
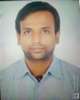
- Open Access
- Authors : Chandrashekarappa B Gaddikeri , Manjunath V S , Praveen Ahuja
- Paper ID : IJERTV10IS020270
- Volume & Issue : Volume 10, Issue 02 (February 2021)
- Published (First Online): 08-03-2021
- ISSN (Online) : 2278-0181
- Publisher Name : IJERT
- License:
This work is licensed under a Creative Commons Attribution 4.0 International License
Evaluation of Equivalent Elastic Modulus for Orthotropic Behavior of PCB
Chandrashekarappa B Gaddikere
Technical Lead Engineer, CAE
Manjunath V S
Technical Manager, CAE
Praveen Ahuja
Global Program Manager, CAE
Abstract PCB (Printed Circuit Board) is widely used in various engineering applications. PCB mechanically supports and electrically connects electronic components. To check the failure of component on PCB, it is important to perform PCB simulation for various load conditions. PCB construction varies with the number of component on PCB and criticality of circuit. Hence, material properties also changed according to type of PCB. In this paper, the importance of material properties in PCB analysis is discussed. PCB is fabricated by incorporating copper layers in sequence with FRP (fiber reinforced polymer) composite layer, for the purpose of forming conducting circuit. CLT (Classical Lamination Theory) is used to find the material properties of FRP laminate in PCB. Average properties of PCB material are determined by force balance equation. Based on this knowledge, a OrthoPCB tool is developed using the Python script to determine orthotropic elastic modulus properties of any PCB. The properties generated by the computational tool can be used for FE simulation and the results are validated by test results.
The main requirement here is to determine the effective orthotropic elastic modulus properties of a copper cladded laminate (PCBs). The use of the effective implies properties of the entire laminate.
Keywords Classical Lamination Theory, Composite material, Natural frequency, Orthotropic material, PCB.
-
INTRODUCTION
For modern electronics, such as smart phones or other consumer electronics, improvement goals are much smaller scale, increased power, tougher durability, and more cost effectiveness. Electronic circuits in industry are normally manufactured through the use of PCB. The boards are made from glass reinforced plastic with copper tracks in the place of wires. Components are fixed in position by drilling holes through the board, locating the components and then soldering them in place. The copper tracks link the components together, forming a circuit. For mounting the electrical components on the printed circuit boards, an assembly process is required. This process can be done by hand or through specialized machinery. The assembly process requires the use of solder joint to place the components on the board. PCBs are constructed according to the number of components to mount on it.
Depending on the number of planes or layers of wiring, which constitute the total wiring assembly or structures the PCBs can be classified in following three types:
-
Single sided board: Means wiring is available only on one side of the insulating substrate where components are mounted only on one side of board, it is used in simple circuits.
-
Single sided board: Means wiring is available only on one side of the insulating substrate where components are mounted only on one side of board, it is used in simple circuits.
-
Multilayer Board: A multilayer PCB board (Fig.1) is used in situations where the density of connections needed is too high to be handled by two layers or where there are other reasons such as accurate control of line impedances or for earth screening. The multi-layer board makes use of more than two PCBs with a thin layer of what is known as prepreg material placed between each layer, thus making a sandwich assembly. Advantages of multilayer PCBs include high reliability and uniform wiring. However, the initial costs are higher than that of one-layered PCBs. Also, repairing a multilayer PCB is quite difficult.
-
-
PROBLEM DEFINATION
The PCBs are widely used in all the electronic devices or equipments and its mechanical properties will be differing from PCB to PCB based on the number of layers and its thickness. Since there is no proper data available on PCB orthotropic material properties, most of the FE simulations has been carried out using isotropic material properties which affects the accuracy of virtual test simulation results. Hence, in the absence of material test data, it is necessary to evaluate the orthotropic material properties of PCB using empirical formulae to obtain the accuracy in the simulation.
-
PROBLEM SOLUTION AND IMPLEMENTATION
The orthotropic behavior of PCB can be evaluated by using either of the two approaches.
-
Physic testing for PCB
-
Using empirical formulae
-
physical testing for PCB
One of the most common physical testing method is tensile testing and it is used to determine the behavior of a material. Instron Micro Tester is used for the determining the Youngs modulus of the PCB. The instrument setup is shown in the Fig.2.This type of testing may be performed under ambient or controlled heating or cooling conditions to determine the properties of a material. Proper precautions and standardized steps are performed to obtain the accurate results and for the individuals safety. The results of the tensile testing are used to determine how the material under loading conditions behave and also to determine the Youngs modulus of PCB. It is desirable to plot the data in terms of true strain and true stress. Extensometer fig.4 installed at certain location of the Instron micro tester to record the strain at certain loading intervals.
Fig.2 Instron micro testing machine. Fig.3 Scheme showing test setup
-
Empirical Formulae
Printed circuit boards (PCBs) are composed of alternating layers of glass reinforced epoxy laminate / prepreg and copper foil. Core material is a rigid sheet of fiberglass resin material that has two sheets of copper adhered to either side. Some material may have a copper sheet on only one side. The copper is measured in ounces (oz). PCB manufacturers will refer to the copper thickness in ounces, but during board lay-up, or when the materials are stacked together, the inch/mm thickness is used. Pre-Preg material is made of similar material as the core material but is in a soft, pliable form and comes in standard-sized thin sheets. Copper foil is a thin sheet of copper that is placed on or between Pre-Preg materials and bonds to the Pre-Preg with the adhesive that is part of the Pre-Preg as shown in the fig.6
Fig.6 Layers within the PCB Fig.7 Details of PCB Layers
PCB exhibits orthotropic behavior and its having two or more different types of materials (FR4 and Copper) called as hybrid composites and, more specifically interplay hybrid composites. Material Properties of PCB depend on the properties of composite laminate and copper. This paper describes about to find equivalent elastic modulus of PCB considering the isotropic material properties of copper and FR4 using formulae.
Equivalent elastic modulus of PCB in-plane Exypcb and out of plane Ezpcb can be calculated using below formulae.
= [1 × (
1
)] + [2 × (
1
)] +
+ [ × (
)]
1
= [(
1
2
) /1] + [(
) /2] +
Fig.4 Placement of Extensometer Fig.5 Youngs modulus FR4 and Pre-peg
True stress is defined as
Term definitions;
+ [( ) /]
= F/A
Where F is the applied force
A is the cross sectional area of the specimen True strain is defined as
= ln (L/Lo)
Where, L is the Change in lengt Lo is the original length
True strain definition in nothing but the incremental change in the length to the original length. As long as the deformation under the tensile loading is uniform, the true strain can be calculated mathematically. Here in this experiment the true strain is calculated from the Extensometer readings. The strain is directly recorded from the extensometer and the stress is calculated mathematically from the load applied to the cross section of the specimen used. A graph is plotted with stress on X axis and strain on Y axis as shown in the fig.5. The slope is calculated to get the youngs modulus of the material.
Similarly, youngs modulus is determined for other two directions
-
Exypcb is the elastic modulus, in plane of the PCB
-
Ezpcb is the elastic modulus, out of the PCB
-
Exyln is the elastic modulus, in-plane of layer n
-
Ezln is the elastic modulus, out of the plane of layer n
-
tln is the thickness of layer n
-
tpcb is the overall thickness of the PCB
-
-
-
-
PROCESS AUTOMATION USING ORTHOPCB TOOL DEVELOPMENT
Orthotropic material properties of PCB can be calculated either by physical testing method or by empirical formulae. Both methods are time consuming hence, to standardize & simplify the process a customized GUI based computational tool is developed using python language called OrthoPCB. The
(Eypcb and Ezpcb)
computational tool developed is a part of the hand calculation approach to automatically calculate the orthotropic mechanical properties for PCB (Fig.8).
Fig.8 Overview of OrthoPCB Computational tool
OrthoPCB tool is having 2 separate sections for inputs and outputs. User must feed just few inputs such as number of layers in the PCB and isotropic youngs modulus of copper and di- electric to generate the effective orthotropic mechanical properties for PCBs. Tool generates layers based on the input provided in the input panel and each layer consist of metal and dielectric. Thickness details of each layer in mills needs to be input manually to the tool. Tool output section generates the effective orthotropic youngs modulus of PCB in-plane (Exypcb) and out of plane (Ezpcb).
-
FEA CORRELATION WITH PHYSICAL TEST RESULTS
The orthotropic properties obtained from the OrthoPCB computational tool can be validated by comparing simulation results with the physical test results on ADAS camera system.
Test Result
Gauge-1
Gauge-2
Strain, in microns
485.17
392
Test Result
Gauge-1
Gauge-2
Strain, in microns
485.17
392
Fig. 9 Physical test of PCB Table 1: Physical test result of PCB
Physical test is performed on ADAS camera model shown in fig.9 and the strain gauges are placed near the screw hole locations of the PCB (gauge-1 and gauge-2) to collate the strain results and it has been tabulated (Table 1). FE Simulation is also carried out on the same ADAS camera model considering the Isotropic material properties and tool generated orthotropic material properties and deviation in the results tabulated.
Isotropic FE analysis results are shown in fig.10 and fig.11 below which indicate the strain at the same locations.
Fig. 10 Total deformation Fig. 11 von Mises strain plot
Table 2: Isotropic FEA results of PCB
Similarly, orthotropic FE analysis results are shown in fig.12 and fig.13 below which indicate the strain at the same locations
Fig. 12: Total deformation plot Fig. 13: von-Mises strain plot
Table 3: Orthotropic FEA results of PCB
By observing both physical test results and FEA results a comparison study and result deviation is tabulated below table4
Table 4: Strain % deviation from test Strain comparison chart
Above test and FEA comparison results clearly indicates that percentage deviation between orthotropic FEA results and test results are almost closer.
-
CONCLUSION
The OrthoPCB computational tool assist to generate the orthotropic material properties in-plane (Exypcb) and out of plane (Ezpcb) by considering the isotropic youngs modulus of copper and FR4. Tool is extensively helpful in standardizing and simplifying the process of orthotropic material property computation for the PCBs. Mechanical properties generated from the tool closely match orthotropic behavior of PCB hence, better FEA to test correlation is observed. Tool does not have limitation in handling any number of PCB layers and quickly generates orthotropic properties with bare minimum inputs.
-
FUTURE WORK
Currently OrthoPCB tool can handle only copper and di- electric materials within PCB layers and it is not generating other mechanical or thermal properties such as Poissons ratio & coefficient of thermal expansion. With the help of empirical formulae, tool can be enhanced in future to generate Poissons ratio & coefficient of thermal expansion and also to handle Aluminum metal & di-electric material constituents in the PCB layer stack-up.
REFERENCES
-
SANJAY MAHESAN REVATHI , EXPERIMENTAL AND COMPUTATONAL ANALYSIS ON THE EFFECT OF PCB LAYER COPPER THICKNESS AND PREPREG LAYER STIFFNESS ON SOLDER JOINT RELIABILITY
-
ASHOK KUMAR AIYYASWAMY, CHARACTERIZATION OF ELECTRONIC BOARD MATERIAL PROPERTIES UNDER IMPACT LOADING
-
HONG-KONG POLYTECHNIC UNIVERSITY,PCB TRAINING MATERIAL2013
-
VINOD NIRALE ,EVALUATION OF EFFECTIVE THERMAL CONDUCTIVITY IN PCB
-
MADENCI, THE FINATE ELEMENT AND APPLICATIONS IN ENGINEERING USING ANSYS,XVI ED. SPRINGER,2007
-
INTRODUCTION TO ANSYS MESHING LECTURER 3,18.0 RELEASE.
-
STEPHEN HALL,FULL-FILED DISPLACEMENT/STRAIN MEASUREMENTS AND DIGITAL IMAGE CORRELATION PRINCIPALS AND METHODS
-
ROMMEL CINTRUN,DR.VICTOR SAOUMA STRAIN MEASUREMENT WITH DIGITAL IMAGE CORRELATION SYSTEM VIC-2D
-
PO-CHIH HUNG AND A.S VOLOSHIN IN-PLANE STRAIN MEASUREMENT BY DIGITAL IMAGE CORRELATION
-
KUN-YEN WANG,DEVELOPMENT AND APPLICATION OF COMPOSITE MATERIAL LAMINATION THEORY FOR PRINTED CIRCUIT BOARD
a.