
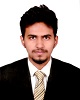
- Open Access
- Authors : Mohammad Raffi
- Paper ID : IJERTV9IS050263
- Volume & Issue : Volume 09, Issue 05 (May 2020)
- Published (First Online): 14-05-2020
- ISSN (Online) : 2278-0181
- Publisher Name : IJERT
- License:
This work is licensed under a Creative Commons Attribution 4.0 International License
GSM Assisted Unmanned Farming Vehicle (UFV)
Mohammad Raffi
Department of Automobile Engineering Hindustan Institute of Technology & Science Chennai, Tamil Nadu
AbstractThe main objective of designing this vehicle is to ease the farmers for the future agriculture purposes. In the present scenario, there are many recent Developments in the field of robotics and agriculture on a large scale. The methodology used in this paper is DTMF (Dual Tone Multi- Frequency). The unmanned farming vehicle (UFV) is controlled by a cell phone, through this we can make the vehicle communicate on a large scale over a large distance. This will help the farmer to control his Agricultural works from a far distance without going in the field with an easy control. The UFV has a number of advantages as well as important features such as automatic avoiding obstacles in its way. It can sense soil moisture and intimates weather moisture is present or not. It can also sow seeds in the field and also harvest the field. As a result, this machine can also be used to reach the places where farmers make harder efforts for farming such as hill areas, mountains etc. where land is not plane. This is how we can use this vehicle in different fields as well as for research purpose by further manipulation in programming it can be modified accordingly.
Keywords Soil Moisture Detection System, Relays, Obstacle Avoidance, Seed Sowing, Harvesteing, Easiness in Agriculture Technology
-
INTRODUCTION
Agriculture was the key development in the rise of human civilization. A remarkable change in agricultural practices has occurred over the past century in response to new technologies, and the development of world agricultural markets. This also has led to technological improvements in agricultural techniques. With the knowledge of design and applied science the robotics in this era plays a vital role in all the sector. The robotics have agility to perform any task with tireless time and in any harsh atmospheric conditions. Similar to this functions of the vehicle the GSM Assisted Multi frequency robotic control system have the capability to perform the agricultural task with the versatility to control the function from any location unless network is available. Our work provides the advantages of automation in seed sowing, obstacle avoidance, soil moisture detection as well as robust control by a cell phone, through this we can make this farming machine communicate from a very large distance provided there must be network connection in cell phone due to its wider range as large as the coverage area of the service provider. In this vehicle, we are controlling it through a wireless communication system using DTMF technology. As the system is supplied with 6.5V and the call is made to the vehicle, the user is required to press button
i.e. 2, 4, 6, 8 on the transmitting phone, the vehicle will move front, left right and back respectively. But if any obstacle is sensed by the vehicle, it will change its direction accordingly. This is also an intelligent system which includes soil moisture sensor which displays the weather the soil is moist or dry. Also,
this machine is an integration of various further agricultural units such as seed sowing and harvesting.
Fig. 1. Unmanned Farming Vehicle Small Scale Model
-
WORKING METHODOLOGY
-
Project Description
Fig. 2. Block Diagram of UFV System
Block diagram of farming vehicle as shown above. The vehicle contains components Arduino (ATmega328P), DC motor, mobile, battery, blade, seeding bottle, IR sensor, soil moisture. It works as per flow shown in block diagram. Remote provides operating command to a transmitter, via RF signal the transmitter transmit the signal to the vehicle. This signal received by receiver section of the vehicle and it physically operated. DC motor will actuate and the motor get revolution as per receiving command using motor drivers. Wheels are connected through DC motors, so that the motors get revolution the wheels are also rotated as given order reverse, forward, left and right with respective button present on remote. Firstly, burn the code into microcontroller Arduino using flash magic and switch on the power supply. Now send the command to the receiver mistreatment transmitter and
receiver these commands then automaton perform the cutting and seeding operation as per the given commands.
-
Technology Used in UFV
When a telephonic key is pressed the Dual Tone Multi Frequency produces a sound frequency, in todays world it finds several applications in the field of telecommunication. Each key is assigned to different frequency in the telephone dial-pad and there are two tones one high frequency and low frequency and that are generated simultaneously when a key is pressed. In a dial-pad each of the four rows of keys are assigned with a low frequency tone and each of the three column are assigned with a high frequency tone. There are sixteen DTMF signals, each one is made up of two tones from eight different frequency signals. Twelve of these signals are commonly used by consumers with four being reserved for military use or use by exchanges. The keys A, B, C, D are sometimes absent from phone sets utilized in homes and offices. These keys are system tones used for configuring phone exchanges and to hold out special functions.
The DTMF keypad for customers use is designed in a fourrow by three column matrix. Each dial row is represented by a low tone frequency and each column by a high tone frequency.
Fig. 3. Mobile Dial Pad with respect to its Frequencies TABLE I. DTMF Decoded Frequency Output
The frequencies used are 697 Hz, 770 Hz, 852 Hz, 941 Hz, 1209 Hz, 1336 Hz, 1477Hz, and 1633 Hz. The frequencies are carefully chosen in such a way as to prevent harmonics. Thus, one can notice that no frequency is a multiple of another and the difference or sum between any two frequencies is not equal
to any other frequency. The frequencies were initially designed with a ratio of 21/19, which is slightly less than a whole tone. Additionally, the frequencies generated have to be within an error tolerance of 1.5% and the higher
-
-
WORKING PROCEDURE
-
Equipments Required for the Machine
The following equipments have been used for the construction of the machine,
-
DC Motor
-
Printed Circuit Board
-
Relays
-
LCD Display
-
Lead Acid Battery
-
Soil Moisture Sensor
-
Infrared Obstacle Sensor
-
Motor Driver
-
DTMF Decoder Module
-
Arduino UNO
In this project we use the DTMF decoder module to convert analog signals from dial pad to digital signals which given as input to the Arduino accordingly which machine works. Then connected audio jack to the mobile and decoder module through which analog signals transfer to it. The L293D motor driver is a high voltage dual H bridge driver which are used to control DC and stepper motors. It is a 16 pin Integrated Chip which can controls two motors at a time in any direction. In this project we use this driver to run the motors as per the instructions given. A cell phone is connected to the vehicle through a 3.5mm audio jack (as shown in fig), receives call from the calling Subscriber. According to the generated DTMF frequencies from the cell phone, caller can control the movement of robot. IC L298N is designed in such a way to control two geared DC motors which takes command from the DTMF decoder through a Microcontroller. H-Bridge circuit is as shown in fg. 4 below.
Fig. 4. Motor and Motor Driver Connection Circuit Diagram
Fig. 5. Motor Assembly on Vehicle Chassis
-
-
Working Flow Chart & Circuite Diagram of UFV
Fig. 5. Working Flowchart of the UFV
Fig. 6. Circuit Diagram of UFV
-
-
RESULT ANALYSIS
GSM is utilized to communicate with vehicle through android and send the charges to the Microcontroller. As per the guidelines given by the client the vehicle moves in forward, turn around, left and right bearing to drop the seeds at a specific position. Four wheels are associated at the base for the adaptable development of vehicle. Two DC engines are utilized to drive the wheels associated with the robot. L293D is utilized to drive the DC engines. IR sensor is utilized to identify diverse obstruction in the way of the vehicle. In the event that any obstruction is distinguished in the way of the vehicle, it automatically diverts. In Seeding motors are utilized to drop a seed. Plant cutting is finished by engines. Using the soil moisture sensor, we can check weather moisture is present or not.
Fig. 7. Working Small Scale Model of UFV
Fig. 8. Soil Moisture Measurement
Fig. 9. Seeder Instrument for Seed Sowing
Fig. 10. Obstacle Detection Sensor IR Sensor
Fig. 11. Cutter for Harvesting Process
-
CONCLUSION
This project made in effort to overcome some problems in agriculture. The rapid growth in the industries is influencing the labours who are situating in the villages to migrate to the cities. This creating the labour problem for the agriculture. The wages for the labour is also more. As the prices of commodities such as food grains, fuels, cloths and other essentials of way of life is increasing chop-chop the labours demand for a lot of wages from the homeowners. This factors influencing the farmers who are interested in agriculture activity to leave their land uncultivated. By implementing this project in the field of agriculture we can help the farmers in different stage of agriculture i.e. during the seeding, irrigating and cutting. The project here is all about automatic control features with latest electronics technology using microcontroller and GSM phone line. The project works automatically and hence reduces the manpower.
REFERENCES
[1] Yun Chan Cho, who worked on developing a Remote Robot Control System based on DTMF of Mobile Phone. [IRJET] [2] [https://[doi 10.1109_IFOST.2014.6991152] Shifat, A. S. M. Zadid_ Rahman, Mohammad Shaifur_ Fahim-Al-Fatta — [IEEE 2014 9th International Forum on Strategic Technology (IFOST) – Cox's Bazar, Bangladesh (201.pdf]- [doi 10.1109_embeddedsys.2014.6953157] Srivastava, Amritanshu_ Vijay, Shubham_ Negi, Alka_ Shrivastava, — [IEEE 2014 International Conference on Embedded Systems (ICES) – Coimbatore, India (2014.7. (1)
-
J. Clerk Maxwell, A Treatise on Electricity and Magnetism, 3rd ed., vol. 2. Oxford: Clarendon, 1892, pp.68-73.