
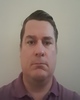
- Open Access
- Authors : Dimitrios E. Mazarakos , Spyridon Kontogiannis , Anargyros Karakalas , Georgios Michalelis
- Paper ID : IJERTV12IS020150
- Volume & Issue : Volume 12, Issue 02 (February 2023)
- Published (First Online): 09-03-2023
- ISSN (Online) : 2278-0181
- Publisher Name : IJERT
- License:
This work is licensed under a Creative Commons Attribution 4.0 International License
Design and Analysis of a VTOL/Fixed wing UAV
Dimitrios E. Mazarakos
Mechanical Engineering and Aeronautics Depart.
University of Patras-Rion/Patras, Greece
Spyridon Kontogiannis,
Mechanical Engineering and Aeronautics Depart.
University of Patras-Rion/Patras, Greece
Anargyros Karakalas,
Mechanical Engineering and Aeronautics Depart.
University of Patras-Rion/Patras, Greece
Georgios Michalelis,
Mechanical Engineering and Aeronautics Depart.
University of Patras-Rion/Patras, Greece
AbstractIn this technical paper, the design and analysis methodology for a fixed/VTOL UAV is fully presented. This methodology was developed during the Airbus Drone Challenge 2017 for the presentation of the Hygeia Ex Machina (HEM) UAV concept. The methodology is consisted of the design parameters of the competitions and the design steps for the UAV preliminary design review are fully addressed. These steps include iterative multidisciplinary aero structural calculations using both numerical and algebraic equations of aircraft motion for different flight phases (hovering/climb/cruise/turning/ landing etc.) The aero structural calculations reach the airworthiness quality level for safe handling operations for both Remote Control and Automatic Control mode. The design and analysis procedure of UAV HEM won out a Technical Proficiency Certificate by AIRBUS meeting all the core requirements.
Keywords:- Aerodynamics;VLM; structures; UAV;stability;
-
INTRODUCTION
In nowadays, the Unmanned Vehicle Systems (UAV/UAS) technology grows continuously. As these systems are important in many sectors such as: agricultural, military, security etc, there is also the necessity of hybrid/ multiple role platforms that mixes characteristics of aircrafts modes (fixed wing, helicopter, multicopper drone etc). The proposed methodology introduces the main design guidelines of an Remote and Automatic Controlled UAV with fixed and Vertical Take off modes including: a) aerodynamics/flight mechanics, b) mass/inertia and structural considerations, c) dynamic stability and d) systems integration. This methodology was applied during the Conceptual Design phase of UAV Hygeia-Ex Machina (HEM) for AIRBUS Cargo Drone Challenge 2017. The challenge based on development of cargo UAV systems that carry transplants in regions with low mobility. The HEM concept earned a certificate of technical proficiency by AIRBUS, meeting all the requirements.
-
DESIGN METHOD
-
Work Break Down structure and plan of activities
At early design steps, the Team established a working plan with all the major aspects for investigation. As a mixed role
aircraft, the HEM concept should combine various flight characteristics like: a) take-off & climb as helicopter/multicopter drone, b) horizontal flights and maneuvers as fixed wing aircraft, c) vertical descent and landing.
Figure 1: WBS and plan of activities
Understanding the requirements and the systematic review of the specifications was the first activities that set the design and analysis limits. Especially, for the aerodynamic surfaces sizing/flight mechanics and the mass/inertia activities an iterative process was set in order to reach satisfactory results. A structural optimization algorithm was also developed for minimization of the mass/ inertia. For the aerodynamics and flight mechanics, an algorithm was developed calculating the stability derivatives and the loads assessment for the structural calculations. All the design aspects from the analysis was implemented in CAD representations including the UAVs Systems.
-
System Requirements
At the beginning of the challenge, AIRBUS set various requirements, establishing minimum acceptance criteria for the concepts. These requirements are summarized in TABLE 1:
Take-off/ Landing
Vertical take-off/Landing
Main lifting Surface
At least one
MTOW (kg)
<25
Maximum span and length
Span<5 m length < 4m
TABLE 1: UAV system requirements
and structural considerations
Cruise Speed (m/s)
22<Vcruise<55
Vertical climb speed (m/s)
1.5<Vvert<2.0 for vertical climb rate and DL>18 kg/m^2 for VTOL stability at crosswinds.
Transportation
-Modular,
Max dimensions of the individual parts < 2m
-Carried by 2 average size people
-Ease transportation using van. Transportation box size: 1.5m X 1.5m X 1.3m
Payload and range
-5 kg for >60 km range
-3 kg for >100 km range
Flight envelope
-Reaching the cruise altitude (90m from ground) with 1.5 m/s<Vvert< 2.0 m/s.
-Minimum speed 80 km/h at cruise altitude of 90m for fixed wing mode.
-Maximum speed 194 km/h a at cruise altitude of 90m for fixed wing mode.
-Loiter: 5 minutes
Reaching the ground altitude with Vvert=1.5 m/s.
-20 min turnaround between the max-distance missions
Payload location and dimensions
-Single payload bay, near the CoG
-Minimum dimensions 450mm x 350 mm x 200 mm
-The payload bay shall be located and accessible from the lower side of the aircraft and must be interchangeable with payload bay of same size and same interface. (Payload concept shall be modular to fulfill applications different from the cargo use case. e.g. sensor payload)
Powerplant
4<drive propellers<10
Energy storage unit
Rechargeable batteries
Equipment mass (kg)
3.38
Head/Crosswind
10 m/s
Weather conditions
-Moderate rain
-30 to 40 Celsius degrees
Safety
-Safe operation in all flight modes
-Mitigation of catastrophic failures
The requirements are the basis for the specifications review stage.
-
System Specifications Review (SRR) and evaluation
For the conceptual design, a multidisplinary design method should be developed evaluating the requirements and setting the design priorities for the development of numerical tools for calculations.
Basic Specs
Wing loading (kg/m^2)
5<W/S<1OO
Mean aero chord/Wing SurfaceCmean/ Sw
TBD
Take-off Weight (kg)
12<MTOW<25
Aspect Ratio AR
TBD
Reynolds Number
Re=600K
Lift Coefficient CL
TBD
Zero lift
coefficient
Cd0=0.08
Drag Coefficient CD
TBD
Wing Span (m)
2<b<5
Necessary Power for cruiseP1cruise
TBD
Disk loading (kg/m2)
5<DL<50
Necessary Power for VTOL
P2vto
TBD
Wing Incidence angle (deg)
Up to 2
Wing Angle of attack (deg)
Up o 8
degrees due
to VTOL transition to fixed wing
Bank angle (deg)
Up to 10
Slip angle (deg)
Up to 10
Design Limitations
Aspect Ratio
4<AR<15 for both aerodynamic
TABLE 2: SRR for UAV design and analysis
The wing loading is both aerodynamic and structural aspect. This parameter affects the CL and CD coefficients and the velocity, powerplant size but also basic mass and inertia characteristics. These values were set under investigation (To Be Defined) by the multidisciplinary method. The bank and slip angles were considered low (<10 degrees) avoiding non- linear control analysis during the analysis.The SRR also sets the limitations of this method, reducing the iterative steps of the design. Thus, the developmental time and the concept cost is minimized. These parameters are also important for the further industrialization of UAV product.
-
-
DESIGN AND ANALYSIS
The design and analysis process includes basic topics:
a) aerodynamics and flight mechanics-loads assessment , b) weights, systems and structures, c) CoG arrangement and d) Dynamic stability. It is an iterative process where aircrafts parts (fuselage, wing, tail etc.) and its systems (motors, navigation, etc) are fully defined as geometries and sizing dimensions. For this reason a MATLAB code was developed for the aerostructural optimization of the UAV.
-
Aerodynamis and Flight mechanics
This step includes the SRR outcome and aerodynamic/flight mechanics equations in order to specify design specs such as: mean aerodynamic chord, drag & lift coefficients etc. The aerodynamic and flight mechanics calculations are taking into considerations the UAVs flight envelope/profile: a) Vertical take-off, climb, descent and landing using vertical propeller driven thrusters (Pvt) and b) horizontal flight-cruise and maneuvers using propellers (Pprop). This mixed profile does not use all the motors simultaneously. The aircraft motion is described by the governing equations for cruise (1), maneuver (2), vertical climb and descent (3),(4):
(Pprop/W)=V*q*Cd0*(1/(W/S)+V*(1/ARe)*(1/q)*(W/S)(1)
(Pprop/W)=(V*Cd0*q/(W/S))+q*V*(1/ARe)*(n/q)2*(W/S) (2)
(Pvt/W)= (0.5*Vclimb+SQRT ((0.5*Vclimb)2+Vhover2) (3) & Vhover =SQRT(W/(2**disk) (4)
The cruise condition was the most crucial as the aircraft must have a range greater than 60 km .
Figure 2: Pprop vs W/S for cruise condition (graphical method)
From the graphical method analysis [1],[2], the parameters that selected were: W/S =35 kg/m^2 and Disk Loading= 24 kg/m^2, using 2 motors for the horizontal flight (better CoG arrangement/power effects distribution)and 4 motors for vertical flight (better stability under crosswinds for hovering phase). The result of this analysis is summarized in Table 3 where TBD values are specified.
Calculated (TBD) values for the basic specifications
Aspect Ratio (AR)
7.0
Lift coefficient CL@cruise
1.0
Dragcoefficient CD@cruise
0.15
MTOW (kg)
22.0
Necessary Power for cruiseP1cruise, max (W)
2000
Necessary Power for VTOL P2vto max(W)
5000
TABLE 3: Calculated values for the basic specs
-
Loads Assessment
The loads assessment is based on the prediction of the important forces and moments that are transferred to the aircraft during the flight. These loads takes into consideration any gusts loads due to wind shear, upwind, downwind etc. The main expression of this loads are based on the load factor n:
Nz=L/W and Nx= (T-D)/W (5)
Flight phase
Values
Vertical take-off and climb
Nx=0.0
Nz=1.5
Cruise& Acceleration Horizontal flight
Nx=2.0
Nz=1.0
Coordinate Turn
Nx=0.0
Nz=1.5
Vertical descent and landing
Nx=0.0
Nz=-1.5
TABLE 4: Loads assessment for the analysis
The loads assessment is the baseline for the weights calculations and the structural analysis.
-
Weights and structures
The weights and structures analysis is based on the evaluation of the maximum load factors and MTOW as well as the loading condition of each flight mode [3],[4]. The basic mass/structural components are the wing, fuselage, tails, the landing system and interiors. For these parts, an iterative numerical code was developed taking into consideration the static equilibrium (bending, shear loads) and the necessary moment of inertia of each section (wing, fuselage and tails). For each section the mass was also calculated. The equations are summarized in :
Mass , M= *V, (6)
Bending stress := /W where W= I/y (7) Shear Stress := P/F (8)
Figure 3: Vertical Motion Inertia loads (Equivalent structural model)
Figure 4: Shear force and bending moment distribution along the fuselage (vertical motion)
Figure 5:Horizontal flight inertia loads (Equivalent structural model)
Figure 6: Shear force and bending moment distribution along the fuselage (vertical motion)
Figure 7: Fuselage's stringers and Frames Moment Inertia & Cross section Area along the fuselage
Figure 8: Wing structural integrity (Bending moment along the wing span)
The iterative process was started with anmax initial MTOW=25kg as the maximum value from the flight mechanics analysis. The material selection for all the structural parts was High Modulus and quasi-isotropic CFRP. The philosophy of the design was based on monolithic skins
& ribs for wing and fuselage that withstand shear loads and square cross-section stringers that withstand bending and axial loads. All the parts and the joints are glued together with epoxy adhesive with shear strength greater than 20 MPa, creating a high stiffness to mass ratio airframe.
TABLE 5: Structural mass components overview
Hygeia Ex Machina Structural Components mass
Part
Item specification
Weight (kg)
Fuselage (including cargo bay)
CFRP stringers with bulkheads and skins
1.9
Wing
Monolithic skins, ribs and beams made of CFRP
1.7
Horizontal Stabilizer
0.45
Vertical Stabilizer
0.65
Total Structural Weight (kg)
4.7
-
Aircraft Systems Arrangement and CoG location
The sizing of the aircraft aerodynamic surfaces was performed with the aerodynamics/flight mechanics algorithm that was important for the aircraft efficiency, both power and range [5]. The structural calculations and the mass prediction was used for all the structural components sizing process. For the non-structural mass components, a list of necessary equipment was gathered taking into considerations the power consumption calculations, the necessary stored energy, and the dimensions of these parts.
Payload and Range (km)
>100 for payload 3 kg
>60 for payload 5 kg
Battery pack
Voltage= 8-30V
4 packs of 5400 mAh Battery mass= 3.4kg
Propulsion powerplant
2 motors/ propellers for fixed wing condition 2 x 0.65 kW
Flight Control and Remote Control System
Max 1.5 kg
VTOL powerplant
4 motors/rotors for VTOL 4 x 980 W
Motor/rotor masses (kg)= 2.2
TABLE 6: Nonstructural mass components overview
Considering the structural and non-structural masses, the dimensions of the equipment, the payload specifications and the requirements of the assembly/packaging options, the general layout of the aircraft was created. The CoG location was located on 20%-25% of wings MAC and it dependents only on the battery and payload mass changes for different flight scenarios (low payload-long range and high payload- medium range) .
-
Dynamic Stability
The flight performance and Dynamic stability includes the investigation of aerodynamic coefficients and the stability derivatives using both numerical (panel method) code [6], [7] and algebraic calculations.The analysis was performed using vortex lattice methods for inviscid flow and further algebraic correction equations were used for viscous flow [8]. For the handling quality, a sophisticated Flight Control System was developed with a software capability to control the 2 propulsion motors, 4 vertical motors for Vertical Flight and the control surface servomotors. In addition, for Remote control mode the Flight Control System can be connected with a R/C receiver with a 14 channel transmitter in order to control its mode independently.
Figure 9: VLM analysis for aerodynamic performance
For the HEM performance during the Hover and steady vertical climb condition, the proposed methodology based on Flight Mechanics was introduced [9],[10]. The methodology takes into consideration the basic dimensions of the HEM and estimates the power on VTOL motors and the necessary aerodynamic forces on Vertical tail for efficient trim. The methodology investigates the stability around the longitudinal
and vertical axis regarding the side force, produced by lateral wind gust with magnitude 10 m/s.
Figure 10: VTOL operation: Acting forces (vertical view)
Figure 11: VTOL operation: Acting forces (Lateral view)
As the longitudinal stability is the most important due to the sensitivity with the Center of gravity during the fixed wing mode flight, the trim condition is estimated relative to the moment arm for various elevator deflections (e in degrees).
Figure 12: Static Longitudinal stability and elevator effectiveness
The static margin secures that the HEM is longitudinally stable, as shown in the figure above which corresponds to a static margin of 39% [11],[12],[13]. The real value of the complex phugoid and short period modes is on the negative axis, so HEM longitudinally is stable.
Figure 13: Longitudinal stability modes (short time and phugoid)
Figure 14: Lateral stability modes (spiral, roll, Dutch roll)
Even if, the spiral lateral mode is expected to be light unstable, this condition can be resolved using the high aileron surface correcting the possible dive during the turn and a 5- degree dihedral angle at the wing root.
For the Vertical Take-off and landing the CoG is placed below the rotors and it is unconditionally stable. The high disk loading secures the possible instability during the crosswinds due to the large side area of the fuselage.
For the HEM performance during the Hover and steady vertical climb condition, the proposed methodology based on Flight Mechanics was introduced. The methodology takes into consideration the basic dimensions of the HEM and estimates the power on VTOL motors and the necessary aerodynamic forces on Vertical tail for efficient trim. The methodology investigates the stability around the longitudinal and vertical axis regarding the side force, produced by lateral wind gust with magnitude 10 m/s.
TABLE 7: Hover/climb static stability parameters.
HEM side area Ss (m^2)
0,56
Air Density rho (kg/m^3)
0,9
Climb speed V climb (m/s)
1,5
Take-off Weight MTOW (kg)
24,2
Horizontal Distance between CoG and CP Xcp (m)
0,05
Horizontal Distance between CoG and propeller location lp (m)
0,4
Horizontal Distance between CoG and Vert. tail location lv (m)
0,9
For the stability around the longitudinal axis, the VTOL motors power must be changed to manage the crosswind.
Figure 15: Necessary Motor Power (Pvt) for VTOL crosswind operation
For the stability around the vertical axis, the vertical tail must be activated during the crosswind to manage the lateral gusts. The rear propeller can also affect the stability positively, introducing a stabilizing lateral force [12],[13].
The overall analysis led to a result that the HEM air worthiness and handing quality was excellent. Low modifications on Flight Control system and General layout were important, reaching the best quality criteria.
-
-
COMPUTER AIDED DESIGN (CAD)
The CAD overview was based on representation of aerodynamic surfaces and structural members. In addition joints, and nonstructural mass components were included checking the mass and inertia budget [14],[15]. Moreover, a modular design was set as priority including quick release joints between the connections. An easy to be transported aircraft in a box with maximum dimensions 1.5 m X 0.8 m X
0.8 following the requirements.
The whole structure was divided into smaller components that are easier to handle and store for transportation/ship ability purposes.Wings are locked on fuselage using lock pins which can be accessed from the lower part of the wing near the root. When the pins are unplugged, the wings were separated from fuselage structure.
Input Data for the HEMs crosswind stability on hover/climb conditions
Vertical Distance between CP and CoG H(m)
0,05
Lateral Distance between Motor position and CoG d(m)
0,65
Side Force coefficientCs
1,0
CrosswindVg (m/s)
1 to 10
Figure 16: Assembly/disassembly process of the main components
The skin structure on the upper aerodynamic surface of the aircraft relates to the fuselage structure using simple push clips .When the upper surface skin is removed the part of the inner structure is available for maintenance or adjustments. The securing parts of the VTOL motors support arms are also accessible. By turning the screws securing the support arms the latter can be removed.When the support arms of the VTOL motors are unplugged they can be easily removed from the aircraft and stored. Here it should be noted that they can be replaced with different arms with different motors given that the wiring for providing power is the same.
The payload box is inserted inside the payload bay and it secured in the horizontal plane using secure lock pins. These pins can be moved in proper slots in order to be adjustable for different payload boxes with various dimensions.
Figure 18: UAV HEM accommodation inside the transportation box
-
FINANCIAL ANALYSIS-COST IMPACT
For the financial funding of the HEM, extensive financial research on aviation industry was performed. The development costs were considered, and a break-even analysis was performed to estimate the return of investment (ROI).
Figure 19: UAV HEM Financial analysis
The break-even analysis is performed assuming that the customer will have paid the full amount upon delivery. If a different payment policy is chosen by the manufacturer the break-even point will change significantly andthe new results should be considered. Following this, a marginalprofitable plan is the sale of 60 units (at least) with 150K euro per unit cost.
Figure 17: Payload Cargo Bay basic components
All the components are gathered and placed inside a box for transportation. In the following figures the parts have been placed inside a box having dimensions 1500x850x700. The box dimensions can be further decreased if the components are placed carefully in predefined positions.
-
PRELIMINARY DESIGN CONCEPT
The preliminary design analysis was concluded to a mixed mode unmanned air vehicle (both fixed and VTOL) with advanced flight characteristics [16]. The basic layout is presented in Figure 20 and the technical specifications in Table 8.
Figure 20: UAV Hygeia Ex Machina (PDR view)
Lf/df=3.5
|
|
Empennage |
Inverted U-Tail configuration Horizontal tail NACA 0012
CFRP skin and CFRP skin 0.8 mm with Rohacell core foam for the control surface. Vertical tail (Tandem-Double Fin) structural component with 1mm CFRP skin and CFRP skin 0.8 mm with Rohacell core foam for the control surface. |
Unit Sale cost (without taxes) in euro |
150 K |
TABLE 8: UAV Hygeia Ex Machina Specifications
HEM Technical Specifications |
|
Main Dimensions |
Length: 1636 mm Width: 2846 mm Height: 825 mm |
Wing loading (W/S) (kg/m2) |
27.3275 |
CD |
0.108 |
Disk loading (DL) (kg/m2) |
22.58 |
MaxTOW (kg) |
21.862 |
Range (km) |
>100 for payload 3 kg >60 for payload 5 kg |
Battery pack |
Off the self, rechargeable and swappable batteries Voltage = 8-30V 2 x Thunderpower TP9000-6SHV(26.1 V) (for propulsion) 4 x Multistar High Capacity Lightweight 4S 6000mAh 2C Multi-Rotor Lipo Pack (14.8 V) (for VTOL rotors) 1x Turnigy Heavy Duty 5000mAh 3S 60C Lipo Pack (for electronic systems) |
Electronics |
ESC: TurnigyAquaStar 120A Watercooled ESC w/Programming Card Servos: 6 x Turnigy TGY-9018MG Metal Gear Servo 2.5kg/ 0.10sec / 13g |
Propulsion powerplant |
Pure electric motors Directly driven 2 motors/ propellers for fixed wing condition 2 x 1015 W AXI 4120/14 GOLD LINE V2 |
VTOL powerplant |
Pure electric motors Directly driven 4 motors/rotors for VTOL 4 x 1100 W AXI 5320/18 GOLD LINE |
VTOL Propellers |
Off the self, fixed pitch propellers 4 x Tiger Motor 22×6.6 CarbonFibre propeller |
Propulsion Propellers |
Off the self, fixed pitch propellers 2 x Quanum DJI Style Carbon Fibre Propeller 18×5.5 |
Vstall (m/s) |
23.0 |
Vcruise (m/s) |
26.56 |
Vmax (m/s) |
30 |
Wing |
wing with plain flap. Root airfoil: NACA 4421 Tip airfoil: NACA 4412 1mm. lateral bolts. Hoerner Winglets at the tips |
Fuselage |
|
Table 9: Hygeia ex Machina Drone Technical Specifications
REFERENCES
[1] Raymer D. P., Aircraft design: A conceptual approach, AIAA education series, 1992. [2] Roskam J. Edward L., Airplane aerodynamics and performance. Published by Design Analysis and Research, DARCorporation, 1997. [3] McCormick B. W., Aerodynamics Aeronautics and Flight Mechanics 2nd Edition, John Wiley & Sons, Inc., New York,1995. [4] Anderson. J. D., Jr, Introduction to flight, 3rd Edition, McGraw-Hill Book Company, International Edition, AerospaceScience Series, 1989 [5] Spedding G.R., McArthur, J., Span Efficiencies of Wings at Low Reynolds Numbers, Journal of Aircraft, Vol 47, No. 1,2010, p.p. 120- 128. [6] Drela M., Xfoil, an analysis and design system for Low Reynolds airfoils, MIT department of Aeronautics andAstronautics, Cambridge,Massachusetts
[7] Fluent Inc., FLUENT 6.3 User Guide, Sept. 2006. [8] McArthur J., faculty of the graduate school University of Southern California, aerospace and mechanical engineering, PhD.Dissertation Aerodynamics of wings at Low Reynolds number. [9] Philips W. F., Lifting Line Analysis for Twisted Wings and Washout-Optimized Wings, Journal of Aircraft, Vol 41 No.1,2004, p.p. 128-136 [10] Wilcox D.C. Turbulence modeling for CFD , DCW Industries,
November 1994
[11] Mosak P., Winglet design for sailplanes, Free flight 2/92. [12] Maughmer M. D.,Design of winglets for high performance sailplanes, AIAA 2001-2406 , 2003, Vol 40, No.6 [13] Abbot, I,H., and von Doenhoff A. E.: Theory of wing sections, 2nd Edition, Mc Graw-Hill Book Company, New York, 1949;also, Dover Publications, Inc., New York, 1959 [14] Houghton, E.L., Carpenter, P.W.,: Aerodynamics for Engineering Students, 5th edition, Buttreworth-Heinemann,Oxford,2003. [15] Megson, T.H.G. : Aircraft Structures for Engineering Students, 3rd edition, Buttreworth-Heinemann, Oxford, 1999 [16] Perkins C.: Airplane Performance ,Stability and Control, 1st edition Wiley,1949