
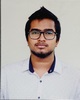
- Open Access
- Authors : Rojith M. Nair , Anway M. Pawar , Abhishek V. Yenpure , Purva B. Todmal, Dr. Vikas R. Deulgoankar, Anand Bhise
- Paper ID : IJERTV10IS100186
- Volume & Issue : Volume 10, Issue 10 (October 2021)
- Published (First Online): 03-11-2021
- ISSN (Online) : 2278-0181
- Publisher Name : IJERT
- License:
This work is licensed under a Creative Commons Attribution 4.0 International License
Development and Finite Element Analysis of Heavy Duty Sorting Conveyor for Agriculture Application
Dr. Vikas R. Deulgoankar
Dean ( student affairs) & Associate professor Department of Mechanical Engineering, MMCOE, Pune
Rojith M. Nair
Department of Mechanical Engineering, MMCOE, Pune
Anway M. Pawar
Depatment of Mechanical Engineering, MMCOE, Pune
Abhishek V. Yenpure
Department of Mechanical Engineering, MMCOE, Pune
Purva B. Todmal
Department of Mechanical Engineering, MMCOE, Pune
Anand Bhise
Director, Mechatol Product Engineering solution pvt. Ltd
Abstract The present work deals with design development and finite element analysis of conveyor system useful for grading and separation of tomatoes for farming applications. A two-stage conveyor that separates tomatoes based on grade and size has been designed. This separation improves the financial yield of the farmers. Material selection of the conveyor components has been carried out using Ashby Charts. Computer aided models of components are prepared using SolidWorks software. Solid modelling has been carried out considering dimensional aspects. Finite element analysis has been carried out using ANSYS Software. Static and modal analysis of the conveyor components has been carried out. Stresses obtained from static analysis are in close correlation with the available literature. Natural frequencies are devised from free vibration modal analysis. Mass participation factor evaluations for base and trolley frames are presented in this work. Present conveyor design shows improvement in performance over traditional ones.
KeywordsRoller conveyor, finite element analysis, modal analysis, material selection
-
INTRODUCTION
With the advent wheel, humans have been immensely benefited. The growth in all sectors was impacted immensely in production and financial aspects. Industrial revolutions that started between 1830 to 1840 were accelerated due to this invention. Industries that possessed land in acres or hectors for operation, employed labor for transfer of material from one place to another with the working site. This consumed considerable time and consequently affect production rate. The development of conveyor system began in 1892 for transfer and handling of material within the industrial unit. The conveyor system saved substantial amount of time and effort and enhanced the production rate. For industries with hazardous environments the conveyor systems resulted into reduction of workplace risks. Different stages of conveyor development and gradual change in design as needed has resulted into the systems that are available today. A conveyor can be designed for a specific product or material handling purpose. The conveyor systems are classified as flat belt,
troughed belt and magnetic belt conveyors, gravity roller conveyor and powered roller conveyor, wheel, chain, and slat conveyors.
In present work design, development, and finite element analysis a powered roller chain conveyor for tomato separation unit has been carried out. The design has been carried out with the use of Conveyor Equipment Manufacturing Association (CEMA) standard. The design phase includes material selection with the use of Ashby charts, evaluation of component dimensions with the failure of theories and simulation of the component behavior using finite element analysis technique. Components of the present system include feeding & rejection conveyors, base & trolley frames, drive rollers, motors, frames supported on castor wheels, plates, take-up assembly and trays. The roller assembly includes a roller guide passing through the roller and is attached to the angle sections mounted on chain which rotates the entire assembly. The frames and frame components are secured using bolted joints. Overall length of the assembly is 7000mm and the load carrying capacity is 2000kg. Self-weight of the entire conveyor assembly is 2224 kg. The conveyor is powered with the use of a chain drive mechanism wherein the sprockets are mounted on both the ends and are coupled with a single continuous roller chain. Sorting operation of farm yield i.e., tomatoes occur with respect to their sizes. When the feed conveyor is loaded with tomatoes, first stage sorting occurs at this instant itself. The pitch of rollers on first stage feeder is 38 mm, hence tomatoes of diameter smaller than 38mm are unable to continue their journey and pass through this gap and are collected at the bottom. The tomatoes of larger diameter that remain on the conveyor during first stage are carried upward to the for second stage sorting. The roller pitch in second stage is 47 mm, and hence tomatoes with size of 47mm or larger will be sorted for further packing and tomatoes of smaller size are collected in the tray attached to the trolley frame. The present system has been designed to be semiautomatic and hence manual intervention is needed to remove the tomatoes collected at the base and trolley frames.
-
MATERIAL SELECTION, CAD MODELING AND FINITE ELEMENT ANALYSIS OF CONVEYOR SYSTEM
Material selection in present work has been carried out using Ashby charts. Material conforming to the component performance under stipulated loads has been selected. Adopting the material selection process from Ashby charts, material for shaft, frames and rollers has been selected. Performance index (for strength) is of paramount importance in material selection and hence material with highest performance index has been selected. In present application the drive shaft is subjected to a combination of transverse load and torque. The load magnitude is 6.67kN and torque magnitude is 95N-m. Permissible deflection for this load- torque combination is the deciding factor for the material selection and hence Youngs Modulus Verses Density chart has is opted for selection of material for shaft. In similar manner for frame Strength Verses Density chart has been used. For chain selection IWIS standard has been adopted.
Computer aided model of the conveyor system has been prepared using SolidWorks software. Accounting for geometry of individual components, solid models of individual components has been prepared. These solid models are further given constraints of orientation and alignment from assembly considerations. The computer aided model of conveyor system along with stage 1 & stage 2 rollers, input (feed) and output locations, base & trolley frames, castor wheels at the base, take-up device and electric motor are shown in figure 1.
Fig. 1. Fabrication Drawing of conveyor system
Behavior simulation under stipulated loads for trolley frame, base frame, drive roller and shaft has been carried out using finite element analysis technique. The finite element analysis has been carried out using ANSYS software. In preprocessing stage, the STEP files of conveyor components are imported into S environment. The imported models were further verified for surface or geometry losses and other associated import errors. Meshing and application of boundary conditions & assigning of materials has been carried out in preprocessing stage. The trolley and base frames are meshed using beam elements. Total number of elements for trolley frame are 440 and nodes are 449, for base frame total elements are 496 and nodes are 506. Material selected for both the frames is SCM 435 has yield strength of 350 MPa and Poissons ratio of 0.29. All the six degrees of freedom of the nodes at the castor wheels
are arrested and load are imposed at the load locations on both the trolleys. On the base frame, a total downward force of 2527 N has been applied equally distributed over 14 different locations on top members. The CAD and meshed models of base frame are shown in figure 2.
Fig. 2. Computer aided and meshed models of base frame
The finite element model of base frame with loads and constraints and the solved model is shown in figure 3
Fig. 3. Base frame model with boundary conditions and stress plot
For trolley frame the material properties are same as those of base frame, difference being the magnitude of load applied and the number of load locations. The load magnitude of 20050 N has been applied at 30 different locations distributed equally at the load locations on trolley frame. The computer aided and meshed model of trolley frame is shown in figure 4.
Fig. 4. Computer aided and meshed model of trolley frame
The constraints are applied at the base nodes at castor wheels. All the six degrees of freedom are arrested to simulate the physical situation. The model of trolley frame with boundary conditions and stress plot is shown in figure 5.
Fig. 5. FE model of Trolley frame with boundary conditions and stress plot
The drive roller and shaft are meshed using ten nodes tetrahedral element. Total number of elements for drive roller
are 9151 and nodes are 18327 while for the shaft total elements are 8151 and nodes are 13591. Material for drive roller is plain carbon steel with yield strength of 220 MPa and corresponding Poissons ratio is 0.28. Material for the drive shaft is EN24 with yield strength of 470MPa and corresponding Poissons ratio of 0.285. The computer aided and meshed model of drive roller is shown in figure 6.
Fig. 6. Computer aided and meshed model of drive roller
The rollers are attached using bolted joints to the frames. At both the extreme ends of the roller fixed support constraint is applied which correlates with physical situation of roller fitment. A force of 2420 N has been applied on the entire roller. The finite element model of roller with boundary conditions and stress plot is shown in figure 7. Results of finite element analysis of shaft are mentioned in the succeeding section of results and discussion, however the models of same are avoided.
Fig. 7. FE model with boundary conditions and stress plot
To predict the vibrational traits of base and trolley frames, free vibrational modal analysis has been carried out. For both the frames four mode shapes and corresponding amplitude displacement with associated frequency has been analyzed.
Figure 8 shows the first two mode shapes while figure 9 depicts the third and fourth mode shapes of base frame. Figure 10 and figure 11 shows the 1st& 2nd and 3rd and 4th mode shape for trolley frame, respectively.
Fig. 8. Mode shape 1st and 2nd for base frame
Fig. 9. Mode shape 3rd and 4th for base frame
Fig. 10. Mode shape 1st and 2nd for trolley frame
Fig. 11. Mode shape 3rd and 4th for trolley frame
-
RESULT AND DISCUSSION
The finite element analysis of the conveyor components has been carried out to simulate their behavior under stipulated load conditions. From finite element analysis stress, displacements and factor of safety shaft, drive roller, trolley frame and base frame are evaluated. These outcomes are summarized in table 1.
Table 1. Summary of finite element analysis results
Component |
Factor of Safety |
Displacement (mm) |
Stress (MPa) |
Shaft |
2.49 |
0.795 |
189 |
Drive Roller |
1.866 |
1.1617 |
117.77 |
Base Frame |
2.32 |
0.8 |
95.2 |
Trolley Frame |
2.79 |
3.64 |
125 |
The maximum value of stress 189 MPa is observed in drive shaft which is attributed to the collective action of torque and uniformly distributed force on it, however corresponding factor of safety value is 2.49 that signify safety of shaft design. The stress value observed in trolley frame is 125 MPa and corresponding factor of safety value is 2.79. The stress value is far below the permissible stress value of 350 MPa. Maximum displacement is also observed in trolley frame. Additional stiffener plates are suggested to be welded to enhance the stiffness at the central portion.
From modal analysis the mode shapes and frequencies are evaluated. In addition to this, mass participation factors in X, Y and Z directions are devised for base and trolley frames. The mass participation factor signifies the amplitude of displacements corresponding to each mode shape. The magnitudes of mass participation factors in X and Z directions for base frame are negligible as compared with those in Y directions, while for trolley frame the magnitudes of mass participation factors are considerably increased however still their magnitude remains less than those in Y direction. The outcomes of modal analysis for base frame are summarized in table 2.
Table 2 Summary of modal analysis results for base frame
Base Frame |
Mass Participation (mm) |
Resultant Amplitude (mm) |
Frequency (Hz) |
Mode Shape1 |
0.427 |
0.182 |
63.501 |
Mode Shape2 |
0.0019113 |
0.116 |
80.8 |
Mode Shape3 |
2.23E-13 |
0.281 |
90.036 |
Mode Shape4 |
0.035163 |
0.284 |
116.79 |
The outcomes of modal analysis for trolley frame are summarized in table 3.
Table 3 Summary of modal analysis results for trolley frame
Trolley Frame |
Mass Participation Factor (mm) |
Resultant Amplitude (mm) |
Frequency (Hz) |
Mode Shape1 |
0.64482 |
0.132 |
29.372 |
Mode Shape2 |
0.0056179 |
0.226 |
44.803 |
Mode Shape3 |
0.00042365 |
0.141 |
51.833 |
Mode Shape4 |
0.0072574 |
0.146 |
57.311 |
. CONCLUSION
Following are the inferences drawn from the design and finite element analysis.
-
A two-stage sorting conveyor mechanism for grading of tomatoes based on sizes has been designed. This mechanism is helpful to grade the tomatoes based on size which will increase the income of tomato farmers, as tomatoes of same size are sorted.
-
Concrete base for material selection using Ashby charts for components of the conveyor has been established. The said conveyor is proposed to be manufactured as put into service.
-
The values of factor of safety and the magnitude of stresses induced in the shaft, drive rollers, trolley and base frames fall in safe zone.
-
From modal analysis of trolley and base frames, it is observed that the maximum frequency of 116.79 Hz occurs for fourth mode and corresponding displacement is 0.284mm for base frame. This is attributed to the position, orientation, and overall combination of base frame members.
-
For trolley frame, the maximum value of stress occurs at the bottom members. This indicates effective load transfer through every individual member
-
For drive roller, the maximum stress is observed in central portion which is attributed to the simply supported beam behavior of drive roller.
-
For base frame, the frontal tapered portion and corresponding members are subjected to stress. This is attributed to the geometry of the conveyor system. The stresses induced are within permissble limits.
REFERENCES
-
Deulgaonkar, V.R., Joshi, K., Jawale, P., Bhutada, S., and Fernandes, S. (2021). Failure Analysis of Timing Device Piston and Supply Pump Vanes in Fuel Injection Systems for Transport Utility Vehicles. Journal of Failure Analysis and Prevention, 21, 7, 172.
-
Deulgaonkar, V.R., Ingolikar, N., Borkar, A., Ghute, S., and Awate, N. (2021) Failure Analysis of Diesel Engine Piston in Transport Utility Vehicles, Engineering Failure Analysis, 120, 105008.
-
Deulgaonkar, V.R., Pawar, K., Kudle, P., Raverkar, A., and Raut,
-
(2019). Failure Analysis of Fuel Pumps Used for Diesel Engines in Transport Utility Vehicles. Engineering Failure Analysis, 105, 11, 1262.
-
-
Deulgaonkar, V. R., Kulkarni, M.S., Khedkar, S.S., Kharosekar, S.U., and Sadavarte, V.U.(2020). Self-weight and Durability Analysis of Bus Body Structure Using Finite Element Analysis. International Journal of Vehicle Structures and Systems. 12(3) 7, 101.
-
Deulgaonkar, V.R. (2020). Analysis of Auxiliary Structure Mounted on 8×8 Military Vehicle Chassis for Off-Road Logistics. International Journal of Vehicle Structures and Systems. 12(3) 7, 85.
-
Deulgaonkar, V.R., Kulkarni, M.S., Khedkar, S.S., Kharosekar, S.U., Sadavarte, V.U. (2020). Modal Analysis of Bus Body Structure Using Finite Element Analysis Technique,International Journal of Vehicle Structures and Systems. 12(3) 5, 96.
-
Deulgaonkar, V., Patil, M., and Patwardhan, V. (2020). Design and Drag Analysis of Fixed Wing Unmanned Aerial Vehicle for High Lift. International Journal of Vehicle Structures and Systems. 12(2) 6, 140.
-
Deulgaonkar, V.R., Shitole, V.A., and Panage, R.M. (2019). Design and Analysis of State Transport (S.T) Utility Vehicle ~ Bus., International Journal of Vehicle Structures and Systems., 11(2) 6,127.
-
Deulgaonkar, V.R. (2019). Analysis of Vibration Characteristics of Transport Utility Vehicle by Finite Element Method, International Journal of Vehicle Structures and Systems., 11(1) 5, 64.
-
Deulgaonkar, V.R. (2019). Finite Element Analysis of Chassis Integrated Structure for Tractor Trolley in Agricultural Applications. International Journal of Vehicle Structures and Systems, 11(1) 5, 69.
-
Deulgaonkar, V.R. (2018). Finite Element Analysis and Experimental Simulation of Chassis Mounted Platform for Off- road wheeled combat and transport utility vehicles. International Journal of Vehicle Structures and Systems, 10 (1) 7, 66
-
Deulgaonkar, V.R. (2016). Gradient Load Evaluation of Chassis Frame Mounted Specialized Structure Designed for Heavy Off- road Vehicles. International Journal of Vehicle Structures and Systems., 8(2) 5,586.
-
Deulgaonkar, V.R. (2016). Vibration Measurement and Spectral Analysis of Chassis Frame Mounted Structure for Off-road Wheeled Heavy Vehicles. International Journal of Vehicle Structures and Systems., 8(1) 5, 23.