
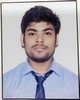
- Open Access
- Authors : Mafiz Uddin Ahmed
- Paper ID : IJERTV12IS120038
- Volume & Issue : Volume 12, Issue 12 (December 2023)
- Published (First Online): 05-01-2019
- ISSN (Online) : 2278-0181
- Publisher Name : IJERT
- License:
This work is licensed under a Creative Commons Attribution 4.0 International License
Experimental Setup of A Battery Operated Motor-Wheel Assembly
Mafiz Uddin Ahmed
Cyient Ltd. (Hyderabad)
Abstract Conventional vehicles contrarily affect the climate
because of fuel utilization and ensuing emanations of , prompting air contamination. These emanations are broadly
acknowledged as a trigger for a worldwide temperature alteration and enactment. Electric Vehicles are an Eco-Friendly Choice. Electric vehicle as compared to the conventional Internal combustion engine do not pollute the air. It results in zero emission and the surrounding air doesn't get dirtied. In an electric vehicle, motor works as a prime mover and battery pack acts an energy source. In order to safely manage the battery pack an electronic system called the Battery management system (BMS) needs to be built. A BMS is basically the brain and heart of a battery pack. It manages the temperature, state of charge, voltage protection and cell health monitoring of the battery pack.
The first part of the project deals with finding the different forces acting on the vehicle like the aerodynamic drag, rolling resistance, grading resistance and acceleration resistance. These are the forces which needs to be overcome by the motor. Thus, finding the total tractive effort of the vehicle and ultimately the power required by the motor.
In the second part of the project, the capacity of battery pack is calculated. On the basis of the torque required by the motor and the vehicle requirement, suitable capacity of cell is calculated. A collection of such cells is arranged into modules and ultimately these modules combined together to build the required capacity battery pack.
Keywords Electric Vehicles; Internal combustion engine; Motor, Battery, Battery pack
-
INTRODUCTION
-
Dynamics of vehicle
The fundamentals of vehicle design require the essential principles of physics, mainly the Newton's second law of motion. In keeping with Newton's second law the acceleration of an object is proportional to the net force exerted on that. Hence, an object accelerates when the net force functioning on it is not zero. In an exceedingly vehicle several forces act thereon and also the net or resultant force governs the motion in keeping with the Newton's second law. The force required to move the vehicle forward is delivered by the propulsion unit of the vehicle. This force of the propulsion unit helps the vehicle to beat the resisting forces because of gravity, air and tire resistance. The acceleration of the vehicle depends on:
Figure 1:Forces acting on a vehicle going uphill [1] Resistive Forces:
When a vehicle is in motion, it encounters resistive forces that tries to slow down its motion. These resistive forces are
-
Rolling resistance
-
Aerodynamic drag
-
Uphill resistance [1]
Rolling resistance:
The hysteresis within the tire material is that the reason for the rolling resistance of tires on hard surfaces.
This resistance force is given by:
= P
When a vehicle is moving up an incline, the normal force (P) is
restored by the component thats perpendicular to the paved surface. Hence, the equation will be rewritten as:
= P cos ()
where
P = Normal load acting on the centre of the rolling wheel [N]
= rolling resistance coefficient
= road angle [radians] [1]
Aerodynamic drag:
When a vehicle traveling at a travelling at a specific velocity in air, it encounters a force resisting its motion. This force is named as aerodynamic drag.
The aerodynamic drag is given as:
1
-
the power delivered by the propulsion unit
-
the conditions of the road
=
2
2
-
the vehicles aerodynamics
-
the composite mass of the vehicle
The tractive force (Ft) in the contact area between the road surface and the tires of the driven wheels moves the vehicle forward. The power plant produce the tractive force (Ft) and it is transferred to the driving wheels via the transmission and the final drive. [1]
where
= density of air [ kg/m3]
= vehicle frontal area [ m2]
= Co-efficient of Drag
= vehicle speed [ m/s] [1]
Grading resistance:
The grading resistance is given as:
= Mgsin()
where
M = mass of the vehicle [kg]
g = acceleration constant [m/s2]
= road angle [radians] [1]
Acceleration resistance:
During acceleration and braking, inertial forces also occur besides the driving resistance occurring in steady state motion. The acceleration resistance is given as:
=
where
= rotational inertia constant
M = mass of the vehicle [kg]
= vehicle speed [ m/s] [1]
Total driving resistance:
The traction force (Ft) which is required at the drive wheels is created from the driving resistance forces and is given as:
= + + + [1]
Power:
the power required (Preq):
= [1]
Dynamic equation:
The dynamic equation of motion of car along the longitudinal direction is expressed as:
=
-
The fossil-fuel vehicles contribute 60 percent of PMs (particulate matter-related atmospheric pollution), and
over 20 percent of 2.
-
In IC Engine, the linear motion of the piston needs to
be converted to rotational motion. This causes major problem for mechanical balancing.
-
Not only the internal combustion engine is not self-
starting like an induction motor. Further the power output of an Internal Combustion engine is always uneven. Many accessories are needed to resolve these issues.
-
So as to preserve a decent operating condition, CI
engine need regular maintenance (service) intervals for air filters, fuel filters replacement, spark plugs, oil change, etc.). For this reason, a vehicle with IC Engine is dearer to take care of compared with an electrical vehicle. [2]
Recent developments in vehicle industries have trended towards Electric vehicle due to the following reasons:
-
Electric vehicles have zero exhaust gas emission because of the absent of IC engine. Moreover, depending on the source of the electric energy (e.g., renewable) the overall CO2 impact of an electric vehicle is smaller compared with an IC engine vehicle.
-
In an electric vehicle, we are going to have direct
rotational motion and uniform power output with an induction motor. Many components within the IC engine may be avoided here. As a result, great response rate and better power to weight ratio comes naturally to an EV leading to superior vehicle performance.
-
Having fewer moving parts and components an
The first term on the right side is the total tractive effort and the second term is the total tractive resistance. [1]
Torque by the wheels:
=
where
= total tractive effort
= Rolling Radius [1]
Torque by the motor:
=
where
GR = Gear ratio [1]
-
-
-
Advantage of Electric Vehicle over IC Engine
A vehicle is conventionally operated using IC engine. However, use of IC engines over time can have certain negative impacts:
-
The petrol and diesel-run vehicles are hugely
inefficient as nearly 70 percent of the valuable fuel simply is wasted.
electric vehicle is simpler and cheaper to take care of. -
An electric motor has fewer sources of possible
failures because of the lesser number of moving parts as compared to an internal combustion engine. Also, due to the high torque and high-speed characteristic of the electric Vehicle, there is no need for a multi-stage gearbox, a single-step mechanical gearbox is enough for propulsion. [2]
Table 1 summarizes the basic differences between IC engines and Electric vehicle. Figure 2 represent a typical block diagram of an Electric vehicle.
Table 1: Comparison of electric vehicle with IC engine [2]
Parameter
Electric Vehicle
IC Engine
Prime mover
Motor
Engine
Energy storage
Battery Pack
Fuel tank
and exhaust
gas emission
No exhaust gas emission
Exhaust gas emission
Reliability
With less moving parts, fewer sources of possible failures
Many moving parts, can leads to possible failures
Powertrain efficiency
Overall efficiency between 75-95%
Efficiency between 18-24%
Cost of ownership
Maintenance cost is low
Maintenance cost is high
Figure 2: Block Diagram of an Electric Vehicle [7]
-
-
Development of Battery pack of an Electric vehicle
A battery back is a set of any number of (ideally) identical batteries or individual battery cells. they will be configured in an exceedingly series, parallel or a mix of both to deliver the required voltage, capacity, or power density. The term battery pack is usually employed in relevancy cordless tools, radio- controlled hobby toys, and battery electric vehicles. Components of battery packs include the individual batteries or cells, and the interconnects which supply electrical conductivity between them.
Cells:
Cells are the smallest individual electrochemical unit, and deliver a voltage that depends on the cell chemistry.
-
There are primary (single use) and secondary(rechargeable) cells
Batteries:
Batteries and battery packs are made up from groups of cells.
-
These cells can be wired together in series, in parallel, or in some combination of both.
-
Sometimes they are packaged in a single physical unit. For example, automotive 12V lead-acid batteries comprise six 2V cells in series
Figure 3: 12V lead-acid battery [3]
-
Other times, the connections are external to the cells The symbol used for cell and battery is shown below:
Figure 4: Symbols for (a) cell and (b) battery [3]
Cells connected in series:
-
When cells are connected in series, the battery voltage is the sum of the individual cell voltages
-
However, battery capacity is equal to individual cell capacity since the same electrical current passes through all of the cells (charging and discharging all cells at the same rate) [3]
Cells connected in parallel:
-
When cells are connected in parallel, the battery voltage is equal to the cells voltage.
-
However, battery capacity is the sum of the cells capacities, since the battery current is the sum of all the cell currents. [3]
Stages of Battery Pack Design
-
Stages of Battery Pack Design are:
-
Cell configuration
-
Series
-
Parallel
-
mpns theory
-
-
Structure
-
Case, cover, end plates, ties rod, cell holder, baseplate
(Mechanical)
-
Busbar, wiring harness, fuse and plugs (Electrical)
-
Cooling jackets, safety valves, thermistors (Thermal)
-
-
Safety
-
Vibration, shock abuse, crash (Mechanical)
-
Short circuit and overcharge/over discharge (Electrical)
-
Thermal runaway and thermal management (Thermal)
-
-
Control
-
Vibration control and hardware robustness (Mechanical)
-
Cell monitoring and BMS (Electrical)
-
-
Application
-
Interface (between different sub-system)
-
Telemetry (Tells where the vehicle is, and how long it can go) [3]
Battery Pack construction and management
-
-
-
Battery Pack:
-
Electrical Design:
-
Deals with capacity, voltage and current
-
High voltage isolation
-
Short circuit scenarios
-
Efficient power delivery
-
-
Thermal Management:
-
Improve Pack efficiency
-
Mitigate thermal accidents
-
Increase cell/pack life
-
-
Mechanical Design:
-
Safe structure for extreme condition
-
Cost, productivity and reliability
-
Ease of assembly and service
-
Aesthetics, compactness and lightweight
-
-
Battery Management System:
-
Maintain cell/pack operating limit
-
Prevent safety concerning events
-
Control thermal systems
-
Communication and diagnostics [3]
-
-
Figure 5: Battery Pack of Tesla Model-S [8]
-
-
METHODOLOGY
-
Motor Power Calculation
Figure 6: Setup of Motor Wheel assembly The wheel shown in the above figure is of MRF
brand. Its size is 130/70-17 and its weight is 5kg. In order to run the wheel, the motor must overcome all the forces acting on the wheel. Since the wheel is not in contact with the ground, there is no rolling and gradient resistance. Only Aerodynamic drag is acting on the wheel. The acceleration values of motorcycles without a passenger vary from 3 to 3.5 m/s^2 for a normal start.
In our experiment we are calculating the amount of resistance force required to be overcome in order to run the wheel from 0-45km/hr at an acceleration of 3m/s^2. The mass of the wheel assembly is taken as 7kg.
Thus,
Mass, m = 7 kg(assumed) Acceleration, a = 3 m/s^2 Initial speed, u = 0m/s Final speed, v = 45 km/hr
= 12.5 m/s
As we know, v = u + a*t
12.5 = 0 + (3*t) t = 12.5/3
= 4.167 s
1 2
Step 2: Find out the Watt hour of the battery:
To run the 986 W motor for 1 hour = 986 * 1 hour = 986 Watt hour
To extend the life of the battery pack, we do not want to discharge the batteries more than 80%. Therefore, take efficiency of 80% for battery.
i.e. (986/0.8) = 1233 Wh
Aerodynamic Drag, = 2
We know,
= 1.225 kg/m^3
= 0.72 m^2
= 0.84
Thus, = 57.88 =
= m*a [1] [1]
Step 3: Convert Watt hour of battery into Ampere hour of battery:
Power = Voltage * Current [3]
Watt hour = Voltage * Ampere hour 1233 = 48 * Ampere hour
Ampere hour = 1233/48 = 25.68 =26 (approx.)
Therefore, to run the 986 W motor for 1hr, 48V 26Ah lithium- ion battery is needed.
= m*a = 7*3 = 21 N
= (21 + 57.88) N = 78.88 N
Thus, the wheel has to overcome this 78.88 N force to get
propelled.
The propelling power required to overcome this force:
= = 78.88*12.5 = 986 W
Thus, in order to run the wheel of 7kg at a speed of 45 km/hr
with an acceleration of 3m/s, we need a motor of 986 W power.
-
Battery Pack Calculation
Figure 7: Motor Controller and power source assembly In our experiment we are trying to replace the power
source shown in above figure with a battery in order to run the 986 W motor.
Step 1: Find out the current (in amps) consumed by the motor to run:
Let voltage 48 V Then,
Power =Voltage * Current [3] 986 = 48 * I
I = 20.54 amps (Theoretically)
-
-
CHARGING OF ELECTRIC VEHICLES
The battery pack of an Electric vehicle is generally required to be recharged after a particular interval of times. For instance, in the present study the estimated recharge time of the developed prototype is 1 hour approximately.
While safety, reliability, and luxury are all important when choosing a vehicle, with plug-in hybrid electric vehicles (PHEVs) and battery electric vehicles (BEVs) theres another critical factor to consider; the time taken to charge. While replenishing an ICE vehicle takes just some minutes, the time needed to replenish the motive battery on PHEVs and BEVs is significantly longer.
Several varieties of wattage are now available. Hybrid vehicles have both a fuel powered drivetrain and an electrical drivetrain which might be organized in numerous ways. Some types, like mild hybrid, have a smaller battery and this can be charged from a mix of the ICE and a generator. And regenerative braking provides some charge to increase the range while the vehicle is slowing down and therefore the motor acts in reverse as a generator. PHEVs and BEVs include the power to infix to the mains grid and recharge the battery from there, while the vehicle is stationary.
There are a number of different ways to charge the electric cars battery pack. Essentially, it comes down to two main considerations: Where we decide to charge and how fast we decide to charge. These are interconnected, and the charging speed will depend on which particular EV we choose, its battery capacity and what sort of charging system we are using. [6]
There are three categories or forms of charging: Trickle Charge, AC Charge and DC Charge.
-
Trickle Charge:
The slowest method of charging the EV reception, employing a standard (three-prong) 220V plug. it's only recommended in urgent cases,
with caution and consultation with electricity providers.
-
AC Charge:
Having a wall box installed enables to charge 3-4 faster using AC Household Charging. AC Public Charging is additionally available.
-
DC Charge:
The fastest way to charge the EV at a public DC Fast charging station with power from 50kW and above. With this method we will be able to top up our battery from 20 to 80% in approx. 40 minutes. There also are some ultra-fast charging stations that already provide over 150kW. [6]
Home vs. public charging:
There are two options charging the Electric Vehicle at home using our own domestic mains electricity supply, or making use of public charging stations. This will affect the types and speeds of charging available to us.
Option 1: Home charging
Figure 8: Home Charging [6]
Around 80% of all Electric Vehicle charging is currently done at home. Usually overnight while owners sleep waking to a completely charged battery the following morning that just about always provides quite enough EV range for many peoples daily travel needs. There are two kinds of home charging available: Using Trickle Charge with the household current or AC Household Charge with an installed wall box. Here are the key differences:
-
TRICKLE CHARGE
-
Provides charging through a regular (three- prong) 220V plug that comes with the EV. the opposite end is just plugged directly into our EV
-
Doesnt require installation of additional charging equipment
-
Can deliver 13 to 16 km of range per hour of charging
-
Charging speed: approx. 65 km of range in 5 hrs. (overnight), or 200 km in 14 hours
-
Using Trickle Charge is merely recommended in urgent cases once we have low battery charge and can't drive to a public station or access an AC wall box reception. this is often because the utilization of household electricity may cause problems related to electricity bills and electrical loads, so we should always use this charge solution with caution and talk over with our electricity provider before first use. Purchasing an ICCB (In Cable Control Box) cable when using Trickle Charge is usually recommended, for optimum reliability and peace of mind.
-
-
AC HOUSEHOLD CHARGING WITH WALLBOX
-
The most common and recommendable home charging option
-
Provides charging through a 230V outlet which allows charging 3 to 4 times faster than Trickle Charge depending on the acceptance rate of our specific model and the charger
-
Especially useful if we have time to top up our electric vehicle overnight: it takes around 6 hours to fully charge a 40-kWh battery car
-
Requires the installation of a dedicated EV charging wall box, which should be fitted by a trained electrician
-
Ideal if we have a garage or driveway in which it can be positioned
-
There may also be financial incentives in our local region or country to minimise purchase and installation costs [6]
-
Option 2:
Public charging Station
Figure 9: Public Charging Station [6]
Increasingly convenient due to the ever-growing network, these stations can often be located throughout urban centers specifically and permit us to top up our battery on the go if we'd like to travel longer distances.
Public charging offers AC Charging with a wall box or
-
within the majority of cases DC Fast Charging.
And both options are quicker than charging at home: AC Public Charging will be 3 to 10 times faster than AC Household Charging, counting on the charging station output and our Electric Vehicles capacity to handle AC Chargers.
-
DC FAST CHARGERS
-
It is presently the fastest way to charge an EV.
-
Provides charging power above 50kW through a voltage above 450V and current up to 125A.
-
It is capable of charging from 20 to 80% of charge in approx. 40 minutes.
-
Utilizes Combo DC (CCS for Combined Charging System).
-
Use of DC Charge should be kept to a minimum so as to assist prolong high- voltage battery life. [6]
AC versus DC charging explained:
The national grid supplies Alternating Current, but electric cars require Direct Current to charge the battery pack.
-
-
An Alternating Current charger provide the Electric Vehicles onboard charger, which then converts the AC power to DC allowing the battery to charge. The dimensions of the onboard charging device are limited by space. Due to this restricted space, the quantity of power delivered to the battery is comparatively low which suggest that charging is sometimes slower.
-
A Direct Current fast charger bypasses the onboard charging device by supplying power on to the EVs battery. The DC charger is external to the car therefore, it isnt constrained in size or cost. Meaning that charging is sometimes much faster.
-
Figure 10: AC Verses DC Charging [6]
So which connector for which charging type?
We might be asking ourself if we need an adapter for different charging methods and types. Presently there is not a universal connector for all Electric Vehicles and all chargers. But the different types of connectors do correspond with the different levels of charging, making things simpler for EV drivers.
Heres an overview of the main connector types:
Figure 11: Overview of the Main Connector types [6] AC Charging Connectors:
Type 1 and Type 2 connectors are the most frequently used AC sockets mainly for AC Household Charging.
DC Charging Connectors:
For fast charging, the Type 2 CCS, which stands for Combined Charging System are the most commonly used connectors. These two connectors are not interchangeable however a CHAdeMO port cannot charge using an SAE Combo plug, and vice versa. So before driving to a charging station we need to know if our car is compatible with the connectors availabl. [6]
-
-
CONCLUSION
The transition from Internal combustion Engine to Electric Vehicle is a necessity. Electric Vehicles are an Eco-Friendly Choice. Electric vehicle as compared to the conventional Internal combustion engine do not pollute the air. It results in zero emission and the surrounding air doesn't get dirtied.
The first part of the project is briefly focused on the dynamic forces of the vehicle. It tells about all types of forces acting on the vehicle. In order to move the vehicle, the motor needs to overcome the net resistive forces acting on the vehicle. The motor power calculation of a wheel assembly has been calculated. The wheel taken into consideration is of MRF brand. Its size is 130/70-17 and its weight is 5kg. In order to run the wheel, the motor must overcome all the forces acting on the wheel. Since the wheel is not in contact with the ground, there is no rolling and gradient resistance. Only Aerodynamic drag is acting on the wheel. The acceleration values of motorcycles without a passenger vary from 3 to 3.5 m/s^2 for a normal start. The mass of the wheel assembly is taken as 8kg. We made calculations for net resistive forces and the effort needed to overcome this force. We found out that in order to run the wheel of 7kg at a speed of 45 km/hr with an acceleration of 3m/s, we need a motor of 986 W power.
In the second part of the project, we have discussed about the cell, battery, cells connection, Functional components of an electrochemical cell, the calculation to measure the capacity of the battery needed to run a 986 W motor and finally all the various ways to charging an electric vehicle.
A battery pack is a set of any number of (ideally) identical batteries or individual battery cells. they will be configured in an exceedingly series, parallel or a mix of both to deliver the required voltage, capacity, or power density. Components of battery packs include the individual batteries or cells, and the interconnects which supply electrical conductivity between them. In this experiment we are trying to use battery as the power source in order to run the 986 W motor. In first step we have found out the current (in amps) consumed by the motor to run. Then we focused on the Watt hour of the battery and at last Converted the Watt hour of battery into Ampere hour of battery. After the calculations we found out that to run the 986 W motor for 1hr, 48V 26Ah lithium-ion battery is needed.
Lastly the different ways to charge the electric cars battery pack has been explained. Essentially, it comes down to two main considerations: Where we decide to charge and how fast we decide to charge. These are interconnected, and the charging speed will depend on which particular EV we choose, its battery capacity and what sort of charging system we are using. Presently there is not a universal connector for all Electric Vehicles and all chargers. But the different types of connectors do correspond with the different levels of charging, making things simpler for EV drivers. Type 1 and Type 2 connectors are the most frequently used AC sockets mainly for AC Household Charging. For fast charging, the Type 2 CCS, which stands for Combined Charging System are the most commonly used connectors. The connectors CHAdeMO and SAE are not interchangeable. However, a CHAdeMO port cannot charge using an SAE Combo plug and vice versa. So before driving to a charging station we need to know if our car is compatible with the connectors available.
REFERENCES
[1] https://www.studocu.com/in/document/rajiv-gandhi- proudyogiki-vishwavidyalaya/hybrid-andelectrical- vehicles/hev-notes-pdf-1/38220741 [2] https://x-engineer.org/automotive- engineering/vehicle/electric-vehicles/advantages-of- electric-vehicles/ [3] Research on Li-ion Battery Management System. Dongping XU, Lifang Wang, Jian Yang, Institute of Electrical Engineering Chinese Academy of Science Beijing, China 100190 [4] www.wikipedia.org [5] https://www.avnet.com/wps/portal/abacus/solutions/mark ets/automotive-and-transportation/automotive/power- train-and-ev-hc-phev-systems/ev-on-board-chargers/ [6] https://www.kia.com/eu/about-kia/experience- kia/technology/electrification/charging-methods-for- electric-cars/ [7] https://circuitdigest.com/article/an-engineers- introduction-to-electric-vehicles [8] https://www.bloomberg.com/graphics/2017-lithium- battery-future/img/2017-lithium-battery-future- facebook.png [9] Mehrdad Ehsani, Yimin Gao and Ali Emadi. Modern Electric, Hybrid Electric and Fuel Cell Vehicles, Fundamentals, Theory and Design. CRC Press. Taylor & Francis Group. 2010. [10] Etkin Özen. Design of Smart Controllers for Hybrid Electric Vehicles. Middle East Technical University.Ankara. Turkey. August 2005
[11] Leon. C. Rosario. Power and Energy Management of Multiple Energy Storage [12] Systems in Electric Vehicles. Cranfield University. Dcmt Shrivenham Swindon. Wiltshire. United Kingdom. June 2007