
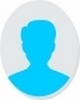
- Open Access
- Authors : Saurav Patwardhan , Advay Deshpande
- Paper ID : IJERTV11IS090076
- Volume & Issue : Volume 11, Issue 09 (September 2022)
- Published (First Online): 28-09-2022
- ISSN (Online) : 2278-0181
- Publisher Name : IJERT
- License:
This work is licensed under a Creative Commons Attribution 4.0 International License
Comparison of Strength of Generatively Designed 3D Printed Models under Uniaxial Load
Saurav Patwardhan
Department of Manufacturing Engineering, College of Engineering, Pune
Department of Mechanical Engineering, College of Engineering, Pune
Advay Deshpande
Department of Manufacturing Engineering, College of Engineering, Pune
Department of Mechanical Engineering, College of Engineering, Pune
Abstract This research aims to investigate the utility of generative design as a viable alternative to conventional design practices for structural members on the basis of strength and deformation. The necessity of generative design may arise due to either space constraints in a particular application or the need for a specific load taking capacity from a set amount of material mass. In this project, a total of 3 models were created one for tension, one for compression and one for bending; first according to generative design using an artificial intelligence computer software and then according to conventional design practices and known specimens. It was ensured that the masses of these models were approximately equal. These models have then been 3d printed using an open-ware printer using ABS plastic by the FDM process and have been tested using ramped loading to compare their load bearing ability, strength, and failure pattern.
Keywords3d printing, anisotropy, fused deposition modelling, failure pattern, generative design
-
INTRODUCTION
Generative design is an iterative design process that involves a program that will generate a certain number of outputs that meet certain constraints, and a designer that will fine tune the feasible region by changing minimal and maximal values of an interval in which a variable of the program meets the set of constraints, to reduce or augment the number of outputs to choose from. Generative design is a CAD engineering software function in which a designer collaborates with artificial intelligence algorithms to generate and evaluate hundreds of potential designs for a product idea. The process starts with defining the goals and constraints of the project. These include, but are not limited to, design parameters such as product size or geometric dimensions, permissible loads and operating conditions, target weight, materials, manufacturing methods, cost per unit. By using generative design, engineers can create and simulate thousands of designs in a fraction of the time it would normally take. As additional benefit, the generative design process can yield highly customized complex shapes as the best solutions which can be cast or processed through high- resolution additive manufacturing.
Automated software that can take load and space constraints as inputs and then generate completely organic designs is freely available in the market today. These software generated CAD files that can be further manufactured using additive manufacturing techniques. It is
impractical, costly and often impossible to manufacture these complex shapes using subtractive manufacturing techniques due to the presence of numerous curves, angular features and irregular holes and cavities along with a lack of symmetry and regularity in the design. Practical applications of such generative designs are slowly entering the mainstream industrial domain now. Generative design has been extensively used by architectural firms for new building designs because of the flexibility it offers in that it can work its way around many spatial or material constraints to provide optimal design solutions.
Fig. 1. Application of Generative Design Motorbike Swingarm
It is observed here that generative design is used not only because it was impossible to use conventional design in that application but as a better alternative to conventional design practices. The possibility of weight reduction using generative design has been well documented. But there is a lack of information regarding the strength of generative designs when compared to conventional design which we aim to explore. This question will go a long way in determining whether generative design should be used only where conventional design fails to suffice or will it eventually be considered as a completely better alternative altogether which can give multifaceted advantages like weight reduction, higher load taken to material used ratio, greater flexibility in fixturing possibilities for mating parts as compared to conventional designs.
-
LITERATURE REVIEW
Although 3D printing is only recently starting to become mainstream with a large number of applications, it has been the subject of a great deal of research. Research which
involves varying process parameters and studying their effect on the quality of the print is widely available.
The work of Tianyun Yao et al. has been critical in understanding the behaviour of 3D printed models using an experimental approach [1]. The PLA (Polylactic Acid) material specimens, designed according to the current plastic- multipurpose test specimens standard ISO 527-2-2012, were printed in seven different angles
(0, 15, 30, 45, 60, 75, 90) with three layer thicknesses
(0.1mm, 0.2mm, 0.3mm) for each angle. The relative
residual sum of squares between theoretical data and experimental data were all close to zero, so the results that the theoretical model can accurately predict the ultimate tensile strength of FDM materials for all angles and thicknesses were confirmed. It was also found that the ultimate tensile strength decreased as the printing angle becomes smaller or the layer becomes thicker.
Tianyun Yao et al. have also published a thorough comparison of the analyses of the theoretical model and experimental result which focus on the separation angle and tensile failure [2]. Most of the research is based on the experimental approach and comparing the failure of the same material, varying the parameters that affect the strength. Almost all the previous research showed that the 3D printed parts are anisotropic by nature i.e., they exhibit different strengths in a different direction. The raster orientation defines the direction, and the strengths are different parallel to it and perpendicular to it. The strength of the part is highest when the raster orientation is parallel to the loading direction, and it starts to decrease as the raster angle increases. A minimum stress value is attained when the raster angle is 90 degrees [3].
Behzad Rankouhi et al. have conducted the same research using ABS as their test material. In this study, a comprehensive effort was undertaken to represent the strength of a 3D printed object as a function of layer thickness by investigating the correlation between the mechanical properties of parts manufactured out of acrylonitrile butadiene styrene (ABS) using fused deposition modelling and layer thickness and orientation [4]. Divyathej M, Varun M, and Rajeev P have carried out a series of mechanical tests on ASTM standardised parts for ABS [5]. They performed a tensile test, compression test, flexure test, and thermogravimetric analysis. Bishwonath Adhikari has conducted research investigating the failure mechanisms of 3D printed parts in his thesis [6]. James Allum, Andy Gleadall, and Vadim V Silberschmidt have investigated the fracture of 3D printed polymers. They have questioned whether the major cause of 3D printing failure is weak layer bonding as is widely accepted [7]. They hypothesize that the micro-scale geometric features on the filament may be an important factor in the failure of these prints.
Evangelos Tyflopoulos et al. have publised a comprehensive review studying the current state of generative design and understanding the future needs and scope of generative design [8]. On structural design and optimization, Hu et al. have presented a texture-guided generative structural design approach based on topology optimization and texture synthesis [9]. Cang et al. introduced
a one-shot generation of near-optimal topology by a novel machine learning mechanism [10].
Christoph Bader and Neri Oxman have presented a novel generative design algorithm aimed at multi-material 3D printing [11]. The method offers a fast, automated, and controllable way to explore an expressive set of symmetrical, complex, and coloured objects, which makes it a useful tool for design exploration and prototyping. They describe a recursive grammar for the generation of solid boundary surface models suitable for a variety of design domains.
It is observed that there has been substantial research on the mechanical properties of standardised 3D printed specimens and there is a considerable amount of literature that deals with generative design and additive manufacturing. However, there has been no overlap between the two and there is no available data to specifically study the mechanical properties of generatively designed 3D models. Here we aim to bridge this gap.
-
EXPERIMENT DESIGN AND METHODOLOGY Our aim is to study and compare 3d printed models of
generatively designed structural members with conventionally designed structural members for load bearing capacity, strength, and failure occurrence.
Software Used: Autodesk Fusion 360 (Academic), Solidworks 2018
3D Printer Used: Lulzbot FDM Printer (0.5mm nozzle) Apparatus: Steel wire, plywood frame, M6 screws, plastic bucket, electronic weighing scale, stopwatch
-
Model Creation and 3D Printing
Two sets of models were to be created. Each set of models would have 3 models: Tension specimen, Compression Specimen, Bending specimen
-
Generative Model Design: The generatively designed components were created first using the generative design space in Autodesk Fusion
360. For tension & compression, two square plates were given to the algorithm with a fixed load. For bending, a vertical plate with fixture holes was generated and a perpendicular groove to take the load was modelled and given to the software.
Procedure followed:
-
Create preliminary fixture models which are basic shapes to fix the model to the testing frame
-
Create the necessary holes and additional cylindrical bodies around these holes to indicate obstacle geometry and facilitate the fixation of the models to the testing frame.
-
Specify the fixture plate and load bearing features as geometry to be preserved. Specify the cylindrical bodies around the holes as geometry to be avoided.
-
Apply the load scenarios and amounts.
-
Specify manufacturing method, permissible overhang and other manufacturing related inputs like infill
%.
After specifying these constraints, the software solves several iterations and provides 2-3 converged solutions after some time. Once these solutions are generated, the converged solution can be used to create a new part in Fusion 360 after which it can be exported into an STL file ready for 3D printing.
Note The model for tension had some geometry protruding out of the square plate. Hence, around 2.5 mm of material was added to the square plates on one side to orient it properly for 3D printing.
Fig. 2. Generative Models
-
-
Conventional Model Design: Each generative model was analysed for its mass properties using the inbuilt feature of Fusion 360 and each models mass was noted.
-
Conventional Compression and Tension
These models were designed keeping in mind the standard tensile test specimen.
Fig. 3. Standard Tensile Test Specimen
The cross-sectional area of the column for the tension and compression test model was selected in such a manner that the total mass of the model would be approximately equal to that of the generatively designed model. A suitable fillet was given, and the cross section was reduced to ensure that failure only occurs at the reduced cross section. Hence, there is a difference in the cross-sectional area of the model for compression and tension.
Fig. 4. Conventional Models Tension, Compression
-
Conventional Bending:
A standard cantilever beam design was taken as the basis of the model. A beam of uniform cross-section was created with its length and groove position the same as that of the generatively designed part. However, the mass was found to be lesser than the generative bending specimen. Suitably sized triangulations were added to the cantilever such that the mass of the model became approximately equal to the mass of the generatively designed model. Triangulation is used in frame structure to provide it strength and support.
Fig. 5. Conventional Model Bending
-
-
3D Printing Process: Due to the complex design features in the models, subtractive manufacturing is not suitable for these models. Owing to its low cost and ease of use, 3D printing is selected as the preferred method of manufacturing the models. The models for this project were created using Fused Deposition Modelling. 3D printers which use FDM Technology construct objects layer by layer from the very bottom up by heating and extruding thermoplastic filament. Specialized programs or Slicers "cut" CAD models into layers and computes the way the printer's extruder would assemble each layer. In addition to thermoplastic, a printer may extrude support materials too.
-
Review of Print Orientation and Anisotropy in FDM Parts: When 3d printing any part, which is going to take load, print orientation becomes crucial. This is due to the inherent anisotropy that FDM parts
possess due to their layer-by-layer construction. As a 3D Printer builds the object layer by layer, so the strength in the Z-axis is impacted by the internal bonds between the layers. The part made by most 3D printing technologies is strong in X- and Y- axes, and weak in Z-axis, because the bonds formed between layers are weaker. The general conclusion is all the internal bonds are referred to as anisotropic, which means their physical properties are different when measured in different directions.
Fig. 6. Anisotropy in 3D printing
The part should be oriented so that it would be printed with layers matching the required axis of strength, and it often works when part receives mechanical stress from only one direction. For functional parts, it is important to consider the application and the direction of the loads. For example, FDM parts are much more likely to delaminate and fracture when placed in tension in the Z direction compared to the XY directions (up to 4-5 times difference tensile strength). If a part is oriented horizontally such that the layers will be perpendicular to the acting force, the layer adhesion becomes an important factor that will need to be considered. Under such a force, the ABS fibres will not undergo any elongation or compression, instead, the layers will delaminate and peel off one after another. Thus, it becomes essential to orient the part such that the force acting on the part is along the axis of the fibres. This will allow the fibres to take any occurring tensile or compressive stress and give the part much better mechanical properties. The same has been illustrated using the models used in this project below:
Fig. 7. Print orientation Cura Slicer Software
-
-
Model Observations
Fig. 8. 3D printed models overview (with weighing scale)
All 6 models were successfully printed one at a time. As the printer is an openware printer, some warping and deformation were observed as expected. Some warping was observed at the end plates on the tension and compression models. More importanly, all the load bearing features and geometries were printed sufficiently accurately. There was a considerable amount of support structures that were necessary to print the generative models. These support structures were manually removed using a heated blade and pliers subsequently. The parts were then weighed on an electronic scale to ensure that each pair of parts is of approximately the same mass.
The masses have been tabulated below:
TABLE I. MASS OF 3D PRINTED MODELS
Sr. No
Load Type
Mass of Generative Model (gm)
Mass of Conventional Model (gm)
%
difference between masses
1
Tension
80
77
3.75%
2
Compression
57
55
3.51%
3
Bending
100
96
4.00%
The masses of the generatively designed models are slightly greater than those of the conventionally designed models. This is likely due to some residual support structures sticking onto some of the thinner features. These structures could not be aggressively removed due to the possibility of the load bearing feature completely breaking. However, the differences are quite small as can be seen from the table.
-
Testing Setup Description
Conventionally, tests for tension and compression are done on a Universal Testing Machine which plots the results on its control computer.
However, it required a standard specimen having a defined shape. This was not possible in this particular case as the generative models are irregular and not of a standardised shape and dimension. Hence, those models cannot be suitably tested in a universal testing machine.
Instead, a uniform testing setup which can be applied to both the conventional models and the generatively
designed models was deemed necessary for easy and reliable comparison between the two. For this purpose, a wooden frame was designed as follows:
Fig. 9. Testing Setup Components
Thicknesses: Square Plate = 18mm
Pillar = 36mm Material: Plywood Weight= 15.2kg Additional wt. = 20kg (for stability)
The loading was done in a ramped manner. The load was increased incrementally with respect to time till the model failed.
-
-
OBSERVATIONS
All the models were designed to take a load of 10 kg i.e.
98.1 N. The factor of safety that was taken was 2. So, it is expected that the components take at most 20kg i.e. 196.2 N force without yielding or deforming excessively. The testing setup designed for this experiment was designed to sustain a load of 50 kg i.e 490.5 N at the most. If the specimens do not fail even at this load, a new testing method should be used to test them to see which one fails first, the conventional design or the generative design.
-
Tension Specimens
Both the tension specimens were subjected to ramped loading by attaching them to the top surface of the testing frame and suspending the weight using a steel wire. The tension specimens successfully sustained the load without any kind of deformations. They were tested till a load of 50 kg i.e. 490.5 Newton. The conventional tension specimen only underwent a slight deformation and bending on the bottom square plate to which the load was attached.
Fig. 10. Tensile Models Conventional, Tensile
This is most likely due to the weight being slightly off centre causing this slight bend. Since the generative design had supports for the plates and the load was evenly distributed across several members, it showed no such deflections. The generative design model has two thin members on the periphery at one side of the model. These are flexible enough to be bent by hand. The same was done when the specimen was under load. They were still found to be completely flexible just as in the unloaded condition. The generative design also showed a small but growing crack which is not a tensile failure but a case of layer separation upon closer inspection. One of the load bearing members suffered a small vertical crack (in the direction of the force) which may grow with the application of a greater force.
-
Compressive Specimens
Both the generative as well as conventional compression specimens were loaded in a ramped fashion by placing the water bucket on their top plate and then adding water continuously. The generative compression specimen sustained 50kg i.e. 490.5 N with no issues. The generatively designed compression specimen successfully sustained the load without any measurable deformation or change in shape. Both the top plates and all the load bearing structures showed no cracks, layer splits or deformations. This specimen was completely unaltered from before. No defects were observed.
Fig. 11. Compressive Models Conventional, Tensile
-
Bending Specimens
The conventional bending specimen failed due to layer delamination at a load of 26.24 kg or 257.4 N. The infill angle of these parts was 45 degrees. This may have caused the part to delaminate. The component failed near the end of the triangulation where the rectangular cross section of the beam started. The holding plate of the bending specimen was intact and remained screwed onto the testing frame as before. The extending portion of the beam after the triangulation completely separated and fell down along with the load.
Fig. 12. Bending Models Conventional, Tensile
The generative bending specimen failed due to breakage of its holding plate through the middle at a load of 43.16 kg
i.e. 423.4 N. The generatively designed specimen failed in an entirely different manner. The weight bearing part of the specimen actually remained intact with no deformation or cracks or delamination. However, the plate which was holding the screws and resting on the testing frame split through the middle and came away from the testing frame completely. The rest of the model was intact. The screws which were used to secure the model stayed embedded in the testing frame while the model broke and fell away from it.
-
-
DISCUSSION OF RESULTS AND CONCLUSION
-
Tension Specimens
The specimens designed for tension were quite easily strong enough for the intended load. Both the specimens did not yield or break at a load which was 5 times the intended load which highlights the validity of the design. The bending of the square plate of the conventional design was due to a slight imbalance in the weight distribution of the applied load which caused a moment in the plate. The load bearing column in the conventional design is a straightforward design which gave more than satisfactory performance and does not necessarily warrant change. The generative design specimen was better with respect to load distribution as it did not allow the top or bottom plates to deform or warp due to the peripheral placement of the load bearing members. However, the small crack that was observed may propagate further if the same load is applied for a longer duration or a larger magnitude of the load is applied. Further failure of the component is hard to predict and hence the component cannot be used any further for its intended application. The inherent tensile strength of ABS is high enough for it to not be a factor and instead, layer adhesion and delamination are more important considerations when 3D printed designs are studied. The generative design had two flexible thin members which were found to be non-load bearing. These structures
were completely redundant and a waste of material. The conventional design does not warrant any changes as such. However, the generative design shows much better stress distribution and may give better performance if failure factors specifically related to FDM 3D printing are properly accounted for.
-
Compression Speciens
The specimens designed for compression were strong enough for the intended load. Both the specimens did not yield and break at a load which was 5 times the intended load which highlights the validity of the design. Failure of such a component due to crushing is highly unlikely and will need a substantially higher load to fail the component by crushing. The load bearing column of a conventional specimen had a small enough length to cross sectional area ratio to avoid buckling. The square plate on which the load was placed was a thin feature and it was resting only on the central column in the conventional design. Hence it was prone to failure due to it bending. The failure observed in the square plate was again due to delamination of a layer. The failure site was almost completely flat indicating that an entire layer had come off as is the case in delamination. The generatively designed model did not experience this problem as its square plate was supported from underneath by peripheral load bearing members again just like the tensile specimen. The generative specimen can be viewed as a better design in case of compression since it did not show any defect whatsoever and prevented the bending of the loading plate. The inherent compressive strength of ABS is high enough for it to not be a factor and instead, layer adhesion and delamination are more important considerations when 3D printed designs are studied.
-
Bending Specimens
Both the bending specimens showed completely different failures which was an unexpected result. The conventional bending specimen could withstand the intended load successfully and only failed when loaded well beyond the 20kg mark. The individual top and bottom fibres of the bending specimen did elongate and compress respectively as expected. However, the part failure was extremely clean with the fracture being straight and almost in a single plane. The failure occurred just where the reinforcement triangulation ended, and the smallest cross section was about to start. This proves that the triangulation was essential in allowing the specimen to sustain the applied loads and would have failed much earlier if not for the triangulation. The failure of the part again points to layer adhesion being the primary cause. The generatively designed part sustained more than 4 times the intended load of 10 kg and more than twice the ultimate Factor of Safety load of 20kg. This design was inherently better as there were no cracks, defects and it showed a much better and even stress distribution. The failure of this part was due to a large crack which went right through the holding plate in which the screws were inserted to fix the specimen to the test frame. The actual load bearing elements of the specimen did not fail and would have sustained even greater loads if the holding plate would not have failed so violently.
A thicker holding plate would have allowed the component to sustain higher loads. This design also showed certain redundant features and protrusions in the model which did not play any useful part in carrying the load and ended up increasing the manufacturing complexity of the part.
All the designs, both conventional and generative were capable enough to sustain the designed load with its factor of safety which was 196.2 N. There was no difference in the load carrying capacity for tensile specimens whereas the generative models were better than their conventional counterparts in the case of compression and bending. The ABS filament fibres are inherently very strong and can sustain the intended loads without any major issues. The major problem in 3D printing is layer delamination which needs to be taken care of by printing the parts in the correct orientation and applying the loads along the layer direction. If the load is applied perpendicular to the layer direction, the layers will peel off much before the fibres actually fail. Generatively designed parts can be used as a viable alternative to conventional design practices as they can deliver similar or better performance while using the same amount of material.
However, generative design algorithms may create redundant features in the design which play no functional role. The development of these algorithms should attempt to make sure that these redundancies are removed before a converged solution is generated to further optimise material usage.
To conclude, additively manufactured generative designs are viable options which may be used to design components in the future as they have the potential to deliver superior performance while needing lesser inputs from designers thereby saving time while also making sure material usage is much more optimal than in the case of conventional shapes and hence should be utilised in practical applications more often in the future.
-
-
FUTURE SCOPE
The tension and compression specimens have withstood a load of 490.5 N successfully. This is a much higher load than what they were designed for. A more robust test setup with a higher loading capacity will have to be designed and used to test these parts until they fail. To definitively compare generative design with conventional design, a number of these samples should be printed using varied process parameters and should then be tested. A sample size of 1 pair of specimens per design is too low to conclusively compare the two processes. Carry out Finite Element Analysis of these parts using a computer to understand whether the practical results are in line with the theoretical and simulated results. Understand the major design flaws in the generative designs by investigating the smaller cross sections and finding out which geometries show excessively high stress values. Understand the underlying working of this AI algorithm during the design iterations. Design a suitable generative design component in a real- world application and test its performance under real world conditions. Design generatively designed specimens which can be tested using an ASTM or ISO standard and can be
held in a conventional Universal Testing Machine. Repeat the experiments using a different material such as PLA for the parts. Repeat the experiments using a different 3D printing process other than FDM.
-
REFERENCES
(PLA) materials with different printing orientations, Composites Part
B: Engineering, vol. 163, pp. 393-402 2019.
[2] Tianyun Yao, Juan Ye, Zichen Deng, Kai Zhang, Yongbin Ma, Huajiang Ouyang, Tensile failure strength and separation angle of FDM 3D printing PLA material: Experimental and theoretical analyses,Composites Part B: Engineering, vol. 188
[3] Hossain, Mohammad Shojib, et al. Improved Mechanical Properties of Fused Deposition Modeling-Manufactured Parts Through Build Parameter Modifications, Journal of Manufacturing Science and Engineering, 2014 [4] Rankouhi, Behzad & Javadpour, Sina & Delfanian, Fereidoon & Letcher, Todd, Failure Analysis and Mechanical Characterization of3D Printed ABS With Respect to Layer Thickness and Orientation
Journal of Failure Analysis and Prevention
[5] Bishwonath Adhikari Strength and Failure Mechanisms in 3D printed parts Aalto University School of Engineering [6] TY – JOUR; AU – Allum, James; AU – Gleadall, Andy; AU – Silberschmidt, Vadim; PY – 2019/12/01; T1 – Fracture of 3D-printed polymers: Crucial role of filament-scale geometric features; DO – 10.1016/j.engfracmech.2019.106818; JO – Engineering Fracture Mechanics [7] Tyflopoulos, Evangelos; Tollnes, Flem David; Steinert, Martin; Olsen, Anna State of the art of generative design and topology optimization and potential research needs DS 91: Proceedings of NordDesign 2018, Linköping, Sweden, 14th – 17th August 2018 ISBN: 978-91-7685-185- 2 [8] J. Hu, M. Li, S. Gao, Texture-guided generative structural designs under local control, Computr-Aided Design 108 (2019) 1 11. doi:https://doi.org/10.1016/j.cad.2018.10.002. [9] R. Cang, H. Yao, Y. Ren, One-shot generation of near-optimal topology through theory-driven machine learning, Computer-Aided Design 109 (2019) 12 21. doi: https://doi.org/10.1016/j.cad.2018.12.008. [10] Christoph Bader, Neri Oxman Recursive symmetries for geometrically complex and materially heterogeneous additive manufacturing, Computer-Aided Design; Volume 81,2016,Pages 39-47, ISSN 0010- 4485,https://doi.org/10.1016/j.cad.2016.09.002. (http://www.sciencedirect.com/science/article/pii/S0010448516301087