
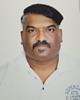
- Open Access
- Authors : Deepak Jadhav , Rajesh Magar , Anbarasan K
- Paper ID : IJERTV11IS120009
- Volume & Issue : Volume 11, Issue 12 (December 2022)
- Published (First Online): 12-12-2022
- ISSN (Online) : 2278-0181
- Publisher Name : IJERT
- License:
This work is licensed under a Creative Commons Attribution 4.0 International License
Design Optimization of Chassis Frame Long Member for Truck Application
Deepak J Jadhav
Chassis Integration group,Engineering Research Center Tata Technologies LTD, Pune
Plot No 25, Rajiv Gandhi Infotech Park, Hinjawadi, Pune, India 411 057
Rajesh Magar, Anbarasan K
Chassis Integration Group, Engineering Research Center Tata Technologies LTD, Pune
Plot No 25, Rajiv Gandhi Infotech Park, Hinjawadi, Pune, India 411 057
Abstract Chassis frame is the most important part of a commercial vehicle. Its main function is to safely carry the maximum load under all designed operating conditions. Hence it should be rigid enough to withstand various forces coming on it like bending forces, twisting forces, vibrations and other forces. An important factor in chassis frame design is to have adequate strength as well as torsional stiffness for better handling characteristics. Therefore, maximum shear stress induced in the frame and deflections during various operating conditions are important criteria for the chassis frame design. Cross-member assist the Long members to overcome lateral, bending and mainly torsional loads
The ladder chassis frames main structural component is long member to which all the other parts and cross members are attached. The chassis frame acts as the skeleton of the automobile so it should be able to with stand against various load condition but at the same time it should be light weighted to reduce the inertia effect. Now a day the focus of the manufacturing industries is to increase pay load capacity on possible less weight.
In this paper, a robust design optimization approach that can be used for optimization of chassis frame long member for truck application discussed.
Firstly, we are compering different material and other theoretical factors and Secondly, Analytical method is used to calculate the shear forces (SF) and bending moment (BM) and other engineering required parameters or calculations of the long member.
KeywordsLadder frame,Stiffness,Stress,Optimization
-
INTRODUCTION
Frame is a ladder shaped structure with two longitudinal rails/beams (Frame Long members) and properly located many integrating and reinforcing cross members, which form the ladder structure that is used as the interface/platform between the power package and the body package in automobiles.
This structure should ensure certain needs and requirements (functions) for the functioning of the automobile. The two primary load-carrying members are called long -Members and are joined together at proportionate points by cross-members. The Long members and cross members form an integral structure for the support of all chassis equipment and payload. Although the simplest frames have straight side-members in the plan and elevation views, packaging requirements for modern, high-powered engines frequently require more complex shapes at the engine area.
This structure should possess both flexibility and rigidity for the successful functioning of the vehicles in various applications and operating conditions the design application of the frame to rigid truck frame application.
-
BACKGROUND
Chassis frame forms the backbone of a heavy vehicle, its principal function is to safely carry the maximum load for all designed operating conditions. It must also absorb engine and driveline torque, endure shock loading and accommodate twisting on uneven road surfaces. To achieve a satisfactory performance, the construction of a heavy vehicle chassis is the result of careful design and rigorous testing.
It should be noted that this ladder type of frame construction is designed to offer good downward support for the body and payload and at the same time provide torsional flexibility, mainly in the region between the gearbox cross member and the cross member ahead of the rear suspension. This chassis flexing is necessary because a rigid frame is more likely to fail than a flexible one that can weave when the vehicle is exposed to arduous conditions. A torsionally flexible frame also has the advantage of decreasing the suspension loading when the vehicle is on uneven surfaces
A. Ladder type chassis Frame
Ladder chassis is considered to be one of the oldest forms of automotive chassis automobile chassis that is still been used by most of the commercial vehicles till today. It is also resembles a shape of a ladder which having two longitudinal rails (Long member) inter linked by several lateral and cross members as shown in fig.2 .1
Fig.2 .1 Ladder chassis frame
-
BENCHMARK DATA COLLECTION FOR LONG MEMBER
Collect all long member details of competitors running vehicles for easily finalize section
3) The special relationship of the frame to the vehicle is largely determined by location requirements of chassis and payload equipment.
V. LONG MEMBER DESIGN INUT DATA REQUIREMENT
Design inputs are the physical and performance characteristics of a long member that are used as a base for long member design.
-
Vehicle and other required details
While optimizing Long member following parameters to be considered.
-
Aggregate weight and there position
-
Gross vehicle weight (GVW)
-
Vehicle payload
-
Wheelbase
-
Front overhang
-
Rear overhang
-
Factor of safety as per application
-
5.1 A) Weight and CG details required for all aggregates and payload distrubution.
Table 3.1
-
-
LONG MEMBER DESIGN FACTORS Design of long member means optimizing the sections through various techniques according to the strength/load requirements.
-
Following Important Factors considered in designing of long member:
-
Profile of the long member.
-
Section of the Long Members
-
Material of the long member
-
Section Modulus of the long member
-
Maximum allowed stress on the long member
-
Maximum allowed Bending moment on the long member
-
4.1 Functions of Frame long members
-
Load bearing to carry the payload (principal function), Long member section should withstand all the loads with minimum structural material. (More strength to weight ratio structures/sections)
The design should also ensure the following: ·
-
Provision to manufacture with existing tooling, easy manufacturability.
-
Cost consideration, and weight consideration.
Example.
Fig 5.1 Weight distribution/aggregate positions
-
-
Packaging:
-
Interface/platform for power package and Body package.
-
Provisions for mounting all the aggregates (support, attachment, location, and alignment).
5.1 B) Gross Vehicle weight
Vehicle Weight is the total weight of vehicle including ULW and Payload it includes the combined weight of every axle placed under the chassis.
5.1 C) Vehicle Payload
Payload is the load which can be carried by a vehicle (legally), In simple words it tells us the weight of goods which can be transported by that specific vehicle. It is also known as Rated Load.
-
D,E & F) Vehicle/Long member dimensions.
There seems to be some difficulty in understanding the application of wheelbase related to front and rear overhang where axle units are involved. The following diagrams illustrate the methodology in the determination of the relevant dimensions.
-
OL- Overall Length (FO+WB+HAU+ROH)
-
FOH-Front Overhang (Distance from front end to front axle Centre)
-
WB Wheel base (Distance between front axle and rear axle Centre)
-
HAU-Half axle unit (Half the distance from rear first axle and rear 2nd axle)
-
ROH-Rear Overhang (Distance from Centre of rear most axle to rear end)
-
VI OPTIMIZATION METHODOLOGY
Techniques that attempt to improve or find the best Long member design can be classified into below categories.
-
Long member Profile Selection
-
Long member cross section selection
-
Long member Material Selection
-
Long member Size optimization
6.1 Long member Profile selection
A) Crank Profile Long member
Merits of crank section long member
The frame is narrowed down at the front to give room for the vertical movement of the front axle as it travels over road bumps & other road inequalities. Also it reduces CAB CG height, this type of configuration will provide better stability
& ride quality.
Upswept at the rear provided to give room for the vertical movement of the rear axle as it travels over road bumps & other road inequalities.
Better Long member section utilization & weight reduction
Demerits of crank section long member
Frame section narrowed down at front which reduces section modulus at front, In downhill condition as Load transfer takes place at front & there is possibility of failures in Long members Tooling investment is high
Flexibility of Holes changes difficult to manage due to tooling change.
Manufacturing require higher capacity hydraulic press setup which is expensive
B) Straight Profile Long member
Merits of Straight section long member
The frame is straight throughout length, which provides robust design with more section modulus gives better strength & stiffness.
Manufacturability is simple, gives cost benefit due to lesser tooling cost.
Flexibility of Holes changes is easy to manage due to CNC punching.
Demerits of crank section long member
These kind of Frames have two different widths in same assy. Front portion suddenly swallowed outward. This will give advantage for engine packaging & dropping on line.
Frame section is same throughout so weight of frame increases.
Time required for CNC Hole punching is more, hence more cycle time for development
Manufacturing require CNC programming
6.2) Long member cross section selection
A truck or other vehicle rolling across a beam or girder constitutes a system of concentrated loads at fixed distances from one another. For beams carrying only concentrated loads the maximum bending moment occurs under one of the loads. The largest of these various values is the maximum moment that governs the design of the beam.
FACTS ABOUT C SECTION AND I SECTION:
The frame resists vertical and lateral bending through the side- members.
As the primary load input is vertical, due to the payload effect, the side-members are designed first to resist this load, and second to resist the lateral inputs
Long -members are designed as longitudinal beams.
An I shaped member would perform this task more efficiently than a channel shaped member. However an I shaped member has several limitations, fabrication of contoured profiles are difficult, manufacturing costs are high, and attachment of components and cross-members is complicated.
Channel sections have one unique property; the shear center is not coincident with the centroid:
6.3 Long member material selection
Select and replace Low strength material with appropriate high strength material with reduction of component material thickness and getting eight advantage without much affecting strength requirement
Table 6.3 Long member material comparison 6.4- Long Member Size Optimization.
Varying the section with the same material the weight changes proportionally to the section area. The goal is to choose the optimal geometry to reach the maximum load capacity with minimal material use independent from any specific material. One main constraint for this optimization method is the increasing risks of buckling the thinner the sections are designed.
Formulae for find out optimized section long member Basic Bending Equation
Different Section calculation formulae
A. SFD and BMD calculations
Vehicle GVW 16200 Kg = 158867.73N
Weight on Each long member = 158867.73/2 = 79,433.865N Long member material = E46 = Yield 460 MPa
Factor of safety considered as 3
Where,
M= bending moment
I = moment of inertia of the section about the bending axis. = stress at a distance y from the centroid/neutral axis.
E = Youngs Modulus of the material of the beam. R = radius of curvature of the bent beam
FOH |
1422 |
||
WB |
5500 |
||
ROH |
2851 |
||
Load Body ROH |
2851 |
||
Total Length |
9773 |
||
GVW |
16200 |
||
Unladen FAW |
2910 |
||
Unladen RAW |
2002 |
||
Pay Load |
11288 |
||
Load Body Start |
1600 |
||
Load Body length |
8173 |
||
UDL (Kg/mm) |
1.38 |
||
Load Location (from frt face) |
5686.50 |
||
FAW |
2536 |
||
RAW |
8752 |
||
FAW |
5446 |
||
RAW |
10754 |
||
GVW |
16200 |
||
Max Bend mmt (Kgmm) |
5507474.3 |
||
LONG MEMBER,RH |
|||
POINT LOADS |
|||
S.NO |
Aggregate |
Distance from Long member Front (mm) |
Load (kg) |
1 |
CAB Mounting Front, RH |
250 |
103.5 |
2 |
CAB Mounting Rear, RH |
1614 |
81.5 |
3 |
Engine Mounting Front, RH |
662 |
135.5 |
4 |
Engine Mounting Rear, RH |
1450 |
187.0 |
5 |
Steering Gear Box Mount-1 |
260 |
71.0 |
6 |
Radiator Front, RH |
270 |
20.0 |
7 |
Fuel Tank Mounting, Front,RH |
2297 |
195.6 |
8 |
Fuel Tank Mounting, Rear, RH |
3107 |
164.4 |
9 |
Silencer Mtg.-1 RH |
2587 |
2.5 |
10 |
Silencer Mtg.-2 RH |
3377 |
44.5 |
11 |
Airtank-1, RH |
8537 |
13.8 |
12 |
Airtank-2, RH |
8887 |
26.2 |
13 |
Distance b/w frame front face and load body start |
2251 |
1.6 |
Uniform distributed load acting (kg/mm) |
0.05 |
VII CONSIDERATION OF ALTERNATIVE MANUFACTURING PROCESSES
Replace the expensive and non-flexible manufacturing processes to unexpansive a flexible process. So modification and design change incorporation will easy and lead to faster product development cycle.
- <>Press forming
Expensive and very difficult process to adopt new design changes or modification requirement
-
Roll Forming
Less expensive, fast process for incorporate regular changes
-
Hot Forming Expensive than Press forming but strength of material get improved due to process.
-
Hydroforming
Tube hydroforming allows engineers to optimize their designs through cross sectional reshaping and perimeter expansion. Combined with the ability to inexpensively create the holes that are required for vehicle subsystem interfaces, hydroforming has become a critical technology for structural components in mass-produced vehicles.
Shear Force Diagram
Bending Moment Diagram
-
KEY BENEFITS OF CHASSIS LONG MEMBER OPTIMIZATION
The most attractive benefit of optimization is its ability to reduce any unnecessary weight. Size optimization means that less raw material is needed. Extra weight also negatively impacts energy efficiency. Parts will cost more for shipping as well. All these advantages translate directly into actual cost savings which is important in a competitive market.
As design constraints and performance expectations are factored in at the early stages of conception, it does not take as much time as without to come up with the final design. A faster process also means a shorter time-to-market duration which is especially important for new products in a competitive market
Weight reduction min. 5 -10% can achieve with this method
Light Weight long member and cost saving also it will increased pay load of vehicle
Section Changes comperasion
-
CONCLUSION
-
To optimize the Long member section following sequence of options to be worked out
-
First Option: Web height should be increased which is having highest strength to weight ratio
-
Second option: Increase flange width, which has better strength to weight ratio.
-
Third Option : Increase thickness of section, which has poor strength to weight ratio.
-
-
Increase in thickness gives more moment of inertia at extreme fibers, which is highest stressed zone.
-
If increased weight in Long member can be compensated at cross members & reinforcements then increase in thickness is best option.
X . FUTURE SCOPE
-
Long member with composite material introduction which is light weight and higher strength also corrosion resistance
-
Topology optimization is new approach will drastically improve design with a very less time through 3D design and analysis softwares
XI. ACKNOLEDGEMENT We wish to express our sincere thanks to Mr. K Anbarasan Sir and Mr. Rajesh Magar for their help and guidance given time to time
REFERANCES
[1] Design and Durability Analysis of Ladder Chassis Frame 1Gurjar, M., 2Deshmukh, S., 3Goswami, S., 4Mathankar, V.,5Shrivastava, S. 1Asst. Professor, 2,3,4,5Engineering Student Mechanical Engineering Department, IES IPS Academy, Indore (M.P) [2] IJESRT Design and analysis of Tata 2518TC truck chassi frame with various cross section using CAE tools , Akash Singh Patel ,Jaideep Chitransh Department of Mechanical Engineering, UCER, Allahabad,India
[3] Commercial vehicle frame Design [4] Shape Optimization of Automobile Chassis Aayush Chugh, Rachit Ahuja, Sukriti Ranjan IRJET paper [5] Mathematical Analysis of Section Properties of a Platform Integrated with Vehicle Chassis Prof. Deulgaonkar V.R, Prof. Dr. Kallurkar S.P, Prof. Dr. Matani A.G