
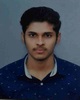
- Open Access
- Authors : Praveen Kumar V , Pranav R Joshi , Kiran Kumar D , Jayanth Y, Dr. Umesh G.L
- Paper ID : IJERTV12IS040055
- Volume & Issue : Volume 12, Issue 04 (April 2023)
- Published (First Online): 24-04-2023
- ISSN (Online) : 2278-0181
- Publisher Name : IJERT
- License:
This work is licensed under a Creative Commons Attribution 4.0 International License
Fabrication of Automatic Can Crusher
Praveen Kumar V
Department of Mechanical Engineering Bangalore Institute of Technology,Bengaluru-04,India
Kiran Kumar D
Department of Mechanical Engineering Bangalore Institute of Technology,Bengaluru-04, India
Pranav R Joshi
Department of Mechanical Engineering Bangalore Institute of Technology,.Bengaluru-04, India
Jayanth Y
Department of Mechanical Engineering Bangalore Institute of Technology ,Bengaluru-04,India
Dr. Umesh G.L
Assistant Professor Department of Mechanical Engineering
Bangalore Institute of Technology ,Bengaluru-04, India
Abstract- The main aim of this project is to fabricate a Can Crusher machine to reduce the scrap volume and use the Cans so that carrying them to the recycle site becomes easy. Now-a-days, a large number of cans are used in hotels, canteens etc. and a large volume of spaceis required for storing or dumping the used Cans. This project includes fabrication of a CanCrusher using single slider crank mechanism which will reduce the volume of cans at least 70%. This report demonstrates the necessary calculation,assembling and fabrication of themachine. Under this project work, two Can Crushers have been constructed.. The model isupgraded to an electrically operated one. Finally, a comparison between the two Can Crushers, i.e. manually operated and electrically operated, is made, regarding their efficiencies,cost of construction etc. and presented here in this report.
-
INTRODUCTION
Can Crushers are used in mechanical and allied industries which crush cans made of different materials. The Can Crusher machine is widely used in beverage industries or in scrap dealers shop to reduce the volume of the cans. Consequently , it leads to the reduction of the transportation cost. This machine is primarily used to save space and for recycling. It can be placed anywhere . In todays life most of the food items are packed in cans like Cold and hot drinks and other beverages.Commercial establishments like cafeteria and bars, have to deal with leftover cans. Storage of these cans is often a problem and these increases total volume of the trash. Therefore, using can crusher in such places proves to be advantageous.
-
LITERATURE SURVEY Elfasakhan.A, et.al. (2012) presented a new design. This Can Crusher which can crush a single can at a time consists of a hardware and software. The hardware includes mechanical structure, servomotor, light sensor, microcontroller and pneumatic system. The pneumatic system has been used instead of an electrical motor since electrical motor with the needed specification (torque and horsepower) is very expensive. The software is the maestro for operating and controlling different system components.
More.S,R, et.al. (2013) have presented a review on study of jaw plates jaw crusher which tells us that crushers are major size reduction equipment used in mechanical, metallurgical and allied industries which crushes different types of soft and hard materials. This paper provides the background of swing jaw plates of jaw Crusher and kinematics and dynamic analysis are done to improve the design.
Saif.Set.al.(2014)have proposed a paper on fully automatic Can Crusher using pneumatics and microcontroller sensor.
KhanapureL.R., et.al.(2014) have presented a paper which provide crushing action in both the strokes thus making it a dual stroke Can Crusher and provide automatic falling of crushed cans and automatic feed of new cans to be crushed so as to keep the crushing area free from human intervention thus providing safety to the operator.
Wakchaure.Cet.al.(2016)have presented a paper on design and fabrication of automatic Can Crusher using double acting cylinder for pneumatic system and ics.
From the above research papers,we have found that a number of methods are used for fabricating the Can Crusher including pneumatic system with ICs, motors etc. Pneumatic Can Crushers use automation reducing human intervention. However the use of air compressor, valves and pipelines make the equipment more expensive which is not suitable for small scale recycling plant. Further in the manually operated models of the research papers the crushed cans need to be removed manually and also new cans need to be placed every time. Therefore we have chosen this project to fabricate an auto- feed, cost effective Can Crusher where the removal of crushed cans is not manual.
-
WORKING
A combination of a number of rigid bodies assembled together in such a way that the motion of one causes constrained and predictable motion to the others is known as a mechanism. As many mechanisms can be obtained as the number of links in a kinematic chain by fixing , in turn, different links in a kinematic chain. This method of obtaining different links in a
kinematic chain is called inversion of mechanism. A mechanism is the mechanical portion of the machine that has the function of transferring motion and forces from a power source to output. The mechanisms in this project are as follows:
-
Inversion of single slider crank mechanism
-
Chain drive mechanism for power transmission.
Inversion of Single Slider Crank Mechanism:
The kinematic chain is a combination of four or more kinematic pairs, such that the relative motion between the links or elements is completely constrained. The simplest and the basic kinematic chain is a four bar chain . For a four bar chain , the sum of the shortest and longest link lengths should not be greater than the sum of the remaining two link lengths if there is to be continuous relative motion between the two links .A single slider crank chain is a modification of the basic four bar chain. It consists of one sliding pair and 3turning pairs. This type of mechanism converts rotary motion into reciprocating motion and vice versa. Links of a slider crank chain are:
1.Frame and cylinder 2.Crank 3.Connecting rod 4.Crosshead or piston
Four different mechanisms can be obtained by fixing each of the link of the single slider crank chain. In the first inversion, link 1 i.e. frame and cylinder is fixed. In the second inversion, link 2 i.e. crank is fixed. In the third and fourth of inversions link 3 i.e.connecting rod and link 4 i.e.crosshead is fixed respectively. In this project, we use first inversion.
-
Base
-
Motor
-
Crank
V. MAIN PARTS
3D MODEL
-
-
PROPOSED MODEL
-
Plummer block
-
Connecting member
-
Crusher
-
Sheet metal frame
ADVANTAGES
-
Maintenance cost is low
-
Number of part is less
-
Less floor space
-
Greater safety to the worker
-
Life span of the machine is high
DISADVANTAGES.
-
Time consuming
-
Crusher plate wear
SAFETY, CARE AND MAINTENANCE
Before starting the operation, check the following items Check the mechanism for proper operation.Check the alignment of crank drives, crushing plate and bearing in the unit. Dont insert the any material or object between the during operation of crushing. Check the lubrication of bearing drive in the unit. Handle carefully while crushing the work
FEATURES OF THIS PROJECT
-
It is compact in size.
-
It can be moved easily.
-
Low electrical power consumption.
-
It can be utilized at our Place.
-
-
CONCLUSION
After the successful fabrication of the Can Crusher, te machine was tested from which we obtained the above- mentioned observations. The cans were crushed up to the desired volume in the manually operated Crusher. Further we have seen that the Cans were crushed to a much smaller volume in the electrically operated one. The crushers have been fabricated keeping in mind about the minimum power requirement and minimum effort to the operator The manually operated Can Crusher will be suitable for small scale recycling plants while the electrically operated Can Crusher will be suitable for medium or large scale recycling plants.
-
ACKNOWLEDGEMENT
We would like to thank our Head of the Department, Dr. T V SREERAMA REDDY and our guide Dr. UMESH G. L. for their valuable advice and technical assistance.
-
REFERENCES
-
0613.
[3] Mr. Shadab Husain, Mohammad Shadab Sheikh presents paper on Can crusher machine using scotch yoke mechanism. IOSRJournal ofMechanical and Civil Engineering (IOSR-JMCE) e-ISSN: 2278- 1684, p-ISSN: 2320-334X PP 60-63. [4] Wakchaure.C , et.al . (April, 2016), Design and Fabrication of Automatic Can Crusher,Imperial Journal of Interdisciplinary Research,2(7),217-223.78 [5] M r. Ramkrushna S. More , Sunil J. Rajpal publishes an paper on study of crusher. International Journal Of Modern Engineering Research (IJMER), Vol 3, Issue.1, 2013