
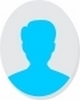
- Open Access
- Authors : R. M. Patil , M. V. Kavade
- Paper ID : IJERTV12IS020033
- Volume & Issue : Volume 12, Issue 02 (February 2023)
- Published (First Online): 21-02-2023
- ISSN (Online) : 2278-0181
- Publisher Name : IJERT
- License:
This work is licensed under a Creative Commons Attribution 4.0 International License
Finite Element Analysis of Wheel Bracket Used in Pachat Kutti Machine
Mr. R.M.Patil, Prof. M.V.Kavade Mechanical Engineering Deptartment Rajarambapu Institute of Technology Sakharale, Islampur, India.
Abstract: – A wheel bracket assembly used for wheel mounting, the most critical region for fatigue damage and failures are reported at the weld joint. This study presents a methodology in three dimensional Finite Element Model to calculate Equivalent Stress Intensity at the weld region. Three Dimensional model was created using CATIA while it was used in ANSYS to perform post processing analysis for obtaining expected solution. The results were obtained through non linear static analysis in terms of total deformation, equivalent stress on wheel bracket. LEFM Simulation uses a three dimensional Finite Element Fracture Analysis method, based on a static Non-Linear Structural analysis, in conjunction with global local technique in ANSYS within the local model. This study assumes that a flaw exist in weld due to welding process, material in-homogeneity, air voids, slugs or impurities in weld, improper surface machining and many more.
Keywords: Wheel bracket, Deformation, Equivalent Stress Intensity, Flaw
-
INTRODUCTION THEORY OF WHEEL BRACKET:
Thrash Shredder (Pachat Kutti machine) is a technology
used in agriculture, attached with a tractor with the help of 3 point linkage and powered through the drive shaft, used for chopping the dry leaves and crop residue on the fields into small pieces.
Leaf Shredder works on vacuum principal and Cutter bar assembly. The vacuum drum sucks the dry leaves from the field & feeds them in to Cutter bar assembly, where the leaves are cut in to small pieces & spread back on the ground.
The Organic residue cut in to small pieces by Thrash Shredder; gets converted in to organic manure there by increasing the fertility of the soil.
Since they are not covered by standards or manufacturer's published information, and require custom engineering. The cost of a catastrophic failure in this power range can have grave consequences on product life and on the profit and loss statement.
Wheel bracket connected to the chassis. Two wheel brackets shares the entire weight of machine. Wheels are attached to the wheel brackets. Grade 2 steel material is used to manufacture the wheel bracket. Two side plates are welded with top plate and shaft is located at the top to connect with the chassis. Two support plates at front and back are welded to support the shaft.
Manufacturers use the following criteria:
-
types of stresses those are important.
-
fatigue stress range criteria.
-
allowable stress limits in welded and non-welded members.
-
allowable load limits on the wheel bracket components.
-
material surface finish criteria in critically stressed areas.
-
materials of construction and their limitations.
-
fabrication techniques, constructed tolerances and tolerance controls.
-
-
OBJECTIVE
In wheel bracket, weld joint which is most probable part to fail against fatigue. Hence it needs to find out the stresses in various regions by nonlinear static analysis of the wheel bracket.
The objective is,
Non-linear Static Structural Analysis:-
To carry out non-linear static analysis of the wheel bracket assembly using ANSYS. This is done to find out safe value of resultant displacement and Von Misses stresses. A special attention is required to get convergence of non-linear system.
-
NON-LINEAR STATIC STRUCTURAL ANALYSIS OF A WHEEL BRACKET
Mathematically, the finite element method (FEM) is used for finding approximate solution of partial differential equations (PDE) as well as of integral equations. The solution approach is based either on eliminating the differential equation completely (steady state problems), or rendering the PDE into an equivalent ordinary differential equation, which is then solved using standard techniques such as finite differences, etc.
In solving partial differential equations, the primary challenge is to create an equation which approximates the equation to be studied, but which is numerically stable, meaning that errors in the input data and intermediate calculations do not accumulate and cause the resulting output to be meaningless. The Finite Element Method is a good choice for solving partial differential equations over complex domains or when the desired precision varies over the entire domain.
To perform an accurate analysis a structural engineer must determine such information as structural loads, geometry, support conditions, and materials properties. The results of such an analysis typically include stresses and displacements.
-
PERFORMING A STATIC ANALYSIS Following are the steps in brief to perform the analysis:
-
Build Geometry
-
Define Material Properties
-
Generate Mesh
-
Apply Loads
-
Obtain Solution
-
Present the Results
Yield strength N/mm2
460
Poissons ratio
0.3
Yonugs modulus N/mm2
2×105
MATERIAL PROPERTIES TABLE 1:MATERIAL PROPERTIES OF STEEL MATERIAL
-
-
GEOMETRY OF WHEEL BRACKET
SOLID MODEL DETAILS
This creates a hex-dominant mesh that consists of hexahedral elements, prism elements and tetrahedral elements as shown in Fig.2. The hexahedral elements and prism elements yield more accurate solution than tetrahedral elements in non-linear finite element analysis.
Fig. 2: Three types of elements included in the hex-dominant mesh
Fig. 3 shows the FEM model of the existing design. The force of 8340 N is applied on top of the shaft. This force is produced by Thrust. There is also self weight (g). The material used for FE Analysis is Non Linear.
-
BOUNDARY CONDITIONS
Fig.3 Boundary conditions
The FEM Model having boundary conditions as shown in fig.
-
MESHING
Fig. 1 – 3D model of wheel bracket
-
-
ANALYSIS OF WHEEL BRACKET
Finite element analysis (FEA) is one of the most popular engineering analysis methods for Non linear problems. FEA requires a finite element mesh as a geometric input. This mesh can be generated directly from a solid model for the detailed part model designed in a three-dimensional (3D) using CATIA (Fig.1). The wheel bracket is made of up Grade 2 Steel material. For wheel bracket part, extracted and meshed using Hex Dominant Quadrilateral and Triangular elements.
Hex dominant quadrilateral element creates a high- quality hex-dominant mesh of an arbitrary 3D geometric domain. It has the benefits like controlling the directionality of the output hex dominant mesh, and avoiding ill-shaped elements induced by nodes located too closely to each other.
Fig. 4 Mesh model of wheel bracket
The model of wheel bracket as shown in Fig. 1 was designed in CATIA and later loaded in to ANSYS to perform non linear static structural analysis. The meshing was been done for the wheel bracket.
MESHING OF PARTS
The process for generating a mesh of nodes and elements consists of three general steps:
-
Set the element attributes.
-
Set mesh controls.
-
Meshing the model.
It is not always necessary to set mesh controls because the default mesh controls are appropriate for any models. Alternatively, it can use the Smart Size feature to produce a better quality free mesh.
MESHED COMPONENTS TABLE 2: ELEMENT COUNT FOR MESHED COMPONENTS.
Result table is prepared with the current design criteria for static strength and fatigue strength.
Static strength criteria = 0.7 x Syt
Static strength criteria (for weld) = 0.6 x Syt
A fatigue strength criterion is given for life of 1 E+06 cycles with 97% confidence level.
TABLE 3: NON-LINEAR STATIC STRUCTURAL ANALYSIS RESULT
TABLE
Component |
Element type |
Node Count |
Element Count |
Wheel Bracket |
Hex dominant quadrilateral element |
10188 |
5357 |
Component Name |
Von- Mises Stress (MPa) |
Allowable Stress (MPa) |
Factor of Safety |
Remark |
||
Static Criteria |
Fatigue Criteria |
Static |
Fatigue |
|||
Shaft |
35.05 |
322 |
315 |
9.18 |
8.98 |
Safe |
Wheel Bracket Top Plate |
35.05 |
322 |
315 |
9.18 |
8.98 |
Safe |
Weld |
26.31 |
210 |
55 |
7.98 |
2.09 |
Safe |
Wheel Bracket Back Support Plate |
35.05 |
322 |
315 |
9.18 |
8.98 |
Safe |
Wheel Bracket Front Support Plate |
43.49 |
322 |
315 |
7.35 |
7.19 |
Safe |
Wheel Bracket Side Plate |
52.53 |
322 |
315 |
6.13 |
5.98 |
Safe |
-
DEFORMATION PLOT
Following figures are the Total Deformation Plots for the Wheel Bracket Assembly.
Fig.5 Total deformation of wheel bracket
-
EQUIVALENT (VON-MISSES) STRESS PLOT
Fig.6 Equivalent stress of wheel bracket
-
RESULTS TABLE
Performing the non linear static structural analysis for wheel bracket following results was obtained.
-
Minimum Von-mises stress = 0.08598 Mpa
-
Maximum Von-mises stress = 78.761 Mpa
-
Total Deformation = 0.25661 mm
CONCLUSION
-
Static nonlinear analysis was carried out and maximum equivalent stress is 78.761 Mpa which was less than the yield strength of a given material and for applied load, hence the design is safe.
-
From the structural analysis, it is found that least factor of safety is 2.09 existsin the weld part as shown in Table 3.
-
There are many limitations to perform experimental analysis like cost of an assembly, cost of experimental setup, time required for testing and hence overall testing cost required is very high. Hence FEA analysis was done which is less expensive and more accurate.
REFERENCES
[1] Umesh S. Ghorpade, D. S. Chavan, Vinaay Patil & Mahendra Gaikwad, Finite element analysis and natural frequency optimization of engine bracket, International Journal of Mechanical and Industrial Engineering (IJMIE) ISSN No.22316477, Volume-3, Issue-1, July 2013. [2] Soji Yamakawa and Kenji Shimada,2003, Fully-automated hex- dominant mesh generation with directionality control via packing rectangular solid cells, Carnegie Mellon University, Pittsburgh, U.S.A. [3] Mr. Vinod M. Bansode, Mr. Ramesh B. Mali, Mr. Dattatraya P. Mali, Mr. Yogesh C. Jadhav, Non-linear static structural analysis of a butt weld joint in a drum pulley assembly, Journal of Emerging Technologies and Innovative Research (JETIR) (ISSN-2349-5162), Volume 6, Issue4, April 2019, [4] Rahul S Kadolkar, Anand C Mattikalli, Finite element analysis of engine mounting bracket, International Research Journal ofEngineering and Technology (IRJET), e-ISSN: 23950056, Volume: 03 Issue: 09, Sep -2016
[5] G. Ashokkumar, M. UmaMahesh, S. Madhu Sudhan, T.CHOLAI RAJ, Design and analysis of wheel rim by using Catia & Ansys, International Research Journal of Engineering and Technology (IRJET), e-ISSN: 2395 0056, p-ISSN: 2395-0072, Volume: 03,Dec –2016