
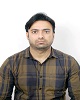
- Open Access
- Authors : Vishal Shukla , D. P. Chakraborty , C Raghu Kumar , Umesh Shivangi , Jacky Du
- Paper ID : IJERTV10IS090219
- Volume & Issue : Volume 10, Issue 09 (September 2021)
- Published (First Online): 20-01-2022
- ISSN (Online) : 2278-0181
- Publisher Name : IJERT
- License:
This work is licensed under a Creative Commons Attribution 4.0 International License
Iron Ore Tailing Beneficiation – a Potential Resource for Future
Vishal Shukla *a, C. Raghu Kumar a, D. P. Chakraborty a Umesh Shivangi b, Jacky Du c
a Process Technology Group, Tatasteel Ltd.Jamshedpur-831001, India
b LONGi Magnet India Pvt Ltd, Bangalore, India
c LONGi Magnet India Pvt Ltd, China
Abstract:- During the processing of iron ores, a large quantity of low-grade tailings containing abundant iron values in fine particle size range is produced. Due to the increasing demand in the high-grade ores for the metallurgical operations and the stringent environmental conditions on the mining activity, it is essential to utilize the waste tailing pond slimes. Recovery of iron values form these tailing ponds not only enhance the life of the existing operating mines but also finds the route to achieve the sustainable process. Iron ore tailing/slime (-150 m) is produced after scrubbing and wet screening of a low-grade iron ore.
Tailing beneficiation of iron ore has been addressed either by flotation or wet high intensity high gradient separation. The present study aims to recover iron values from discarded slime containing assay ~56% Fe, ~6.5% SiO2, and ~7.0% Al2O3 from Noamundi processing plant by using high gradient magnetic separator (HGMS). In this process, the tailings is effectively processed with vertical pulsating high gradient magnetic separator to produce a relatively high-grade iron concentrate. The results of investigation indicate that this novel process is capable of producing an iron concentrate assaying ~ 60% Fe and ~3.25% alumina with a yield of ~55 % on weight basis and recover > 65 % iron bearing particles from the tailings. More importantly, the corresponding tail contained ~45% Fe. It was concluded that this novel process may be effectively used to recover iron values from low-grade hematite tailings.
Key Words: Iron ore slime, Fe Recovery, HGMS,Yield & Noamundi
-
INTRODUCTION
India is endowed with huge iron ore deposits and occurs mostly as oxides in nature. The deposits are fairly well distributed in the states of Jharkhand, Chattisgarh, Orissa, Karnataka, Maharashtra, Goa and Andhra Pradesh. The lack of consistency with respect to the ratio of Al2O3 to SiO2 make these ores unsuitable for direct use in the blast furnace and need washing prior to industrial use. During processing/washing of these iron ores, a large amount of extremely ne particles (typically less than 45 microns), called slimes (as high as 15 20% by weight of the run of mine ore) are being generated. Though slimes are currently being dumped into tailing ponds, locking the enormous land space as well as precious water resources, this fraction of the mined material contains recoverable iron values (assaying 4560% Fe). Same process is depicted in Figure 1. If, it beneciated (to a lower alumina content) and pelletized, it would become an excellent part of the blast furnace burden (BF grade) or the feed to sponge iron kilns (DRI grade). Rapid depletion of high grade ores, need for resource conservation and, the increasing demand for steel in India are driving the iron ore industry towards nding appropriate strategies for the beneciation and utilization of alumina rich iron ore slimes.
The review of literature on processing of Indian iron slimes is enormous where in centrifugal concentration devices, selective dispersion selective flocculation, inverse cationic column flotation, wet high intensity magnetic separation (WHIMS) have been used. However, most of the work on industrial scale centers either on inverse cationic column flotation or WHIMS. Keeping in view the large reserves, in order to establish the commercial feasibility of the high gradient magnetic separator process for Indian iron ore slimes and as a prelude to commissioning a full scale plant, designed and developed a portable pilot plant set up for conducting onsite trials using the slimes and producing the concentrate and tailings in a continuous mode. Successful results of these plant trials conducted at the Tata Steels Noamundi Iron Ore Mines to carry out the fine particle processing studies on iron ore wash plant tails from various plants spread across Orissa with an aim to produce pellet grade concentrates (Fe > 60%, SiO2 + Al2O3 <6%).
-
Characterization studies
2 .1.1 Material
Fig.1. Layout for slime generation
-
-
EXPERIMENTAL
A representative portion of the slime sample was prepared by coning and quartering method and used for characterization studies. The chemical analysis of the head sample assays is tabulated in Table.1. Particle size analysis, size wise chemical analysis, and XRD studies were carried out to know the feasibility to understand the nature of the sample.
Table 1
Chemical analysis of the head sample
Fe%
Al2O3%
SiO2%
P%
55.3
8%
7%
0.3
-
Size analysis
Size analysis of the head sample was performed by laboratory vibratory sieve shaker. The particle size distribution by weight is shown in Table.2. It indicates that d80 size of the head samples is 50 microns.
Table 2
Particle size distribution by weight
Size Fraction (µm)
Wt%
Cum Wt%
+1000µm
0.5
0.5
+500µm
0.8
1.3
+250µm
1.2
2.5
+150µm
2.5
5
+75µm
6.1
11.1
+50µm
7.2
18.3
-50µm
81.7
81.7
-
Mineralogy
X-ray diffraction (XRD) was carried out for identification of different phases present in the feed sample to shows the presence of hematite, quartz, kaolinite, magnetite and goethite in the feed sample along with percentage as shown below;
Table 3 Mineralogy distribution
Mineralogy
%
Hematite
52
Goethite
25
Chlorite
8
gibbsite
7
Kaolinite
8
-
About the technology -High Gradient Magnetic Separator (HGMS)
Vertically pulsating HGMS utilizes combination of magnetic force, pulsating fluid and gravity to continuously separate magnetic (iron bearings) minerals and non-magnetic (gangue) minerals. The equipment possesses the advantages of high beneficiation ratio, high recovery, adaptability to varying particle sizes, and minimized matrix blocking. The equipment is reliable, easy to operate and maintain as depicted in Figure 2.
-
Methodology for experiments
Fig.2. High Gradient Magnetic Separation
The plant trials were performed at Tata Steels iron ore mines at Noamundi. The slime sample was withdrawn periodically from the hydrocyclone overow, that is, the tailings of the beneciation plant as schematically shown in Figure 3. The fresh slimes sample was stored in a tank for a set of continuous scale tests. The representative samples were sujected to chemical analysis by classical methods, the mineralogical studies , particle size analysis by classical fine sieve and sub sieve analysis methods. The results of characterization studies are given in Table 3. The quantity thus collected was sufcient to run the continuous tests for a few hours. Impeller was used to stir the collected slime sample in the tank, so as to avoid settling and segregation during the test work.
Fig.3. Schematic diagram for proposed and pilot set up at site
The portable pilot plant set up was run at a slime 250 kg/h of dry solids at a pulp density of ~10% g of solids/100 ml of slurry. A typical particle size distribution and chemical analysis of the slime sample used in this test work is given in table No 1. 80% of the material in the slimes was ner than 45 µm. X-ray diffraction of the sample conrmed the presence of minerals like hematite, goethite, gibbsite, kaolinite and quartz, as shown in table No 3. Initially pilot trials were carried out varying the type of feed, % solids, ring rpm and intensity. This was followed up with a cleaner and scavenger stage for improving the grade and recovery. A photograph of the pilot plant set up connected to the slimes collection and storage tank for conducting onsite trials in the continuous mode is shown in Figure 4.
Fig.4. Schematic of Noamundi owsheet, showing the stream from which the slimes samples were withdrawn for the pilot plant trials
-
-
RESULTS AND DISCUSSION
Encouraging results were obtained from the pilot trials and beneficiation potential of hydrocyclone overflow (slime) utilizing HGMS was established. Along with this, HGMS pilot trials were also conducted with hydrocyclone underflow and feed to evaluate the performance of HGMS different type of feed.
-
Hydrocyclone overflow (slime): Hydrocyclone overflow(slime) was upgraded to Fe% ~ 63% and Al2O3 ~ 3.25% from the feed of Fe% ~ 56% and Al2O3 ~ 7% with a yield of 54% (refer Table-4).
Table 4
Optimised result for slime processing
Magnetic Field (Gauss)
Ring RPM
Pulsation (Pushing/min)
Yield%
Fe%
SiO2%
Al2O3%
P%
Magnetic
6000
3
200
54.0
63.15
2.42
3.25
0.10
Non-Magnetic
46.0
47.49
9.43
11.57
0.17
Feed
100.0
55.94
5.65
7.07
0.13
-
Effect of Operating Parameters on Yield of HGMS
Effect of operating parameters like slime pulp density, Ring RPM, Pulsation and Magnetic Field intensity have also studied during trial. Relationships with yield were developed and same are given and discussed below.
-
Effect of field intensity on Yield and grade of HGMS product
Tests were carried out by varying the intensities at 2000 to 13000 and 15,200 gauss at a constant ring speed of 3 rpm, 1.1 g/cc,15 g/cc & 20g/cc pulp density and frequency of 200 cycles /min. The results are shown in Figure 5. The results indicate that an increase in intensity and % solid increases the weight % yield (i.e 20% to 60%) and % Fe (i.e.58% to 61%) distribution of concentrate, but decreases the grade of concentrate.
Fig.5. Relationship between Magnetic Intensity, PD and Yield
-
Effect of Ring RPM on yield of HGMS
The rpm of the ring was varied between 1 to 3 keeping frequency at 200 cycle /min, intensity at 8000 gauss and 1.1 g/cc pulp density. The results are graphically shown in Figure 6. The results indicated that an increase in rpm insignificantly decreased the grade of concentrate and significantly increased the wt% yield (i.e 20% to 60%) and % Fe (i.e.58% to 61%) distribution of concentrate.
Fig.6. Relationship between process parameters and Yield
HGMS test work was carried out using different process parameters. From the relationship it was observed that the yield of iron decreases with decrease of magnetic field and , irrespective of PD. In case Ring RPM, a maximum yield was observed at Ring RPM 3. As ring rpm decreases led to decrease in yield also.
-
-
CONCLUSIONS
Response of High gradient magnetic separation for Noamundi slime is quite encouraging during trial. Slime, hydrocylone overflow, which is 16% of ROM considered as a tailing, can be processed through HGMS to reduce the slime loss and recover iron value from slime.
-
Slime tailing fraction generated from the experiment contains 40 to 47% Fe% which is much lower (by ~10%) than the present scenario, whereas concentrate Fe% is about 63% with 54% yield and can be used for production of BF grade pellets.
-
Concentrate with assay >63% Fe and <3.3 Alumina was achieved with yield more than 50%.
-
Corresponding Tails Fe grade was closer to 45%.
High Gradient Magnetic Separation technology process for beneciating alumina rich iron ore slimes is a commercially attractive technology option worth considering in the context of current challenges facing iron ore industry in India.
ACKNOWLEDGEMENTS
The authors are thankful to Noamundi Processing team, OMQ for their help and support in commissioning and running the pilot plant set up at Noamundi mines. The authors would also like to thank the Natural Resource Department team at Tata Steel for their help in sample preparation and analysis during the trial period. Authors are grateful to Tata Steel Management for their constant help and support during the course of these plant trials and publishing this work.
-
Colloids and Surfaces
REFERENCES
-
JIN, R., HU, W, and HOU., 1987. Mechanism of selective flocculation of hematite from quartz with hydrolysed polyacrylamide. Colloids and Surfaces, vol. 26. pp. 317331.
-
Transactions of the Indian Institute of Metals
-
Venugopal Tammishetti, Beena Rai, Pradip, Vishal Shukla, D. P. Chakraborty, Ashok Kumar, 2016. Selective Flocculation of Iron Ore Slimes: Results of Successful Pilot Plant Trials at Tata Steel, Noamundi.
-
Mineral Processing and Extractive Metallurgy
-
S Roy and A Das, 2008. Characterization and Processing of low grade iron ore slimes from the Jiling area of India. Min. Processing and Ex. Meta. Rev., 29, (5), pp. 213 231.
-
International Mineral Processing Congress IMPC 2010
-
Y.Tong., J.Zhang and J.Wernham, 2010. The research on application of new technologies in HGMS with horizontal magnetic line. Proc. XXV IMPC, Brisbane, Australia, pp 1283-1286.
-
International Mineral Processing Congress IMPC 2012
-
Vasumathi, N and Vijaya Kumar, T V and Subba Rao, S and Prabhakar, S and Bhaskar Raju, 2012. Recovery of values from tailing ponds of iron ore washing plants. In: International Mineral Processing Congress IMPC.