
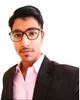
- Open Access
- Authors : Yousuf Pasha Shaik
- Paper ID : IJERTV10IS010189
- Volume & Issue : Volume 10, Issue 01 (January 2021)
- Published (First Online): 29-01-2021
- ISSN (Online) : 2278-0181
- Publisher Name : IJERT
- License:
This work is licensed under a Creative Commons Attribution 4.0 International License
Literature Review on Applications of Plastics/Composite Materials Under Deep Oceans
Mr. Yousuf Pasha Shaik
Applied Logistics and Polymer Sciences Hochschule Kaiserslautern
Pirmasens, Germany
Abstract. – This research project is concerned about finding the applications of plastic/ composite components under deep oceans, which can withstand high pressure, as well as can operate at depth (1400 meters). Since 1600 BC usage of polymers by us has benefited in many ways such as the ancient Mesoamericans first processed natural rubber into balls, figurines, and bands. In the coming years, the importance of plastics and rubber has increased, experimentation with natural polymers, horns, waxes, natural rubber, and resins, until the nineteenth century, when the development of thermoplastics. Even though various plastic materials are available for commercial and domestic applications, only a few of these thermoplastics in comparison to volume and are of relatively low priced, such as Low-density polyethylene (LDPE), high-density PE (HDPE), polypropylene (PP), PVC, PS, and polyethylene terephthalate (PET) they take approximately 90 percent of the total demand (1). A combination of two or more materials leads to superior properties, which are called composites. In particular, they are mostly used in many applications (structural applications, functions in the automobile industry, aerospace, marine. etc) (2). Hence in this project, an attempt has been made to summarize the applications of plastic/ composite components used in deep oceans and under specified conditions..
KeywordsPolymers; Composites; Marinre Plastics; Fibers;
-
INTRODUCTION
-
Plastics
The word Plastics is taken from Greek PLASTIKOS- which means they can be shaped or molded (3). The great advantage of plastics is that they can be used in various fields, over other materials which have limitations and limited types according to on the availability in nature, but plastics can be tailored based on the requirement and even combination of materials is also possible to fulfill the application (composites) and get the best out of them. Some plastics occur in nature (rubber), some are made through the plastics chemical processed used in synthesis (condensation, poly-addition, cross- linking). There are three types of plastics basically: Thermoplastics, Thermosetting polymers, Elastomers.
Linear- Monomer units are linked together to form a linear polymers. Linear structure of polymers is where the carbon- carbon bonds formed are of linear structure.
Examples : Nylon, PVC, High-density polyethylene, etc. Applications: PVC- health care, construction, electronics, automobile.. etc Nylon: food packaging, textiles, carpets, electronics..etc HDPE(recyclable) : plastic bottles, corrosion resistance pipes.etc
Branched- Monomer units are joined to form branched structures of different length. As chain entanglements are increased as a result polymer properties (polymer strength, toughness, glass trasition temperature) also increase.
Examples : LDPE, glycogen, Starch, etc. Applications:LDPE-computer components,wash bottles, tubings..etc
Cross-linked structures- The monomer units are cross-linked together to form cross-linked chains. These are connected by covalent bonds. Which mean that a bond of one polymer chain links to a bond of another polymer chain .
Examples : Rubber, Bakelite
Applications: hoses, belts, flooring, medical gloves.
Network- Monomers are joined to form a large 3D network.The 3-Dimensional network formed by the molecules lead to the irreversible curing (4).
Examples: Epoxy, Phenol formaldehyde
Applications- Epoxy: Manufacturing of adhesives, plastics, paints, coatings..etc
Elastomers-Elastomers are the amorphous polymers existing above their glass transistion temperature with viscoelasticity (Both viscous, elastic properties) with weak intermolecular forces which leads to elongation for low amount of stresses applied, and has high failure strain compared to other materials. This term is often interchangeable with Rubber.
Examples- Chloroprene rubber, Butyl rubber, Styrene butadiene rubber, synthetic polyisoprene..etc
-
Classification of plastics
The Plastics can be classified into 2 types: Thermoplastics, Thermosets
-
Thermoplastics
These thermoplastics cure reversibly, softens when heated above the glass transition temperature, and becomes hard when curing (cooling) .
Structure : These are generally in Linear-structure.
Properties: Transparent High strength, Toughness Hardness, Chemical resistance Waterproofing
Examples: ABS (Acrylonitril Butadiene Styrene) Acrylics Polycarbonates, polyethylene (PE) Polypropylene, Polystyrene Polyether ketone (PEK), Polyether ether ketone (PEEK) PVC (polyvinyl chloride) Liquid crystal polymers, Vinyl, Acetals, Fluorocarbons Cellulose, Polyamide, Polyethylene sulfide.
Applications of thermoplastics
These are a few applications of thermoplastics which are used in daily applications (phone covers, toys, electrical products, dashboards, car rims, bearings, cables, hoses, sheets, windows, Gardner pipes, automobile industry, aerospace applications, etc)
-
Thermosets
-
They cure irreversibly they become hard and can´t be refused after curing continuous heating of the products lead to the degradation of plastics. These are 3D network, the remolding is not formed so easily, so they can´t be reused. Whereas in the thermoplastics, they are linear and they slide so they re- used. Exmaples : Alkydes, Allylic, Silicon, polyurethane
Amine, Vinylester, Bakelite, Epoxies, Phenolics, Polyester Applications: Electrical Equipment,Motor Brush holders Printed circuit boards, Circuit breakers, Kitchen utensils, handles, Encapsulated material, Spectacle lenses, knobs.
2. Composite Materials
To be simple and precise, composite material is a combination of two or more dissimilar materials/ substances (micro/ macro) which don´t chemically react with each other (differ in chemical composition). Composites comprise a continuous phase (matrix Phase), and reinforcement Phase. Composites have hybrid properties (high strength, high toughness, high hardness, tensile strength, flexural strength), which can´t be obtained by the plastic materials (thermoplastics, thermosets), and these are light in weight, strong and stiff, ratios of strength to weight and stiffness to weight is greater than Al and steel. One more advantafe is these properties can be tailored.
-
-
LITERATURE REVIEW ON PLASTICS/ COMPOSITES UNDER DEEP OCEANS (DEEP OCEANS) AT HARSH CONDITIONS (PRESSURE- 135 BAR, DEPTH-
1400 METERS)
-
Applications of composite materials
-
Submarine Domes
-
Landers
-
Cables
-
U-Boat Worx
-
Aanderaa sea-Guard CTD
-
HUGIN
-
Rapid pro-CTD
-
The advantages of composite materials for marine structures, notably their high specific properties, resistance to degradation in water, and flexible fabrication to produce special shapes, become even more valuable when underwater applications are considered. Nevertheless, apart from a few exceptions, there are not many structural applications of composites underwater at present. The reasons will be discussed here. Three types of application will be considered:
-
Oceanographic
-
Offshore
-
Submarine
1.1 SUBMARINE BOW DOMES
Construction with the composites is now the materialof choice for sonar domes on surface ships and submarines. On submarines, they are made of steel or glass-reinforced plastic (GRP) with a ½ inch rubber boot covering the exterior of it domes on submarines are truly massive structures that can measure almost 34 feet across and weigh over 43,000 pounds, as they are built to match the hulls cross-section shape The domes must have a high degree of acoustic transparency to avoid the signal disconnections. The domes were made with the
polyester resin, and alternating piles of woven roving and made from E-Glass, by this application both the acoustic transparency and the overall strength is increased (5).
Fig 1: Submarine Bow Dome, (5)
Materials uses in Submarine Bow Dome:
Polyester – Thermosetting plastics
E-Glass fibers- E-Glass or Electrical grade glass (Originally developed for the insulation purpose in electrical wirings) Properties – low cost, high-strength, high-stiffness Manufacturing technique- based on the complexity of the product RTM, VARTM, injection molding, Autoclave .etc are used
-
LANDERS
Fig- MAP instrumentation support structure in the composites for 6000 meters.
Benthic Landers are mostly prepared with aluminum and steel due to weight proportionalities. Recently these Landers are prepared with composites, which is a glass and epoxy structure and 1.5 meters height, which is designed to support a range of
probes and instrumentation on the ocean floor, which can operate under 6000 meters of depth and is replaced with an aluminum alloy structure. This composite lander was developed by IFREMER, the MAP (module autonomous pluri- disciplinary). The main reason for replacing the aluminum alloy structure is corrosion with some other devices. This is made of a hand lay-up method. Generally, at a higher thickness to radius ratio, the buckling failure is not observed.
-
CABLES
A submarine deep-sea cables are those laid on the sea bed which helps in carrying the communication signals all across the ocean and seas. Modern cables are typically about 25 millimeters (0.98 in) in diameter and weigh around 1.4 tons per kilometer (2.5 short tons per mile and 2.2 long tons per mile) for the deep- sea sections which comprise the majority of the run, although larger and heavier cables are used for shallow- water sections near shore.
Fig: submarine cable, (6)
-
DEEP SEA CABLES
The deep-sea cables belong to this same family of cables, the components and its alignment are little but different to obtain the phenomenal pressure of 500 bars. The deep-sea cable has a special gel in it which prevents the instable behavior at up to 500 bar pressure. In addition to that, the operating condition is 5000 meters. The outer cable here is made of reinforced polyurethane sheath (6).
Fig: deep sea cables, [8]
Composites like 2024-T8, 7075-T6, and SAP with 14% Al2O3 these have higher strength and can be used in many applications.
-
U-BOAT WORX
The story of u boat worx began in the year 2005 building the private underwater submarines which can withstand the pressure of 100 meters to 3000 meters.
C- RESEARCHER SERIES: The C-Researcher series offers scientists, researchers, documentary makers, and explorers the most outstanding submersibles ever built. Apart from the fact that these versatile submarines are ideally suited for research, their view, efficiency, and speed make them also perfect for those who simply wish to take in the views of the deep sea. This can accommodate 3 persons to travel in it.
Fig- U-Boat Worx, C-Researcher series, (7)
Materials: Acrylics (for the transparent dome) Titanium (hulls) Acrylics : polymethyl methacrylate
Titanium: Titanium (PT-3V, PT-5V are called marine alloys). Compositions: PT-3V (Ti-4Al-2V) PT-5V (Ti-5Al-1.5V14Mo)
As a part hull, this has several advantages high specific strength, high corrosion resistance in the fields of oil, water, gas, stratal water, drilling water (low maintenance costs), and light in weight when compared to steel. The titanium can stand up to 6000 meters of depth under deep oceans, so this is preferred in the construction of Hulls. The reasons for using titanium in hulls are good weld-ability, adaptability to various kinds of heat treatments, and machining processes.
The submersibles feature the largest and thickest acrylic windows ever made. Each cruise submarine, for example, has two acrylic hyper-hemispheres and one pilot window. The acrylic of the deep-diving windows is incredibly thick more than 20 cm (7.8 inches) (7).
The process used here is the autoclave process, which is then subjected to high temperature and high pressure to initiate the polymerization process, annealing to release the stresses that may have developed.
Fig: Acrylic shell of U-Boat Worx &Outer casing of C- Researcher, (7)
Working conditions Based on the use depth as criteria C- RESEARCHER 2, C- RESEARCHER 3, and C-
RESEARCHER 3LH which can travel to a depth of 3000 meters, 2500 meters, 1700 meters (7). The pressure can withstand up to 30 MPa. The initial use of acrylics was started in the year 1950 in the applications of Bathysphere, Bathyscaphs as window panels, due to the ergonomic manufacturing process and light in weight and less expensive than Glass. Due to the properties like durability and impact strength, various color choices, clear visibility, scratch-free, lightweight
Acrylic Applications- Acrylic helmets, Acrylic aquarium, Acrylic helmets, windows for swimming pools (ocean theme parks), Sub-marine windows, airplane canopy.
-
HUGIN
HUGIN is an autonomous underwater vehicle. Which may even be named as AUV /marine robot offering the ultimate autonomous remote subsea survey capability, and can function without tethers, cables, or remote control, they have a multitude of applications in oceanography, environmental monitoring, and underwater resource studies. A key element in the Hugin concept is the application of a common technology that makes the systems adaptable for navy and commercial applications.
Key features Operating depth of 3000, 4500 & 6000 meters Pipeline and subsea structure inspection Oceanographic surveys; Environmental monitoring; Marine geological survey
Materials used- The vehicle body is made from carbon fiber laminate material and syntactic foam. The pressure containers are made either from titanium or sea-water resistant aluminum depending upon depth requirements.
Carbon fiber Carbon fiber reinforced polymer (CFRP) composites which are also called carbon-fiber laminates. These are light in weight and more fuel- efficient when compared to aluminum. Carbon laminate is extremely strong and stiff because of its woven layers, pure carbon fibers bonded together by a hardened plastic, such as epoxy resin makes it harder and stiffer.
Syntactic foam: Syntactic foam is a class of material made using pre-formed hollow spheres (commonly made of glass, ceramic, polymer, or even metal) bound together with a polymer. The syntactic portion refers to the ordered structure provided by the hollow spheres. The foam term relates to the cellular nature of the material. The unique properties of high strength and structural integrity at low density, greater stiffness, strength, impact and shock properties, and attractive syntactic foam have become widely used in subsea buoyancy applications, many defenses, and navy applications, Oceaneering projects such as cable and hardball floats and instrumentation support which can withstand higher pressure and temperature.
Battery systems- The Hugin system uses two different types of battery systems, based on the pressure specifications. Pressure tolerant batteries eliminate the need for pressure containers and thus the inherent risk for explosions due to battery hazards. Especially in deeper waters, the pressure tolerant designs allow for higher battery energy and endurance.
The two battery technologies in use for HUGIN AUVs are:
Lithium Polymer Battery.-The lithium-ion polymer battery is an electrical rechargeable and pressure tolerant. The battery is built up by commercial poached cell batteries gathered in battery blocks that are assembled into complete batteries for the HUGIN AUVS.A lithium-ion battery is the rechargeable battery of the lithium- ion technology, using a polymer electrolyte instead of liquid electrolyte, having high conductivity and semi-solid gel polymers like (The lithium polymer cells use solid polymer electrolyte (SPE), Polyethylene Oxide, Polyacrylonitrile (PAN), Poly-Methyl methacrylate (PMMA), Polyvinylidene Fluoride (PVDF) form this electrolyte. These provide higher specific energy than other aluminum battery types.
Aluminum Oxygen Semi Fuel Cell (ALHP FC battery)
ALHP FC is a unique energy source that produces electrical power from aluminum and oxygen. No other power source can drive an AUV like the HUGIN 3000 with all payload systems running for 60 hours at 4 knots.
-
Rapid Pro CTD
The main functions of rapid pro-CTD is measuring conductivity, temperature (thermistor), and depth while this device can be connected and can be operated through via mobile phone as well, which would be an added advantage to control the device (1).
Fig- Rapid pro CTD, [4]
Depth rating: 2000 meters
Materials used: Titanium casing/ PEEK housing (Polyether ether Ketone) Polyurethane and ceramic sensor components Composite and titanium sensor materials.
-
Additional materials
There are still some materials which are available which can with stand the pressure of 15 mpa, such as TECRAN ABS (grey), TECANYL 731 (grey), TECANYL GF30 (natural), TECAPRO MT(white), TECAFORM AH (natural), TECAFORM AD (natural), TECAFORM AH GF (natural), TECAMID 6 (natural), TECAMID 6 GF30 (black), TECAMID 66 (natural), TECAMID 66 CF20 (black), TECARIM 1500,
TECADUR PBT GF30 (natural), TECANAT (natural), TECANAT GF30, TECAFLON PTFE (natural), TECAPEI
(natural), TECATRON (natural), TECATRON GF40 (natural),TECAPEEK GF30(natural), TECAPEEK GF30 (natural), TECAPEEK CF30 (black), TECAPEEK PVX
(black). These are some list of materials which can with stand the higher pressure limits ranging from 15Mpa (4).
-
-
CONCLUSION
To summarize and conclude this theory, different types of plastic components/ composite components which can withstand harsh conditions under deep oceans (higher temperature, pressure) are discussed where higher temperature and pressure act on them:
-
Polyester, E-Glass which possess high strength, high stiffness and are used in submarine applications.
-
Glass and epoxy are used in Benthic Landers' higher compressive strength, low cost, good temperature resistance, and good flexural properties are seen.
-
Polyethylene, polycarbonate which is used in deep-sea cables protects from chemical resistance when compared to alloys/ metals. The polycarbonate is tough, transparent, low density, and sometimes the composites like 2024-T8, 7075-T6, and SAP with 14% Aluminum trioxide.
-
Some underwater submersibles use Acrylics (polymethyl methacrylate) and composites with platinum compositions, which platinum has the best melting, boiling point, hardness, tensile strength, and in some applications PEEK is used (Rapid pro-CTD).
-
Carbon fiber with syntactic foam is being used in an underwater submersible named HUGIN which can withstand higher depth ranges and higher pressures due to the usage of carbon fibers they possess better properties and strength to weight ratio is also good.
-
-
REFERENCES
-
Valeport Product Designer. Valeport Corporation. [Online] Aug 2017. https://www.valeport.co.uk/products/rapidpro-ctd/.
-
Wikipedia. [Online] 2021. https://en.wikipedia.org/wiki/Composite_material.
-
wikipedia. U boat worx. [Online] Dec 2020. https://en.wikipedia.org/wiki/U-Boat_Worx.
-
Ensingerplastics. Ensingerplastics:COM. [Online] https://www.ensingerplastics.com/en/shapes/plastic-material- selection/mechanical-properties.
-
Ericgreeneassociates. Ericgreeneassociates Corporation. [Online] 2012. http://www.ericgreeneassociates.com/images/History_of_Submari ne_Composites.pdf.
-
LEONI CABLES. LEONI. [Online] LEONI. https://www.leoni- marine.com/en/products-services/cables/sealine-underwater- cables/.
-
U-Boat Worx. U-Boat Worx Corporation. [Online] 2009. https://www.uboatworx.com/model/c-researcher.
-
Sea Bird Scientific. Sea Bird Scientific Corporation. [Online] June 2018. https://www.seabird.com/profiling/sbe-19plus-v2-seacat- profiler-ctd/family-cms.block?productCategoryId=54627473770.
- [Online]
-
KONGSBERG. Kongsberg Corporation. [Online] 2016. https://www.kongsberg.com/globalassets/maritime/km- products/product-documents/hugin-family-of-auvs.
-
Richerd Millis. Kongsberg. Kongsberg Hugin . [Online] 2014. https://www.kongsberg.com/maritime/products/marine- robotics/autonomous-underwater-vehicles/AUV-hugin/.
-
Aandrea a Xylem Brand. Aandrea. [Online] 2012. https://www.aanderaa.com/productsdetail.php?SeaGuard-II-DCP- 53.
- [Online]