
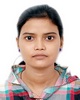
- Open Access
- Total Downloads : 15
- Authors : Ms. Jyoti Rathore , Er. Rahul Malik , Kamya Dhingra
- Paper ID : IJERTV8IS040183
- Volume & Issue : Volume 08, Issue 04 (April – 2019)
- Published (First Online): 13-04-2019
- ISSN (Online) : 2278-0181
- Publisher Name : IJERT
- License:
This work is licensed under a Creative Commons Attribution 4.0 International License
Fluid Structure Interaction Analysis of Tapered Wing of Aircraft
Ms. Jyoti Rathore
M.tech Student, Mechanical Department,
-
College of Engineering, DCRUST University, Haryana
Kamya Dhingra
Assistant Professor, ECE Department, Dr Akhilesh Das Gupta Institute of technology & Management, IP University, New Delhi
Er. Rahul Malik
H.O.D., Mechanical Department,
P.M. College of Engineering, DCRUST University, Haryana
Abstract Fluid structure interaction (FSI) analysis, which is the most emerging area of numerical simulation and calculation. FSI occurs due to flow of fluid influences the properties of a structure or vice versa. The fluid structure interaction phenomenon is not specific it occurs in almost every field of engineering and always remains attraction of engineers and researcher of different fields. Commercial available software ANSYS is used in this study to analyze fluid structure interaction of the wing of cross section NACA2412 airfoil.
Keywords- 1 ANSYS Workbench, 2CFD, 3 FSI,4 NACA Airfoil, 5RANS
wing is called as leading edge and thin end is trailing edge. Length of straight line joining the leading edge to trailing edge of airfoil is known as chord length of airfoil. Line joining the locus of points which is equidistant from upper surface to lower surface is known as camber line of airfoil. When camber line is coincide with the chord line, the airfoil will be symmetrical. If camber line lies above the chord line of airfoil, it will be positive cambered airfoil. Present work has been carried out on NACA2412 airfoil, which is positive cambered airfoil.
-
INTRODUCTION
Aero elasticity is an aerodynamic phenomenon in which we study the effect of the aerodynamic forces on elastic bodies, when solid body interacts with fluid. During analysis of dynamic system of structure, if aerodynamic loading is taken into account then the resultant phenomenon is classified as aero elastic. Theory of elasticity deals with the effect of external displacement and aerodynamic forces on deformation and stress of an elastic body. Deformation of a structure of body is generally not depends on the extent of external forces acts on it so in most of the case deformation is to be assumed as a very small and presume it will not affect by the action of forces acts externally. Based on this assumption the change in dimension of body was neglected often and calculations are purely consider by taking the initial shape of the object, in other words initial dimensions of object is taken for calculation. While reality is different in most of the problems of aero elasticity. The extent of aerodynamic forces depends upon structure body attitude relative to the flow. External loading of body is generally determined by elastic deformation of the body. In other words to determine the magnitude of aerodynamic force pre knowledge of elastic deformation is required. So design of flight vehicles is strongly influenced by aero elastic phenomenon and hence its analysis is very important.
Aircraft wing
In aviation field effort is continuously made to decrease the weight of the wing while increasing its strength, so that it can supports the weight of whole aircraft by producing the enough lift force. The cross section of wing is known as airfoil, which may be symmetrical or cambered. Thick end of
Fluid-structure interaction (FSI)
Fluid Structure Interaction is a multi-physics coupling between the laws that describe structural mechanics and fluid dynamics. This phenomenon can be characterized by stable or oscillatory interactions between a moving or deformable structure and internal fluid flow or surrounding. Stresses exerted on the structure due to passing of airflow over the structure and it leads to strains are on the solid object. This induced stress and strains causes body will deformed. The extent of deformation totally depends upon the velocity and pressure of flow of fluid and also on the properties of material of the actual structure.
Fluid-structure interactions can be classified into three groups:
-
Zero strain interactions: such as the transport of suspended solids in a liquid matrix.
-
Constant strain steady flow interactions: The constant force exerted on an oil-pipeline due to viscous friction between the pipeline walls and the fluid.
-
Oscillatory interactions: In this interaction the induced strain in the solid structure will move in such a way that the source of strain is diminished and the structure will returns to its previous state only for the process to repeat.
-
-
SOME RESEARCH STUDY RELATED TO FSI ANALYSIS
Fluid- Structure interaction problems have been investigated by Goud et. al (2014) on AGARD 445.6 wings at transonic flow regime. The simulated result of wing at this speed was compared by previous result. The tip motion of wing was noted during flutter test at M=0.9, while dynamic pressure is
varied. At each Mach number they observed a flutter boundary means tip displacement maintains its amplitude, it will be neither increasing nor decreasing. The region above flutter boundary has been found as unstable and region below flutter boundary was found to be stable.
Computational test has been carried out for fluid structure interaction between an elastic body and laminar incompressible flow by Turek and Hron (2015). They used a configuration consisting of incompressible laminar channel flow around an elastic object which leads to self-induced oscillation in the structure. The solid body with elastic part was submerged in channel flow which results in self-induced oscillation and deformation in body. They provide many displacement Time graph at different working condition and along different direction.
Coupled fluid structure method was used by Yun and Hui (2011) to analyse the flutter characteristics of vibration in turbomachinery blade. An aeroelastic model of blade vibration was developed to solve the three-dimensional RANS equations and to evaluate aerodynamic forces on the blade. The equation of fluid dynamics and structure dynamics was integrated for simulation. Rotor blade was seen to be stable at peak efficiency and at stall with 100 percent rotational speed in flutter analysis of blade. They concluded that coupled fluid-structure method was capable in predicting the blade stability and also in computing the magniyude of amplitude and frequency.
Sangeetha et. al (2015)explains the Fluid-Structure Interaction on AGARD 445.6 wing at Transonic Speeds. Since extensive research has been done in the field of aero- elasticity using this model, this configuration was chosen. The main objective of this paper was to study the fluid structure interaction over the wing of aircraft and determine the aero elastic properties through modeling as well as analyzing the AGARD 445.6 wing structure using CATIA V5 to generate the solid model and the stress analysis was done using ANSYS-FLUENT.
Schuster et al (1990) analyzed the aero elastic static effect on fighter aircraft by using 3-dimensional Navier- Stokesalgoritham. They developed and tested an aero elastic analysis method for extreme flight conditions for fighter aircraft, which is operating at flight conditions where shock, boundary layer separation, vortices and even high unsteady flow might be present. They found very encouraging result when compared their results with static tunnel data on an aero elastically tailored wing and fuselage configuration.
-
RESEARCH METHODOLOGY
Design modeler OF ANSYS are used to create the geometries models. Thesurface and volume mesh of fluid domain are formed using ANSYS Fluent and the finite element mesh is created by ANSYS Meshing. The simulation setup includes essential steps such as assigning the material properties, boundary conditions and numerical schemes for the two different models. At the end of the simulation setup, the fluid model consists of mediums air where the wing is placed
inside the fluid domain such that the flow passes the plate within desired time period, whereas the structural model is a simple plate member with one ends fixed in position. Figure 01 represents location of wing inside the fluid domain, where fluid is taken as air. Meshing over the wing has been carried out in CFD mesh which is shown in figure 02. Second order implicit scheme was adopted for the analysis in FLUENT while the model was taken as K-epsilon model.
Figure 01: Wing inside a fluid domain
Figure 02: Meshing over the wing
-
RESULTS AND DISCUSSION
-
Total deformation contour, equivalent stress contour, equivalent elastic strain contour, displacement versus time plot and stress versus strain plot are shown in this section, which is obtained by the post processing in ANSYS fluent. Figure 03 shows the displacement variation and figure 04 showing the stress developed and its variation along the span of the wing. Figure 05 represents the equivalent elastic strain contour and showing maximum strain near the root at mid chord of the wing. This location is same for maximum
equivalent stress also. Figure 06 represents transient behaviour of displacement for the time period of 1.25 sec and it becomes steady for the remaining time period of flow.
Figure 03: Total deformation contour
Figure 04: Equivalent stress contour
Figure 05: Equivalent elastic strain contour
Figure 06: Displacement VS Time Curve
Figure 07: STRESS VS STRAIN PLOT
CONCLUSION:
Conclusion have been made on the basis of the results obtained by the post processing of CFD after the flow past over the wing for 10s. Total deformation contour in Fig. 3 shows the maximum deformation at the tip of the wing, which is around 2.5 mm. Displacement of structure, reduces from tip to root and it went to almost zero at the root as we expected. Fig. 4 shows the least value of equivalent shear stress near the leading edge, trailing edge and tip of the wing. Transient condition of displacement during the time interval 0 sec to 1.5sec has been observed and corresponding magnitude of equivalent displacement is 2.5 mm. Stress strain curve shows the linear relationship between them.
REFRENCES:
-
T. Sai Kiran Goud, Sai Kumar A, Dr. S. Srinivasa Prasad (2014), IJEIT, Analysis of Fluid-Structure Interaction on an Aircraft Wing, Vol. 3.
-
Jian Tang, Satish Chimakurthi, Rafael Palacios, Carlos E. S. Cesnik, Wei Shyy (2008), AIAA, Computational Fluid-Structure Interaction of a Deformable Flapping Wing for Micro Air Vehicle Applications, Vol. 46.
-
Chowla Sangeetha, Mr. Veeranjaneyulu, Dr. MSN Guptha (2015), IJETA, Fluid Structure Interaction on AGARD 445.6 Wing at Transonic Speeds, Vol. 2, Issue 4.
-
David M. Schuster, Joseph Vadyak, Essam Atta (1990),Journal of Aircraft, Static Aeroelastic Analysis of Fighter Aircraft Using a Three-Dimensional Navier-Stokes Algorithm, Vol. 27, Issue 9.
-
Seok-Ho Son, Byung-Lyul Choi, Won-JinJin, Yung-Gyo Lee, Cheol-Wan Kim, Dong-Hoon Choi (2016), IJASS, Wing Design Optimization for a Long Endurance UAV Using FSI Analysis and the Kriging Method, Vol. 17, Issue 3.
-
Hannes Schmuvker, Felix Flemming, Stuart Coulson (2010),IJFMS, Two Way Coupled Fluid Structure Interaction Simulation of a Propeller Turbine, Vol. 3, Issue 4.
-
T. Liaghat, F. Guibault, L. Allenbach, B. Nennemann (2014), IMECE , Two Way Fluid Structure Coupling in Vibration and Damping Analysis of an Oscillating Hydrofoil,Vol. 3.
-
F. Liu, J. Cai, Y. Zhu (2001), Journal of aircraft, Calculation of Wing Flutter by a Coupled Fluid Structure Interaction Method, Vol. 38, No. 2.
-
Zheng Yun, Yang Hui (2011), Chinese journal of aeronautics, Coupled Fluid-Structure Flutter Analysis of a Transonic Fan, Vol. 24.
-
Jaroslav Hron, Stefan Turek(2015), Institute of Applied Mathematics and Numerics, University of Dortmund, Germany.A Monolithic FEM/Multigrid Solver for an ALEFormulation of Fluid- Structure Interaction With Applications in Biomechanics.