
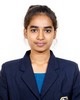
- Open Access
- Authors : Amrutha Rajamani
- Paper ID : IJERTV12IS030106
- Volume & Issue : Volume 12, Issue 03 (March 2023)
- Published (First Online): 25-03-2023
- ISSN (Online) : 2278-0181
- Publisher Name : IJERT
- License:
This work is licensed under a Creative Commons Attribution 4.0 International License
Heat Shields for Re-Entry Vehicles: A Review
Amrutha Rajamani
Department of Aerospace Engineering, Politecnico Di Milano, Italy, 20026
Abstract The Thermal Protection System is a crucial part of a space vehicle that ensures the success of a mission. This review is a study of various thermal protection mechanisms and materials used in various missions and the advancements required in each field according to the analyses conducted. The thermal and mechanical properties of the important ablative and reusable heat shield materials and the various environments encountered by the spacecraft in space missions are detailed as well. The thermal analysis methods and numerical modelling with relevant theoretical models required for thermal simulation are discussed. Some significant developments in planetary missions are studied.
Keywords Thermal Protection System, Re-entry vehicles, Spacecraft heat shields.
Space vehicles that enter the earths atmosphere require thermal protection systems to protect them from aerodynamic heating. The TPS system used by space vehicles inhibits the conduction of heat on the interior of the vehicle by combining an underlying layer of thermal insulation with high-temperature-resistant surface materials [5]. The materials used in space vehicles for thermal protection can be mainly categorized into two: Ablative and reusable materials. The subcategories of these materials and the material properties to be considered for an efficient TPS are discussed in this section.
INTRODUCTION
The Thermal Protection System (TPS) protects a spacecraft from extreme heat while entering the atmosphere and the severe low temperature and radiation while orbiting in space. A complicated array of materials comprises the TPS to help keep the astronauts and payloads safe during flights. There are two basic categories of TPS: ablative and reusable. The main selection criteria are using the lightest weight protection capable of handling the heat in a given area. However, in some cases, a heavier type is used if additional impact resistance is needed. The ablative TPS on the space capsule Apollo and ceramic tiles and blankets on the Space Shuttle Orbiter was designed as add-ons to the main load-bearing structure of the vehicles. Space vehicles that enter the earths atmosphere require thermal protection systems to protect them from aerodynamic heating. The TPS system used by space vehicles inhibits the conduction of heat on the interior of the vehicle by combining an underlying layer of thermal insulation with high-temperature-resistant surface materials. Friction with the atmosphere during re-entry produces extreme temperatures that require specialized shielding systems to protect space vehicles. In addition to heat, space vehicle thermal protection systems shield systems and the airframe from extremely cold conditions during parts of the orbit.
-
MATERIALS FOR THERMAL PROTECTION SYSTEMS
The term thermal protection system (TPS) refers to various materials applied externally to the outer structural skin on an orbiter to maintain acceptable temperatures, especially for the re-entry phase of a mission. Materials used for a TPS are selected for their high-temperature stability and weight efficiency.
-
ABLATIVE MATERIALS
The ablative heat shields burn off during re-entry and couldn't be re-used. This insulation is robust and reliable, and the single-use nature was appropriate for a single-use vehicle. Following are the various categories of ablative materials used in TPS where each material possesses specific heat protection, impact resistance, and weight characteristics, which determined the locations where it was used and the amount used [1].
Ablative thermal protection materials are usually classified by density into high-density, mid-density and low-density. The material strength increases with density, but so does the thermal conductivity. This requires a trade-off between mechanical and insulation efficiency, which is different for each mission. For instance, if a high-density material is used but the heat flux on the vehicle is too low to cause pyrolysis, then the materials high conductivity can allow heat flux conduction into the material, leading to the failure of the thermal protection system.
Figure 1: Re-usable vs. Ablative TPS.
Figure (1) shows a comparison of ablative and re-usable TPS in regard to the spacecraft velocity and the atmospheric altitude and density encountered in types of missions.
-
RE-USABLE MATERIALS
-
Reusable thermal protection systems (TPS) consist of materials that are mechanically or chemically unchanged by flight missions and can be safely flown a number of times (with or without servicing). The various materials used for re-usable TPS are categorized as the following: Carbon- Based Materials, Silicon-Based Materials, and Polyamides.
-
-
MATERIAL PROPERTIES TO BE CONSIDERED
Due to the wide variation of the temperatures experienced by a space vehicle, the TPS selected for the Space Shuttle was composed of many different materials. Each material's temperature capability, durability and weight determine the extent of its application on the vehicle.
Improvements to these materials have been the subject of much research as enhanced capability material (i.e., more durability, higher temperature capability, greater thermal shock resistance and lower thermal conductivity) improves thermal protection material and vehicle performance. Future re-entry vehicles capabilities will depend upon the capabilities of TPS being developed and available to them.
-
Heat load. Regulating the flow of heat into and out of the vehicle is the main role of thermal protection systems. In most situations, a TPS is designed around the aerodynamic heating during a vehicles re-entry into the Earths atmosphere. The TPS system must be able to withstand high temperatures without excessive degradation of material properties.
-
Mechanic loads. Extreme aerodynamic pressure and in-plane inertial, dynamic, and acoustic loads are all mechanical loads on the TPS. The TPS must withstand these loads without failure.
-
Deflection limits. The TPS shapes the vehicles aerodynamic profile. Surface deflections of the TPS need to be below a certain limit to maintain this aerodynamic profile and prevent local overheating and system failure.
-
Impact loads. The TPS can be subjected to many types of impact during installation, launch, flight, and landing. Having adequate impact resistance is an important requirement of a TPS.
-
Chemical deterioration. High surface temperatures during re-entry make the TPS susceptible to oxidation. It may also be altered during maintenance.
-
Low-cost operability. A TPS will require maintenance throughout its life, in addition to the initial fabrication and installation costs. A TPS should be easily replaceable or repairable as well as designed to withstand a certain amount of damage without requiring immediate repair.
-
Lightweight. Due to the large amount of space a TPS occupies, it makes up most of the launch weight. To prevent the need for increased fuel requirements, a TPS must be as lightweight as possible.
-
-
ABLATION AND THERMAL RESPONSE FOR HEATSHIELD ANALYSIS
The use of ablative materials has been a classical approach in the design of Thermal Protection Systems (TPSs) for over 60 years in a wide range of applications. The term ablation refers to the process of removing a material surfac through vaporization, chemical reactions, and/or erosion [10].
In the aerospace field, ablative materials are mainly used in the manufacture of heat shields. This type of thermal protection mechanism dissipates the high entering heat fluxes and the corresponding thermal loads via a phase change in the material, which results in the loss of ablative material mass. the ablation process involves a wide range of physical and chemical phenomena, most of which mutually interact.
-
THERMAL SIMULATION FOR ABLATION
During the atmospheric hypersonic flight of a spacecraft, a bow shock forms, increasing the temperature near the surface of the vehicle and creating an interaction between the bow shock and the boundary layer. The viscous flow in the boundary layer, in turn, increases the wall temperature, and the heat is transferred to the heat shield by energized particles through radiation and convection. The heat is thus transmitted by conduction from the outer surface of the shield to the entire underlying coating layer. Then, when the virgin ablative material has undergone adequate heating, a change of state begins [4].
A number of physical, chemical and mechanical phenomena are involved in the process of ablation. Simulation of the thermal response of ablative materials is very crucial for understanding the effectiveness of each material in its application. Developing an appropriate model for the simulation of ablation requires many factors to be considered.
A simple geometry considered for the thermal simulation of ablation is shown in Figure (6). The external surface is exposed to a convective and radiative heating environment [10]. The TPS can be a single or multi-layer composite and the inner layer is bonded to the structural component.
Figure 2: Simulation Geometry of Ablation TPS.
Many models of increased complexity have been introduced to simulate ablation and pyrolysis including one-dimensional and multidimensional representations. In the 1960s, Aerotherm Corporation developed the CMA code coupling the internal energy balance and decomposition equations with a general surface energy balance boundary condition and a thermochemical ablation model [8].
In 1997, NASA Ames Research Center developed the Fully Implicit Ablation Thermal response program (FIAT) code which solves the same equations as CMA but could achieve greater numerical stability.
-
FIATv2
The FIATv2 is the most recent upgraded version of the FIAT and combined into a single code. The FIATv2 application is available in ITAR (International Traffic in Arms Regulations
which is a United States regulatory regime to restrict and control the export of defence and military- related technologies to safeguard national security) and non- ITAR versions in which the ITAR version is available only for those working for the Crew Exploration Vehicle (CEV) program. The FIATv2 application runs in a Unix environment on Mac, PC and Linux platforms.
An example of a FIATv2 grid is illustrated in Figure (3) in which the temperature, pressure and density are defined at cell centres and the fluxes are defined at cell interfaces. FIATv2 generates a grid for each material ply automatically based on the material type and thickness. The grid in the top material is compressed in case of a recession. The maximum cell size does not exceed 0.1 inches.
The FIATv2 has three input files: one for the material properties, another for the surface environments and the main file contains all other input quantities. The code writes five output files and includes optimized ply thickness if optimization of ply thickness is performed to achieve a specified maximum temperature at a selected material interface. Some material properties may be input as a function of pressure. An air or radiation gap can be implied in the model according to the requirements defined by the user.
Figure 3: FIATv2 grid example with recession.
-
NUMERCAL MODELLING FOR FIATv2
The computation of numerical properties like density, mass flow and heat flux are discussed in section 3.2. The subsurface mass and energy conservation equations derived from a finite control volume are depicted in Figure (4). The pyrolysis gas flow is assumed to be in a quasi-steady state in the surface-normal direction.
The reduction in heat transfer coefficient due to the injection of pyrolysis gases and surface ablation into the boundary layer is accounted for by a blowing correction which is evaluated from the ratio of the blown (ablating) to the unblown (non-ablating) heat transfer coefficients The blowing correction equation involves a blowing correction parameter and a non-dimensional mass blowing rate [3] low.
Since the top ply is compressed to account for the recession the equations are complicated with some extra terms accounting for the non-Lagrangian movement of the grid. The surface energy balance (SEB) employed in FIATv2 is illustrated in Figure (5) which is used to determine the aerothermal conditions at the ablation surface at temperature Tw.
Figure 4: Internal mass and energy balances derived from a finite control volume.
The derivation of the surface energy balance is from the sum of various types of energy flux to and from the surface. The equation is simplified by assuming equal diffusion coefficients and equal Stanton numbers for heat and mass transfer (CM =CH).
Figure 5: Derivation of the surface energy balance.
-
ANALYSES SAMPLES
The non-ITAR version of FIATv2 provides two samples which are reported here. The first sample is the highest heat load location on a CEV-like geometry for a lunar-return skipping trajectory whose results are shown in Figure (6) and the second one is an arc jet test condition with three environments shown in Figure (7).
The analyses are performed for two different TPS materials: carbon phenolic, a pyrolyzing material used on the Pioneer Venus entry probe and Shuttle Reinforced Carbon-Carbon (RCC) which is a non-pyrolyzing material which is used on the Shuttle Orbiter.
For the lunar-return skipping trajectory case, the surface layer of heat shield material is to be optimized for a maximum temperature of 950 R at its lower surface. The initial guess for thickness is 3.5 inches while the estimated thickness is between 1 to 6 inches. The grid on the top material has a finer resolution to accompany recession while the subsurface cells have uniform grids.
The lunar skipping flight trajectory environment has two pulses with a cooldown phase. The first one ishigh-heatinging pulse with a short duration and the second pulse has a lower magnitude but a long duration. The pyrolyzing material (carbon phenolic) has a greater surface blowing than the non- pyrolyzing material (RCC) in each pulse.
Figure 6: Environment for lunar skipping flight trajectory.
On the other hand, the RCC has a greater solid ablation rate since the pyrolyzing carbon phenolic accounts for the internal decomposition. In the first heat pulse, the carbon phenolic has a higher pyrolysis gas blowing rate than the char ablation rate. It is vice versa in the second pulse since the phenolic has already been depleted near the composite surface.
Due to the high thermal conductivity of RCC at a lower temperature, a greater TPS thickness is required to limit the bondline temperature to 950 R which is 7.7 inches than for the carbon phenolic which requires only 3.3 inches for the same.
The three heating conditions run for the arc jet environment were cold-wall heat fluxes of 900, 1000 and 1100 W/cm2 which are 100 % heating with +/- 10% heating environments at a stagnation pressure of 0.75 atm for 30 seconds followed by 30 minutes cool down at low pressure. The thickness of the sample is 2 inches and no thickness optimization is carried out in this case. Each environment can be re-used for different scaling factors.
A fully implicit ablation and thermal response program have been developed for the simulation of one-dimnsional transient transport of thermal energy in a multilayer stack of isotropic materials and structures which can ablate from a front surface and decompose in-depth. The code is numerically more stable and solves a much wider range of problems compared with the existing explicit code.
Figure 7: Arcjet Environment.
Applications of the code include the analysis of aeroshell heatshields of Stardust, Mars 2001, and Mars Microprobe using the advanced Light Weight Ceramic Ablators developed at the NASA Ames Research Centre.
The FIATv2 launched in 2006 has expanded capabilities than the FIATv1 released in 1998 and has incorporated many upgrades enabling the code to simplify and facilitate the user to manage certain configurations of input parameters. FIATv2 is available to qualified individuals and organizations who have accessed the Non-disclosure and Software Usage agreement from the NASA Ames Research Centre.
-
-
TPS TECHNOLOGY FOR PLANETARY MISSIONS
The ablative TPS although a classical technique has proven to be very effective for planetary entry missions over many years due to its high heat load capacity and heating rates through a phase change and mass loss. NASA has employed ablative TPS for the planetary entry probes to date.
-
JUPITER MISSIONS
The Galileo mission to Jupiter by NASA was one of the most challenging missions it entered the Jovian atmosphere at a velocity of 47.4 km/s using fully dense carbon phenolic for the forebody which was the best ablative available at that time. The Giant Planet Facility (GPF) and a laser test facility were developed by NASA to understand the quality of TPS. The GPF was dismantled after the Galileo program.
The heat shield ablation in the Galileo probe is shown in Figure (8). It was studied from the ablation data of Galileo that the recession at the stagnation point was less than the predicted value and the recession at the shoulders was greater than the predicted value. The TPS thickness distribution was determined by adding some margins to the conservative thickness predicted.
Figure 8: Heatshield ablation in Galileo probe.
For a Jovian equatorial entry, 50% more mass fraction than the Galileo probe would be required and an even greater mass fraction will be required for probes entering higher altitudes. It is because the entry velocity is greater for higher altitudes which in turn increases the heating rates.
The heating increases with the cube of the entry velocity. For such missions, better TPS materials are required to reduce the TPS mass fraction since the fully dense carbon phenolic will lose a major amount of ablative mass by char spallation. A better ground test facility is required to qualify such an advanced material for Jupiter entry probe design.
-
MARS MISSIONS
NASA has delivered many landers and rover missions successfully to Mars so far. Several Mars lander missions like Mars Viking (1976), Mars Pathfinder (1997) and Mars exploration Rover (2003) have used a blunt 70-degree half- cone angle aeroshell and same forebody TPS material, Lockheed-Martin's SLA-561. Over the years, the entry, descent and landing mechanisms are sophisticated as the payload masses are increasing.
The Phoenix (2008) and Insight (2018) were landers sent to the Mars arctic region to look for water/ice and to the near- equatorial region to measure seismic and in-depth thermal variations, respectively. The Curiosity Rover (2012), weighing nearly a metric ton, was delivered to the Gale Crater to characterize the climate and geology of Mars to determine if it could have supported life in the past. Curiosity, powered by a multi-mission radioisotope thermoelectric generator (MMRTG), is still operational.
A similar, slightly heavier rover, Perseverance, was launched in 2020 for a 2021 landing at the Jezero Crater, where it will study the history and geology of Mars, attempt to produce oxygen from the CO2 atmosphere, explore other resources such as subsurface ice and cache samples for the next mission to retrieve and return. These missions were or will be, successfully protected by a set of thermal protection materials developed by industry and by NASA.
Mars missions, since the last decadal survey, have used materials including the NASA-invented Phenolic Impregnated Carbon Ablator (PICA), manufactured by Fiber Materials Inc. (now Spirit AeroSystems), various Super Lightweight Ablators from Lockheed Martin Space Systems (SLA-561V, SLA-561S, and SLA-220), and Acusil II from Peraton Inc. These materials are fully capable of withstanding the predicted heating for Mars missions and for the upcoming Dragonfly mission to Titan, from small vehicles (Pathfinder- sized) to large vehicles like Mars Science laboratory (MSL) launched in 2011.
The Mars atmosphere is primarily carbon dioxide, CO2, with about 4% nitrogen, N2. The oxygen in the CO2 at Mars will react with the carbon in the PICA char via oxidation and will cause the PICA to recede (get thinner) during entry. Surviving the entry conditions expected for current and even future missions is not the issue. However, as vehicle sizes grow, manufacturing and assembly issues will arise with these materials.
Although PICA is a capable TPS material, it has limitations due to how it is manufactured and its inherent material
properties. PICA heat shields can be cast in a single piece for small vehicles (<1.5m diameter) such as Stardust and OSIRIS-REx. However, for large aeroshells, PICA is applied in a tile format with filled gaps. PICA is manufactured from
~0.5m by 1.0m Fiberform (carbon reinforcement) rectangular blocks that are either 0.15m or 0.20m thick, which limits the net tile size.
In addition, these blocks have an inherent fibre direction that is perpendicular to the through-the-thickness direction, resulting in double the thermal conductivity in the fibre direction compared to the through-the-thickness direction. In order to retain the low thermal conductivity in the through- the-tile direction (toward the structure), the tile surface angle to the fibre is limited to 20.
This constraint further limits the achievable PICA tile size. To add even more complexity, PICA has a very low strain-to- failure, making it very brittle. Tile size, thickness, and attachment to structure method are all limited by this brittleness. Improving these properties is paramount to extending PICAs usefulness.
Various forebody TPS materials suitable for Mars entry and Titan entry with the potential limits of heat rate and pressure are shown in Table (1).
Table 1: Potential Heat Shield TPS Materials.
-
-
CONCLUSIONS
The Thermal Protection System (TPS) is an essential component of space vehicles to protect them against the aerothermal heating imposed on them during the atmospheric entry. Different types of TPS, including passive, semi-passive and active systems, have been developed and utilized in the last few decades. With the increasing demand for reusable launch vehicles (RLV) as well as new goals for interplanetary manned missions, the quest for developing effective TPS has been accelerated.
In 2003,Colombiaexploded upon re-entry into the atmosphere; a piece of insulation foam had broken during launch and struck the left wing, the shuttles heat shield was compromised and causing the breakup of the shuttle. After these two incidents, the safety of this kind of space travel was called into question and on July 21, 2011, Space
ShuttleAtlantiscompleted the last ever shuttle flight and the remaining three were retired.
In this review, the most important aspects of a Thermal Protection System while designing for a mission including the material type, mechanism, modelling and analyses required were discussed. The study shows that the TPS is indeed a crucial part of any successful space mission.
Abbreviations and Acronyms
CH = Stanton number for heat transfer
CM = Stanton number for mass transfer
Hr = recoveryenthalpy
h = enthalpy
= mass flux
P = pressure
q = conduction heat flux
qrad = radiative heat flux
T = temperature
t = time
= surface absorptance
= surface emissivity
= density
eueCH = heat transfer coefficient
= Stefan-Boltzmann constant
= surface-normal coordinate
c = char
g = pyrolysis gas
s = solid
w = surface (wall)
REFERENCE
[1] Steg. L. Materials for Re-Entry Heat Protection of Satellites. September 1960. [2] L.B. Keller. Development of Characterized and Reproducible Syntactic Foam of Phenolic Nylon for Heat Shields. Hughes Aircraft Report No. P66-49. December 1965. [3] N. H Kemp. Surface Recession Rate of an Ablating Polymer. AIAA Journal. 1968. [4] R. Finke. Calculation of Re-entry-Vehicle Temperature History.Institute for Defence Analyses, 1990.
[5] S. D. Williams, Donald. M. Curry. Thermal Protection Materials.NASA Reference Publication 1289. 1992.
[6] H.K Tran, D.J Rasky, L. Esfahani. Thermal Response and Ablation Characteristics of Lightweight Ceramic Ablators. Journal of Spacecraft and Rockets. December 1994. [7] Tran H.K. Phenolic Impregnated Carbon Ablators (PICA) as Thermal Protection Systems for Discovery Missions. NASA Technical Memorandum. 1997. [8] R. R Costa, J.A Silva, S.P Wu, Q.P Chu, J. A Mulder. Atmospheric Re- entry Modeling and Simulation. Journal of Spacecraft and Rockets. 2002. [9] B. Laub, E. Venkatapathy, Thermal Protection System technology and facility needs for demanding future planetary missions. NASA Ames Research Center. 2003. [10] F.S. Milos, Y.K. Chen, and T.H. Squire. Updated Ablation and Thermal Response Program for Spacecraft Heatshield Analysis. Thermal Protection Materials & Systems Branch NASA Ames Research Center, 2006