
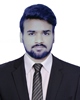
- Open Access
- Authors : Shreeyash Uddhav Jadhav , Suraj Ramu Gowda , Vedant Ajay Utikar
- Paper ID : IJERTV10IS090149
- Volume & Issue : Volume 10, Issue 09 (September 2021)
- Published (First Online): 25-09-2021
- ISSN (Online) : 2278-0181
- Publisher Name : IJERT
- License:
This work is licensed under a Creative Commons Attribution 4.0 International License
Design & Manufacturing of Steering System for FSAE Vehicle
Shreeyash Uddhav Jadhav
B.E Mechanical Engineer
JSPMs Rajashri Shahu College of Engineering Tathawade, Pune, India 411033
Suraj Ramu Gowda
-
Mechanical Engineer
JSPMs Rajashri Shahu College of Engineering Tathawade, Pune, India – 411033
Vedant Ajay Utikar
Pursuing B.E Mechanical Engineering JSPMs Rajashri Shahu College of Engineering
Tathawade, Pune, India – 411033
Abstract – The following article will help you in understanding about how a steering system is an FSAE vehicle is designed and manufactured considering all types of stresses, strains and other mechanical properties acting on it. The primary objective of the steering system is to enable the driver to continuously manoeuvre the path of the vehicle and provide a good steering response to the driver. This report focuses on the design, manufacturing and tuning of the steering system. The main focus was given on reducing the weight of the system along with reducing the free play at the steering wheel to ease the handling and increasing the stability at high speeds.
Key words: – Steering System, FSAE, Objective, Manoeuvre
-
INTRODUCTION
-
A steering system is a system of a vehicle on which a driver gets the first feedback about the surface of the road. The steering system consists of components, linkages, etc. which allows a vehicle to follow the desired course. This system is used to steer the front wheels present in the vehicles in right or left direction. The steer is given with a component which is called the steering wheel. This steering wheel is positioned in front of the driver and is connect to the front wheels with a column, universal joints and gears. There are 2 types of steering geometry mainly in the industry today. First one is the Ackerman Steering Geometry and second one is the Anti-Ackerman Steering Geometry. In the FSAE vehicle we use the Anti-Ackerman Steering Geometry as it has more advantages for a race car over the other type of geometry.
Figure 1: Steering system
-
DESIGN CONSIDERATIONS
Whilst designing any system, it is important to take into account various conditions the system will be exposed to. Steering is one of the two systems which takes input from the driver and transfers it to the tire. Following are the considerations made while designing the steering system.
-
Coefficient of friction between road and tire = 1
-
Weight of the car = 250 kgs
-
Minimum radius of the track = 4.5 m
II. DESIGN OBJECTIVES
-
Design a new system with eliminated bulky support and improvised ergonomics using a singleuniversal joint.
-
To introduce an adjustable steering geometry as required for different dynamic events.
-
To minimize the compliance in the system this will ease the handling and provide better stability at high speeds.
-
To optimize the weight of the system to less than 3 kgs.
-
Reducing the turning radius to 4m.
-
-
DESIGN PROCEDURE Considerations in the system
design
Setting the Design Objectives
DFMEA of the system
Steering geometry
Selection of steering mechanism
Location of Rack and Pinionusing simulations
Selection of intermediate mechanism
Material selection
Analytical design of gears
System design and modeling (including custom gearbox)
Manufacturing and assemblyof the system using fixtures
Event based wheel alignment during testing
-
DFMEA
Failure Modes and Effects Analysis (FMEA) is a systematic, step by step failure analysis technique which evaluates the processes for possible failures and to prevent them by correcting the process ratherthan reacting to its effects after the failure.
Design Failure Modes and Effects Analysis (DFMEA) is first done by identifying all the components of the system. This is followed by identifying the failure mode for each component, its causes, effects on the system and the vehicle as a whole. After the above step, severity of the failure, likelihood of occurrence of failure and its detection is rated for each failure mode.
DFMEA of a system helps the designer to identify the most critical components of the system andmodify the design so as to reduce the risk of its failure.
Table 1: DFMEA of steering system.
Component
Failure cause
Failure effect
Se ve rit y
Preventi ve
measur e
Steering Wheel
Lesser torque applied during FEA
System Failure
10
Verification of Steering torque
Quick Release
Fatigue erosion
Increased free play
4
Hardening of splines
Friction bearing Universal Joint
No sustainabl e material used
Decreased stability at high speeds
6
Use of needle bearing UJ
Rack & Pinion
Improper Design
Increased effort and wear
7
Research on gear design
Rod – ends
Misaligne d Line of Action
System Failure
10
Fixtures to be used in Manufacturing process
Steering Column
Excessive torque applied
Input required from driver increases
8
Validation of torque
-
SELECTION PROCESS
-
Steering geometry and percentage
It is the geometric arrangement of linkages in the steering of a car or other vehicle designed to solve theproblem of wheels on the inside and outside of a turn needing to trace out circles of different radii.
Ackerman steering
Anti-Ackermansteering
No skidding at front tires
Leads to excessive skid
Less response to driverinputs
Very poor response
1.9º camber gain
0.9º camber gain
Better for skid pad
Better at high speeds
Table 2: Comparison of Steering Geometry
-
Anti-Ackerman steering neither provides good response nor provides stability during cornering.
-
Ackerman steering is stable and thus better for skid pad but is a bit less responsive.
Figure 2: Mechanism to determine optimum Ackerman percentage.
Thus, it was necessary to find a trade-off between stability during cornering and responsiveness. For this,a mechanism was incorporated between the knuckles which would provide an experimental value for the steering geometry as per the events.
Event
Ackerman Percentage
Skid pad
86
Autocross
37
Event
Ackerman Percentage
Skid pad
86
Autocross
37
Based on testing results and driver feedback, following values were chosen:
Figure 3: Manufactured rack and pinion
-
Location of rack and pinion
The two major factors deciding te position of rack and pinion are:
-
Inversion of the four bar mechanism
-
Packaging
-
Case 1: Steering rack behind the front axle.
This position would solve the problem of packaging the wheel assembly inboard. However, this resulted in early inversion of the linkages. It restricted the turning of the inner wheel to 28°. The outer wheel for 80% Ackerman would turn 21° giving a turning radius of 4.3m which is far away from desired.
Table 3: Finalized steering geometries
-
-
-
Steering mechanism
The rotary motion of the steering wheel is transferred to the wheels of the car via a suitable mechanism. This mechanism takes input from the steering column and transfers it to the tie rods which are further connected to the wheels. This chooses mechanism
-
Must convert rotary motion into linear
-
Have a linear output
-
Sustain the steering torque
iv.
Case 2: Steering rack ahead of front axle.
This pushed the point of inversion forward and the desired turning angles were achieved. Also, during cornering, the outer wheel handles more loads and the tie rod attached to this wheel will be under tension which is safer than it being under compression. The problem of packaging was solved by selecting rims with greater step offset as required.
Selection of intermediate mechanism.
After prototyping of the chassis and the seating position of the driver, the angle of the steering wheelwas finalized as 20º with the vertical. This could be achieved with three mechanisms as:
Rack and Pinion
Recirculating Ball
Fewer moving parts
More complex with moremoving parts
Less mechanicaladvantage
More mechanicaladvantages
Less wear if hardenedinitially
More parts result inincreased total wear
Requires less space and is lightweight
Requires less space but is too heavy
Alternative for
Choice
Steering geometry
Ackerman (37% for autocross) (95% for skid pad)
Steering mechanism
Rack and pinion
Location of steering mechanism
Ahead of front axle
Intermediate mechanism
Single UJ
Alternative for
Choice
Steering geometry
Ackerman (37% for autocross) (95% for skid pad)
Steering mechanism
Rack and pinion
Location of steering mechanism
Ahead of front axle
Intermediate mechanism
Single UJ
Table 4: Alternatives for steering mechanism
Thus, we can conclude that rack and pinion mechanism have many advantages over the other two except that of less mechanical advantage. This problem was solved by a discussion with the suspension and wheel assembly team. It was decided to increase the steering arm length to gain mechanical advantage over the uprights.
Accordingly, a custom rack and pinion was designed and manufactured.
Table 5: Alternatives for intermediate mechanism.
Thus, with a discussion with the suspension team, the height of the gearbox was increased and a single UJ was selected by giving an inclination to the gearbox.
To summarize with, following selections were made:
Single UJ
Bevel gearbox
300 grams
900 grams
No additional supportstructure required
Additional support required
Increased height of rack andpinion
Less height of rack and pinion
igh sensitivity at small turning angles as desired forautocross
No such desired effect
Table 6: Summary for selections amongst alternatives
-
-
MATERIAL SELECTION
Selection of appropriate material considering the operating conditions, fatigue life, elasticity hardnessetc. decides the endurance limit of the component. Following were the considerations for componentstaken into account prior the selection of materials:
-
Steering wheel: Sustain the steering torque, provide adequate grip and be lightweight.
-
Quick release: Have high wear resistance.
-
Column and single UJ: Sustain Steering torque.
-
Rack and pinion gears: Must not fail against bending load on teeth and have a thigh BHN.
-
Gearbox casing: Rigid and lightweight.
-
Clevis: Serve the functionality.
-
Tie rods: Must not buckle under dynamic forces.
Following is a table consisting major components of the system, their materials and process used for its manufacturing.
Component
Material
Steering wheel
Composite (carbon fiber)
Quick Release
Mild steel (hardened)
Column
Mild steel
Single UJ
Steel
Rack and pinion gears
EN 19 (hardened)
Gearbox casing
Aluminum 6082
Clevis
Mild steel
Tie rods
Mild steel
Table 7: Material selection
-
-
CALCULATIONS
-
Turning radius:
As stated in the objectives, the desired turning radius is 4m which was decided considering that the least turning radius of the track among all the dynamic events would be 4.5 m.
Figure 4: Turning radius
As seen above the turning radius of the vehicle is:
We have,
Ackerman % * 100 By solving at 95% we get,
= 27.24
In the Lotus software, a kinematic analysis was performed and the above angles were obtained at a racktravel of 39mm, eye to eye 380mm and a steering arm length of 60mm.
Accordingly, rack and pinion was designed for 39mm travel on either side or pinion lock to lock180º.
-
Rack and pinion gear
-
Rack travel (either side) = 39mm
-
Pinion (either side) = 90º
-
Module = 1.5mm
a)
Dpinion = 49.65 mm
b)
Zpinion = 33
-
Zrack = Zpinion
Zrack = 33
-
Tooth depth (h) = 2.25m
h = 3.375mm
-
Addendum (ha) = 1.00m
ha = 1.5mm
-
Dedendum (hf) = 1.25m
hf = 1.875mm
Figure 5: Sectional front view
-
Steering Ratio
Steering ratio is defined as the ratio of angle turned by the steering wheel to that turned by the wheels of the car.
Mathematically,
Steering ratio = 3.60
-
C Factor
C-factor in steering is defined as rack travel per 360º rotation of pinion.
Figure 6: Sectional side view
-
-
-
Steering effort:
Total mass of the car = 250 kgs
Load transfer during braking = 27.5 kgs
Maximum weight on front end = 0.45 250 + 27.5
= 140 kgs
= 1373.5 N
Steering effort is the force applied at the steering wheel to produce a torque about the steering axisresulting in turning of the front wheels.
The weight on the front axle is equal to the net force transmitted by the rack to the tie rods.
Net force in the rack (Frack) = 1373.5 N
This force is generated by a torque in the pinion.
Torquepinion = Frack Radiuspinion
Torquepinion = 34.094 Nm
This is the torque produced in the steering whel by the driver.
The radius of steering wheel is 230 mm
Fdriver = 148.23N = 15.11 kgs
C factor = Dpinion
C factor = 155.98 mm
-
-
CONCLUSION
This is the way in which a steering system is to be designed and similarly manufactured for a FSAE vehicle. These calculations are made with respect to a car which is designed by us. Similar calculations can be done for other vehicles which are using different types of steering geometry and can be validated with the help of various software like ANSYS or LS – DYNA. This will give an idea that how good the system is designed
-
REFERENCES
-
Steering: Wikipedia, a free encyclopedia – https://en.wikipedia.org/wiki/Steering
-
Wheel steering system – https://www.ripublication.com/irph/ijert_spl/ijertv6n3spl_15.pdf
-
Design & Fabrication of Steering System for Transportation Vehicle
– https://www.ijitee.org/wp-
content/uploads/papers/v8i10/I8430078919.pdf
-
Design & Analysis of Steering System for Solar Vehicle – https://www.ijert.org/design-analysis-of-steering-system-for- solar-vehicle
AUTHORS
Shreeyash Uddhav Jadhav completed Bachelor of Engineering in Mechanical Engineering from the JSPMs Rajarshi Shahu College of Engineering, an Autonomous College Accredited by SPPU, India. His research interests include Vehicle modeling, track simulation, vehicle dynamics and electric vehicle powertrain design. He also has experience in design and manufacturing the vehicle dynamics system for an FSAE car.
Shreeyash Uddhav Jadhav completed Bachelor of Engineering in Mechanical Engineering from the JSPMs Rajarshi Shahu College of Engineering, an Autonomous College Accredited by SPPU, India. His research interests include Vehicle modeling, track simulation, vehicle dynamics and electric vehicle powertrain design. He also has experience in design and manufacturing the vehicle dynamics system for an FSAE car.
Suraj Ramu Gowda completed Bachelor of Engineering in Mechanical Engineering from the JSPMs Rajarshi Shahu College of Engineering affiliated to Pune University, India. Author is passionate about design, analysis and manufacturing of Automobiles and Electric Vehicle design, and has experience in vehicle simulation software. He also has core research in analytical vehicle dynamics.
Suraj Ramu Gowda completed Bachelor of Engineering in Mechanical Engineering from the JSPMs Rajarshi Shahu College of Engineering affiliated to Pune University, India. Author is passionate about design, analysis and manufacturing of Automobiles and Electric Vehicle design, and has experience in vehicle simulation software. He also has core research in analytical vehicle dynamics.
Vedant Ajay Utikar is pursuing Third Year of Engineering in Mechanical Engineering from the JSPMs Rajarshi Shahu College of Engineering, an Autonomous College Accredited by SPPU, India. Author is passionate about design, analysis and manufacturing of various components which are related to Automobile & its peripherals. Along with this he has hands on experience of designing, manufacturing and testing of various Automobile components and its peripherals.
Vedant Ajay Utikar is pursuing Third Year of Engineering in Mechanical Engineering from the JSPMs Rajarshi Shahu College of Engineering, an Autonomous College Accredited by SPPU, India. Author is passionate about design, analysis and manufacturing of various components which are related to Automobile & its peripherals. Along with this he has hands on experience of designing, manufacturing and testing of various Automobile components and its peripherals.