
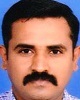
- Open Access
- Authors : Mr.Santosh Pandurang More
- Paper ID : IJERTV13IS030117
- Volume & Issue : Volume 13, Issue 03 (March 2024)
- Published (First Online): 23-03-2024
- ISSN (Online) : 2278-0181
- Publisher Name : IJERT
- License:
This work is licensed under a Creative Commons Attribution 4.0 International License
Implementation of Sustainable Manufacturing
Published by : http://www.ijert.org
International Journal of Engineering Research & Technology (IJERT)
ISSN: 2278-0181
Volume 13, Issue 03 March 2024
Mr.Santosh Pandurang More
Principal, K P Patil Institute of Technology Mudal, Kolhapur Maharashtra.
INTRODUCTION
Green manufacturing is a term used to describe manufacturing practices that do not harm the environment during any part of the manufacturing process. It emphasizes the use of processes that do not pollute the environment or harm consumers. SWAT analysis carried shows advantages, disadvantages and barrier of green manufacturing. Also paper discuss case study of CML Corporation.
Keywords:
Green manufacturing, sustainable manufacturing, SWOT analysis, CML Corporation
SUSTAINABLE MANUFACTURARING CYCLE
KEY FINDINGS WHAT DOES SUSTAINABLE MANUFACTURING MEAN?
The term sustainable manufacturing. is about preserving Planet Earth through care for the environment and recycling of materials. Perhaps reflecting a climate of global competition in their sector, others felt sustainability referred to future security providing products that the market wants, ensuring profitability or maintaining customer focus. Whilst concern for the environment, energy use, recycling and business continuity were all identified as key deliverables, alarmingly only 13% mentioned that sustainability brought commercial advantage. This suggests a fundamental problem manufacturers do not generally see a way to exploit sustainability in their products and marketing & manufacturing Executive Summary
The Concept of Green Manufacturing
Green manufacturing is a term used to describe manufacturing practices that do not harm the environment during any part of the manufacturing process. It emphasizes the use of processes that do not pollute the environment or harm consumers, employees, or other members of the community. Green manufacturing addresses a number of manufacturing matters, including recycling, conservation, waste management, water supply, environmental protection, regulatory compliance, pollution control, and a variety of other related issues.
EXAMPLE OF SUSTAINABILE SYSTEM
IS IT IMPORTANT AND BENEFICIAL?
Sustainable manufacturing emphasis on reduction of waste, elimination of greenhouse gases. Recycling of material help us to maximizing resources. Sustainable manufacturing gives more stress on converting O/P into I/P. Those who do embrace sustainability effectively are likely to gain significant competitive advantage.
WHY IS SUSTAINABILITY SUDDENLY IMPORTANT?
The Stern Review and the climate change bill have heightened public interest in the issues of sustainability and suggest that more legislation is in the pipeline. 89% of those surveyed are already affected by environmental legislation or levies yet only 39% have made the necessary changes to accommodate the requirements. Around half are affected by the WEEE directive and almost a quarter by the End of Life Vehicles directive. Just under half (48%) of respondents have achieved the environmental standard ISO14001. The majority now report sustainable policies within their annual reports and cite customers as the main driver.
61% of companies affected by legislation have failed to adapt. Many are working towards meeting legal requirements but 11% of those questioned admit that their organizations have yet to make any effort to meet the
current environmental legislation. With the likelihood of more stringent carbon taxation and legislation arising from the intermediate targets that bring us towards the 60% reduction by 2050, those organisations who choose to ignore legislation as well as customer pressure are clearly destined to a future of declining business and increasing costs.
ARE SUSTAINABLE POLICIES WELL RECEIVED?
One fifth of those questioned only applied sustainable policies in particular areas of their business, with just one quarter feeling that sustainability has been fully accepted within their organizations and 71% seeing internal resistance. Only 5% have found that sustainability policies have had a positive impact on attracting and retaining staff even though it has been shown that ethical and sustainability credentials are major factors considered by graduates when choosing an employer.
Only 2% of companies are being guided into a sustainable future by their leaders
at board level. Leadership is critical, but the message must also be adopted throughout the organization and embedded in its culture. Staff buy-in is essential for getting the most from sustainability initiatives, whether incremental or radically innovative. Half-hearted adoption of sustainability may be a significant reason why many companies are failing to unlock the business potential.
WHAT ARE COMPANIES DOING?
Whilst most companies have adopted policies to recycle materials such as office supplies, scrap and oil, 7% are still not adopting even these basic steps. 36% of companies have replaced core materials with more sustainable alternatives. Of these, the vast majority (80%) have shifted to recycled materials. Nearly half are looking for more sustainable or renewable resources, with 55% choosing environmentally friendly options. Only 40% are using measures such as renewable energy and water management.
Nowadays, it is usual for companies to recycle paper, printer consumables and other office supplies, and most manufacturing companies recycle scrap metal and materials off-cuts, oil etc. It is a concern that still 7% of the UKs largest manufacturers are not even doing this much. Based on the reported benefits that companies are deriving from their sustainability initiatives, we must conclude that many of the remaining 93% are only doing the basics. In todays climate, this is not enough: such actions will not bring additional business or lead to innovative differentiated products.
HISTORY
Eco-designed" products appeared at the end of the 80's) reflecting market pressure from consumer concern and the pressure for regulations. It involved changes to :
-
Materials
-
Energy consumption (particularly in use)
-
Elimination of obvious toxic chemicals.
-
Emphasis on packaging.
-
Using biodegradable materials to replace non- biodegradable materials (using recycled paper and cardboard instead of plastic)
-
Making packages of recyclable materials (e.g. using PET plastic)
-
Reducing total material content of packaging (thinning out the walls of a container, introducing "soft refills" for reusable "hard containers")
-
Developing reusable, "long-life" containers (e.g. the Body Shop approach)
-
To implement recycling it was necessary to design packages so that different material could be easily separated.
CML Ltd, a medium sized New Zealand company, is the largest panel furniture manufacturer in Australasia. For years it has been a large player in the New Zealand market for Ready-To-Assemble (RTA) office and home furniture, and it has also a strong presence in its export markets Australia, USA and Asia; approximately 70 percent of all production is exported. CML has achieved its growth by competing through a good cost-quality mix, and through the variety and flexibility of its products. Recent investments in manufacturing technology and machinery have significantly enhanced the capacity and flexibility of CMLs manufacturing processes. The plant in New Zealand has the cpacity to manufacture over 500,000 pieces of furniture per annum. While a continuous improvement approach is being used at CML to further extend its manufacturing performance, sustainability has been identified as a new opportunity to significantly improve CMLs competitiveness.
PROJECT INITIATION:
The first reason for CML to initiate that it provide the company with an opportunity to be a forerunner of sustainable thinking in its New Zealand market and its main export markets Australia and USA. Sustainability is also expected to open new market opportunities in Asia and Europe, and to help maintain the companys established reputation of an innovative and modern enterprise with responsibility for the environment. It should be noted that currently only a small minority of all NZ companies think about environmental certifications or initiatives in the environmental sector. CML considered it a good opportunity to become a member of this elite group. CML is a family- owned business and a typical SME with very limited staff and financial resources. While its manufacturing processes, information technology and quality systems have been developed strategically over the last few years and are up to international standards, the company by then had no experience in the area of sustainable manufacturing. As the panel furniture market is very competitive, and product price a major determinant of consumer choice, no significant staff and management resources could be dedicated to a strategically oriented sustainability project without creating a potential cash flow problem in the short term. Some of the aspects covered during this collaboration include the introduction of Computer Integrated Manufacturing (CIM), Just-in-Time (JIT) principles, lean manufacturing and mass
customization. The development of a holistic framework to support CML and other SMEs in their quest towards world class manufacturing, and the sustainability theme is integrated in this overall framework.
SCOPE AND OBJECTIVES DEFINATION
The original project objectives are drafted by CML in May 2004. As mentioned above, they are based on CMLs desire to develop its competitiveness in new and existing markets through the development of a green brand for their organization and their products. However, it needs to be mentioned that another strong driver for the project has been the personal attitudes towards sustainability of the key players. Their strong commitment is particularly important to provide the necessary support and to overcome roadblocks to the project, for example by justifying financial resources, providing staff time for student supervision, making contacts, and in particular by raising the environmental awareness and creating a broader support basis for the project work in the organization. The original objectives are summarized under the main theme To assist in design and implementation of a number of initiatives to kick-start the Green Manufacturing project at CML. The project scope is covered under four main headings:
-
-
Assist in performing a supply chain analysis for the purpose of acquiring Forest Stewardship Council (FSC) certification. In order to get FSC certification, CML must provide proof that its raw material (Medium Density Fiberboard (MDF) and particle board wooden panels) come from sustainable forests.
-
Assist in identification of strategic threats or opportunities through researching relevant local and international environmental laws and regulations.
-
Assist in review of CMLs waste management policies according to these laws and regulations, by providing relevant data and intelligence. This requires collecting, collating and documenting data regarding the type and amount of waste generated during the production processes and the cost of their disposal.
-
Assist in starting a Product Stewardship project. This involves identification of opportunities and recommendation of ideas for elimination or sustainable management of packaging material, such as cardboard and polystyrene. As at the start of the project none of the project instigators had any specialized background or experience in sustainable management or environmental analysis, this original project scope is still relatively vague.
-
Modern manufacturers recognize the need to use resources efficiently. This extends right through the production process where they need to be very cognizant of the resources they use, by-products created and ultimately waste that cannot be used. You will find that manufacturers are very careful to use the minimum of resources, transform or modify those resources as efficiently as possible and when
the process is completed, create as least waste and by- products as possible.
-
Manufacturers are leading in programs to reduce waste and the impact on the environment as part of their commitment to sustainability. Sustainable manufacturing and world class manufacturing are one and the same. Environmentally sustainable products, services and technology are all crucial to the global performance and future excellence. , we can use resource efficiency to industry competitiveness and profitability, and showcase local companies that are achieving sustainable outcomes.
SWOT AND STAKEHOLDER ANALYSIS:
The systematic analysis of Strengths, Weaknesses, Opportunities and Threats (SWOT) creates a framework for achieving insights and formulating development goals in line with the requirements of the organization and other stakeholders, while taking into consideration the salient parameters of the existing and future external environment. Data for the CML SWOT analysis was collected and evaluated through a series of interviews, group discussions, and evaluation of a wide range of relevant literature, case studies and other sources. STRENGTHS:
High standard of production and information technology, quality management and health and safety management; high degree of support from representatives from territorial authorities, regional councils, central government, business groups and industry associations; availability of internationally accepted and locally proven cleaner production methodology; proven benefits of cleaner production and waste minimization in both financial and environmental terms.
WEAKNESSES:
Lack of experience and resources; no strong drivers for sustainability outside the project; no quantified short and long term benefits as yet. Opportunities: cost reduction (energy, waste disposal, raw materials, etc.); increased market shares in New Zealand, Australia and USA; new market opportunities in Europe and Asia; new product ranges for environmentally conscious customers; early alignment with future environmental legislation, avoiding costly adhoc initiatives; powerful branding and marketing tool.
THREATS:
Growing low cost competition from Asia reducing margins and opportunities for sustainable production; long term benefits hard to quantify; loss of market share if no progress on sustainability; competitors faster in development of sustainable brand; global economic crisis could stifle demand for sustainable products; upcoming local legislation with unforeseen impacts, e.g. New Zealand Packaging Accord, etc.; new international trade boundaries based on new environmental legislation. To identify the benefits and risks of integrating sustainability in the CMLs processes, an analysis of the internal and external stakeholders of the company was also performed. A Stakeholder is any group or individual who can affect or is affected by the achievement
of an organizations objectives. When the salient stakeholders do not get the attention they should have, some benefits may disappear and risks can become critical. Stakeholders also influence the life cycle of the products. In order to perform a structured analysis and to achieve more specific and meaningful results, stakeholder analysis was performed by considering the three dimensions that determine the salience of stakehoders, namely power, legitimacy and urgency. Stakeholders were differentiated into the categories of internal stakeholders, stakeholders along the value chain, stakeholders in the local community, and societal stakeholders. The main stakeholders impacted on by CMLs move towards sustainable manufacturing are identified as follows:
INTERNAL STAKEHOLDERS:
Employees production;
Employees office, management and administration.
STAKEHOLDERS ALONG THE VALUE CHAIN:
Customers (Asia, USA and Europe); Retailers;
Suppliers.
Customers (Australia and New Zealand); International electronics manufacturers (customers);
STAKEHOLDERS IN THE LOCAL COMMUNITY:
Neighborhood civilian communities. Local government;
Neighborhood companies;
SOCIETAL STAKEHOLDERS:
-
Non-governmental Organizations (NGOs);
-
New Zealand Government;
-
International Governments;
-
Competition (national);
-
Competition (international);
-
Natural environment; Customer organizations (e.g. Consumers Institute New Zealand);
-
Labour Unions.
From this analysis it is conclude that CML needed to implement a process or tool to quickly identify the stakeholders that are involved in and important to a decision by the company. For CMLs sustainability project different governmental institutions and an Australian environmental group (which had just started lobbying for stricter environmental standards for furniture) were identified as the most critical stakeholders at the moment, in terms of opportunities as well as threats. It was also determined that CML needs to monitor its customers behavior and preferences towards green furniture very closely in order to prevent their claims becoming urgent. Lastly, it is notice
that international competition can become a dangerous
stakeholder if they decided to move into CMLs markets.
CASUAL LOOP ANALYSIS-:
Causal loop analysis was the third tool applied to identify the dynamic nature of the changes caused by the introduction of sustainable manufacturing in the company.
The causal loop analysis identified four major reinforcing loops (Ri), and three balancing
loops (Bi). The diagram represents the behavior of the system as sustainable products and processes are developed and put in place. The implementation of sustainability at CML requires various environmentally friendly product and process improvement projects to be undertaken which require Investment Capital. The Material Cost Loop and the Process Investment Loop (balancing loops B1 and B2) show the short term decreasing effect of sustainability on CMLs Profit and Investment Capital. On the other hand, as can be seen in the Environmental Production Loop (reinforcing loop R4), the increase of Investment in Environmentally Friendly Processes leads to an instant decrease in the Material Waste and Energy Consumption. When the Material Waste and Energy Consumption is decreased the Production Costs are also decreased, leading to an increase in Profit. The implementation of environmentally friendly products and processes lead to financial rewards for CML through increased product sales and waste reduction. The Sustainability Sells Loop (reinforcing loop R1) shows the competitive advantage that CML can achieve through the increase in the Product Attractiveness of its environmentally friendly furniture and packaging. Another strategic advantage is the qualification of CMLs products into overseas markets through compliance with environmental standards. The Market Expansion Loop (reinforcing loop R2) shows that CML can increase its Market Share through the increased Introduction of Environmentally Friendly Products and Packaging. There is an initial delay after the Introduction of Environmentally Friendly Products and Packaging due to time it takes for Compliance with Environmental Standards (e.g. it took CML two years to comply with the Enviro-Mark® standard, due to the time it takes for external auditing, etc.). The increase in Market Share is also delayed because the growth does not occur instantaneously immediately after the qualification for the market, rather it increases as products become established on the market and
consumer awareness rises over time. By advertising CMLs environmentally friendly products and manufacturing processes the company can develop a reputation as a sustainable business and reap the associated increase in product sales. The Brand Reputation Loop (reinforcing loop R3) shows that increasing the Advertising of CMLs Sustainable Compliance, increases the Consumer Awareness and therefore the Number of Sales of furniture products and Profit increase. There is a delay in the consumer awareness, because it takes time for the advertising to take effect by filtering through to more customers. The Brand Investment Loop (balancing loop B3) counter-acts this positive influence because Advertising of CMLs Sustainable Compliance will lead to increased Marketing Expenditure resulting in a decrease in CMLs Investment Capital.
The Sustainability Sells Loop is currently one of the most important and influential loops, because customers around the world are beginning to demand environmentally friendly goods. The Brand Reputation Loop also currently has a strong influence on product sales, and through fast advertising of CMLs sustainable compliance, the company has the opportunity to get the first to market advantage for sustainable furniture manufacturing in Australasia.
Perhaps the most important loops in CMLs situation at the moment are the three balancing loops, as they represent the initial investment hurdle that the company has to overcome in order to fully implement its green manufacturing aspirations. As time goes by, the influence of these loops will decrease, after having made the required initial investments. In the coming years, once CML has established itself as a complying sustainable manufacturing company, the Market Expansion Loop will become very important. The Environmental Production Loop will have a constant influence over time, because the financial benefits of less wasteful manufacturing processes and lower production costs will always exist. Overall it can be concluded that the short term decreasing impacts on the Profit and Investment Capital of the balancing loops are outweighed by the reinforcing loops. It is widely predicted that the demand for sustainable products will increase in the coming years and companies will need to comply with environmental regulations in order to remain competitive in the market. In the long term CML will benefit by establishing themselves early and gaining the environmentally friendly reputation and production process abilities. On the other hand, it is easy to see the difficulties for the company in investing in sustainability because of the requirement and effects of the short term investment costs on the overall capital.
ECOLABELS:
Apart from cost savings, for example through energy efficiency and waste reduction measures, most of the economic benefits of sustainable production can only be met if the message on the sustainability of a companys products is clearly and effectively communicated to the market. A credible environmental label, called ecolabel, is a label that correctly identifies the environmental impact of a product in production and use. Thus ecolabels offer customers the opportunity to choose products with low environmental
impact. For manufacturers such labels, which are generally controlled by a third party, are an instrument to reward their environmental leadership in the market place. While there are many different voluntary and mandatory environmental performance labels and declarations with different levels of credibility, they all share a common goal, which is: through communication of verifiable and accurate information, that is not misleading, on environmental aspects of proucts and services, to encourage the demand for and supply of those products and services that cause less stress on the environment, thereby stimulating the potential for market-driven continuous environmental improvement". An important task during the initial phase of the project was to identify the most appropriate type of environmental labeling for CMLs situation. Particular emphasis was put on identifying New Zealand and international ecolabels, which would offer the most effective means of promoting CMLs environmental achievements. Another important aspect was the availability of a support programme or a step-by-step approach associated with some ecolabels that could help CML achieve the required standards of sustainability. After extensive research, three ecolabels were considered the most promising for CMLs purposes: Environmental Choice New Zealand label, Forest Stewardship certification, Environmental Choice, part of the Global ecolabelling Network (GEN), has developed a set of specifications and license criteria for New Zealand businesses that want to use their label. The label is supported by the New Zealand government and is subsidized by the Ministry for the Environment. However, at this stage Environmental Choice is lacking a strong impact on the New Zealand market: three licenses were issued in the first eight years after introduction, and this only recently increased to twelve licenses. There are currently no label specifications available for the furniture category, and the efforts and cost for developing an appropriate specification and for using the label are relatively high. Therefore it was concluded that the Environmental Choice label does not provide a feasible option for CML at this stage. The Forest Stewardship Council (FSC) is an independent international non-governmental organization, which supplies accreditation services and a trademark for companies that are using wood from forests that are managed in an environmentally suitable, economically compatible and socially advantageous way [18]. Although CML already complies with most of the criteria for FSC Chain of Custody certification, and its MDF board originates from sustain ably managed forests, research determined that at this stage it didnt appear to be economically feasible for CML to apply for certification. The certification process is a five stage, step-by-step pathway to reaching objective evidence of an organizations accomplishments in Health, Safety and Environmental (HSE) management. At the end of this programme the organization is prepared for international environmental management systems standards. The HSE management practices in the programme include assured compliance with relevant legislation and improved resource productivity through waste reduction, energy efficiency or raw material reduction. Other factors apart from enhanced public image,
brand value, and marketing ability through use of the label, are more effective risk management and lower insurance cost. The five stage approach starting from Bronze Level (indicating compliance with current HSE legislation) to Diamond Level (implementation of an internal management and audit programme to correct and drive continual improvement) fitted exactly the requirements of the medium-sized, under-resourced CML organization.
OBJECTIVES REDIFINATION
One of the core results of the first project stage, which lasted for about six months, was a set of refined project objectives. The amended objectives were based on a much better understanding of the project team of sustainability in general, and of the particular issues and factors related to its introduction at CML Ltd. The main project objective was rephrased into To build a foundation for incorporating sustainable furniture production at CML Ltd. The following sub-objectives were formulated, together with a detailed work plan and milestones:
-
Develop an in-depth understanding of sustainability in general and its benefits and risks for CML in particular. Work in this sub-objective follows on the foundation developed in the first project stage, with strong emphasis on identifying and quantifying specific benefits and risks for CML associated with its move towards sustainability.
-
Establish a life cycle inventory of furniture production at CML. In order to increase the sustainability of furniture production the life cycles of CMLs products must be analyzed. Different product groups with different life cycles will be identified (for example to differentiate between products with vinyl finishing and paint sprayed products). The life cycle inventory will identify all inputs and outputs of all process steps. Initially the life cycle inventory will focus on internal processes, as much of the information on the suppliers will be more difficult to obtain. The life cycle inventory will be used to develop measurement systems and to identify trade-offs with other performance objectives. It is a prerequisite for further steps in the project, in particular for life cycle assessment. It will also be required as a basis for identifying those process inputs and outputs, which require high attention due to their high impact on sustainability and/or their high potential for improvement. For this task a ranking system will be developed and applied.
-
Identify opportunities to increase the sustainability of CMLs manufacturing processes. For the process components, which require a high level of attention, as identified in the previous sub objective, alternative solutions need to be found that are also in line with CMLs other competitive objectives (e.g. cost reduction, quality, etc., see [4]). For each component, the different levels of the waste management hierarchy (reduce, reuse, recycle, combustion, landfill; see e.g. [21]) are investigated to identify opportunities for improvement. 4. Integrate sustainability in CMLs management processes.
-
As a leader in the foodservice equipment industry, we have a certain obligation to help set the standards for good businesswhether its by ensuring quality at every turn or
ensuring a focus on sustainable manufacturing. In establishing our Sustainable Manufacturing Initiatives, we have identified a starting point. One that is, first and foremost, consistent and achievable. As part of this plan, we have involved our manufacturing plants, our offices, our vendors and, where applicable, our customers.
-
Another objective is to support our customers sustainable objectives with efficient and long lasting products through product research and development. This kind of thinking has led to numerous advances, including packaging design and reduced water usage. Complete overviews of the areas identified as part of our Sustainable Manufacturing Initiatives are on the pages that follow.
-
Employee initiatives created a corporate team and smaller, facility-focused teams to lead the implementation of sustainability into everyday business. To achieve this, an environmental policy statement in line with the requirements of the programme will be developed. Apart from this, other possibilities and/or requirements for integrating sustainability in CMLs management processes will be investigated in order to establish a continuous improvement programme with respect to sustainability of its production. Finally, a sustainability database with all collected information will be established to ensure optimum communication and documentation, and seamless continuation of the sustainability project in the future.
CURRENT PROJECT ACTIVITIES AND OUTCOMES
Current activities in the project have been concentrated on the establishment of a life cycle inventory, the identification of improvement opportunities, and the integration of sustainability into CMLs processes and management system. At the same time, a number of smaller sub-projects were defined and initiated in areas where a significant potential for improvement was identified. In order to create more support and momentum for the projct, emphasis was placed on those issues which also promised short term success, in line with the authors strategic approach to process innovation in SMEs (see [9]). Two areas of development are briefly introduced below to illustrate some of the progress achieved so far.
LIFE CYCLE INVENTORY:
The life cycle inventory of CMLs products created an overview of all materials that go into each step of the production process, and of the elements that are the outputs of that particular step. The life cycle inventory has been used as a tool for identifying opportunities for improvements. An important conclusion from this research is that differentiating separate product lines at CML is not useful, as all products are assembled from a range of panels that have different treatments. There are also particular panels that are laminated on one face and painted on the other side. For these reasons the life cycle inventory has to be created as one single flow diagram with multiple possible process routes. The inventory is the basis for identifying waste in the process, and for quantifying the potential for improvement of each waste element. In order to prioritize
the improvement measures, each element is assessed against four ranking criteria, which are:
-
Possible financial benefits;
-
Quantity of waste produced;
-
Severity of consequences of waste production;
-
Likelihood of future cost increase.
The impact of each waste element for each criterion was then rated on a six-point scale ranging from none to very high. The result was a ranked list of priorities for waste reduction efforts.
WHAT ARE THE FUNDAMENTAL ISSUES?
If we want to move to a sustainable manufacturing system
What do you need to be able to do?
-
Material :
Can each materials task be reversed? -Reversible Manufacturing. Eliminate use of some elite materials and promote abundant ones.
-
Multi-materials :
Ensure that mixed / composite materials can be separated.
-
Disassembly :
Design product for disassembly. Modular design- updates replacement of modules
only.
-
Imperfect Inputs :
Reverse Trends-towards fast processes with perfect virgin Inputs. Flexible technology
to work with impure used materials.
-
Design :
Rather than choose ideal material combination to make product.
-
Indirect Materials :
Eliminate use of materials in process that dont form part
of final product.
PRESSURES:
-
-
-
Economical
-
Environmental
-
Social
-
Improving efficiencies
-
Reducing costs
-
Improving quality and safety through reducing manual handling of glass.
ACTIONS TAKEN:
The introduction of an automotive glass processing plant has allowed the following:
-
More efficient processing through reduced
manual handling – Glass handled only once
-
Strong focus on safety management and shop
floor training
-
Every piece of glass is tracked entire way through
the process
-
Weekly reporting systems
-
Best Practice is shared through the Pilkington group
-
Eliminating waste from the manufacturing
process through business operation system sheets.
-
Data collection & measurement of performance
against budget is extensive
-
Focusing on improving yield and uptime
BARRIERS IN ADOPTING SUSTAINABLE MFG.
-
Undeveloped organizational environmental culture.
-
Ignorance of own environmental impacts.
-
Lack of knowledge and experience with environmental issues.
-
Absence of effective environmental legislation.
-
Lack of awareness of trends or not believing that sustainability will benefit the company.
-
Limited financial and staff resources available for environmental projects.
-
Conflicts between environmentally friendly practices and other business objectives.
DRIVERS FOR SUSTAINABLE MFG.
-
Pressures on SME for adoption of environmental practices.
-
Customer pressure.
-
Business to business pressure from larger organizations.
-
Cost reductions.
-
Pressure from other external stakeholders.
-
Potential new market opportunities.
-
Owner values or employee aspirations
-
ACHIEVMENTS:
Environmental indicators reduced by company in several years.
-
30% in Carbon Dioxide emissions
-
39% in waste generated from site
-
57% in water usage
for the future moving toward worlds best practice through Benchmarking In the space of two years Brintons has achieved a 20% improvement in its manufacturing performance levels. Brintons – a longstanding world leader in woven Ax Minster carpets established its Australian operations in Geelong in 1960 and now employs around 140 people Australia wide. A privately owned company, Brintons is known for its quality woven Ax Minster carpet used in commercial and residential installations. The company has faced recent challenges and tough international competition with a program aimed at taking it to worlds best practice. Brintons Carpets is a bespoke (custom-made) manufacturer to customer requirements. The company designs and manufactures to niche markets like casinos, luxury cruise ships, airports, hotels and landmark projects such as the Sydney 2000 Olympics, the MCG refurbishment and the highly acclaimed Melbourne Airport Commonwealth games running track carpet as well as producing beautiful residential carpets in a variety of colors
and styles. With import tariffs are continuing to be reduced to 5% in 2010, the challenges of competing with low cost imports and alternative-flooring products remains. In response, the company introduced the BEST (Brintons Excellence through Structure & Teamwork) initiative, which began in 2003. The importance of teamwork and developing the organizational maturity to lead, accept and adopt changing cultures required for sustainability has been paramount. Brintons has an environmental policy that both guides and reinforces the company towards environmental excellence.
CONCLUSION-
Less material usage. Less chemical usage. Less energy usage. All this adds up to lower operating costs for you and a better planet for all of us. Sustainable manufacturing emphasis on reduction of waste, elimination of greenhouse gases. Recycling of material help us to maximizing resources. Sustainable manufacturing gives more stress on converting O/P into I/P. This helps to minimize scrap after end of product life & also maximize resources available. Elimination of greenhouse gases leads to cleaner environment, reduce depletion of ozone layer & maintain temp of earth.
To promote sustainable management of the natural and human environment and its resources by advancing our knowledge on the interactions between the biosphere, ecosystems and human activities, and developing new technologies, tools and services, in order to address in an integrated way global environmental issues
REFERENCES:
1] Brundtland, G.H., Our Common Future, World Commission on Environment and Development, 1987
2] Rainer Seidel, Mehdi Shahbazpour, Marco Oudshoorn,
Implementation of sustainable manufacturing practices in SMEs
3] Brundtland, G.H., Our Common Future. World Commission on Environment and Development, 1987
4] New Zealand Business Council for Sustainable Development: Dedicated to Making a Difference, http://www.nzbcsd.org.nz, retrieved 25 January 2006
5] Dr. Rainer Seidel, Mehdi Shahbazpour, Manuel Seidel
Establishing Sustainable Manufacturing Practices in SMEs
6] Shahbazpour, M., & Seidel, R. (2006), Using Sustainabilty for Competitive Advantage. Paper presented at the 13th CIRP International
conference on Life Cycle Engineering, Leuven, Belgium.
7] Waddock, S. A., & Graves, S. B. (1997). The corporate social performance financial performance link. Strategic Management Journal, 18(4), 303-319