
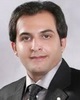
- Open Access
- Authors : Nima Rezazadeh
- Paper ID : IJERTV9IS061017
- Volume & Issue : Volume 09, Issue 06 (June 2020)
- Published (First Online): 09-07-2020
- ISSN (Online) : 2278-0181
- Publisher Name : IJERT
- License:
This work is licensed under a Creative Commons Attribution 4.0 International License
Investigation on the Time-Frequency Effects of A Crack in A Rotating System
Nima Rezazadeh Graduated Master Degree
Department of Mechanical Engineering Islamic Azad University, Seman, Iran
AbstractIn this essay, a rotor-bearing system has modeled by finite element method to examine the effect of breathing crack on it. Next, coefficient matrices of desired system has extracted, and then crack and its breathing behavior has modeled. In the next step, "Houbolt" procedure has used to system responses in transient and steady state operation can be achieved. Different crack depths in the shaft have considered. To investigation on system responses, time signal, Fourier transform, and finally the energy diagram of continuous wavelet transform coefficients have illustrated. Comparing numerous figures it can be seen that wavelet transform has a great capacity in distinguishing cracks.
Keywords Breathing crack; Fourier transform; Continuous wavelet transform; Transient signal; Houbolt
-
INTRODUCTION
High-pace loaded rotor systems are widely distributed in machines and equipment of various branches of technology, including transport or petrol industry. Condition monitoring of this equipment with a high resolution is one of the major task for many engineers worldwide. Detection of fatigue cracks in early time is necessary to decline catastrophic failure of rotating systems in which can result economic losses and accidental dangers. Many rotary machines, such as turbines, which are used in power producing industry, turn on for once and work in a steady state for a long time. Therefore, the methods that study the health of rotating equipment during steady-state operation have attracted the attention of many researchers in the recent years. On the other hand, some rotating systems, such as jet engines, are turned on and off consecutively, so the analysis of the transient response for this type of machine is significant.
In the field of health monitoring of systems, many researchers have been using numerous non-destructive techniques to detect possible defects and calculate the safety of structures. Recent advances in computers, sensors, and other electronic technologies have made the use of non-destructive methods and tests more and more effective and efficient in detecting defects in structures than destructive methods. Among all methods in detection of cracks in rotor systems, vibration-based methods have the most efficiency [1]. The principal idea in Vibration-based procedures is that in the methods investigator can use of variations in system features such as stiffness, damping and mass occur which will cause significant variations in modal properties such as natural frequencies, modal damping and mode shapes. An illustration of this is that reducing of system stiffness is the significant indicator of existing crack [2].
The geometry of crack has a great effect on the dynamics and characteristics of the cracked rotor. Therefore, the cracks
can be classified mainly into three groups: longitudinal, slant and transverse cracks. Transverse cracks are most common and serious. Transverse crack appears perpendicular to the axis of the shaft and has large influence on the dynamic behavior and characteristics of the cracked rotor. This kind of crack reduces the cross-sectional area near to the crack surface of shaft and produces serious damage to the shaft. These cracks are generated when the rotor system is subjected to fluctuating bending stresses (i.e. cyclic stresses) [3]. Moreover, due to the tiny crack edge in heavy shaft in industrial application, crack is breathing during its rotation (i.e. opens and closes) and the probable non-linear effects of this phenomenon should be considered [4].
Liong and Proppe (2013) studied the breathing mechanism of a cracked rotor and its effects on the rotor system, resulting in the weight of the shaft appearing and the inertial forces. A method has proposed to estimate cross-sectional stiffness reduction, which includes crack. This method is based on the continuous area model instead of the elastic linear fracture mechanics. Crack breathing was modeled with a parabolic surface. As long as the crack is shallow, the straight-line enclosure line was used, while the parabolic closure line was used for deep crack [5]. Silani et al. (2013) focused on analyzing the vibrations of rotating systems, including cracks, and calculated the flexibility matrix of the cracked element using modified integral-capture limits. These modified limits provide more accuracy than conventional methods. The effect of these corrections has shown on the flexibility matrix coefficients for a simple rotor system including open crack. Furthermore, a new finite element method has introduced to can model the breathing behavior of the crack. Then, the short-term dynamic response of the rotor system analyzed using the Fourier transform. The ability of short time Fourier transform to detect small cracks studied in the case of transient response [6].
Xuelien Chen (2016) examined a finite element model of a rotor system with a slant crack and two discs. Two types of linear and non-linear bearings were used to simulate bearings, while slant crack was modeled with time-variable stiffness. In this paper, the effects of two-disc eccentric phase difference have evaluated on the nonlinear responses of the rotor-bearing system in the operation of the steady state and starting operation. The results for lateral vibrations have shown that the resonant super-harmonic component associated with the first critical bending speed can be observed in the linear bearing state; however, in the case of nonlinear bearings, this component is not visible. For torsional vibrations, the super- harmonic component associated with the first natural torsional frequency can be seen in both linear and nonlinear bearing
forces. The sharp phase difference between the two disks can reduce the vibration of the rotor [7]. Jain et al (2016) evaluated the dynamic behavior of a multi-crack rotor system in both theoretical and experimental modes, taking into account variables such as shaft depth and location, as well as shaft rotational speed. In this work, the Langrangian method extension has been used to analyze the dynamic behavior of the shaft with several cracks and using the Langrangian formula. The effects of crack depth on the stiffness of the shaft and the natural frequencies of the rotor system have been analyzed in a test. Natural frequencies of the system have been obtained using a hammer impact test in static conditions. Also, the dynamic response of the rotor is analyzed by exhalation using OROS [8].
Guo et al. (2017) set up an experiment to study dynamic response of a rotor with a breathing crack as it passed through its 1/2, 1/3, 1/4 and 1/5 subcritical speeds. The vibration signals of the testbed during the coasting-up process were collected. Whirl orbit evolution at these subcritical speed zones was analyzed; in addition, the Fourier spectra obtained by FFT were used to investigate the internal frequencies corresponding to the typical orbit characteristics. The results showed that the appearance of the inner loops and orientation change of whirl orbits in the experiment were agreed well with the theoretical results had obtained previously. The presence of higher frequencies 2x, 3x, 4x and 5x in Fourier spectra showed the
Fig. 1. Shaft cracked element and side view of rotor-bearing system
In this regard, []is the mass matrix of the rotor system, []is the gyroscopic matrix, [] is the stiffness matrix, [] is the force vector, and {}is the dispacement vector of the whole system all reside in the coordinates, as well as is the angular speed of the system. The matrix coefficients of the Equation of motion of the rotor system can be introduced as following Equations:
56
0 1
0 2
2l
56
2l 4l2
0 0 4l2]
36
3l 4l
0 0
2
4l2]
0
0 0
3l 4l
2 0 ]
56
0 1
0 2
2l
56
2l 4l2
0 0 4l2]
36
3l 4l
0 0
2
4l2]
0
0 0
3l 4l
2 0 ]
156
0 156
0 -22l 4l2
causes of subharmonic resonances at these subcritical speed zones [9]. Czajkowski (2017) used modal analysis in which
1
1
[M ]= 22l 054 0
0 4l2
0 13l 1
(2)
would be able to simulate behavior of a non-rotating Jeffcott
0 54 -13l 0
cracked rotor. Simulation results presented changes in natural frequencies of the system with the changing angular position of the rotor. Those changes were observed as doubled natural frequency peaks in the rotors frequency responses. They appeared only for the cracked rotor and could be explained by
0 13l
[-13l 036
-3l2 0
0 -3l2 -2
shaft stiffness changes due to the opening and closing of crack faces under gravity [10].
0 36
0 -3l 4l2
Gupta et al. (2019) have been using of artificial neural
[M2]= 3l 00 4l2
(3)
network to introduce crack and unbalancing in a rotor system. In this study, they extracted a confusion matrix by statistical features. Then, by the help confusion matrix, the class of crack
-36 0 0 -3l 36
0 -36 3l 0 0
0 -3l -l2 0 0
and unbalance was decided [11]. Shah and Vakharia (2019) have been tested two shafts, one healthy and the other cracked. In the case of a cracked shaft, the experiment was performed in the presence of and without the presence of a balancing and in
[ 3l 0 0md 0 0 0
[M ]= [ 0 md 0 0]l2 -3l
order to observe changes in the vibrational pattern, the value and angle of the phase. Differences in vibration responses led
3 0 0 0 0
0 0 0 0
to the detection of crack and crack place. The Wavelet energy package is used to better locate the crack. The presence of crack
0
[M ] = [ 00 0 0
0 0 0
]
(5)
has led to changes in the dynamic behavior of the rotor. The 1x and 2x harmonics for responding to steady state are important parameters in the care of cracked rotor status [12].
-
ROTOR-BEARING SYSTEM MODELING
4 0 0 ID 0
0 0 0 ID
0
36 0
-3l 0 0
2
-
Healthy shaft elements, bearings and discs modeling
[G1]=C* 00
-3l 4l 0
36 -3l 0 0
(6)
The equation of motion for a rotor system like that is shown in Fig. 1 can be introduced as Equation (1):
-36 0
-3l 0
0 -3l 36
0 l2 3l
[M]s{q}s-[G]s{q}s+[K]s{q}s={Q}s (1)
[M]s{q}s-[G]s{q}s+[K]s{q}s={Q}s (1)
0 0 0 0
[G2] = [ 0 0 0 0 ](7)
{q}={q1,q2,q3,q4,q5,q6,q7,q
8}
(12)
8}
(12)
Due to presence of cracks in the rotor system, the stiffness of the system and systems force vector, as will be mentioned
0 0 0 IP
0 0 IP 0
12
0 12
follow, are constantly updated and changed with shift rotation. Conversely, other coefficients, including mass matrices, damping, and gyroscopic effects, remain constant. To obtain the above matrices in the general coordinates of the system using finite element principles, the fixed matrices of each
0
0
* 6l
-6l 0
4l2 0
4l2
(8)
element, disk and bearings are assembled[13].
[K1]=DAssuming isotropic bearings, the bearing damping
-12 0 0
-6l 12
coefficients are equal to c =c =0 and c =c =c to which c
0 -12 6l 0
0 12
uv vu
uu vv b b
0 -6l 2l2 0 0 6l
value that is referred as the bearing damping value.
[ 6l 0 0 2l2 -6l 0k k
(9)
-
Crack modelling in the rotor system
In this work, it is assumed that a transverse crack is
[K2]= [ uu uv]breathing. Moreover, Energy Release Rate (SERR) method is
kvu kvv
cuu cuv
(10)
applied. The flexibility matrix is written as Equation (13) for a bending element without crack [14].
c
c
[]= [vu
cvv ]
2 2 l3 0
0 l2
In the recent Equations A*=
EI
4l2 0
4l2]
Al
, =
4l2 0
4l2]
Al
, =
420
2Ar
120l
, = 2Ar
120l
and
3EI
0
l3
l
l
3EI –
2
2EI
(13)
=
3 respectively. It should be noted that the mass and
Cuc =
2EI 0
2
l 0 l l 0
stiffness matrices of the shaft element are symmetrical and the matrix of the gyroscopic effects of the shaft element is symmetrical skew. The vector {Q} can include any type of force acting on the rotor system, whether external forces applied to the shaft, to the disk, or to the support forces or to the forces caused by the unbalancing. In this paper, only the disk unbalancing force is considered. For a disk of mass "md" and eccentricity e, relative to its center, the vector of force {Qd} can be written as follows. It should be noted that in the following relations is the angle created by the torsional vibrations and
l2 – 2EI EI l
[2EI 0 0 EI ]is the length of each element of the shaft, which divides the total length of the shaft by the number of elements and the EI is the bending stiffness of the shaft. For cracked elements, the flexibility matrix is extracted as Equation (14).
0
0
]
34/r
c44/r
0
0
]
34/r
c44/r
c11.r 0 0
is the disc angular speed of the disk, so in these relationships t+ is the general angle of the period as shown following figure.
1 0
F
F
0
0
= [
0
0
c22.r
0
0
0
c33/r c c43/r
(14)
In the above matrix, F = Er2
, r is the radius of the shaft
0 (1-2)
and is the Poisson's coefficient. Additional flexibility coefficients created by cracks are available in the reference [15]. By multiplying reversing the flexibility matrix in the T transfer matrix and the TT transformer of this matrix, the stiffness matrix of each element of the shaft can be obtained.
Fig. 2. Transverse section of a shaft element
-1 0
0 -l
1 0 0
(15)
0
0 -1 0
0
0 1
p>0 0 0 -1
0
0 0
0
0 -1 0
0
0 1
0
0 0 -1
0
0 0
+mde mde
sin(t+) cos(t+)
+mde mde
sin(t+) cos(t+)
d T
-1 l
0 0 1 0
4*4
4*4
{Q }={Fx,Fy,0 ,0}
Fx=mde(+ )2cos(t+) Fy=mde(+ )2sin(t+)-
(11)
[K ] [K ]e
uc 8*8
=[T]8*4
*[c
uc]-1 *
(16)
4*4
4*4
0
0]
0
1
[T]T 4
*8
T]T
4*8
0
0]
0
1
[T]T 4
*8
T]T
4*8
It should be noted that the above relationships are derived
e
[K ] [K ]c 8*8
=[T]
8*4
*[cc]-1 *[
(17)
from the static equilibrium state, assuming that the reference is selected, so terms of forces that caused by the weight of disk have been ignored. Also in Equation (12), the displacement vector of the rotor system is defined for both sides of each element.
The total stiffness matrix of shaft can be extracted by adding all element has assembled matrix together. It should be noticed that procedures have described in the previous section are used to assemble the stiffness matrix. In this way, the stiffness matrix
of all elements except the element containing cracks is equal to each other and remains unchanged.
signal and the red graph is related to the cracked shaft signal with the desired depth.
uc
uc
[Ke] c
104*104
[Ke] c
104*104
(18)
In the above relationships, [Kc] is the stiffness matrix of the cracked element and [Kuc ] is the stiffness matrix of the healthy
element, and |Ke| is the assembled stiffness matrix of all the elements in the case when the crack is fully open.
-
Modeling of breathing behavior of crack in the rotor system
Breathing cracks in both fixed and rotary shaft coordinates have variable stiffness and during a full shaft rotation cycle, different modes can be assumed for the contact position of the crack edges with each other. It is a bit more difficult to analyze such cracks because the change in the stiffness of the breathing cracks itself depends on another factor. That is the weight of the shaft because in heavy shafts, static deformation is greater than the amplitude of vibrations, and linear and time-variable behavior can be considered for breathing of carck. However, in light or weightless shafts (compared to other components that are connected to the shaft, such as discs, blades, etc.), opening and closing situation of crack is a function of the vibration amplitude and it will be created nonlinear behavior [16, 17]. In general, the breathing mechanism is the result of the distribution of stress around the cracked area, which results from the following two categories of forces:
(A) Static forces such as weight or bearing reaction forces. (B) Dynamic forces such as unbalancing, etc.
To modelling breathing mechanism, the resulted that obtained by Darpe are used [14].
-
Obtaining the system response and analyzing the answers
For the rotor-bearing system with a mid-span disk including bellow properties:
Fig. 3. System responses in steady-state operation with healthy shaft and cracked shaft with various crack depths
Comparing the graphs in steady-state operation for healthy and cracked shafts, it can be seen that existence of cracks has caused a shock at a specific time. This shock has produced an increase in vibration amplitude at a specific time. Moreover, there is a linear correlation between crack depth and a rise in vibration amplitude. On the other hand, this time of impact can
kg
d
d
L=500*10-3m, m =5.5 kg, d=20*10-3m,=7800
m3
, E=2.08*
1011N
m2
be interpreted as resonance, after which the amplitude of the vibrations returns to its normal condition. In the following, for these cases diagrams of Fourier transform are illustrated. It
e=0.01*10-3
m
m, cb=100 N. m , kb=
105N
m , ID=0.01546m4
should be noted that to draw the Fourier transform diagram, two different modes are considered, the first mode is when the
We obtain the elements number of n=15 the system's response in the transverse direction (q ) and on the left, the element
horizontal and vertical axes are in linear scale, in which case the diagram is drawn with more magnification. The second case
containing the crack means
1
element 12, and for the steady-state
is related to the time it takes to create a better image than what
happens as a result of crack. The vertical axis was drawn on a
operation mode with rotational speed 0=80rad/s, and for primary angular acceleration = 30/2 by using the
"Houbolt" method. For more information on this numerical method and other available numerical methods for solving multiple equations, see the reference [18].
-
-
INVESTIGATING SYSTEM RESPONSES UNDER CRACK
logarithmic scale and the horizontal axis on a linear scale. In this case, for a better view, the diagram with a larger magnification is also drawn, which can be seen in Fig. 4.
-
Steady-State Analysis
The system responses are obtained by MATLAB, and then diagrams of signal for non-cracked and cracked modes with different depths are compared in Fig. 3. It should be mentioned that the blue lines in each figure is related to the healthy shaft
Fig. 4. Fourier transform for steady-state operation in cases of healthy and cracked shaft with various depths (the second diagram with magnification)
For the case where the vertical axis is plotted on a logarithmic scale, the Fourier transform diagrams of the rotor system with a healthy and cracked shaft are as follows.
Fig. 5. Fourier transform diagram when the vertical axis is on a logarithmic scale for the operation of a steady-state rotor mode with a healthy and cracked shaft with various depths (the second diagram with magnification)
From the recent diagrams, it is obvious that the Fourier transform diagram, when drawn without magnification, does not have the appropriate resolution in linear axis mode, but after zooming, it is observed that as a result of cracks and breathing behavior, the peak is related to 2x harmonics. It is easy to see that it was previously considered a sign of crack in the references. But it is observed in some cases that Fourier transform diagram for the rotor system is plotted with a vertical logarithmic axis. As a result, cracks and breathing behavior are created small peaks with periods of rotation equal to the period of shaft rotation. These small peaks increase in proportion to the growth in crack depth, and can be considered as a sign of cracks in the rotor system's response in steady-state operation mode. As the next step, from the responses of the desired system, the continuous wavelet transfrom with the mother function "Morlet" and for the scales of 1 to 128 has been done.
The diagram of the energy coefficients of the wavelet is also shown in Fig. 6.
Fig. 6. Energy diagram of continuous wavelet transform coefficients for rotor system with cracked shaft in steady-state operation and various crack dpths
By a glance in recent energy coefficients, it can be seen that existence of crack has caused some high-energy points. Moreover, intensity of these points are correlated with crack depth. Also a separation due to crack has created at the top of the diagram.
-
Transient Analysis
The responses of a rotor-bearing system are unsteady-state or transient when it starts from the stop mode (it has an incremental acceleration) as well as when it is turning off (it has a decreasing acceleration). Therefore, to analyze the transient operation, the starting up situation is considered. In this case, the time signal, Fourier transform (two modes) and continuous wavelet transform coefficients are compared. It should be noticed that the system is going through its first critical speed.
Fig. 7. System responses in transient operation with healthy shaft and cracked shaft with various depths
From the signal diagrams in transient state (i.e. Fig .7), it is practically impossible to extract any specific information, and more than the previous case, that is, the operation of the steady- state state, a more precise method is needed to analyze the signal. For this purpose, the Fourier transform diagrams for the desired system and at different crack depths are shown in Fig. 8 and Fig .9.
Fig. 8. Fourier transform for transient operation in cases of healthy and cracked shaft with various depths (the second diagram with magnification)
Fig. 9. Fourier transform diagram when the vertical axis is on a logarithmic scale for the operation of a transient rotor mode with a healthy shaft and cracked shaft with various depths (the second diagram with magnification)
Compared with Fourier diagrams that have plotted for steady-state operation above, Fourier graphs in the case of transient state do not show any profitable details concern to cracks effects. In the Fourier transform diagrams with Linear Scale Axis, there is no distinction between a healthy shaft signal and a cracked shaft in a normal display. In the magnified charts, just main peaks have some differences in amplitude. These differences are related to the critical speeds of the system. In the case of displaying Fourier transform with vertical axis on a logarithmic scale, there is some difference in amplitude at the beginning of the period.
In magnified graphs, some small peaks are visible. Moreover, these low-amount peaks are corresponded to the cracked shafts period of rotation. As the depth of the crack increases, these peaks can be more apparent, due to a growth in their amplitudes. However, for the transient signal of the single shaft in the desired rotor system, continuous wavelet transform with the "Morlet" mother function is used and the results are shown in the form of energy diagrams of the wavelet coefficients in Fig. 10. To have a more clear observation, the magnified graph of the coefficients energy is plotted along with the coloring change.
Fig. 10. Energy diagram of continuous wavelet transform coefficients for rotor system with cracked shaft and in transient operation (The second diagram with magnification and coloring change)
The recent graphs have been showing that due to crack some distortion are introduced. Additionally, in critical speeds points are more colorful than other times. It is also visible from
the diagrams shown in higher magnification, as the crack depth increases, the blue range increases, which is almost average energy points (according to the color line next to the diagram).These are completely separated for a relative depth of
0.35 these points.
REFERENCES
-
Kushwaha, N., Patel, V.N., Modelling and analysis of a cracked rotor: a review of the literature and its implications, Arch Appl Mech. 90 (2020) 12151245.
-
Carden, E. Peter, and Paul Fanning., Vibration Based Condition Monitoring: A Review, Structural Health Monitoring .3 (2004) 35577.
-
Sabnavis, Giridhar et al., Cracked Shaft Detection and Diagnostics: A Literature Review, The Shock and Vibration Digest. 36 (2004) 287-296.
-
Mobarak Hossain, Helen Wu, Crack breathing behavior of unbalanced rotor system: A Quasi-static numerical analysis, Journal of Vibroengineering. 20 (2018) 1459-1469.
-
Liong, R. T., & Proppe, C., Application of the cohesive zone model for the evaluation of stiffness losses in a rotor with a transverse breathing crack, J. Sound Vib. 332 (2013) 2098-2110.
-
Silani, M., Ziaei-Rad, S., & Talebi, H., Vibration analysis of rotating systems with open and breathing cracks, Applied Mathematical Modelling. 37 (2013) 9907-9921.
-
Chen, X., Nonlinear responses analysis caused by slant crack in a rotor- bearing system, Journal of Vibroengineering. 18 (2016) 4369-4387.
-
Jain, A. K., Rastogi, V., & Agrawal, A. K., Experimental investigation of vibration analysis of multi-crack rotor shaft, Procedia engineering. 144 (2016) 1451-1458.
-
Guo, C., Yan, J. & Bergman, L.A., Experimental Dynamic Analysis of a Breathing Cracked Rotor, Chin. J. Mech. Eng. 30 (2017) 11771183.
-
Mariusz Czajkowski, Baej Bartoszewicz , Zbigniew Kulesza, Modal analysis of a rotor with a cracked shaft, Journal of Vibroengineering. 19 (2017) 150-159.
-
Gupta R.B., Singh S.K., Detection of Crack and Unbalancing in a Rotor System Using Artificial Neural Network, In: Prasad A., Gupta S., Tyagi
R. (eds) Advances in Engineering Design. Lecture Notes in Mechanical Engineering. Springer, Singapore(2019).
-
Shah, B. A., & Vakharia, D. P., Testing for detection of crack in rotor using vibration analysis: an experimental approach., International Journal of Quality & Reliability Management. 36 (2019).
-
Bachschmid, Nicoló, Pennacchi, Paolo, Tanzi, Ezio, Cracked Rotors, A survey on static and dynamic behavior including modelling and diagnosis, Springer, 2010.
-
A.K.Darpe, K.Gupta, A.Chawla, Coupled bending, longitudinal and torsional vibrations of a cracked rotor, J. Sound Vib. 269 (2004) 33-60.
-
Papadopoulos, C. A., & Dimarogonas, A. D., Coupled longitudinal and bending vibrations of a rotating shaft with an open crack, J. Sound Vib. 117 (1987) 81-93.
-
Stoisser, C. M., & Audebert, S., A comprehensive theoretical, numerical and experimental approach for crack detection in power plant rotating machinery, Mechanical Systems and Signal Processing. 22 (2008) 818- 844.
-
Green, I., & Casey, C., Crack detection in a rotor dynamic system by vibration monitoringpart I: analysis., J. Eng. Gas Turbines Power. 127 (2005) 425-436.
-
Singiresu, S. R. , Mechanical vibrations, Addison Wesley, 1995.