
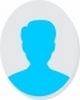
- Open Access
- Authors : Koku-Ojumu B.E , Kehinde A. S , Faboro O. P , Omojola O. O
- Paper ID : IJERTV10IS100170
- Volume & Issue : Volume 10, Issue 10 (October 2021)
- Published (First Online): 06-12-2021
- ISSN (Online) : 2278-0181
- Publisher Name : IJERT
- License:
This work is licensed under a Creative Commons Attribution 4.0 International License
Effect of Water /Cement(W/C) Ratio and Coconut Shell Ash (CSA) on Some Engineering Properties Concrete
Koku-Ojumu B.E, Kehinde A. S, Faboro O. P, Omojola O. O Nigeria Building and Road Research Institute
(NBRRI)
Abstract: The cost of cement for concrete works which increases as the population grows, this material is becoming unaffordable and it important for construction works, thus the need to find alternative material such as coconut shells (Agricultural waste) as a partial replacement of cement in concrete production is sacrosanct. This coconut shells were collected and burnt in the open air (uncontrolled combustion) for 3hrs to produce coconut shell ash (CSA). This study was directed toward studying performance of cement and coconut shell ashes in concrete under varying water to cement ratio. These mixes were proportioned to have cement replacements in the range of 0 and 10 percent by weight. For each percentage, water to cement ratio was varied between 0.4 – 0.6, in steps of 0.1. The work investigated the physical properties, setting time of cement paste, workability, pozzolanic activity index, compressive and tensile strength of concrete elements with cement partially replaced with C.S.A. 90 Nos. 150x150x150mm concrete cubes and 60 Nos. 150 x 300mm cylinder specimens were produced and cured for 7, 14, 28, 45, 90 days respectively. The mix ratio of 1:1.5:3 (Cement: Fine aggregate: Coarse aggregate). The workability of concrete mix was found to increase as water-cement ratio is increased from 0.4 to 0.6 and decrease as percentage replacement of cement with CSA increased from 0% to 10%, which means that coconut shell ash(CSA) can be used as a retarder in slowing concrete setting time. The results on compressive strength shows that the strength value (tensile and compressive) decreased as the percentage replacement increased from 0% to 10% replacement. It was observed that for each percentage replacement, there is variation in the tensile strength. The characteristic compressive strength of
34.07 N/mm2 of the 0% replacement and 0.4 water-cement ratio is the highest. All concrete mixes were found to pass the Strength Activity Index of 75% according to (ASTM C 618- 08).
Keywords: Compressive Strength, Tensile strength, Workability, Concrete, Coconut shell ash, Cement
INTRODUCTION
The application of concrete material in construction industry were highly demand which growing rapidly demonstrate the need for various types and properties of concrete to meet the diverse needs of the user (Alwi,2009). This, coupled with the pollution associated with cement production, has necessitated a search for an alternative binder which can be used sorely or in partial replacement of cement in concrete production.
A considerable amount of coconut shells remains in the environment as waste, so utilization of these materials for construction will be an important step to improve
sustainability and eco-friendly construction. The concrete even releases huge amount of CO2 into atmosphere and to reduce that we have partially replaced with coconut shell ash.
More so, disposal of agricultural waste materials such as rice husk, groundnut husk, corn cob and coconut shell have constituted an environmental challenge, hence the need to convert them into useful materials to minimize their negative effect on the environment (Habeeeb and Mahmud, 2010).
Coconut shells have good durability characteristics, high toughness and abrasion resistant properties; it is suitable for long standing use. Coconut shells are mostly used as an ornament, making fancy items, house hold utensils, and as a source of activated carbon from its charcoal. The powdered shell is also used in the industries of plastics, glues, and abrasive materials and it is widely used for the manufacture of insect repellent in the form of mosquito coils and in agarbathis.
According to FAO statistics (Food and Agriculture Organization) 2007, global production of coconuts was
61.5 MT with Indonesia, Philippines, India, Brazil and Sri Lanka as the major contributors to coconut production. The total world coconut area was estimated as approximately 12 million hectares and around 93 percent is found in the Asian and Pacific region. The average annual production of coconut was estimated to be 10 million metric tons of copra equivalents. Of the world production of coconut, more than 50 percent is processed into copra. While a small portion is converted into desiccated coconut 5 and other edible kernel products, the rest is consumed as fresh nuts. Also, the mass ratio of water-to-cement content is one of the most fundamental parameters in concrete mixture proportioning. The w/c ratio has a significant influence on most properties of hardened concrete in particular strength and durability due to its relationship with the amount of residual space i.e. capillary porosity, in the cement paste.
REVIEWED LITERATURES:
(Utsev and Taku ,2012) carried out research on Coconut shell ash as partial replacement of ordinary portland cement in concrete production. Author has produced concrete cubes using various replacement levels between 0 to 30 percentage of OPC with CSA. He has casted total 54 cubes and cured by immersing them in water for 7, 14 and
28 days respectively. Compressive strength, Density, setting times and pozzolanic activity index were determined. He has concluded that the densities of concrete
cubes for 10-15% replacement was above 2400Kg/m3 and the compressive strength increased from 12.45N/mm2 at 7days to 31.78N/mm2 at 28 days curing which meets the requirement for use in both heavy weight and light weight concreting. Thus, 10 -15% replacement of OPC with CSA is recommended for both heavy weight and light weight concrete production.
(Tarun et al., 2014) carried out study on Effect of strength of concrete by partial replacement of cement with flyash and addition of steel fibres. Steel fibres having aspect ratio 50 were used between 0 to 2%. Author has replaced cement by 40% & 60% of Class F fly ash. All the results obtained were compared and examined with respect to the control specimen. Author has noticed that due to the addition of steel fibre in concrete, it enhances its overall strength especially the flexural and split tensile strength. Author has concluded that, the 40% and 2% are the optimum percentages of adding flyash & steel fibres respectively which showed the maximum improvement in tensile and flexural strength.
(Oyedepo et al., 2015) carried out an experimental research on Performance of coconut shell ash and palm kernel shell ash as partial replacement for cement in concrete. Using a mix design ratio of 1:2:4 and water binder ratio of 0.63, concrete cubes were casted using varying ordinary Portland cement (OPC): palm kernel shell ash (PKSA) and ordinary Portland cement (OPC): coconut shell ash (CSA) ratios of 100:0, 90:10, 80:20, 70:30 , 60:40 and 50:50 respectively. Author has noticed that the partial replacement of cement with 20% PKSA and CSA in concrete gives an average optimum compressive strength of 15.4 N/mm2 and 17.26 N/mm2 respectively at 28 days. While,10% replacement with CSA gives the optimum value of compressive strength which is 20.58 N/mm2 at 28 days. Such strength is suitable for both light weight and heavy weight concrete respectively. Thus, the researcher has concluded that the use of PKSA and CSA as a partial replacement for cement in concrete, at lower volume of replacement, will enhance the reduction of cement usage in concretes, thereby reducing the production cost and the environmental pollution caused by the dumping of the agricultural waste. (Neetesh et al., 2014) carried out research on Utilization of coconut shell in different forms in concrete. Replacement of cement by CSA in concrete showed that the density of concrete cubes for 10-15% replacement was above 2400 Kg/m3. This paper shows that at 30% replacement the average density decreases from 2525.5 Kg/m3 to 2314 Kg/m3. The achieved value of compressive strength meets the requirement for use in both heavy weight and light weight concreting. With the increase in the amount of CSA, the setting time also increases. The initial setting time increases from 1 hr 5 min at 0% replacement to 3 hrs 26 min at 30% replacement while the final setting time increases from 1 hr 26 min at 0% replacement to 4 hrs 22 min at 30% replacement. Author has also noticed that with increasing percentage replacement of OPC with CSA, the pozzolanic activity index decreases and the compressive strength decreases with increasing percentage replacement of OPC with CSA. 10% replacement gives the optimal- 28days-strength-for-OPC-CSA-mix-which-is-31.78N/mm2.
(Sanjay and Rajeev,2015) carried out the study on Effect of coconut fibre ash on strength properties of concrete. Coconut fibres are collected and the fibre are properly dried and burnt in the open air with a temperature range of 600c to 700c. Author has collected the ash and made to pass through 150-micron sieve after the fibres turned into the ash. Replacement is done between 0 to 25% & the cubes are tested at 7, 28, 60, & 90 days. Paper shows that the workability of the concrete decreased as the CFA content increased & the compressive strength of CFA concrete increased with curing aging but decrease with increasing the percentage of coconut fibre ash. Author has concluded that the optimum compressive strength of 59.25N/mm2 was obtained at 5% replacement at 90 days of ages.
From economic, technological and ecological points of view, cement has an undisputed role to play in the future of the construction industry. Therefore, the variation in cement characteristics and their effects on concrete properties had been a major area of research in concrete technology for last two decades, it is observed that, a very limited work has been carried out in the arena of difference effect of water-cement(w/c) and water-binder (w/b) ratio on engineering properties of concrete. In this scenario, the present investigation has focused to study the effect of water/cement ratio on some engineering properties of coconut shell ash concrete.
The objectives of this project are:
-
To determine the water w/c ratio, testing different concrete cubes and cylinders with and without coconut ash ranging from 0.4-0.5-0.6 percent using 1:1.5:3 mix proportion.
-
Investigating the mix ratio of concrete by partially replacing cement with pozzolana (coconut ash). From a control of 0% natural pozzolana content, then increasing the natural pozzolana content to 10%.
-
Testing for compressive strength of concrete containing pozzolana at 7 days, 14 days, 28 days, 45 days and 90 days in accordance with ASTM C- 109.
MATERIALS AND METHODS
The materials used for the project consists of the following namely
Coconut shell ash(CSA): this was obtained locally in Badagry, Lagos state. The coconut shell was sun dried for forty-eight hours to remove moisture from it. It was then subjected to uncontrolled combustion using open air burning for three hours and allowed to cool for about 12hours. The burnt ash was collected and sieved through a BS sieve (75 microns). The resulting ash, which has the required fineness, was collected for use.
The chemical analysis of the CSA and the cement used was also determined using X-Ray fluorescence (XRF) spectrometer to evaluate for possible pozzolanic activity and classification of the CSA (see Table1).
Cement: Dangote cement, a brand of ordinary Portland cement available locally in Nigeria was used.
Water: The water used was obtained from the laboratory taps (Civil engineering laboratory, University of Lagos) was used both for the mixing of concrete as well as in curing of the cubes. These mixes were proportioned to have cement replacements in the range of 0 and 10 percent by weight. For each percentage, water to cement ratio was varied between 0.4 – 0.6, in steps of 0.1.
The work investigated the physical properties, setting time of cement paste, workability, pozzolanic activity index, compressive and tensile strength of concrete elements with cement partially replaced with C.S.A. 90 Nos. 150x150x150mm concrete cubes and 60 Nos. 150 x 300mm cylinder specimens were produced and cured by water immersion for 7, 14, 28, 45, 90 days respectively. The mix ratio of 1:1.5:3 (Cement: Fine aggregate: Coarse aggregate).
The density and strength with respects to their controls and w/c ratios result are presented in tables below.
DISCUSSION OF RESULTS
Physical and Chemical of CSA
Table 1 presents the physical and chemical properties and oxide content of CSA and cement used. CSA has higher silica of 66.32% compared to cement with 15.99%. This shows that the mixture has enough silica which could lead to better strength development at later age. According to (ASTM C618-15), a pozzolan is of Class N if the sum of SiO2, Al2O3, and Fe2O3 is greater than 70%, SO content is less than 4% and when LoI is less than 10%. The measure of pozzolanic activity is confirmed by the Strength Activity Index (SAI),
Table 1: Showing the Cementitious properties of substance
OXIDES PRESENT
COCONUT SHELL ASH(CSA) %
DANGOTE CEMENT 42.5N
%
SiO2
66.32
15.99
Al2O3
8.79
4.60
Fe2O3
5.35
2.87
CaO
6.25
58.86
MgO
0.87
2.15
P2O5
0.51
0.36
K2O
3.26
0.26
SO3
0.69
0.22
TiO3
0.83
0.24
Mn2O3
0.12
0.05
SiO2+ Al2O3+ Fe2O3
80.64
–
LOI
4.28
9.63
Setting Time
This means that The setting times increases with increase in the amount of coconut shell ash. The initial setting time increases from 1 hour 40minutes at 0% replacement to 2 hours at 10% replacement while the final setting time increases from 3 hour 20 minutes at 0% replacement to 4 hours 20 minutes at 10% replacement. However, BS12
(1978) recommends initials and final setting times to be not more than 45 minutes and 10 hours respectively of which the CSA/OPC pastes passes in final setting time.
Physical Properties of Aggregates
From table 3, it shows the physical properties of aggregates. The fine and coarse aggregates had uniformity coefficients (Cu) of 3.69 & 1.5 respectively while they had a coefficient of curvature (Cc) of 1.2 & 1.04 respectively. For the coarse aggregate, it was also observed that 96.95% of the aggregate was retained on the 5mm sieve and 3.05% passed through the sieve. According to Unified Soil Classification, the fine aggregates is classified as gap- graded medium to coarse sand while the coarse aggregates are gap-graded granite. Also, there is slight a distinct difference in the granite and sand used in this investigation. The granite and sand recorded bulk density values of 1350.33 kg/m3 and 1393.37 kg/m3 respectively, indicating that the sand was 3.09 % lighter than granite. The specific gravity of the sand and granite were 2.65 and 3.28 respectively. The aggregate crushing value of the aggregates was done to determine their relatve resistance to crushing under a gradually applied compressive load. From the analysis, ACV for granite was found to be 20.83%.
PARTICLE SIZE DISTRIBUTION
OF AGGREGATES
100
80
60
PARTICLE SIZE DISTRIBUTION
OF AGGREGATES
100
80
60
Table 3: Physical Properties of Aggregates
Physical Property
Sand
Granite
Uniformity Coefficient (Cu)
3.68
1.5
Coefficient of Curvature (Cc)
1.2
1.04
Specify Gravity
2.65
3.28
Dry Density (Kg/m3)
805.41
828.43
Bulk Density ((Kg/m3)
1393.37
1350.33
Moisture Content (%)
0.73
0.63
Aggregate Crushing Value (%)
–
20.83
40
40
GRANITE
GRANITE
20
20
SAND
SAND
0
0 . 0 1
0
0 . 0 1
1
GRAIN SIZE (MM)
1
GRAIN SIZE (MM)
100
100
PERCENTAGE PASSING (%)
PERCENTAGE PASSING (%)
Figure 1: Particle Size Distributions for Aggregates
The results of Sieve Analysis tests on the concrete constituent materials show the following trends (fig 1): The fine and coarse aggregates had uniformity coefficients (Cu) of 3.69 & 1.5 respectively while they had a coefficient of
curvature (Cc) of 1.2 & 1.04 respectively. For the coarse aggregate, it was also observed that 96.95% of the aggregate was retained on the 5mm sieve and 3.05% passed through the sieve. According to Unified Soil Classification, the fine aggregates is classified as gap- graded medium to coarse sand while the coarse aggregates are gap-graded granite.
SLUMP TEST
Table 4, shows the slump values and the effect of CSA on degree of workability. The workability of the fresh concrete, as determined by the slump test in accordance with section 7.2 of BS 5328, for all the mix proportions with 0% and 10% of cement replaced with C.S.A at water/cement ratios of 0.4, 0.5 and 0.60 is presented in table 4.
Table 4: Slump Values and Degree of Workability
%Percentage Replacement
Water- Cement Ratio
Slump Value
Degree of Workability
0
0.4
54
Medium
0.5
59
Medium
0.6
90
Medium
10
0.4
52
Medium
0.5
55
Medium
0.6
85
Medium
Workability of water cement ratio
SLUMP (MM)
SLUMP (MM)
From the figure 2, it was observed that the workability increased as the water-cement ratio increased from 54 mm to 90 mm at 0.4 to 0.6 water-cement ratio for 0% percentage replacement and from 52 mm to 85 mm at 0.4 to 0.6 water-cement ratio for 10% percentage replacement. The result of the slump test showed that all of the mixes have medium degree of workability. It was observed that the workability reduced with increasing content of C.S.A for each water-cement ratio. This can only indicate a dehydrating effect of C.S.A as its content is increased.
VARIATION OF WORKAB I L I TY WITH WATER CEMENT RATI O
100
90
80
70 0% C.S.A
60 10% C.S.A
50
0 . 3 50 . 40 . 4 50 . 50 . 5 50 . 60 . 6 5
WATER- CEMENT RATIO
VARIATION OF WORKAB I L I TY WITH WATER CEMENT RATI O
100
90
80
70 0% C.S.A
60 10% C.S.A
50
0 . 3 50 . 40 . 4 50 . 50 . 5 50 . 60 . 6 5
WATER- CEMENT RATIO
Figure 2: Variation of Workability with water cement ratio for each percentage replacement
Compressive Strength
The compressive strength decreases with increasing percentage replacement of OPC with CSA. It is observed
that at 28-day curing age, the control, having 0% C.S.A inclusion specimens decreased by 7.24% when compared with 10% replacement of cement with C.S.A for 0.4 water- cement ratio. These values are 10.08% and 19.33% for water cement ratios of 0.5 and 0.6 respectively. From figure 3, a linearly inverse relationship was observed between the water-cement ratio and compressive strength for each percentage replacement. For the 0% percentage replacement, the 28-day compressive strength for 0.6 water-cement ratio increased by 11.83% when compared with the 28-day compressive strength for 0.5 water-cement ratio. This value is 1.5% when comparing the 0.5 and 0.4 water-cement ratios. For the 10% percentage replacement, these values are 26.21% increase for the 0.6 and 0.5 water- cement ratios and 3.58% increase for 0.5 and 0.4 water- cement ratios. This is an indication that increasing the water-cement ratio of any concrete will decrease compressive strength. The general trend shows the strength value decreases as the percentage replacement increases from control to 10% replacement. This is an indication that, the substitution of cement with C.S.A beyond the 10% replacement level is not recommended for use in heavy loaded structure.
V A R I A T I O N O F C O M P R E S S I V E
S T R E N G T H W I T H P E R C E N T A G E R E P L A C E M E N T A N D W A T E R –
C E M E N T R A T I O
V A R I A T I O N O F C O M P R E S S I V E
S T R E N G T H W I T H P E R C E N T A G E R E P L A C E M E N T A N D W A T E R –
C E M E N T R A T I O
40
35
30
25
20
15
10
5
0
40
35
30
25
20
15
10
5
0
7 days
14 days
28 days
45 days
90 days
7 days
14 days
28 days
45 days
90 days
PERCENTAGE REPLACEMENT-W/C RATIO
PERCENTAGE REPLACEMENT-W/C RATIO
MPRESSIVE STRENGTH (N/MM2)
MPRESSIVE STRENGTH (N/MM2)
Figure 3:Variation of Compressive Strength (N/mm2) with Percentage Replacement of C.S.A
It was also observed that for every percentage replacement, there is an increasing trend in the compressive strength due to the effect of the curing age. From Fig 4, the strength values increased as the curing ages increase progressively. This shows the effect of water in the development of strength in normal concrete.
VARIATIO N O F
CO M PRESSIVE STRENGTH WITH CURING AGE
35
15
VARIATIO N O F
CO M PRESSIVE STRENGTH WITH CURING AGE
35
15
-5 0
-5 0
7 14 21 28 35 42 49 56 63 70 77 84 91
CURING AGES (DAYS)
7 14 21 28 35 42 49 56 63 70 77 84 91
CURING AGES (DAYS)
0%-0.4 W/C
0%-0.4 W/C
0%-0.5 W/C
0%-0.5 W/C
0%-0.6 W/C 10%-0.4 W/C
10%-0.5 W/C 10%-0.6 W/C
0%-0.6 W/C 10%-0.4 W/C
10%-0.5 W/C 10%-0.6 W/C
VARIATION OF TENSILE
STRENGTH WITH PERCENTAGE REPLACEMENT AND W/ C RATIO
VARIATION OF TENSILE
STRENGTH WITH PERCENTAGE REPLACEMENT AND W/ C RATIO
Water-Cement Ratio
14
45
Water-Cement Ratio
14
45
7
28
90
7
28
90
Linear (7)
10
5
0
0 . 4 0 . 5 0 . 6 0 . 4 0 . 5 0 . 6
PERCENTAGE REPLACEMENT-W/C RATIO
Linear (7)
10
5
0
0 . 4 0 . 5 0 . 6 0 . 4 0 . 5 0 . 6
PERCENTAGE REPLACEMENT-W/C RATIO
COMPRESSIVE STRENGTH
(N/MM2)
COMPRESSIVE STRENGTH
(N/MM2)
RENGTH (N/MM^2)
RENGTH (N/MM^2)
Figure 4: Variation of Compressive Strength (N/mm2) with Curing ages(days)
The index decreases with increasing percentage replacement of OPC with CSA. All 10% percentage replacement of cement specimens at all water-cement ratios met the minimum permissible 75% suggesting pozzolanic activity occurring during all the period. The maximum SAIs for 0.4 water-cement ratio is 91.79 % (at 28 days). This value is 93.92 % (at 7 days) and 81.82% (at 7 days) for 0.5 and 0.6 water-cement ratios respectively. This signifies that up to 10% replacement could be adopted as optimum replacement levels of cement with C.S.A for normal concrete production.
TENSILE STRENGTH
From figure 5, It was observed that for each percentage replacement, there is variation in the tensile strength. The 28-day tensile strength reduced from 5.83 N/mm2to 3.89 N/mm2as water cement ratio increases from 0.4 to 0.6 for the control. The reduction was from 5.22 N/mm2 to 3.22 N/mm2 for 10% replacement of cement with C.S.A. The 28-day tensile strength increased by 15.66% when comparing the 0.6 and 0.5 water-cement ratios and by 20.95% when comparing the 0.5 and 0.4 water-cement ratios. These values are 22.67% and 20.21% respectively for the 10% replacement of cement with C.S.A.
Figure 5, the tensile strength of the control (0% C.S.A) was found to reduced when compared to the tensile strength at 10% replacement of cement with C.S.A for all water cement ratios.
Figure 5:Variation of Tensile Strength (N/mm2) with Percentage Replacement of C.S.A
7
6
5
4
3
2
1
0
7
6
5
4
3
2
1
0
0%-0.4 W/C
0%-0.5W/C
0%-0.6 W/C
0%-0.4 W/C
0%-0.5W/C
0%-0.6 W/C
TENSILE STRENGTH(N/MM^2)
TENSILE STRENGTH(N/MM^2)
From Fig 6, as curing age increases from 0 to 90 days, a gradual increase in tensile strength was observed. The general trend shows a linear relationship between the curing ages and the tensile strength and it was uniform for all percentage replacement along its curing ages.
VARIATION OF COMPRESSIVE
STRENGTH WITH CURING AGE
VARIATION OF COMPRESSIVE
STRENGTH WITH CURING AGE
10%-0.4 W/C
10%-0.5 W/C
0
10%-0.4 W/C
10%-0.5 W/C
0
50
CURING AGE
50
CURING AGE
100
100
10%-0.6 W/C
10%-0.6 W/C
Figure 6: Variation of Tensile Strength (N/mm2) with Curing Age
CONCLUSION
-
Coconut shell ash was found to be pozzolanic based on its chemical compositions and therefore can be used as supplementary cementitious material.
-
The results of Sieve Analysis tests on the concrete constituents materials gave the following results. The fine and coarse aggregates had uniformity coefficients (Cu) of 3.68 & 1.5 respectively and coefficient of curvature (Cc) of 1.2 & 1.04 respectively, and according to Unified Soil Classification they are classified as gap-graded medium to coarse sand and gap-graded granite respectively.
-
The characteristic compressive strength of 34.07 N/mm2 of the 0% replacement and 0.4 water- cement ratio is the highest.
-
C.S.A was found to have a lesser ability to resist crushing which is a fundamental reason why there is a decline in the compressive strength value.
-
The Slump test results on concrete showed that the workability decreased as the content of C.S.A increased from 90mm to 85mm at 0% to 10% replacement of cement with C.S.A. There is decrease in workability as a result of the weight property of C.S.A. is low compared to cement.
-
The characteristic tensile strength of 5.83 N/mm2 of the 0% replacement and 0.4 water-cement ratio is the highest at 28 days.
-
C.S.A can be successfully used only as partial replacement and never as total replacement of cement in concrete production for non-structural applications.
-
For every percentage, the compressive strength of the concrete increases from a minimum at a curing age of 7 days to a maximum at 90 days.
-
REFERENCES
-
Alwi, W. A. B. W. 2009 (Strength And Endurance Lightweight Foamed Concrete For Structural Materials).
-
Habeeeb, G. A and Mahmud, H. B. (2010): Study on properties of RHA and its use as cement replacement material. Materials Research Journal, 13(2): 185-190
-
Utsev, J. T., Taku, J. K. ,Coconut Shell Ash As Partial Replacement of Ordinary Portland Cement In Concrete ProductionInternational Journal Of Scientific & Technology Research Volume 1, Issue 8,September 2012
-
Tarun Sama, Dilip Lalwani, Ayush Shukla, Sofi A., Effect of Strength of Concrete by Partial Replacement of Cement with Flyash and addition of Steel Fibres, Journal of Civil Engineering and Environmental Technology, Volume 1, Number 1; August, 2014.
-
Oyedepo OJ , Olanitori LM and Akande SP, Performance of coconut shell ash and palm kernel shell ash as partial replacement for cement in concrete, J.Build. Mater. Struct. (2015) 2: 18-24
-
Neetesh Kumar, Dilip Kumar, Utilization of Coconut Shell in Different Forms in Concrete, IJSRD – International Journal for Scientific Research & Development| Vol. 2, Issue 07, 2014.
-
Sanjay Sen, Rajeev Chandak , Effect of coconut fibre ash on strength properties of concrete Int. Journal of Engineering Research and Applications, Vol. 5, Issue 4, ( Part -1) April 2015, pp.33 -35.
-
ASTMC618-15, Standard Specification for Coal FlyAsh and Raw or Calcined Natural Pozzolan for Use in Concrete, ASTM International, West Conshohocken, PA,2015 www.astm.org.
-
BS 3892 (1982): Specification for pulverized fuel ash for use as a cementitious compound in structural concrete, BSI, Gaylard & Sons, London.
-
BS EN 206 1 (2000): Concrete Specification, Performance, production and conformity, BSI, Gaylard & sons, London.