
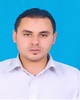
- Open Access
- Authors : Abdelaziz. El. Abdelsalam , Magdi Ahmed El Hadiri , Naji S. Abdelwanis
- Paper ID : IJERTV12IS010023
- Volume & Issue : Volume 12, Issue 01 (January 2023)
- Published (First Online): 16-01-2023
- ISSN (Online) : 2278-0181
- Publisher Name : IJERT
- License:
This work is licensed under a Creative Commons Attribution 4.0 International License
Investigating The Effect of SMAW Parameters on The Hardness of Commercial Carbon Steel
Abdelaziz. EL. Abdelsalam *, Magdi Ahmed El Hadiri** Naji S. Abdelwanis ***
-
College of Mechanical Engineering Technology-Benghazi, Benghazi, Libya
** College of Mechanical Engineering Technology-Benghazi, Benghazi, Libya
*** Industrial and Manufacturing Systems Engineering, University of Benghazi, Benghazi, Libya
Abstract:- This work studies the effect of some parameters of shield metal arc welding (SMAW) process, namely the welding current and electrode type, on the hardness of Mild Steel by utilizing a statistical approach. Specimens having dimensions of 200 mm× 50 mm× 4 mm, which were welded by shield metal arc welding (SMAW) with single V-Butt joint, were used for investigation. Three different types of electrodes, E6010, E6013 and E7018 and three levels of welding current 90A, 110A and 130A were selected to carry out the experiment.. Statistical analysis using descriptive charts were employed to examine the hardness of the welded metal, the result showed that regardless of the type of the used electrode, when the amount of current increase, the hardness increases too, and the optimum value of hardness was produced when using the electrode of type E7018 at welding current of 130A with 76.5 HRC.
Keywords:- SMAW, Rockwell hardness test, welding current, electrode type.
-
INTRODUCTION.
Steel is an important engineering material that exist in many practical applications in every days life. It has been applied in many areas such as vehicle parts, truck bed floors, automobile doors, domestic appliances etc [1]. Steel is known to be very versatile; it can be formed into desired shapes by processes such as rolling and forging; it can be treated to attain a wide range of mechanical properties which enable it to be used for an enormous number of applications [2].
On the basis of the percentage of carbon content, steel is divided into low carbon steel, medium carbon steel and high carbon steel. Low carbon steel has carbon of less than 0.3%, medium carbon steel has carbon content of 0.0.3% to 0.69% and high carbon content have carbon content of 0.7% to 2.2%. An interesting fact in connection with the above percentages is that, steel with carbon content that is below 0.08%. categorized as dead or mild steel whose properties are similar to iron [3]. Its well known that as the carbon content increases the hardness also increases, the metal becomes harder and stronger but less ductile and more difficult to weld.
Joining processes considered as one of the most important techniques to evaluate steel components parts. Welding, which is a joining process, is considered one of the most important means of fabrication available to industry.
The Deutche Industrie Normen (DIN) defined the welding as, a metallurgical bond on metal joints or combination that carried out in melting or liquid conditions". Welding is an activity of combining two or more parts of objects by the application of heat, pressure or a combination of the two in such a way that it blends as a single object [4].
Many problems that inherent to welding can be avoided by proper consideration of the particular characteristics and requirement of the process. Its essential to properly select welding parameters for a given task to provide a good weld quality [5]. The major types of welding parameters are current (effecting the heat input), voltage usage, polarity, welding filler type, welding filler size, are length, electrode angle, arc travel speed and welding technique. Perhaps the most commonly used welding process is the shielded metal arc welding (SMAW) in the electric arc welding group [6]. The Shielded Metal Arc Welding SMAW is a welding process, widely used in the construction industries and in repairing, as it offers more flexibility and portability. it is also known as stick welding, because it utilizes a consumable electrode which is coated with protective coating called flux which provides the shielding of joint. During welding, the flux coating on the electrode starts to burn that causes the release of shielding gas which protects the base metal and weldment from the atmospheric contamination [7].
-
EXPERIMENTAL WORK
This part describes the methodology and work plan used in executing the research work and the challenges encountered.
In this work three different grades of welding electrode E6010, E6013 and E7018 were used. Three different levels of welding current 90,110 and 130 Amperes were applied. The experiment was carried out with the object of knowing how these individual variables affect the hardness of the welded joint and the interaction effect between these factors.
The main material used in this research work is sheet of mild carbon steel with the dimension of (1000 mm * 200 mm *4 mm) obtained from local workshops in Benghazi. The chemical composition of the basic material is presented in table 1.
Table (1) The chemical composition of the base material
Element
Fe%
Mn%
Pb%
C%
Content
99.095
0.782
0.091
0.032
-
Sample Preparation:
The base metal sheet of 4 mm thick was cut into 36 equal pieces with dimensions of 200×50 mm each using CNC plasma cutting machine.
The samples for welding were further cut into two equal parts, cleaned using abrasive sand paper to eliminate all possible coatings, corrosion or rust that may have accumulated on the material, and chamfered to produce 30° half groove angle on one side with the aid of a grinding machine to have smooth and uniform surfaces.
-
Welding procedure.
The welding was carried out using shield metal arc welding process with 36 specimens, the plates properly clamped to avoid misalignment during welding process. Before welding, surface of each specimens was cleaned using acetone in order to eliminate surface contamination, welding was applied to fuse the two flat plates together with an included angle of 60. Welding of butt joint samples in horizontal position was performed continuously. Single-pass; autogenous, bead-on-plate SMAW welds were made along the center line of the specimens as shown in figure 2.
Figure (2) specimens welded using SMAW process
-
Hardness Testing
Hardness testing of welding joints was performed in accordance to ASTM E18-79 standard using Rockwell Testing Machine. The sample specimen was placed with the surface on the anvil, and slowly turning the hand wheel until the specimen was raised to touch the indenter. The numbers were read directly from the dial indicator and converted to the Rockwell number. Hardness Test was done in a row to include the Base Material, Heat Affected Zone and Weld Metal; the readings were taken from the center of the fusion welding zone (point 0) towards the base material with equal space of 5 mm on both sides of the weld joint and each point was taken three times up and down at a distance of 15 mm to reduce statistical errors. Schematic representation of Butt and Groove welded joint with the locations of hardness testing is shown in figure 3.
Figure 3. Schematic representation of Butt welded joint with the locations of hardness testing
-
-
RESULTS AND DISCUSSION The results of the hardness test are summarized in table 1.
Table 1. Rockwell hardness test results.
lectrodes
Current
Rockwell hardness test (HRC)
-20
-15
-10
-5
0
5
10
15
20
E7018
130
53.1
53.9
54.6
60.4
76.6
58.2
54
53.7
50.6
110
51
51.1
52.7
55.4
64
54
51
50.7
50
90
46.6
47.5
49.8
50.6
57.9
53.5
49.8
49.3
48.3
E6013
130
40
47.1
48.2
53.9
66.5
55.1
48.7
47.5
47
110
49.3
51.5
51.9
52.8
60.2
54.8
48.5
45
43.2
90
42.9
46.4
48
50.1
58.1
52
47
49.1
47.3
E6010
130
48.5
51.9
53.9
55.4
68.1
57.6
54.8
52.6
49.2
110
48.4
50
51.7
53.4
66.7
56.8
53.5
51.7
48.3
90
47.9
49.1
50.4
52.1
63.4
53.2
51.7
49.4
48.6
From the table 1 it can be observed that, the hardness of weld metal was higher than base metal in all specimens. After a certain distance these values decrease almost to the hardness of the base material. The variation in properties across the weld can be attributed to several issues, essentially to residual stresses just created after welding, chemical composition of filler wire was higher than the base metal, very rapid heating and cooling of weld metal and high solidification rate.
ROCKWELL HARDNESS TESTE
-
Effect of Weld Current on the hardness of the welded metal
ELECTRODE E 7018
80
60
40
20
0
– 20 – 15 – 10 – 5
0
5 10 15 20
130 A
110 A
90 A
Figure 4. electrode type (E7018) & varying current.
ELECTRODE E6013
100
HRµ
50
-20
-15
-10 -5 0
0
5 10 15 20
130 A 110 A 90 A
Figure 5. electrode type (E6013) & varying current.
ELECTRODE E6010
80
70
60
HRµ
50
40
30
20
10
0
-20
-15
-10 -5 0
5 10 15 20
130 A 110 A 90 A
Figure 6. electrode type (E6010) & varying current.
The influence of the welding current in the weld metal can be seen in table 1. and figures 4, 5 and 6 which show that the hardness of the welded samples increased slightly with the increase of the welding current from (90 A to 130 A). This phenomenon can be related to structural changes of weld metal during solidification and chances of formation of defect in the various welding conditions. The weldment increased hardness value may be due to carburization. These increased hardness values indicate that the welded joint will be prone to brittleness than the base metal; hence post welding heat treated will be required to optimize the mechanical property [7].
-
Effect of Electrode type on the hardness of the welded metal
Electrodes
Current
-20
-15
-10
-5
0
5
10
15
20
E7018
130 A
53.1
53.9
54.6
60.4
76.5
58.2
54
53.7
50.6
E6013
40
47.1
48.2
53.9
66.6
55.1
48.7
47.5
47
E6010
48.5
51.9
53.9
55.4
68.1
57.6
54.8
52.6
49.2
The influence of the type welding electrode, in the weld metal at current 130 A summarized in Table 2. Table 2. Effect of the electrode type on the welded joint of mild steel at 130A
the hardness distribution in different zones; weld zone (FZ), heat affected zone (HAZ) and base metal (BZ) Figure 7.
CURRENT 130 A
90
80
70
60
HR
50
40
30
20
10
0
– 20
– 15
– 10 – 5 0
5 10 15 20
E7018 E6013 E6010
Fig7. fixed current (130 A) & varying electrode type
The hardness value with E7018 is higher than the other electrodes at the weld metal zone. while, E6013 produces the lowest hardness value on the weld metal which is about 66.6 HRC. However, E7018 produces the highest average hardness value which is about 76.5 HRC. While, Concerning the effect of welding electrode on hardness at welding current 110 A summarized in table 3.
Table 3 Effect of the electrode type on the welded joint of mild steel at 110A
Electrodes
Current
-20
-15
-10
-5
0
5
10
15
20
E7018
110 A
51
51.1
52.7
55.4
64
54
51
50.7
50
E6013
49.3
51.5
51.9
52.8
60.2
54.8
48.5
45
43.2
E6010
48.4
50
51.7
53.4
66.7
56.8
53.5
51.7
48.3
nevertheless, the hardness distribution in different zones; weld zone (FZ), heat affected zone (HAZ) and base metal (BZ) in the weld metal at can be seen in Figure 8.
CURRENT 110A
80
70
60
HR
50
40
30
20
10
0
-20
-15
-10 -5
0
5
10
E7018
E6013
15 20
E6010
Fig8. fixed current (110 A) & varying electrode type
The hardness value with E6010 is higher than the other electrodes at the weld metal zone. while, E6013 produces the lowest hardness value on the weld metal which is about 60.2 HRC. However, E6010 produces the highest average hardness value which is about 66.7 HRC. Furthermore, the influence of the type welding electrode at current 90 A in the weld metal can be seen in Table 4.
Table 4. Effect of the electrode type on the welded joint of mild steel at 90A
Electrodes
Current
-20
-15
-10
-5
0
5
10
15
20
E7018
90 A
46.6
47.5
49.8
50.6
58.9
53.5
49.8
49.3
48.3
E6013
42.9
46.4
48
50.1
57.1
52
47
49.1
47.3
E6010
47.9
49.1
50.4
52.1
63.4
53.2
51.7
49.4
48.6
the hardness distribution in different zones; weld zone (FZ), heat affected zone (HAZ) and base metal (BZ) in the weld metal at can be seen in Figure 9.
CURRENT 90A
80
HR
60
40
20
0
-20
-15
-10 -5 0
5 10 15 20
E7018 E6013 E6010
Fig9. fixed current (90 A) & varying electrode type
The hardness value with E6010 is higher than the other electrodes at the weld metal zone. while, E6013 produces the lowest hardness value on the weld metal which is about 57.1 HRC. However, E6010 produces the highest average hardness value which is about 63.4 HRC.
-
-
CONCLUSION
-
The effect of varied welding parameters was examined and discussed in order to be able to predict the behavior of welded commercial carbon steel samples using shield metal arc welding. The results showed that the selected welding parameters have significant effect on the mechanical properties of the welded samples.
The hardness of the base metal before welding was recorded to be 47 HRC and after applying the welding process increased around the joint area (HAZ -FZ). As the welding current increased the hardness of the welded joint material increased.
The effect of welding electrode was obvious during this research, whereas, the hardness value with E7018 is higher than the other electrodes at the weld metal zone which is about 76.5 HRC at welding current 130A, while, E6013 produces the lowest hardness value on the weld metal which is about 66.6 HRC at 90A.
REFERENCES
[1] Talabi, S.I.a, Owolabi, O.B.b, and others. (2014). Effect of welding variables on mechanical properties of low carbon steel welded joint. Advances in Production Engineering & Managemen,Vol 9,181-186. [2] M. A. Bodude1, I. Momohjimoh. (2015). Studies on Effects of Welding Parameters on the Mechanical Properties of Welded Low-Carbon Steel.Journal of Minerals and Materials Characterization and Engineering, Vol3,142-153.
[3] Randy Chiong, Noman Khandoker, Sumaiya Islam, Edwin Tchan. (2019). Effect of SMAW parameters on microstructure and mechanical properties of AISI 1018 low carbon steel joints:An experimental approach. IOP Conf. Series: Materials Science and Engineering, 495 (2019) 012093. [4] Jasman, Irzal and Pebrian. (2018). Effect of Strong Welding Flow on the Violence of Low Carbon Steel Results of SMAW Welding with Electrodes 7018. Teknomekanik Vol.1, 24-31. [5] Ikechukwu Owunna, Aniekan E.Ikpe, and J. I. Achebo. (2018). 3D Finite Element Modelling of Weld Bead Penetration in Tungsten Inert Gas (TIG) Welding of AISI 1020 Low Carbon Steel Plate. European Mechanical Science, Vol 2, 96-105. [6] Tewari, S. P., Gupta, A., Prakash, J. (2010). Effect of Welding Parameters on the Weldability of Material, International Journal of Engineering Science and Technology, 2(4): 512-516. [7] S. Farrukh Haider 1, M. M. Quazi.(2019). Effect of Shielded Metal Arc Welding (SMAW) parameters on mechanical properties of low-carbon, mild and stainless-steel welded joints: A review. Journal of Advances in Technology and Engineering Research, 5(5): 191-198 [8] Mikell P. Groover. FUNDAMENTALS OF MODERN MANUFACTURING Materials, Processes, and Systems, 4th Edition. 2010, John Wiley and Sons, Inc. USA.