
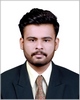
- Open Access
- Authors : Ganesh Nikam , Onkar Dake , Aditya Deshpande
- Paper ID : IJERTV10IS090018
- Volume & Issue : Volume 10, Issue 09 (September 2021)
- Published (First Online): 08-09-2021
- ISSN (Online) : 2278-0181
- Publisher Name : IJERT
- License:
This work is licensed under a Creative Commons Attribution 4.0 International License
Design and Fabrication of Sugarcane Trash Removal Machine
Mr. Ganesh Nikam
Mechanical Department
KIT College of Engineering Kolhapur, India
Mr. Onkar Dake, Mr. Aditya Deshpande
Mechanical Department
KITs College of Engineering Kolhapur, India
Abstract Sugarcane, one of the most important crops of India, is a renewable, natural agricultural resource providing sugar and bio-fuel as well as by-products like, fiber and fertilizer. The production cost of sugarcane is increasing year after year. This reduces the profit margin of cane growers and sugar industry. Most of the cultural operations are delayed or not taken up at all for want of sufficient labour at reasonable wages, resulting in low production and productivity of sugarcane. Harvesting of sugarcane is the laborious operation which involves base cutting, de-trashing,de-topping, bundle making, loading and transport of sugarcane to the sugar mill. Labour requirement of sugarcane harvesting ranges from 850 to 1500 human hours/Hectares, which is the highest as compared to other operations. Mechanization of sugarcane harvesting isessential not only for reducing the production cost and drudgery involved in manual harvesting operations, but also to ensure quality produce. Mechanical combine harvesters that are presently available are of high capacity and require high capital investment. Sugarcane de-trasher using tractor as power source would be less
expensive and suitable for small and medium farmers. Among the sugarcane harvesters presently available, this machine would be the cheaper, causing less deterioration of the sugarcanes on storage. A tractor mounted de-trasher suitable for small and medium farmers is an essential requirement for mechanizing the harvesting of sugarcane to tide over the labor scarcity.
I INTRODUCTION
Sugarcane crop plays a vital role in nations economy, being one of the most commercialized crops in India. It provides income to the grower, and employment for numerous farm workers throughout the year. Sugarcane occupies about 2.5 per cent of the gross cropped area in India and provides raw material to more than 450 sugar mills. About 45 million sugarcane farmers, their dependents and a large mass of agricultural laborers are involved in cane cultivation. Besides, about half a million skilled and semi-skilled workers, mostly from rural areas, are engaged in the sugar industry. Sugarcane is grown in two distinct agro-climatic regions: the tropical and sub-tropical; Maharashtra, Karnataka, Gujarat and Tamil Nadu being the important cane growing states in tropical region while Uttar Pradesh, Punjab, Haryana and Bihar are the four important states growing sugarcane in North India. Uttar Pradesh has the largest area of two Mha in the country under sugarcane. Area, production and productivity of sugarcane in India for the last decade are shown in Table
-
PROBLEM STATEMENT
With agriculture facing a shortage of manpower, need for automating the various activities in the field arises or it is becoming the necessity. With this problem keeping inmind, a simple machine has been designed and fabricated for Sugarcane Trash Removal Machine. As the machine moves, the trash remover cuts the trash present between the sugarcane. This machine can be used effectively in the sugarcane field. To use this machine in sugarcane field the seeds should be sowed at a distance equal to or more than the width of this machine. This machine has simple design but this machine required mini tractor to rotate the shaft. Only the belt and pulley arrangement is used in the machine. This machine eliminates the need of no. of workers and makes the work easier, economical and efficient.
-
Objectives
-
To study the physical and mechanical properties of sugarcane related to de-trashing.
-
To evaluate the functional parameters influencing sugarcane de-trashing.
-
To design and develop a tractor operated de-trashing machine.
-
-
-
TRASH CONTENT
Trash content of the cane at the time of harvest varies depending upon the variety and the agricultural practices adopted. As per the package of practice of sugarcane, it is to be de- trashed at regular interval for the removal of dried, yellowish green, bottom leaves. This operation is skipped by the farmers nowadays due to the drudgery involved in the job and lack of labors. Hence, the trash content at the time of harvest will vary depending upon the practices adopted by the farmers. The trash available at
the time of harvest is removed mainly by two operations viz., de-topping and de-trashing.
Dry Leaves of sugarcane or trash
The amount of trash available at the time of harvest is assessed at different farmers field and expressed as the trash content per millable cane for the uniformity of representation. The trash content removed by de-topping and de-trashing are tabulated separately.
-
Need of De-trashing :
From the plantation of sugarcane when it grows upto 6 to 8 months i.e. in the middle of July to September, process of removal of trash i.e. dried leaves of sugarcane takes place. The process of de-trashing helps air to travel free across the field and hence it improves the growth of sugarcane. Also the trash removed from cane dropped in the foot of sugarcane, gives very good form of manure and helps in mulching and also produce good bacteria required for sugarcane. Hence it is important process.
-
Need of mechanization in De-trashing of sugarcane:
Sugarcane trash removal involves de-trashing, cleaning leaves from green sugarcane.Labor requirement of sugarcane de-trashing ranges between 850-1000 and 1200- 1500 Hours per Hectare in tropic and sub-tropic regions of India, respectively, which is the highest as compared to other cultural operations involving costs in the range of ` 14,500- 16,000 ha-1 approximately.
Hence mechanization of sugarcane de-trashing is essential not only for reducing the production cost but also for reducing drudgery involved in manual de-trashing operations, and also to ensure quality produce. Shortage of labor is one of the reasons why many farmers have walked away from this promising crop. Mechanization is considered as an alternative not only to solve the problem of labor shortage but also to reduce the cost of production.
Indian agriculture is characterized by small and scattered holdings and sugarcane cultivation is no exception. An average Indian farmer is financially weak and is not in a position to spend a huge sum of money on costly equipment. Further for repair and maintenance, the farmer depends on the local artisans. Therefore, it is imperative that only low cost simple technology will find wide acceptance. It is therefore, necessary that the system of mechanization
suitable for Indian conditions must take care of the above mentioned points before developing indigenous technology. To meet this requirement we are trying to solve the problems of farmers, raised due to financial aspects in cultivating or cleaning/de-trashing of sugarcane. By designing the sugarcane trash removal machine.
-
Methods of De-trashing :
The term "de-trashing" refers to the use of mechanical equipment to reduce the trash matter in cane by techniques other than burning. If sugar is the main product from caneand if green cane harvesting is the only option, then some form of de-trashing is highly desirable. In many sugarcane producing countries, Cleaning or de-trashing is done manually by hands. It is traditional method to clean roots from unwanted leaves. Ingreen cane, the trash is removed and the stalks are topped, using a wide range of cane knives and de- trashing devices. A variety of mechanisms has been investigated for the removal of tops and leaves. Loose leaves can be removed pneumatically using high velocity air. Pneumatic separation efficiency depends on the quantity and velocity of the air used. Chopping cane into smaller sections enhances the trash removal efficiency.
There are different methods of de-trashing mechanism vise:
-
Cutting system with forced friction (cylindrical blades): In this system,the leaves are cut and torn by the action of stem cylindrical blades. The performance of this equipment was varies from 77.30 to 90.10 per cent removal of leaves with zero per cent damage to sugarcane and yield 150 to 313 kg man- h-1.
-
System of friction force: Here the roller is made with steel wire, string, piano and V-belts that cleared away the leaves. The performance was varies from76.60 to 89.80 per cent with 1.10 per cent of damage to sugarcane and156 to 190 kg man-h-1 performance. This system had some shortcomings but no apparent damage was observed. The friction marks were clearly visible, with 1 to 2 mm of material removed from the shell after the action of the rollers.
-
System of impactfriction: In this system, flexible cords attached to rotating rollers that provide a large impact force by the centrifugal forcein cane sugar, promote the removal of leaves. The performance was in the range
90.30 to 91.30 per cent with 0.60 to 1.40 per cent of damage and yield 162 to 178 kg man-h-1.
-
-
De-trashing / cleaning by Impact Friction method:
We are going implementation impact friction method to manufacture sugarcane trash removal machine with implementation impact friction method- In this method, the one driving shaft is connected to tractor (prime mover). The power transmitted to shaft from tractor which results in rotation of shaft. Gear wheel is mounted on the main shaft which meshes with another gear on other shaft which is fixed on the frame of machine. Two pulleys are mounted on these shafts one on main shaft and other on another shaft. There are four shafts mounted on outer frame of machine by means of bearing. Four pulleys are mounted on shaft, one on each shaft.
Two v-belts are attached between shafts which are interconnected and lower shafts which are mounted on outer
frame of machine. Another two v-belts are attached between outer shafts each on same side for power transmission. On the end of shafts which are attached to outer frame of machine are attached with rollers which rotate along with shafts. Flexible cords or ropes are attached to these rollers. Rotation of rollers results in rotation of flexible cords, which results in impact on leaves to remove the dry leaves. Together this the impact friction method works for de- trashing.
III SUGARCANE TRASH REMOVAL MACHINE
Sugarcane Trash Removal Machine
The one driving shaft is connected to tractor (prime mover). The power transmitted to shaft from tractor which results in rotation of shaft. Gear wheel is mounted on the main shaft which meshes with another gear on other shaft which is fixed on the frame of machine. Two pulleys are mounted on these shafts one on main shaft and other on another shaft. There are four shafts mounted on outer frame of machine by means of bearing. Four pulleys are mounted on shaft, one on each shaft. Two v-belts are attached between shafts which are interconnected and lower shafts which are mounted on outer frame of machine. Another two v- belts are attached between outer shafts each on same side for power transmission. On the end of shafts which are attached to outer frame of machine are attached with rollers which rotate along with shafts. Flexible cords or ropes are attached to these rollers. Rotation of rollers results in rotation of flexible cords, which results in impact
on leaves to remove the dry leaves. Together this the impact friction method works for de-trashing.
Flexible cords attached to rotating rollers that provide a large impact force by the centrifugal force in cane sugar, promote the removal of leaves. During the leaf cleaning procedure, the cleaning element works in the situation of large deformation and is subjected to a periodic and dynamic load. Therefore, it is easy to fatigue breakdown. A cleaning mechanism consists of a powered rotatable cleaning shaft supporting a plurality of elongate flexible members extending radially. Rotation of the cleaning shaft in a direction such that
the plurality of flexible members contact a cane stalks and force leaves on a cane stalk in the direction towards the base of a cane stalk to remove the leaves from the cane stalk.
The equipment separates the top of mature cane, breaking it and removing the green leaves. The cleaning system consists of a feeding tube, a cylinder, a bottom roll, roll one side, a roll cutter and a fan mounted on a stationary platform. It is powered by a diesel engine. The equipment has been tested for different varieties of sugarcane and for different speeds of rotation of the rollers.
-
Potential Benefits:
-
Cost savings in terms of reduced wear and maintenance
-
Increased factory capacity due to reduced quantities of extraneous matter.
-
Reduced energy consumption for the same amount of sugar produced.
-
Lower losses of sugar in filter cake, bagasse and molasses.
-
Easier factory operation due to lower viscosity of syrups and molasses.
-
Improved sugar quality.
-
IV DE-TRASHING TECHNIQUES
High speed rotation of the brush type cleaning elements push, rub and strike the sugarcane stalk and separate the leaves from the sugarcane. The different orientations of the cleaning systems are as follows:
-
Cane bottom feeds first; brush rotates in the same direction
-
Cane bottom feeds first; brush rotates in the opposite direction
-
Cane top feeds first; brush rotates in the same direction
-
Cane top feeds first; brush rotates in the opposite
direction
The de-trashing trials are conducted on the above four systems and evaluated on the basis of the de-trashing efficiency. The de-trashing efficiency is calculated using the following formula.
De-trashing Efficiency % = (Mass of de-topped caneMass of de-trashed cane) ×100/ (Mass of de-topped caneMass of cleaned cane)
The first and the fourth system showed a high de-trashing efficiency. This is because; in both systems the brushes are working opposite to the direction of the leaves formation.
De-Trashing systems with their Efficiency
A. De-trashing Efficiency :
The de-trashing efficiency of different combinations of the spiral angle of de-trasher brushes (A), the de-trasher roller speed (N), and the input roller speed (S) are reported in Appendix-V The de-trashing efficiency data were analyzed as per three way analysis of variance and the significance of each factor and their combinations were studied using Fishers least significant difference (LSD) procedure in completely randomized block design by AgRes Software statistical package. Analysis of variance of the de-trashing efficiency values with respect to the tested de-trashing combinations at 0.01 level showed that the factors, the spiral angle of de-trasher brushes (A) and the de-trasher roller speed
(N) were highly significant at their one-way and two-way interactions. The factor input roller speed (S) was non- significant for the de-trashing efficiency. Based on these results it can be concluded that the de-trashing efficiency for the four spiral angles and the four experimental de-trasher speeds were not the same. It can also be concluded that the de-trashing efficiency at a spiral angle depends on the de- trasher roller speed.
V DESIGN PROCEDURE AND MATERIALS
The study into sugarcane leaf-removal machinery uring harvest process aimed at studying the situations of harvesting sugarcane of farmers and at using sugarcane leaf-removal machinery. The CO-86032 variety of sugarcane having a harvesting period of 14 months was used as sample. Sugarcane harvest field, Fig 6.1 shows length between plant spots of gross sugarcane in the field. Density of sugarcane plant is the ratio of sugarcane stem to area. The quantity of sugarcane production can be weighed by random sugarcane stem which was cut on part of the cane top and leaf was removed.
Designing of Machine was developed using CATIA V5 R16 software as per above dimensions.
-
Materials Used:
-
Roller with rope: There are 4 Mild Steel Rollers present of Ø150*300 mm with Ø6 mm drill hole. Theelastic cord like material i.e. ropes are attached to the roller
-
MS Square Pipes: are used to manufacture basic frame structure. Total pipe used is 2.6 m in length.
-
Shaft: The power of tractor. 25 mm Diameter Steel Shafts are used for better Rigidity and performance.
Sugarcane plant position in Plot
-
Pedestal Bearings: are used for providing support for rotating shaft. Total 12 Pedestal Bearings are used in this machine, 8 of Bearing No. UCP205 and 4 of Bearing No. UCP206 fixed witp/8 hexagonal head bolt.
-
Gears: are major parts in this major which transmit the power from one shaft to another. 2 Spur gears are used in this case with bore diameter 25 mm.
-
V-Groove drive pulley: with 5 Diameter and 25 mm Bore Diameter made of Steel used . Total 6 pulleys are used on which 4 V-Belts of 4 L/A size is used.
-
V Belts are used for transmission of power
-
PTO: To connect main shaft of machine to tractor Power Take-off Universal Joint of bore diameter 25 mm is used, which transmit power from tractor to machine.
-
Ropes: are required for cutting purpose as it hit the dry leaves at greater velocity without harming or damaging the sugarcane. Ropes are of 6 mm diameter and made of Polypropylene materials.
-
-
Manufacturing of Machine:
-
Product concept: The basic idea or the concept to manufacture the sugarcane trash removal machine is to reduce the labour cost, increase accuracy in work and saving of time. For this requirement we think on the product which is easy to operate, cost efficient and time saving machine. This is done by thinking on concept how to apply any mechanism to do such work. Ones the mechanism is finalise i.e. impact friction method, then basic sketch or drawing of the machine is done.
-
Research: There are two important things to research at this stage: firstly, demand. If the product solves a problem, are a lot of people looking for a solution to that problem. Research is done by meeting the farmers listening the problems they are facing to do such work and asking them there is any need of such type of machine. Secondly, are there products out there already that are similar to yours? If so, it doesnt necessarily mean your idea wont be a success.
-
Product Design Development: At this stage, development of product design begins . There are a number of things must be considered here:
-
Have a firm idea of products function.
-
Thinking about how strong and long-lasting the product will be
-
How reliable is the product. What will the manufacturing costs be.
-
thinking about complexity in manufacture, factoring in how many parts each unit is made from.
-
What are the materials needed for production.
-
-
CATIA modeling: This process uses 3D rendering software in order to produce a computer model of final design. This can help to reveal any potential issues that werent evident from the product design itself. The catia of the sugarcane trash removal machine is done to
Length of Belt:
(4)
(5)
visualize the final machine design.
(L = Length of belt, mm; D1 = Diameter of driver pulley, mm;D2 = Diameter of driven pulley, mm; C = Centre to centre distance of belt, mm)
Centrifugal Tension:
(6)
(Where, Tc = Centrifugal Tension;W= weight of belt; g = Acceleration due to gravity; V= Velocity of belt)
Centrifugal Stress:
-
Manufacturing :
-
First the MS steel bars are cut into required dimensions. According to primary and secondary members.
-
The basic frame structure is done by welding the
(Where A= area of belt; Tc= centrifugal tension)
Power Transmitted per Belt:
(7)
(8)
bars i.e. primary and secondary members according to the design of machine.
-
The main drive shaft is fitted with the gear and is its end is fitted with arrangement of PTO shaft to connect with tractor.
-
The four shafts are then fitted on outer frame with help of bearings.
-
The ends of shafts are then connected with rollers by means of nut and bolts. The ropes are tied with rollers.
-
Main driving shaft and rotating shafts are then connected by V-belts and pulleys.
-
The entire assembly is the sugarcane trash removing machine.
-
-
Testing and Analysis: The machine is then tested in the required region i.e. in the sugarcane farms. The mechanism and the proper working of machine is analyzed, required changes and improvements are done accordingly.
-
-
CALCULATION
Selection of power source :
From Thai Agricultural Research Journal 2016, breaking leaves force is 40-50 N Calculation of power required for sugarcane harvesting is given below;
T = F x r (1)
(T = Torque of the cutter, N-m ;F = Force required to cut sugarcane, N; r = Radius of the cutter, m )
Power Rating:
P = 2/60 (2)
Engine shaft torque:
(Where, p= power transmitted per belt ; k=constant ;v = velocity of the belt ; 1= Tension in tight side, N; = Centrifugal tension, N)
Solid Shaft subjected to twisting moment
(9)
(3)
Velocity of the belt:
-
CONCLUSION
The Sugarcane Trash Removal machine is designed and fabricated. There found that the large amount of leaves are harvested with sugarcane and they are proceed, which make dust n surrounding. Sometimes the wires get stuck and thus machine stops. This problem was solved by changing the materials of wires from Polypropylene to Soft Rubber wires. By using this mechanism problem of the leaves extraction from sugarcane is reduced. Comparing with manual harvesting only 10% of labors are required for entire operation. It makes the process faster hence reduces most of the harvesting time and labor required to operate the machine is also less. So, it reduces the labor cost. The machine is used by maximum number of farmers definitely farmer can overcome the labor shortage problem. This reduces the labor cost and process become faster and easy. The productivity is also increased.
REFERENCES
-
Investigation On De-trashing Cum Conveyance Of Sugarcane And DevelopmentOf Tractor Operated Whole Cane Combine Harvester by Joby Bastine
-
A Study of Sugarcane Leaf-Removal Machinery during Harvest by Sopa Cansee, Department of Mechanical Engineering, Faculty of Engineering, Thailand.
-
https://www.researchgate.net/publication/322050396
-
https://www.researchgate.net/publication/331950478
-
https://www.researchgate.net/publication/283870068