
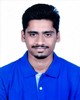
- Open Access
- Authors : Sarvesh Bhalchandra Telang , Tejas Prakash Vaidya
- Paper ID : IJERTV10IS090066
- Volume & Issue : Volume 10, Issue 09 (September 2021)
- Published (First Online): 14-09-2021
- ISSN (Online) : 2278-0181
- Publisher Name : IJERT
- License:
This work is licensed under a Creative Commons Attribution 4.0 International License
Design and Optimization of a Vacuum-Assisted Power Brake System for Light Commercial Vehicles
Sarvesh Bhalchandra Telang1
Dept. of Mechanical Engineering
NBN Sinhagad School of Engineering, Pune, India Savitribai Phule Pune University
Tejas Prakash Vaidya2
Dept. of Mechanical Engineering
RMD Sinhagad School of Engineering, Pune, India Savitribai Phule Pune University
Abstract The brake system is the most crucial system in automobiles that ensures road safety. Vacuum brake boosters are now widely used in a variety of vehicle types, ranging from small cars to heavy commercial vehicles. Improvements in the braking systems will only be possible through basic research, the application of sound engineering concepts, and testing, resulting in small but significant design changes. Following this, the work presented in this paper focuses on the design and development of a Vacuum-assisted Power Brake System for Light Commercial Vehicles (LCVs). This is carried out by comprehending and troubleshooting various current problems associated with the system, designing and modeling the brake system's components using SolidWorks, which include the brake booster, master cylinder, and brake pedal, analyzing a variety of suitable materials by utilizing ANSYS Workbench software and testing the optimized model. During this, we calculated and tested the system while keeping the critical values of parameters for LCV in mind. As a result, the best vacuum brake system configuration for the LCV is determined considering system performance, cost, and complexity.
Keywords Brake Booster, Light Commercial Vehicles, Master cylinder, Power Braking System
-
INTRODUCTION
Many vehicles today use vacuum-assisted brake systems because of their simple design and use of intake vacuum to multiply brake force. In this system, a vacuum diaphragm is linked to the vacuum port of the engine intake manifold. The brake booster also plays a crucial role when stopping a car with disc brakes. This unit assists in stopping the vehicle by providing additional force to the brakes. Without it, stopping distances would be much longer, placing the driver at the risk of a collision while performing an emergency stop. The brake booster is powered by a vacuum system connected to the engine's intake manifold. When the brake pedal is pushed, a vacuum is circulated through it, which applies pressure to the hydraulic brake lines. It multiplies the applied force by nearly two to three times. This lowers the amount of pedal effort needed to bring the vehicle to a stop, making braking easier and safer. However, when it comes to the brake booster of a light commercial vehicle, there are a few problems that must be discussed. The failure of a diaphragm or a check valve may result in a loss of power assist. Partial intake vacuum, the smaller size of the diaphragm, leakage in the master cylinder, or the injection of brake fluid into the booster is just a few of the factors that can reduce the effectiveness of the brake
booster. In this paper, we present an optimized system that addresses these current issues by proposing major design changes and material improvements, taking into account all of the parameters that can influence the efficiency of the commercial vehicle braking system.
-
METHEDOLOGY
-
Problem Identified
In the present system, concerns have been raised about vacuum brake boosters of LCVs, which are responsible for the increased stopping distances and, as a result, the risk of accidents. The main source of concern is low vacuum pressure from the engine. A loose or cracked hose, which lets air into the system, is typically the problem. Vacuum leaks cause the engine to idle poorly and pause while accelerating.
Another issue is, a large internal diaphragm in the vacuum brake booster gets harden and develops internal leaks over time. This problem is much more prevalent in cold, dry climates, where the diaphragm material degrades more quickly. However, the larger the diaphragm, the greater the amount of power assist. To solve this issue, we have designed a large-sized diaphragm with appropriate material, which is vulnerable to leaks. Furthermore, frequent breakdowns are found due to damaged internal parts or a blocked check valve, which is possibly due to broken grommets, causing vacuum leak from the booster and ultimately resulting in less brake power amplification. Blockages in the check valve allow air to penetrate the brake fluid and form air bubbles, lowering hydraulic pressure in the master cylinder, resulting in less efficient braking.
-
Need for Study
When it comes to braking in order to avoid an accident or harm, every millisecond matters. The driver's reaction and response time is greatly reduced since brake boosters enable effective breaking with much less force required to exert on the pedal. In light commercial vehicles, when the brake booster fails it can draw excess vacuum from the engine.
This happens when the diaphragm fails, allowing air to bypass the seal. The engine then feels as if it will stall when the brakes are applied, and the idle will drop. It may make it difficult to push the brake pedal, resulting in a long time to
stop the vehicle. Stalled engines can cause serious problems in addition to decreased brake efficiency, necessitating further research. In addition, many brake booster OEMs are accelerating the adoption of advanced materials to reduce the weight of the system. Following that, commercial vehicle manufacturers are implementing progressive weight reduction as part of their strategy to meet fuel economy targets. This industry is constantly on the lookout for ways to reduce weight while improving performance and safety. This can enhance commercial vehicle performance in all of the following aspects: fuel economy, acceleration, braking as well as emission reductions.
-
-
DESIGN OF BRAKE BOOSTER
-
Selection of Parameters
To commence with, we considered the parameters for a light commercial vehicles brake system such that the design can withstand the critical condition of failure. The table below summarizes the most optimally chosen parameters:
Table- I: System Parameters
Parameters
Values
Gross Vehicle Weight of Light Commercial Vehicle (Kg)
3500
Vehicle Speed (km/h)
100
(27.7778 m/s)
Braking Distance (m)
114.7
Reaction Distance (m)
69.5
Stopping Distance (m) = Braking dist. + Reaction dist.
184.2
Vehicle Acceleration (m/s2)
3.4
Driver Reaction time (s)
2.5
Pedal Force Fp (N)
500
Pedal lever ratio lp
4
-
Stopping distance and Required Output Force Calculation
-
Stopping distance:
The length of the path ahead that is visible to the driver is referred to as sight distance. On a highway, the available sight distance should be long enough for a vehicle moving at or close to the designed speed to stop completely before hitting an obstacle in the direction. While longer lengths of visible roadway are ideal, the desired sight distance at each point along the roadway should be sufficient enough for even a below-average driver to stop the vehicle. Stopping distance is the ombination of two distances: (1) the first is the distance covered by the vehicle from that time the driver notices an obstacle which would need a stop till the time when the brake pedal is pressed; and (2) The second is the distance between applied brakes and when the vehicle comes to a complete stop. These are known as the brake reaction distance and the braking distance, respectively.
-
Brake Reaction Distance:
seconds for brake reaction time reaches the 90th percentile. It is deemed appropriate for conditions that are more complicated than those used in road tests.
-
Braking Distance:
The following equation can be used to calculate the approximate braking distance of a vehicle driving on a level roadway at the design speed of the roadway:
Fig. 1 Braking Distance Formula
Deceleration rates of more than 3.4 m/s2 [11.2 ft/s2] are experienced by approximately 90% of all drivers.
d = 0.039 (1002/ 3.4) = 114.7
Stopping Distance = Braking dist. + Reaction dist. = 114.7 + 69.5 = 184.2 m
The determined sight distance is based on a brake reaction time of 2.5 seconds and a deceleration rate of 3.4 m/s2 [11.2 ft/s2].
Fig. 2 Stopping Distance Standard Table
-
Output Force required to stop a vehicle of 3.5 ton weight travelling at 100 km/h:
Kinetic Energy = ½ mv2
Kinetic Energy = ½ *3500 * 27.7782 = 1350310.802 J
As previously stated, the brake reaction time used in design should be wide enough to account for practically all drivers' reaction times under most highway conditions. Based on the results of the study, most drivers have 2.5-second brake reaction times to stop sight situations, as well as for elderly drivers. For all drivers, the suggested design criterion of 2.5
Fout Fout Fout
= Kinetic Energy/ Stopping Distance
= 1350310.802/ 184.2 = 7330.6775
= 7330.6775 N
T = Stopping Distance/ Vehicle Speed T = 184.2/ 27.7778 = 6.631 sec.
-
-
Booster Force Calculation:
The power brake system is supposed to provide the required output force to bring the vehicle to a complete stop at the desired speed. The input pedal force must be amplified using vacuum and hydraulic pressure produced in the master cylinder in order to achieve this force. Vacuum boosters raise braking system gain by eight to nine times for most heavy commercial vehicles and three to four times for light commercial vehicles. The effect of the pedal force is increased eight times. While this high gain allows for optimum braking effectiveness with limited pedal forces, if the booster fails, the driver will most likely be unable to generate enough pedal force to decelerate the vehicle to a safe level. Therefore, the brake booster must be responsive enough for the driver to modulate braking effectiveness when low pedal forces are present. In light of this, we've chosen an optimal boost ratio that is practical for a power brake system with sufficient vacuum.
-
Boost Ratio (B):
The boost ratio B is defined as the ratio of the pushrod force against the master cylinder piston to the pedal effort input into the booster,
Fout = Fplp+FA
FA = Fout – Fplp = 7330.6775 500 * 4 FA = 5330.6775 N
Where FA = Booster force, N Fp = Pedal force, N
lp = Pedal lever ratio = X/Y = 330.44/82.57= 4
B = (Fplp+FA)/Fp
B = (500*4 + 5330.6775)/ (500*4) = 3.6653 4
The boost ratio can be calculated using the basic mastervac measurements and spring forces. The reaction disc's outer diameter is Do. The reaction piston's diameter is Dr.
The following calculations are for a single-diaphragm mastervac with a 250 mm (9.8 in.) diameter assist piston. The reaction disc and piston have diameters of 43 and 31 mm (1.693 in. and 1.22 in. respectively). The boost assist produces a push rod force, which is computed first.
-
Effective booster force (FB):
The effective booster area AB is equal to the booster area minus the pushrod area,
AB = /4 (250)2 /4 (12)2 = 489.743 cm2
[AB = /4 (9.8)2 /4 (0.424)2 = 75.288 in2]Where a pushrod diameter is 12 mm or 1.2 cm (0.424 in.)
For an effective vacuum of 7.928 N/cm2 (11.47 psi; 80% of maximum) and a mechanical efficiency of 0.95, the booster force is:
FB = (AB) * (Effective Vacuum) * mechanical Efficiency FB = 489.743*7.928*0.95 = 3688.548 N
The diaphragm piston return spring force opposes the boost motion, so the effective booster force FB is smaller. Hence,
FB = (FB) (Spring Return Force) = 3688.548- 155.7 FB = 3532.848 N
Where, a return spring force is considered as 155.7 N (35 lb). The computations thus far show that the booster portion produces a hydraulic pushrod force of 3532.848N. The manually produced force against the hydraulic pushrod is calculated next.
-
Manually Produced force (Fr):
The rubber reaction disc functions similarly like pressurized hydraulic fluid. The pressure in the reaction disc pr is equal to the effective booster force divided by the difference in cross- sectional area of the reaction disc A2 and the reaction piston A1,
pr = (FB)/ /4 ((A2)2 (A1)2)
pr = (3532.848) (4)/ ((4.3)2 (3.1)2) = 506.549 N/cm2
Any surface in contact with the reaction disc is subjected to the control pressure pr. As the piston pushes a part of the reaction disc, the reaction piston force is the product of the reaction piston area A1 and the pressure, hence
Fr = pr Al = 506.549 X (/4) * 3.12 = 3823.274 N
The total force on the master cylinder piston and, hence, the brake line pressure producing force is given by the sum of the effective booster force (FB) and manually produced input force (Fr):
Ftotal = 3532.848 + 3823.274 = 7356.122 N > 7330.6775 N
Therefore, Ftotal > Fout
Hence, the designed vacuum brake booster is capable of producing greater output force than is required.
-
-
Components of the System:
Table- II: System Components
Sr. no
Component
Qty
Sr. no
Component
Qty
1
Brake pedal
1
18
Hydraulic Push Rod
1
2
Brake pedal support bracket
1
19
Diaphragm Return Spring
1
3
Support Bracket Nut
4
20
Vacuum Check Valve
1
4
Pedal Pivot Pin
1
21
Master Cylinder
1
5
Pedal Bolt
1
22
Master Cylinder Nut
2
6
Clevis Lock nut
1
23
C Ring
1
7
Valve Rod
1
24
Primary Piston
1
8
Spacer
1
25
Primary seal
2
9
Valve Body
1
26
Primary Piston Spring
1
10
Dust Boot
1
27
Secondary Piston
1
11
Front Booster Casing
1
28
Secondary seal
2
12
Rear Booster Casing
1
29
Secondary Piston Spring
1
13
Poppet Spring
1
td>
30
Brake Oil Reservoir
1
14
Valve Return Spring
1
31
Reservoir Grommets
2
15
Reaction Disc
1
32
Reservoir Diaphragm
1
16
Diaphragm
1
33
Reservoir Cover
1
17
Diaphragm Plate
1
34
Reservoir Lid
2
4
6
5
Fig. 3 Brake Booster Assembly Isometric View
21 30
22 18
11 9 15 8 2
29 3
27 26 24
34
33
19 12
17 16
7
10 14
Fig. 4 Assembly Sectional View
32 13
1
31 28
25
23
Fig. 5 Master Cylinder Exploded View
Y
X
Fig. 6 Brake Pedal Draft
Fig. 7 Rear Booster Casing Draft Fig. 8 Valve Body Draft
20
(Ref. Table 2)
Fig. 9 Master Cylinder Draft Fig. 10 Front Booster Casing Draft
Fig. 11 Vacuum Check Valve
Fig. 12 Assembly Exploded View
-
Analysis
-
Brake Pedal Analysis
Fig. 13 Total Deformation Fig. 15 Maximum Principal Stress
Fig. 14 Equivalent Stress Fig. 16 Factor of Safety
-
Master Cylinder Analysis
Fig. 17 Total Deformation
Fig. 18 Equivalent Stress
Fig. 19 Maximum Principal Stress
Fig. 20 Factor of Safety
-
Material Study
-
Brake Pedal
Properti
-es
Materials
Stainless Steel
Aluminium
Composite Material
Grade
Fe 410
E- 34
D- 513
EDD- 1079
AlZnMg 7204
AlCuM g1
AlSi 6009
AlZn Mg 7075
PP GF30
%
PA 6 GF 30%
PA 66 GF30%
ABS GF30
%
Density (kg/m3)
7890
7924
7848
7975
2900
2800
2710
2850
1140
1350
1370
1190
Youngs Modulus (mpa)
2E5
2.06E5
2.1E5
2.2E5
0.7E5
0.72E5
0.69E5
0.71E5
5000
0.15E5
0.15E5
6000
Poisson s Ratio
0.315
0.34
0.35
0.34
0.33
0.32
0.29
0.31
0.315
0.35
0.35
0.34
Yield Strength (mpa)
283.8
360
205.1
334.1
310
230
228
450
100
190
160
80
Ultimate Strength (mpa)
387.8
450.8
367.8
340.5
380
370
340
530
0
0
0
0
Master Cylinder
Properti
-es
Materials
Stainless Steel
Aluminium
Cast Iron
Grade
Fe 410
Al-Si5Cu3
Ductile cast iron ASTM A395 grade
Density (kg/m3)
7890
2750
7800
Youngs Modulus (mpa)
200000
71000
152000
Poisson s Ratio
0.315
0.333
0.27
Yield Strength (mpa)
283.78
228
414
Ultimate Strength (mpa)
387.79
290
276
Brake Pedal
Properti
-es
Materials
Stainless Steel
Aluminium
Composite Material
Grade
Fe 410
E- 34
D- 513
EDD- 1079
AlZnMg 7204
AlCuM g1
AlSi 6009
AlZn Mg 7075
PP GF30
%
PA 6 GF 30%
PA 66 GF30%
ABS GF30
%
Density (kg/m3)
7890
7924
7848
7975
2900
2800
2710
2850
1140
1350
1370
1190
Youngs Modulus (mpa)
2E5
2.06E5
2.1E5
2.2E5
0.7E5
0.72E5
0.69E5
0.71E5
5000
0.15E5
0.15E5
6000
Poisson s Ratio
0.315
0.34
0.35
0.34
0.33
0.32
0.29
0.31
0.315
0.35
0.35
0.34
Yield Strength (mpa)
283.8
360
205.1
334.1
310
230
228
450
100
190
160
80
Ultimate Strength (mpa)
387.8
450.8
367.8
340.5
380
370
340
530
0
0
0
0
Master Cylinder
Properti
-es
Materials
Stainless Steel
Aluminium
Cast Iron
Grade
Fe 410
Al-Si5Cu3
Ductile cast iron ASTM A395 grade
Density (kg/m3)
7890
2750
7800
Youngs Modulus (mpa)
200000
71000
152000
Poisson s Ratio
0.315
0.333
0.27
Yield Strength (mpa)
283.78
228
414
Ultimate Strength (mpa)
387.79
290
276
Table- III: Material Properties
Table- IV: Chemical Composition of alloys
Aluminium alloys
AlZnMg
AlCuMg
Alsi 6009
AlSi5Cu3
Chemical Composition
Si- 0.4%
Fe- 0.98%
Al- 96.15%
Cu- 4%
Fe- 0.5%
Si- 0.05%
Si- 1%
Mg- 0.2%
Cu- 2%
Mn- 0.04%
Fe- 0.05%
Si- 6%
Mn- 0.3%
Ti- 0.02%
Mg- 0.8%
Fe- 0.8%
Mg- 2.9%
Al- 93.8%
Zn- 0.25%
Mn- 0.6%
Cr- 0.28%
Cu- 2.33%
Mn- 0.8%
Ni- 0.3%
Zn- 6.1%
Ni- 1.04%
Cu- 0.6%
Zn- 0.5%
Ti- 0.2%
Mg- 1.65%
Cr- 0.1%
Pb- 0.1%
Other- 0.15%
Zn- 0.02%
Ti-0.1%
Sn- 0.1%
Al- 87.17%
Other- 0.15%
Ti- 0.2%
Al- 87.05%
Other- 0.15%
Table- V: Analysis Results
Brake Pedal Analysis
Master Cylinder Analysis
Stainless Steel
Stainless Steel
Material
Fe 410
(2.4058 Kg)
E- 34
(2.4160 Kg)
D-513 (2.3928 Kg)
EDD- 1079
(2.4319 Kg)
Material
Steel Fe 410
(1.4391 kg)
Force Applied (N)
1000N
1000N
1000N
1000N
Pressure Applied (MPA)
8 MPA
Min
Max
Min
Max
Min
Max
Min
Max
Min
Max
Total Deformation (mm)
0
1.9388
0
1.8854
0
1.7811
0
1.6989
Total Deformation (mm)
0
0.0045105
Von-Mises Stress (MPA)
0.00913
129.72
0.0095106
129.12
0.006752
124.92
0.0068617
125.17
Von-Mises Stress (MPA)
1.55E-05
180.41
Maximum Principal Stress (MPA)
-14.788
131.52
-19.683
135.03
-20.38
135.4
-18.31
133.87
Maximum Principal Stress (MPA)
-91.832
83.223
Factor of Safety
2.1876
15
2.788
15
1.6421
15
2.6697
15
Factor of Safety
1.573
15
Aluminium
Aluminium
Material
AlZnMg(7204) (0.88427 kg)
AlCuMg1 (0.85377 kg)
AlSi(6009) (0.82633 kg)
AlZnMg(7075) (0.86902 kg)
Material
Al-Si5Cu3
( 0.50158 Kg)
Force Applied (N)
1000N
1000N
1000N
1000N
Pressure Applied (MPA)
8 MPA
Min
Max
Min
Max
Min
Max
Min
Max
Min
Max
Total Deformation (mm)
0
5.3357
0
5.3872
0
5.6103
0
5.4595
Total Deformation (mm)
0
0.01265
Von-Mises Stress (MPA)
0.00701
125.41
0.0092024
129.61
0.008843
130.29
0.0090686
129.84
Von-Mises Stress (MPA)
2.31E-05
173.91
Maximum Principal Stress (MPA)
-16.37
132.43
-15.709
132.19
-10.533
128.47
-13.891
130.88
Maximum Principal Stress (MPA)
-99.329
84.853
Factor of Safety
2.4719
15
1.7746
15
1.75
15
3.4658
15
Factor of Safety
1.311
15
Composite Material
Composite Material
Material
PP GF30% (0.44761 kg)
PA6 GF30% (0.41164 kg)
PA66 GF30% (0.41774 kg)
ABS GF30% (0.47285 kg)
Material
Ductile cast iron ASTM A395 grade (1.4227 Kg)
Force Applied (N)
1000N
1000N
1000N
1000N
Pressure Applied (MPA)
8 MPA
Min
Max
Min
Max
Min
Max
Min
Max
Min
Max
Total Deformation (mm)
0
77.551
0
24.953
0
25.909
0
64.73
Total Deformation (mm)
0
0.005988
Von-Mises Stress (MPA)
0.00913
129.72
0.00697
125.32
0.009685
128.87
0.0095106
129.12
Von-Mises Stress (MPA)
7.58E-06
195.61
Maximum Principal Stress (MPA)
-14.788
131.52
-18.359
133.93
-21.869
136.59
-19.683
135.03
Maximum Principal Stress (MPA)
-75.291
79.321
Factor of Safety
0.77086
15
1.5161
15
1.2416
15
0.61957
15
Factor of Safety
1.411
15
Selected Material
Fig. 21 Comparison of Brake Pedal Analysis Results using Line graph
-
-
RESULTS AND DISCUSSION
The primary objective of brake pedal analysis was to reduce the total mass by selecting appropriate material and optimising system parameters while ensuring design safety. When it comes to the mechanical strength of the brake pedal and its associated structure for LCVs, a value of 1500N is considered the force that the structure should be able to withstand without failure. Such a large value of force is only possible in very rare cases, and only with certain leg orientations in the seated position. However, the average force applied by the driver on the brake pedal during moderate braking of a LCV is usually less than 500N. In the event of a vacuum booster failure, the force can be in the range of 800- 1000N. Taking this into consideration, we applied a total force of 1000N on the brake pedal. For this amount of pedal force, the master cylinder is expected to withstand at least 8 MPA of pressure. As shown in the aforementioned material study table (Ref. Table 3), we have examined materials that are currently active in the market and widely used in the automotive industry. The line graph compares the results of analysis for different materials. It clearly demonstrates the difference in stress values, values of overall deformation, and safety factor.
To keep the pedal light, cost-effective and capable of meeting challenging OEM specs, we have selected Polyamide 6 GF30% material. This material has a safety factor of 1.5161, which means it can withstand 1.5 times the applied load of
1000N, meeting the requirement. According to the analysis results, a polyamide brake pedal weighs 0.41 kg, which is nearly 83% less than a conventional steel pedal (2.4 kg) and 52% less than aluminium brake pedal (0.85 kg).
Despite this, the strength and stress values of a polyamide brake pedal are comparable to those of steel and aluminium for the same applied force. Aside from that, Polyamide 6 GF30% is very cost effective due to its ease of manufacture, low tooling cost, light weight, and low transportation and logistics costs. In addition, it has higher flexural strength and shock resistance than steel and aluminium.
Most OEMs prefer Cast Iron and Aluminium as a standard material for Brake master cylinders. As these materials have good castability and can be surface treated with alumite coating for hardness and anti-rust treatment. Aluminium has a high wear resistance, which aids in preventing piston wear caused by brake oil pressure during each brake stroke. It also has a high thermal conductivity, which helps in lowering the temperature of the mater cylinder's internal chamber. The Al- Si5Cu3 alloy is preferred due to its light weight and high pitting & corrosion resistance. The use of anodic and heat treatment can significantly improve corrosion resistance of this alloy. The stresses and deformation of Al-Si5Cu3 are within the acceptable limits. The graph shows that, the safety factor at
8 MPA pressure is 1.311, indicating that it can effectively tolerate 8 MPA pressure.
Despite having a similar safety factor, the aluminium master cylinder weighs 0.50158 kg, which is roughly 65% less than steel and cast-iron master cylinder. This weight reduction also contributes in lowering the fuel consumption. This material also allows for a smooth bore, which reduces wear caused by each brake stroke and results in a longer service life.
-
CONCLUSION
In this study, the efficient design of a vacuum assisted brake booster for a light commercial vehicle (LCV) is presented, considering performance, cost, weight, and complexity. The current system is examined, with a focus on the existing concerns with brake booster of light commercial vehicles. Accordingly, changes have been made to the design. The system is modified based on critical parameters such as vehicle stopping distance, driver reaction time, deceleration rate, vehicle gross weight, input pedal force, and pedal lever ratio. The total booster force is calculated and ensured to be greater than the output force required to stop a vehicle weighing 3.5 tonnes travelling at 100 km/hr. Based on the final values, the 3d modelling is done by using Solidworks and Autodesk Fusion 360 softwares. The design modifications are shown in the drafts. The material analysis is performed using ANSYS 19.0 software on various materials and the results are compared using a line chart to draw the distinction in stress values, total deformation, and factor of safety. By using Polyamide 6 GF30% material, the weight of the brake pedal is reduced by 83% compared to conventional steel and 52% compared to aluminium. This material was chosen for its ease of manufacture, large-scale production in one cycle with injection moulding, low tooling cost, and high flexural strength. The weight of the master cylinder is reduced by nearly 65% when compared to steel and cast iron by using AlSi5Cu3 (LM4) alloy, which was preferred for its light weight, high corrosive and wear resistance, and high thermal conductivity.
REFERENCES
-
Rudolf Limpert, Brake Design and Safety, Third Edition R-398, Published by SAE International with a Product Code of R-398, ISBN of 978-0-7680-3438-7 (2011)
-
American Association of State Highway and Transportation Officials, A POLICY on GEOMETRIC DESIGN of HIGHWAYS and STREETS, ISBN: 1-56051-156-7, (2001)
-
Andrew Day, Braking of Road Vehicles ISBN: 978-0-12-397314-6
-
S. Senthil Gavaskar, P. K. Devan, T. G Loganathan, Failure Analysis of Brake System in Light Commercial Vehicles using SQC Tools, International Journal of Engineering Research & Technology Vol. 3 Issue 11, ISSN: 2278-0181, November (2014)
-
E. Ajay Kumar, B. Praveen Kumar, Analysis of Master Cylinder of Hydraulic Braking System Using ANSYS, International Journal of Engineering Science and Computing Volume 6 Issue No.10 October (2016)
-
Dr. K. K. Dhande, Prof .N. I. Jamadar, Sandeep Ghatge, Conceptual Design and Analysis of Brake Pedal Profile, International Journal of Innovative Research in Science, Engineering and Technology Vol. 3, Issue 11, November (2014)
-
Ramprsad S. Krishnamachari, DESIGN MODEL OF A VACUUM- ASSISTED HYDRAULIC BRAKING SYSTEM, Department of Mechanical Engineering and Applied Mechanics the University of Michigan, Ann Arbor Ann Arbor, MI 48109-2125 Technical Report 96-12 October, (1996)
-
Luke Deptula and Alaa Noah, Assessing the Costs & Benefits of Effective Lightweighting Technologies, Center for Automotive Research, July (2015)
-
Martinho Soares, Metal Morphosis, Optimization of joining processes for new automotive metal-composite hybrid parts, Ghent, 24/02/2016
https://www.metalmorphosis.eu/images/News/Content_Files/Final_Eve nt_PPT/6_Automotive%20hybrid%20components%20-
%20composite%20brake%20pedal%20joined%20by%20EMP%20tech nology.pdf
-
C. H. Hughes, Ductile Iron, Metals Handbook, American Society for Metals , Vol. 15, 9th edition (1988)
-
American Society of Automotive Engineering Inc., Warrendale, PA, (1989)
-
Elvira Khafizova, Rinat Islamgaliev, and Vil Sitdikov, Strength and Fatigue of an ultrafine-grained Al-Cu-Mg alloy, Ufa State Aviation Technical University, Ufa, Russia (2017)
-
Rob Thompson, Automotive Maintenance & Light Repair, Chapter 10 Brake System Principles, ISBN-13: 978-1-337-56439-7 (2019).
-
MIM Sargini, SH Masood, Suresh Palanisami, Elammaran Jayamani and Ajay Kapoor, Finite element Analysis of Automotive Arm Brake Pedal for Rapid Manufacturing, Department of Mechanical and Product Design Engineering, Swinburne University of Technology, Malaysia, (2020)
-
-
https://www.repairsmith.com/i/blog/brake-booster-check-valve/
AUTHORS PROFILE
Sarvesh Bhalchandra Telang
B.E., Mechanical Engineer, NBN Sinhgad School of Engineering, Pune, Maharashtra, India. The author has
1.5 years of Industrial experience in materials, manufacturing and application engineering field, 1 Research paper published in international conference, currently pursuing a Master's degree in Commercial Vehicle Technology at TU Kaiserslautern, Germany. Research interests are in Automotive Design and Manufacturing, Machine Learning, Robotics, Numerical Methods and CAE.
Tejas Prakash Vaidya
B.E., Mechanical Engineer, RMD Sinhgad School of Engineering, Pune, Maharashtra, India. The author has
2.5 years of Industrial experience in Commercial Vehicles Business Unit in Launch Management department, currently pursuing a Master's degree in Operational Excellence (M.B.A and Engg.) at Hof University of Applied Sciences, Germany. Research interests are in New Product Development, Automotive Design, Production Management, Machine Learning, Numerical Methods and CAE.