
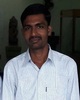
- Open Access
- Authors : Ashokkumar M , Kirankumar B. Balavalad , Ayappa Vajjaramatti
- Paper ID : IJERTV9IS050405
- Volume & Issue : Volume 09, Issue 05 (May 2020)
- Published (First Online): 19-05-2020
- ISSN (Online) : 2278-0181
- Publisher Name : IJERT
- License:
This work is licensed under a Creative Commons Attribution 4.0 International License
Design and Simulation of Silicon Nanowire based Nano Capacitive Pressure Sensor
Ashokkumar M Department of Electronics and Communication Engineering
Basaveshwar Engineering College Bagalkot, Karnataka, India
Kirankumar B. Balavalad Department of Electronics and Communication Engineering Basaveshwar Engineering College Bagalkot, Karnataka, India
Ayappa Vajjaramatti Department of Electronics and Communication Engineering Basaveshwar Engineering College Bagalkot, Karnataka, India
Abstract This paper presents a nano capacitive pressure sensor with enhanced sensitivity using silicon nanowires. The work presented here reports the design and simulation of nanowire based capacitive pressure sensor for human blood pressure measurement. Usually ordinary circulatory pressure of a human is 120/80 mmHg. This range can deviate if a person has hypertension or any other medical issues. Hence this pressure measurement is a very first thing that is done before any diagnosis or treatment. Many conventional devices exist to measure the pressure and also digital devices are now being commercialized for measurement. The accuracy with which these digital devices function is always a concern. In this paper we present a nanowire- based cap active pressure sensor which can operate efficiently over the pressure range of 0 to 300 mmHg. A equivalent pressure of around 40kPa pressure is applied on the sensor for measurement and the sensor shows a good sensitivity of 2.5 X 10- 6 pF/kPa.
Keywords- MEMS, sensor, pressure sensor, nanowire, capacitive pressure sensor.
-
INTRODUCTION
Nanotechnology is a very rapidly growing technology for development of nano sized sensors and actuators. There is a lot of works reported on MEMS based pressure sensors. Capacitive pressure sensors are well suited for low pressure sensing applications. Works in [1][2][3][4][5] describes the development and analyses of MEMS based capacitive pressure sensors. Silicon nano wire based capacitive pressure sensors are gaining high attentions because of their small dimensions and better sensitivity. Nano sensors are probably going to affect our economy and society a lot and the technology, practically identical to that of semiconductor innovation [6]. The nanowire is largely suitable development of biosensor/biomedical sensors as, the properties of silicon nanowires depicts that they are mechanically, electrically stable [7]. Silicon nanowires-based transistors are developed by authors in [8]. Silicon nanowires are largely used for biomedical sensing applications, one such example, were the sensor was developed for carotid blood pressure of horses [9][10]. Currently, most common disease is high blood pressure. This can be detected using miniature pressure sensors [11][12]. A micron sized capacitive pressure sensor with 3m electrode spacing was developed by authors [13]. Other applications were nanowire sensors are used are intraocular pressure, intracranial pressure measurements were mostly short-term measurements. For long term implantable pressure
sensors, the influence of biological environment should be considered [14][15][16][17]. Among the wide sector of biomedical sensing applications that the silicon nanowire sensors have been used for, some of them are applied to physiological body movements [18], human heartbeats [19], blood flow [20], pulse rate [21], drug delivery [22], protein [23], tumor detection [24], DNA sensing [25] and stem cell research [26]. The idea of using nanowires in piezoresistive pressure sensors has been reported in literature, but these sensors are suited for high pressure sensing. Capacitive sensors are reported to be best suitable for low pressure sensing applications. In this work we report the design and analysis of silicon nanowire based capacitive pressure sensor for human blood pressure monitoring. The pressure range considered varies from 0 to 300 mmHg which is approximately equal to 40kPa. The device provides a sensitivity of 2.5 X 10-6 pF/kPa. In the next sections the design, simulation and analysis aspects of the sensor is discussed.
-
DESIGN OF SILICON NANO CAPACITIVE PRESSURE SENSOR
The sensor is optimized for pressure sensing range of 0 to 40kPa using theory of plates [27]. The sensor is a parallel plate capacitive pressure sensor, using free and fixed electrodes respectively. The top (free electrode) is completely made up of array of silicon nanowires. Air is considered as the dielectric material. The bottom plate is made up of aluminum. Fig. 2.1 shows the designed sensor. The sensor is designed using COMSOL/Multiphysics. The dimensions used for the design and modelling of the sensor is mentioned in TABLE I.
Fig. 2.1. Model of Nano capacitive pressure sensor
TABLE I. DIMENSIONS OF THE NANO CAPACITIVE PRESSURE SENSOR
Name
Size
Length
300nm
Width
300nm
Thickness
2nm
Gap between two plates
10nm
Gap between two Nanowires
1nm
Material properties play a very important role in efficient behavior of these sensors. The materials properties considered for the simulation and analysis of the nano capacitive pressure sensor are mentioned in TABLE II. Only important properties are mentioned in TABLE II.
TABLE II. MATERIAL PROPERTIES
Parameter Name
Value
Density(kg/m3)
2320
Youngs Modulus (GPa)
169
Poissons Ratio
0.22
Relative Permittivity
4.5
The complete view of the sensor is shown in Fig. 2.2. The sensor image shown is the simulation model taken form COMSOL/Multiphysics. The top of the sensor showing the array of silicon nanowires is shown in Fig. 2.3.
Fig. 2.2. Sensor model
Fig. 2.3. Top view of the sensor showing array of silicon nanowires
-
SIMULATION AND RESULT DISCUSSION
-
Simulation Environment
The model shown in section II is simulated using COMSOL/Multiphysics using electromechanics physics. A square diaphragm is considered for simulation as it provides better stress/strain distribution. The model dimensions and the material properties used for simulation are mentioned in TABLE I and TABLE II., respectively. A free tetrahedral meshing is employed on the sensor for FEM analysis. The parameters considered are mentioned in TABLE III. As boundary conditions on top plate a known variable pressure of 0 to 40kPa is applied and temperature is kept constant at 25 . The sensor is biased with an external voltage of 1 V. Silicon nanowire array is placed as top electrode, were each nanowire is of 300nm in length, 1nm in width and thickness of 2nm. Each nanowire is separated with a separation of 1nm. The dielectric material has thickness of 10nm. The side view of the simulated sensor is shown in Fig. 3.1. The nano capacitive pressure sensor is simulated and analyzed for the parameters like, displacement, capacitance and sensitivity. The displacement of the sensor shows linear behavior with the applied pressure. Where as the capacitance varies nonlinearly. Further the results are discussed in the next subsection.
Fig. 3.1. Side view of the simulated nano capacitive pressure sensor
Sl. No.
Parameter
Size in (nm)
1.
Maximum element size
16
2.
Minimum element size
1
3.
Maximum element growth rate
1.2
4.
Resolution of the curvature
0.4
5.
Resolution of narrow regions
0.6
Sl. No.
Parameter
Size in (nm)
1.
Maximum element size
16
2.
Minimum element size
1
3.
Maximum element growth rate
1.2
4.
Resolution of the curvature
0.4
5.
Resolution of narrow regions
0.6
TABLE III. MESH PARAMETERS
-
Results and Discussions
The core sectional view of the sensor displacement for applied pressure is shown in Fig. 3.2. The displacement v/s applied pressure graph is shown in Fig. 3.3. Form the graph it can be observed that the displacement varies linearly with the applied pressure. The maximum displacement of the sensor at 40kPa of pressure is around 3.009 nm.
Fig. 3.3. Cross-sectional view of the displaced sensor with applied pressure
Fig. 3.4. Displacement (nm) v/s Applied pressure (MPa) plot of the nano capacitive pressure sensor.
The capacitance v/s applied pressure graph is presented in Fig.
3.5. It can be observed from the figure that the capacitance varies non-linearly with the applied pressure. The maximum
capacitance obtained at the pressure of 40kPa is around 1.2fF. The developed sensor has a sensitivity of 2.5 X 10-6 pF/kPa.
Fig. 3.5. Capacitance (F) v/s Applied Pressure (Pa) plot of nano capacitive pressure sensor.
-
-
CONCLUSION
The paper presents design and simulation of a silicon nanowire based nano capacitive pressure sensor for human blood pressure monitoring. The simulated sensor has a good sensitivity of 2.5 X 10-6 pF/kPa, which is very good. The sensor has a potential application in medical field for patient blood pressure monitoring. As it is in nano scale it can be easily mounted into the human body.
REFERENCES
-
Kirankumar B. Balavalad, B. G. Sheeparamatti, A Critical Review on MEMS Capacitive Pressure Sensors, Sensors & Transducers journal, IFSA publication, ISSN: 2306-8515, e-ISSN 1726-5479 Volume 187, Issue 4, pp-120-128, April 2015.
-
Kirankumar B Balavalad, B. G. Sheeparamatti. "Sensitivity Analysis of MEMS Capacitive Pressure Sensor with Different Diaphragm Geometries for High Pressure Applications", International Journal of Engineering Research & Technology (IJERT), ISSN: 2278-0181, Vol. 4
– Issue 03 (March – 2015), www.ijert.org
-
Vinay Shettar, Sneha Kotin, Kirankumar B. Balavalad & B. G. Sheeparamatti, Simulation of different MEMS Pressure Sensors, International J. of Multidispl. Research & Advcs. in Engg.(IJMRAE), ISSN 0975-7074, Vol. 6, No. II (April 2014), pp. 73-81, 2014.
-
Kirankumar B Balavalad, B G Sheeparamatti and Veekshit B Math Design and Simulation of MEMS Capacitive Pressure Sensor Array for Wide Range Pressure Measurement International Journal of Computer Applications 163(6):39-46, April 2017.
-
R. S. Jakati, K. B. Balavalad and B. G. Sheeparamatti, "Comparative analysis of different micro-pressure sensors using comsol multiphysics," 2016 International Conference on Electrical, Electronics, Communication, Computer and Optimization Techniques (ICEECCOT),
Mysuru, 2016, pp. 355-360.
doi: 10.1109/ICEECCOT.2016.7955245
-
B. Bhushan,Introduction to Nanotechnology, Springer Berlin Heidelberg New York (2006).
-
Michalis Florides https://www.researchgate.net/publication/311065506 Silicon_Nanowires_and_their_Applications, November 2016.
-
Yi Cui, Zhaohui Zhong, Deli Wang, Wayne U. Wang, and Charles M. Lieber, High Performance Silicon Nanowire Field Effect Transistors
NANO LETTERS 2003 Vol. 3, No. 2 149-152
-
Booth, J. A Short History of Blood Pressure Measurement; SAGE Publications: Sauzend Oakes, CA, USA, 1977; Volume 70, pp. 793799.
-
Druzhinin, A.; Lavitska, E.; Maryamova, I. Medical pressure sensors on the basis of silicon microcrystals and SOI layers. Sens. Actuators B Chem. 1999, 58, 415419. [CrossRef].
-
Eaton,W.P.; Smith, J.H. Micromachined pressure sensors: Review and recent developments. Smart Mater.Struct. 1997, 6, 530. [CrossRef].
-
Ferrario, D.; Falhi, A.; Grossenbacher, O.; Sola, J.; Proenca, M.; Porchet, J.-A.; Allemann, Y.; Rimoldi, S.F.; Sartori, C. Noninvasive and Nonocclusive Blood Pressure Estimation Via a Chest Sensor. IEEE Trans. Biomed. Eng. 2013, 60, 35053513.
-
Chau, H.-L.; Wise, K. An ultraminiature solid-state pressure sensor for a cardiovascular catheter. IEEE Trans. Electron Devices 1988, 35, 2355 2362. [CrossRef].
-
Borges-González, J.; Kousse_, C.J.; Nielsen, C.B. Organic semiconductors for biological sensing. J. Mater. Chem. C 2019, 7, 1111 1130. [CrossRef].
-
Potkay, J.A. Long term, implantable blood pressure monitoring systems. Biomed. Microdevices 2008, 10, 379392. [CrossRef].
-
Yang, C.; Zhao, C.; Wold, L.; Kaufman, K.R. Biocompatibility of a physiological pressure sensor. Biosens. Bioelectron. 2003, 19, 5158. [CrossRef].
-
Peishuai Song, Zhe Ma, Jing Ma, Liangliang Yang, Jiangtao Wei, Yongmei Zhao, Mingliang Zhang, Fuhua Yang and Xiaodong Wang, Recent Progress of Miniature MEMS Pressure Sensors, Micromachines 2020, 11, 56; doi:10.3390/mi11010056 www.mdpi.com/journal/micromachines.
-
Chen, H.; Xue, M.; Mei, Z.; Bambang Oetomo, S.; Chen, W. A review of wearable sensor systems for monitoring body movements of neonates. Sensors 2016, 16, 2134. [CrossRef] [PubMed].
-
19. Ng, J.; Sahakian, A.V.; Swiryn, S. Sensing and Documentation of Body Position during Ambulatory ECG Monitoring; IEEE: Piscataway, NJ, USA, 2000.
-
Iwasaki, W.; Nogami, H.; Takeuchi, S.; Furue, M.; Higurashi, E.; Sawada, R. Detection of site-specific blood flow variation in humans during running by a wearable laser Doppler flowmeter. Sensors 2015, 15, 2550725519. [CrossRef] [PubMed].
-
Nomura, S.; Hanasaka, Y.; Katsuda, Y.; Hirota, R.; Ishiguro, T.; Takada, K.; Uryu, M.; Ogawa, H. Human pulse detection using multiple silicon microphones toward estimation of physical condition. Inf. Technol. J. 2012, 11, 476479. [CrossRef].
-
Li, Y.Y.; Cunin, F.; Link, J.R.; Gao, T.; Betts, R.E.; Reiver, S.H.; Chin, V.; Bhatia, S.N.; Sailor, M.J. Polymer replicas of photonic porous silicon for sensing and drug delivery applications. Science 2003, 299, 2045 2047. [CrossRef] [PubMed].
-
Mariani, S.; Pino, L.; Strambini, L.M.; Tedeschi, L.; Barillaro, G. 10000- fold improvement in protein detection using nanostructured porous silicon interferometric aptasensors. ACS Sens. 2016, 1, 14711479. [CrossRef].
-
Washburn, A.L.; Shia, W.W.; Lenkeit, K.A.; Lee, S.-H.; Bailey, R.C. Multiplexed cancer biomarker detection using chip-integrated silicon photonic sensor arrays. Analyst 2016, 141, 53585365. [CrossRef].
-
Fritz, J.; Cooper, E.B.; Gaudet, S.; Sorger, P.K.; Manalis, S.R. Electronic detection of DNA by its intrinsic molecular charge. Proc. Natl. Acad. Sci. USA 2002, 99, 1414214146. [CrossRef].
-
Rajagopalan, J.; Saif, M.T.A.MEMSsensors and microsystems for cell mechanobiology. J. Micromech. Microeng. 2011, 21, 054002. [CrossRef].
-
K. B. Balavalad and B. G. Sheeparamatti, "Design simulation and analysis of piezoresistive micro pressure sensor for pressure range of 0
to 1MPa,quot; 2016 International Conference on Electrical, Electronics, Communication, Computer and Optimization Techniques (ICEECCOT), Mysuru, 2016, pp. 345-349.
doi: 10.1109/ICEECCOT.2016.7955243.