
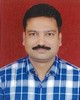
- Open Access
- Authors : Nitin S N
- Paper ID : IJERTV10IS110104
- Volume & Issue : Volume 10, Issue 11 (November 2021)
- Published (First Online): 15-12-2021
- ISSN (Online) : 2278-0181
- Publisher Name : IJERT
- License:
This work is licensed under a Creative Commons Attribution 4.0 International License
Digital EBHS Analysis
Nitin Nandimath
ER & D
Tata Technologies.Ltd Pune, India
Abstract The comfort of good NVH is one of the strongest brand differentiators. So good NVH performance is needed for Luxury vehicles: while for others, any edges they can gain over competitors will pay back handsomely in brand equity and loyalty.
EBHS stands for Equivalent Body hole size. It is one of the measure of vehicle NVH and climate control performance.
The complete vehicle has to protect the occupants from external elements (Water/air/Noise/Vibrations etc) and also should provide comforts with the help of HVAC, Seats, Trims and various sealing solutions.
KeywordsEBHS, NVH,Air,Water,Noise
-
BACKGROUND
The tyre/road interface causes airborne sound radiation from the contact zone as well as from the surfaces of the vibrating tyre. It also causes structure borne source transmitted as forces from the wheel into the suspension. The car engine also has both source components. Also Body panels has holes, cutouts, CED holes, air escape holes, mounting holes. If these holes are not plugged these become source of poor EBHS. Due to the ever increasing complexity of the body-in-white (BIW), it is a very challenging exercise to understand how noise propagates through the labyrinth of the vehicles structure. Today, acoustic engineers perform ultrasound or smoke tests to identify these noise paths. However, this is only feasible late in the development process once prototypes are available, and moreover, the physical tests do not tell anything about the actual trajectory of these noise paths nor how to block them in the optimal way
Key points
-
Need of Digital Analysis – Body shell baffle location Digital Analysis for sealing of Air bourn & Acoustic leakage.
-
Preparation of single sealing surface cad data with reference to latest released 60R cad data.
-
Review the sealing surface by taking various sections & checking for continuity of panel section.
-
Where ever the continuity is disconnected then check the same location in other sections for discontinuity, if yes then it is identified as potential leakage.
Overall noise level in DBA Articulation Index-and thus Sound Quality of In-cab noise with the acoustic package including Baffles in BIW should be in line with the vehicle level benchmark database – this target will be achieved by both the supplier and customer with care taken that body is well sealed [EBHS of the vehicle Cab is
< 50 cm²] and there is less structure-borne noise. Sound transmission is hence a very
II METHODOLOGY DETAILS
Overall noise level in DBA Articulation Index-and thus Sound Quality of In-cab noise with the acoustic package including Baffles in BIW should be in line with the vehicle level benchmark database – this target will be achieved by both the supplier and customer with care taken that body is well sealed [EBHS of the vehicle Cab is < 50 cm²] and there is less structure-borne noise. Sound transmission is hence a very complex problem with multiple aspects and of mixed air- and structure borne nature. It is hard to make a general split in frequency ranges between air- and structure borne transmission, it depends very much on the concrete application, but for car interior noise, the transmission path below 500Hz is dominantly structure borne and above 800Hz
it is mainly airborne (but small components may vibrate and radiate at higher frequencies and large cavities may have important airborne components at lower frequencies. Identifying all potential air-borne noise paths between the passenger compartment and the vehicle's exterior. Furthermore, it allows the engineer to improve the acoustic isolation by suppressing individual noise paths (using virtual plugs and sealants) using CAD data only.
Vol. 10 Issue 11, November-2021
Upper body panels forming
Traditionally, the first detection of environmental leakages into and from cabin have been dependent on physical prototypes
-
-
DESIGN FOR SEALING AND QUALITY ASSURANCE PROCESS
A design process is developed to address cabin sealing & corrosion protection issues at design concept development stage. The process is based on a design approach of defining and continuously updating the collection of parts that form a strategic sealing barrier. Definition of a strategic sealing barrier enables virtual EBHS evaluation of nominal CAD assuming idealized sealants.
Concept of body shell sealing surface
Under body panels forming
Sealing Surface for SUV Category
Detection: Idealization of cabin sealing surface in CAD & checking of each & every opening for sealing design.
Correction: Physical verification of cabin sealing effectiveness by EBHS test. Troubleshooting for leak detection with reference to idealized cabin sealing surface.
The EBHS performance is improved drastically post Digital EBHS Analysis.
The EBHS value before digital EBHS analysis process
EBHS values post digital EBHS analysis process (Hatchback, sub4 meter, CUV)
The EBHS performance is improved drastically post digital EBHS analysis.
EBHS values before digital EBHS analysis process (Hatchback, sub4 meter, CUV)
IV EBHS Performance Automotive Trend
Car cabin Sealing POC- 1
V IMPROVEMENTS OF METHODOLOGY
-
Identification of air leakage paths in early stage of project is possible and can relate physical test.
-
We can analyses the leakages in cad stage only, which can be iterated many times
-
Potential leakage path analyses is done in cad review and solution can identify such as plug, expandable tape or baffle in cad data phase itself.
-
The time required to meet pat target for EBHS is lesser in time if compared with physical test.
-
Quick response for solution can be generated & physical test can be done for confirmation.
-
Identifying all potential air-borne noise paths between the passenger compartment and the vehicle's exterior.
-
Can avoid the uses of costly solutions during vehicle launch to tackle issues related to sealing requirement.
-
Digital audits for signoff & quality assurance by check sheets.
-
Increased customer comfort and quality perception during vehicle usage.