
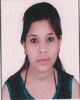
- Open Access
- Authors : Lalita Katre , Badal Harinkhede
- Paper ID : IJERTV10IS030127
- Volume & Issue : Volume 10, Issue 03 (March 2021)
- Published (First Online): 26-03-2021
- ISSN (Online) : 2278-0181
- Publisher Name : IJERT
- License:
This work is licensed under a Creative Commons Attribution 4.0 International License
Continuously Reinforced Concrete Pavement: A Review
Lalita Katre
-
ech Student, Civil Engg. Department School of Engineering Technology G H Raisoni University Saikheda (M.P.)
Badal Harinkhede
Assistant professor , Civil Engg. Department School of Engineering Technology G H Raisoni University Saikheda (M.P.)
Abstract Recently there has been a significant shift in transportation mode from Railways towards the Road sector. Nowadays about 60 percent of freight and 80 percent of traveller transport is met by Road transport in our nation, that demonstrates the requirement for development of an honest road network. In our nation flexible pavement (bitumen) is commonest for each national and state highways. Majority of roads are engineered with typical hydrocarbon bitumen pavements considering its lower initial value, although the life cycle value of those pavements are terribly high compared to rigid pavements because of frequent repairs and conjointly want for complete resurfacing at interval of 4-5 years. Any fuel consumption of vehicles is far higher on this sort of pavement than that on rigid pavement.
Continuously reinforced concrete is often a wonderful pavement solution for ponderously traveled and loaded roadways, together with interstate highways. These days CRCP are often designed and constructed systematically and reliably to produce superior long-term performance with immensely low maintenance.
Keywords Continuously reinforced concrete, Transverse construction joints, Crack Spacing, Steel stress, Crack Width, Steel Reinforcement.
-
INTRODUCTION
Continuously reinforced concrete pavements (CRCP) contain continuous longitudinal reinforcement, typically steel, and dont have transverse joints except wherever necessary for construction functions or at bridge approaches or transitions to alternative pavement structures. Continuous reinforcement could be a strategy for managing the transverse cracking that happens altogether new concrete pavements. In new concrete, natural volume changes because of cement-water hydration are restrained by the pavement base and alternative physical options adjacent to the concrete, inflicting stresses to develop within the concrete. The aforementioned stresses develop faster than the concrete's strength thus, at certain point, full- depth cracks form, effectively dividing the pavement into individual slabs.
In concrete pavement the longitudinal reinforcing steel is continuous all over the pavement length. Its a joint less concrete pavement sufficiently bolstered to regulate cracking, without the help of weakened transverse joints such as are utilized in ordinary or conventional type of articulate concrete pavement. Reinforced bars within the concrete are lapped to make continuous reinforcement holding the pavement along altogether varieties of weather and preventing formation of enormous cracks that might otherwise cut back the service
lifetime of the pavement. CRCP has all the significant benefits of concrete pavements like durability, high structural strength, nonskid surface and sensible visibility at midnight, wet or dryfeatures that build concrete, and particularly continuously reinforced concrete, a permanent road egression material.
-
FUNDAMENTALS OF CRCP DESIGN Coming up with a CRCP involves orientating the various geometric pavement features like thickness, longitudinal and crosswise or transverse reinforcement, construction joints, slab width, shoulders, and pavement transitions supported on site-specific traffic, climatic, and premise parameters. The designer selects pavement styles that will be appropriate to realize the required performance level for the design stretch selected. As in all pavement designs, the aim is to use provincially obtainable materials to the greatest extent viable, but without any adjustment of pavement performance. The crack spacing, crack width, steel stress, and bond development length inaugurated as a function of reinforcement restraint and atmospheric conditions each affect the CRCP structural integrity in the long period. Its necessary that carefulness has taken during the CRCP design, materials choice, and construction method so that a crack pattern develops that minimizes development of pavement distresses.
Punchouts: A punchout is a sort of distress that usually occurs between closely spaced transverse cracks in CRCP. It is defined as a block or wedge of CRCP thats delimited by 2 contiguous transverse cracks, a longitudinal crack, and the pavement edge.
-
BEHAVIOR OF CRCP
Following construction of a CRCP, variety of mechanisms impact progress of stresses in the slab and thus the genesis of cracks. Throughout the early age, temperature and moisture alterations bring on volume modification in the concrete that are restrained by reinforcement and base friction, resulting in the event of stresses.Since concrete is weak in tension, whenever the stresses that develop are beyond the tensile strength of the concrete, transverse cracks carve to mitigate the stresses. Reinforcement obeys to keep cracks closed as safeguarding the cracks tight is necessary in nourishing load transfer through aggregate interlock. This, in turn, decreases pavement flexural stresses because of traffic burdening.
Tight cracks are also advantageous to circumvent water infiltration and intrusion of incompressible through the
cracks. Consecutive drops in temperature and therefore the impact of drying shrinkage in the concrete tend to diminish the transverse crack spacing further. Externally-influenced stresses because of wheel loads, and subsequent seasonal (climatic) changes, further decrease the crack spacing over time, however at a far slower rate. Overall, its been observed that the crack spacing declines rapidly throughout the prior age of the pavement, as far as about one or two years. Behind this stage, the transverse cracking pattern remains identical until the slab reaches the end of its fatigue life.
-
CRACK SPACING
CRCP slab tranche distribute traffic loads in the longitudinal and transverse directions. In the exhibition of short transverse crack spacing with penurious load transfer, although, the slab can perform further as a beam with its lengthy dimension in the transverse direction. Noteable transverse flexural stresses because of traffic loading can then emerge.
Consequently, longitudinal cracks may eventually form, developing into a distress state generally known as a punchout. On the other side, larger crack spacings can cause wider cracks that have underneath load transfer and are more liable to spalling. Estimation of long-term execution of CRCP informs that CRCP with reasonable subbase support, and with extended lanes or tied concrete shoulders, provided magnificent durable performance.
It come into sight from these more neoteric considerations that crack spacing does not emerge to have as remarkable an effect on punchouts or other distresses as was formerly believed. To cut down both of CRCP distresses, the AASHTO-86/93 Guide suggests controlling crack spacing to fall between 3.5 and 8 ft (1.1 m and 2.4 m). It has been observed, however, that crack spacings of less than 2 ft (0.6
m) have executed well under good soil-support situations. An examination of LTPP data has shown some trend for a higher possibility of punchouts when crack spacings are there.
-
CRACK WIDTH
Crack widths have a critical impact on CRCP execution in various ways. Immoderate crack widths may lead to unpleasant situations such as infiltration of water that could later consequence in orrosion of the reinforcing steel and softening of the support layers. Incompressibles can also enter into vast cracks, and since the pavement is restrained to contraction and expansion as well as traffic burdening, this can in turn result into excessive bearing stresses at the cracks. If uncurbed, these stresses can generate crack spalling. Furthermore, wider cracks mean that less contact exists between the faces of the crack, resulting in indigent aggregate interlock. The result of this is an increment in slab deflections and flexural stresses that, in turn, lead to more spalling, faulting, secondary cracking, and punchouts. Generally, an excessive percentage of longitudinal steel leads to smaller crack widths. The consequences of field performance estimations have found that an ample amount of longitudinal steel in the span of 0.6 percent to 0.85 percent adequately keeps crack widths rationally dense all over the pavement life.
The depth of the reinforcement is an extra necessary component in controlling crack width. Utmost inspection in Illinois reveals that when reinforcement is allocated above mid-depth, the cracks are further confined leading to inferior punchouts and patch up over the long term. For reasons of enough cover, reinforcement should not be allocated closer than approximately 3.5 to 4 in (89 to 101 mm) from the surface of the CRCP.
-
REINFORCEMENT STRESS
The magnitude of stress that evolve in both the concrete and reinforcement will also affect CRCP performance in the long term. As mentioned earlier, the reinforcement obeys to prohibit volume changes in the concrete, keeping cracks dense. Consequently, serious stresses emerge in the reinforcement at the crack locations. Reinforcement design has to consider viable fracture and/or intemperate plastic distortion at these locations. Excessive yield or fracture of the reinforcement may lead to wide cracks, corrosion, and loss of load transfer that may later consequence in nasty distress.
-
-
DESIGN INPUTS OF CRCP
-
The design inputs of CRCP are divided into six major categories as follows:
-
Design Criteria
-
Concrete Properties
-
Reinforcement Type and Properties
-
Pavement Support
-
Climate
-
Traffic
-
CRCP DESIGN CRITERIA
Design criteria for CRCP are often no different than other concrete pavements; however, some divergences do exist and are worth noting. Design criteria are pre-established criterion that are needed when designing a pavement structure.
1. Restricting or limiting Criteria on Crack Spacing, Crack Width, and Steel Stress
The AASHTO-86/93 Guide nominates managing crack spacing to fall within 3.5 to 8 ft (1.1 m to
2.4 m). However, the new CRCP design approach expressed in the AASHTO Interim MEPDG does not provide suggestions on the command of minimum crack spacing due to the several components that affect this variable involving reinforcement percentage. A maximum average crack spacing of 6 ft (1.8 m) is however suggested. While it does not determine a minimum crack spacing, the AASHTO Interim MEPDG does rather suggest designing for small crack widths to assure durable performance.
The AASHTO-86/93 Guide limits the crack widths to 0.04 in (1 mm) to avert spalling. However, crack widths of 0.024 in (0.6 mm) have been found to be more worthwhile in decreasing water penetration, and thus diminishing corrosion of the steel, nourishing the integrity of the support layers, and securing high load transfer efficiency. The AASHTO Interim MEPDG speculates and requires a maximum crack width of 0.020 in (0.5 mm) over the whole design period. Regardless of what approach is used, the use
of corrosive deicing salts should be taken into attention when choosing the crack width measure. Reinforcement design has to consider possible fracture and/ or excessive plastic distortion.
To achieve this, the stress in the reinforcement is generally limited to a suitable percentage of the utmost tensile strength to not only avert fracture, but to limit the amount of plastic deformation. Table 1 shows the utmost permissible working stress for steel with yield strength of 60 ksi (420 MPa) that is suggested by the AASHTO-86/93 Guide. It can be noted that in some cases, the AASHTO- 86/93 Guide permits a working stress above the yield strength that could result in a contingency of some plastic deformation. Consequently, it should be noted that a-little wider crack openings may result when permanent deformation is permitted.
-
CONCRETE PROPERTIES
Furthermore, to strength of concrete and elastic modulus, a numerous of other concrete properties effect CRCP performance. These involve the heat of hydration, coefficient of thermal expansion, and shrinkage potential of the concrete mix. All concrete properties should be flawlessly selected conforming to site-specific conditions so that ample of structural extent is granted, capable of resisting the assumed traffic loads. The concrete should also have the required characteristics to undergo the contemplated environmental conditions.
Durability characteristics like alkali-silica reactivity (ASR) potential, freeze-thaw damage, sulfate attack, and others that can be reduced or even avoided with appropriate design of the paving mixture. Perhaps, this should be appraised throughout the design of the pavement via the buildout of project specifications and/or special provisions.
-
REINFORCEMENT TYPE AND PROPERTIES Various kinds of reinforcement have been utilized in CRCP, but by far the most usual is deformed steel bars. Other innovative materials involve solid stainless steel, stainless steel clad, and other proprietary materials like fiber reinforced polymer (FRP) bars. Regardless of a higher upfront or initial cost, these all oath to give more corrosion resistance than steel bars. At present, however, execution of these materials has been more targeted more for their use as dowel bars. Deformed steel bars are the most widely trusted type of reinforcement for CRCP.
The variation in volumetric changes in the steel and the concrete produces stresses in both materials. Stress transfer from the steel to concrete depends on the steel surface area and the shape of the surface deformations on the reinforcing bar (rebar). It is thus important that the rebar conform with requirements specified in AASHTO M 31, M 42, or M 53 for billet-steel, rail-steel, or axle-steel deformed bars respectively. The needed yield strength of reinforcing steel for use in CRCP is usually 60,000 psi (420 MPa), designated as English Grade 60 (metric Grade 420).
The use of higher quantities of carbon in steel production generally increases its strength, but often with no noteworthy change in its elastic properties (modulus) which control crack widths. The elastic modulus of steel
reinforcing bars is generally in the order of 29,000,000 psi (200,000 MPa). Another property of interest for CRCP reinforcement design is the coefficient of thermal expansion of the steel. Depending on the difference in the steel and concrete CTE, differing restraint will consequence, leading to different crack patterns.
-
PAVEMENT SUPPORT
BASES
Pumping of support layer material through CRCP cracks and joints is a common mechanism furnishing to punchout formation. The erosion produced by pumping action may also result in enlarged pavement deflections that can lead to spalling at the cracks. The use of a base layer built with non-erodible, impermeable materials is generally enumerated on CRCP subjected to hefty traffic loads to minimize pumping. In addition to managing pumping, the base layer provides a steady platform during construction and may serve other motives like controlling frost action and controlling shrink and swell of the subgrade because of moisture changes.
The structural foundation that the base layer yields to the pavement depends primarily on its thickness and stiffness (elastic or resilient modulus). A stabilized base is usually 4 to 6 in (100- to 150-mm) wide as utilized under CRCP. A minimal base thickness of 4 in (100 mm) is needed for constructability contemplation. Significant base thicknesses should be issued when unstabilized materials are utilized and/or to control frost action or shrink-swell subgrade conditions. In these instances, a well-graded granular non- frost liable material may be used for the additional needed frost susceptible depth.
-
SUBGRADES
The performance of any pavement – involving CRCP – is affected by the support given by the subgrade. Subgrades that provide constant support and that are not affected by moisture differences consequence in better performing pavements than those with shrinking and swelling changes due to moisture alterations. To grasp benefit of the support capabilities of a subgrade, the designer should provide sufficient drainage and stabilization of the subgrade materials as needed. Additionally, it is suitable to divide the project in sections with similar support characteristics for pavement design purposes. The use of abrupt transitions between cuts and fills are needed, mainly in bedrock areas or at bridge approaches, to reduce stresses under the slab due to differential support. It has been noted that even in areas that exhibit constantly poor support (as opposed to intermittent support), CRCP has demonstrated superior performance.
-
DRAINAGE
While far less than for jointed pavements, water infiltrating through cracks and joints in a CRCP may bestow to moisture-accelerated damage because of erosion and loss of support underneath the pavement slab. While ensuring tight transverse crack widths may reduce the infiltration of water, the use of erosion resistant balanced bases may be
warranted, especially for pavements exposed to high levels of precipitation and/or high traffic volumes.
-
-
CLIMATE
The climatic conditions anticipated during placement and during the service life of the CRCP should be considered during the design stage as they affect the cracking nature and thus may affect the potential growth for punchouts in the long term. For example, the precipitation expected in the region will affect the selection of the drainage system required.
CRCP construction in hot climatic areas causes an increment in the concrete heat of hydration and thus the slab temperature at set. Antecedent temperature drops can result in short crack spacings and meandering cracks, increasing the potential for punchout occurrence.
Additionally, when surfacing during hot weather, the pavement is more liable to experience excessive moisture loss from the pavement surface, which may result in subsequent spall development. Apart from air temperature, low ambient humidity, and high wind speeds can also contribute to higher moisture loss from the concrete surface. While climatic influence on early-age CRCP behavior will vary based on the project location and time of year of construction, previous investigations of early-age CRCP behavior have demonstrated that the time of day when the pavement is situated can affect the crack pattern.
For example, when constructing CRCP in hot weather and placing in the late afternoon and early evening, the concrete heat of hydration will usually occur at a different time than the peak air temperature. This can consequence in a lower temperature drop in the concrete, and thus more uniform crack spacing.
While designing CRCP, sufficient selection of the design temperature drop should be made. The design temperature drop is occasionally based on both the average concrete curing temperature after placement and the lowest slab temperature during the year for where the CRCP will be constructed:
where,
TD = TH – TL
TD Design Temperature Drop (°F or °C) TH = Average concrete curing temperature after placement (°F or °C), and TL = Average daily low temperature during the coldest month of the year (°F or °C).
-
TRAFFIC
The level of traffic to which a pavement structure will be subjected dictates a number of design considerations. All pavements, involving CRCP, are initially designed to restrict the level of traffic loads to which they will be subjected under specific environmental situations. For this cause, traffic is distinguished based on how it will affect the level of stresses in the pavement structure. Primary traffic characteristics involved load configuration, traffic volume, traffic classification, traffic distribution, growth rate, and traffic wandering.
4. CRCP DESIGN METHODS
Several design procedures for determination of slab thickness and the quantity of reinforcement needed in CRCP have been thrived in the past. The two most pertinent because of their common use and/or level of validation include:
-
AASHTO-86/93 Guide for Design of Pavement Structures
-
AASHTO Interim MEPDG AASHTO-86/93 Design Procedure Although the AASHTO-86/93 Guide method does not directly consider one of the initial failure mechanisms in CRCP (punchout development), this procedure has been used for design of CRCP by making similar considerations to those for the design of braced/jointed concrete pavements. Additionally, because reinforcement keeps cracks compact in CRCP, a-little improvised load transfer coefficient is usually used, which consequences in a moderate reduction in thickness for this pavement type under similar traffic and environmental conditions. The AASHTO-86/93 method also includes design methods/procedures for the selection of reinforcement. These procedures are based on a desired span of crack spacing, maximum crack width, and maximum steel stress. It should be noted that it has been reported that this design procedure tends to misjudge the needed steel. The AASHTO-86/93 design procedure is currently the most extensively used design procedure for design of CRCP.
AASHTO Interim MEPDG
Over the last tenner, the National Cooperative Highway Research Program (NCHRP) has managed a crucial effort to develop the next generation of pavement design procedure based on mechanistic- empirical methods. In this design procedure, specific mechanistic-empirical models for prognosis of CRCP performance have been developed. The task starts with the choice of a trial design including layer thicknesses, materials, reinforcement, shoulder features, and construction information. Site-specific situations including environment, foundation, and traffic are also considered. Performance norms in terms of punchouts and IRI are then specified, along with the reliability level for each measure. The MEPDG also has limiting design criteria on crack width (over design period), crack spacing, and crack load transfer efficiency (over design period as well). The method precisely predicts punchout development as a function of the crack width and load transfer efficiency due to aggregate interlock at transverse cracks.
Stresses due to loading are predicted as a function of load transfer efficiency, and continuously evaluated and modified throughout the design period. Exhaust damage as a function of the stress level and strength is estimated and gathered, and punchout development is subsequently predicted.
IRI is also predicted during the design period as a function of the initial smoothness conditions, punchout evolution, and site-specific conditions. Once the trial design is estimated, its predicted performance is checked against design criteria at the specified reliability level. If the design requirements are satisfied, the trial design is considered as a
viable alternative that can later be evaluated in terms of lifecycle costing. Contrarily, a new trial design is estimated.
-
ADVANTAGES OF CRCP
Following are the advantages of Continuously Reinforced Concrete Pavement:
Joint less concrete pavement, CRCP renders magnificent smooth riding surface for the vehicles that maximizes the comfort for the passenger
CRCP is more durable, which can last 40-50 years without much maintenance problem during the life of the pavement. Concrete actually hardens over time. After its first month in place, concrete continues to slowly gain about 20% strength in first 12 months.
It needs nominal cost of maintenance and reclamation.
It minimizes the baneful dynamic loads that are implemented to the vehicles and pavement.
It offers best visibility. Concrete emulate light, which increases visibility and can save on street lighting costs. During summer riding over flexible pavement causes difficulties due to bitumen sticking to the tyres. Visibility also gets afflicted due to sparkling pretense of flexible pavement.
Air and noise environment revamp along the widely populated existing corridor. The noise level would diminish substantially.
Concrete can withstand even the heftiest traffic loads. There's no need to worry about ruts, shoving effects common with asphalt pavements.
Concrete's hard surface makes it smoother for rolling wheels. Studies have even appeared that this can increase truck fuel efficiency. Savings in fuel to the amount of 20 percent, may be considered eventually reducing the vehicle operating cost.
Concrete roads accelerate increased speed and thereby savings in time and money. Nearly maintenance free service decreases traffic disturbances and thus reduces man-hour loss to the road users.
-
CONCLUSION
-
In comparison with flexible pavement, CRCP gives additional design life of at least 10 years. Further, it offers vastly superior riding quality, less disruption to traffic movement and substantial saving in vehicle operating cost comprising reduced consumption of fuel, lubricants etc.
Despite possible higher upfront cost, building highways using CRCP could give a number of advantages such as lower durable life cycle cost, low maintenance (because of the absence of transverse joints), reduced water penetration due to lesser joints and tighter transverse cracks, smoother pavements over time (because of the absence of transverse joints), and capability to handle burlier truck loading and volumes. Further, at the end of service life, it can be comfortably converted to a composite pavement by utilizing Hot Mix Asphalt (HMA) overlays or using thin bonded concrete overlay, to give a enduring and smoother pavement.
REFERENCES
-
Seongcheol Choi a, Soojun Ha b, Moon C. Wonc Horizontal cracking of continuously reinforced concrete pavement Sunder environmental loadings.
-
By seong-min kim effect of bond stesses & slip model for continuously reinforce concrete pavements.
-
Amrut Nashikkar,Nirav Shah Siddharth, Nautiyal Vinayraj, A.K.Vivek Sahay In Partial Fulfilment of the requirements of the course Infrastructure Development and Financing.
-
E J Yoder Concrete Roads Alternate Construction Methods, Brajendra Singh, Principles of Pavement Design, National Seminar on Concrete Roads & pavements.
-
CRCP design and construction practices in USA, Web Site of Cement Reinforcing Steel Institute (CRSI) [6] V. William, Jr. P.E Wagner, Reinforcement is an asset to concrete, Wire Reinforcement Institute, Inc., Mclean, Virginia.
-
Life Cycle Cost analysis & Techno-Economic Study for the use of Reinforced Concrete Roads in National Highways & Expressways,
INS/Pub/035
-
Pydi Lakshmana Rao & S R Mediratta, Building Better Roads with Continuously Reinforced Concrete Pavement for Airports Runways, National Highways & Expressways, American Concrete Institute,
ACI, India Chapter 23
-
Pydi Lakshmana Rao, Continuously Reinforced Concrete Pavements
The Path of Wisdom (Durable, Virtually Maintenance Free, Environment Friendly, Saves Fuel & Money), Journal IRC