
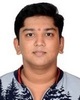
- Open Access
- Authors : Nikhil Navin Shete , Omkar Madhukar Patil , Pratiksha Gitaram Thube , Mukku Prashant Reddy, Pallavi Vivek Dongre
- Paper ID : IJERTV9IS090472
- Volume & Issue : Volume 09, Issue 09 (September 2020)
- Published (First Online): 30-09-2020
- ISSN (Online) : 2278-0181
- Publisher Name : IJERT
- License:
This work is licensed under a Creative Commons Attribution 4.0 International License
Fly Ash based Geopolymer Concrete
*1 Pallavi Vivek Dongre, *2 Pratiksha Gitaram Thube, *3 Omkar Madhukar Patil
*4 Nikhil Navin Shete, *5 Mukku Prashant Reddy
*1Professor , *2Student,
Department of Civil Engineering,
Vishwaniketan’s Institute of Management Entrepreneurship and Engineering Technology, Raigad, Maharashtra, India.
Abstract:- Manufacturing of Portland cement process that releases large amount of Carbon dioxide into atmosphere. To reduce this pollution another cementitious materials like Geopolymer can be used. OPC can be replaced Fly ash based Geopolymer concrete. This research paper reviews experimental investigations on ordinary Portland cement cubes and fly ash based geopolymer concrete cubes that are Strength of Geopolymer concrete with different water/geopolymer ratio,Comparision of Compressive strength between OPC and Geopolymer concrete with respect to curing temperature as well as Compressive strength of fly ash based geopolymer concrete cubes in different curing time.
Keywords: Ordinary Portland cement, Fly ash based Geopolymer Concrete, Compressive strength, Curing time, Curing temperature.
INTRODUCTION
Manufacturing of Portland cement is a resource exhausting, energy intensive process that releases large amount of the greenhouse gas (CO2) into the atmosphere. Production of one ton of Portland cement requires about 2.8 tons of raw materials, including fuel and other materials. As a result of de-carbonation of lime, manufacturing of one ton of cement generates about one ton greenhouse gas. At present, efforts have been made to promote the use of pozzolana to practically replace Portland cement. Recently, another class of cementitious materials, produced from an alumino- silicate activated in a high alkali solution, has been developed. This cementitious material is termed as geopolymer. The mortar and concrete made from geopolymer possess similar mechanical performance and appearance properties to those from Portland cement. It is well known that geopolymer have excellent performance with respect to fire resistance, acid resistance and stabilization/solidification of heavy metal waste.
MATERIALS
WATER- Although the water itself is often not considered when dealing with materials that go into the production of concrete, it is an important ingredient. Typically, optimum quantity of water is used, such that we can easily get the workability required so that we can have a workable and ease of concrete mixing. The old rule of 3 thumb for water quality is If you can drink it, you can use it in concrete, although good-quality concrete can be made with water that is not really potable. Indeed, more bad concrete is made by using too much drinkable water than by using the right
amount of undrinkable water. When in question, the suitability of the water is determined by comparing the strength of concrete made with the suspect water to the strength of concrete made with known acceptable water.
Geopolymer An alkaline liquid could be used to react with the silicon (Si) and the aluminium (Al) in a source material of geological origin or in by-product materials such as fly ash and rice-husk ash to produce binders [9]. Because the chemical reaction that takes place in this case is a polymerization process, he coined the term geopolymer to represent these binders. Geopolymer are members of the family of inorganic polymers. The chemical composition of the geopolymer material is similar to natural zeolite materials, but the microstructure is amorphous. The polymerization process involves a substantially fast chemical reaction under alkaline conditions on silicon aluminium minerals that results in a three-dimensional polymeric chain and ring structure consisting of SiOAlO bonds (Davidovits, 1994). To date, the exact mechanism of setting and hardening of the geopolymer material is not clear, but the formation of geopolymer materials can be described as shown in Equation (Davidovits, 1994; van Jaarsveld et al., 1997):
The last term in Equation reveals that water is released during the chemical reaction that occurs during the formation of geopolymer. This water, expelled from the geopolymer matrix during the curing and further drying periods, leaves behind discontinuous Nano pores in the matrix which provide benefits to the performance of geopolymer. The water in a geopolymer mixture, therefore, plays no role in the chemical reaction that takes place; it merely provides workability to the mixture during handling.
This is in contrast to the chemical reaction of water in a Portland cement concrete mixture during the hydration process. The two main constituents of geopolymer are the source materials and the alkaline liquids. The source materials for geopolymer based on aluminasilicate should be rich in silicon (Si) and aluminium (Al).
Fly Ash Fly ash is one of the residues generated in combustion, and comprises the fine particles that rise with the flue gases. Ash which does not rise is termed bottom ash. In an industrial context, fly ash usually refers to ash produced during combustion of coal. Fly ash is generally captured by electrostatic precipitators or other particle filtration equipment before the flue gases reach the chimneys of coal-fired power plants, and together with bottom ash removed from the bottom of the furnace is in this case jointly known as coal ash. Depending upon the source and makeup of the coal being burned, the components of fly ash vary considerably, but all fly ash includes substantial amounts of silicon dioxide (SiO2) (both amorphous and crystalline) and calcium oxide (CaO), both being endemic ingredients in many coal-bearing rock strata
Aggregates make up about 75% of the volume of concrete, so their properties have a large in hence on the properties of the concrete .Aggregates are granular materials, most commonly natural gravels and sands or crushed stone, although occasionally synthetic materials such as slags or expanded clays or shales are used. Most aggregates have specific gravities in the range of 2.6 to 2.7, although both heavyweight and lightweight aggregates are sometimes used for special concretes Also, because they are less expensive than Portland cement, aggregates lead to the production of more economical concretes. In general, aggregates are much stronger than the cement paste, so their exact mechanical properties are not considered to be of much importance (except for very high-strength concretes). Similarly, they are also assumed to be completely inert in a cement matrix, although this is not always true, as will be seen in the discussion on the alkaliaggregate reaction. For ordinary concretes, the most important aggregate properties are the particle grading (or particle-size distribution), shape, and porosity, as well as possible reactivity with the cement. Of course, all aggregates should be cleanthat is, free of impurities such as salt, clay, dirt, or foreign matter. As a matter of convenience, aggregates are generally divided into two size ranges: coarse aggregate, which is the fraction of material retained on a No. 4 (4.75-mm) sieve and fine aggregate, which is the fraction passing No. 4 sieve but retained on a No. 100 (0.15-mm) sieve.
Sodium Hydroxide, Sodium silicate solution a combination of sodium silicate solution and sodium hydroxide (NaOH) solution can be used as the alkaline liquid. It is recommended that the alkaline liquid be prepared by mixing both of the solutions together at least one day prior to use. The sodium silicate solution is commercially available in various grades. A solution with a NaO/SiO ratio by mass of approximately 2 (say,NaO = 14.7%, SiO = 29.4%, 2 22 2 and water = 55.9%) is recommended. Sodium
hydroxide with 98% purity, in take or pellet form, is commercially available.
METHODOLOGY
- WATER GEOPOLYMER SOLID RATIO TEST.
CONSTITUENTS
Aggregates -20mm (Retaining),14mm(Retaining),7mm(Retaining).Crushed sand, Water, Alkaline liquids :- Sodium Hydroxide, Sodium Silicate, Alkaline liquids to fly ash ratio(A/F RATIO) – 0.3 , 0.35 , 0.4.(TOTAL 3 CUBES OF EACH).
MIX PROPORTION
- Aggregate fly ash ratio as 0.3
- volume 0.15 M3
- Weight of concrete = 8.100 KG
- Mass of combined aggregates=77% of 8.1kg= 6.237kg
- Mass of 20mm aggregates=15% of 6.237kg=935.5g
- Mass of 14mm aggregates=20% of 6.237kg=1.2474kg
- Mass of 7mm aggregates=35% of 6.237kg=2.183kg
Fine sand=30% of 6.237kg =1.8711kg
- Now, taking alkaline liquid to flash ratio=0.3
Mass of fly ash=1.863/(1+0.3)=1.433kg
- Mass of alkaline liquid=0.4299kg
- Mass of NaOH solution=0.4299/(1+2.5)=0.1228kg
- Mass of sodium silicate solution=0.307kg
PROCEDURE
- Slump cone test to determine A/F RATIO.
- Calculating Amount of f each Constituents.
- Calculating WATER/ GEOPOLYMER SOLIDS RATIO.
- Mixing of Concrete as per calculations of material.
- Casting of 3 Cubes.
- Compacting.
- Curing for 27 days
- Adopting compressive test for each cubes.
- Take average of each test for result
- RELATIONSHIP BETWEEN EFFECTS OF CURING TEMPERATURE ON COMPRESSIVE STRENGTH.
CONSTITUENTS
- Fly ash, Crushed sand, Alkaline liquid, Coarse Aggregate, A/F RATIO-0.35, Curing temperature- 30C, 60C, 90C.TOTAL CUBES-3(OPC) 3 (FLY ASH GEOPOLYMER CUBES).
PROCEDURE
- Slime Cone test to determine A/F RATIO.
- Mixing of Fly ash concrete.
- Mixing of OPC concrete.
- Casting of 3 cubes each.
- Curing in oven for 24 hours.
- Curing in different temperature (30, 60, 90)
- Adopting compression test for each cube.
- Note the Difference between results.
- Fly ash, Crushed sand, Alkaline liquid, Coarse Aggregate, A/F RATIO-0.35, Curing temperature- 30C, 60C, 90C.TOTAL CUBES-3(OPC) 3 (FLY ASH GEOPOLYMER CUBES).
- RELATIONSHIP BETWEEN EFFECTS OF CURING TIME ON COMPRESSIVE STRENGTH.
CONSTITUENTS
- Fly ash, Crushed sand, Alkaline liquid, Coarse Aggregate, A/F RATIO-0.35, Curing time 95 hours,(TOTAL CUBES 7).
PROCEDURE
- Mixing of Concrete by A/F RATIO 0.35
- Casting 7 cubes of Fly ash Geopolymer concrete.
- Oven curing in 60
- Performed Compression test at 5 hours to 95 hours.
- Noted difference between strength in each cube.
CONCLUSION
This paper presented the development of geopolymer concrete. The binder in this concrete, the geopolymer paste, is formed by activating by-product materials, such as low- calcium (Class F) fly ash, that are rich in silicon and aluminium.
In the experimental work, the fly ash from a local power generation plant was used as the source material. A combination of sodium silicate solution and sodium hydroxide solution was used as the activator. The geopolymer paste binds the loose coarse and fine aggregates and any unreacted materials to form the geopolymer concrete. After comparison of results by test performed it can clearly observed that ordinary Portland concrete can be replaced with fly ash based Geopolymer concrete
Higher concentration (in terms of molar) of sodium hydroxide solution results in a higher compressive strength of geopolymer concrete.
Higher the ratio of sodium silicate-to-sodium hydroxide liquid ratio by mass, higher is the compressive strength of geopolymer concrete.
As the curing temperature in the range of 30 to 90 °C increases, the compressive strength of geopolymer concrete also increases.
Longer curing time, in the range of 6 to 96 h (4 days), produces larger compressive strength of geopolymer
concrete. However, the increase in strength beyond 48 h is not significant.
REFERENCES
- Review on Fly Ash Based Concrete without Ordinary Portland cement By Mohd Mustafa Al Bakri, H. Mohammed, H.Kamarudin, I. KhairulNiza and Y. Zarina.
- Performance of Fly Ash Based Geopolymer Mortars In Sulphate Solution By S. Thokchom1, P. Ghosh and S. Ghosh.
- Strength and Workability of Low Lime Fly-Ash Based Geopolymer Concretely B. Siva Konda Reddy J. Varaprasad and K.Naveen Kumar Reddy.
- Strength and Water Penetrability of Fly Ash Geopolymer Concrete by Monita Olivia and Hamid R. Nikraz.
- Performance Of Geopolymeric Concrete Reinforced With Steel Fibres By Susan, Bernal; Ruby, De Gutierrez; Silvio, Delvasto; Erich, Rodriguez.
- Valorisation of Fly Ashes by Geopolymerisation by J.L. Provis P. Duxson R.M. Harrex C-Z.Yong J.S.J. Van Deventer.
- Compressive Strength and Workability Characteristics of Low- Calcium Fly Ash-Based Self-Compacting Geopolymer Concrete by M. Fareed Ahmed, M. FadhilNuruddin, and NasirShafiq.
- Geopolymer Concrete with Fly Ash By N A Lloyd and B V Rangan.
-
J. Davidovits, Properties of geopolymer cements, Proceedings of the first International conference on alkaline cements and concretes vol.1, SRIBM, Kiev (1994) 131-149.
- Geopolymer Institute. 2010. What is geopolymer? Introduction Institute Géopolymère, Saint-Quentin, France. Accessed on January 29, 2010, at http://www.geopolymer.org/science/introduction.
- Fly ash-based geopolymer concrete Djwantoro Hardjito, Steenie E Wallah, Dody MJ Sumajouw,& B Vijaya Rangan Faculty of Engineering and Computing,CurtinUniversityofTechnologyPerth,WesternAustralia
- Influence of Curing Types on Strength of Geopolymer Concrete Prof.K.Vijai, Associate Professor, Dr. R.Kumutha, Professor & Head Department of Civil Engineering Sethu Institute of Technology Pulloor, TamilNadu, and Dr B.G.Vishnuram, Principal Easa College of Engineering & Technology, Coimbatore.
- Geopolymer Concrete with Fly Ash By N A Lloyd and B V Rangan Curtin University of technology, GPO Box U 1987, Perth 6845, Western Australia, Australia.
Email n.lloyd@curtin.edu.au.HYPERLINK “mailto:n.lloyd@curtin.edu.au.%3cv.rangan@curtin.edu.au”<HY PERLINK
“mailto:n.lloyd@curtin.edu.au.%3cv.rangan@curtin.edu.au”v.ran gan@curtin.edu.au>
- On the Development of Fly Ash-Based Geopolymer Concrete by Djwantoro Hardjito, Steenie E. Wallah, Dody M. J. Sumajouw, and B.Vijaya Rangan.
- Concrete Construction Engineering Handbook by Edward G. Nawy, Editor in Chief.