
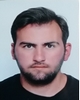
- Open Access
- Authors : Georgios Kafaridis
- Paper ID : IJERTV10IS110010
- Volume & Issue : Volume 10, Issue 11 (November 2021)
- Published (First Online): 08-11-2021
- ISSN (Online) : 2278-0181
- Publisher Name : IJERT
- License:
This work is licensed under a Creative Commons Attribution 4.0 International License
High Speed – High Rise Elevators. A Quick Guide
Georgios Kafaridis
Abstract: This paper highlights the new trends in high-speed elevators and discusses the impact in modern buildings design, construction, and operation. Additionally, it focuses on the technological innovations and how these are implemented in high-speed elevators. All these implementations are resulting into a modern, comfortable, safe and energy efficient vertical transportation. As these implementations are penetrating, the overall calculations are affected, and new parameters are inserted to an integrated application.
Keywords: Energy efficiency, roping, safety components, European Norms
INTRODUCTION
The modern trend in city built, that includes tall buildings, would not be feasible without the development of faster and more reliable elevators.
Nowadays the largest metropolitan centers have competed each other in building such buildings which are considered as landmarks that reflect dynamism and financial growth. At the same time, another competition takes place, the one that has to do with the fastest elevator. It seems that Olympic Games moto citius, altius, fortius is a constant pursuit of every human activity. At the present paper we are dealing with the modern trends at high speed high rise elevators and we are presenting the features that differentiate them from conventional ones, as well as the calculations in such elevators according to the European Norm 81- 50:2014 ( 81-50: 2014).
CHAPTER 1. TALL BUILDINGS – HIGH SPEED ELEVATORS
According to the Skyscrapers Center Institute, the tall buildings are discriminated in 3 categories based on their height (h): Talls h<300m
Supertalls h>300m
Megatalls h>600m
Nowadays, there are 3 Megatalls and 151 Supertalls buildings worldwide.
The following chart shows the 10 tallest-to-tip buildings worldwide, with descending classification as they are referred to the cbtuh.org. The tallest to-tip building is Burj Khalifa, Dubai. Its height reaches 828 meters while the highest floor is on 585 meters. Far East and Middle East countries have plenty of tall buildings while USA follows that pace and Europe lags.
Nowadays, the fastest elevator has a speed of 20 m/s. This elevator is installed by Hitachi in 2016, in the skyscraper CTF Financial Center (#7), 530 m high, located in Guangzhou, China. It needs 43 seconds to travel from the lowest to the highest (95th) floor. The previous record was held by Taipei 101 (#10) elevator, in Taiwan which is travelling with 16, m/s (60,6 km/h) speed, whereas inside the tallest building (Burj Khalifa), the fastest elevator travels at speed of 10 m/s. Elevators at a speed higher than 1 m/s require technologically enhanced parts to meet the demands of a normal operation.
The tests of such improved parts must take place in real conditions. Therefore, the large elevator companies invest in elevator test towers constructions.
Figure 1.1: Top 10 tallest to-tip buildings [1]
Source: https://www.ctbuh.org/
Table 1.1: The tallest Elevator Test Towers worldwide
/ |
Name |
Location |
Country |
Company |
Height (m) |
Further notes |
1 |
hyssenkrupp Testturm |
Zhongshan |
China |
Thyssen |
248 |
Completion year: 2018 |
2 |
hyssenkrupp Testturm |
Rottweil |
Germany |
Thyssen |
246 |
30m of 246 are in deep |
3 |
G1 Tower |
Hitachinaka |
Japan |
Hitachi |
213,5 |
Elevator test with speed up to 18 m/s |
4 |
Hyundai Asan Tower |
Icheon |
South Korea |
Hyundai |
205 |
Elevator test with speed up to 18 m/s |
5 |
Mitsubishi Solaé Test Tower |
Inazawa |
Japan |
Mitsubishi |
173 |
This is the Test Tower with the most floors (40) |
6 |
Shanghai New Research Tower |
Shanghai |
China |
Hitachi |
172 |
|
7 |
Nippon-OTIS Shibayama Test Tower |
Shibayama |
Japan |
Otis |
154 |
The tallest Test Tower between 1998 and 2004 |
8 |
National Lift Tower |
Northampton |
UK |
Express Lift Company / Otis |
127,45 |
Since 2015, it is used as the largest drainage test tower |
9 |
OTIS Bristol Research Center |
Bristol, Connecticut |
Otis |
117 |
||
10 |
Basarab Tower |
Bucharest |
Romania |
– |
114 |
Currently, this tower does not belong to any company. This was built in 1988, for testing the elevators that were going to be installed in People's House |
KONEs Tytyri Elevator R & D cer |
Lohja |
Finland |
KONE |
333 (in depth) |
This Test Tower is completely underground. Elevator test with speed up to 17m/s |
Source: https://de.wikipedia.org/wiki/Aufzugstestturm
CHAPTER 2. ELEVATORS MODERN TRENDS
-
Elevators of 1:1 (direct) and 2:1 (inderect) roping
Roping (r) is the ratio of the traction sheaves speed to the speed of the travelling car. r = =
The roping ratios that are commonly used by elevators are 1:1 (direct roping) or 2:1 (indirect roping, 4:1 rarely used).
= linear speed of traction sheave
= lift car speed
P = weight of lift car, chassis, and car door
Q = payload
W = counterweight = P + 2
T1 = rope stress at the car lift part
2 = rope stress at the counterweight part
F = T1 – 2 = suspended load
S = T1 + 2 = static load
Roping
Roping Illustration
Conditions
1:1 Direct
With single or double wrap
=
T1 = P+Q
T2 = W = P +
2
F = T1 T2 =
2
S = T1 + T2 =
2P +3
2
2:1 Indirect
= 2*
T1 = P+Q
2
T2 = W = +
2 2 4
F = T1 T2 =
4
S = T1 + T2 =
P + 3
4
Roping
Roping Illustration
Conditions
1:1 Direct
With single or double wrap
=
T1 = P+Q
T2 = W = P +
2
F = T1 T2 =
2
S = T1 + T2 =
2P +3
2
2:1 Indirect
= 2*
T1 = P+Q
2
T2 = W = +
2 2 4
F = T1 T2 =
4
S = T1 + T2 =
P + 3
4
Table 2.1: Roping Types
Table 2.2:
Advantages Disadvantages of 1:1 and 2:1 roping
A/A
Comparison criterium
1:1
2:1
Notes
1
Ropes tensile stress
High
Low
2:1 roping has an advantage, due to weight of lift car and counterweight are distributed between the 2 parts of the rope
2
Rope bending
Low
High
2:1 roping falls short due to the multiple use of pulleys
3
Static load at sheaves center
Heavy
Light
2:1 roping has an advantage due to weight of lift car and counterweight are distributed between the 2 parts of the rope
4
Motoring machine stress by suspended load
High
Low
2:1 roping has an advantage due to weight of lift car and counterweight are distributed between the 2 parts of the rope
5
Motors efficiency
Less efficient
More efficient
2:1 roping has an advantage due to the double rotation speed that requires lower gear ratio
6
Frictions safety limit
efa in case of emergency braking condition (2nd traction condition)
High
Low
2:1 roping falls short due to lower friction (f) coefficient, because of the higher rotation speed.
7
Possibility of lift cars undesirable suspension when counterweight is stalled
(3rd traction condition)
Low
High
2:1 roping falls short, due to smaller 1 ratio because the lift car
2
load is distributed between the 2 parts of the rope
8
Empty car weight
Light
Heavy
2:1 roping falls short, because to meet the requirements of the 3rd slip condition (EN 81:50), it is required heavier lift car to be installed
9
Compensation chain weight
Not necessary
Necessary
2:1 roping falls short because it requires the use of double weighted compensation chain compared to 1:1 roping
10
Smooth start and stop
Less
More
2:1 roping has an advantage, because the lower suspended load (F) and the use of VVVF inverters provide less electric lag to the motoring start. As a result, there is a smoother start to the motoring machine.
11
Cost
Low
High
2:1 roping requires more expensive equipment
-
Machine Room Less Elevators (MRL)
In such elevators, the motoring machine is placed at the headroom of the well. Therefore, there are no space requirements for machine room. To overcome the problem of space narrowness inside the well, gearless motoring machines are developed. The roping ratio is usually 2:1. The first MRL elevator developed in 1996 by KONE (Finland). This model named KONE Monospace [2],[3].
MRL elevators are applied to low and middle rise. At high rise elevators it is preferred to create a separate machine room space, however it is use gearless motoring machines.
Table 2.3: Advantages/Disadvantages of MRL Elevators
/
Comparison criterium
Conventional Elevator
MRL Elevator
Notes
1
Machine room space requirements
YES
NO
MRL has the advantage because the machine is located inside the well
2
Headroom of the well
Low
high
MRL has a disadvantage, because the headroom of the must be at least 30 cm to be placed the motoring machine
3
Difficulty in maintenance and repairments
Low
High
MRL has a disadvantage due to the space narrowness
4
Guide rail fatigue
Low
High
MRL has a disadvantage because the motoring machine is hanged upon the guide rails causing an additional compressive load
-
New types of elevators
New advanced elevators have been developed for more efficient passenger service in tall buildings. These new advanced types are:
-
Double Deck Elevators, where 2 separate cars are connected, and they are travelling inside the same well. In this way, the capacity of the elevator is doubled. These cars are not integral, but they can be divided to run independent travels inside the well
-
Antiseismic elevators which are detecting the early imperceptible earthquake vibrations that occur within 7 to 30 seconds before the main vibration (P waves). This function leads the passengers to leave the car safely at the closest floor. Then and if the S waves do not exceed a predefined limit, the elevator is set to operational mode.
-
Green Elevators, with high energy efficiency. This type of elevators saves significant amount of energy consumption, has low carbon footprint, and returns energy to the indoors energy requirements of the building.
-
Jump Elevators, which are useful during the construction phase of a building. That is because the machine room of the elevator can slide to the guide rails and rise the same time with the rise of the building construction.
-
Ultra-high speed elevators are shaped aerodynamically to reduce the air resistance, the noise, and the vibrations. Also, aerodynamic shape of the car is useful for the effective setting of the atmospheric pressure inside them to avoid the pain in the passengers ears.
Smart traffic innovations are applied to modern elevators to achieve shorter standby and travel time. These are:
-
Destination Selection System where the passengers are obliged to choose their destination floor before their boarding to the car. Then, an advanced software informs them to go to the more appropriate car for their destination. This innovation causes significant time saving to passengers service.
-
xpress elevators which are leading only to specific floors that are defined as sky lobbies. Then, the passengers are transferred to other elevators to reach their destination.
-
Currently are testing elevators without ropes. At these modern types of elevators, the traction would be magnetic. Moreover, the rotary motors will be replaced by 4 linear motors with permanent magnets, placed to the 4 corners of the elevator cars. This technology is already applied to ultra-high-speed trains.
CHAPTER 3. PARTS THAT ARE DIFFERENTIATED IN HIGH-SPEED ELEVATORS
-
Motoring Machine
A major technological innovation of our times is considered the gearless motoring machine, which is used at high-speed elevators. At these, the traction sheave is connected in-line to the motor, removing the need of reduction gear use. As a result, there are no energy losses, no noise caused by reduction gear, power savings, less volume and weight.
Table 3.1: Comparison between geared and gearless elevator motoring mahines
/
Comparison in
Geared motoring machines
Gearless motoring machines
Notes
1
Reduction gear
YES
NO
2
Motor type
Asynchronous induction motors with short-circuited rotor
Permanent Magnets Synchronous Motors
3
Motors RPM
1500 rpm
50 200 rpm
4
Use of inverter
Optional
Mandatory
5
Transmission
Angular 90
Linear
6
Weight, volume, noise, power consumption
High
Low
7
Efficiency
Low
High
Gearless machines have higher efficiency due to the absence of reduction gear, the use of PMSM and VVVF inverters
8
Longevity
Low
High
Gearless machines have greater longevity because they provide higher torque combined with lower RPMs.
9
Cost
Low
High
-
Permanent Magnet Synchronous Motors (PMSM)
Gearless machines are using exclusively PMSM, which can rotate with low-speed equal to the traction sheaves speed. These are multi-polar motors with 3-phase current field coils at the stator only, while in rotor there are permanent magnets instead. They are considered as a great technological innovation and their development is an aftermath of the discovery of new strong neodymium magnets.
Table 3.2: PMSM electric motors vs asynchronous motors
/
Comparison
PMSM
Asynchronous motors
Notes
1
Efficiency
High
Low
PMSMs have higher efficiency because they are equipped with permanent magnets rather than three-phase windings. As a result, PMSMs have less resistance heating and less magnetic losses.
2
Energy savings
High
Low
PMSMs have an advantage due to higher efficiency.
3
Motor speed response to inverter variations
Fast
Slow
PMSMs have an advantage because they are electrically self-excited.
4
Noise and vibrations
Small
Big
PMSMs are operating at lower RPMs.
5
Operation in high temperature
Unsustainable
Sustainable
PMSMs fall short because permanent magnets specifications are massively affected by high temperature.
6
Cost
High
Low
Permanent magnets are costly and generally there is a limited production of PMSMs.
-
VVVF Inverters
PMSMs are driven exclusively by VVVF inverters (Variable Voltage Variable Frequency), which are setting accurately the motors rotation speed and torque by modifying properly the frequency and the voltage of the power supply [4]. Therefore, VVVF inverters achieve smooth motor operation both in acceleration and deceleration. Furthermore, VVVF inverters recycle energy, because in generating mode the generated power is destined for inside-building power needs.
The use of VVVF inverters provides to the motors the following advantages
Table 3.3: VVVF advantages
/
Advantage
Reason
1
Reduction of motors heat stress in start mode
Reduced inrush current
2
Reduction of motors heat stress in operation mode
When the motor is in generating state, the generated power is consumed by an additional resistance, or it is destined for inside-building power needs instead of stressing motors three-phase windings
3
Increasing the overall number of starts per hour
Because of motors overall heat stress reduction
4
Correction of the power factor (cos=1)
Furthermore, the use of VVVF inverter offers the whole mechanical installation of the elevator the following advantages:
-
Significant energy savings
-
Lift cars smooth start and stop
-
Better lift cars floor levelling
-
Reaching of high speeds during lift cars travel by increasing power frequency (f50Hz)
-
Reduction of reducers mechanical fatigue
-
Less use of motors brakes leads in less brake abrasion
-
Human rescue through UPS use [5]
-
-
-
Ropes (Wire Ropes)
The following symbols must be used for the standardized rope designation in the rope certificate [6]:
Rope specs: 13 8 x 19 S NFC 1370/1770 U sZ
Nominal Diameter (13mm) Number of strands (8 strands)
Number of wires per strand (19 wires) Strand construction (S = Seale)
Core type (NFC = Natural Fiber Core)
Rope grade outer wires/inner wires (N/mm2) Wire finish (U = Ungalvanized)
Lay (s=lay left hand)
-
Ropes construction type:
Seale (S) 1-9-9: They have 3 layers consisted by different cross section wires at each layer. However, every wire in a single layer has the same cross section with the other wires that are included in the same layer. The outer layer has thicker wires which are more resistant to abrasion but not to bending fatigue. This rope type is used when it is necessary to last longer rather than not get abrased (e.g., for Elevators without many pulleys)
Figure 3.1
Source: PFEIFER DRAKO, Elevator Products, 2019
Warrington (W) 1-6-6-6:
The outer layer wires are alternately thick and thin. This feature gives the rope higher flexibility and resistance to bending stress, however it deprives resistance to abrasion compared to Seale ropes. These ropes (W) are used when it is necessary to resist to fatigue bending rather than to outer layer abrasion (e.g., for elevators with many small diameter pulleys or inverse bending pulleys)
Filler (F) 1-6-6-12: They combine the advantages of S and W ropes. They include thin wires for higher flexibility, larger fill factor for higher resistance to fracture and thick wires in the outer layer for better traction with traction sheave. Such wires are used at high-speed elevators, where little elongation, large fill factor, higher flexibility, breaking, and flexural strength are required.
Figure 3.2
Source: PFEIFER DRAKO,
Elevator Products, 2019
Figure 3.3
-
Elevator ropes for tall buildings
Mid and/or high-rise elevators must deal with the following problems:
Ropes elastic elongation: During passengers entrance in the elevator, takes place an undesirable drop of the lift car because of the ropes elastic elongation.
Ropes plastic elongation (Permanent elongation): Plastic elongation occurs due to the constant tensile that the ropes are submitted. Thats because of the weight of lift car and counterweight. Even at the early operation of an elevator, the ropes are elongated plastically
and a after a peiod, the elongation is so intense and as a result the counterweight drops on the buffer. At this point, it is required to cut part of the ropes. This task is expensive and requires immobilization of the lift car.
-
Rope Untwist
Source: PFEIFER DRAKO, Elevator Products, 2019
During the elevators installation in a tall building, it is possible for the ropes to get untwisted due to their own weight. The untwisted ropes have less resistance to abrasion and their life cycle is significantly decreased. The untwist should be clear and distinguishable. Therefore, the ropes in tall buildings have a colored line drawn along the rope. The manufacturers of ropes constitute that the untwist should not exceed the ½ of a full round every 10m of a rope. Lang type ropes are more liable to such untwist because the individual wires are wrapped around the center of the rope in one direction.
Ropes with the proper specifications and requirements are used in tall buildings. Steel wire core ropes are preferred in this case due to their higher breaking strength and less plastic elongation.
-
-
Compensation chains
The force resulting from the mass of the ropes, acts variably, because it acts either on the part which suspends the lift car or on the part which suspends the counterweight. We do not often concern about the compensation of this variable force in conventional elevators, because it is considered negligible. However, in high rise elevators (>30m) the mass of the ropes is so significant we cannot ignore it. Thus, it is necessary to compensate it.
Compensation chains are used for this purpose. They are installed to connect the down area of the lift car with the down area of the counterweight. For this connection are used riveted tensioning pulleys at the bottom of the well.
According to EN 81-20 5.5.6, for nominal speeds that exceed 3 m/s, it is obligatory to compensate the weight of the suspension ropes [7]. For lower speeds, such means are optional. For lifts whose rated speed exceeds 3,5 m/s there shall be an anti-rebound device as well.
Compensation chains are covered with a flexible plastic PVC material, to insulate the noise of their movement. The choice of the appropriate compensation chain is based on the weight per meter which is desirable to be identical with the total suspension ropes weight per meter. At 2:1 roping, the weight of the compensation chain should be twice as much the one used for the 1:1 roping.
-
Slide guides
During the lift car travel across the slide guides, sometimes it is observed undesirable vibrations, sudden unexpected movement, and noise due to guides misalignment. At high elevators, these imperfections impact drastically, while in conventional elevators they rarely lead in irreversible situations. Furthermore, the tall buildings are susceptible to climate conditions. In high winds, some high-rise buildings could sway as much as 45cm off center, for a total sway of 1 meter. Extreme temperature variations cause expansion and contraction of the building as well as earthquakes can make the deviate from the vertical line [8]. Thus, the more the structural elements of a building are suffering, the more serious impact that have to lifts installation misalignment.
That is the reason why in high-rise and high-speed elevators are applied roller guides. n elevator car navigates between a pair of rails that are attached to the structure of the building.
he wheels of a guide surround the rail on three sides, helping to control side-to side and front-t-back movement. These rollers include three or six roller tyres which are laminated by neoprene rubber. This design has been special engineered to dampen noise and vibration. Moreover, they are spring-loaded to compensate for unbalanced cars or misaligned conditions.
-
Mechanical Safety Components
-
Safety Gear – OverSpeed Governor (OSG)
At high-speed elevators it is required the use of progressive safety gears, both for lift car and counterweight, according to the accepted rule of EN 81-20 [7].
-
progressive safety gear for lift car when u > 0,63 m/s
-
progressive safety gear for counterweight when u > 1 m/s Safety gear for counterweight can be replaced by:
-
A safety gear for lift car that triggers also in the ascending direction
-
A safety device for rope braking
-
A safety device for sheave or sheaves axis braking
According to EN 81-20 [7], for progressive safety gear the average retardation in the case of free fall of the lift car with rated load or the counterweight or the balancing weight shall lie between 0,2 g and 1 g (5.6.2.1.3). So, in case that the nominal speed of the lift car is u = 3m/s and the deceleration provided by the safety gear is = 0,6g = 6m/s2, then:
-
Braking time is t == 3 = 0,5 sec
6
2 2
2 2
-
Braking space is S = = 3 = 0,75 m
2 26
The overspeed governor (OSG) should be fly ball type and should be activated when the speed of the lift car exceeds the limit of 1.15un.
When OSG triggers in the up direction, then the tension weight should be bigger compared to the weight that is used for down direction. The bigger the tension weight, the less the rope slipping during the OSG trigger. OSG ropes are fatigued in greater tension; thus, they need to have greater braking strength.
-
-
Buffers
-
At high-speed elevators are used energy dissipation buffers. These are hydraulic buffers consisted of one piston rod, one metallic spring and a cylinder, divided in 2 tubes (inner and outer cylinder) which are communicating through small, drilled holes in the wall of the tube. When the piston rod is pressed, the hydraulic fluid is forced out through the hole and is collected to the outer cylinder. After the buffer has impacted and the piston rod is released, the compressed spring returns the piston rod back to the starting position.
High speed elevators require deeper well than usual, for buffers use [9]. Moreover, for ultra-high-speed elevators are use 3-stage telescopic buffers.
CHAPTER 4. CALCULATIONS OF LIFT COMPONENTS ACCORDING TO EN 81-50
-
Guide rail calculation
Guide rails should be dimensioned according to the worst-case scenario i.e., lift car loaded with its full payload. When compensation chain is used, then its weight should be considered in the overall calculations. However, payload is not static, so it is more accurate to consider that it acts off-center of the lift car. That is the reason why EN 81-50 defines 2 different applications of the payloads position in the lift car [10].
-
Payload Q lays 1
off center
8
-
Payload Q lays 1
off center
8
For each one of the 2 applications there are 3 conditions that should be examined. 1. Safety gear activation
It is considered that safety gear is triggered, so the overall load applied to the guide rails is multiplied by K1 factor. 2. Regular operation
It is considered that lift car is travelling with steady speed. The overall load applied to the guide rails is multiplied by K2=1,2. 3. Car lift load
It is considered that car lift is stopped at a floor level, empty, while the 40% of payload is applied at the car lift entrance.
These conditions are examined to evaluate if the resulting tensions are lower than the maximum permissible tension of the guide rails material ( = 205 2 ).
-
Bending stress , Y axis
-
Bending stress , X axis
-
Compression stress and tension stress
-
Combined bending and compression/tension stress and evaluation if it is
-
Flange bending stress and evaluation if it is
-
Guide rails and buckling stress. Maximum permissible deflection = 5mm
-
-
-
Calculation of minimm permissible safety factor on suspension ropes
EN 81-50 refers to the minimum permissible safety factors on suspension ropes, considering the specificities that any installation might have [10]:
-
The total number of traction sheaves (Nt) and the total number of pulleys (Np)
-
Traction sheaves and pulleys diameter (Dt, Dp)
-
The number of pulleys with simple (Dps) or reserved bends (Dpr)
-
The value of the groove angle
-
The ropes diameter (d)
EN-50 suggests the method of equivalent number (Nequiv) of pulleys, following the steps [10]:
-
Estimation of equivalent number of traction sheaves Nequiv(t), considering the value of the groove angle (Table 5, par. 5.12.2.2, EN 81-50).
-
Calculation of
K=( )4 =
)4
(
(
-
Calculation of the total equivalent number of pulleys Nequiv(p) Nequiv(p) = K * (Nps + 4* Npr)
-
Calculation of the total equivalent number of pulleys and sheaves Nequiv Nequiv = Nequiv(t) + Nequiv(p)
5. Calculation of =
6. Final calculation of safety factor Sf, in accordance with Nequiv and ratio derived from Fig 10, par. 5.12.3, EN 81-50 From the previous process, we reach to the following conclusions:
-
-
A traction sheave equals to bigger number of equivalent pulleys compared to a regular pulley. That is because the overall tension in suspension rope is greater in traction sheaves because it is a result of bending stress and wear due to slipping.
-
A reversed bended pulley has 4 times larger number of equivalent pulleys from a simple bended pulley.
-
The Dt/Dp is affected heavily as the pulleys diameter gets decreased. That is because in the calculation process this ratio is raised in the 4th exponent.
-
The minimum Sf gets increased as Nequiv gets increased and as ratio Dt/d gets decreased.
-
-
Traction calculation
-
Tension calculation at both parts of suspension rope when car lift is accelerating or decelerating
The suspension ropes traction occurs if the condition 1 is true.
2
Where T1 = rope stress at the car lift part
2 = rope stress at the counterweight part
e = 2,71 (natural logarithms base)
= angle of wrap of the ropes on the traction sheave
f = friction factor (For sheaves with V groove: f = )
2
= friction factor between suspension ropes and traction sheave = groove angle
-
The value of slipping limit (efa) is only affected by angle of wrap a of the ropes and the friction factor f.
-
The traction or the slipping of the ropes depends in the tension ratio 1 of the 2 parts of the ropes.
2
When the elevator is moving with steady speed or it is stopped, the T values are considered as follows: T1 = (P+Q) *g (rope stress at the car lift part, Nt)
T2 = W*g (rope stress at the counterweight part, Nt)
When the car lift is moving up with acceleration a, then from the 2nd Newtons Law it is:
T1 (P +Q) *g = (P + Q) *a => T1 = (P + Q) (g + a)
W*g – T2 = W*a => T2 = W*(g – a)
Table 4.1: Possible situations of car lift movement and the resulting stress values
Situation Parts
Car lift part 1
Counterweight part 2
Moving up with acceleration
1 = ( + )( + )
2 = ( )
Moving up with deceleration
1 = ( + )( )
2 = ( + )
Moving down with acceleration
1 = ( + )( )
2 = ( + )
Moving down with deceleration
1 = ( + )( + )
2 = ( )
It is observed that when the car lift is moving with acceleration or deceleration the stress that is acted by the masses of car lift and counterweight, they are simulate artificial gravity (g±a) rather than real g.
-
-
Evaluation of traction in traction sheave
When a lift is planned to be installed, the traction examination is fundamental. The traction condition is 1 .
2
Where:
-
T1, T2 are the forces in the portion of the ropes situated at either side of the traction sheave
-
is the angle of wrap of the ropes on the traction sheave
-
f is the friction factor (f =
)
2
is the friction between the ropes and the sheave is the groove angle
2
2
Traction should be tested at the following conditions through the evaluation of 1
ratio:
1st condition: Lift car in the well with 125% of the rated load.
2nd condition: Emergency breaking condition. Traction should be ensured in two sub-conditions.
-
Lift car descending at the lowest point of the well, loaded with 100% of the rated load and decelerating due to emergency break.
-
Lift car ascending at the highest point of the well, empty and decelerating due to emergency break. 3rd condition: Counterweight stalled condition
These 3 traction conditions are represented in the following table for both direct and indirect roping. In every table we examine additionally the use of compensation chain which is necessary for high speed high rise elevators.
It is worthy to be noted that the use of compensation chain improves the traction in every condition and in both types of roping. The dynamic and kinematic features of traction or slipping are differentiated in elevators with indirect roping because:
-
The moving speed of the suspension ropes is double to the moving speed of the car lift
-
The deceleration of the suspension ropes is double to the deceleration of the car lift, in case of emergency breaking
-
The masses of car lift and counterweight are acting by half at the rope part stress.
Evaluation of traction in direct roping
Figure
Description
Rope Tension (without compensation)
Rope Tension
(with compensation)
Requirement
1 condition
= 0,10
Car lift is stopped at the lowest floor, loaded with the 125% of the payload
1 = (P+1,25*Q)*g +
Mrope*g 2 = W*g
1 = (P+1,25*Q)*g
+ Mrope*g
T2 = (W+ Mcomp) g
Traction
1
2
2.1 condition
= ,
+
Car lift is moving down to the lowest point of the overall travel, loaded with its full payload and emergency braking is occurring
T1 = (P+Q) *(g+a) +
Mrope*(g+a) T2 = W*(g-a)
T1 = (P+Q) *(g+a) +
Mrope*(g+a)
T2 = (W+ Mcomp)(g- )
Traction
1
2
2.2 condition
= 0,10
1+
10
Car lift is moving up to the highest point of the overall travel, loaded with its full payload and emergency breaking is occurring
T1 = (P+Mcable) *(g- a)
T2 = W*(g+a) +
Mrope*(g+a)
T1 = (P + Mcable + Mcomp) *(g-)
T2 = W*(g+a) +
Mrope*(g+a)
Traction
2
1
3 condition
= 0,20
Slipping must be ensure, just for the car lift not to be lifted and be dropped sharply.
T1 = (P+Mcab) *g T2 = Mrope*g
T1 = (P + Mcab +
Mcomp) *g T2 = Mrope*g
Traction
1
2
Evaluation of traction in indirect roping
Figure
Description
Rope Tension
(without compensation)
Rope Tension
(with compensation)
Requirement
1st condition = 0,10
Car lift is stopped at the lowest floor, loaded with the 125% of the payload
T1
P + 1.25Q
= g
2
+ Mrope g
W
T2 = 2 g
T1
P + 1.25Q
= g
2
+ Mrope g
T2 = + *g
2
1
2
2.1 case
= 0,10
1+2
10
Car lift is moving down to the lowest point of the overall travel, loaded with its full payload and emergency breaking is occurring
T1 = ( P+Q )*(g+a) +
2
Mrope*(g+2a)
T2 = W*(g-a) 2
T1 = ( + )*(g+a) +
2
Mrope*(g+2a)
T2 = +*(g-a) 2
1
2
2.2 case
= 0,10
1+2
10
Car lift is moving up to the highest point of the overall travel, empty load and emergency breaking is occurring
T1 = (P+Mcab)*(g-a)
2
T2 = W*(g+a) +
2
Mrope*(g+2a)
T1 = P+Mcab+Mcount*(g- 2
a)
T2 = W*(g+a) +
2
Mrope*(g+2a)
2
1
3rd case = 0,20
Slipping must be ensured, just for the car lift not to be lifted and be dropped sharply. Motoring machine should not be powerful enough to lift the car lift in this case.
T1 = (P+Mcab)*g
2
T2 = Mrope*g
T1 = P+Mcab+Mcount*g
2
T2 = Mrope*g
1
2
-
-
Evaluation of traction in overspeed governors sheave
The purpose of these calculation is for the OSGs ropes traction to be evaluated. This is necessary, because in case of OSG activation, the ropes must activate the safety gear without slipping.
We name the following symbols:
MG= Tension weight (includes OSG sheave and ropes weight)
FE = Activation force of the safety gear
c = car lifts nominal speed
u = OSGs activation speed (u = 1,15*uc )
= friction factor between ropes and sheave = 0,10
1+
10
= groove angle f =
(2)
= angle of wrap of the ropes on the sheave, 180 = 3,14 rad Ropes traction condition 1
2
We carry out evaluation process whether there is traction in the 2 following situations:
Direction that safety gear acts |
Stress in the 2 parts of the ropes |
Required tension weight |
Required activation force of the safety gear |
Down |
1=MG'/2 + FE, 2=MG'/2 |
MG' 2 (1) |
( 1) 2 |
Up |
1=MG'/2 2=MG'/2 – FE |
MG' 2 (1) |
(1 ) 2 |
It is observed that when safety gear is activated when car lift is moving up, the required tension weight is times bigger to the required tension weight when car lift is moving down.
It is also observed that for given tension weight, the activation force of the safety gear in the up direction must be efa times smaller than the activation force of the safety gear in down direction.
REFERENCES
-
Council on Tall Buildings and Urban Habitat. (2019): Height to Architectural Top. CTBUH. Available online: <URL: https://www.ctbuh.org/resource/height> (accessed on August 18th, 2021).
-
KONE Corporation (2008): The Machine-Room-Less Elevator Platform: KONE Monospace Special. KONE Corporation. Lohja, Finland
-
LIFTINSTITUT (2018): EU-TYPE EXAMINATION CERTIFICATE KONE MonoSpace 700/3000 S MonoSpace/ N MonoSpace/ E MonoSpace. Certificate No. NL 16-400-1002-002-61. Revision no. 7. Amsterdam, The Netherlands.
-
Bachtis N. 2013 Inverter . Available online: <URL: https://www.electrologos.gr/i-chrisi-toy-inverter-stis- michanes-anelkystiron> (accessed on August 18th, 2021).
-
Staugiannoudakis G. 2013 . Available online: <URL: https://www.electrologos.gr/nees- taseis-stoys-anelkystires-kai-kritiria-epilogis>. (accessed on August 18th, 2021).
-
Pfeifer Drako 2019 Elevator Products: Steel Wire Ropes in Elevators. Pfeifer Drako Drahtseilwerk GmbH, Mülheim an der Ruhr, Germany.
-
EN 81-20:2011 Safety rules for the construction and installation of lifts Lifts for the transport of persons and goods Part 20: Passenger and goods passenger lifts. European Committee for Standarization.
-
ELSCO 2019 Why ELSCO?. ELSCO Elevator Roller Guides Inc. Owings Mills, Maryland (MD), USA.
-
Henning 2019 Liftpuffer/Liftbuffer HPL/HPM. Henning GmbH. Schwelm, Germany.
-
BS EN 81-50:2014 Safety rules for the construction and installation of lifts Examinations and tests Part 50: Design rules, calculations, examinations and tests of lift components. BSI Standards Publication.