at 600°c for 6 hours, 15 hours and 24 hours duration shows an increase in yield strength by 6-7% as compared to the respective property of the alloy in As received condition and there is a decrease in yield strength for the samples subjected to thermal oxidation at 750°c and 900°c for durations of 6 hours, 15 hours and 24 hours by 0.5% to 24.72%. There is an increase in yield strength by 4.9% for the alloy sample in Solution heat treated, aged followed by air cooled specimen as compared to the respective property of the alloy in As received condition.
Ultimate tensile strength increases by 5.8% to 6.6% for the samples subjected to thermal oxidation at 600°c for 6 hours, 15 hours and 24 hours duration as compared to the alloy sample in As received condition. There is a decrease in Ultimate tensile strength for the samples subjected to thermal oxidation at 750°c and 900°c for durations of 6 hours, 15 hours and 24 hours by 1.26% to 27.8%. There is an increase in Ultimate tensile strength by 8.6% for the alloy sample in Solution heat treated, aged followed by air cooled specimen as compared to the respective property of the alloy in As received condition.
A plot of tensile test results is plotted with Yield strength, ultimate tensile strength and % elongation against different conditions of thermal oxidation is represented in figure3 for better understanding.
Table 3 Tensile test results of Ti-8Al-1Mo-1V alloy subjected to different cycles of heat treatment.
SAMPLE DESIGNATION
YIELD STRENGTH
MPa
% CHANGE IN PROPERTY*
ULTIMATE TENSILE STRENGTH MPa
% CHANGE IN PROPERTY*
% ELONGATIO N
% CHANGE IN PROPERTY*
ASR
965.67
0
992.45
0
23.7
0
STA
1015.7
+4.92
1086.1
+8.6
17.6
-34.65
TO-6-600
1034.8
+6.68
1062.5
+6.59
15.7
-50.9
TO-6-750
960.5
-0.538
980.08
-1.26
20.6
-15.04
TO-6-900
876.93
-10.11
907.84
-9.3
15.1
-56.95
TO-15-600
1043.6
+7.46
1074.8
+7.66
14.9
-59.06
TO-15-750
905.72
-6.62
949.76
-4.49
19.7
-20.3
TO-15-900
835.52
-15.57
886.58
-11.94
11.5
-106.0
TO-24-600
1034.5
+6.65
1054.5
+5.88
17.6
-34.65
TO-24-750
922.6
-4.66
930.39
-6.67
15.1
-56.9
TO-24-900
774.26
-24.72
776.45
-27.8
5.39
-339.7
*As compared to respective property value of alloy in ASR condition: Yield strength: 965.67MPa, Ultimate Tensile Strength:
-
and Elongation % 23.7
1200
1000
800
YIELD STRENGTH MPa
1200
1000
800
YIELD STRENGTH MPa
600
400
200
ULTIMATE TENSILE STRENGTH
MPa
% ELONGATION
600
400
200
ULTIMATE TENSILE STRENGTH
MPa
% ELONGATION
0
0
Figure 3. plot of variation of Yield strength and ultimate Tensile test results of Ti-8Al-1Mo-1V alloy subjected to different cycles of heat treatment with respect to time and temperature.
-
-
CONCLUSIONS:
-
The results of systematic investigation carried out on structure and properties of Ti-8Al-1Mo-1V alloy subjected to different cycles of thermal oxidation heat treatment indicate that:
-
Micro hardness (knoop hardness number) is more at the surface and reduces gradually to core. The maximum number achieved is 548.8 for sample To-24-900; it is revealed that the hardness increases with temperature and time duration.
-
From Microstructure studies the effect of thermal oxidation varies from15 microns at 6 hrs duration 600°C and 150 microns at 24 hours duration 900°C and it is known that the effect of oxidation varies proportional to temperature and time duration.
-
From tensile test the yield strength and ultimate tensile strength increases from 6% to 7% as compared to the value of the sample in ASR condition and there is a decrease in yield strength for the samples subjected to thermal oxidation at 750°c and 900°c for durations of 6 hours, 15 hours and 24 hours by 0.5% to 24.72%. There is a decrease in Ultimate tensile strength for the samples subjected to thermal oxidation at 750°c and 900°c for durations of 6 hours, 15 hours and 24 hours by 1.26% to 27.8%.
It is hoped that the results of this investigation is useful for engineers and researches working in the field of Titanium alloys and applications.
REFERENCES:
-
Plasma surface metallurgy Z. Xu and F. F. Xiong, science press, Beijing and Springer Nature Singapore Pte Ltd.2017
-
Experimental study on the dynamic mechanical properties of titanium alloy after thermal oxidation Xiaoyan Niu, Yingjie Yu, Lianhua Ma, Liangbiao Chen
-
Oxidation of Pt-7M and OT4-1 Titanium alloys in Air G. G. Maksimovich, V. N. Fedirko, and A. T. Lizun
-
Specific features of the oxidation of complex titanium alloys in the As-cast and Recrystallized states N. Yu.Poryadchenko, I. V. Orysch, M. M.
Kuzmenko, N.D. Khmelyuk, M.E. Holovkova, L. D. Kulak and M.P. Brodnikovskyi
-
surface hardening of titanium by thermal oxidation W. YAN, X.X. WANG Materials Science and Engineering, Zhejiang University, Hangzhou 310027, peoples republic of china
-
Influence of the Nature of Alloying Elements on the Adherence of Oxide Films Formed on Titanium Alloys A. M. Chaze and C. Coddet
-
Thermal Oxidised Coating on Surface of Titanium Alloy for improvement of Tribological Properties in Vacuum Yong Liu, Zhuyu Ye, Dezhuang Yang, Shiyu He Space Materials and Environmental Engineering Lab., Harbin Institute of Technology, Harbin 150001, china
-
Effect of Prior Oxidation on Tensile Properties of Bare and Al3Ti Diffusion Aluminide Coated Near Titanium Alloy Titan 29A Chandrakanth Parlikar. Md Zafir Alam, Dipak K. Das
-
The effect of heat treatment on the mechanical properties of the alloy Ti-8Al-1Mo-1V P. J. Fopiano and C.F. Hickey, Jr. Army Materials and Mechanics Research center Watertown, Massachusetts 02172
-
Microstructure and Strength of Solution Treated Ti-8Al-1Mo-1V S.J. Vijaykumar, E.S.K. Menon, S. Banerjee and R. Krishnan. Metallurgy Division, Bhabha Atomic Research Centre, Trombay, Bombay-400085.
-
Studies on Mechanical and Tribological Properties of Titanium Alloys Unpublished Thesis work By K. C. Santhosh, under guidance of Dr. B. K. Muralidhara, Bangalore University, Bangalore