
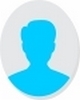
- Open Access
- Authors : Arif Mohmad Bhat
- Paper ID : IJERTV11IS080110
- Volume & Issue : Volume 11, Issue 08 (August 2022)
- Published (First Online): 01-09-2022
- ISSN (Online) : 2278-0181
- Publisher Name : IJERT
- License:
This work is licensed under a Creative Commons Attribution 4.0 International License
Influence of Coarse Aggregate Shape Factors on Bituminous Mixtures
Arif Mohmad Bhat1
1 Post Graduate Scholar, Mewar University, Chittorgarh, Rajasthan, India.
Abstract – Aggregates are the major component in pavement construction. Aggregate qualities such as size, shape, texture, influence the serviceability and durability of bituminous roads. The shape of aggregate particles has a significant effect on functioning and performance of bitumen pavement. The research represents a laboratory study of different particle shape of aggregates such as cubical, disc, rod and blade. Surface textures of rough and smooth were used. Low medium and high aggregate gradations are used dense bituminous mixes were studied with different proportions of different shapes of coarse aggregates. The cubical particles were desirable and best rutting resistance. The mixture cubical and rod shaped aggregates has showed good result on stability. Flaky and elongated particles showed low compatibility and high breakage. The particle index was shown to be an adequate measure of the combined contribution of particle shape, angularity and texture to the stability of the aggregate. The object of the study was not only to investigate the shape factors effect on bituminous mixes but also obtain a better understanding of various factors responsible for mixture strength. Various types of aggregates has been tested and their combinations and was found that different aggregate combination gave different strengths and different workability and stability.
Keywords: Aggregate, Rutting, Texture, Shape, gradations, breakage etc.
1 INTRODUCTION
Permanent Deformation or rutting of bituminous pavement is one of the major concerns of highway engineers. Excessive tire pressure is the main cause of deformation of the pavement. Besides excessive loading, the improper mixing of asphalt content, coarse aggregate content, shape and texture results in the deformation of pavement surfaces bituminous mixes consists of 90-95 % of coarse aggregate by weight. They constitute the maximum of pavement volume. Thus the study of aggregates is proved to be beneficial for the pavement designs. Aggregates which are flat and elongated tends to break during mixing and placing of pavement. Under the roller they also have a tendency to break under huge loads. Blade shaped aggregates accounts for very large void ratio which also results in deformation of pavement surface. Therefore aggregate shape is one of the most important property of aggregate which has o/to be taken in consideration before designing the mix in order to avoid pavement failure and deformation
There are two types of aggregates, one is naturally occurring and another is manufactured from rocks taken from quarries. Aggregates can be distinguished in three shape properties.
-
Shape
-
Angularity
-
Texture
Below diagram shows the difference between angularity shape and texture of the aggregates
Figure. 1: Aggregate
Aggregate characteristics are very complex and cannot be determined adequately by any single test. As a result conflicting results have been reported on how aggregate shape reforms influence the quality of bituminous mixtures. Visual representation is the most common method of judging the shape of aggregate.
1.2 IMPORTANCE
Aggregate shapes influence the serviceability and performance of the pavement to a great extent. Therefore it is important to select proper shape and size of aggregate in order to increase the functionality of pavement and to increase the service life of pavements. In this research it is known that different particle shapes constitute different properties when tested. Flat and elongated particles tends to break during mixing, compacting and under the influence of traffic loads. Cubical particles showed great resistance to breakage under heavy loads. Blade shaped particles large void ratio which may later get filled and can deform the pavement surface, when subjects to repeated traffic loads. And also due to these voices the workability of the mix reduced. Hence the study of effect of blade shaped aggregates is essential and important. Lower the percentage of blade shaped aggregates, greater will be the workability and greater will be the stability of the pavement. Kurtz and sebaaly (1992) found a direct correlation between the potential of pavement mixes and the shape and texture of the coarse aggregate particles. Li and kett (1967) founded in their study that flat and elongated particles could be permitted in a mixture without adverse effect on its strength.
2 MATERIALS AND METHODS:-
The main goal of this research work was to investigate the effect of coarse aggregate shape and texture on the performance of the bituminous pavements.
-
Aggregate
Aggregates influence greatly in the load transfer capacity of pavements. Therefore it is important that they should be tested before the construction. Aggregate should not only be strong and durable but they should also have proper shape and texture and also proper size in order to be get used in the mix. Many testes are also done on aggregates such as for water absorption, strength toughness and shape. The coarse aggregate was sieved and partitioned into four size fractions, namely 25 to 20mm, 20 to 12.5mm, 12.5 to 7.5mm and 7.5 to 4.75mm.
Below figure shows the different types of aggregate shape particles used in this study.
Figure.2: Aggregate Shape Used In This Study
-
Rounded Aggregates
Figure.3: Rounded Aggregates
They are the natural aggregates available on the seashore in the form of gravel. They results in the minimum percentage of void ratio (30%-40%) and gives more workability of the bituminous mix. Due to their rounded shapes they are very
poor in interlocking behavior which results in weak bond in the mix and thus gives less strength. Hence they are not preferred in high strength mix.
-
Irregular Aggregates
They are shaped by attrition but are not fully rounded, these consists of small stones and gravel, and offer reduced workability to rounded aggregate. They will develop strength slightly lower than angular aggregates the irregular shapes are formed between the aggregates. The bondage between the aggregates is very low due to friction between the aggregates is very low due to its irregular shape and it develop low workability of concrete
Figure. 4: Irregular Aggregates
-
Elongated Aggregates
In elongates aggregates, the length of the aggregates is higher than its width. It is having low compression strength and recommended for concrete. If we use the elongated aggregate in concrete, the voids ratio will become high compared to the other aggregates.
Figure.5: Elongated Aggregates
-
Flaky Aggregates
The flaky aggregates are having a very light thickness, and it can easily crack. Due to its lower workability, it is not used in mix and it also gets broken da to its minor thickness. The flaky and elongated aggregates are having less thickness. They gives less compressive strength to the mix and is not used.
Figure .6: Flaky Aggregates
-
-
Bitumen Binder
Since the prime goal of the study was to investigate the effect of coarse aggregate shape on bitumen pavement, asphalt was limited to one type and thus, was not a factor in the results obtained from the study. The bitumen binder component of a bitumen makes up about 6-7 % of the total bitumen mixture and binds the coarse aggregate together.
-
Shape of Aggregates
Crushed limestone was used to produce two types of aggregate gradations. Aggregates which may fall into a particular size are rounded, cubical elongated and flaky. It is known that elongated and flaky have less strength and durability than cubical and rod shaped aggregates and hence they are much preferred and elongated and flaky shaped aggregated should be avoided. The most common method of judging the shape of aggregate is by visual examination.
-
Tests For Shape
The particle shape of the aggregate is determined by the percentage of flaky and elongated particles in it. Aggregates which are flaky and elongated are the flakiness index is defined as the percentage by weight of aggregate particles whose least dimension is less than 0.6 times their mean size. Test procedure had ben standardized in India (IS: 2386part-1). The elongation index of an aggregate is defined as the percentage by weight of particles who greatest dimension is
1.8 times their mean dimension. This test is applicable to aggregates larger than 6.3 mm. This test is also specified in (IS: 2386 Part-1). However there are no recognized limits for the elongation index.
-
Particle Index of Aggregates
Particle index is the combined effect of particle shape and surface texture of aggregates were determined in accordance
with ASTM test method for index of aggregate particle shape and texture (D3398). The equipment consists of a cylindrical test mold 152mm and 178mm high and steel rod 16mm diameter and 610mm long with one side rounded hemispherical for rounded tip.
The aggregate used for this test is single size aggregate fraction washed and oven-dried is filled in three equal layers. Each layer is compacted with 10 equally distributed blows of tamping rod dropped from a height of 51 cm above the aggregate surface. Now the procedure was repeated with only 50 blows this time on each layer. The weight of the contents of the mold in each case was determined and the corresponding percentage of voids was calculated using the bulk specific gravity of each aggregate fraction.
The below equation gives the value of the pi
PI = 1.25V10 0.25V50 32
Where. V10 = percent voids in the aggregate compacted with 10 blows per layer.
V50 = percent voids in the aggregate compacted with 50 blows per layer.
Below table shows the calculated value of particle index of different size of aggregates. The weighted value is the product of the aggregate grading times the corresponding particle index of each size group. The particle index is the summation of the weighted values, which are 18.0, 15.5, 14.2, 12.9 and
15.5 for cubical, rod, disk, blade and dense aggregates respectively.
A higher particle index value indicates that the aggregate is close to cubical in shape. The flat and elongated particle index is close to lower particle index.
Table 1: Particle Index of Different Shape of Aggregate
-
Particle shape analysis
It was carried out in terms of elongation ratio, flatness ratio, shape factor, and sphericity by direct methods. The shape
parameters can be determined from the following equations. The mean value for each aggregate size is listed in Table below.
Table 2: Aggregate Geometric Characteristics From Direct Measurement.
Shape
Elongation Ratio
Flatness Ratio
Shape Factor
Sphericity
CUBE
0.80
0.74
0.66
0.86
ROD
0.72
0.70
0.62
0.88
DISC
0.85
0.59
0.59
0.87
BLADE
0.73
0.57
0.48
074
Normal Aggregates
0.75
0.60
0.51
0.76
The above data indicates that the higher the shape factor, the aggregate is more likely to be cubical The flatness, elongation ratio values obtained for cubical shape aggregates are 0.73, 0.81 and both the values are larger than 2/3. Sphericity of blade shape aggregate is low comparative to the other shapes and the sphericity value higher
indicates the roundness of the aggregate. Shape factor is generally in between 0.3 to 0.8 for pavements. For all the shapes it falls within the limits only.
Marshall Design values
The Marshall test is a popular and proven method to measure the load and flow rate asphalt specimens, beginning with compaction into mounds using manual or automated Marshall compacters, and conditioned in water bath at the specified temperature The Marshall test is a routine test that enables one to determine strength indexes such as stability and flow for the design of a hot mix asphalt Mixtures. Other Mixtures design criteria such as Density, air voids, Voids filled with bitumen & voids mineral aggregate are also Obtained from this test below table list to mixture Characteristics of Different aggregate shapes.
TABLE 3: MARSHALL DESIGN VALUES OF DIFFERENT SHAPES OF AGGREGATES
ROD
DISC
size
10
20
30
40
50
10
20
30
40
50
Stability
1406.25
1478.62
1398.85
1400.80
1452.00
1455.43
1504.57
1422.73
1437.17
1431.41
Flow
2.24
2.20
2.12
1.79
1.59
2.42
2.52
2.19
2.00
1.98
Air voids
4.02
4.06
4.03
4.00
3.88
3.45
3.73
3.69
4.19
4.16
Density
2.455
2.459
2.464
2.467
2.478
2.468
2.467
2.473
2.465
2.470
VFB
72.77
72.57
72.77
72.35
73.56
75.84
74.28
74.53
71.91
72.10
VMA
14.78
14.81
14.79
14.87
14.68
14.30
14.52
14.48
14.93
14.89
CUBE
BLADE
size
10
20
30
40
50
10
20
30
40
50
Stability
1601.23
1622.52
1628.35
1662.89
1611.48
1105.14
1045.23
1097.08
1108.97
1237.03
Flow
2.32
2.89
1.98
1.99
1.89
2.07
1.70
1.62
2.09
2.33
Air voids
3.32
3.66
3.65
3.89
4.10
3.35
3.52
3.54
3.56
3.80
Density
2.540
<>2.560 2.540
2.540
2.580
2.502
2.506
2.541
2.552
2.593
VFB
76.51
74.63
74.69
73.40
72.28
76.37
75.44
75.31
75.21
73.94
VMA
14.14
14.42
14.41
14.61
14.79
14.17
14.32
14.34
14.35
14.58
DBM
Stability Flow
Air voids
Density
VFB
VMA
1502.85
3.2
3.98
2.87
82.25
15.23
-
Flakiness Index and Elongation Index Test
-
The shape test of aggregates determines the shape and size of particle.
-
Size & shape of aggregates directly has impact on strength of concrete, bond strength, workability of concrete, cement requirement and cost required for concrete.
-
Rounded, elongated and flaky aggregates offer good workability but less bond strength and mechanical strength.
-
Angular & irregular aggregates offers lesser workability but good bond strength and mechanical strength.
-
There two terminologies related to the shape of aggregates and its test.
-
Flakiness Index
-
Elongation index
-
-
Aggregates are called Flaky & Elongated aggregates when its length is larger than its width and width is larger than its thickness.
-
I.e. length>width>thickness.
-
Flaky & elongated aggregates are not suitable for concreting. It does not form a very good bond with concrete. These are generally obtained from poorly crushed rocks.
Flakiness Index:
-
The flakiness index is defined as the, percentage of aggregates by weight whose least dimension is less than 0.6 times than mean size.
-
The procedure to find out flakiness index is as per IS: 2386 part 1.
-
The apparatus used for this test is as shown below
Figure7: Thickness Gauge
Elongation Index:
-
-
The Elongation index is defined as the, percentage of aggregates by weight whose larger dimension (generally length) is 1.8 times more than mean size.
-
This test is application to aggregates lager than the 6.3mm size.
-
The procedure to find out Elongation index is as per IS: 2386 part 1.
-
The apparatus (Elongation gauge) used for this test is as shown below.
Figure8: Elongation Gauge
Apparatus & Equipment:
-
A standard thickness gauge
-
A standard length gauge
IS sieves of sizes 63, 50 40, 31.5, 25, 20, 16,
12.5,10 and 6.3mm
-
A weighing balance of capacity 5kg, readable and accurate up to 1 gm.
Recommended Values of Flakiness Index and Elongation Index
-
Flaky & elongated aggregates are not suitable for concreting. It does not form a very good bond with concrete. These are generally obtained from poorly crushed rocks.
-
Thus avoid this kind of aggregates in pavement as well.
-
IRC recommendations for maximum limits of flakiness index for different types of pavements are as given.
TABLE.4: RECOMMENDED VALUES OF FLAKINESS INDEX AND ELONGATION INDEX IN DIFFERENT TYPES OF PAVEMENTS
S.No
Type of Pavement
Maximum Limit of Flakiness Index IN %
1
Bituminous carpet
30
2
Bituminous Asphaltic concrete
25
3
Bituminous Penetration Macadam
Bituminous Surface Dressing (Single Coat, Double Coat & Percolated) Built up spray grout
25
4
Bituminous Macadam
25
5
WBM base course and surface course
15
-
-
Impact Test Of Aggregate (Aggregate Impact Value)
-
Aggregate impact value is defined as the ability of aggregates to have resistance against shock and impact, toughness.
-
It also can be defined as the load at which aggregates start cracking due to the impact and shocking.
-
In Impact test of aggregate, the aggregates are tested to find out toughness of aggregate to absorb shock and impact.
-
Impact and shock can break the aggregates and it can leads to pavement failure.
Impact Test: (As per IS: 2386(Part IV)-1963 Methods of test for aggregate for concrete)
IS: 2386(Part IV)-1963 Methods of test for aggregate for concrete.
Apparatus & Equipment:
-
Impact Testing machine
-
Sieves of size 12.5mm & 10mm.
-
Cylindrical metal measure
-
Tamping Rod
-
Balance (0-10kg)
Oven (3000c).
Figure. 9: Aggregate Impact Value Apparatus
Sample Preparation of aggregates:
-
Aggregate sample should be passed through the 12.5mm IS sieve and retain on the 10mm IS sieve.
-
The aggregate sample should retained on 1.mm sieve. And oven dried for at least 4 hours in oven at temperature 0f 110º C.
-
The cylindrical steel cylinder is filled with sample filled about 1/3 full and tamped with rod with 25 strokes. Further fill the cylinder again with 1/3 quantity of sample and tamped with rod with 25 strokes. Repeat the same procedure one more time.
-
-
Table.5 -Maximum Allowable Impact Value Of Aggregate For Different Types Of Pavements
5 CONCLUSION
Four different types of aggregates were used to determine the effect of shape of particles in bituminous mixes.
It is observed from the study that stability increase with increase in the proportion of cubical aggregates. Cubical aggregates exhibit greater interlocking and internal friction which results in higher stability than flat thin and elongated aggregates. The stability and voids filled in bitumen increases with the increase in the percentage of cubical aggregates in the mix. When we increase in the proportion of blade type aggregates, the air voids and voids in mineral aggregates increases. Mixes prepared with replacement of 20% cubical, blade, rod and disk aggregates shown higher stability values. The particle index (PI) was shown to be an adequate measure of the combined contribution of particle shape, angularity, and surface texture to the stability of an aggregate. The particle shape also determined how aggregate packed into a dense configuration and also determines the internal resistance of the mix.
The shape tests give only a rough idea of the relative shapes of aggregates. Flaky and elongated particles should be avoided in pavement construction, particularly in surface course.
6 REFRENCES
[1] .ASTM :D3398-00,Standarad test method for index of aggregate particle shape and texture [2] Boutilier, O.D. (1967). A study of the relation between the particle index of the aggregate and the properties of bituminous aggregate mixtures. Proceedings of Association of Asphalt Paving Technologists, 36, 157- 179 [3] Brown, E.R., McRae, J.L, and Crawley, A.B. (1989) Effect of aggregate on performance of bituminous concrete. ASTM STP 1016, Philadelphia, 34-63. [4] D. Sakthibalan (2007) Influence of Aggregate Flakiness on Dense Bituminous macadam & Semi Dense Bituminous Concrete. [5] Fletcher, T., Chandan, C., Masad, E., Sivakumar, K. (2002), Measurement of Aggregate Texture and Its Influenc on HMA Permanent Deformation, Journal of Testing and Evaluation, American Society for Testing and Materials, ASTM, Vol. 30, No. 6, 524-531.
S.No |
Types of Pavements |
Aggregate Impact Values (Max.) |
1 |
Water Bound Macadam (WBM) Sub- Base Course |
50 |
2 |
Cement Concrete, Base Course |
45 |
3 |
|
40 |
4 |
Bituminous macadam, base course |
35 |
5 |
|
30 |