
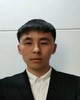
- Open Access
- Authors : Yongjie Cheng , Yanshuang Wang , Gaofeng Wang , Zijun Wang, Guanghui Zheng, Ximing Yuan, Dong Cheng, Wenbin Li
- Paper ID : IJERTV11IS120047
- Volume & Issue : Volume 11, Issue 12 (December 2022)
- Published (First Online): 21-12-2022
- ISSN (Online) : 2278-0181
- Publisher Name : IJERT
- License:
This work is licensed under a Creative Commons Attribution 4.0 International License
Determination of Optimum Oil Feeding for Intermediate Bearing
Yongjie Cheng1Yanshuang Wang1*, Gaofeng Wang2Zijun Wang2 Guanghui Zheng3Ximing Yuan3Dong Cheng4, Wenbin Li4
-
School of Mechanical Engineering, Qilu University of Technology (Shandong Academy of Sciences), Jinan 250353, China.
-
Luoyang Bearing Science and Technology Co. , Ltd. Luoyang 471039,China.
-
Shandong Golden Empire Precision Machinery Technology Co., LtdLiaocheng 252035, China.
-
Yantai Tiancheng Machinery Co., Ltd., Yantai 264006, China.
Abstract- Intermediate bearing heating model and convective heat transfer model between intermediate bearing and lubricating oil were set up. On this basis, the finite element model for heat analysis of intermediate bearing was established. The influence of the amount of supply oil on the temperature of the roller in contact with the inner and outer raceway is analyzed. And the optimum amount of supply oil, which is the amount of the supply oil when the location of the highest is temperature lowest, is obtained. The influences that the change of intermediate bearing radial force, rotating speed of inner ring and outer ring speed to the optimum amount of supply oil were analyzed. The results show that the optimum amount of supply oil of inter-shaft bearing is related to radial force, the rotating speed of the inner ring and outer ring speed and the oil temperature. And with the increase of them the optimum amount of feeding oil increases.
Keywords- The generation of heat, convective heat transfer, optimum oil feedin
-
INTRODUCTION
parts inside the bearing and the lubricant. On the other hand, it will also change the loss of viscous friction power of the bearing and the operating temperature of the bearing chamber. This paper mainly studies the optimum oil feeding when the maximum temperature of the intermediate bearing is the lowest, so as to facilitate the determination of the oil feeding of the intermediate bearing.
-
HEAT GENERATION MODEL OF THE INTERMEDIATE
BEARING
The power loss in the intermediate bearing due to friction slip between the internal parts is as follows:
-
Elastic hysteresis friction power loss.
When the bearing is in normal operation, the rolling body rolls on the inner and outer raceway under radial load, and the contact surface between the rolling body and the inner and outer raceway will produce elastic deformation. However, due to the elastic hysteresis of the material, the resistance moment of the pressure on the contact surface of the front half to the rolling body is greater than that of the rear half. Therefore, elastic hysteresis friction power loss is generated [9,10]:
With the increase of the working speed of the intermediate
=
bearing, a series of problems such as the sliding between the cage and the roller, the damage of the contact surface, and the instability of the cage are caused [1, 2, 3]. If effective lubrication and cooling cannot be obtained, the working temperature of the intermediate bearing will be too high, resulting in bearing failure. For example, the ring raceway and rolling element backfired or burned, and the cage guide surface is ablated et c. Affects engine performance [4, 5, 6 ]. The change in bearing temperature is not only related to its own
=1 (1)
Where: is the elastic lag friction moment; is the angular velocity of the rollers; is the number of rollers.
-
Sliding power loss between the roller and inner and outer rings.
When the bearing rotates at a certain speed, the linear speed on the contact surface between the roller and the inner and outer ring raceway may not be equal, resulting in relative sliding. The resulting power losses are:
heating, but also related to its own heat dissipation capacity [7,
1
= 00 +
(2)
8]. One of the main ways of bearing heat dissipation is to
transmit it to the bearing seat through the outer ring. The other is to transfer heat to the surrounding lubricating oil. The former is not easily changed due to its inherent structure. The second type is the convection heat transfer between the inside of the bearing and the surrounding lubricant.
When changing the amount of oil supplied, On the one hand, it will change the convection heat exchange between the
Where: is the roller shear stress between the roller and the inner and outer ring raceways; is the relative sliding speed between the roller and inner and outer ring; 2 + 1 is
the number of carrying rollers.
-
Friction power loss between roller and cage pocket.
When the bearing operates normally, there is a normal force between the roller and the cage pocket, and the rolling experience is in a free state in rare cases. Sliding friction power
loss due to interaction between rollers and cage pockets (Liu et al., 2020; Lu et al., 2021; Deng et al., 2017):
for specific heat exchanger surfaces: In the laminar flow:
1 1
=
2
[00 + 2 =1 + [ 2= 0.332
3 2 ( < 5 × 105) (9)
1] ] (3)
Where: is the sliding friction coefficient; is the
In the turbulence:
1
= (0.037 0.8 850) 3 (5 × 105 < < 107)
roller diameter; is the normal force between roller and cage pocket; is the normal force between roller and cage
(10)
Where: is Prandtl criterion, = is
pocket in the on-bearing area; is the rotation speed of the
Reynolds number = is the convection heat
roller in the non-load bearing area.
transfer coefficient; is
the
characteristic size; is the
-
Sliding friction power loss between cage pocket and guide ring.
The friction between the holder and the guide collar is:
( )
relative flow rate of the fluid relative to the heat transfer end
face; is the thermal conductivity; is the specific heat capacity; is the density; is the kinematic viscosity of the
fluid.
Its power loss is:
=
1
1 1
2
( = , ) (4)
When calculating the convection heat transfer coefficient of the inner rings of the intermediate bearing, = + , =
2
= 2 ( )( = , ) (5)
Where: is the dynamic viscosity of lubricating oil; = 1 = 1; 1 is the smaller of the diameter of the guide
surface of the cage pocket and the diameter of the guide surface
0 .25 .
2
When calculating the convection heat transfer coefficient
+
of the side guard; 2 is the larger of the diameter of the guide
surface of the cage pocket and the diameter of the guide surface
of the side guard; is the diameter of the guide surface of the cage pocket; is the width of the guide surface of the
between inner and outer rings of bearings, =
0 . 25 ( ) .
2
, =
2
cage pocket.
-
Viscous friction power loss.
In fluid-lubricated bearings, the rollers are subject to flow- around resistance when they rotate in a mixture filled with oil and gas lubrication. When the roller rotates around its axis, it will suffer the flow resistance moment of the fluid.
Where: and are bearing inner diameter and inner ring retainer diameter respectively; and are bearing
outer diameter and outer ring retainer diameter respectively.
When calculating the convection heat transfer coefficient on the raceway surface of inner and outer rings of the bearing,
Roller flow around resistance is:
2
= , =
0.07()
2
. ()
is the rotation angular velocity
= 8 ()
(6)
of the inner (outer) rings of the bearing.
Where: is the drag coefficient of flow around; is the density of oil gas mixture; is the length of roller; is the diameter of the bearing pitch circle; is the cage pocket
speed.
The loss of friction power is:
B. Convection heat transfer coefficient between cage pocket and inner and outer ring.
( )
= 0.175
(11)
=
(7)
2
(1+ )
The total power loss of the intermediate bearing is:
= + + + + (8)
-
-
CONVECTION HEAT TRANSFER SYSTEM BETWEEN THE
INTERIOR OF INTERMEDIATE BEARING AND LUBRICANT.
A. Calculating the convection heat transfer coefficient between the end face of bearing inner and outer rings and
Where: takes the inside diameter of the cage pocket
when calculating the convection heat exchange coefficient
between the inner ring and the outside diameter of the holder when calculating the convection heat transfer coefficient
between the outer ring; take the gap between the cage
pocket and the inner and outer rings respectively.
C. Convective heat transfer coefficient of roller surface.
the end face of intermediate bearing inner and outer rings and the raceway surface.
In the calculation, the model is simplified as the
convective heat transfer model when the fluid sweeps the flat
0.19(2 +)
=
( )
(12)
plate. Different feature sizes and Reynolds numbers are used
=
2 (13)
Where: is the surface temperature of roller; is the fluid temperature; is the acceleration of gravity; is the thermal expansion coefficient of flow volume; is the roller
diameter.
-
ESTABLISHMENT OF FINITE ELEMENT MODEL
While the twin-rotor system is in operation, the rollers need to go through the load-bearing and non-load-bearing zones for one revolution in the raceway, but the rotation time of the rollers is relatively short. For example, if the inner ring speed is 10000r/min, it will take 0.006s for the rolling body to rotate once. During this time heat diffuses less into the solid. Therefore, it is assumed that the temperature of the bearing is axially symmetric when it is stable. You can simplify 3D to 2D for calculation.
The simplified finite element model is shown in Fig. 1:
Fig. 1. Finite Element Model.
Fig. 2 shows the temperature distribution of intermediate bearing under a certain working condition. It can be seen from the diagram that the temperature at the contact area between roller and inner and outer raceways is higher. This is the area where failure is likely to occur due to high temperatures. The influence of changing oil feed on contact point temperature of roller and inner and outer raceways is mainly analyzed below.
Fig.2.Temperature distribution of intermediate bearing.
-
ANALYSIS OF CALCULATION RESULTS
Fig. 3 shows the variation of temperature at the contact point between the roller of intermediate bearing and the inner and outer ring raceway with the amount of lubricant
entering. It can be seen from the figure that there is a lubricating oil flow, which makes the temperature at the contact point between the roller and inner ring and outer ring the lowest. When the fuel supply is higher or lower than this value, the temperature at the contact points will increase. That is, the optimum oil feeding of the intermediate bearing under this working condition is the oil feeding quantity that makes the temperature at the contact point the lowest.
Fig. 3. Lube oil inlet temperature 70 degrees.
Fig. 4 shows the relationship between radial force and optimum oil feeding. It can be seen from the diagram that the optimum oil feeding to the bearing increases with the increase of radial force. And when the oil inlet temperature of the bearing is changed, the optimal oil feeding of the intermediate bearing also increases. When the radial force of the intermediate bearing increases, the speed of each part of the bearing changes less, and the power loss of the bearing increases accordingly. This results in an increase in the optimum oil feeding.
Fig. 4. The diagram of the optimum oil feeding changing with the radial force.
Fig. 5 shows the relationship between bearing inner ring speed and optimum oil feeding. It can be seen from the diagram that the optimum oil feeding to the bearing increases with the increase of inner ring speed. The optimum oil feeding of the intermediate bearing increases when the inlet temperature of the bearing is changed. When the speed of the bearing inner ring changes, the angular rotation speed of the roller decreases, and the convection
heat exchange between the roller and oil decreases. At this point, the power loss of the bearing increases with the inner ring speed. The optimum oil feeding for the intermediate bearing increases accordingly.
Fig. 5. The diagram of the optimum oil feeding changing with the inner ring speed.
Fig. 6 shows the relationship between bearing outer ring speed and optimum oil feeding. It can be seen from the diagram that the optimum oil feeding to the bearing increases with the increase of outer ring speed. The optimum oil feeding of the intermediate bearing increases when the inlet temperature of the bearing is changed. When the speed of the outer ring of the intermediate bearing increases, the rotation angle speed of the roller also increases, and the convection heat transfer between the roller and the lubricating oil also increases. The power loss of the intermediate bearing increases as well. However, the increment of convection heat transfer is less than the increment of bearing power loss, which leads to the increase of the optimal oil feeding of the bearing, but the increment is smaller than the change of inner ring speed.
Fig. 6 The diagram of the optimum oil feeding changing with the outer ring speed.
The optimum oil feeding is related to radial force, low- pressure rotor speed and high-pressure rotor speed. When a certain parameter is changed and other parameters remain unchanged, the optimum oil feeding under a certain working condition can be determined. According to the recorded data (Fig. 4~Fig. 6), use 1st0pt software to fit the formula. The
calculation formula for determining the optimum oil feeding is:
= + 10() + 10() +
+ (14)
Where: is the radial load; is the low-pressure rotor speed; is the high-pressure rotor speed; is the
oil inlet temperature.
= 0.361770971761543
= 35889.8701658327
= 15097.875935
= 46.7673
= 182276.054881019
-
CONCLUSION.
The optimum oil feeding and the radial load of the intermediate bearing, the inner ring speed, the outer ring speed and the inlet temperature are related and increase as they increase.
The oil feeding value calculated according to different radial loads, inner ring speed and outer ring speed. And the oil feeding value obtained at a certain value of the inlet oil temperature. A formula for calculating the optimum oil supply of intermediate bearings is presented.
ACKNOWLEDGMENTS
This research was funded by Shandong Provincial Key Research and Development Program (Major Science and Technology Innovation Project) (Grant No. 2022CXGC010304) and National Natural Science Foundation of China (Grant No. 52075274 ) .
REFERENCE
[1] Zheng, D. X., Chen, W. F,.& Zheng, D. T. (2021). An enhanced estimation on heat generation of angular contact ball bearings with vibration effect, International Journal of Thermal Sciences, 159, 2021, 106610. https://doi.org/10.1016/j.ijthermalsci.2020.106610. [2] Yan, K., Wang, Y. T., Zhu, Y. S., Hong, J., & Zhai, Q. (2016).Investigation on heat dissipation characteristic of ball bearing cage and inside cavity at ultra high rotation speed, Tribology International, 93, Part A, 470-481. https://doi.org/10.1016/j.triboint.2015.09.030.
[3] Tan, D. Q., Li, R., He, Q., Yang, X. Q., Zhou, C. C., & Mo, L. L. (2021).Failure analysis of the joint bearing of the main rotor of the Robinson R44 helicopter: A case study, Wear, 477, 203862. https://doi.org/10.1016/j.wear.2021.203862.
[4] Wang, S. S., Guo, H., Lei, J. Z., & Zhang, Y. Z. (2017). Status and prospect for failure analysis on wear of rolling bearings in china, Bearing, 10, 58- 63. [5] Brown, J. R., & Forster, N.H. (2000). Operating temperatures in mist lubricated rolling element bearings for gas turbines, AIAA-2000-3027, 1268-1274. [6] Wang, Y. S., Zhu, H. F., & Liu, Z. (2012). Finite element analysis on temperature field of bearing with shaft, Journal of Aerospace Power, 27(05),1146-1152. [7] Yang, L. Q., Xue, W. H., Gao, S. Y., Liu, H. W., Cao, Y. F., Duan, D. L.,Li, D. Z., & Li, S. (2022) Study on sliding friction and wear behavior of M50 bearing steel with rare earth addition, Tribology International, 174, 107725. https://doi.org/10.1016/j.triboint.2022.107725.
[8] Gao, D. H., & Liu, Y. X. (2017). Thrust ball bearing design and calculation based on Hertz theory, Modern Manufacturing Technology and Equipment, 3, 43-44. [9] Kitahara, T., & Okamoto, J. (1983) Friction Torque of Instrument Ball Bearings under Combined Radial and Thrust Load, Journal of Japan Society of Lubrication Engineers, 28(4), 279-286. [10] Liu, J., Li, X. B., Ding, S. Z., & Pang, R. K. (2020). A time-varying friction moment calculation method of an angular contact ball bearing with the waviness error, Mechanism and Machine Theory, 148, 103799, https://doi.org/10.1016/j.mechmachtheory.2020.103799. [11] Lu, C. M., Niu, Z., Lu, J. F., & Li, F. (2021). Simulation analysis of friction moment characteristic of rolling-sliding bearing, Mechanical drive, 45(09), 139-144. [12] Deng, S. E., Sheng, M. J., Deg, K. W., Lu, Y. J., Li, M. L., & Dai, Y. B.(2017). Friction torque of double-row spherical roller bearings, Journal of Aerospace Power, 32(07), 1666-1675.