
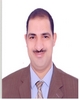
- Open Access
- Authors : Mohammed, A. S., Mohamed, O. M., Al Najjar, A., And Awwad, A. H.
- Paper ID : IJERTV12IS110196
- Volume & Issue : Volume 12, Issue 11 (November 2023)
- Published (First Online): 08-12-2023
- ISSN (Online) : 2278-0181
- Publisher Name : IJERT
- License:
This work is licensed under a Creative Commons Attribution 4.0 International License
Maximizing the Benefit of Old Center Pivot Irrigation Systems in Egypt
Mohammed, A. S., Mohamed, O. M., Al Najjar, A., and Awwad, A. H. On Farm Irrigation and Drainage,
Agricultural Engineering Research Institute, ARC, Giza, Egypt.
Owner and director of ATIC Company.
AbstractThe use of center pivot irrigation systems in Egypt has become more common in recent years due to increased coefficient uniformity, distribution uniformity, the high application efficiency, and the lack of labor with this system, which covers a large area that can be irrigated, and its ability to achieve high economic feasibility compared to other irrigation methods. Water- soluble nutrients can also be added to soil and crops grown under undesirable topographic conditions. For all of these matters, center pivot irrigation systems in Egypt have become rapidly widespread since 1982, also, due to the low quality of irrigation water in most areas of newly reclaimed lands, corrosion of tower pipes has been observed, leading to a loss of water pressure and reduce water distribution, so alternative solutions to metal tower pipes were considered to avoid this. Therefore, the aim of this research is to replace iron pipes with high-density polyethylene (HDPE) in an open field experiment in sandy soil in New Salhiya, Sharqia Governorate, and to clarify the effect of this on coefficient uniformity, distribution uniformity, the application efficiency, friction losses and economic feasibility (as a result of the replacement) in wheat crop productivity and seed quality. The results indicated that:
The coefficient uniformity under modified of center pivot system (HDPE) and center pivot system (with iron pipe) were 93.7% and 84.9% respectively, while the distribution uniformity under modified of center pivot system (HDPE) and center pivot system (with iron pipe) were 90.4%and 75.5%respectively. The application efficiency under modified of center pivot system (HDPE) and center pivot system (with iron pipe) were 90.4% and 85.2% respectively. The production yield increased with modified of center pivot system (HDPE) compare with center pivot system (with iron pipe) by ratio 19.4%. The quality of seeds under modified of center pivot system (HDPE) was excellent (used for Taqawy) but under center pivot system (with iron pipe) was only good (used for grind). Increase in revenues with modified of center pivot system (HDPE) compare with center pivot system (with iron pipe) by ratio 20.5%.
Keywords: center pivot system, High Density Poly Ethylene, distribution uniformity, coefficient uniformity, wheat crop.
-
INTRODUCTION
Irrigation systems are one of the basic components of agriculture, as these projects achieve their goals that contribute and support our countrys economy, and the large agricultural areas and giant projects established by state institutions and all major agricultural companies, and all of these projects depend on the center pivot irrigation system. Center pivot irrigation system is a long pipe whose beginning is fixed in the center of the plot of land and rotates around itself on wheels to cover an area of land in the form of a large circle whose area may exceed 150 fedden, meaning more than 630,000 meters for one circle or plot of land .In addition to It has been proven in all neighboring countries (Saudi Arabia – Libya – Sudan – Iraq) and in all their farms that iron pipes that are coated or lined from the inside with plastic materials fail – the life of the lined pipe does not exceed 5:6 years in its best condition – for several reasons that we will explain in a comparison. Pivot device lined with Pivot device to which HDPE equipment is attached late (ATIC Company). Center pivot irrigation system are popular modern irrigation systems that has been widely used in the world compared to flooding irrigation and furrow irrigation approaches. Center pivot irrigation system has some advantages, as lower labor costs, more efficient water use, and less soil tillage (New and Fipps, 1976). Many of farmers in the world are adopting advanced irrigation systems (Center pivot irrigation system) to increase yield (Gathala et al., 2020; Levidow et al., 2014; Reportlinker, 2021). Farmers are encouraged because of directly and easily way to increase crop productivity by this system (German and Parker, 2018). In Zambia, for example, the number of Center pivot irrigation system has continued to grow over the last fifteen years (German et al., 2020). The government's want to increase yield and improving the economy has lead about reason policies for agriculture which have led to an increase of capital into agriculture (infrastructures of agricultural and advanced equipment of irrigation) (Li and Wang, 2016; UNCTAD, 2011). These led to the adoption of Center pivot irrigation system in farm lands that used in the past traditional irrigation (furrow or flood) making yield more water-efficient and more productive. In addition, woodland and shrubland have been go to new Center pivot irrigation system-irrigated farm land (German et al., 2020). The area which irrigated by sprinkler irrigation systems has increased for better meet the water requirements of crop and increase the application efficiency of water and the production. For example, sprinkler irrigation systems as about 23% of the 3.5 Mha of irrigated land in Spain. One of the different types of sprinkler irrigation
systems is center pivot which has several advantages like the low of invest cost compared with fixed sprinkler system, the high automation and the high application efficiency of water. Due to these reason, their use has become popular around the world (Allen et al., 2000). Thus, center pivot system is used in about 3240% of the irrigated land in many Spanish Irrigation area (MAGRAMA, 2011). In USA, the land irrigated by center pivot system has increased by 50% from 1986 to 1996 (Evans, 2001), while it accounted for 83% of the sprinkler systems in 2008, it means about 47% of the 22.2 Mha of irrigated land (USDA, 2008). (Thompson et al. 1993) said that during fixed sprinkler irrigation a total amount of energy equivalent to 24% of the net radiation was go from the plant environment to the water droplets as they warmed during fling and after they impacted the canopy and land. This leads to the losses by evaporation with sprinkler irrigation water during and after the irrigation. This water evaporation modifies the crop microclimate. A reduce of air temperature and air vapor pressure deficit has been found (Cavero et al., 2009).
Abd El-Wahed and Atef (2012) evaluated the effects of operating pressure (P), height of sprinkler above the ground surface (H) and spacing between sprinklers (S) on the uniformity parameters [(, Distribution uniformity (DUlq) and coefficient of uniformity (CU) coefficient of variation (CV)] under center pivot system. The quantitative variables were (P20, 40 and 60), (S200, 250 and 300) and (H150, 175 and
-
The obtained values of CU and DU were higher under the highest P, closer Sand higher H. In contrast, CV was lower under the highest P, closer S and higher H. Both CU and DUlq were increased with increasing the P and S, P and H and decreasing S with an increase H. While the CV decreased with increasing the P and S, P and H. Also, decreasing Sand increase H. The highest CU values were recorded when the center pivot was operated under (P60, S200 and H200) and (P40, S200 and H200) without significant differences between them. Also, the highest DU and the lowest CV were recorded when the center pivot was operated under (P40, S200 andH200). So, it is recommended to operate the center pivot at (P40,S200 and H200) to save the pumping costs in studied area and similar conditions. Center pivot irrigation system is often preferred by farmers due to its automation possibilities and better for them (Hanson and Orloff, 1996 and Dechmiet al., 2003); low requirements of labor and ability to irrigate large area (Kincaid, 2005); easy for operation and has the capacity to achieve highly uniform and efficient irrigation results in saving of water and high farm profitability (Tarjuelo et al., 1999). The uniformity coefficients are often determined from measurements with cans which collect the water in located above the crop or on bare soil (Mateos et al., 1997). There are two methods to measure the uniformity, Coefficient of uniformity and the distribution uniformity. Distribution uniformity (DU) is usually defined as a ratio of the smallest accumulated depths in the distribution to the average depths of the whole distribution. The largest depths could also be used to express DU, but since the low values in irrigation are more critical, the smallest values are used. Coefficient of uniformity (CU) is a one of the first criteria defined to express uniformity. This coefficient is derived from catch-can data assuming that the catch-cans represent the same area. It is a measure of the absolute difference from the mean divided by the mean. (Burt
et al., 1997). Distribution uniformity is the areas which receive the least of irrigation water by look on the low quarter (DUlq). They suggested the DUlq is expressed as a decimal. So, both CU and DUlq coefficients give complementary information. Uniformity is increased when the two coefficients (CU and DUlq) are closer (Ort´zet al., 2010).
Moazed et al. (2010) studied the effect of space between the sprinklers on CU under fixed irrigation system. Also, (Clark et al., 2003) studied the effect of space between the sprinklers on CU under center pivot system. They found that the elongated spacing between sprinkler decreasing CU value. Distribution uniformity of water increases when the height of sprinkler is increased (Alazba et al., 2004). Increased height gives a larger wetted diameter for the same nozzle of sprinkler type and size, and consequently the overlap percentage (%) is increased and the application uniformity of water along the lateral is improved (Allen et al., 2000). Increasing the height of sprinkler usually produces better irrigation uniformity for a direction and wind speed, but it also increases evaporation losses and drift (Faci et al., 2001).
-
-
MATERIALS AND METHODS
The experiment was done in season (2022-2023) under open field conditions in sandy soil at New Salhia, Sharqia Governorate, Egypt, it is located between latitudes of 30°35' 18.11'' N – 31°51'25.06'' E on center pivot irrigation systems to maximize the benefit of old center pivot irrigation systems by changing the water flow through a pipe made of a different material in the manufacturing material (iron) to HDPE material, HDPE is the first letters of High Density Poly Ethylene, which means high-density polyethylene, to study the effect of this replacement on application efficiency, distribution uniformity, friction losses, coefficient uniformity, productivity, and return from growing the wheat crop. This research was carried out in partnership between the Agricultural Engineering Research Institute and ATIC Company, which were able to contribute to supporting this method of irrigation by rationing and conserving water while maximizing the profitability or productivity of the agricultural project. Agriculture projects, as we mentioned previously, depend on irrigation with pivot devices, and this was our first goal rationing this water – whether the water is exposed to problems of shortage and deficit or is abundant – as this rationing and proper and direct direction of crops without wasting water with preserving and even increasing the yield is the primary goal of this research, so an action has been done to modification the center pivot irrigation system with HDPE system which consists of the main pipes made of this material and a group that is coordinated from reinforced and treated plastic and metal materials and plastics. The equipment is suspended from a pivot irrigation device parallel to the pipe of the device (Fig.1).
-
Some physical and mechanical properties
Table (1) presents the soil bulk density data obtained experimentally from the study area where the soil bulk density was evaluated using following the method specified by Black (1965). Following the method of Peters (1965) the field capacity was determined and the permanent wilting point was determined by Stakman and Vander Hast (1962) through pressure membrane testing, in accordance with the procedures.
The soil under investigation was mechanically analyzed according to Black (1965) using established standard protocols. Table (1) also showed some of the main physical and mechanical properties of the soil representing the selected area. The soil chemical properties of the field experiment is
presented in table (2) and table (3) showed the irrigation water chemical characteristics at the study region.
A. Friction Losses
A large amount of research has been conducted over the past years to create different formulas that can calculate the
friction losses in pipes. Most of this work has been developed based on experimental data. Friction losses in pipes is affected by a number of factors, such as the internal roughness of the inner surface of the pipe, the size of the inner diameter of the pipe, the viscosity of the fluid, as well as the change in height between the ends of the pipe and the length of the pipe through which the fluid moves, so the Darcy-Weisbach equation is now accepted as the most accurate in calculating friction losses in pipes. Although it is more difficult to calculate and use than other equations that calculate friction losses with the introduction of computers, it has now become the standard equation for calculating fluid hydraulics.
Where,
hf : head loss (m), f: friction factor, L: length of pipe work (m), D : inner diameter of pipe work (m), V: velocity of fluid (m/s), g := acceleration due to gravity (m/s²).
Before the developed of personal computers, Hazen- Williams equation was very famous among piping engineers because of its simple mathematical properties. However, the Hazen-Williams results depend on the value of the friction factor, CHW, used in the equation, and the Hazen-Williams equation only gives good results when the fluid is water and can produce significant inaccuracies when this is not the case, the equation of Hazen-Williams is:
Where,
hf : head loss (m), L: length of pipe work (m), D: inner diameter of pipe work (mm), CHW: Hazen-Williams coefficient, Q: Flow rate (l/s).
-
Evaluation of Uniformity
Figure (2) showed the planning of cans location under center pivot systems and showed that under the stand, the evaluation cans were placed 5 meters (A) between the cans inside each tower, bringing the total number of cans to 80 cans apart in a row extending from the center of the pivot device directly to the edge of the circle and another row also extending from the center of the pivot device with an angle of 45 degrees between two rows (B). When starting the irrigation device, water must not enter the evaluation cans until the pressure and speed of the device reach the maximum. Each can was 15 cm in diameter and 20 cm in height. Each can represent an irrigation area as part of a field, so the volume captured by each can is the water depth multiplied by the area represented. The cans were placed across the side road. The can locations were level and far enough away from the side to ensure no water could get into the cans. When the central (lateral) axis is passed over all the cans, the water volumes in each can are measured and recorded for further processing. There are many equations that calculate the Evaluation of Uniformity (istribution uniformity and coefficient of uniformity) including these equations:
B. Coefficeient of Uniformity (CU)
The modified equation of Heermann and Hein (1968) given by (ASAE, 2001) was used to calculate the center pivot coefficient of uniformity (CU).
Where,
Ds: water depth (mm) collected by a catch can to a distance S from the center pivot. s: a subscript that denotes the position to a distance S. n: number of the catch can.
-
Distribution uniformity (DUlq)
The equation of Merriam and Keller 1978 was used to calculate low quarter irrigation distribution uniformity (DUlq).
Where,
ADC25: lowest quarter of the average water depth of a group of catch can measurements.
ADC: total average water depth of a group of catch-can measurements.
-
Description and components of center pivot system.
Table (4) and (5) showed that graduation in diameter lengths from 200 mm up to 110 mm under modified center pivot system (HDPE) and diameter are fixed 153.21 mm under old center pivot system (with iron pipe), where the axis of center pivot systems are 417 meters long, has 10 spans (where a span is defined as the pipeline and the supporting truss between two supporting towers), each span being about 43 meters. The total irrigated area is about 125 feddan. Fixed sprinkler panel
sprinklers (FSPS) were used along the spans with the overhang from the axis of the system.
While the modified center pivot irrigation system (HDPE) consists of a number of high-density polyethylene (HDPE100) pipes along the length of the device. They are connected by heat fusion welding to machines designated for this purpose to form a single-unit pipe in each tower.
Then suspended with metal clamps parallel to the main pipe of the device and of the same length. This equipment is characterized by (it is the only irrigation method that this allows it to be characterized by the ability to control the rise and fall of the nozzles according to the age and length of the plants grown under the pivot device.
The HDPE pipe is designed to withstand the pressure of irrigation water at the highest pressure levels (8 bar: 10 bar), and the pipe ends with a washing valve at the end of the devices connection (Over Hung), and the pipe has holes for each distance that determines According to Computer Sheet) and from each hole a (¾ inch) elbow tube emerges in the
shape of the letter U. It is installed according to the technical standards for the connection and installation processes, in particular, and at the end of it hangs a (¾ inch) high pressure hose of two different lengths in a row, in two parallel rows on either side of the pipe and perpendicular to the pipe, and at the end there are sprinkles nozzles they are calibrated and arranged according to the programming of the equipment and the materials used in its installation, taking into account the technical and engineering principles in the components and specifications of the equipment elements, in a way that maintains the balance and suitability of the movement of the device after installing the equipment and its accessories, in a way that does not affect the movement of the device and does not cause differences in the dynamics of that movement and the ideal distribution of water pressures. Whether the pivot is with or without equipment, the highest and strongest materials have been chosen so that the equipment will last for years and long agricultural seasons.
The HDPE1000 pipe has a wall thickness twice the wall thickness of the iron pipe in the pivot. Therefore, it is obvious that the inner diameter of the polyethylene pipe is smaller than the inner diameter of the iron pipe, even if their outer diameter is the same, because the calculations, equations, and dealing numbers that relate to the flow and pressure of water are on the scale of the inner diameter. The pipe has no regard to the geometric outer diameter. This fact has many advantages related to the lifespan and weight of the pipe, as the weight of a polyethylene pipe filled with water is less than the weight of an iron pipe filled with water.
Therefore, the equipment is a group of high-density polyethylene pipes (withstands a pressure of 10:8 bar) that are installed with calculations of the length and diameter, then moving to another length with a smaller diameter or with an equal diameter along the length of the pipe, and so on according to engineering equations and rates governed by water conduction, speed, pressure, and the resulting loss. On the friction of water with the pipes of the pivot irrigation device as it flows through it. This is followed by the process of calculating the hole distances in the pipes and finally installing the nozzles with their different sizes and openings, all within a Computer Sheet that specifies all the specifications and details of the installation.
-
Wheat crop
Wheat crop was cultivated in growing seasons 2022 – 2023. The planting process commenced on 25 November 2022 and harvesting was carried out after a duration of 170 days (on 15 April 2023). To support the growth of the crop, nitrogen fertilizers were introduced into the irrigation water throughout the growing season. The application followed the recommended doses provided by the Ministry of Agriculture in Egypt.
-
-
RESULTS AND DISCUSSION
-
Reasons for using polyethylene material
Six reasons for using polyethylene material which are
1) Polyethylene is basically chemically inert, so its pipes do not rust or corrode, regardless of the quality or composition of the liquid or gas it transports. This system resists chemical influence from surrounding factors, so there is no need for a
protective layer for the polyethylene pipe, 2) the thermal welding connection system ensures the creation of a homogeneous system. The fusion welding of this system with the welding machine designated for this purpose at the installation site is very strong, and unlike other types of joints and connections such as rings, arrow sleeves, lockers and other mechanical fastening systems, there is no and does not result from welding. Fusion means a risk of leakage resulting from poor connection, as each group of pipes becomes a tower in the pivot as a single pipe, 3) Optimum flow thanks to the smooth surface inside the pipes. The inner surface remains smooth and constant, no matter how long the pipe is and how long the system runs, due to the absence of the possibility of accumulation of fungi that impede flow due to the biologically inert nature of PE, 4) The polyethylene system has adequate resistance to fluctuations in ground temperature and weather, as well as what is known as resistance to geological conditions, especially in the desert with varying temperatures between summer and winter and day and night, 5) Low capital for complete operations with this type of pipe, low installation costs, ease of transportation, replacement and exchange of parts, as well as ease of changing or transporting between sites of use and 6) A long and proven record of excellent performance for nearly 50 years, with spread throughout the world and in all areas of transporting gas, water, liquid waste, and…, the life of the HDPE high-density polyethylene pipe extends for very long years (there is) a global scientific table – Resulting from laboratory tests and various site tests – to calculate the life of the pipe according to the factors and conditions of its use or operation.
-
The reason for replacing the metal iron pipe with HDPE The aim of this suspended equipment is changing the path
of irrigation water, taking advantage of the devices chassis
and transmission and movement group, while avoiding the operation of the devices main iron pipe in the event. The irrigation water contains heavy metals such as iron or other elements that are added to the irrigation water, such as acids and fertilizing compounds, which directly and negatively affect the efficiency of the devices main ion pipe. Likewise, figure (3) showed that when the pipe has become more rusty (what is known as a corrosion or baroma) with many holes in the pipes body as a result of its operation for many years, as well as problems with pipe joints such as screws, gaskets, flanges, water outlets, etc., in addition to what occurs from the reactions of iron over the agricultural seasons due to fertilization with acids, chemicals, etc. During our observation of center pivot irrigation for many years, we may notice that the inner wall of the body of the main iron pipe changes completely from 4 to 5 seasons – that is, within two to two and a half year – regardless of the type and source of irrigation water, and the change occurs with different amounts of burrs, rust, or fungi that it is usually attached to the iron metal or to the inner lining of the pipe, which makes the inner diameter vary along the length of the pipe. This is reflected in the nature and calculations of water flow. The device loses the ability to regulate the distribution and pressure of water, which negatively affects the uniformity of the crop and its productivity. As time passes and the life of the devices operation, the problem gets worse.
-
Friction losses
The pipe of the pivot device through which the irrigation water flows is made of iron, and this metal causes the irrigation water to lose a large amount of pressure, so much so that in some devices the pressure at the end of the device is very weak, and consequently, this makes the crops at the end of the device weak in production which reduces the quantity and affects the quality of the agricultural product, Therefore, we investigated making the water flow through a pipe made of a different material in the manufacturing material (HDPE), so table (6) showed that the loss in irrigation water pressure is much less compared with iron material to avoid the next three problems with iron material : (1) either long use over many agricultural seasons over the life of the device, or (2) special formations in irrigation water and the heavy metals it naturally contains that cause corrosion of the pipe, or (3) excessive addition of acids and chemicals to that water, which leads to the pipes iron reacting with these chemicals. Thus, it becomes clear that these problems negatively affect the efficiency of the devices main pipe, which is usually made of galvanized iron or even lined, Other than that the metal rusts or its material reacts with fertilizing elements and various irrigation water formulations or components. (Fig. 3). Therefore, thought was given to manufacturing high-density polyethylene pipe (HDPE).
We made a comparison between the pressure at the end of the iron pipe and the polyethylene pipe, and the result of our studies, scientifically, practically, in the field, and statistically, in numbers, was that polyethylene achieves our goals. To confirm these results, we relied on the studies of three equations for Hazen Williams & Darcy Weisbach & Manning Churchill. They studied the comparison of the difference in the size of pressure loss in two different types and materials of pipes and we reviewed the difference between an iron pipe and a polyethylene pipe, data in table (7) showed that the pressure at the end of the HDPE pipe was not affected to a significant extent, as it was affected in the case of the iron pipe, which had a greater effect so it was achieved through their studies and our review that what we searched for is evident from table No. 7. Accordingly, we manufactured what we called the HDPE equipment, where we manufactured a pipe made of high-density polyethylene (HDPE), it is suspended by a pivot and the length of the device.
-
Indicators of Irrigation Uniformity Evaluation
The characteristic of the equitable distribution of irrigation water along the length of the pivot device according to engineering equations – with calculations of conductance, pressure, length and internal diameter of the pipe – according to what the equipment with decreasing or equal pipe diameters produces of uniformity of pressure and reduction of losses
throughout the length of the HDPE pipe between (end & center), and it is important It is important to mention here that the pivot device may not require pressure regulators.
-
Coefficient uniformity (%)
Figure (4) showed that the coefficient uniformity under modified of center pivot system (HDPE) was 93.7% and was
84.9 % with center pivot system (center pivot system with iron pipe) by increasing 8.8 %.
-
Distribution uniformity (%)
Figure (4) showed that the distribution uniformity under modified of center pivot system (HDPE) was 90.4% and was
75.5 % with center pivot system (center pivot system with iron pipe) by increasing 14.9 %.
-
Application efficiency (%)
Figure (4) showed that the application efficiency under modified of center pivot system (HDPE) was 90.4% and was
85.2 % with center pivot system (center pivot system with iron pipe) by increasing 5.2 %.
So it's important Developing and raising the efficiency of the Pivot irrigation device and re-operating it like new, and preserving the parts and components responsible for the devices dynamics or movement (tires / gear box / gear motor
/ cables / knees / …) in order to reduce the loads.
-
Applied water depth (mm)
Data in figure (5) showed that the deviation in actual water application about values of average water application or low quarter actual water application (which were 2.585 mm and
2.438mm respectively) under modified of center pivot system (HDPE) wasn't big so the uniformity was big.
While data in figure (6) showed that the deviation in actual water application about values of average water application or low quarter actual water application (which were 2.54 mm and
1.92 mm respectively) under center pivot system (center pivot system with iron pipe) was big compared with modified of center pivot system (HDPE) so the uniformity was small.
-
Production yield & Total Revenues for wheat crop
For all of the above, ATIC has assisted the Agricultural Engineering Research Institute at the Ministry of Agriculture in applying a comparison between two Pivot devices, one of which had HDPE equipment installed and the other was not installed in it. Both devices were planted with
wheat crops, and we made sure that the date of planting was the same and all agricultural transactions and operations, including fertilization and service. The agricultural sector is completely identical in terms of the method, quantity, and history of each operation.
Based on the data from table (8) found that production yield with pivot irrigation under the HDPE Suspended achieved 3.0975 Ton/fed compared with Center pivot (with iron pipe) which was (2.4975 Ton/fed) an increase in the quantity of the crop equivalent to 19.4% and an increase in revenues (by 3026.5 LE/fed.) equivalent to 20.5% .
The quality difference is also noted, as the wheat produced under the HDPE Suspended was chosen as (Taqawe) because they conform to the specifications and quality standards for Taqawe and seeds prepared for planting at a higher price (revenue due to the difference in quality was 206.5 LE/fed.) while under center pivot system (with iron pipe) the seeds were good and used for grind only.
-
Feasibility study and payback period for HDPE equipment with different crops
We found it necessary to clarify here the economic feasibility of installing HDPE equipment. How and when will the value invested in installing the equipment be recovered? Based on field data collected through a statistical and digital inventory, from a scientific, practical, and field study with two projects (during the four agricultural seasons and on which the study was conducted were wheat and beet crops in the Salhiya project and the peanut and potato crops in Al-Awainat), which used HDPE in center pivot irriation system and normal center pivot irrigation system were applied in Egypt by installing the equipment on a pivot area of 150 fedden, meaning that the length of the device is approximately
450 meters and data in table 4 showed the crops that took place under the equipment produced 10% to 15% increasing of the same crops produced under Pivot, for
which the HDPE equipment was not installed and data in table (9) showed the revenues of those crops and the quantity of each crop produced from growing it under the pivot without installing equipment. Therefore, the HDPE equipment works to reduce the cost and increase the return, and this is the goal (Good investment).
Data in table (9) showed that the excess quantity in the crop was evaluated at the market price in the year of agricultural production, and the result was that the increase in the yield of one agricultural season was greater than the cost of installing the HDPE equipment. We notice from the aforementioned table that the lowest revenues were peanut revenues, as revenues from the sale of the entire pivot crop amounted to 2,700,000 LE. The increase in yield was achieved in the various pivots in the processing, and we took into account an average production of 12.5%, which amounted to 337,500 LE. Therefore, the revenue achieved from the lowest agricultural season in terms of the volume of sales of the crop (peanuts) – regardless of the agricultural costs that are not mentioned. This study covered the cost and the value invested in developing the pivot was recovered in less than one agricultural season, that is, in less than six months.
Generally, the average increase in production was calculated at 12.5%, and here it represents a full net profit, as the costs of agricultural operations in the center pivot from the beginning of agricultural operations to the end of harvest are the same costs, whether in the pivot for which the Suspended was installed or the pivot for which it was not installed. Therefore, the increase in production do not bear any cost. The desired and targeted result was achieved, whether by increasing revenues, quality, or increasing the yield, as is clear from the numbers and actual results, Table No. 8 and 9.
The cost of replacing bad metal pipes with other pipes or replacing them with a fully lined pivot device is high, while in the case of HDPE equipment, maintenance and replacement are inexpensive, less than (20%), with ease of performance or installation, also the cost of the operation is less than a quarter of the value of a new device while increasing the productive life of the pivot, and the investment cost is recovered in just one agricultural season even in the lowest yielding crops, through reducing costs and increasing crop yield.
-
-
CONCLUSION
-
Visibility of the equipment and ease of maintenance: ease and speed of maintenance operations, as it does not require high human efficiency and all parts can be dismantled and installed by hand.
-
Quality: HDPE pipes made of inert and strong materials that work to withstand weather conditions and not interact with fertilization processes with acids, salts, elements and heavy metals in irrigation water, such as iron, for example.
-
The device overturns due to low tower at the beginning and end especially old devices, while HDPE Suspended is as close to a straight line as possible, unlike the structure the iron pipe of the pivot, which is low at both ends of each tower and high in the middle.
-
Old pivot devices: contain amounts of rust accumulated which impedes the flow of water and increases its resistance and thus weakens its pressure. While the HDPE pipe is characterized by a soft and smooth inner wall, which achieves water speed faster than the iron pipe.
-
Algae and fungi: HDPE pipes and components of the equipment are designed in terms of color and composition to prevent the formation of any fungi, algae, or other organisms that can create objects and masses that attach or stick to the wall of the water paths.
-
Saving: saving on the cost of irrigation water, electricity, or operating fuel, and planting time, as full maturity occurs at the ideal time, so harvesting occurs earlier With HDPE Suspended, compared with regular devices.
-
Homogeneity: The cultivation under HDPE Suspended had regular germination, with complete uniformity in the shape and size of the shoots throughout the life of the plant, and that the date of completion and completion of maturity was typical, which achieved the transition to the next agricultural season (the next crop) at the most appropriate time, emphasizing that this reduces the cost.
-
-
RECOMMENDATION
We advise companies and agencies that rent their pivot irrigation devices to others to take into account the culture and thought of the tenants and their dealings with the land and the pivot irrigation device, and this dealing requires HDPE equipment to preserve the components of the center pivot irrigation device and the land, where installing the HDPE suspended equipment achieves savings in production, fair distribution, and rationing irrigation water in old and even new pivots while reducing the cost of the amount of energy and water, as the best elements and goals of successful investment are always achieved by working to maximize profit, production, and revenues and reducing costs and expenditures (expenses) because HDPE suspended equipment achieves three main goals for center pivot irrigation, especially with the severe water shortage expected throughout the world. These goals are:
-
Increasing the useful life of new and old pivots
-
Increase and uniformity of size and yield (quantity and quality).
-
Regulating water and reducing the difference in pressure between the center and the end.
-
-
REFERENCES
-
Alazba, A.A.;Alghobari, H.M. and Alotay, A.A. (2004).Assessment of Surface and Subsurface Water Uniformities for Center Pivot. J. King Saud Univ., Agric. Sci., 16:127-136.
-
Allen, R.G., Keller, J., Martin, D., 2000. Center Pivot System Design. The Irrigation Association, VA, USA, 300 pp.
-
ASAE. (2001). Test procedure for determining the uniformity of water distribution of center pivot and lateral move irrigation machines equipped with spray or sprinkler nozzles. ANSI/ASAE Standard S436.1, American Society of Agricultural Engineers, St. Joseph, MI.
-
ASAE. (2001). Test procedure for determining the uniformity of water distribution of center pivot and lateral move irrigation machines equipped with spray or sprinkler nozzles. ANSI/ASAE
Standard S436.1, American Society of Agricultural Engineers, St. Joseph, MI.
-
ATIC Company (2020). International Agricultural Trade Centre.
-
naggar@aticconsulting.com, info@aticconsulting.com
-
-
Black, G. R. (1965). Methods of soil analysis part. I. Black, C. A (ed.), Madision, Wisconsin. pp. 374-390.
-
Burt, C. M.;Clemmens, A. J.;Strelkoff, T. S.; Solomon, K. H.;Bliesner, R. D.; Hardy, L. A.; Howell, T. A. and Eisenhauer,
D. E. (1997). Irrigation performance measures: Efficiency and uniformity. J. Irrig. Drain. Eng. 123: 423-442.
-
Clark, G. A.;Srinivas, K.; Rogers, D. H.; Stratton R. and Martin,
V. L. (2003). Measured and simulated uniformity of low drift nozzle sprinkler. Trans. ASAE 46: 321330.
-
Dechmi, F.;Playa´n, E.;Faci, J. and Tejero, M. (2003).Analysis of an irrigation district in northeastern Spain. I: Characterisation and water use assessment. Agric. Water Manage. 61: 7592.
-
Evans, R.G., 2001. Center Pivot Irrigation; Research Report. USDA-Agricultural Research Service, Sidney, MT, USA.
-
Faci, J. M.; Salvador, R.; Playa´ n, E., and Sourell, H. (2001). Comparison of fixed and rotating spray plate sprinklers. J. Irr. Drain. Eng. 4: 224236.
-
Gathala, M.K.,Laing, A.M., Tiwari, T., Timsina, J., Islam, M.S., Chowdhury, A.K., Chattopadhyay, C., Singh, A.K., Bhatt, B.P., Shrestha, R., 2020. Enabling smallholder farmers to sustainably improve their food, energy and water nexus while achieving environmental and economic benefits. Renew. Sust. Energ. Rev. 120, 109645.
-
German, L.A., Hepinstall-Cymerman, J., Biggs, T., Parker, L., Salinas, M., 2020. The environmental effects of sugarcane expansion: a case study of changes in land and water use in southern Africa. Appl. Geogr. 121, 102240.
-
German, L.A., Parker, L., 2018. The social construction of shared growth: Zambia sugar and the uneven terrain of social benefit. J. Agrar. Chang. 19, 181201.
-
Hanson, B. R. and Orloff, S. B. (1996).Rotator nozzles more uniform than spray nozzles on the center-pivot sprinklers.California Agriculture. 50: 32-35.
-
Heermann, D.F. and Hein, P.R. (1968). Performance characteristics of self-propped center pivot sprinkler irrigation system. Trans. ASAE 11:11-15.
-
Kincaid, D. C. (2005). Application rates from center pivot irrigation with current sprinkler types. Appl. Engi. Agric. 4: 605610
-
Levidow, L., Zaccaria, D., Maia, R., Vivas, E., Todorovic, M., Scardigno, A., 2014. Improving water-efficient irrigation: prospects and difficulties of innovative practices. Agric. Water Manag. 146, 8494.
-
Li, G., Wang, W., 2016. Investing in Africas agriculture: solidifying foundation for sustainable and inclusive development. Retrieved from. https://openknowledge.wor ldbank.org/handle/10986/25188.
-
M.H. Abd El-Wahed and Atef S., 2012. Performance Assessment of Center Pivot Irrigation System Under arid Areas condition (2012). Misr J. Ag. Eng., 29 (4): 1515 – 1532 M.H.
-
MAGRAMA, 2011. Encuesta de superficies y rendimientos de cultivos en Espana (ESYRCE). Ministerio de Agricultura, Alimentación y Medio Ambiente.
-
Mateos, L.; Mantovani, E. C. and Villalobos, F. J. (1997).Cotton response to non-uniformity of conventional sprinkler irrigation.Irrig Sci. 17: 4752.
-
Merriam, J. L., and Keller, J. (1978). Farm irrigation system evaluation: A guide for management, Dept. of Agricultural and Irrigation Engineering, Utah State Univ., Logan, Utah.
-
Moazed, H.;Bavi, A.;Boroomand-Nasab, S.; Naseri, A. and Albaji, M. (2010).Effect of climatic and hydraulic parameters on water uniformity coefficient in solid set systems. J. Applied Sci., 10: 1792- 1796.
-
New, L., Fipps, G., 1976. Center Pivot Irrigation. The Texas A&M University System. Available online: https://oaktrust.library.tamu.edu/handle/1969.1/86877. Reportlinker, 2021.
-
Ort´z, J. N.; de Juan, J. A. and Tarjuelo, J. M. (2010). Analysis of water application uniformity from a center pivot irrigator and its effect on sugar beet (Beta vulgaris L.) yield. BiosystemsEngineering, 105:367379.
-
Peters, D. B. (1965). Water availability in methods of soil analysis. Black C. A. (ed). American Society Agronomy Mon, (9):281.
-
Stakman, W. P. and Vander hast, G. G. (1962). The use of pressure membrane apparatus to determine soil moisture contents at Pf 3.0 to 4.2 Taclusiv Institute for land and water management research not No.159.
-
Tarjuelo, J. M.; Montero, J.;Honrubia, F. T.; Ortiz, J. J. and Ortega, J. F. (1999).Analysis of uniformity of sprinkler irrigation in a semiarid area.Agric. Water Manag.40: 315-331.
-
Thompson, A.L., Gilley, J.R., Norman, J.M., 1993. A sprinkler water droplet evaporation and plant canopy model: II. Model application. Transactions of the ASAE 36, 743750.
-
UNCTAD, 2011. An investment guide to Zambia: Opportunities and conditions. Cavero, J., Medina, E.T., Puig, M., Martinez-Cob, A., 2009. Sprinkler irrigation changes maize canopy microclimate and crop water status, transpiration, and temperature. Agronomy Journal 101, 854864
-
USDA, 2008. Farm and Ranch Irrigation Survey (2008). Vol. 3, Special Studies-Part 1 of the 2007 Census of Agriculture, AC-07- SS-1, National Agricultural Statistics Service