
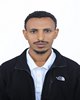
- Open Access
- Authors : Hunegnaw Ylkal Truneh , Dr. Getachew Alemu , Talegeta Moges Balcha
- Paper ID : IJERTV10IS070293
- Volume & Issue : Volume 10, Issue 07 (July 2021)
- Published (First Online): 09-08-2021
- ISSN (Online) : 2278-0181
- Publisher Name : IJERT
- License:
This work is licensed under a Creative Commons Attribution 4.0 International License
Fuzzy Logic based Automatic Plant Watering System
Hunegnaw Ylkal Truneh 1, Dr. Getachew Alemu 2, Talegeta Moges Balcha 1
1 Department of Electrical and Computer Engineering, College of Engineering, Assosa University, Assosa, Ethiopia.
2 Department of Electronics, School of Electrical and Computer Engineering, Institute of Technology, Addis Ababa University, Addis Ababa, Ethiopia
Abstract: – In this Study, design of fuzzy logic based automatic plant watering system for the crop maize is done. The health of a plant or crop is influenced by many different factors; like wind speed and direction, radiation, temperature and humidity and so on. The plant watering requirement for any crop is the amount of water that must be applied to meet the crop's evapotranspiration (ET) needs. The longer the growth period of the crop is the higher the water requirement. The dry moisture value is also the higher water requirement. Due to this, automatic plant watering system is the best solution for managing of water and to increase the production rate of the crop. Automatic plant watering system was done based on Fuzzy logic controller, which has three input parameters and one output parameter. The input parameters are moisture value of the soil (with range of 0 to 100 Percent), evapotranspiration difference (with range of -10 to 10 mm/day) and month after sowing of the crop (with range of 0 to 140 day). The output parameters are the duration of valve opening (with range of 0 minute to 30 minute). Penman-Monteith equation is used to compute the actual evapotranspiration of the specific crop from climate conditions. The difference between actual (calculated) evapotranspiration and the desired evapotranspiration is one of the input parameters for the fuzzy interface system. The evapotranspiration estimation has four input variables. These are humidity, temperature, radiation and wind speed. The duration of valve opening is gradually increased with the decreasing of Moisture value, mid-season of the crop sowing period and the decreasing of evapotranspiration difference. When the evapotranspiration difference is highly negative, the moisture value of the soil is dry and the month after sowing of the crop is in mid stage, the duration of valve opening was very long. And also, when the evapotranspiration difference is highly positive, the moisture value of the soil is wet and the month after sowing of the crop is in initial stage and late stage, the duration of valve opening was zero or very short.
Keywords: Fuzzy logic, Evapotranspiration, Fuzzy interface system, Penman-Monteith equation, plant watering.
-
INTRODUCTION
Plant watering system is artificial use of water to land or soil. It is used to assist in the growing of agricultural crops, maintenance of landscapes, and re vegetation of disturbed soils in dry areas and during periods of insufficient rainfall. Additionally, plant- watering system has a few other uses in crop production, which includes protecting plants against frost, suppressing weed growing in grain fields and helping in preventing soil consolidation. Plant watering is a system that is installed in agricultural land to improve the efficient use of water [1].
The continuous extraction of water from earth is reducing the water level due to which lots of land is coming slowly in the zones of un-irrigated land. This problem can be rectified if we use fuzzy logic based automated plant watering system in which the plant watering will take place only when there will be acute requirement of water [1]. In the field of agriculture, plant watering system plays key role. Effective utilization of water resources as well as preventing water losses is equally important. For this estimation of water, requirement of the crop is needed. The plant watering requirement for any crop is the amount of water that must be applied to meet the crop's evapotranspiration (ET) needs. The amount of ET includes water that is needed for both evaporation and transpiration. Evaporation occurs from all wet surfaces, including soil, water and plants. Transpiration is the evaporation from plant through the leaves stomata. Both evaporation and transpiration occur in response to climate demand [2]. The highest water crop needs are thus found in areas which are hot, dry, windy and sunny. The lowest water needs are found when it is cool, humid, cloudy and with little wind or no wind. The influence of the climate on crop water needs is given by the reference crop evapotranspiration (ETo). The ETo is usually expressed in millimetres per unit of time, e.g. mm/day, mm/month, or mm/season. Grass has been taken as the reference crop. Crops need high amount of water at middle stage of their growth [3]. Plant watering systems are divided in to two as manual and automatic plant watering system.
-
MEHODOLOGY
The procedure that follows to complete this study are as follows.
-
Reviewing various related materials, the area of the research was selected that is Benishangul Gumuz region specifically around Assosa
The environmental data was taken from three consecutive years 2017, 2016 and 2015 of Assosa, Ethiopia [8] to get the desired evapotranspiration value.
Specifically, this study concerns for the crop maize. The maize farms from June first to half of November based on the local rain season of Assosa. The evapotranspiration is Calculated using the PenmanMonteith equation.
The software used in this study are MATLAB 2017a. Penman-Monteith equation was used to compute the actual evapotranspiration of the specific crop from climate conditions. The difference between actual (calculated) evapotranspiration and the desired evapotranspiration is one of the input parameters for the fuzzy interface
Result by have been applied analysis based on the different values to input parameters of moisture, evapotranspiration difference and month after sowing, the corresponding crisp output of the fuzzy logic on the valve was determined.
Result by have been applied analysis based on the different values to input parameters of moisture, evapotranspiration difference and month after sowing, the corresponding crisp output of the fuzzy logic on the valve was determined.
-
-
SYSTEM MODELING AND DESIGN
The Fuzzy logic based automatic plant watering system consists of different parts: Input variables for Evapotranspiration calculation, evapotranspiration estimation or calculation, comparator, desired evapotranspiration, fuzzy logic controller, length of sowing period, moisture measurement and duration of valve opening as illustrated in Fig.3.1. Input variables temperature, humidity, net radiation and wind speed are fed to evapotranspiration (ETo) estimator block which computes actual value of evapotranspiration.
Humidity measurements
Desired Evapotranspiration
Moisture Measurement
Temperature Measurements
Evapotranspiration Calculation
Comparator Fuzzy logic controller
Duration of Valve Opening
Net Radiation
Wind Speed Measurements
Length of sowing period of
Fig. 3.1: Block diagram of the fuzzy based plant watering system
-
Temperature measurement
The temperature of an object is the amount of hotness or coldness in the environment that is generated by an object or system, allowing us to sense or detect any physical change to that temperature producing either an analogue or digital output. Temperature Sensor collects real-time data from the environment. It is the mean daily air temperature at 2 m height [°C].
-
Humidity measurement
Water vapor i the gaseous state of water and invisible to the human eye. The amount of water vapor that is needed to achieve saturation increases as the temperature increases. Humidity is the amount of water vapor present in the air. Humidity sensor is collects real-time data from the environment. The humidity sensor just senses the moisture of the soil. Humidity measurement is used to estimate the reference evapotranspiration.
-
Net radiation measurement
Net radiation is the difference between incoming solar radiation and outgoing infrared radiation. Earth absorbs incoming solar radiation and outgoing infrared radiation is lost to space. The net radiation (Rn) is the difference between the incoming net shortwave radiation and the outgoing net longwave radiation: high radiation will accelerate evapotranspiration [4].
The energy emitted by the sun is often called short-wave radiation because approximately 99% of the sun's energy is emitted in the short wavelengths. The percentages of the total energy emitted in various wavelengths from the sun are [5]: 9% in the ultraviolet wavelengths, 45% in the visible and 46% in the near infrared. Of this radiation, on average [5]: 20% is absorbed in the atmosphere by clouds and gases, 31% is reflected back to space and 49% is absorbed by the earth's surface (on a sunny day – 75%, on a cloudy day – 15%).
-
Wind speed measurement
Wind is characterized by its direction and velocity. Wind direction refers to the direction from which the wind is blowing. For the computation of evapotranspiration, wind speed is the relevant variable. Wind speed is a fundamental atmospheric quantity and caused by air moving from high pressure to low pressure, usually due to changes in temperature. Wind speed is one of the inputs for the reference evapotranspiration. To compute ETo the wind speed at 2 m above the ground surface is necessary.
-
Evapotranspiration Estimation
Water is used by crop through evaporation from the soil or water surface and by transpiration through the leaves. In the early stages of crop growth, most water is used through evaporation. The combined use of Evaporation and Transpiration is called evapotranspiration (ET). The total evapotranspiration varies from crop to crop. This quantity depends on seasonal conditions such as temperature, humidity, wind and sunlight hours as well as the length of the growing period. The Food and Agriculture Organization (FAO) of the United Nations has been proposed the famous and well-known Penman-Monteith equation, Allen et al. [6] as the most adequate method of calculating the reference evapotranspiration (ETo). The crop water requirements which is equal to the evapotranspiration (ET) for any crop can be calculated from the equation below
ETc = Kc x ETo (1)
Where,
= Reference evapotranspiration [mm/day] ETc = Water requirement of the crop
Kc= Crop coefficient
The crop reference evaporation (ETo) is determining from meteorological data. The FAO penman-Monteith method is maintained as the Best standard method for the computation of ETo from meteorological data. Evapotranspiration (ET) is the combination of evaporation and transpiration of hydrological cycle. Both evaporation and transpiration show the effect on hydrological cycle. Climatic conditions have direct influence on the evapotranspiration. The evapotranspiration as calculated with PenmanMonteith equation (2) and which has been adapted by the FAO (Food and Agricultural Organization) so far [6] is given by:
0.408 ( ) + 900 ( )
Where,
=
+ 237 2
+ (1 + 0.342)
(2)
= Reference evapotranspiration [mm.day-1]
= Slope vapor pressure curve [kPa.°C-1]
= Net radiation at the crop surface [MJ.m-2.day-1] G = Soil heat flux density [MJ.m-2.day-1]
= Psychometric constant [kPa.°C-1].
T = mean daily air temperature at 2 m height [°C]
2 = wind speed at 2 m height [m.s-1]
( )= Saturation vapor pressure deficit [kPa]
= Actual vapor pressure [kPa]
= Saturation vapor pressure [kPa]
The slope of saturation vapor pressure curve (, kPa/°C) can also be obtained in terms of air temperature (T, °C) as given by
Murray [19] in the following formula.
4098[0.6108 exp ( 17.27T )]
= T + 273
(237.3 + T)2
Also, the following best fit equation given by [20], it can be used for computation of .
(3)
= 0.00021501T2 0.00025132T + 0.061309 (4)
Saturated air vapor pressure es [kPa], can be obtained from the equation
17.27T
= 0.6108 exp (
T + 237.3
) (5)
The equation is reduced and can be expressed as given by [20]. It is used here for estimating saturated air vapor pressure es.
= 7.167 × 105T3 + 7.167 × 104T2 + 0.061309 × T + 0.57075 (6)
Vapor pressure of the actual air ea [kPa] depends on saturated air vapor pressure es and relative humidity RH that is defined as the ratio of actual vapor pressure in the air (ea) to that of saturated air (es) at the same temperature. Relationship between these three parameters is given by
Where,
RH = Relative humidity
es = saturated vapor pressure
ea =
es × RH
(7)
100
Soil heat flux density [MJ/m2 day] G is directly depending on net radiation; hourly value can be approximated as 0.1 times of net radiation.
The psychometric constant, is given by,
= 0.1 × (8)
= (9)
1.005(
= °
) × 101.3
(10)
Where,
= psychometric constant [kPa °C-1] P = atmospheric pressure [kPa]
= latent heat of vaporization, 2.45 [MJ kg-1]
0.622 × (2.51 0.00236 × (°))
Cp = specific heat at constant pressure, 1.013 10-3 [MJ kg-1 °C-1] = ratio molecular weight of water vapour/dry air = 0.622
-
Desired Reference Evapotranspiration
The reference evapotranspiration (ETo) is an important agro metrological parameter which has been used in water requirement of crop [7]. It is calculated using penman-Monteith equation by taking the average annual measured values of temperature, humidity, radiation, and wind speed. In this works to get the desired evapotranspiration value, the environmental data was taken from three consecutive years 2017, 2016 and 2015 of Assosa in tables below. Table 3.1 to Table 3.3 indicate annual temperature measurements at Assosa zone in the year 2017 to 2015 [8]. The data is used to calculate the reference ETo by taking average temperature of the month which is given in below tables.
Specifically, this thesis concerns for the crop maize. This crop farms from June first to half of November based on the local rain season of Assosa. The Average evapotranspiration of the month is given below for the three consecutive years. As illustrated in the Table 3.10 the highest evapotranspiration was calculated from November. This value is 15.3 mm/day. The lowest evapotranspiration was calculated from August. This value is 4.3 mm/day in the year 2017 and in Table 3.11, the highest evapotranspiration was calculated from November. The value of highest evapotranspiration was 18.6 mm/day. The lowest evapotranspiration was 4.8 mm/day, which was recorded in July 2016. At high evapotranspiration value, the water requirement for the specific crop is high and at low evapotranspiration value, the water requirement for the specific crop is low.
As illustrated in Table 3.3 the highest evapotranspiration was calculated in November. This value is 12.4. The lowest evapotranspiration was calculated in August, year 2015 whose value is 5.3 mm/day.
TABLE 3.1: FROM JUNE TO NOVEMBER THE ETo CALCULATION OF THE YEAR 2017
Month
Jun17
Jul17
Aug17
Sep17
Oct17
Nov17
Humidity (%)
57
72
77
72
56
31
Radiation (%)
28
12
14
28
41
39
Wind speed
4.5
4.3
4
4
3.1
3.8
Temperature
31
27
27
27
30
31
ETo (mm/day)
10.6
5.4
4.3
5.2
8.0
15.3
TABLE 3.2: FROM JUNE TO NOVEMBER THE ETo CALCULATION OF THE YEAR 2016
Month
Jun16
Jul16
Aug16
Sep16
Oct16
Nov16
Humidity (%)
61
75
72
65
55
27
Radiation (%)
21
4
12
22
29
45
Wind speed
4.9
4.3
3.8
3.8
3.1
4
Temperature
30
27
28
30
32
33
ETo(mm/day)
9.5
4.8
5.3
7.4
9.2
18.6
TABLE 3.3: FROM JUNE TO NOVEMBER THE ETo CALCULATION OF THE YEAR 2015
Month
Jun15
Jul15
Aug15
Sep15
Oct15
Nov15
Humidity (%)
67
70
72
68
63
40
Radiation (%)
17
14
16
26
28
37
Wind speed
4.7
4.5
3.8
3.6
3.1
3.4
Temperature
29
29
28
30
31
31
ETo (mm/day)
7.5
6.7
5.3
6.6
7.2
12.4
From [9] the maize mean water requirement during initial-stage is 1.3 mm/day, however within this stage slight variation in ETc is observed across the locations, where it varies between 1.1 to 1.7 mm/day. During developmental-stage, ETc is increases and it varies between 1.4 to 5.0 mm/day, whereas across the locations it varies between 1.0 to 5.7 mm/day. During the mid- stage season mean water requirement is also increases and varies between 5.0 to 6.6 mm/day whereas across locations it varies between 3.8 to
8.3 mm/day. During the late-season stage, ETc decreases progressively up to end of crop season. The ETc at this stage varies between 6.4 to 2.5 mm/day whereas across the locations it varies between 7.8 to 1.8 mm/day. The stage wise mean ETc for maize is 20.1, 94.5, 232.9 and 89.5 mm during initial-stage, dev-stage, mid- stage season and during late- stage season respectively. The total water requirement of maize is varying with its climate condition. For example, in the paper [9] the total water requirement higher at Bharuch (520.5 mm) whereas lower at Khedbrahma (380.7 mm). It is seen that the amount of water requirement increases with the stage of crop and across the locations. Variation in water requirement is more in mid-season stage followed by developmental stage of crops across the locations and less variation is observed in initial stage. The crop coefficient of the maize at different stages is as followed. During the initial stage, season of the maize crop coefficient is 0.3. At the development stage, season the crop coefficient is 1.2. At the mid stage season, the crop coefficient is 1.2 and at the late-stage season the crop coefficient is 0.35.
Generally, the evapotranspiration varies in average from 4.3 to 18.6 mm/day based on the local rain season of Assosa from three consecutive years. This evapotranspiration is good for the farming of maize. The climate condition between June and October is good for the farming of maize. The evapotranspiration values for those moths are between 4.3 to 10.6 mm/day. Therefore, between 5 to 10 mm/day in average for three consecutive years is better to use as a desired reference evapotranspiration. Therefore, the desired evapotranspiration is 8 mm/day in average.
-
-
Comparator
The purpose of the comparator compares the evapotranspiration estimation and the desired evapotranspiration. The Error value (evapotranspiration difference) is used as one input of the fuzzy logic controller.
-
Fuzzy logic Controller
Fuzzy set theory can handle real life uncertainties and therefore ideal for nonlinear, time varying and hysteretic system control. The membership functions are distributed according to the possible values of each variable after fuzzification [10,11]. There is no mathematical model exists for all parameters. Therefore, fuzzy logic technique is most suitable for modelling. Fuzzy logic controller behaves like human brain so it is better with doing this controller. The input parameters for fuzzy logic controller are the evapotranspiration differences, The soil moisture value and Length of sowing period of crop. Fuzzy logic controller decides the valve opening time. The fuzzy system could control the watering quantity by using fuzzy control rules to limit opening and closing time of valve. Mamdani inference algorithm will employ as fuzzy control model for this closed-loop control system [2]. Fuzzy controller will design by MATLAB fuzzy logic toolbox
Input data Fuzzifier Inference Engine
Defuzzifier Output Data
Rule Base
-
The FIS Editor
Fig.3.2: Fuzzy logic controller structure
The fuzzy logic control system modelled in MATLAB is being illustrated in Fig.3.3. In this figure, the input variables are defined as moisture value, evapotranspiration difference (error) and month after sowing. The fuzzy Inference System is called the maize using Mamdani method. Lastly, the output variable is shown that is the duration of valve opening
.
Fig.3.3: The fuzzy logic controller for plant watering system MATLAB Modelling
TABLE 3.4: MEMBERSHIP FUNCTION VALUE FOR INPUT VARIABLE MOISTURE VALUE
Membership Function name
Type of MF
Parameter range
Dry
Trapmf
[-1 0 20 30] Medium
Trimf
[15 40 65] Wet
Trapmf
[50 60 100 101] -
Input Variable Membership Functions
-
Fig.3.4: The input variable moisture MF
The moisture value is one of the input variable membership functions and it has three categories as illustrated in Fig.3.4. The MF has the range of 0 to 100%. And by divide in to three categories denoted by dry, medium and wet. Then the Dry has the range of 0% to 30%, medium has the range of 15% to 65% and wet has the range of 50% to 100%. The type of membership function for the Dry and wet is trapezoidal whereas the membership function for medium is triangular.
The evapotranspiration difference input variable has five categories as illustrated in Fig.3.5. The membership functions are denoted by LN, SN, EQ, SP and LP. And the evapotranspiration difference has a range of (-10) to (10) mm/day. The LN category has the range of -10 to -6 mm/day. The SN categry has the range of -7 to -1 mm/day, the EQ category has the range of -1.5 to
1.5 mm/day, the SP category has the range of 1 to 7 mm/day and the LP category has the range of 6 to 10 mm/day. The type of membership function for the SN, EQ, and SP is triangular and the membership function for the LN and LP is trapezoidal.
The length of sowing period input variable has four categories as illustrated in Fig.3.6. The membership functions are denoted by initial-stage, dev-stage, mid-stage and late-stage. The sowing period has a range of 0 to140 days. This range was taken from local rain season of maize in the case study area. The initial-stage category has the range of 0 to 20 days, the dev-stage category has the range of 15 to 65 days, the mid-stage category has the range of 40 to 110 days and the late-stage category has the range of 100 to 140 days. The type of membership function for all the initial stage, dev-stage, mid stage and late stage is triangular.
TABLE 3.5: MF VALUE FOR INPUT VARIABLE EVAPOTRANSPIRATION DIFFERENCE
Membership Function name
Type of MF
Parameter range
LN
Trapmf
[-11 -10.5 -7.5 -6] SN
Trimf
[-7 -4 -1] EQ
Trimf
[-1.5 0 1.5] SP
Trimf
[1 4 7] LP
Trapmf
[6 7.5 10.5 11] Fig.3.5: The input variable Evapotranspiration difference MF
Fig.3.6: The input variable length of sowing period MF
TABLE 3.6: MF VALUE FOR INPUT VARIABLE MONTH AFTER SOWING
Membership Function name
Type of MF
Parameter range
Initial-stage
Trimf
[0 10 20] Dev-stage
Trimf
[15 40 65] Mid-stage
Trimf
[40 75 110] Late-stage
Trimf
[100 120 140] TABLE 3.7: MF VALUE FOR OUTPUT VARIABLE DURATION OF VALVE OPENING
Membership Function name
Type of MF
Parameter range
Zero
Trimf
[0 0.5 1] v-short
Trimf
[0.5 3 5.5] Short
Trimf
[3 7.5 12] Long
Trimf
[10 15 20] v-long
Trimf
[18 24 30] -
Output variable membership functions
Fig.3.7: The output variable duration of valve opening MF
The duration of valve opening output variable has five categories as illustrated in Fig.3.7. The membership functions are denoted by zero, v-short, short, long and v-long. For this thesis, the duration of valve opening has a range of 0 to 30 minute. The zero category has the range of 0 to 1 minute. The v-short category has the range of 0.5 to 5.5 minutes. The short category has the range of 3 to 12 minute, the long category has the range of 10 to 20 minute and the v-long category has the range of 18 to 30 minutes. And for all the type of membership function for the zero, v-short, short, long and v-long is triangular.
-
Fuzzy Inference System Design
The linguistic fuzzy variables large negative (LN), small negative (SN), equal (EQ), small positive (SP), large positive (LP), initial-stage, dev-stage, mid-stage, late-stage, dry, medium, wet compares the three fuzzy sets; evapotranspiration difference, moisture value and month after sowing. The first input has five fuzzy variables and second input has three fuzzy variables whereas third input has four fuzzy variables, and used to develop Linguistic Rules in Table 3.17 to Table
-
The products of these rules are then aligned to determine the duration of valve opening of the actuator. The Table 3.17 to Table 3.19 shows how input linguistic variables derive the output fuzzy sets, which are zero, v-short, short, long, v-long.
3.3.4.1. Fuzzy Rules
Rule editor helps to edit the list of rules that defines the behaviour of the system. In rule based fuzzy systems, the relationships between variables are represented by means of fuzzy if-then rules for the crop maize 60 rules have been formed for description of fuzzy logic modelling. Since, we have three inputs (moisture value, evapotranspiration difference and month after sowing) for the fuzzy system. And, since each of these three inputs have different fuzzy variables. This moisture value has three fuzzy variables. These are wet, medium and dry. The evapotranspiration difference has five fuzzy variables. It includes LN, SN, EQ, SP and LP and also month after sowing has four fuzzy variables. It also includes initial-stage, dev-stage, mid-stage and late-stage. By simple combination, we can get 60 rules, which have been used, in our system.
Tables 3.8, 3.9 and 3.10 show the fuzzy rule-based system. As an example, some of these rules are given below:
-
If (the moisture is dry) and (Evapotranspiration difference is LN) and (length of sowing period is Initial stage) then (duration of Valve opening is long)
-
If (the moisture is dry) and (Evapotranspiration difference is SN) and (length of sowing period is Initial stage) then (duration of Valve opening is long)
-
If (the moisture is dry) and (Evapotranspiration difference is EQ) and (length of sowing period is Initial stage) then
(duration of Valve opening is short)
-
If (the moisture is dry) and (Evapotranspiration difference is SP) and (length of sowing period is Initial stage) then (duration of Valve opening is v-short)
-
If (the moisture is dry) and (Evapotranspiration difference is LP) and (length of sowing period is Initial stage) then (duration of Valve opening is zero)
-
If (the moisture is dry) and (Evapotranspiration difference is LN) and (length of sowing period is Dev-stage) then (duration
-
of Valve opening is v-long)
TABLE 3.8: FUZZY INPUT VARIABLES AND CORRESPONDING OUTPUT WHEN THE MOISTURE IS DRY
Month after sowing
ETo Difference
LN
SN
EQ
SP
LP
Initial stage
Long
Long
Short
v-short
Zero
Dev stage
v-long
v-long
Long
Short
v-short
Mid stage
v-long
v-long
Long
Short
v-short
Late stage
Long
Long
Short
v-short
Zero
TABLE 3.9: FUZZY INPUT VARIABLES AND CORRESPONDING OUTPUT WHEN THE MOISTURE IS MEDIUM
Month after sowing
ETo Difference
LN
SN
EQ
SP
LP
Initial stage
v-short
v-Short
Zero
Zero
Zero
Dev stage
Short
Short
v-Short
Zero
Zero
Mid stage
Short
Short
v-Short
Zero
Zero
Late stage
v-short
v-Short
Zero
Zero
Zero
TABLE 3.10: FUZZY INPUT VARIABLES AND CORRESPONDING OUTPUT WHEN THE MOISTURE IS WET
Month after sowing
ETo Difference
LN
SN
EQ
SP
LP
Initial stage
Zero
Zero
Zero
Zero
Zero
Dev stage
v-short
Zero
Zero
Zero
Zero
Mid stage
v-short
Zero
Zero
Zero
Zero
Late stage
Zero
Zero
Zero
Zero
Zero
-
Length of sowing period of crop
The correct choice of planting time is one of the most important decisions that a crop producer needs to make. It can be critical as far as crop yields and quality achieved are concerned. It can have an important bearing on various costs of production, such as the costs of insect and disease control. Moreover, it determines the season of harvest, and this normally affects prices received for the product. The highest water crop needs are thus found in areas which are hot, dry, windy and sunny. The lowest water needs are found when it is cool, humid, cloudy and with little wind or no wind. The influence of the climate on crop water needs is given by the reference crop evapotranspiration (ETo). Grass has been taken as the reference crop. Crops need high amount of water at middle stage of their growth.
-
Soil Moisture
Water contained in soil is called soil moisture. The water is held within the soil pores. Soil water is the major component of the soil in relation to crop growth. If the moisture content of a soil is optimum for crop growth, crops can readily absorb soil water. Not all the water, held in soil, is available to crops. Soil water dissolves salts and makes up the soil solution, which is important as medium for supply of nutrients to growing plants.
Soil moisture sensor measures the soil water and is critical in the whole decision. Outside temperature: To prevent water evaporation, the water planting process will avoid when the outside temperature is high.
-
Valve
This block is controls by the fuzzy logic controller by receiving the signal that is the duration of the valve opening time. Variable valve timing (VVT) systems is used. These systems refer to valve actuation systems that are able to change the duration of the valve timing [12].
-
-
RESULTS AND DISCUSSION
-
RESULTS
As discussed in chapter three, there are three input parameters for fuzzy logic controller. By combining two of these three input parameters alternatively, we can obtain three different surface plot of duration valve opening (moisture value with month after sowing, evapotranspiration difference with month after sowing and moisture value with evapotranspiration difference) as shown below. Based on the fuzzy rule, a surface plot of Duration of valve opening fuzzy prediction can be obtained, as shown in Fig.4.1. It shows that the duration of valve opening is gradually increased with the decreasing of Moisture value and mid-season of the crop sowing period. In this figure, the duration of the valve opening is highly increased in middle season that is between 20 days and 100 days after sowing and in the dry moisture is below 35%. In this case, the duration of valve opening is high.
When we combine month after sowing with evapotranspiration difference, a surface plot of Duration of valve opening fuzzy prediction can be obtained, as shown in Fig.4.2. It shows that the duration of valve opening is gradually increased with the decreasing of evapotranspiration difference and mid-season of the crop sowing period. In this figure the duration of the valve opening is highly increased in middle season that is between 20 days and 100 days after sowing and below the -2 (SN) of evapotranspiration difference. In this case, also the duration of valve opening is high.
Based on the fuzzy rule, a surface plot of Duration of valve opening fuzzy prediction can be obtained, as shown in Fig.4.3. It shows that the duration of valve opening is gradually increase with the decreasing of Moisture value and with the decreasing of evapotranspiration difference. In this figure the duration of the valve opening is highly increased below the -2 (SN) of evapotranspiration difference and in the dry moisture that is below 35%. In this case, the duration of valve opening is high.
As illustrated in Fig.4.4, the values of 50% (the moisture is medium), 0 (the evapotranspiration is zero) and 70 days (the month after sowing is mid stage) have been applied to the input variables of moisture, evapotranspiration difference and month after sowing respectively. The corresponding crisp output of the fuzzy logic on the duration of valve opening is 7.52 minute.
As illustrated in Fig.4.5, the values of 59% (the moisture is wet), 2.22 (the evapotranspiration difference is small positive SP) and 20 days (the month after sowing is initial stage) have been applied to the input variables of moisture, evapotranspiration difference and month after sowing respectively. The corresponding crisp output of the fuzzy logic on the duration of valve opening is 0.6 minute.
As illustrated in Fig.4.6, the values of 23.7% (the moisture is dry), (-5.3) (the evapotranspiration difference is large negative LN), and 82 days (the month after sowing is mid stage) have been applied to the input variables of moisture, evapotranspiration difference and month after sowing respectively. The corresponding crisp output of the fuzzy logic on the valve is 22.5 minute
Fig. 4.1: Surface view of Moisture value and crop sowing period Fig. 4.2: Surface view of ETo difference and sowing period
Fig. 4.3: Surface view ETo difference and moisture value Fig. 4.4: Rule view of fuzzy design plant watering system
Fig. 4.5: Rule view of fuzzy design plant watering system
Fig. 4.6: Rule view of fuzzy design plant watering system
Generally, when the evapotranspiration difference is highly negative, the moisture value of the soil is dry and the month after sowing of the crop is in mid stage then the duration of valve opening is very long. And when the evapotranspiration difference is highly positive, the moisture value of the soil is wet and the month after sowing of the crop is in initial stage and late stage then the duration of valve opening is zero or very short.
-
Discussion
This chapter discusses the designed system and its output, evapotranspiration estimation, desired evapotranspiration and difference of evapotranspiration. And also, it discusses the designed automatic plant watering system and output displays of duration of valve opening. The Evapotranspiration estimation value is compared with the desired evapotranspiration value and the error value (evapotranspiration difference) used as the one input of the fuzzy logic controller, in order to control the duration of valve opening. In the fuzzy controller design, we have three basic inputs Evapotranspiration difference, Moisture value and Month after sowing.
Evapotranspiration: to calculate the evapotranspiration difference, we need to know the evapotranspiration calculation, which is dependent on four variable parameters. These are: Humidity measurement, Temperature measurement, Radiation measurement and Wind speed measurement. Depending on different values of each of these four parameters, we get different value for evapotranspiration calculation and consequently which enables us obtain different values for evapotranspiration difference. For example, we have demonstrated in Fig.4.7, Fig.4.8 and Fig.4.9 as follows.
Exemplary explanation for Calculation of evapotranspiration input value
In the following part, we will consider three cases in which we do different analysis based on different input parameters of evapotranspiration estimation. And extract one of the three inputs of fuzzy controller to be designed values. We should notice that fuzzy logic controller has three inputs (moisture measurement, evapotranspiration difference and month after sowing) and in the following discussions, we have obtained for one of the three inputs (that is only for the evapotranspiration node input) for three different cases as follows. And, we have generated three different figures correspondingly.
Fig. 4.7: Evapotranspiration difference Simulink diagram
Fig. 4.8: Evapotranspiration difference Simulink Diagram Fig. 4.8: Evapotranspiration difference Simulink Diagram
Case 1: Based on the input values of the evapotranspiration estimation of Fig.4.7, the evapotranspiration difference is nearly zero
-0.3747 (zero). This result is obtained from the difference between the desired reference evapotranspiration and the evapotranspiration estimation. The desired reference evapotranspiration value is 7.13 mm/day. The evapotranspiration estimation is calculated by setting 67% for humidity measurement value, 29oC for temperature measurement, 17% for radiation and 4.7 mph for wind speed by using PenmanMonteith equation. The evapotranspiration estimation obtained for this setup is 7.5 mm/day in June 2015 at Assosa. In this case, the desired evapotranspiration and the evapotranspiration estimation are nearly equal.
Case 2: Based on the input values of the evapotranspiration estimation of Fig.4.8, the evapotranspiration difference is 1.71 (small positive (SP)). This result is obtained from the difference between the desired reference evapotranspiration and the evapotranspiration estimation. The desired reference evapotranspiration value is 7.13 mm/day. The evapotranspiration estimation is calculated by setting 72% for humidity measurement value, 27oC for temperature measurement, 12% for radiation and 4.3 mph for wind speed by using PenmanMonteith equation. The evapotranspiration estimation obtained for this setup is 5.4 mm/day in July 2017 at Assosa as shown in Fig.4.8. In this case, the desired reference evapotranspiration is greater than the evapotranspiration estimation.
Case 3: And also based on the input values of the evapotranspiration estimation of Fig.4.9, the evapotranspiration difference is – 3.857 (small negative SN). This result is obtained from the difference between the desired reference evapotranspiration and the evapotranspiration estimation. The desired reference evapotranspiration value is 7.13 mm/day. The evapotranspiration estimation is calculated by setting 57% for humidity measurement value, 31oC for temperature measurement, 28% for radiation and 4.5 mph for wind speed by using PenmanMonteith equation. The evapotranspiration estimation obtained for this setup is 10.64 mm/day in June 2017 at Assosa. In this case, the desired reference evapotranspiration is less than the reference evapotranspiration estimation. Fig.4.9 shows the output display of this value.
As we have seen for each three cases, we have obtained three values (-3.857 (small negative SN), -0.3747 (zero) and 1.719 (small positive SP) for the evapotranspiration difference input node of the fuzzy logic controller. And we use these three inputs (-3.857,
-0.3747 and 1.719) independently with other two inputs (moisture value and month after sowing).
As explained in the first part of this topic the three variables are dependent on different cord and can have different values. And having seen how the evapotranspiration difference is calculated, now we will consider and analyse the fuzzy logic controller system by applying all the three input variables that is evapotranspiration difference, moisture value and month after sowing as follows.
We will show the following analysis based on the different values of the mentioned inputs. Based on the Case 1 above, the evapotranspiration difference has been calculated and it used as one of the inputs for fuzzy logic controller. This evapotranspiration difference value -0.3747, the moisture value 50% and the month after sowing of 60 days are inputs for fuzzy logic controller. The output value of fuzzy logic controller is 7.084 minute (short). In this case, the valve is open for nearly seven minutes.
Secondly, based on the input values of the evapotranspiration estimation of Fig.4.11, the evapotranspiration difference is -8.173 (large negative LN). This result is obtained from the difference between the desired reference evapotranspiration and the evapotranspiration estimation. The desired reference evapotranspiration value is 7.13 mm/day. The evapotranspiration estimation is calculated by setting 31% for humidity measurement value, 31oC for temperature measurement, 39% for radiation and 3.8 mph for wind speed by using PenmanMonteith equation. The evapotranspiration estimation obtained for this setup is 15.3 in November 2017 at Assosa. In this case, the desired reference evapotranspiration is less than the reference evapotranspiration estimation. The evapotranspiration difference value -8.173 (large negative LN), moisture value 50 % (medium) and the month after sowing 60 days (dev-stage) are inputs for fuzzy logic controller. The output value of fuzzy logic controller is 22.5 minute (v-long).
Fig. 4.10: MATLAB Simulink diagram of automatic plant watering system
Thirdly, based on the input values of the evapotranspiration estimation of Fig.4.12, the evapotranspiration difference is 1.71 (small positive SP). This result is obtained from the difference between the desired reference evapotranspiration and the evapotranspiration estimation, as explained above in case 2. The evapotranspiration difference value 1.71 mm/day (small positive SP), the moisture value 50% (medium) and the month after sowing 60 days (mid-stage) are inputs for fuzzy logic controller. The output value of fuzzy logic controller is 2.56 minute (very short).
Fourthly, based on the input values of the evapotranspiration estimation of Fig.4.13, the evapotranspiration difference is -8.173 (large negative LN). This result is obtained from the difference between the desired reference evapotranspiration and the evapotranspiration estimation. The desired reference evapotranspiration value is 7.13 at 100 running time. The evapotranspiration estimation is calculated by setting 31% for humidity measurement value, 31oC for temperature measurement, 39% for radiation and 3.8 mph for wind speed by using PenmanMonteith equation. The evapotranspiration estimation obtained for this setup is
-
mm/day in November 2017 at Assosa. In this case, the desired reference evapotranspiration is less than the reference evapotranspiration estimation. The evapotranspiration difference value -8.173 (large negative LN), moisture value 50% (medium) and the month after sowing is 130 days (late-stage) are inputs for fuzzy logic controller. The output value of fuzzy logic controller is 7.5 minute (short).
Fig. 4.9: MATLAB Simulink diagram of automatic plant watering system
Fig. 4.12: MATLAB Simulink diagram of automatic plant watering system
Fig. 4.10: MATLAB Simulink diagram of automatic plant watering system
Fig. 4.14: MATLAB Simulink diagram of automatic plant watering system
Fifthly, based on the input values of the evapotranspiration estimation of Fig.4.14, the evapotranspiration difference is (-8.173). This result is obtained from the difference between the desired reference evapotranspiration and the evapotranspiration estimation. The desired reference evapotranspiration value added with the sine function is 7.13. The evapotranspiration estimation is calculated by setting 31% for humidity measurement value, 31oC for temperature measurement, 39% for radiation and 3.8 mph for wind speed by usig Penman-Monteith equation. The evapotranspiration estimation obtained for this setup is 15.3 mm/day in November 2017 at Assosa. In this case the desired reference evapotranspiration is less than the reference evapotranspiration estimation. the evapotranspiration difference -8.173 (large negative LN), the moisture value 30% (dry) and the month after sowing 15 days (initial-stage) are inputs for fuzzy logic controller. The output value of fuzzy logic controller is 7(Seven) minutes (short). The above discussion was summarized in below Table.
TABLE 4.1: SUMMERY OF THE RESULT
Input variables for Evapotranspiration
Input values for Evapotranspirat ion
ETo
Desired ET
Input values for Fuzzy
Output value
ET difference
Moisture value
Month after sowing
Duration of valve opening
Humidity
67%
7.5 mm/day
7.15
mm/day
-0.374 mm/day
50 %
60 days
7.84 minute
Temperature
29 oC
Radiation
17%
Wind speed
4.7 mph
Humidity
31%
15.3
mm/day
7.15
mm/day
-8.173 mm/day
50%
60 days
22.5 minute
Temperature
31 oC
Radiation
39 %
Wind speed
3.8 mph
Humidity
72%
5.4 mm/day
7.15
mm/day
1.71 mm/day
50%
60 days
2.56 minute
Temperature
27 oC
Radiation
12%
Wind speed
4.3 mph
Humidity
31%
15.3
mm/day
7.15
mm/day
-8.173 mm/day
50%
130 days
7.5 minute
Temperature
31 oC
Radiation
39 %
Wind speed
3.8 mph
Humidity
31%
15.3
mm/day
7.15
mm/day
-8.173 mm/day
30%
15 days
7.08 minute
Temperature
31 oC
Radiation
39 %
Wind speed
3.8 mph
-
-
CONCLUSION AND RECOMENDATION
-
Conclusion
The work presented in this study are automatic control plant watering system based on fuzzy logic controller. The increasing of humidity and the decreasing of temperature, radiation and wind speed is led to increase the evapotranspiration and vice versa as illustrated Fig.4.7, Fig.4.8 and Fig.4.9. At high evapotranspiration value, the water requirement for the specific crop is high and vice versa. The evapotranspiration difference, the moisture value and the month after sowing have effects on the growing of crops. The duration of valve opening is gradually increased with the decreasing of Moisture value, mid-season of the crop sowing period and the decreasing of evapotranspiration difference. As illustrated in Fig.4.5, the values of the moisture is 59% (wet), the evapotranspiration difference is 2.22 small positive (SP) and the month after sowing is 20 days (initial stage) have been applied to the input variables of moisture, evapotranspiration difference and month after sowing respectively. The corresponding crisp output of the fuzzy logic on the duration of valve opening is 0.6 minute. As illustrated in Fig.4.6, the values of the moisture is 23.7% (dry), the evapotranspiration difference is large negative LN (-5.3), and the month after sowing is mid stage (82 days) have
been applied to the input variables of moisture, evapotranspiration difference and month after sowing respectively. The corresponding crisp output of the fuzzy logic on the valve is 22.5 minute (V-long).
When the evapotranspiration difference is highly negative, the moisture value of the soil is dry and the month after sowing of the crop is in mid stage, the duration of valve opening was very long as illustrated in Fig.4.6. And also, when the evapotranspiration difference is highly positive, the moisture value of the soil is wet and the month after sowing of the crop is in initial stage and late stage, the duration of valve opening was zero or very short as illustrated in Fig.4.5.
-
Recommendation
Future research areas related to the plant watering system are listed below
-
In this paper the fuzzy logic system was develop for only one crop, no longer work for other crops. Therefore, the fuzzy system in this paper needs to be improved to be applied for those other crops.
This study work may be refined by considering exact measurement of environmental data at different local time.
REFFERENCES
-
G. Kumar, Water Irrigation by using wireless sensor network", International Journal of Scientific Research Engineering & Technology, 2014.
-
V.S.Rahagadale and D.S. Choudhary, "On Fuzzy Logic based Model for Irrigation Controller using penman-Monteith equation," 2nd National Conference on Information and Communication Technology, Gondia, 2011.
-
Vrieling, A. de Leeuw, Jan Said, Mohammed Y., Length of growing period over Africa, variability and trends from 30 years of NDVI Time Series. In: Remote sensing, Vol. 5, No. 2. pp. 982-1000, 2013.
-
NASA, Clouds & Radiation Fact Sheet," [Online]. Available: https://earthobservatory. nasa.gov/Features/ Clouds/clouds6.php. [Accessed 06 june 2018].
-
Wallace, John, and Peter Hobbs. Atmospheric Science an Introductory Survey. 2nd ed. New York: Elsevier, 2006.
-
Allen.R, "Crop Evapotranspiration Guidelines for Computing Crop Water Requirements," FAO Irrig. Drainag., Rome, 1998.
-
R. G. Allen, "Reference evapotranspiration (ETo) and crop water requirement (ETc) of wheat and maize in Gujarat," Journal of Agrometeorology, vol. 1, no. 17, pp. 107-113, 2015
-
National Metrological Service Agency at Assosa branch
-
Pandey, R. Mehta and Vyas, "Reference evapotranspiration (ETo) and crop water requirement of wheat andmaize in Gujarat," Journal of Agrometeorology, vol. 1, no. 17, pp. 107-113, June 2015.
-
R. Bellazzi, "Qualitative models and fuzzy systems:an integrated approach for learning from data," Artificial Intelligence in Medicine, vol. 14, no. 12, p. 528, 1998.
-
Gunturi, V.N. Rohit, "Micro Controller Based Automatic Plant Irrigation System," International Journal of Advancements in Research & Technology,
vol. 2, no. 4, pp. 2278-7763, 2013.
-
Li, L., Tao, J., Wang, Y., Su, Y. et al., "Effects of Intake Valve Closing Timing on Gasoline Engine Performance and Emissions," SAE Technical Paper 2001-01-3564, 2001.
-
F.Touati, M. Al-Hitmi and K.Behmed , "A fuzzy logic based irrigation managment system in arid rgions applied to the state of Qatar," Sustainable Irrigation and Drainage, vol. IV, no. 189, November 2012.
-
B. Stauffer and D. Spuhler, "Automatic Irrigation," SSWM University, 27 april 2018. [Online]. Available: http://www.sswm.info. [Accessed 15 may 2018].
-
The Fedral Demotratic Repuplic of Ethiopia Centeral Stastical Agency, "Area and Production of Crops," vol.1, ADDIS ABABA, 2008.
-
N. Siddique, A Hybrid Approach Based on Fuzzy Logic,Neural Networks and Genetic Algorithms, Switzerland: Springer International Publishing
, 2014.
-
Ruiz, J. Gutiérrez, and J. Fernández, "A fuzzy controller with an optimized defuzzification algorithm," IEEE Micro, vol. 11, no. 10, pp. 1-10, 1995.
-
A. Mamdani, "An experiment in linguistic synthesis with a fuzzy logic controller," International Journal of Man-Machine Studies, vol. 7, no. 1, pp. 1-13, 1975.
-
L. Zadeh, "Outline of a new approach to the analysis of complex systems and decision processes," IEEE Transactions on Systems, Man, and Cybernetics, vol. 3, no. 1, pp. 28-44, 1973.
-
Car N. and Christen E., "Using a mobile phone Short Messaging Service (SMS) for irrigation scheduling in Australia Farmers participation and utility evaluation," Computers and Electronics in Agriculture, vol. 84, no. 3, pp. 132-143, 2012.
-
Zhang, L. Bengtsson, L.Liao, "Soil moisture variation and waterconsumption of spring wheat and their effects on crop yield under drip irrigation,"
Irrigation Drainage System, vol. 5, no. 22, pp. 253270, 2008.
-
S.Tale and Sowmya p., "Intelligent Automatic Irrigation System," (IJCSIT) International Journal of Computer Science and Information Technologies,
vol. 7, no. 1, pp. 141-143, 2016.
-
V. R. Gunturi, "Micro Controller Based Automatic Plant Irrigation System," International Journal of Advancements in Research & Technolog, vol. 2, no. 4, pp. 2278-7763, April 2013.
-
F. W. Murray, "On the computation of saturation vapor pressure," J. Appl. Meteor, vol. 6, pp. 203-204, 1967.
-
M. El-Gayar, "Climate parameters used toevaluate the evapotranspiration in delta central zone of egypt," in Fourteenth International Water Technology Conference, Cairo, Egypt , 2010.
-
T. A. Izzuddin, M. A. Johari, M. Z. A Rashid and M. H Jali, "Smart Irrigation Using Fuzzy Logic Method," ARPN Journal of Engineering and Applied Sciences, vol. 13, no. 2, pp. 1819-6608, 2018.
-
A. Salam Al-Ammri, Sherin Ridah, " Smart Irrigation System Using Wireless Sensor Network," International Journal of Engineering Research & Technology, vol. 3, no.01, pp. 2278-0181, 2014.
-
S. Muhammad Umair, R. Usman, Automation of Irrigation System Using ANN based Controller International Journal of Electrical & Computer Sciences, vol.10, no.02, pp. 104602-5757, 2010.
-
G.Kokkonis, S.Kontogiannis, D.Tomtsis, A Smart IoT Fuzzy Irrigation System IOSR Journal of Engineering, vol.7, no.06, pp. 2278-8719, 2017.
-
Obota, M. E., and H. C, Soil moisture-based irrigation control system for rice cropping using wireless sensor network The International Journal of Engineering and Science. Vol.2, pp. 37-43. Inyama. 2013.
-
S. Siva Sankari and G. Mary Jansi Rani, A Wireless Monitoring and Controlling Automatic Irrigation Field, International Journal of Advanced Research in Electrical, Electronics and Instrumentation Engineering, Vol. 3, Issue 12, pp. 2278 8875, December 2014.
-
R. Yan, H. Sun, and Y. Qian (2013) Energy-aware sensor node design with its application in wireless sensor networks, IEEE Trans. Instrum. Meas., vol. 62, no. 5, pp. 11831191.
-
L.L.Pfitscher An automated irrigation system for rise cropping with remote supervision proceeding of international conference on power engineering, energy and electrical devices, vol. 50, pp 90. , 2011.
-
Xinrong Zhang Bo Chang, Design of Water saving irrigation Monitoring System Based on Fuzzy-PID, Journal of Control Engineering and Technology (JCET), vol. 2, no. 3, P. 124-129, 2012.
-
Siddique, N. (2014). A Hybrid Approach Based on Fuzzy Logic, Neural Networks and Genetic Algorithms. United Kingdom: Springler.
-
Kala, J., T.J. Lyons, I.J. Foster,U.S.,Nair, Validation of a siple steady-state forecaste of minimum noctural tempratures, Journal of Applied metrology and Climatology, vol. 48, P. 624-633, 2009.