
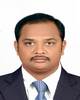
- Open Access
- Authors : Dr. S. Parthasarathy , R. Thangasankaran , P. Clement Paul , M. Arjun
- Paper ID : IJERTV11IS060063
- Volume & Issue : Volume 11, Issue 06 (June 2022)
- Published (First Online): 13-06-2022
- ISSN (Online) : 2278-0181
- Publisher Name : IJERT
- License:
This work is licensed under a Creative Commons Attribution 4.0 International License
High Gain Ripple Less DC-DC Power Converter for EV Application
Dr. S. Parthasarathy, Professor /EEE,
K.L.N College of Engineering, Pottapalayam, Tamil Nadu
Mr. R. Thangasankaran, Assistant Professor/EEE,
K.L.N College of Engineering, Pottapalayam, Tamil Nadu
Mr. P. Clement Paul, Final Year/EEE,
K.L.N College of Engineering, Pottapalayam, Tamil Nadu
Mr. M. Arjun, Final Year/EEE,
-
College of Engineering, Pottapalayam, Tamil Nadu
Abstract- Nowadays, most attention is paid to electric vehicles in the transport systems and the use of renewable energy in the power systems. The main drawback in conventional converters is high ripple current, which reduces the lifespan of the converter and overall system. Where the rippleless DC-DC Converter has very lower ripple values of both output voltage and output current compared with allowed ripple values under closed loop analysis which in terms reduces switching losses and the efficiency of the converter is increased, by reducing the ripple the steady state of the converter is obtained with lesser delay compare with conventional ones. An integral part of any modern-day electric vehicle is power electronic circuits (PECs) consisting of DC-DC converters. Enhancing overall performance of the EV system, where DC- DC controllers play a vital role in EV, the output of the converter is measured and compared with a reference voltage. The DC-DC converter is controlled to extract maximum power from the source to control the load and this converter operates in Continuous Conduction Mode. Analysis is made for both Open-Loop and Closed-Loop of the converter in MATLAB/Simulink R2020a.
Keywords- DC-DC Converter; Duty Cycle; Pulse Width Modulation; Closed loop.
-
INTRODUCTION
An electric vehicle (EV) is one that uses one or more electric motors for propulsion. It has low running costs as they have less moving parts and hence its maintenance is less when compared with other conventional vehicles and also it is environmental friendly as they use little or no fossil fuels (petrol or diesel).It can be powered by a collector group system, with electricity from extravehicular sources, or it can be powered autonomously by a battery (sometimes charged by solar panels, or by converting fuel to electricity using fuel cells or a generator). While the EVs are controlled by using DC-DC Converters, Nowadays the standard for modern battery electric
vehicles are now considered to be lithium-ion batteries as they have a greater longevity and are excellent at retaining energy. Despite this improved efficiency, there are still challenges with these batteries as they can experience thermal runaway, which have, for example, caused fires or explosions in the Tesla model S, although efforts have been made to improve the safety of these batteries.
Babu, P. Ramesh, S. Ram Prasath, and R. Kiruthika have proposed paper of Simulation and Performance Analysis of CCM Zeta Converter with PID Controller.[1] They have Designed, Analyzed, Simulated, Close loop, Continuous Conduction Mode of Zeta Converter in their proposed paper. As proposed in the paper, The Converter works in continuous current mode (CCM) only. But, The Boosting of Input Voltage is not that much high. But The Converter has Lower Output Voltage Ripple and has High Efficiency.
Choudhary, Piyush, and Som Nath Mahendra have proposed paper of DC-DC Cuk converter for solar photovoltaic array which has an inductor current of 20% and 50% more.[2] Piyush Choudhary and Som Nath Mahendra both have made the calculations and analysis, CCM mode operation, Transfer function, State Space Analysis, Simulation of Cuk Converter. A Voltage sensor is placed on the output side to take feedback of output voltage.
Gnanavadivel, J., ST Jaya Christa, and R. ThangaSankaran has proposed paper of an interleaved converter [3] where it operates with an input of 90 V- 260V and is also bucked for 48 V for type of control and is also rectified with lesser ripple and improved power factor.
Saravanan, S., and N. Ramesh Babuhave proposed a step-up dc – dc converter [4] with high voltage gain with the combination of a sepic converter with diode where they obtained output is 300Vfor an input of 30V. The switched capacitors are used in converters to achieve high static gain and this topology is suitable for renewable energy-based applications having low input dc voltage.
Ye, Haixiong, GuangzheJin, Wang Fei, and Noradin Ghadimi have proposed non-isolated Interleaved dc/dc converter [5] with high voltage conversion with low voltage stress about 190 W at 40 kHz and the result of this proposed converter is a good candidate for renewable applications and output power achieved is 182 W with 40 kHz switching frequency.
Wai, R. J., and R. Y. Duan have proposed a high efficiency converter [6] and the converter is designed with one switch and with inductors, diodes and a capacitor and it is concentrated with fuel cells to offer higher energy density and more conventional battery systems. The aim of this
study is to design a high-efficiency high voltage-gain converter with a coupled inductor to regulate a stable constant DC voltage. It is able to operate with soft switching in a pulse width-modulation (PWM) way without high voltage and current stresses. Unfortunately, the voltage gain is limited below four in order to achieve the soft switching.
Amir, Asim, Aamir Amir, Hang Seng Che, Ahmad Elkhateb, and Nasrudin Abd Rahim have proposed a Non-isolated DC-DC Boost Converter [7] high voltage gain offered, voltage stresses on each component involved and the efficiency of the high gain topologies. For the converters under discussion, operation under ideal and non- ideal conditions has also been highlighted. Based on this study, authors present a guide for the reader to identify various high voltage gain topologies for photovoltaic (PV) systems.
In the DC-DC Boost Converter, the output voltage Vo is higher than the input voltage Vin and from the above surveys it clearly mentioned that DC-DC Converter is the heart of the EV and renewable applications and by comparing proposed converter with other surveys it has lower ripple at the output voltage and current and also it works with Continuous Conduction Mode.
-
PROPOSED DC-DC CONVERTER CONFIGURATION:
-
The circuit configuration of the proposed DC-DC converter is shown in Figure 1. It operates at an input voltage of 12 – 36 V. The power circuit strategy is presented with two inductors, one capacitor, four diodes and one MOSFET switch operating at a switching frequency of 20 kHz.
Figure:1 Proposed DC-DC Converter Circuit Diagram
The proposed Converter is designed for 100W applications. The regulated output voltage and output current will be 60V and 1.664 A respectively.
OPERATING MODES OF PROPOSED CONVERTER
The operation of the proposed converter is divided into two modes, when control switch S is ON and switch S is OFF. When switch S is turned ON, inductors L1 and L2 are charged in parallel by input voltage Vin through Diode D1 and D2 respectively. Capacitor C is discharged through load. Diodes D3 and D4 are reversed biased. Figure 2 describes operation when switch S is turned ON.
Boost converter circuit is designed using a single inductor, single diode and single switch. The operational modes of boost converter can be categorized into two modes, one when switch S is turned ON and another when switch S [MOSFET] is turned OFF. When switch S is turned ON, the inductor is charged by input voltage Vin through switch S.
Figure 2 picturies the mode of operation when switch S is turned ON. In practical boost converter circuits, the value of internal resistances of switch and diodes are finite, and Figure 3 shows the mode of operation when Switch S [MOSFET] is turned OFF, the inductor is discharged through load and diode.
Figure:2 Equivalent Circuit and current direction of converter when switch is ON
When switch S is turned OFF, inductor L1, L2 and voltage source is discharged in series through Diode D3 and D4. Here diodes D1 and D2 are reversed biased. Figure 3 picturizes the operation when switch S is turned OFF.
Figure:3 Equivalent Circuit and current direction of converter when switch is OFF
III. DESIGN OF DC-DC CONVERTER The Design specifications of the proposed Converter is given below the duty cycle of the proposed Converter is designed by using the formula;
TABLEI: DESIGN SPECIFICATION OF THE CONVERTER
PARAMETERS |
VALUES |
Supply voltage () |
12 V |
Input Inductor (1) |
700 µH |
Input inductor (2) |
700 µH |
Output Capacitor () |
4600 µF |
Output Power () |
100W |
Output Voltage( ) |
60V |
Switching Frequency() |
20 kHz |
IV. RESULTS AND DISCUSSIONS
= (1+ )
(1)
(1)
4.1 Open loop Simulation of DC-DC Converter
The inductor L1 and L2 of the proposed converter is designed by using the formula;
The DC-DC Converter is Simulated in MATLAB/Simulink R2020a is shown below. Open loop simulation diagram of the proposed converter. Two inductors and One capacitor were added in this circuit. This
( )
1
(2)
MATLAB circuit is designed and simulated to analyze the Switched Inductor Boost converter. The output waveforms of output voltage, output current, Inductors current,
The output capacitor Co of the proposed converter is
designed by the formula;
Capacitor voltage and switching pulse were analyzed. By this, the working of the proposed Boost converter is analyzed. There is a scope with 8 inputs were has the all
Where,
(1)1
(3)
waveforms mentioned above. The switching pulse is given by Pulse Generator.
Vo Output Voltage
Vin Input Voltage D Duty Cycle
fs Switching frequency
1- Change in inductor current Io- Output Current
1- Change in voltage of capacitor
The design specification of the converter is very
much important where it is used to calculate the desired parameters which it is going to use for desirable output applications, from using the above equations (1), (2) and
(3) the designed values for the Proposed Converter are listed in Table I.
Here in the open loop simulation shown in figure 4 the output waveform of the two inductors along with the output current and voltage is measured in the scope through mean block for non-discrete values measured at the output and at the output side of the converter a capacitor is used in order to reduce ripples at the output side and each of the diode voltage and the MOSFET voltage is measured in the scope with the bus selector tool which is available in MATLAB\Simulink R2020a.
Figure 4: Open loop Simulation of DC-DC Converter
Figure 4 shows the open loop simulation diagram of the proposed converter. Here, different duty cycles are used to analyze the efficiency of the converter.
Figure 5 shows the output voltage waveform of the DC-DC converter. The desired output voltage is 60V but it is not achieved in open loop control; instead, an output voltage of 51.64 V is obtained, with a steady time of 0.1sec in the open loop simulation.
TABLE: II: OUTPUT VOLTAGE OF OPEN LOOP
Input Voltage (Vin) |
Desired Output Voltage (Vo) |
Actual Output Voltage (Vo) |
12V |
60V |
51.64V |
4.2. Closed loop Simulation of DC-DC converter using PI controller.
Figure 5. Output Voltage of open loop simulation of DC- DC Converter
The PI controller is the most commonly used in closed loop systems because of its performance in terms of simplicity. It produces an error signal by comparing the desired output signal with the actual output signal. Figure
6 shows the closed loop simulation diagram of the proposed converter.
Figure 6: Closed loop Simulation of proposed DC-DC Converter
is less than one and due to decrease in the ripple the steady time is achieved with constant desired output voltage at 1.7 sec and the output voltage becomes stable and constant in closed loop system.
Figure 7. Output Voltage of closed loop simulation of DC-DC Converter
Figure 7 shows the output voltage waveform of the DC-DC converter under closed loop control. The
desired output voltage of 60 V is obtained in this type of control which is obtained at a steady time of 1.7 sec.
Here, 5% of the output voltage is 3V and the peak-to-peak voltage of the proposed converter is 0.012 V. The output allowable ripple voltage by IEEE standards is up to 5% of the output voltage but we have achieved a ripple of 0.4% of the output voltage [14] which
Figure.8- Output Current Waveform of DC-DC Converter
Figure 8 shows the output current waveform under closed loop simulation and the output current 1.76A is obtained at the steady time of 1.6 sec.
Here,2% of output current is 0.0352A and the peak- to-peak current of the proposed converter is 0. 0003A.The output allowable ripple current by IEEE standards is up to 2% of the output current [3] but we have achieved a ripple current of 0.8% of the output current which is less than one
.So by this, the proposed converter is justified as ripple less converter.
Figure.9- Wave form of Switching Pulse, Inductor L1 Current, Inductor L2 Current under closed loop
Figure 9 shows the Waveforms of Switching pulse, Inductor L1 current, Inductor L2 current of DC-DC converter. When, MOSFET Switch is turned ON. The Inductor L1 and L2 are charging. When, MOSFET Switch is turned OFF. The Inductor L1 and L2 are discharging.
This Proposed Converter Operates in Continuous Conduction Mode (CCM) when simulated under Closed loop. Where figure 9 shows the switching pulse waveform of the proposed converter which is generated by pulse generator with the switching frequency of 20kHz and with a duty cycle of 66.66 % and has Ton =33.33µsec and Toff
=16.67 µsec.
TABLE- III: PERFORMANCE ANALYSIS OF DC-DC CONVERTER BY VARYING DUTY CYCLE WITH CONSTANT I/P VOLTAGE [OPEN LOOP]
In the above Table III, we have discussed varying duty cycle with constant input voltage under open loop simulation where we generate and change the duty cycle with the help of PWM generator.
TABLE-IV: PERFORMANCE ANALYSIS OF DC-DC CONVERTER BY VARYING I/P VOLTAGE WITH CONSTANT O/P VOLTAGE
[CLOSED LOOP]
(V) |
(A) |
(V) |
(A) |
Efficiency |
12 |
10.11 |
60 |
1.664 |
82.29% |
16 |
7.118 |
60 |
1.663 |
87.41% |
20 |
5.529 |
60 |
1.662 |
89.91% |
24 |
4.529 |
60 |
1.661 |
91.38% |
28 |
3.838 |
60 |
1.661 |
92.42% |
32 |
3.331 |
60 |
1.661 |
93.20% |
36 |
2.942 |
60 |
1.661 |
93.87% |
In the above table IV, we have discussed varying input voltage with constant output voltage under closed loop analysis where even though there is a change in the input voltage the output voltage to the load will be maintained constant. In the above table with an input voltage of 12V it has been gained up to 60V which justifies its a High Gain boost Converter.
TABLE- V: PERFORMANCE ANALYSIS OF DC-DC CONVERTER BY VARYING REFERENCE VOLTAGE WITH CONSTANT I/P VOLTAGE [CLOSED LOOP]
(V) |
(A) |
Ref voltage |
(V) |
(A) |
Efficiency |
18 |
1.411 |
30 |
30 |
0.794 |
93.89% |
18 |
2.621 |
40 |
40 |
1.083 |
91.82% |
18 |
4.235 |
50 |
50 |
1.876 |
90.25% |
18 |
6.22 |
60 |
60 |
1.662 |
89% |
18 |
8.593 |
70 |
70 |
1.943 |
87.9% |
(V) |
(A) |
(V) |
(A) |
Duty Cycle |
Efficiency |
12 |
2.737 |
32.05 |
0.890 |
50% |
87% |
12 |
4.796 |
42.17 |
1.171 |
60% |
85.8% |
12 |
7.33 |
51.64 |
1.435 |
66% |
84.24% |
12 |
9.244 |
57.53 |
1.598 |
70% |
82.8% |
12 |
20.69 |
81.46 |
2.263 |
80% |
74.24% |
12 |
33.37 |
96.17 |
2.671 |
85% |
64.14% |
In the above table V we have discussed a constant input voltage by varying reference voltage under a closed loop where we can get a maximum efficiency of 93.89% at 30 reference voltage.
TABLE- VI: PERFORMANCE ANALYSIS OF DC- DC CONVERTER BY VARYING LOAD WITH CONSTANT I/P AND REFERENCE VOLTAGE [CLOSED-LOOP]
(V) |
(A) |
Ref voltage |
% Load |
(V) |
(A) |
Efficiency |
24 |
23.88 |
60 |
20 |
60 |
8.283 |
84.12% |
24 |
15.45 |
60 |
30 |
60 |
5.53 |
84.12% |
24 |
11.44 |
60 |
40 |
60 |
4.15 |
83.72% |
24 |
9.096 |
60 |
50 |
60 |
3.321 |
82.37% |
24 |
7.556 |
60 |
60 |
60 |
2.768 |
81.53% |
24 |
6.467 |
60 |
70 |
60 |
2.373 |
80.81% |
24 |
5.656 |
60 |
80 |
60 |
2.076 |
79.85% |
24 |
5.029 |
60 |
90 |
60 |
1.846 |
78.99% |
24 |
4.529 |
60 |
100 |
60 |
1.661 |
78.71% |
In the above table VI, we have discussed a constant input voltage and reference voltage by varying load under a closed loop where it can be discussed the efficiency varies with the percentage of the load.
CONCLUSION:
In this paper, the design and simulation of a DC-DC converter have been carried out for 12V input and 60 V output. Both open loop and closed loop analysis have been done for the designed converter. Compared with conventional boost converters, the proposed converter has higher voltage gain, and it has low ripple values which is lesser than 1% which justifies is as a ripple less converter with an increased efficiency The proposed converter can be used in renewable systems, solar system applications, EV applications and flood lightning applications. And this proposed converter with Continuous Conduction Mode (CCM) and has high efficiency.
REFERENCES
[1] Babu, P. Ramesh, S. Ram Prasath, and R. Kiruthika. "Simulation and performance analysis of CCM Zeta converter with PID controller." In 2015 International Conference on Circuits, Power and Computing Technologies [ICCPCT-2015], pp. 1-7. IEEE, 2015. [2] Choudhary, Piyush, and Som Nath Mahendra. "Feedback control and simulation of DC-DC Cuk converter for solar photovoltaic array." In 2016 IEEE Uttar Pradesh Section International Conference on Electrical, Computer and Electronics Engineering (UPCON), pp. 591-596. IEEE, 2016. [3] Gnanavadivel, J., ST Jaya Christa, and R. Thangasankaran. "Performance Analysis of an Interleaved DC DC Cuk Converter with PI Controller." International Journal of Pure and Applied Mathematics 120, no. 6 (2018): 11321-11335. [4] Saravanan, S., and N. Ramesh Babu. "Design and development of single switch high step-up DCDC converter." IEEE Journal of Emerging and Selected Topics in Power Electronics 6, no. 2 (2017): 855-863. [5] Ye, Haixiong, GuangzheJin, Wang Fei, and NoradinGhadimi. "High step-up interleaved dc/dc converter with high efficiency." Energy sources, Part A: recovery, utilization, and environmentaleffects (2020): 1-20.
[6] Wai, R. J., and R. Y. Duan. "High-efficiency DC/DC converter with high voltage gain." IEE Proceedings-Electric Power Applications 152, no. 4 (2005): 793-802. [7] Amir, Asim, Aamir Amir, Hang Seng Che, Ahmad Elkhateb, and Nasrudin Abd Rahim. "Comparative analysis of high voltage gain DC-DC converter topologies for photovoltaic systems." Renewable energy 136 (2019): 1147-1163. [8] Ardi, Hossein, and Ali Ajami. "Study on a high voltage gain SEPIC-based DCDC converter with continuous input current for sustainable energy applications." IEEE transactions on power electronics 33, no. 12 (2018): 10403-10409. [9] Das, Moumita, and Vivek Agarwal. "Design and analysis of a high-efficiency DCDC converter with soft switching capability for renewable energy applications requiring high voltage gain." IEEE Transactions on Industrial Electronics 63, no. 5 (2016):2936-2944.
[10] Parthasarathy, S., V. Rajasekaran, and R. Sathishkumar. "Harmonic Mitigation in High Power DC Drive System Using Current Injection Technique." (2011): 93-100. [11] Kheraluwala, M. N., Randal W. Gascoigne, Deepakraj M. Divan, and Eric D. Baumann. "Performance characterization of a high- power dual active bridge DC-to-DC converter." IEEE Transactions on industry applications 28, no. 6 (1992): 1294-1301.
[12] Cuk, Slobodan, and R. D. Middlebrook. "A new optimum topology switching dc-to-dc converter." In 1977 IEEE Power Electronics Specialists Conference, pp. 160-179. IEEE, 1977. [13] Ye-Then Chang, Chia-An Yeh, Masahiro Hamaogi, Fumikazu Takahashi and Yen-Shin Lai, "Current ripple reduction tehnique of DC/DC converter," 2007 7th Internatonal Conference on Power Electronics, 2007, pp. 1087-1091. [14] S. Trampitsch, D. Gruber, M. Lunglmayr, E. Thaller and M. Huemer, "Digital compensation of DC-DC converter voltage ripple for Switched-Capacitor Power Amplifiers," 2016 14th IEEE International New Circuits and Systems Conference (NEWCAS), 2016, pp. 1-4. [15] Fardoun, Abbas A., and Esam H. Ismail. "Ultra step-up DCDC converter with reduced switch stress." IEEE transactions on industry applications 46, no. 5 (2010): 2025-2034. [16] Moradpour, Reza, Hossein Ardi, and AbdolrezaTavakoli. "Design and implementation of a new SEPIC-based high step-up DC/DC converter for renewable energy applications." IEEE transactions on industrial electronics 65, no. 2 (2017): 1290-1297. [17] Tomaszuk, A., and A. Krupa. "High efficiency high step-up DC/DC converters-a review." Bulletin of the Polish Academy of Sciences: Technical Sciences (2011): 475-483. [18] Hassan, Waqas, Dylan Dah-Chuan Lu, and Weidong Xiao. "Single-switch high step-up DCDC converter with low and steady switch voltage stress." IEEE Transactions on Industrial Electronics 66, no. 12 (2019): 9326-9338. [19] Haji-Esmaeili, Mohammad Mehdi, Ebrahim Babaei, and Mehran Sabahi. "High step-up quasi-Z source DCDC converter." IEEE Transactions on Power Electronics 33, no. 12 (2018): 10563-10571.
[20] Shang, Fei, GengNiu, and Mahesh Krishnamurthy. "Design and analysis of a high-voltage-gain step-up resonant DCDC converter for transportation applications." IEEE Transactions on Transportation Electrification 3, no. 1 (2017): 157-167.