
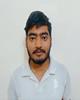
- Open Access
- Authors : Rishav Kumar , Rana Akshat , Shubham Kumar , Hariom Jaiswal
- Paper ID : IJERTV12IS050021
- Volume & Issue : Volume 12, Issue 05 (May 2023)
- Published (First Online): 18-05-2023
- ISSN (Online) : 2278-0181
- Publisher Name : IJERT
- License:
This work is licensed under a Creative Commons Attribution 4.0 International License
Lithium Ion Battery Protection System
Rishav Kumar
Department of Electrical Engineering Gurukul Kangri (Deemed to be University) Haridwar, India.
Rana Akshat
Department of Electrical Engineering Gurukul Kangri (Deemed to be University) Haridwar, India.
Shubham Kumar
Department of Electrical Engineering Gurukul Kangri (Deemed to be University) Haridwar, India.
Hariom Jaiswal
Department of Electrical Engineering Gurukul Kangri (Deemed to be University) Haridwar, India.
Abstract – The Main ideal objective of this major project is to protect the abnormality in lithium -ion battery. The purpose of this research paper to use microcontroller like ATmega328P and sensors like smoke sensor, temperature sensor to monitor the parameters like temperature, leak feasts in griding of Lithium-ion battery of Electric vehicle, and aim to protect it from undesirable condition appear during charging and discharging also with the help of solenoid valve, dangerous fire can be stopped.
Keywords – PCB Board, Heat, LCD (Liquid Cristal Display), cable Fault, sensors, Digital Data, Solenoid valve and Lithium- ion battery.
I.INTRODUCTION
The safety of lithium-ion batteries in electric vehicles is one of top priority of the automobile manufacturer industry. The main target of the paper is to decrease the risk and aim to the improvement of the protection ideas and systems. Due to Constant observance of battery parameters like temperature, gas level, and voltage, current can alert the system for any anomalous and worst condition of emergency. If in sensible case fire or any unexpected impact on the battery may cause the inner tangency of the battery which leads into inordinate warming of thebattery that leads into explosion and fire. Our good sensor-based network can keep batteries which improve battery performance healthy and life time or overall performance increases and saves valuable investment on the vehicle.
-
EXISTING SYSTEM
The automotive business is admittedly serious regarding electrical Vehicles now also the most significant rudiments of associate EV, the Battery Pack. Cost-wise, it constitutes nearly 40% of the vehicle cost. Battery pack contains the Lithium-ion cells that power the EV drivetrain and together with that, a sensible decision referred to as the EV Battery Management System BMS. The BMS monitors each cell of the battery and uses its complicated formula to calculate battery percentage, health and therefore after we extrapolate the battery management facet to an electrical vehicle, the quality gets numerous notches advanced.
Electric vehicle BMS performs a Previously some daily routine performance
-
Cell observance
-
Power improvement
-
Safety of electrical vehicle
-
Battery Charging improvement
-
Power improvement
-
Safety of electrical vehicle
-
Battery Charging improvement
-
Power improvement
-
Safety of electrical vehicle
-
Improvement Battery charging
-
-
LITERATURE SURVEY
The concept of this project model of battery protection system is comes from seeing a lot of hazardous accident happening around the surroundings as transportation are becoming important part of our daily lifestyle. Due to limited renewable source like diesel and petrol has not very long life- span so electric vehicle are starting to replace combustion engine Electrical vehicle have zero carbon emission in comparison combustion engine.
Thus, safety of EVs is most important and therefore, the combination of electrical and electronic information can contribute effectively. Increasing population and demand of safe traveling is one of necessity of any person. As India is a developing country and due to their hot weather in major part of country therefore these factors produce a problem on EVs.
-
Thus, for increasing demand and problem, we have taken review into countless research paper on EVs and their safety parameters like
-
Research on fault diagnosis system of electrical vehicle power battery based on OBD technology.
-
Review of lithium-ion battery safety concerns: the issues, strategies, and testing standards.
-
Thermal safety issues of lithium-ion batteries for electric vehicle application.
-
Battery faults analysis for electric vehicle based on voltage abnormality by combining the long short-term memory neutral network and equivalent circuit model.
-
Discovery of Li-ion battery failure and venting with Carbon Dioxide Sensors.
-
Experimental study on the unique safety strategy of lithium-ion battery integrating fire suppression and rapid cooling.
And we conclude with important point like
-
To gauge back the thermal runaway, the efficiency of gas fire extinguisher must be sensible on suppressing lithium-ion battery fire place. The primary work is to mix a gas fire ending agent (C6F12O) with the water mist system for Lithium-ion battery fire suppression, such the battery flame in initial stage is controlled by the extinguisher and there after the water mist is then applied for effective cooling of the battery.
-
To operate at higher temperature technology lithium-ion battery has an equivocal impact on the performance as well as fast capability fade and aging. Similarly, the decline of battery performance affects the results from reduction of the activity of the conductor material and lithium-ion diffusion rate within the solution and therefore the conductor material. Temperature distribution non uniformity throughout the one battery or pack of Li-ion battery is additionally important operational index which can cause chemical science imbalance over time.
-
The whole power management system IC with full- integration, high-precision and high-trust ability for battery pack of lithium ion which might monitor and defend the system is demonstrated, achieving lower application costs. The IC protects the lithium ion battery from over-voltage, over-current and over temperature once charging and discharging with 0.5m discrimination accuracy.
-
The outline of previous battery fault-experiments with problem like overheating, over charging and nail penetration all indicated the presence of dioxide within the vent-gas. At identical time, CO, H2 and VOCs were set up in several batteries abuse trials, however lacked consistency across completely different testing conditions. Considering the early presence in first effusion, sensible consistency, ability to detect cell out flow and detector feasibility, CO2 wash and-picked because present of indicator for gas venting events.
-
-
PROPOSED SYSTEM
-
PCB LAYOUT
VI.INTERNAL CIRCUIT
VII.HARDWARE
-
Micro-Controller Atmega328p
-
Temperature Sensor LM35
-
Smoke Sensor MQ3
-
Crystal 16Mhz
-
Voltage Regulator 7805
-
Display LCD16*2
-
Relay DC 5V
-
Transistor – BC547
-
Capacitor – 22pF,100uF
-
Resistor 330ohm
-
Variable Resistor – 10Kohm
-
Terminal Block Screw
-
Battery – 12v,2000mah
-
Fan 12vDC
-
Buzzer – 12vDC
-
Motor – 500 Rpm VIII.ATMEGA328P
-
The ATMEGA328P – PN may be a famous microcontroller thanks to it being a significant part within the Arduino board products. The ATMEGA328P-PN is that the8-bit reduced set instruction for computing heart of the Arduino, Uno, and Nano, in a most clock frequency of 20MHz, 32KB programmed FLASH, and 2KB of RAM. TheATMEGA328P- PN contains a handful of on-board peripherals, simultaneously with UART, SPI, timers, ADC, comparators, and a watchdog, and is housed in an enough 28-DIP packages that allow designers to design simply model their styles before committing to surface mount technology. With a temperature difference of -41°C to105°C and voltage range of 1.7V to 5.5V, the ATMEGA328 literally is a multifaceted, cost-efficient micro controller.
IX.TEMPERATURE SENSOR
LM35 is a temperature detector that labors analog signal that proportional to the immediate temperature. The output is proportional to the immediate temperature. The output voltage will directly be taken to get a temperature sensing in Celsius. The output voltage will directly be taken to get a temperature sensing in Celsius. The advantage of Im35 over Thermistor is it doesnt need any external calibration.
LM35TemperaturesensorFeatures-
-
Tag Directly in Celsius (Centigrade)
-
Linear+10-mV/°C multiplier
-
0.5°C Ensured Accuracy (at25°C)
-
Rated for Full55°Cto150°Cvary
-
Appropriate for Remote Application
-
Operates from 4V to 30V
-
Lower than 60-µA Current Drain
-
Low Self – Heating, 0.08°C in Still Air
-
Non – Linearity solely ±¼°C Typical
-
Low -Impedance Output-0.1 ohm for1-mA
X.SMOKE SENSOR
MQ- 3 module is suitable for investigator work Alcohol, Benzine, CH4, Hexane, LPG, CO. Conscious material of MQ- 3 gas device is SnO2,that with lower conduction in clean air. One time the target alcohol gas exists, the sensors conductivity is higher at the side of the gas concentration rising. MQ-3 gas sensor has high sensitivity to Alcohol, and has smart resistance to disturb of gasoline, bank, and vapor.
Identification of MQ-3 Gas device
-
Power requirements: five VDC @ ~160 mA (heater on)/
~60mA (heater off)
-
Current Consumption: 150mA
-
DO output: TTL digital 0 and 1 (0.1Vand5V)
-
AO output: 0.1V -0.3 V (relative to pollution), the most concentration of voltage of concerning 4V
-
Detective Concentration: 0.05mg/L -10mg/L Alcohol
-
Interconnection: 1TTL compatible input (HSW), 1TTL compatible output (ALR)
-
Heaterutilization:notupto750mW
-
In operation temperature: 14to122°F (- 10to50°C)
-
Load resistance: 200k
-
Sensitivity S: Rs (in air)/Rs (0.4mg/L Alcohol) lesser than or equal to 5
-
Seeing Resistance Rs: 2K-20K (in0.4mg/L alcohol)
-
Dimensions: 32 x 22 x 16mm.
XI.POWER SUPPLY
A lithium-ion (Li-ion) battery could be a sort of regenerable battery usually employed in laptops and cell phones to form power, li-ions move from the negative conductor through a solution to the positive electrode. A battery Management System (BMS) is a brilliant element of a battery pack
answerable for modern observation and management. It is the intellect behind the battery and plays an important role in its levels of safety, performance, charge rates, and longevity.
XII.WORKING
We employ 2 sensors LM35 for temperature and MQ3 for smoke detection.
Smoke sensor mostly used to detect any gas leakage or fire outbreak in the battery system.
These days, the problem of electric vehicle (EV) is less configuration on battery so if battery runs for longtime, then it has got heated. That is why we use LM35 to calculate the temperature.
All the data or readings will be showed on display. If in starting condition when the temperature and bank both are below threshold value PREPARED TO GO will display on LED and motor starts. The threshold point of temperature sensor is 32 degree and the smoke is 199 units So, when temperature crosses to threshold point the cooling fan will ON and cools upto 38 degrees after that controller shows INGNITION OFF communication and cut the power supply of motor. When the smoke crosses its threshold value the solenoid valve will ON and controller shows INGNITION OFF message and cut the power supply of motor.
XIII.MODEL
XIV.ADVANTAGES
A more authentic and safety ensuring system for the safety while using EVs.
Automated and trouble-free operation which should not disturb the normal operation of the vehicle.
Automatic battery health parameters monitoring will
XVI.REFERENCES
[1] K. Kadirvel, J. Carpenter, P. Huynh, J. M. Ross, R. Shoemaker, and B.Lum-Shue-Chan, A Stackable, 6- Cell, Li-Ion, Battery Management IC for Electric Vehicles With 13, 12-bit ADCs, Cell voltage balancing, and Direct- Connect Current-Mode Communications, IEEE J. Solid-State Circuits, vol. 49, no. 4, pp. 928934, 2014. [2] Sun P, Bisschop R, NiuH, Huang X. A review of battery fires in electric vehicles. Fire Technol 2020:1e50.st
make Electric vehicle drive more safer and trouble free.
[3] N. Noda, 21century cars and ICs, in 2000 IEEE International
The circuit could have a wide range of application which integrate to the design trends of electronic products currently being released.
Due to simple and cost effective in nature this design can effectively use in small scale of production or startup.
This project has a huge future compass under the aegis of the project, the worthy consumer will take a lot of positive result from this project.
Since the world is heading towards Electric vehicles and safety of Li-ion batteries are very much important for consumer.
Using arrangement of this setup the customer and industry can install low but accurate and effective protection system in their vehicles.
XV.CONCLUSION
The last way to approach for making this hardware module to give simple way of protection.
We tried to conclude almost all the missing requirement for these varieties of platform uses this hardware module effective as much as :
Flexible User friendly
User interactive
Latest use of technology
After all the feature there is lot, more scope left in this platform so the development will continue.
Solid-State Circuits Conference. Digest of Technical Papers
(Cat.No.00CH37056), 2000, pp. 1217.
[4] Johnson. A. Asumadu, Mohammed Haque, Helio Vogel, Charles Willards. Precision Battery Management System [C]. IMTC 2005. [5] Wu Y, Yin Y. Distributed power battery management system based on CAN bus. Automot Eng.2004;27(5): 5303. [6] Deng S, Wang Y, Li X, Huang H. Lithium battery protection circuit design. [7] Electron Technol. 2006;1(10):6872(in Chinese). [8] Chen Y, Li J, Song B. Cortex-M3 + C/OS-II introduction to embedded system development and application (in Chinese).Beijing: Peoples Posts and Telecommunications Press; 2010. p. 1236.
[9] Hande A.. Internal battery temperature estimation using series battery resistance measurements during cold temperatures [J]. Journal of power sources, 2006, 158(2): 10391046. [10] Pesaran AA.. Battery thermal management in EVs and HEVs: issues and solutions [C]. Advanced Automotive Battery Conference, Las Vegas, Nevada. 2001.