
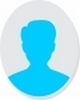
- Open Access
- Authors : Timothy Adewale Adeyi , Omogbolade Lukmon Adepitan , Sakiru Kayode Ekun
- Paper ID : IJERTV11IS080082
- Volume & Issue : Volume 11, Issue 08 (August 2022)
- Published (First Online): 24-08-2022
- ISSN (Online) : 2278-0181
- Publisher Name : IJERT
- License:
This work is licensed under a Creative Commons Attribution 4.0 International License
Characterization of Briquttes from Differents Wood in Nigeria
Timothy Adewale, Adeyi
Institution: Lead City University Ibadan, Oyo State, Nigeria
Department: Department of Mechanical Engineering
Omogbolade Lukmon, Adepitan Institution: Lead City University Ibadan, Oyo State, Nigeria
Department: Department of Mechanical Engineering
Sakiru Kayode, Ekun
Institution: Lead City University Ibadan, Oyo State, Nigeria
Department: Department of Mechanical Engineering
Abstract:- Briquettes production in Nigeria is receiving so much attention lately and most industries are interested in the production as well as maximizing profits. The choice of source of wood from forests has been difficult for researchers to achieving the suitable material for briquettes production from wood.
Six different woods were selected; Afara, Obobo, Ayo, Araba, Obeche and Eku from sawmill industries which are common and easily accessible to many in the country. These woods were briquetted and characterized for their suitability and optimal production of calorific values, combustion, Sulphur and Nitrogenous contents among other characteristics for suitability of optimal briquettes production.
Results shows that, Eku would be better during the rainy season and when transportation of the same has to be by water due to its high resistance to water. Although, Ayo possess the highest calorific value among the six common species of wood examined but has low resistance to water.
Therefore, the characterization of these woods shows that, Ayo would make a better fuel among these woods in which other woods could also be used in some areas depending on the specification of the producers.
Keys words: Briquettes, wood species, characterization, fuel, calorific value
CHARACTERIZATION OF BRIQUETTES FROM DIFFERENT WOOD SPECIES IN NIGERIA. INTRODUCTION
Latest studies have shown that the excessive consumption of carbonated and non-renewable energy (fossil fuels etc.) have added substantially to the global challenges in environmental control, (Cheol et al., 2021; Mcnamee, 2016). For instance, in the United States, the Environmental Protection Agency (EPA) reported in 2022, that the consumption of fossil fuels and related product have added up to 65% of the raising of global greenhouse gas emission (Ibitoye, et al., 2022). Fossil fuels such as natural gas and other sources have been the main source of global energy demands as it has contributed about 80% of the energy drive needed in the world today, (Kpalo et al. 2020). According to Energy Information Administration, the fastest growing source of energy is the renewable forms of energy with a consumption percentage of 3% annually, (EIA, 2009). This can be attributed to the high level of its environmental friendliness with its usage and the reduction of the world global warming. Biomass is one of the most common and easily accessible renewable energy resources. Globally, biomass currently provides energy in the form of combustible biomass and wastes, liquid biofuels, solid biomass/charcoal, and gaseous fuels. This share is estimated to be over 10% of global primary energy, but with over two-thirds consumed in developing countries as traditional biomass for household use (IEA, 2009). Industrialization of many rural areas in the world, most especially in a country like Nigeria, has contributed to greenhouse concentration in the atmosphere. These greenhouse gases have been found to be closely related to one another, (Udehl & Kidak 2019).
Briquetting is a form binding granular and loose materials from wood products to form solid block of combustible materials as energy source and also to for easy movement from one place to another, (Adegoke, et.al. 2010). According to Anon, (Anon, 2012), Briquettes are form of energy (fire) starting or sustaining matter used in homes due to their flammability. Wood residues from forest trees and wood-based companies are suitable biomasses for briquetting such as branches and stumps, sawdust from sawmills which pollute air, land and water, (Anon, 2012). Briquette as a bio-fuel is advantageous in usage when compared to other forms of energy production. Some of the advantages includes handy for ease of transportation, clean fuel for eco friendliness, high calorific value etc, (Adegoke et. al.2009). The energy production in fuel also known as calorific value is an integral part of fuel, (Satyanarayana, 2010). The energy value is defined as the amount of heat that can be obtained from a complete combustion from a unit mass briquette, (Onchieku, et al., 2012).
In Nigeria, a country that depends solely on petroleum products as its major sources of domestic energy has led to the high spike in the prices of these products and its non-availability, (Onuegbu, 2010). In Nigeria, most habitants of the rural settlement, depend majorly on fuel wood such as charcoal, fire-wood, sawdust etc. as their sources of energy for the past
decades. In 2009, the Ministry of Energy in Nigeria, Nigeria consumes over 4,687 kg of wood fuel and the number is likely to increase in the coming year as the demand is on the uprising, (Philip, 2010). Nowadays, some Nigerian industries and research institutes especially the Forestry Research Institute of Nigeria (FRIN) are having keen interest in the production of wood briquettes from sawdust as an alternative source of energy to the fossil fuel. Investigation made in the FRIN in Ibadan. Nigeria disclosed that sawdust generated from wood processing in the institute is usually converted into ceiling boards and particle boards. It is therefore expected that if the sawdust can be converted to briquette it would be more useful as source of fuel for domestic cooking and for necessary consumption of energy purposes. In Nigeria, sawdust as a source of briquetting is readily available with the following advantages; (i) affordable as the price is equivalent as wood fuel, (ii) they burn very well in any kind of solid fuel stove and boiler. (iii) they ignite quickly and burn cleanly, producing only 1% to 6% ash. (iv) the briquette doesnt contain sulphur and burn without odour. (v) the burning of 1 Kg of sawdust briquettes produces 18000kg caloric power, roughly equivalents to that of medium quality coal.
MATERIALS AND METHODS
There many sources of briquettes in Nigeria, however, this study only considered six (6) types of wood sources due to their availability in Nigeria forestry, these are: Sawdust from Obeche (Triplochiton scleroxylon), Araba (ceiba Pentandra), Eku ( Brachystegia spp), Ayo (Holoptelia grandis), Obobo ( Ficus mucuso), Afara (Terminelia superba), These were collected from wood industries and saw mills around the southwest region of the country (Ondo state). The materials from these sources were allowed to dry at a moderate temperature that is, room temperature of about 200C for a period of two weeks (15 days) to ensure proper dryness has taken place. The homogeneity of these samples was ensured within the particles of each of the samples by passing them through 600m sieve.
BRIQUETTE PRODUCTION
In the production of the briquettes, cassava was used as a binder. 100g of sawdust from each sample of the six different woods and 30g of moistened starch were mixed thoroughly until a uniform mixture was obtained of the six different wood samples. In each case, the mixed substrate was fed into a mould for proper compression to form the briquettes by means of the locally fabricated compacting ram (fig 1). Six replicates were produced for each sample. The prepared briquettes were air dried for seven (7) days and then sun dried for about forteen (14) days but because of the inclement of the weather, the briquettes were eventually dried using locally fabricated drying unit which consist of a cuboid framed wood with four (4) 100W bulbs as the drying element (fig 2) for a period of one week. The 36 briquettes produced were tested for their fuel related properties.
Fig 1: Compacting Ram
Fig 2: Drying Unit
Fig 3a: Plan view of briquette species Fig 3b: Side view of briquette species
Figure 3: Briquettes made from the six wood species
CHEMICAL ANALYSIS
The chemical analyses were carried out at the Institute of Agriculture Research and Training (IAR & T), Ibadan, Nigeria. The standard procedure described in official methods of analysis were used for the determination of carbon, hydrogen, nitrogen, oxygen and sulphur content ( Ultimate analysis) and the determination of moisture, ash, crude fibre, crude protein, crude fat and dry matter (Proximate analysis). The Gallenkamp ballistic bomb calorimeter was used in determining the gross heat value of each briquette.
DETERMINATION OF DRY MATTER AND MOISTURE CONTENT
In determining the dry matter and moisture content, 1g of the sample was weighed into a previously weighed crucible. The weight of the crucible along with the sample was before being transferred into the oven set at a temperature ranging between 100C 105C to dry to a constant weight for 5 hours. The crucible and the sample were allowed to cool in a desiccator. The new weight of the crucible plus sample was then taken.
W0 = The weight of empty crucible
W1 = The weight of crucible and sample
W3 = The weight of crucible and dried sample
DETERMINATION OF CARBON AND HYDROGEN CONTENTS
Carbon and hydrogen contents were determined simultaneously by Leibig-Pregle method. 1 g of sample flour was placed in a quartz test tube and burned off through the absorbents magnesium percolate to absorb water and sodium hydroxide to absorb carbon dioxide. The amount of water and carbon dioxide is found from the difference between the two weightings, one before and the other after the absorption of water and carbon dioxide. The percentage of carbon and hydrogen was evaluated thus:
The Constants, 0.2729 and 0.1119 are from empirical equations derived in Leibig-pregle method.
DETERMINATION OF NITROGEN CONTENT
This was determined by Dumas-Pregle method. 0.2g of the sample flour was mixed with powder of Copper Oxide in the ignition tube. Air was displaced from the tube by passing through a stream of C02 until minute bubble appeared in the nitrogen flow meter filled with about 50% solution of potassium hydrogen. The weighed sample was burned off at between 700°C and 750°C in a gas burner and later burned in an atmosphere of C02 with the gas cylinder shut off. After ignition, the combustion product was displaced with carbon dioxide into the nitrogen now meter at a rate of one bubble per second until minute bubble appear in the nitrogen flow meter. The percentage nitrogen content was determined by the equation:
Where: V = Volume of nitrogen in the nitrogen flow meter g = Weight of sample
1.097 = Mass of 1ml of nitrogen at the test condition
DETERMINATION OF SULPHUR CONTENT
1 g of sample flour was wrapped in a filter paper free from ash and it was secured in the platinum wire sealed into a glass rod held fast to the stopper of a flask filled with oxygen. The weighed sample was ignited in filter and inserted in the flask immediately, and the flask was plugged with the stopper. The product was absorbed with a mixture of water and hydrogen peroxide to oxidize the combustion product immediately. The combustion product was titrated with a solution of barium percolate in the presence of the indicator Toron with a pH value of 4.5. The percentage of sulphur was found by the equation:
Where:
T = Titre of Ba (C04)2 solution
V = Volume of Ba (C04)2 solution g = weight of the sample
The titre of the barium chlorate solution is found with 0.01 sulphuric acid. The sulphuric acid was titrated with barium percolate in the presence of the indicator Toron until yellow colour changes to pink. The titre is found by the equation:
Where:
V1 = Volume of H2SO4 used V2 = Volume of Ba(C04)2 M = mole of H2SO4
16 = Atomic mass of sulphur
DETERMINATION OF ASH
Apparatus: Porcelain Crucibles, a Desiccator, Analytical Balances and a Furnace.
Determination: 2g of the sample were weighed into a porcelain, crucible. This was transferred into the muffle furnace set at 550C and left for about 4 hours. About this time it had turned to white ash. The crucible and its content were cooled to about
100C in air, then room temperature in a desiccator and weighed. This was done in duplicate. The percentage ash was calculated from the formula below:
3.3.6 OXYGEN CONTENT
The percentage oxygen content was determined as follows:
Where:
C = % Carbon content
H = % Hydrogen content N = % Nitrogen content S = % Sulphur content Ash = % Ash content
DETERMINATION OF CRUDE PROTEIN
0.2g of sample flour was shaken with 100ml of 0.05M of Sodium Hydroxide solution for 15 minutes. It was then centrifuged at 600rpm for 10 minutes in a 500ml graduated cylinder. 5ml clear extract was added and diluted to 50ml with 30% Sulphur Salicylic acid solution. It was inverted several times and immediately the degree of turbidity at 450nm in a 4cm cell read against the sulphur salicylic acid solution as instrument blank. The percentage protein content was determined using the equation:
Where Y = Calorimeter reading X = % Protein
FIBRE DETERMINATION
Apparatus: Heating mantle, crucibles, furnace, sieve cloth, fibre flask, funnel analytical weighing balance, a dessicator.
Reagents: 0.255N H2SO4, 0.313N NaOH and Acetone.
Determination: 2g of the sample was accurately weighed into the fibre flask and 100ml of 0.255N H2S04 added. The mixture was heated under reflux for 1 hour with the heating mantle. The hot mixture was filtered through a fibre sieve cloth. The filterate obtained was thrown off and the residue was returned to the fibre flask to which 100ml of (0.313N NaOH) was added and heated under reflux for another 1 hour. The mixture was filtered through a fibre sieve cloth and 10ml of acetone added to dissolve any organic constituent. The residue was washed with about 50ml hot water on the sieve cloth before it was finally transferred into the crucible. The crucible and the residue were oven-dried at 105°C overnight to drive off moisture. The oven- dried crucible containing the residue was cooled in a dessicator and later weighed to obtain the weight W1. The crucible with weight W1 was transferred to the muffle furnace for Ashing at 550°C for 4 hours.
The crucible containing white or grey ash (free of carbonaceous material) was cooled in the dessicator and weighed to obtain W2. The difference W1 – W2 gives the weight of fibre. The percentage fibre was obtained by the formula:
DETERMINATION OF CRUDE FAT
Apparatus: Soxhlet apparatus and accessories, oven, desicator and analytical balance.
Reagents: Petroleum spirit or Ether (40°C – 60°C b.pt).
Determination: 1g of each dried sample was weighed into fat free extraction thimble and pug lightly with cotton wool. The thimble was placed in the extractor and fitted up with reflux condenser and a 250ml soxhlet flask, which has been previously dried in the oven, cooled in the desicator and weighed. The soxhlet flask is then filled to 3/4 of its volume with petroleum ether (b.pt. 40°C – 600C), and the soxhlet flask. Extractor plus condenser set was placed on the heater. The heater was put on for six hours with constant running water from the tap for condensation of ether vapour. The set is constantly watched for ether leaks and the heat source adjusted appropriately for the ether to bril gently. The Ether is left to siphon over several times say over at least 10- 12 times until it is short of siphoning. It s after this is noticed that any ether content of the extractor is carefully drained into the ether stock bottle. The thimble containing sample is then removed and dried on a clock glass on the bench top. The extractor, flask and condenser is replaced and the distillation continues until the flask is practically dry the flask which now contains the fat or oil is detached, its exterior cleaned and dried to a constant weight in the oven. If the initial weight of dry soxhlet flask is Wo and the final weight of oven dried flask + oil/fat is WI, percentage fat/oil is obtained by the formula:
ENERGY DETERMINATION
Apparatus: Gallenkamp Ballistic Bomb Calorimeter
Reagents: Benzoic Acid.
Determination: 0.25g of each sample depending on bulkiness was weighed into the steel capsule. A 10cm cotton thread was attached to the thermocouple to touch the capsule. The Bomb was closed and charged in with oxygen up to 30 atm. The Bomb was fixed up by depression the ignite switch to bum the sample in an excess of oxygen. The maximum temperature rise in the bomb was measured with the thermocouple and galvanometer system. The rise in temperature was compared with that obtained for 0.25g of Benzoic value of each sample was determined by the following stepwise calculations:
Calculations:
Mass of Benzoic Acid =W1 gm
Calorific value of 1g Benzoic Acid = 6.32 Kcal/g Heat released from Benzoic Acid = 6.32 x W1 Kcal Galvanometer deflection without sample = T1 Galvanometer deflection of Benzoic Acid = T2 T1
The standardizing is repeated five times and average value calculated for y. Mass of sample = 0.5g
Galvanometer deflection with sample = T3 Galvanometer deflection of sample = T3 – Tl Heat released from sample = (T3 – T1) Y. KCal Calorific value of sample = {T3- T1) Y.Kcal
ENERGY EVALUATION
The approximate energy value (higher heating value) was evaluated using Dulong-Petit formular (Perry and Green, 1997)
Where C = % of Carbon
H = % of Hydrogen O = % of Oxygen
S = % of Sulphur
The lower or net heating value (LHV) is determined by the equation below Where Mw = Product of the fraction of hydrogen in the briquette sample and 9kg.
WATER RESISTANCE TEST
This was carried out by immersing each briquette specie in a bowl of water. This test was carried out to ascertain the following;
(a) the effect of soaking on the volume of each briquette and (b) how long they can remain in water without disintegrating. The result from (b) was used in analyzing the property of the briquette. This is because the briquettes did not show any appreciable increase in volume while in the water and also due to the fragility of some of the briquettes, it was not advisable to pick them out of the water for measuring. Therefore, the briquettes were left in water for one week and a daily record of their response to water absorption was taken
Apparatus: universal testing machine
COMPRESSIVE STRENGTH TEST
Briquettes from six wood species namely Eku, Araba, Afara, Obobo, Ayo and Obeche are tested for their compressive strength. The briquettes were tested to destruction with a manual universal testing machine.
RESULT AND DISCUSSION DRY MATTER RESULT
From the evaluation and results in Table 1, it can be seen clearly that the six (6) woods dry mass matter, it was revealed that Ayo has the highest dry matter content of 98.67% and Obeche has the lowest dry matter content of 92.66%. The dry matter
content of the other four wood briquette samples that is Eku, Afara, Araba and Obobo are 95.76%, 93.96%, 93.81%, 96.88% respectively. This indicates that all the briquette samples would burn easily.
MOISTURE CONTENT
Analysis showed that Obeche has the highest moisture content of 7.34% and Ayo has the lowest moisture content of 1.33%. The moisture contents of the other briquette samples that is, Eku, Afara, Araba, Obobo are 4.245, 6.04%, 6.19%, 3.12% respectively. These can be seen in Table 1. Briquettes with moisture content ranging below 20% wet basis are recommended for good storability and combustibility. Therefore, this also affirm that the six samples of briquette will ignite well, because there will be less evaporation during combustion at the expense of calorific value of the fuel.
RESULT FROM ASH CONTENT
The ash contents of the briquette samples varied from 1.08% for Obobo to 2.27% for Eku. The ash contents of other selected samples are 1.54%, 1.78%, 1.88%, 1.97% for Obeche, Afara, Ayo, Araba, respectively. The result shows that all the samples have values lower than 3%. This means that they all have low ash contents especially Obobo. The results of Ash content in Table 2 shows the amount of inorganic substances that would remain after burning.
Table 1: proximate composition of the six briquette samples
Sample |
%CProtein |
%Cfat |
%Cfibre |
%Ash |
%DM |
%Moisture |
EKU |
07.68 |
05.67 |
39.67 |
02.27 |
95.76 |
04.24 |
ARABA |
03.76 |
02.58 |
41.04 |
01.97 |
93.81 |
06.19 |
OBECHE |
02.97 |
01.24 |
41.29 |
01.54 |
92.66 |
07.34 |
AFARA |
04.28 |
02.72 |
40.06 |
01.78 |
93.96 |
06.04 |
AYO |
03.16 |
01.87 |
43.67 |
01.88 |
98.67 |
01.33 |
OBOBO |
06.14 |
03.26 |
39.26 |
01.08 |
96.88 |
03.12 |
RESULTS OF CARBON AND HYDROGEN CONTENTS
The molar ratio of hydrogen to carbon (H/C) for the briquette samples are 1.684, 1.484, 1.530, 1.473, 1.567 and 1.677 for Eku, Araba, Obeche, Afara, Ayo and Obobo respectively. These values depicted in figure 4 are lower than those obtained for methane (4.0) and iso-octane (2.25) which are good examples of hydrocarbon fuels.
Figure 1: The molar ratio of Hydrogen to Carbon for the six briquette samples
RESULTS OF NITROGEN CONTENTS
From the analysis in Table 3, the nitrogen content of the briquette samples are 0.48%, 0.51%, 0.60%, 0.68%, 0.98% and 1.23% for Obeche, Ayo, Araba, Afara, Obobo and Eku respectively, which are less than 2% in the briquette samples. The results are comparable to coal 1.2% in table 4. Fuel bound nitrogen is an important contributor to oxides of nitrogen (NOx) emission from biomass contribution system.
SULPHUR CONTENTS
The sulphur contents of the six briquette samples varied between 0.00% for Obeche and 0.21% for Obobo in Table 2. Other results include 0.06%, 0.08% 0.13% and 0.18 respectively for Ayo, Araba, Afara, Eku. The sulphur content was observed to fall below 1% in all the samples, which would mitigate the emission of sulphur dioxide (SO2) into the atmosphere causing acid rain. They can all be compared to that of coal, fuel oil and natural gas (methane) that produces no sulphur.
Table 2: Ultimate composition of the six briquette samples
Sample |
%Carbon |
%Hydrogen |
%oxygen |
%Nitrogen |
%Sulphur |
EKU |
51.64 |
07.24 |
44.28 |
01.23 |
00.18 |
ARABA |
47.67 |
05.89 |
41.45 |
00.60 |
00.08 |
OBECHE |
47.38 |
06.04 |
40.76 |
00.48 |
00.00 |
AFARA |
48.64 |
05.97 /td> |
40.54 |
00.68 |
00.13 |
AYO |
49.55 |
06.47 |
41.56 |
00.51 |
00.06 |
OBOBO |
48.96 |
06.84 |
42.86 |
00.98 |
00.21 |
RESULTS FROM CALORIFIC VALUE
The calorific value of the briquette samples varies from 18,745 KJ/Kg for Obeche to 34,857 KJ/Kg for Ayo. The calorific value of other selected briquette samples are 23,676 KJ/Kg, 25,651 KJ/Kg, 31,570 KJ/Kg, 32,228 KJ/Kg for Araba, Afara, Obobo and Eku respectively. From Table 3, it shows that Ayo has the highest calorific value due to the fact that it has the least moisture content and the highest dry matter content, indicating that a higher percentage of the sample would be available for combustion.
RESULT FROM ENERGY EVALUATION
Table 4 revealed that the higher heating values of the briquette samples are 19,855 kJ/kg, 17,085 kJ/kg, 17,317 kJ/kg, 17,693 kJ/kg, 18,525 kJ/kg and 18,637 kJ/kg for Eku, Araba, Obeche, Afara, Ayo and Obobo respectively. The highest heating value of 19,855 KJ/Kg obtained for Eku is 66% that of coal, 46% that for fuel oil and 36% that for natural gas i.e. methane.
Table 3: Heat of combustion of the six briquette samples
Sample |
Galvanometer Deflection |
Calibration constant |
Wt of Sample |
Gross calorific Value in kcal/g |
Gross calorific Value in kJ/kg |
EKU |
04.90 |
0.7856 |
00.50 |
7.699 |
32228 |
ARABA |
03.60 |
0.7856 |
00.50 |
5.656 |
23676 |
OBECHE |
02.85 |
0.7856 |
00.50 |
4.478 |
18745 |
AFARA |
03.90 |
0.7856 |
00.50 |
6.128 |
25651 |
AYO |
05.30 |
0.7856 |
00.50 |
8.327 |
34857 |
OBOBO |
04.80 |
0.7856 |
00.50 |
7.542 |
31570 |
RESULT FROM WATER RESISTANCE TEST
Despite the toughness of the briquette made from Ayo, it was the least resistant to water. It disintegrated in water after twelve hours. The briquette made form Eku shows the highest resistance to water. It started showing signs of disintegration after seven days of soaking it in water, Obobo disintegrated after one day, Afara disintegrated after three days while Araba and Obeche disintegrated after five days. This is illustrated in the bar chart Figure 3
Fig 4: Water resistance property
RESULT OF COMPRESSIVE STRENGTH
In the compressive strength test carried out on the briquette samples, the result in Table 5 were deducted, it shows that the compressive strength of the briquettes varied from 980 kN/m2 for Ayo to 2450kN/m2 for Araba while for the other briquettes it is 1470 kN/m2,1470 kN/m2,1470 kN/m2,1960 kN/m2 for Eku, Obeche, Obobo and Afara.
PHYSICAL CHARACTERISTIC OF THE BRIQUETTES
-
WEIGHT
The weight of the briquettes produced varied from 105.20g for Afara to 120.20g for Ayo, others are 107.0g, 112.10g, 112.90g
& 113.50g for Obeche, Obobo, Araba and Eku respectively. The results Table 4 show that Ayo is the heaviest among all the species.
-
DIMENSION
Table 4 shows the dimensions (length × breadth × height) of the samples measured in mm. They are as follows: 120 × 98 × 38, 117×96×28, 119×97×31, 115×95×22, 117×96×20 and 117×96×26 for Araba, Obobo, Obeche, Ayo, Eku and Afara respectively. The average length of the briquette samples is 117.5mm
-
COLOUR
The Table 4 below shows the colour difference in the briquette samples in which both Obeche and Ayo are creamy brown in colour, while Araba and obobo are yellowish brown, also Eku has a orange brown (maroon) in colour and lastly, Afara which has a cream colour.
CONCLUSION
Briquette samples |
Weight (g) |
Dimension (mm) |
Colour |
Compressive strength (kN/m2) |
AFARA |
105.20 |
117×96×26 |
Cream |
1960 |
OBECHE |
107.00 |
119×97×31 |
Creamy brown |
1470 |
OBOBO |
112.10 |
117×96×28 |
Yellowish brown |
1470 |
ARABA |
112.90 |
120 × 98 × 38 |
Yellowish brown |
2450 |
EKU |
113.50 |
117×96×20 |
Orange brown |
1470 |
AYO |
120.20 |
115×95×22 |
Creamy brown |
980 |
The
Table 4: Physical characteristics and compressive strength of the samples
briquettes produced from the six wood species using cassava starch as binder, has fuel characteristics which makes them a considerably good fuel. Taking the whole range of species tested; the following was deduced:
Sulphur content of the samples is less than 1% and this is good for combustion since good fuels are known to have low sulphur contents.
The low composition of nitrogen in the samples selected will result in low emissions of oxides of nitrogen into the atmosphere and there may not be need for equipment for the removal of oxides of nitrogen in the designed equipment for the combustion of the briquette samples.
Considering the high resistance of the briquette made from Eku to water, it is advisable to go for briquette made from Eku during the rainy season and when transportation of the same has to be by water. Even though Ayo has the highest calorific value among the six briquette samples, but due to its very low resistance to water compared to Eku which has the second highest calorific and highest resistance to water, Eku could therefore be rated as the best in this light among the six selected wood samples.
REFERENCES
[1] Adegoke, I.A, Badejo, S.O., Baiyewu, R.A., Aina, K.S. And Ige, P.O. (2009): Combustion Properties of Charcoal Briquette Produced from Residues of Selected Wood Species. Proceedings of the 33rd Forestry Association Nigeria Conference. [2] Adegoke, I.A., Baiyewu, R.A., Aina K. S, Adesope A.S., Adejoba A.L.and Abah G. B. (2010): Combustion Properties of Briquette Produced from Mixed Sawdust of Tropical Wood Species. Proceedings of the 2nd National Conference of the Forest and Forest Products [3] Cheol, K., Kim, J., Yong, S., Jun, S., Hoon, L., Geon, C., Hyun, D. (2021). Development and validation of torrefaction optimization model applied element content prediction of biomass. Energy, 214, 111. https://doi.org/https://doi.org/10.1016/j.energy.2020.119027 [4] EIA (2009). Annual energy outlook 2009 with projections to 2030, Energy Information Administration, Washington, DC 20585. Web site: www.eia.doe.gov/oiaf/aeo. [5] Ibitoye, S.E., Mahamood, R.M., Jen, T-C., and Akinlabi, E.T. (2022) Combustion, Physical, and Mechanical Characterization of Composites Fuel Briquettes from Carbonized Banana Stalk and Corncob. Int. J. Renew. En. Dev., 11(2), 435-447 https://doi.org/10.14710/ijred.2022.41290 [6] J. M. Onchieku, B. N. Chikamai, and M. S. Rao, 2012 Optimum parameters for the formulation of charcoal briquettes using bagasse and clay as binder, European Journal of Sustainable Development,vol.1,no.3,pp.477492, [7] Kpalo, S.Y., Zainuddin, M.F., Abd Manaf, L. and Roslan, A.M. 2020. Production and characterization of hybrid briquettes fom corncobs and oil palm trunk bark under a low-pressure densification technique. Sustainability, 12: 2468. [8] Mcnamee, P. (2016). Torrefied Biomass for Large-Scale Electricity Generation. Ph.D. Thesis: School of Chemical and Process Engineering, The University of Leeds, 1293. [9] N. Satyanarayana, C. Y. Tao, G. Glaser, Hans-Jorg and P. Ay, 2010. Increasing the Calorific Value of Rye Straw Pellets with Biogenous and Fossil Fuel Additives, Energy Fuels, Vol. 24, pp. 52285234,. [10] Onuegbu, T.U., 2010. Improving Fuel wood Efficiency in Rural Nigeria: A case for Briquette Technology, National Magazine of the CSN., 5(4): 35-39 [11] Onuegbu T.U., Ogbu I.M., Ilochi N.O., Okafor I, Obumselu O.F. and Ekpunobi U.E: Enhancing , (2010). The Efficiency of coal Briquette in Rural Nigeria using pennisetum purpurem. Advances in Natural and Applied Sciences, 4(3): 299-304. [12] Philip, F., 2010. Nigeria looking for Fuel wood Alternative (www.http// deforestationwatch org) retrieved, June 14th 2011. [13] Stout,B.A. and G. Best (2001)Effective energy use and climate change: needs of rural areas in developing countries. Agricultural Engineering International: The CIGR Ejorunal of scientific Research and Development. Vol. III, 19pp. [14] Udehl, B.A. and Kidak, R. 2019. The excessive use of fossil fuel and its impact on climate change in Africa. Curr. J. Appl. Sci. Technol., 32(5): 1-4.