
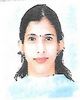
- Open Access
- Authors : Shilpa Suhas Gaikwad , Prof. Shrikant Velankar
- Paper ID : IJERTV10IS060305
- Volume & Issue : Volume 10, Issue 06 (June 2021)
- Published (First Online): 26-06-2021
- ISSN (Online) : 2278-0181
- Publisher Name : IJERT
- License:
This work is licensed under a Creative Commons Attribution 4.0 International License
Design and Implementation of Multimode, Multipurpose Solar Electric Bicycle
Ms. Shilpa Suhas Gaikwad
Dept. of Electronics and Telecommunication Engineering, Vidyalankar Institute of Technology,
Mumbai, India
Prof. Shrikant Velankar
Dept. of Electronics Engineering, Vidyalankar Institute of Technology, Mumbai, India
AbstractThe source of energy required for vehicles like petrol, diesels prices are increasing consistently. The sources of energy which are used for vehicles nowadays, produces pollution on large scale and are responsible for global warming. These non- renewable sources are depleted at very fast rate. We can use solar energy which is pure, environmentally friendly, and everlasting renewable energy source. Solar energy can be converted to electrical energy by using Photovoltaic effect and it is used in solar panels. These Solar panels can be used as an alternate source of energy in electric vehicle. By considering all class of the society as well as to deal with environmental pollution this bicycle is designed. To avoid pollution, electric vehicles are used as a solution. The electric vehicles available in the market are not optimized due to the absence of practical aspect knowledge. If we know the practical aspect, optimization can be achieved. Multimode, multipurpose solar electric bicycle is driven by DC motor installed near rear wheel. This DC motor is controlled by motor controller and it is operated by the charge available from solar panel or 230V A.C mains. This bicycle is optimized by using Arduino mega electronic circuitry. It has three modes; one is Manual cycling mode, Electric Manual mode, and Electric Auto cycling mode. In Manual mode, person must paddle the cycle manually and that energy can be used for bicycle lights. In electric manual mode, the data from throttle is applied to Arduino and accordingly speed is adjusted. In Electric Auto mode the person must rest feet on paddle. In this case data from accelerometer is given to the microcontroller and based on the X,Y and Z co-ordinate data of accelerometer, microcontroller control motor controller by providing PWM output.
Keywords Electric vehicles, Multimode solar electric bicycle, Solar panel, Optimization, Motor controller
- INTRODUCTIONIn lifecycle of every community automotive industry plays vital role. Vehicles uses fossil fuel that amount increases day by day. It results in an increased amount of pollution and world is facing the problem of global warming. As well as these non-renewable resources are reducing day by day. To reduce the amount of pollution instead of fuel we can use electric vehicles where power from battery can be charged by either electricity or by using any renewable source like solar energy. For sustainable and clean mobility, EVs are the right useful option and are becoming increasingly assimilated in many cities, all around the world [1]. Electric vehicles use different technologies than normal conventional vehicles. Performance of electric vehicles depends on three core factors that is Motor, Battery, and Motor controller. Motors converts electrical energy into mechanical energy, and these are superior than gasoline and diesel engine. Motor replaces the internal combustion engine in an electric vehicle and very
important from the electric vehicle design point of view. Batteries are used to store electric charge and provide power to motor through motor controller as well as microcontroller. Batteries that can discharge only ones are call alkaline batteries are called as Primary battery and the batteries that can be recharged are called as secondary battery. Lithium-ion batteries currently have the highest gravimetric energy density of all battery technologies. Therefore, they are widely applied in electric mobility today [2]. The controller is somewhat of a middleman, as it ensures balance and proper flow of energy within an EV. It also serves as the brain, as it figures out how much energy is needed by the vehicle to go smoothly on the road. The controller has heavy wires that are connected to battery and Motor [3].
In EV that are available in market uses these core technologies. It works on two modes namely Manual mode, Auto mode. In manual mode user will pedal bicycle and when Auto mode is selected the power is taken from battery. In this optimization is not achieved as complete battery power is utilized in Auto mode.
- PROBLEM STATEMENTBy considering all class of the society as well as to deal with environmental electric vehicles are used as a solution. These electric vehicles price to performance ratio is not matching with the vehicle that uses non-renewable energy sources and performance of electric vehicle further decreases by considering all types of terrains.
- PROPOSED SYSTEMIf we know the practical aspect, optimization can be achieved. Hence, we have to design and upgrade the ordinary bicycle as Electric vehicle in such way that it is operated with multimode options like manual cycling mode, Electric Manual or Auto cycling mode. In auto mode based on the slope of the road the device should take the decision of speed which will be helpful to save the charge stored in battery. Battery charging is provided by A.C mains supply or solar panel. It should be multipurpose used for cycling, exercising and during night-time the charge stored in batteries can be used for lighting household appliances.
BLOCK diagram of proposed model
Figure 1- Proposed model of bicycle
Figure 2- Block diagram of proposed model
- Microcontroller: Arduino mega 2560 microcontroller board based on AT mega 2560 is used. It has 54 digital input/output pins out of which 15can be used as PWM outputs [4].
- Inertia measurement: To sense the motion of bicycle, MPU- 6050 six axis (Gyro + Accelerometer) motion tracking device is used. The output of accelerometer is given to the microcontroller through I2C bus [5].
- Speedometer: To calculate the speed, number of rotations are counted by using magnetic reed switch that works on the principle of Hall effect [6].
- Throttle: In Electric Manual mode, throttle provides the data to the microcontroller. Based on that data the speed ofthe motor is adjusted and accordingly power is taken from battery [7].
- Display: To display Mode, Battery voltage, Trip, and power dissipation 20 x4 character LCD display with I2C interface option is used [8].
- Mode select switch: 3- way Toggle DPDT switch is used to select the mode [9]
- Solar panel: Two PV based 12V/20W solar panels are used to charge batteries. These two panels are connected in series to charge the battery of 24V [10]
- Battery: Two SMF VRLA batteries of 12V/ 10Ah are used. Batteries are charged by using either solar panel or directly from A.C mains supply [11].
- Motor controller: 24V/350W motor controller is used to run motor. In Electric mode, motor controller will take PWM signal input from microcontroller and control the speed of the motor accordingly [12].
- Motor: E-Bike MY 1016 250W 24V 2650RPM DC motor that comes with 9 Tooth, 25 chain sprockets as well as 4 bolt mounting brackets on the base is used [13].Figure 3- Flow chart of proposed model
Working of this project mainly depends on two sensors
- Speedometer (magnetic Reed switch)
- Inertia measurement Unit (MPU6050)These two sensors are connected to microcontroller, Arduino mega 2560. Speedometer used in this case based upon magnetic reed switch where magnet is placed on weel spokes and magnetic sensor is placed on stationary platform of bicycle. As wheel rotates, magnet placed on spoke also rotates which after one rotation gets in contact with magnetic
sensor. This magnetic sensor is simple switch that gets activated when comes in contact with magnet and generates HIGH pulse. This pulse is sent to microcontroller. Microcontroller sets the TIMER. Working of speedometer is entirely depends on Timer settings. Time required for one rotation is equal to the speed of the wheel.
- In this formula, time and width of the wheel is considered and approximate speed is calculated by the microcontroller.
- Second sensor is inertial measurement unit (IMU) MPU- 6050 which is communicate with the controller on SCL and SDA. MPU 6050 is gyroscope as well as accelerometer that provides 6- axis of data with temperature. It combines 3- axis gyroscope and 3- axis accelerometer and digital processor in small package. It has On-chip Temperature sensor also [14]. We use only accelerometer data available as X, Y and Z axis as we are working on orientation of bicycle.
- When the data from MPU-6050 is given to microcontroller, it is able to detect the state of the cycle.
- Initially microcontroller read the mode selection switch. This switch provides three options:1.Manual mode 2.Electric Manual mode 3.Electric Auto mode
- Manual Mode: In manual mode, user has to pedal bicycle for its working. The data from magnetic reed switch is given to the microcontroller and then displayed on LCD display as Battery voltage, current, speed and power dissipation.
- Electric Manual Mode: In this mode, used has to practically drive the electric bicycle using throttle. Throttle working based on Hall sensor effect. In this case as soon as user give throttle, output of Hall effect sensor varies in voltage. The same data is transferred by microcontroller to motor controller. As it is in Electric Manual Mode the user is controlling the motor, so throttle data is directly diverted to motor controller which drives the motor according to throttle data.
- Electric Auto Mode: In this mode data from MPU-6050 is given to microcontroller in which X,Y and Z axis data is processed and decision is taken according to pre-programmed state of X,Y and Z. The decision about the road surface whether Flat, Inclined or Declined is taken based on the X,Y and Z axis reference value. After that a soft start signal is given to motor controller which start the motor at very low speed but ensure smooth movement of motor. Then according decided terrain there are three conditions.
- If the surface is Flat, then controller makes the motor run at constant speed. Initially it makes the motor to run at the internally set speed at the same time it gets the data from speedometer to cross check the speed. Initially as soon as it reaches to set speed, motor is cut-off. Controller waits till it reaches to negative threshold speed that is lower limit of set speed. When motor reaches below set speed motor again started with a soft start because lower set limit is very close to set limit which is set to around 5km/Hr. In this way at flat surface motor is not continuously ON. It uses inertia mechanism and battery power is used when motor is ON.. In this mode ON time of motor is gradually decreasing due to continuous monitoring of speed and motor RPM. This results into Optimizations of electric vehicle
- If the surface inclined, then motor is soft started after that again data from MPU-6050 is taken if the condition of terrain remains the same then full power with smooth effect is being provided to motor to climb on the slope.
- If the surface is declined, then motor is soft started that provides the initial torque to it and again the data from MPU- 6050 is taken and is condition remains same that if the terrain remains to be declined then motor is completely cut-off as it will run on gravitational force.The circuit schematic is made by using Easyeda software
Figure 4- Schematic diagram of proposed model
Working of circuit diagram is as follows:
- Battery terminal is available with two points. One terminal is connected to voltage level sensor and second is connected to motor via current sensor. In voltage sensor, voltage divider concept is used. In that R1 and R2 are of 10K and 100K. The voltage drop across the resistor is given to microcontrollers analog pin A0. Consider that voltage as V1 that is applied to microcontroller will provide dropdown voltage with respect to battery level. The value can be calculated asThe purpose of voltage divider circuit is that controller is not able to sense voltage level more than 5V, so we have to drop it with respect to incoming voltage within the range 0- 5V. Hence, we use voltage divider to reduce the voltage and we can again recalculate that voltage using voltage divider formula. R1 and R2 values are selected in such a way that value of V1 should not exceed 5V.
- Voltage regulator: The whole circuit is powered by IC 7805voltage regulator which has input range 35V. Voltage regulator convert battery voltage to +5V that will provide power to whole circuit.
- Current Sensor ACS 712: Current sensor is connected in series between Battery terminal and Motor controller. This is terminal based current sensor so IP+ is connected to battery terminal and IP- is given to motor controller. Output of current sensor is provided to controller on analog channel A2. ACS 712 has maximum measurable current of 30Ampere. Based on the battery voltage, current passes through ACS 712 onboard Hall sensor. This Hall sensor detect the current through its magnetic field generation and once detected, hall effect sensor generates voltage proportional to its magnetic field that is used to measure the amount of current [15]. This output is available at Vo is applied to channel 2.
- Switches: Switches are connected according to Pull up concept with one end is connected to Vcc and resistors one end is connected to GND. When switch is Open, controller will get logic 0 and when it is pressed then current will flow through Vcc via resistor to ground. That time controller will get logic HIGH signal. Same working is carried out with Magnetic reed switch, Rocker switch and brake switch. Brake switch is connected to hardware Interrupt digital pin3 of controller. Magnetic reed switch is connected to Analog channel A1 to the controller as this switch works on magnetic field effect. So as per speed of magnet that is placed on rim of wheel, analog signal changes with time.
- SW1 and SW2 works on logic Low concept.
SW1 SW2 Mode 0 0 Manual 1 0 Electric Manual 0 1 Electric Auto
- SW1 and SW2 works on logic Low concept.
- LCD : LCD is I2C enabled 20×4 character display that works on I2C bus. Serial clock(SCL) and Serial Data (SDA) are connected to SDA and SCL pin of microcontroller i.e pin no 20 and 21
- MPU 6050: This is another device connected to same I2C bus of microcontroller. It provides X, Y and Z co-ordinate data over to I2C bus and using that data power to motor driver is varied over digital pin no 6 which is PWM output.
- In Electric manual mode, data from throttle is required as user is controlling the motor using throttle placed on handle. Throttle data is given to analog channel A3 of controller and based on throttle data corresponding voltage is generated. This voltage is available at PWM pin number 6 which is connected to motor controller.
- RESULTSIn Multimode, multipurpose electric bicycle three modes are available namely Pedaling, Electric Manual and Auto mode. In pedaling mode, user has to pedal the icycle. Motor operates in electric manual and auto mode. In Electric manual user can control the speed by using throttle but in Auto mode based on terrain condition cycle will run automatically. Power calculation done for electric manual and auto mode. Readings are taken for No Load condition and with load condition as well as for different terrain conditions like Flat, terrain less than 20 degree and terrain more than 20 degree.
Load condition: No Load
Terrain: Flat
Mode : Electrical Manual
Sr no Throttle Position Voltage (V) Current (A) Power (W) Speed (mph) 1 No throttle 24 1.09 26.16 0 2 Medium Throttle 24 2.1 50.4 10.58 3 Maximum Throttle 24 2.46 59.04 15.58 Mode: Electrical Auto
Sr No Voltage (V) Current (A) Power (W) Speed (mph) 1 24 1.42 34.08 10 Figure 5- Flat terrain (No load)
Load condition: With load 65 Kg
Terrain: Flat
Mode : Electrical Manual
Sr no Throttle Position Voltage (V) Current (A) Power (W) Speed (mph) 1 No throttle 24 0.9 21.6 0 2 Medium Throttle 24 2.98 71.52 10.85 3 Maximum Throttle 24 4.98 119.52 15.58 Mode: Electrical Auto
Sr No Voltage (V) Current (A) Power (W) Speed (mph) 1 24 2.5 60 10 Figure 6- Flat terrain (65Kg load)
Slopy terrain divided in two parts. One with angle is approximately between 5 to 20 degree and other is between 20 to 40 degree. In Electric Manual mode, for the terrain less
than 20 degree, with no load condition, current drawn increases as we increase the throttle. But current drawn is slightly more than flat road condition.
In Auto mode, it consumes more power than flat road condition but if we compare with electric manual mode, we still achieve power optimization.
For with load condition, in Electric manual cycle run with full throttle only and current drawn is 7A with maximum speed of 15.58mph. If terrain is less than 20 degree, then for with load Auto mode cycle should be in moving condition. It draws the current up to 5A and we obtain the power optimization for Auto mode.
Load condition: No Load
Terrain: Increasing Slope less than 20 degree
Mode : Electrical Manual
Sr no Throttle Position Voltage (V) Current (A) Power (W) Speed (mph) 1 No throttle 24 1.14 27.36 0 2 Medium Throttle 24 2.14 51.36 10.51 3 Maximum Throttle 24 2.74 65.76 15.58 Mode: Electrical Auto
Sr No Voltage (V) Current (A) Power (W) Speed (mph) 1 24 2.1 50.4 16 Figure 7- Increasing slope less than 20 degree (No load)
Load condition: With load 65 Kg
Terrain: : Increasing Slope less than 20 degree
Mode : Electrical Manual
0
10.51
Sr no Throttle Position Voltage (V) Current (A) Power (W) Speed (mph) 1 No throttle 24 2 Medium Throttle 24 3 Maximum throttle 24 7 168 15.58 Sr No Voltage (V) Current (A) Power (W) Speed (mph) 1 24 5 120 7 Sr No Voltage (V) Current (A) Power (W) Speed (mph) 1 24 5 120 7 Mode: Electrical Auto
Figure 8- Increasing slope less than 20 degree (65kg load)
If the Terrain is more than 20 degree, (between 20 to 30 degree) in Electric Manual mode, power consumption increases with increase in throttle condition. For auto mode, it draws more current than electric manual to run on the terrain greater than 20 degrees.
For with load Electric Manual mode condition, cycle run only if we apply maximum throttle and obtain maximum speed but in Auto mode it draws maximum current with lowest speed.
Load condition: No Load
Terrain: Increasing Slope more than 20 degree
Mode : Electrical Manual
Sr no Throttle Position Voltage (V) Current (A) Power (W) Speed (mph) 1 No throttle 24 1.29 30.96 0 2 Medium Throttle 24 1.91 45.84 10.51 3 Maximum Throttle 24 2.37 56.88 15.89 Mode: Electrical Auto
Sr No Voltage (V) Current (A) Power (W) Speed (mph) 1 24 2.44 58.56 16 Figure 9- Increasing slope more than 20 degree (No load)
Load condition: 65Kg
Terrain: Increasing Slope more than 20 degree
Mode : Electrical Manual
0
Sr no Throttle Position Voltage (V) Current (A) Power (W) Speed (mph) 1 No throttle 24 2 Medium Throttle 24 3 Maximum Throttle 24 10.5 252 15.58 Mode: Electrical Auto
Sr No Voltage (V) Current (A) Power (W) Speed (mph) 1 24 11 264 2 Figure 10- Increasing slope more than 20 degree (65 Kg)
- RESULTS
Multimode, multipurpose solar bicycle designed for Optimization of battery power. Battery charging is possible with two options- Electrical energy, Solar energy.
This bicycle is operated with three modes: Pedaling, Electric Manual and Electrical Auto. Power optimization is calculated for electrical manual and auto mode. On flat terrain. Approximately 10 to 30% power optimization is achieved without load by using electric auto mode with average speed 10mph. With same terrain for with load power optimization approximately 20% power optimization is achieved.
For the terrain less than 20-degree angle, power optimization achieved is
approximately 20%-25% for No load condition. With load condition we obtain 30% power saving but with compromise in speed.
For the terrain more than 20-degree, less power optimization is achieved. For No load condition value is 10% and for with load condition no optimization is achieved.
The charged batteries are also used for household appliances during nighttime so very useful in village areas.
becomes possible to control motor acceleration with more accuracy level.
Motor, motor driver, Controller and Battery are core factors of this project. In this project, 250W, DLDC motor is used which has Aluminum winding. If motor with Copper winding is used then it reduces current requirement and increases durability, Soft starter MOSFET based motor drivers help to control motor with more accuracy level. For Batteries, instead of Lead acid batteries if Li-Ferrous batteries are used then it will reduce overall weight and charging cycle of bicycle. It will increase On-load time reduces onload heat dissipation with no leakage current.
With the use of these advanced components, it is possible to collect more accurate data and it becomes possible to run the motor for very less orientations also which will help to achieve more optimization along with the more power saving.
VII. REFERENCES
- Recent Advancements and Developments for Electric Vehicle Technology
- TU delft Electrical Car technology.
- 3.https://www.upsbatterycenter.com/blog/electric-vehicle-controller
- .https://www.arduino.cc/en/Main/arduinoBoardMega2560
- https://components101.com/sensors/mpu6050-module.
- https://robu.in/product/mc-38-wired-door-window-sensor-magnetic- switch-home-alarm- system/?gclid=Cj0KCQiA962BBhCzARIsAIpWEL0hacXFWDIbtm 1W0VM5L9u8rcN5Sq8MPksquOLpekgjYIRQMpsAeFoaAotxEAL w_wcB
- https://www.egr.msu.edu/classes/ece480/capstone/fall15/group09/re ports/finalreport.pdf.
- https://www.thingbits.in/products/i2c-20×4-arduino-lcd-display- module
- https://robu.in/product/dpdt-rocker-switch
- https://www.vikramsolar.com/basics-of-solar-photovoltaic-panels/
- https://www.okayapower.com/smf-batteries.php
- https://hacktronics.co.in/electric-bicycle-e-bike/24v-250w-brush- motor-speed-controller-for-electric-bicycle-electric-bike-e-bike- controller-scooter
- https://robu.in/product/24v-350w-my1016z3-electric-motor-for-e- bike-electric-tricycle-electric- motor/?gclid=Cj0KCQiA962BBhCzARIsAIpWEL2rrKLRcpGQv1l_FS-Ygdglyj-
BPK6gYR_7vtA2KwcLs1SOjN690WMaAopVEALw_wcB
- https://www.electronicwings.com/sensors-modules/mpu6050- gyroscope-accelerometer-temperature-sensor-module
- https://www.seeedstudio.com/blog/2020/02/15/acs712-current- sensor-features-how-it-works-arduino
VI. FUTURE SCOPE
In practical aspect of EV, orientation-based drive capabilities are not available. EV that are available in market are operated in electric Manual mode where motor run with the power from battery and motor controller control the speed with the help of throttle.
In this system with the use of Real time or faster version of microcontroller like STM32 [30] based on the ARM Cortex-32-bit processor core that offers new degrees of freedom to MCU uses. It offers products combining very high performance, real- time capabilities, digital signal processing, low power/low voltage operation and connectivity while maintain full integration and ease of development. With the help of such fast controller, it