
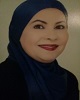
- Open Access
- Authors : Beya Ouertani , Belguecem Tiss , Mohamed Ben Rabeh , Wissem Cheikhrouhou-Koubaa, Hatem Ezzaouia
- Paper ID : IJERTV9IS050251
- Volume & Issue : Volume 09, Issue 05 (May 2020)
- Published (First Online): 13-05-2020
- ISSN (Online) : 2278-0181
- Publisher Name : IJERT
- License:
This work is licensed under a Creative Commons Attribution 4.0 International License
Fe0.986Ru0.014S2 Thin Films, Having Desired Properties for Photovoltaic Application, Synthesized by Spray Pyrolysis Technique
Beya Ouertani(a,b,*), Belguecem Tiss(c), Mohamed Ben Rabeh(d), Wissem Cheikhrouhou-Koubaa(e), Hatem Ezzaouia(a)
a Semi conductor and Advanced Technology Nanostructured Laboratory, Research and Technology Center on Energy, Borj-Cedria Science and Technology Park, BP, 95, 2050 Hammam-Lif, Tunisia.
b University of Carthage, Higher Institute of Environmental Sciences and Technologies of Borj Cedria, Borj-Cedria Science and Technology Park, Tunisia.
c University of Gabes, Faculty of Sciences in Gabes, Laboratory of Physics of Materials and Nanomaterials Applied at Environment, 6072, Gabes, Tunisia.
d Université de Tunis El Manar, Ecole Nationale d'Ingénieurs de Tunis, Laboratoire de Photovoltaïques et Matériaux Semi-conducteurs, BP 37 Le Bélvédère 1002, Tunis, Tunisia.
e Laboratory of Technologies for Smarts Systems, Numeric Research Center, Sfax Technopark, BP 275, 3021, Sakiet-ezzit, Tunisia
Abstract: – A good choice of the ruthenium doping percentage has given high-quality Fe0.986Ru0.014S2 thin films having desired properties for several applications, such as photovoltaic. These layers have been grown by a simple and non toxic technique: spray pyrolysis. In a first step, for an adequate molar ratio of (FeCl3.6H2O : RuCl3.3H2O), amorphous Ru-doped iron oxide thin films were deposited on glass substrate pre-heated at 350°C. Then, a heat treatment at 450°C under sulfur atmosphere (~10-4 torr) in sealed-tube transformed the as obtained films into Fe0.986Ru0.014S2 films. XRD analysis confirmed the FeS2 phase. The estimated compositions were tested by the EDX analysis. Surface morphology is studied by SEM and AFM and the obtained images showed an inhomogeneous granular structure and a rough surface. However, the granular size varies from 150 nm to 300 nm. The optical measurements showed a high absorption coefficient ( > 3.5×104 cm-1 for wave lengths lower than 800 nm). A direct band gad corresponding to a photon energy of 1.55 eV was obtained after plotting (h)2 versus the photon energy (h); which is an estimated value for photovoltaic application. The electron mobility in Fe0.986Ru0.014S2 films has been obtained from Hall Effect measurement where an initial current of 1A and a magnetic field, B = 0.554T, are applied. Our layers show n-type conduction. Electrical measurements (bulk concentration
=1.0209×10+19 cm-3, Sheet Concentration=2.766510+15 cm-2) encourage their use as good low cost materials for solar cells. Indeed, the carrier mobility was measured of about 0.21215 cm2/(V.s), the resistivity was of 2.8821 .cm, and the conductivity was of 0.34696 – 1.cm-1. The bulk concentration was of 1.0209×1019cm-3.
Keywords: Growth, characterization, Electrical, optical, low cost materials, spray pyrolysis, desired band gap.
-
INTRODUCTION:
Nowadays, researchers are of great interest to innovate new low cost materials for solar cells [1-14]. Several research works focused on the Pyrite films fabrication because of their low cost, but unconvincing results were obtained. However, for their use in this area, it needs to improve their properties (optical and electrical). Thus, researchers thought about their doping in the aim to improve their optical and electrical properties to make it more effective as a photovoltaic material. Different dopants were chosen As, Ni, Co, Cu, Al, Ni, Zn, Os, Ru, Mg, Ba, etc [6, 15-24].
Knowing that, the ruthenium has been treated as a good candidate for doping FeS2 thin films in the aim to improve their properties since they were chosen among the low cost materials for solar cells. Indeed, in a previous work [19], a good study was done concerning the Ru-alloyed FeS2 thin films for solar cells application wherein estimated optical results were obtained for the ratio RuCl3.3H2O:FeCl3.6H2O of about 1.56% (high absorbance and a direct band gap corresponding to photon energy of
1.48 eV). In order to fabricate Ru-doped FeS2 films having good properties for solar cells application, which means a good choice of the ratio: RuCl3.3H2O:FeCl3.6H2O; we tried with different ratios close to 1.56% [19]. Hence, a well chosen ratio: RuCl3.3H2O:FeCl3.6H2O of 1.46% allowed us to fabricate Fe0.986Ru0.014S2 thin films having desired optical and electrical properties for solar cells application.
-
GROWTH OF THE FE0.98845RU0.01155S2 THIN FILMS:
Using the simple technique: spray pyrolysis, and non toxic and non cost precursors, amorphous Ru-doped iron oxide films were obtained by spraying FeCl3·6H2O (0.03 M)-based aqueous solution onto pre-heated glass substrates (at 350°C) during 10 min; on which was sprayed, immediately, another layer of an aqueous solution of RuCl3·3H2O (density=3.11 g/mL at 25 °C), during 1 min with the chosen molar ratio: RuCl3·3H2O:FeCl3·6H2O=x:1x (x 0.0146).
The as obtained amorphous Ru-doped iron oxide films were transformed into Fe(1-x)RuxS2 films after heat treatment under sulfur atmosphere (~10-4 torr) at Tsulfuration = 450°C for 3h. Dark films with good adherence to the substrate were obtained. Therefore, the prepared films are treated by XRD to identify the obtained phase, and then their optical properties are obtained after reflectivity and transmittance measurements. Electrical properties are obtained by Hall Effect technique. The surface morphology is investigated by SEM and AFM.
-
EXPERIMENTAL DETAILS:
3.1 Structural properties a-X-ray diffraction
The adequate molar ratio (33 : 65 : 2) of (FeCl3.6H2O : S : RuCl3.3H2O) was used to synthesize Ru-doped FeS2 material. The obtained phase was investigated by powder X-ray diffraction (PXRD) with a Bruker D8 Advance diffractometer equipped with a lynxeye detector. The dichromatic copper radiation (CuK1/2) was used by the 2 scan in the 2 range of 5-70°. Full diffraction power of 40mA/40kV with 0.018° step and 2s time-step were used to record the diffraction pattern represented in Fig.1. The search-match phase identification procedure was applied using the Powder Diffraction File (PDF) database and the PanAlytical XpertPro Highscore software. Two phases were identified in the diffraction pattern: FeS2 (JCPDS card n°: 00-024- 0076) and Fe2O3. The sulfuration of the pre-deposited Ru-doped iron oxide layers under vacuum (~10-4 torr) takes 3h at 450°C.
0.986 0.014 2
0.986 0.014 2
Fe O
Fe O
(3 1 1)
(3 1 1)
2 3
2 3
(4 0 0)
(4 0 0)
1600
Fe Ru S
Fe Ru S
C P S
C P S
( 2 0 0 )
( 2 0 0 )
( 2 1 0 )
( 2 1 0 )
Fe2O3
Fe2O3
( 3 1 1 )
( 3 1 1 )
0
( 0 0 – 0 2 4 – 0 0 7 6 ) P y r i t e
( 0 0 – 0 2 4 – 0 0 7 6 ) P y r i t e
( 1 1 1 )
( 1 1 1 )
( 2 1 1 )
( 2 1 1 )
( 2 2 0 )
( 2 2 0 )
( 2 2 2 )
( 2 2 2 )
( 2 3 0 )
( 2 3 0 )
( 3 2 1 )
( 3 2 1 )
01 0 2 0 3 0 4 0 5 0 6 0 7 0
2 ( ° )
Fig.1 : XRD spectrum of the Ru-doped FeS2 films obtained after heat treatment under sulfur atmosphere (~10-4 torr) at Tsulfuration = 450°C for 3h of the amorphous Ru-doped iron oxide films that had been obtained according to the molar ratio: RuCl3·3H2O:FeCl3·6H2O=x:1x (x 0.0146).
Compared to the initial pyrite peak position, the observed shift towards the low 2 values of the obtained thin film proofs the ruthenium doping of the pyrite material and the synthesis of Ru-doped FeS2. Since the ruhenium atomic radius is larger than that of the iron, replacing Fe by Ru will increase the cubic cell parameter explaining the observed shift of the Bragg peaks position. The refined cubic cell parameter of the Ru-doped FeS2 is a = 5.4180 Ã….
b-Energy Dispersive X-ray Spectroscopy (EDX or EDS) analysis:
To determine the compositions of the Ru-doped FeS2 stacked layers, EDS analysis were carried out using a Thermo Scientific UltraDry Detector. The measured values are summarized in Table.1.
Table.1: EDS analysis of the Ru-doped FeS2 films obtained after heat treatment under sulfur atmosphere (~10-4 torr) at Tsulfuration
= 450°C for 3h of the amorphous Ru-doped iron oxide films pre-deposited by spray pyrolysis according to the molar ratio: RuCl3·3H2O:FeCl3·6H2O=x:1x (x 0.0146).
Element
Net Counts
Weight %
Atom %
(Fe/S %)
(Ru/S %)
S
42682
33.27
26.25
~0.4396 < 0.5
~0.0293
Fe
6104
25.49
11.54
Ru
1655
3.08
0.77
Since the ratio
Fe
S
0.5 , the pyrite phase is stoichiometric represented by FeS2. In this work, the observed ratio is slightly
Fe
less than 0.5 (
0.44 ) in the obtained thin films. Using this ratio, the x value in the proposed formula (Fe
Ru S ) can
S
be calculated from :
Ru 2x S
0.77
26.25
2x x = 0.01465
(1-x) x 2
However the new obtained Ru-doped FeS2 phase formula is Fe0.986Ru0.014S2.
-
Surface morphology Scanning-electron-microscopy
The surface morphology of the Fe0.986Ru0.014S2 films is visualized by a Thermo Scientific Q250 SEM. Fig.2 shows SEM micrographs surface views at different magnifications of Ru-alloyed pyrite films annealed at 450 °C under vacuum (104 torr) for 3h.
Fig.2: SEM views at different magnifications of the Fe0.986Ru0.014S2 films obtained after sulfuration under vacuum (10-4torr) at 450°C for 3h of amorphous Ru- doped FeS2 films deposited on pre-heated glass substrates (at 350°C) for 10 min according to the adequate molar ratio (33 : 65 : 2) of (FeCl3.6H2O : S : RuCl3.3H2O).
Porous surface and inhomogeneous granular structure were shown. The grain size could reach 300 nm. These properties encourage more their application as solar cells.
Atomic-Force-Microscopy
To further investigate the morphology of the obtained films (Fe0.986Ru0.014S2) a characterization by AFM (Dimension 3100 controller NanoscopeIIIa, Digital Instruments, Veeco, Metrology Group) in contact mode at ambient temperature was done. Root mean square (rms) surface roughness value was determined on an area of 2m x 2m for the studied films. The rms was calculated using the roughness analyses software provided by the instrument manufacturer. Fig. 3 shows AFM surface morphology of the Fe0.986Ru0.014S2 film. A granular structure was observed confirming the SEM observation (Fig. 2).
Fig.3 : AFM surface images of the Fe0.986Ru0.014S2 films obtained after sulfuration under vacuum (10-4torr) at 450°C for 3h of amorphous Ru-doped FeS2 films deposited on pre-heated glass substrates (at 350°C) for 10 min according to the adequate molar ratio (33 : 65 : 2) of (FeCl3.6H2O : S : RuCl3.3H2O).
The AFM images of the obtained films show porous and rough surface (Fig. 3), a strong roughness was observed. AFM images (Fig. 3) are in agreement with SEM views, when irregular spherical crystallites and a large grain size dimensions were observed.
-
Optical Properties
Optical absorption spectra of the as-prepared non-doped and Ru-doped pyrite thin films were recorded using a SHIMADZU 3100S spectrophotometer. Fig.4 depicts the optical absorption spectra versus photon energy (h). The transmission and reflectivity variations versus the wavelength (400 nm1800nm) of the obtained films are shown in Fig.4 (a,b).
20
7
6
15
Transmission(%)
Transmission(%)
Reflectivity (%)
Reflectivity (%)
5
4 10
3
2 5
1
400 600 800 1000 1200 1400 1600 1800
nm)
7
(a)
0 400 600 800 1000 1200 1400 1600 180
(nm)
20
6
15
Transmission (%)
Transmission (%)
Reflectivité(%)
Reflectivité(%)
5
4
10
3
2
5
1
4000 600 800 1000 1200 1400 1600 1800 0
(nm) 400 600 800 1000 1200 1400 1600 1800
(nm)
8×104
7×104
(cm-1)
(cm-1)
6×104
5×104
4×104
3×104
(b)
(.h)2 (cm-1.eV)2
(.h)2 (cm-1.eV)2
(.h)2 (cm-1.eV)2
(.h)2 (cm-1.eV)2
Eg ~ 1.55 eV
0.00E+000 0.5 1.0 1.5 p.0(eV) 2.5 3.0 3.5 4.0 4.5
(.h)1/2 (cm-1.eV)1/2
(.h)1/2 (cm-1.eV)1/2
2×104
0.5 1.0 1.5 2.0 2.5 3.0 3.5 4.0 4.5
h (eV)
0 0.5 1.0 1.5 2.0 2.5 3.0 3.5 4.0 4.5
h (eV)
0 0.5 1.0 1.5 2.0 2.5 3.0 3.5 4.0 4.5
h (eV)
(c) (d) (e)
Fig.4: Optical absorption spectra of the Fe0.986Ru0.014S2 (a,c,d, and e), and FeS2 thin films (b), obtained after sulfuration under vacuum (10- 4 torr) at 450°C for 3h of simultaneously amorphous Ru-doped iron oxide, and iron oxide films pre-deposited on heated glass substrates (at 350°C) by spray pyrolysis technique.
It appears that the transmission and reflectivity coefficients measurements of the Fe0.986Ru0.014S2 films (Fig.4(a)) have shown a remarkable decrease comparing to those of the non doped FeS2 films (Fig.4 (b)). However, the obtained Fe0.986Ru0.014S2 films showed a high absorption coefficient ( >2x104cm-1 for < 1900nm) (Fig.4(c)). Plots of (h)n/2 versus the photon energy h, with n=1 and n=4 for these obtained layers are given simultaneously in Fig.4(d) and Fig.4 (e). Three transitions are depicted: an indirect one corresponding to photon energy of about 2.8 eV and two direct ones corresponding to the energies 1.55 eV and 3.72 eV. Thus, the lower energy is attributed to a direct band gap of the Fe0.986Ru0.014S2 phase comparing to the values range of the Fe(1-x)RuxS2 band gaps obtained previously [13]. The two other transitions, direct and indirect, corresponding to the energies 2.8 eV and 3.72 eV could be attributed to the iron oxide phases.
-
Electrical transport properties
To assess the electrical quality of the Ru-doped FeS2 thin films, especially of the Fe0.986Ru0.014S2 ones, Hall mobility measurements were performed and analyzed to extract carrier mobility and carrier concentration. The obtained carrier density
-
and mobility (n) of an n-type semiconductor can be determined from the measured Hall coefficient (RH(B)) and the resistivity ((B)) using the relations:
n rH q.RH B
(1)
and
1
(2)
n n.q. B
Where q is the electronic charge, B is the applied magnetic field, and rH is the Hall factor. In fact, the Hall coefficient RH is given by the following equation:
R VH .t 1
(3)
H IB ne
Recall that when electrons are the charge carriers, RH is negative and when holes are the charge carriers, RH is positive.
In the present work the electron mobility in the as obtained Fe0.98535Ru0.01465S2 films as been obtained from Hall Effect measurement where an initial current of 1A and a magnetic field, B = 0.554T are applied. Our layers show n-type conduction. The electrical measurements such as: the bulk concentration that is about 1.0209×10+19 cm-3, and the sheet concentration that is of about 2.766510+15 cm-2, encourage their use as good low cost materials for solar cells. Indeed, the carrier mobility was measured of about 0.21215 cm2/(V.s), the resistivity was of 2.8821 .cm, and the conductivity was of 0.34696 -1.cm-1.
-
-
CONCLUSION:
An adequate molar ratio was chosen to fabricate Fe0.986Ru0.014S2 thin films having good properties for solar cells application. The morphology study showed a granular structure with grain sizes reaching 300 nm, which means that our layers present a good porosity. A strong roughness was observed. The optical properties of these layers showed a high absorption coefficient (
>2x104cm-1 for < 1900nm) and a direct band gap corresponding to photon energy of 1.55 eV; which is considered as a desired band gap value for solar cells application. In addition, the obtained electrical properties of the Fe0.986Ru0.014S2 layers were optimal for the intended application. Thus, one can say that the obtained Fe0.986Ru0.014S2 thin layers could be used as a material for low cost solar cells application. It could be considered as an interesting plus in the field of low cost materials for solar cells application.
ACKNEWLEGMENTS :
We would like to thank deeply Pr. Habib Boughzala, « Laboratoire de Matériaux et Cristallochimie, Faculté des Sciences de Tunis (F.S.T), Université de Tunis El Manar » for his scientific helps and his support. Our deep thanks go to all the staff of the
« Laboratoire de Photovoltaïque, Centre de Recherches et des Technologies de lÉnergie, Technopole de Borj-Cédria » and specially the Director, Pr. Mongi Bouaicha, for their support. Our deep gratitude and regard to Mr. Taoufik Bouaanane, technician in this same laboratory for his precious electrical measurements. We would like to take this opportunity to express our deep gratitude and regard to Pr. Kamel Khirouni and Pr. Noureddine Bouguila, Laboratory of Physics of Materials and Nanomaterials Applied at Environment-Faculty of Sciences in Gabes, for their support.
REFERENCES:
-
Feng Zhao, YanLiang, Jeong BaeLee, and Seung J.Hwang, Materials Science and Engineering: B, Volume 248, (September 2019), 114404.
-
Cheng Wang, Junsen Zhang, Liangxing Jiang, Li Gong, Haipeng Xie, Yongli Gao, Haiping He, Zhishan Fang, Jincheng Fan, Zisheng Chao, Journal of Alloys and Compounds, Volume 817, (15 March 2020), 152768.
-
Khagendra P. Bhandari, Xinxuan Tan, Peymon Zereshki, Fadhil K. Alfadhili, Adam B. Phillips, Prakash Koirala, Michael J. Heben, Robert W. Collins, and Randy J. Ellingson, Solar Energy Materials and Solar Cells, Volume 163, (April 2017), Pages 277-284.
-
Beau J. Richardson, Leize Zhu, and Qiuming Yu, Solar Energy Materials and Solar Cells, Volume 116, (September 2013), Pages 252-261.
-
Ravi P. Srivastava, and Sarang Ingole, Materials Science in Semiconductor Processing, Volume 106, (February 2020), Article 104775.
-
Tian-Lun Liu, and Jian-Min Zhang, Materials Chemistry and Physics, Volume 2441, (April 2020),Article 122742.
-
B. Ouertani, J. Ouerfelli, M. Saadoun, M. Zribi, M.Ben Rabha, B. Bessaïs, H. Ezzaouia, Thin Solid Films 511 512 (2006) 457 462.
-
B. Ouertani, J. Ouerfelli, M. Saadoun, B. Bessaïs, H. Ezzaouia, J.C. Bernède, Materials Characterization 54 (2005) 431 437.
-
A. Ennaoui, S. Fiechter, C. Pettenkofer, N. Alonsovance, K. Buker, M. Bronold, et al., Sol. Energy Mater. Sol. Cells 29 (4) (1993) 289370.
-
B. Ouertani, J. Ouerfelli, M. Saadoun, B. Bessaïs, H. Ezzaouia, J.C. Bernède, Solar Energy Materials & Solar Cells 87 (2005) 501511.
-
B. Ouertani, J. Ouerfelli, M. Saadoun, B. Bessaïs, M. Hajji, M. Kanzari, H. Ezzaouiaa, N. Hamdadoud, J.C. Bernède, Materials Letters 59 (2005) 734 739.
-
R. Dasbach, G. Willeke, O. Blenk, MRS Bull. 18 (10) (1993) 5660.
-
A. Ennaoui, S. Fiechter, W. Jaegermann, H. Tributsch, J. Electrochem. Soc. 133 (1)(1986) 91106.
-
K. Buker, N. Alnonso-Vante, H. Tributsch, J. Appl. Phys. 72 (1992) 57215728.
-
N. Alonso-Vante, G. Chatzitheodorou, S. Fiechter, N. Mgoduka, I. Poulios, H. Tributsch, Sol. Energy Mater. 18 (1988) 921. [16] R. Sun, G. Ceder, Phys. Rev. B 84 (2011) 245211245217.
-
S.W. Lehner, K.S. Savage, J.C. Ayers, J. Cryst. Growth 286 (2006) 306317.
-
I.J. Ferrer, F. Cabalerro, C. De las Heras, C. Sanchez, Solid State Commun. 89 (1994) 349352.
-
Beya Ouertani, Hatem ezzaouia, and Bertran Tess , Colloids and Surfaces A 525 (2017) 1319.
-
P. Xiao, X.-L. Fan, H. Zhang, X. Fang, L.-M. Liu, J. Alloys Compd. 629 (2015) 4348.
-
Jibo Jiang,Liying Zhu,Haotian Chen,Yaoxin Sun,Hualin Lin, and ShengHan, Journal of Alloys and Compounds,Volume 775, 15 February 2019, Pages 1293-1300
-
YangDing, PeiyuanZeng, and ZhenFang,Journal of Power Sources,Volume 450, 29 February 2020, 227688
-
Xing-HuaTian, and Jian-MinZhang, Materials Chemistry and Physics, Volume 239, 1 January 2020, 122057
-
N.Ouarab, Physica E: Low-dimensional Systems and Nanostructures,Volume 115, January 2020, 113688