
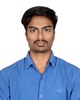
- Open Access
- Authors : B. Ashok , M. K. Naidu , S. Srinivasa Rao
- Paper ID : IJERTV10IS040249
- Volume & Issue : Volume 10, Issue 04 (April 2021)
- Published (First Online): 03-05-2021
- ISSN (Online) : 2278-0181
- Publisher Name : IJERT
- License:
This work is licensed under a Creative Commons Attribution 4.0 International License
Design and Weight Optimization of Aluminium Alloy Wheel Rim for Light Weight Four Wheeled Vehicle
B. Ashok1
1 PG Student, Dept. of Mechanical Engineering, MVGR College of Engineering (A),
Vizianagram, AP, India.
M. K. Naidu2
2 Associate professor, Dept. of Mechanical Engineering, MVGR College of Engineering (A),
Vizianagram, AP, India.
S. Srinivasa Rao3
3 Senior.Engineer, Dept. of Engineering and R&D, Synergies Castings Ltd,
Visakhapatnam, AP, India.
Abstract The purpose of a car wheel rim is to provide a firm base to hold the tire. The rim design is an important industrial activity that influences the quality of the product. While designing such critical automotive components taking care of protection and costs are very important concerns in order to use it safely. The major technical considerations while modeling any new alloy wheel rim are styling, aesthetic, mass, manufacturability, and capability. The present work deals with a newly designed wheel rim to the analysis of equivalent maximum stresses in medium weight vehicles which have a wide range of scope for research for its improved performance and application. A new CAD design of a car wheel rim considered from a standard rim size according to TRA of 17 inches in CATIA V5 software. The solid model is then imported to UG/NX NASTRAN to perform static structural analysis in order to determine the stresses due to different loads. The rim is analyzed as per SAE standards by simulating various tests like radial fatigue test, cornering fatigue test, and impact test. From the analysis, the maximum stresses in the rim are observed to be 65.3MPa, 93.1MPa, and 153.06MPa for radial load fatigue test, cornering fatigue test, and impact test respectively. Further, the design of the rim is optimized to reduce weight without losing its functionality. From the results, it is observed that the stresses generated in the optimized wheel rim are well below the yield stress of the material and safe for the application. The reduction in the weight of the rim is observed to be about 4.08%.
KeywordsAlloy wheel, Radial fatigue test, Cornering fatigue test, Impact test, Static analysis, NX-NASTRAN.
-
INTRODUCTION TO ALLOY WHEEL
In the automotive industry, light-alloy wheels are composed of either aluminum or magnesium. Alloys are the compounds of different materials added in various proportions to enhance the properties. Alloys of aluminum (or) magnesium are lightweight and also provide equivalent strength over pure metals, softer and more ductile. Increase in aluminum castings made to replace magnesium due to its low cost and high-performance. In the alloy wheel, the most stress region is the spoke area as the weight of the body lies more on it. If the weight of the vehicle gets reduced then the suspension will follow the terrain more
closely and thus improves the grip and overall performance, which ultimately leads to fuel consumption and cost-saving.
The Rim profile used for alloy wheels has to be in line with Tire & Rim Association standards [1] as tire & Rim are going to be assembled as a part of vehicle fitment. Styling and loading requirements will vary from OEM to OEM. Prashant Saxena et el [2] the study comparative research of different offset rims has been investigated under different boundary conditions such as load, air pressure. X Jiang et el [3] discusses the design of a new model of an automobile wheel. Considering three different materials namely magnesium alloy, aluminum alloy, and steel, the stress and strain performances of each material can be obtained.
Cast aluminum alloy wheels are generally manufactured by Low-Pressure Die Casting using A356 alloy (with main alloying elements of 7% Si and 0.3% Mg) with a T6 aging heat treatment to obtain better mechanical properties [4,5,6]. Cast aluminum alloy wheels are subjected to a lot of proof tests due to their safety equipment function. The wheel has to pass three types of tests before going into production, there are mainly, a 13° impact test, dynamic cornering fatigue test, rotary fatigue test [7,8,9]. Finite element analysis is carried out by simulating the functionality test conditions to analyze the stress distribution of the alloy wheels [10]. In addition, a wheels overturning moment, lateral stability of the vehicle [11], mechanical quality, and corrosion performance must be validated by accelerated or natural corrosion tests.
Fig: 1 Schematic diagram rim nomenclature
-
Problem Definition
The various articles of stress analysis in the literature reveal that the stress is much greater in the rim as compared to the disk portion of the wheel and reduction in weight results in cost-saving. The failure of rim wheel is due to crack initiated near the hole and spoke which further gets propagated throughout the rim which leads to fatigue failure. Radial and cornering loads determine the performance characteristics of an alloy wheel for structural integrity. Rim spoke should not break while rough driving condition which can analyze through impact analysis. To improve the fatigue life and reduce the weight in the aluminum wheel rim, critical stresses are determined in the spoke area FEA software.
-
Methodology
The approach to our design problem is elaborated through the flow -chart given below:
Fig: 2 Flow chart of methodology
-
-
MODELING OF WHEEL RIM
CATIA modeling software is used for the creation and modification of the rim. The cad model of the wheel rim is prepared for the passenger car wheel rim, 17-inch diameter, 7-inch rim width, the rim of 50 drop center, and J contour are taken as the standard specification in the TRA. During the design of the styling concept of the wheel rim, the spoke profile is made roughly by drawing the spoke
pattern and changing the number of spokes. By taking rim diameter and rim width, the offset, center bore and bolt pattern can be chosen based on manufacturing feasibility in CATIA V5.
Table 1: Specifications of the model wheel rim
Wheel Specifications
Rim Diameter
17
Rim width
7 J
Offset
54 mm
PCD
6×120
Centre Bore
60 mm
Number of spokes
6
Using the CATIA V5 commands modeling of the wheel rim in two-dimensional and three-dimensional planes is done. Selecting the XY plane rim profile is sketched in 2D with respect to the dimensions with the center axis at the origin and considering the center axis the sketch is revolved around 3600. Then selecting one of the surfaces of the revolved rim in one of the plane then rough sketch, of the spoke design is done using 2D commands, the section cut is carried using trim body command in 3D view and using circular pattern feature the number of spokes is designed in symmetrical order and using fillet command the sharp edges are smoothed, the holes used for fitting of nuts and bolts are designed in the same way selecting the surface on which it has to be holed and then 3D view, the material is removed using the trim body command and using pattern feature number of holes are designed or modeled.
Fig: 3 Profile of wheel rim with J Contour
Fig: 4 Isometric view of wheel rim
-
FUNCTIONALITY TEST OF WHEEL
The structural integrity of the wheel can be evaluated using the test methods. The tests evaluate the accelerated fatgue lifetime of the wheel. Wheels that are intended for passenger use must pass an impact test, cornering fatigue test, and radial fatigue test before they go into production.
-
Radial fatigue test
A wheel with a tire is loaded against a rotating drum to simulate straight-ahead driving conditions. Accelerated loads are applied to evaluate stresses into the tire and rim.
-
Cornering fatigue test
The cornering fatigue test entails constraining the rim flange while a force is applied to the hub through a load arm. The test simulates cornering driving conditions.
-
Impact test
The rim flange of a wheel and tire assembly is impact loaded. The assembly is mounted at a 90o angle and 13o angle to the horizontal plane before the load is applied. This test simulates the loading experienced when a vehicle drives over pavement or experiences a sudden impact.
The failure criterion for each of the tests is taken into consideration to be any permanent deformation of the wheel or wheel assembly. This ranges from crack initiation or loss of tire pressure due to wheel deformation depending on the test in question. The alloy wheel rim is going to be structurally validated through the cornering fatigue test, radial fatigue test, and impact test with reference to the Society of Automotive Engineers (SAE) [15, 16].
-
-
STATIC ANALYSIS
The static finite element analysis of the wheel includes radial, cornering fatigue test and impact test. Analysis of the wheel rim is done by simulating the designed wheel rim based on static structural analysis using finite element analysis technique to validate the results in NX-Nastran software. The following procedure is adopted for the rim analysis.
-
Preprocessing to build the model.
-
Post-processing to apply boundary conditions and material.
-
Solution to interpret results.
Material properties:
The material chosen for wheel rim is A356.2 i.e. cast aluminum Alloy which is widely used in the automotive engineering industry. Mechanical properties of material used for the rim are as shown in Table 2.
Table 2 Material properties of Aluminium A356.2
Material Properties
Aluminium A356.2
Ultimate Tensile Strength (Sut)
230 MPa
Tensile Yield Strength (Syt)
186 MPa
Modulus (E)
70 G a
Poissons Ratio
0.33
Density ()
2670 Kg/ m3
-
Cornering Fatigue Test (CFT) on Wheel rim
The 3D model of a wheel rim with the shaft is created in the UNIGRAPHICS, is used to perform Cornering Fatigue Test. The wheel rim is meshed using the tetrahedral element with a mesh size of 0.2 m. The number of elements in the mesh is 53480, and the number of nodes in the mesh is 98343 as shown in Fig.5. Inner flange surface is constrained in all degree of freedom, this can be seen in blue colour at the centre of the wheel and load of 4009.1N is applied on the shaft in the negative Z-direction, as indicated in red colour here the wheel rim, is assigned with aluminium alloy, and the shaft is with structural steel.
Fig: 5 Boundary Conditions for CFT
-
Radial Fatigue Test (RFT) on Wheel rim
The 3D model of a wheel rim with tire and slab assembly is created in the UNIGRAPHICS with slab dimensions of 1000 mm x 500 mm x 75 mm as shown in figure
6. The wheel is meshed using a tetrahedral element. The number of elements was found to be 93052 and the number of nodes was found to be 178491. In Fig. 6, lug holes and mounting flange surfaces are constrained in all degrees of freedom. This can be seen in blue color at the center of the wheel. And the load of 17805N is applied on the slab towards the wheel. This is indicated in red colour. Here the wheel material is assigned with aluminum alloy slab material with structural steel & tire with polyethene.
Fig: 6 Boundary Conditions for RFT
-
13° Impact Test (IMP) on Wheel rim:
-
The 3D model of a wheel rim with tire and slab assembly for a 13-degree impact test is created in the UNIGRAPHICS, with slab dimensions of 250 mm x 150 mm x 75 mm as shown in Fig. 7. The wheel is meshed using tetrahedral element. The number of elements in the mesh is 73607, and the number of nodes in the mesh is 132609. In fig. 7, lug holes and mounting flange surface are constrained in all degree of freedom this can be seen in blue colour at the centre of the wheel. And the load of 6039N is applied on the slab in vertically download direction. Here the wheel material is assigned with aluminium alloy slab material with structural steel.
Fig: 7 Boundary Conditions for IMP
-
-
WEIGHT OPTIMIZATION OF WHEEL RIM Topology optimization is done by removing the
material from rim hub area where we provide elliptical groves and pockets to remove unnecessary material. Here mass is taken as the design variable for minimizing the volume. Here the inner side of the spokes and hub area is considered as a design area while the region's front side styling is taken to be a non-design region. Three appropriate cases are considered to achieve the objective cornering fatigue test, radial fatigue test, Impact test. Base model and optimized CAD model in CATIA after removing material is shown below in Fig.9.
Fig: 8 Base model
Fig: 9 Optimized model
-
RESULTS AND DISCUSSIONS
-
Finite element analysis results for the functionality tests of base model of wheel rim
All the functionality tests like cornering fatigue test, radial fatigue test, and impact test were simulated in NX- Nastran consisting of a different scenario, to find the stresses. Based on the max stress value of each test, further modification are done, to make note that maximum stress value at the air valve and fixed position can be negligible for study because practically failure will not occur at this.
Maximum stress values for the base model of the wheel
Fig: 10 CFT max stress
Fig: 11 RFT max stress
Fig: 12 IMP max stress
From the static analysis of the base wheel rim, the max stress for CFT is 75.30MPa at spokes of the wheel, with the load of 4009.1NM is applied on the shaft in the negative Z-direction as shown in fig. 10, max stress for RFT at the edge of the spoke of a wheel which is 58.52MPa. With the load of 17805N applied on the slab towards the wheel as shown in fig. 11. Max stress for the impact test is 143.18MPa. With the load of 6039N applied on the slab in a vertically downward direction as shown in fig. 12. The stresses in the spoke cross-section were within the yield limit of the material.
-
Finite element analysis results for the functionality tests of optimized wheel rim
Static Analysis is carried out for the optimized design of aluminium alloy A356.2 material. Boundary, loading Conditions and procedure were same as before optimization. To obtain the better weight reduction and better performance of optimized wheel rim.
Maximum stress values for the optimized model of the wheel
Fig: 13 CFT max stress
Fig: 14 RFT max stress
Fig: 15 IMP max stress
After optimization weight of the alloy wheel is reduced and analysis carried out on the optimized design. From the static analysis max stress for CFT is 93.1MPa at spokes of the wheel as shown in fig 13. The max stress for RFT at the edge of the spoke of the wheel is 65.3MPa as shown in fig 14. The max stress for the impact test is 153.06MPa (ignoring the direct impact region) as shown in fig 15. The stresses in the spoke cross-section were within the yield limit of the material.
-
Comparison of alloy wheel mass before and after optimization
In this the optimized alloy wheel material is aluminium A356.2 alloy. By performing the optimization the mass of the allo is reduced by 4.08%, before optimization the mass was 13.24Kg and after optimization its mass is reduced to 12.70Kg. As said earlier the main intention of the project is to reduce the weight and the below table clearly states that the optimized alloy wheel is comparatively very light weight. The comparison of the weight values are given below.
Table 3: Comparison of alloy wheel mass before and after optimization
Mass of alloy wheel rim before optimization (Kg)
Mass of alloy wheel rim after optimization (Kg)
Reduction in percentage
of mass %
13.24
12.70
4.08%
-
Comparison of alloy wheel stresses before and after optimization
Initial model maximum stress for cornering fatigue test is 75.30MPa and maximum stress for optimized wheel CFT is 93.10MPa. Initial model maximum stress for radial fatigue test is 58.82MPa and maximum stress for optimized wheel RFT is 65.30MPa. The stress values were within the yield limit of the material. Impact test initial maximum stress is 143.18MPa maximum stress for the optimized wheel is
-
MPa.The stress values in the spoke cross-section were within the yield limit of the material. i.e., 186Mpa
S.No.
Functionality Tests
Alloy wheel before optimization stress (MPa)
Alloy wheel after Optimization stress (MPa)
1.
CFT
75.3
93.1
2.
RFT
58.82
65.3
3.
IMP
143.18
153.06
S.No.
Functionality Tests
Alloy wheel before optimization stress (MPa)
Alloy wheel after Optimization stress (MPa)
1.
CFT
75.3
93.1
2.
RFT
58.82
65.3
3.
IMP
143.18
153.06
Table 4: Comparison of alloy wheel stresses before and after optimization
E.
93.1
93.1
143.18
143.18
Stresses(Mpa)
Stresses(Mpa)
Comparison between base wheel design results to optimized wheel results
Comparison of alloy wheel stresses before and after optimization
Comparison of alloy wheel stresses before and after optimization
180
160
140
120
100
80
60
40
20
0
153.06
180
160
140
120
100
80
60
40
20
0
153.06
CFT RFT IMP
CFT RFT IMP
65.3
65.3
75.3
75.3
13.24kg
12.70kg
13.24kg
12.70kg
58.82
58.82
Fig: 16 Comparison of stresses before and after optimization of the wheel rim
Fig: 16 Illustrate the graph between stresses to loads of the wheel, in which variation of initial base wheel design functionality test to weight-optimized wheel functionality tests has been shown, in which stress values were within the yield limit of the material.
-
-
CONCLUSION
A wheel rim of 17-inch is designed and analyzed for medium weight vehicle. The material used is aluminum alloy A356.2. Different tests like radial fatigue test, cornering fatigue test, and impact test are simulated to determine the stresses in the wheel rim.
The following conclusions are derived from the results:
-
Initially, base wheel rim had conducted various tests like cornering fatigue test, radial fatigue test, and impact test. The following are the maximum stresses observed in CFT is 75.3MPa, RFT is 58.82Mpa, and Impact test is 143.18 Mpa. The stress values were within the yield limit of the material.
-
The wheel rim is redesigned for better weight reduction and better performance. From the analysis, the following are the maximum stresses for an optimized wheel rim is CFT is 93.1MPa, RFT is 65.3Mpa, and Impact test is 153.06 MPa value stresses in the spoke cross-section was within the yield limit of the material. i.e., 186MPa hence, the optimized design is safe.
-
The weight of the Aluminum alloy wheel rim is optimized by reducing its volume from the inner side of the spokes and hub area is 13.24Kg to 12.70Kg therefore percentage weight reduction is
4.08 % (540gm) achieved. The optimized wheel rim had undergone various tests like cornering fatigue test, radial fatigue test, and impact test is observed to pass through all the requirements without compromising its performance.
There is a reduction in the mass is observed to be 540gm per wheel rim after optimization which accounts for 2.7kg per car by considering the spare wheel. This further reduces the overall weight of the body thus decreases in the cost of production and increases performance and better fuel efficiency.
REFERENCES
-
The Tire and Rim Association, Inc., 2014, 50 Drop center rim contour, J (ISO) Contour for 14, 15, 16, 17, 18, and 24 Diameter Designation.
-
Prashant Saxena, Varun Jain, Sharad K. Pradhan , 2019, Deformation behaviour analysis of different offset rim under different loading using finite element method, Materials Today:
Proceedings, https://doi.org/10.1016/j.matpr.2019.09.119
-
X Jiang, 2018, CAD Lightweight design and analysis of automobile wheel based on bending and radial loads, IOP Conf. Series: Materials Science and Engineering 372 012048 doi:10.1088/1757-899X/372/1/012048
-
Onur kocaturk, Fatih Yasin Elagoz, 2019, Optimization of Rigidity of Aluminum Alloy Wheel", The Seventh International Conference on Fracture fatigue and wear, Pg. 814-819.
-
P. Ramamurty Raju, B. Satyanarayana, 2006, Evaluation of Fatigue Life of Aluminum Alloy Wheels under Radial Loads ,
Engineering Failure Analysis, Vol -15, issue 5,791-800
-
Sourav Das, 2014, Design and Weight Optimization of Aluminium Alloy Wheel International Journal of Scientific and Research Publications, Volume 4, Issue 6, June ISSN 2250-3153.
-
X. Wang and X. Zhang, 2010, Simulation of dynamic cornering fatigue test of a steel passenger car wheel, Int. J. Fatigue, 32, No. 2, 434442
-
liang Yang, Haibo Yang, Hongjian Ta , Peng Hu, Xuewen Cheng and Junlong Lu, 2018, Impact test simulation and structural optimization of aluminum alloy A356.2 wheel hub, IOP Conf. Series: Journal of Physics: Conf. Series 1074 (2018) 012068 doi
:10.1088/1742-6596/1074/1/012068
-
G.V.R.Seshagiri Rao, Akashdeep Gupta,B. Prashanth, 2017, Impact Analysis of Aluminium Wheel© IAEME Publication Scopus Indexed, vol-8, Issue 7, 0976-6359.
-
Suraj L. Gondhali, Atul D. Dhale and Sunil Pagare, 2019, Static Structural Analysis of Car Rim by Finite Element Method, the International Conference on Intelligent Manufacturing and Automation, Pg.181-193.
-
M.K.Naidu, K.Ramji, S.Srinivasa Rao, 2012, Analytical approach for the prediction of steady-state tyre forces and moments under different normal pressure distributions", Journal of Terramechanics Vol.49, issue 5,281-289.
-
R.S. Khurmi and J.K. Gupta (2005) Machine Design, Eurasia Publishing House, (PVT) LTD.
-
R.K. Bansal (2010) Strength of Materials, Laxmi Publications, (PVT) LTD.
-
K.Mahadevan and Balaveera Reddy (2017) Design Data Hand Book", CBS Publishers and Distributors, (PVT) LTD.
-
SAE J328, (2016) Wheels-passenger car and light truck performance requirements and test procedures. Warren dale, (PA): Society of Automotive Engineers, Inc.,
-
SAE J175, (2014) Wheels-impact test procedures-road vehicles. Warren dale, (PA): Society of Automotive Engineers, Inc.,