
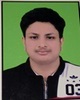
- Open Access
- Authors : Ayush Gupta , Aaryan Kumar Mishra , Abhishek Kumar , Ankesh Parashar, Dr. Umesh G. L
- Paper ID : IJERTV12IS020146
- Volume & Issue : Volume 12, Issue 02 (February 2023)
- Published (First Online): 09-03-2023
- ISSN (Online) : 2278-0181
- Publisher Name : IJERT
- License:
This work is licensed under a Creative Commons Attribution 4.0 International License
Electromagnetic Braking System
Ayush Gupta
Of Department of Mechanical Engineering Bangalore institute of Technology Bengaluru ,India
Abhishek Kumar
Of Department of Mechanical Engineering Bangalore institute of Technology Bengaluru ,India
Ankesh Parashar
Of Department of Mechanical Engineering Bangalore institute of Technology Bengaluru ,India
Aaryan Kumar Mishra
Of Department of Mechanical Engineering Bangalore institute of Technology Bengaluru ,India
Dr. Umesh G.L
Asst. Professor
Of Department of Mechanical Engineering Bangalore institute of Technology Bengaluru ,India
Abstract The electromagnetic braking system is a vital area of research in the field of automotive engineering. This system uses electromagnetic force to stop a moving vehicle, offering several advantages over conventional friction braking systems. In this paper, we provide an overview of the electromagnetic braking system, its working principles, and various types. We also discuss the advantages and disadvantages of electromagnetic braking systems and compare them with conventional braking systems. Finally, we conclude the paper by highlighting some of the current research trends in this area.
-
INTRODUCTION
The traditional friction braking system used in vehicles has several limitations, including wear and tear, noise pollution, and reduced braking efficiency at high speeds. The electromagnetic braking system, on the other hand, uses electromagnetic force to slow down or stop a moving vehicle. This system has gained significant attention in recent years due to its potential to overcome the limitations of conventional braking systems. The electromagnetic braking system offers several advantages, including faster response times, reduced noise pollution, and increased efficiency at high speeds.
-
WORKING PRINCIPLES:
The electromagnetic braking system works based on the principles of electromagnetic induction. When a magnetic field is applied to a conductor, an electric current is induced in the conductor. In the electromagnetic braking system, the magnetic field is created by an electromagnet. When the electromagnet is powered, it generates a magnetic field that interacts with the moving conductor, which could be a rotor or a rail, and induces a current in it. This induced current creates a magnetic field that opposes the original magnetic field, thus slowing down or stopping the conductor.
-
Types of Electromagnetic Braking Systems:
There are various types of electromagnetic braking systems, including eddy current braking, hysteresis braking, and regenerative braking. Eddy current braking uses a stationary coil and a moving conductor, where the magnetic field generated by the coil interacts with the moving conductor, inducing an eddy current that opposes the motion of the conductor. Hysteresis braking uses a magnetic material, such as iron, which generates heat due to hysteresis losses, resulting in the slowing down of the conductor. Regenerative braking uses the motor of an electric vehicle as a generator to recover some of the energy lost during braking and convert it into electrical energy.
-
-
EXPERIMENTAL SETUP
Experiment is conducted in a two-wheeler (Yamaha crux). Aluminium disc of thickness 13 mm is attached to the chain sprocket of bike (fig-1). Electromagnet of 12-volt 14 ampere rating is used and is attached near to the aluminium disc with an air gap of 3 mm (Fig-2). The 3 mm air gap is selected to reduce the reluctance in magnetic field to the disc. The electromagnet can be powered directly from the magneto winding of the vehicle. However, in this experiment two 7 ampere battery in parallel is used.
-
LITERATURE SURVEY
-
Won-Sec-Cho, Moto-hisa-kanda, Ho-Jung-Hwang, and Michael W. Howard (2000) "A Disk-stacked Thick Cylindrical dipole-Antenna for Validation of an Electromagnetic-similarity test site from 30-300MHz" [26]. The proposed broadband short 80Cm-long plate stacked thick barrel shaped dipole recieving wire, which plot that the range is 30MHz-300MHz utilizing the tube shaped co-ordinates framework and M0M as the numerical apparatus and its finding as 8dB-26dB.
There is dependably a route for future extension, past the planned range we can't play out the validation.
-
Bhattacharya Guptha and Chakraborty A (1999) Investigation of rectangular-waveguides and thick- windows as EMI sensors". Utilizations Rectangular co- ordinates framework and M0M Technique, executed utilizing programming device FORTRAN 77 for far field examination and its impediments are for low field impedance.
-
Florian-Krug, Peter-Russer(2003) The Time-Domain Electromagnetic Interference Measurement system. Fast Fourier Transform(FFT) is the numerical apparatus and broadband recurrence examination running 400MHz-500MHz is conveyed. The work is limited for broadband frequencies.
-
R Giannetti, M Macucci and B Tellini (2001) EMI Measurements in LinePantograph Contact Discontinuity in Railway-Transportation-Systems" [29]. The idea is identified with 0.5MHz-1MHz frequencies and damped motions around 20MHz utilizing the fourier change method for Line- Pantograph alone.
-
Electromagnetic brake systems will reduce maintenance cost. The problem of brake fluid vaporization and freezing is eliminated.
-
-
Disadvantage:
-
Dependence on battery power to energize the brake system drains down the battery much faster.
-
Due to residual magnetism present in electromagnets, the brake shoe takes time to come back to its original position.
-
A special spring mechanism needs to be provided for the quick return of the brake shoe.
-
Less effective at lower speeds. It cant stop the vehicle as effectively as drum brakes.
-
-
Equations
During braking a drag force is created in the disc and due to this the disc may deform.
Assuming the maximum speed of vehicle to be 100 kmph, the total weight with passenger be 200 kg.
-
Advantage:
-
-
Problems of drum distortion at widely varying temperatures. Which is common for frictionbrake drums to exceed 500 °C surface temperatures when subject to heavy braking demands, and at temperatures of this order, a reduction in the coefficient of friction (brake fade) suddenly occurs
-
This is reduced significantly in electromagnetic disk brake systems
-
Potential hazard of tire deterioration and bursts due to friction is eliminated.
-
There is no need to change brake oils regularly.
-
There is no oil leakage
-
The practical location of the retarder within the vehicle prevents the direct impingement of air on the retarder caused by the motion of the vehicle.
-
The retarders help to extend the life span of the regular brakes and keep the regular brakes cool for emergency situation. The electromagnetic brakes have excellent heat dissipation efficiency owing to the high temperature of the surface of the disc which is being cooled.
-
Due to its special mounting location and heat dissipation mechanism, electromagnetic brakes have better thermal dynamic performance than regular friction brakes
-
Burnishing is the wearing or mating of opposing surfaces. This is reduced significantly here.In the future, there may be shortage of crude oil, hence by- products such as brake oils will be in much demand. EMBs will overcome this problem.
100kmph=27.7 m/s
By conservation of energy, Work done = change in kinetic energy
Final velocity =0 m/s
Kinetic energy = .5*mass*velocity2 Final kinetic energy =0
Fb x displacement = 0- (.5*200*(27.7)2) Where Fb is braking force
Let the braking distance be 30m Fb x 30 = 76729 Fb = 76729/30 Fb = 2500 N
-
-
CONSTRUCTION:
THE PARTS OF ELECTROMAGNETIC DISC BRAKE ARE:
-
AC MOTOR : AN AC MOTOR IS AN ELECTRIC MOTOR DRIVEN BY AN ALTERNATING CURRENT. IT COMMONLY CONSISTS OF TWO BASIC PARTS, AN OUTSIDE STATIONARY
STATOR HAVING COILS SUPPLIED WITH ALTERNATING CURRENT TO PRODUCE A ROTATING MAGNETIC FIELD, AND AN INSIDE ROTOR ATTACHED TO THE OUTPUT SHAFT THAT IS GIVEN A TORQUE BY THE ROTATING FIELD. WHERE SPEED STABILITY IS IMPORTANT, SOME AC MOTORS (SUCH AS
SOME PAST MOTORS) HAVE THE STATOR ON THE INSIDE AND
THE ROTOR ON THE OUTSIDE TO OPTIMIZE INERTIA AND COOLING.
-
DISC
-
FRAME
-
ELECTROMAGNET
-
PULLEYS & BELT
-
SHAFT CONSTRUCTION
V. ANALYSIS:
Analysis is done using ANSYS R16.2. The 3D model of the disc was created in DS Solid Works 2016. The eddy current brakes change kinetic energy of rotation into heat energy which is lost to the surrounding. The heat energy is also lost by convection. As disc is rotating in air, heat transfer occursby forced convection also. Temperature Distribution Temperature distribution of copper disc is analysed. Electromagnet rating is 12-volt 14 ampere. So highest amount of heat input to disc is 12×14=168 watts. The heat is lost to surroundings by forced convection when disc is moving. The atmospheric temperature is assumed to be 300C. The peak temperature attained is 30.0970C. Because of the incoherence in the copper disc because of the bolts, temperature produced is greater betweethe bolts.
-
RESULT
By using the electromagnetic brake as supplementary retardation equipment, the frictions brakes are often used less frequently and thus practically never reach high temperatures. The brake linings would last considerably longer before requiring maintenance, and therefore the potentially brake fade problem might be avoided. In research conducted by a truck manufacturer, it had been proved that the electromagnetic brake assumed 80 percent of the duty which might otherwise is demanded of the regular service brake (Reverdin 1974). Furthermore, the electromagnetic brake prevents the risks which will arise from the prolonged use of brakes beyond their capability to dissipate heat. This is often presumably to occur while a vehicle descending an extended gradient at high speed. The installation of an electromagnetic brake isn't very difficult. It doesn't need a subsidiary cooling system. It doesn't effect on the efficiency of engine. Electromagnetic brake also has better controllability. Thermal
stability of the electromagnetic brakes is achieved by means of the convection and radiation of the warmth energy at heat. The electromagnetic brakes have excellent cooling efficiency. Electromagnetic brakes have better thermal dynamic performance than regular.
-
Conclusion :
The electromagnetic braking system is an important area of research in the field of automotive engineering, with significant potential to overcome the limitations of conventional braking systems. This paper provides an overview of the working principles, types, advantages, and disadvantages of electromagnetic braking systems. With further research and development, the electromagnetic braking system could become a significant contributor to the development of efficient, safe, and environmentally friendly vehicles
-
FUTURE SCOPE :
The blend of swirl present and attractive powers makes this brake more successful. This brake is often utilized as assistant stopping mechanism in vehicle. The use of abs is often dismissed by utilizing a smaller scale controlled electromagnetic framework. It is often utilized as a neighbourhood of rail mentors to decelerate the prepare occupation fast. Mixture of these brakes expands the brake life and act like completely stacked brakes. These brakes are often utilized as a part of wet condition, so there's no utilization of against slipping instrument .it is completely electrically controlled which brings about fewer mishaps. The braking power delivered during this brake isn't the maximum amount because the plate brakes. Subsequently, it is often utilized as an auxiliary or crisis slowing mechanism within the autos..
-
Figures and Tables
a. How Eddy Current works
Fig 2. Analysis of disc in ANSYS
-
-
ACKNOWLEDGEMENT
We would like to thank our Head of the Department, Dr. T V SREERAMA REDDY and our guide Dr. UMESH G. L. for their valuable advice and technical assistance.
-
REFERENCES
engineering.
[6] Flemming, Frank; Shapiro, Jessica (July 7, 2009). Basics of Electromagnetic Brakes. machine design: pp.5758 [7] Kren, Lawrence; Flemming, Frank (August 5, 1999). "Getting a Handle on Inertia. machine design: pp.9293. [8] Auguston, Karen; Flemming, Frank (September 1999). "Floating Armature Speeds Response. Global Design News: pp.4647. [9] Zalud, Todd; Flemming, Frank (September 9, 1999). "Getting a Grip on Brake Selection. machine design: pp.8386.