
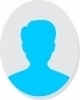
- Open Access
- Authors : Siddhika Pradip Thorve , Sudhakar Umale
- Paper ID : IJERTV11IS090040
- Volume & Issue : Volume 11, Issue 09 (September 2022)
- Published (First Online): 28-09-2022
- ISSN (Online) : 2278-0181
- Publisher Name : IJERT
- License:
This work is licensed under a Creative Commons Attribution 4.0 International License
CFD Analysis of Microchannel Heat Sink with Branching Fins
Siddhika Pradip Thorve1
-
Tech. Scholar Mechanical Engineering Department Sardar Patel College of Engineering, Andheri (West)
Mumbai, Maharashtra, India
Abstract When it comes to cooling electronic chips, which have a high heat flux and small size, a microchannel heat sink (MCHS) has been thought to be the most efficient solution. Future development of high-performance integrated circuits will heavily depend on how well the heat removal rate of MCHS can be increased. One of the most basic and efficient MCHS structures to be used in this investigation is the rectangular channel. MCHS with single branching fins and MCHS with double branching fins with different cases were considered by varying the stem height of the fin from 0.3 to 0.6 mm and were studied with a varying velocity of cooling fluid from 0.25 to 1 m/s at a constant heat flux of 500 kW/m2. Single-phase liquid water flows as cooling fluid in the heat sink to remove heat.
Predicted results, i.e., temperature distribution, heat transfer coefficient, and pressure drop, clearly reveal that heat transfer increases with increasing fin height and also with increasing velocity of cooling fluid. Pressure drop also increases with fin height because flow obstruction rises. It was found that double branching fins have a higher heat transfer rate as compared to single branching fins. Pressure drop also increases in the case of double branching fins than in the case of single branching fins. Therefore, it can be concluded that a heat sink with double branching fins with a stem height of 0.6 mm exhibits maximum heat transfer but at the expense of high-pressure drop.
Keywords Microchannel heat sinks, Heat transfer, Heat transfer coefficient, Branching-fin, Varying fin height.
-
INTRODUCTION
The industry's quick growth has presented new difficulties and opportunities for advancing other fields, such as the quick development of integrated circuits, the rising prominence of advanced energy and power, the continued development of laser technology, etc. From the perspective of heat transfer, these fields frequently use high speed and frequency, high heat flux, and micro/nano-scale technology. The rapid development and reliable functioning of electronic components are already being significantly hampered by thermal management. As a result, this increased the need for better cooling techniques to guarantee the dependable and efficient operation of microelectronic systems.
When it comes to cooling electronic chips, which have a high heat flux and small size, a microchannel heat sink (MCHS) has been thought to be the most efficient solution. Future development of high-performance integrated circuits will heavily depend on how well the heat removal rate of MCHS can be increased. The industry has conducted an extensive study and has used the rectangular channel, one of the most fundamental and practical MCHS structures [1].
To determine how geometric parameters affected rectangular, trapezoidal, and triangular-shaped flow and heat
Sudhakar Umale2
Former Associate Professor Mechanical Engineering Department,
Sardar Patel College of Engineering, Andheri (West)
Mumbai, Maharashtra, India
microchannel heat sinks, Hongtao Wang et al. [1] performed numerical simulations. When the relationship between water viscosity and temperature was considered, there was a good agreement between numerical results and experimental data. Low thermal resistance and high-pressure drop are typical microchannels with a high aspect ratio and small hydraulic diameters. The rectangular microchannel, which has an aspect ratio of 8.904 to 12.442, offers the optimum performance. The rectangle microchannel has the lowest thermal resistance among the three types of microchannels, followed by the trapezoid and triangle microchannels. The heat resistance and pressure drop are also impacted by the channel number. The thermal resistance is decreased by increasing the channel count but at the expense of a high-pressure drop. The channel number has an ideal range for the same power consumption scenario. Fins and other extended surfaces are widely employed to dissipate heat produced by electronic components through forced or natural convection, or both. Fin designs come in a wide variety, both commercially and in academic literature, but there is always an effort to enhance heat dissipation while keeping prices down. Fins of various lengths and widths are frequently used to improve heat transfer. In rectangular parallel microchannel heat sinks with different fin heights, Yogesh K. Prajapati et al. [2] analytically investigated heat transmission and fluid flow behavior. By changing the fin heights from 0.4 to 1.0 mm, seven different cases were considered. For operating parameters where heat flux ranged from 100 to 500 kW/m2, and Reynolds number ranged from 100 to 400, three- dimensional (3D) numerical simulations were performed. In order to dissipate heat, single-phase liquid water was used as a coolant in the heat sink. The predicted resultstemperature distribution, heat transfer coefficient, pressure drop, and velocity profileshowed that heat transfer increases with fin height but decreases for heat sinks with fin heights between 0.4 and 0.6 mm. Because flow obstruction increases with fin height, pressure drop also rises. It has been discovered that maximum heat transfer occurs with fin heights of 0.8 mm, higher than fin heights of 0.9 mm and 1.0 mm (completely closed heat sink). Net convective surface area and typical flow patterns brought on by the presence of open space have been viewed as significant factors affecting the overall thermal performance of the suggested heat sinks.
It is shown that the tree-shaped structure is useful in terms of heat and mass transport, heat sinks, and electronics chip cooling. High-efficient heat conduction in a finite volume can be solved with the help of the tree-shaped fin design. Among the various fin shapes, tree-like or branching fins have better heat dissipation properties than conventional fins [1424].
transfer properties.
Fig. 1 Schematic diagram of Microchannel Heat sink [2]
This literature review reveals that with the continuous development of electronic devices towards high-speed performance and miniaturization, maintaining the device's temperature below the critical limit by dissipating the generated heat has become crucial for researchers. Also, new cooling techniques like jet cooling and cooling by nanofluids have various disadvantages such as application difficulties and costs. Conventional techniques like extended surfaces (fins) and heat sink still preserve their importance due to their low cost, reliability, and simplicity, but conventional heat sink designs have less heat transfer rates; therefore, in this present work, MCHS with branching fins are examined.
-
METHODOLOGY
-
-
Introduction.
The proper methodology is required to achieve the desired objectives. The methodology adopted here consisted of the following steps:
-
Selecting Computation Domain and Developing its Solid Model:
Selecting the computational domain is the initial step. A geometrical model is created by removing unnecessary elements from the computational domain, which is the area across which a phenomena is to be represented. Then, a mesh is created by discretizing the computational domain into tiny pieces.
D. Validation of results:
In this step, simulation results for a Microchannel heat sink with branching fins were cmpared to simulation results for a Microchannel heat sink with rectangular fins to ensure accuracy.
-
-
Geometry Modeling.
A three-dimensional model was developed to investigate the temperature distribution and heat transfer coefficient of the microchannel heat sink with branching fins using the software ANSYS FLUENT 21.0. The heat sink consists of four channels and three fins. Geometries of the heat sink are varied accordingly with the types of the fins. Single-phase cooling water is selected as a coolant because it has excellent heat transfer properties, is easily available, and is cheaper than other options.
Parameters |
Dimensions |
Baseboard Dimensions |
15 mm × 3.7 mm × 0.1 mm |
Stem Height |
1.25 |
Stem Thickness |
0.05 |
Branch height |
0.3 mm to 0.6 mm |
Branch Thickness |
0.13 |
Angle between branches |
45 |
Number of fins |
3 |
Material |
Copper |
Thermal Conductivity |
380 W/mK |
Table I. Dimensions of the microchannel heat sink with single branching fins
-
Executing the solver:
The heat rejected from the heating surface was evaluated using the ANSYS FLUENT 21.0 solver. As needed, the well specified model is employed. A cell zone is referred to as a material with its property. Then, over the necessary inlets, outlets, walls, etc., operational and boundary conditions are defined. Additionally, methods for discretizing different parameters in governing equations are taken into account. Using the stated conditions, the solver finally provides the convergent solution. To ensure that the clearly described model is correct, model validation must be carried out.
-
Analysis of the result:
The converged solution undergoes post-processing in this step in order to be examined in terms of intelligent display tools like contour, streamline, vector, graphs, Figures, animations, etc.
Fig. 2 Microchannel heat sink with single branching fins (Isometric View)
Fig. 2 Microchannel heat sink with single branching fins (Front View)
Parameters |
Dimensions |
Baseboard Dimensions |
15 mm × 3.7 mm × 0.1 mm |
Stem Height |
1.25 |
Stem Thickness |
0.05 |
Branch height |
0.3 mm to 0.6 mm |
Branch Thickness |
0.13 |
Angle between branches |
45 |
Second Branch Height |
45 |
Second Branch Thickness |
0.1 mm |
Angle between second branching |
0.015 |
Number of fins |
3 |
Material |
Copper |
Thermal Conductivity |
380 W/mK |
Table II. Dimensions of the microchannel heat sink with double branching fins
Fig. 5 Meshing of Microchannel heat sink with double branching fins (Isometric View)
Element size for meshing was chosen to be a minimum of 0.03 mm with a linear type of Mesh. The fine mesh was achieved by using face meshing. The total no. of nodes for the Microchannel heat sink with single branching fin and double branching fin geometry are 531794 and 565899, respectively.
-
Governing Equations
According to the different physical phenomena and the governing equations of energy conservations, mass momentum were used for mathematical modelling. These governing equations used are given below:
Continuity Equation:
+ + + = 0 .(1)
t x y z
Fig. 3 Microchannel heat sink with double branching fins (Isometric View)
Conservation of momentum:
X-momentum equation:
2 2
( + + v + w ) = – P + + ( +
2
t x y z
x
2
2
+ ) .(2)
2
Y-momentum equation:
2 2
( + + v + w ) = – P + + ( +
2
t x y z
y
2
2
Fig. 4 Microchannel heat sink with double branching fins (Front View)
+ ) .(3)
2
Z-momentum equation:
2 2
3. Meshing model
( + + v + w ) = – P + + ( +
After 3D geometric modelling of the Microchannel
t x y z x
2
2
2
heat sink with single branching and double branching was
meshed by ANSYS Fluent 21.0 meshing modular. To obtain the specified mesh quality, an automated mesh was created. Fluent with inbuilt meshing was used as it gives good results without compromising mesh quality. Further
+ ) .(4)
2
Conservation of energy
2T + 2T + 2T + q = 1 ( T + u T + vT + wT) .(5)
face meshing was done on the surfaces where the cooling fluid will flow.
2
2
2
k t
x y z
-
Boundary Conditions
The boundary conditions of the numerical analysis are: –
-
Uniform velocity at the inlet.
-
Constant heat flux at the bottom wall.
-
No slip condition for all directions on the wall.
-
Outer walls are insulated.
Microchannel heat sink with single branching fins and double branching fins with different cases were considered by varying the stem height of the fin from 0.3 to 0.6 mm and were studied with a varying velocity of cooling fluid from 0.25 to 1 m/s. Cooling fluid temperature is kept at 293 K. While the ambient temperature is considered as 300 K, and the heat flux given to the base of the Microchannel heat sink is kept constant at 500KW/m2.
-
-
Data Reduction
havr is the average convection heat transfer coefficient given by:
q
III RESULTS
Results were obtained by applying the boundary conditions mentioned above and followed by applying Equations and Iterations. Variation in velocities of cooling fluid will vary the cooling effect. These variations are studied for both the Microchannel heat sink with single branching fins and double branching fins for varying stem height of the fin. Variations are studied using contour plots and compared on graphs.
-
Validation of results:
It was found that no experimental model in the open literature for validating data obtained from the software for the MCHS with tree branching fins. However, the common case of the microchannel heat sink with rectangular fins has been studied extensively.A relatively little variation of 6-8% is seen when comparing software results with experimental data [1]. Only the fins' shape was modified in this investigation; all other elements, such as the fluid type, governing equations, and type of flow, were intact. Therefore, it can be said that the
havr =
TwTm
….(6)
findings for the new cases in this study have a sufficient level
of validity.
where,
Tw is the average bottom wall temperature of the micro- channel heat sink, and q is the heat flux from the electronic component.
Tin + Tout
Parametric analysis is done to validate the obtained results
further by varying the velocity of the cooling fluid from 0,25 m/s to 1m/s. Figure number 6.1 shows the comparison of the average bottom wall temp of MCHS v/s variation in velocity
Tm =
2
where,
.(7)
for a different types of fin geometries. Therefore, it can be
concluded that the CFD model has a reasonable precision.
Tin and Tou are the inlet and outlet fluid temperatures of the microchannel heat sink, respectively.
p = pin pout .(8)
where,
p is the pressure drop of the working fluid between the inlet and the outlet.
The pumping power of the microchannel heat sink is: Pp = Vp ..(9)
where,
V is the volumetric flow rate
SINGLE BRANCHING FIN
RECTANGUAR FINS
DOUBLE BRANCHING FIN
360
340
320
300
280
0 . 2 5 0 . 5 0 . 7 5 1
VELOCITY (M/S)
TEMP. OF MCHS (K)
Fig. 6 Temperature v/s Velocity
-
Grid Independence:
AVG BOTTOM WALL
TEMP. OF MCHS (K)
330
325
320
315
310
305
0 . 2 5 0 . 5 0 . 7 5 1
VELOCITY (M/S)
Fig. 7 Grid Independence
Three cases with element size 0.025mm, 0.05mm, and 0.075mm were used to carry mesh independency test for the present work. Number of elements is 14893703, 2666314, and 924384, respectively. All boundary conditions are kept the same for all three element sizes. The results of the mesh independency are presented in Fig. 6.73. It is observed that the results are almost independent of the number of cells as 0.025mm, 0.05mm, and 0.075mm. Results of mesh size 0.05 mm are in close agreement with 0.025 mm mesh size. Therefore, an Element size of 0.05mm is selected for the rest of the investigation to save time and achieve good results.
-
Contour Plots:
Contour plots are the color bands showing the variation of the respective variables.
-
Temperature Contour Plots
-
-
Microchannel heat sink with single branching fins:
Fig. 8 Temperature contour across section for stem height = 0.6 mm (Velocity = 1 m/s)
STEM HEIGHT = 0.3 mm STEM HEIGHT = 0.4 mm
STEM HEIGHT = 0.5 mm STEM HEIGHT = 0.6 mm
AVG. BOTTOM WALL TEMP OF MCHS(K)
332.75
328.98
327.81
326.68
Fig. 9 Temperature contour of bottom wall for stem height = 0.6 mm (Velocity = 1 m/s)
SINGLE BRANCHING
0 . 2 5
0 . 5
0 . 7 5
1
VELOCITY (M/S)
321.82
319.69
317.96
317.24
318.64
316.85
315.62
314.89
314.89
313.98
312.27
311.89
Fig. 10 Temperature v/s Velocity Graph for single branching fins
Figures 8 and 9, show temperature variation in Microchannel heat sink with single branching fins. While Figure number 10 depicts that out of all the geometries, the least outlet temperature of the fluid and the least average bottom wall temperature are obtained for the Microchannel heat sink with single branching fins having a stem height of 0.6 mm. The largest temperature drop is recorded for the Microchannel heat sink with single branching fins having a stem height of 0.6 mm for the velocity of 1 m/s. For this case, the outlet temperature of the fluid obtained is 296.2 K, and the average bottom wall temperature is
311.89 K.
Increasing the stem height from 0.3mm to 0.6 mm is also observed as there is more temperature drop for stem height of
0.6 mm compared to 0.3 mm, 0.4 mm, and 0.5mm for all velocities.
-
Microchannel heat sink with double branching fins:
Fig. 11 Temperature contour across section for stem height = 0.6 mm (Velocity = 1 m/s)
TTOM WALL TEMP OF MCHS (K)
325.09
323.52
322.68
322.32
317.36
316.56
315.95
314.084
Fig. 12. Temperature contour of bottom wall for stem height = 0.6 mm (Velocity = 1 m/s)
DOUBLE BRANCHING
STEM HEIGHT = 0.3 mm STEM HEIGHT = 0.4 mm
STEM HEIGHT = 0.5 mm STEM HEIGHT = 0.6 mm
0 . 2 5
0 . 5
0 . 7 5
1
VELOCITY (M/S)
313.78
312.73
311.81
311.12
310.77
310.23
309.815
309.65
Fig. 13. Temperature v/s Velocity for double branching fins
Figure number 11 and 12, show the temperature variation in the Microchannel heat sink with double branching fins. While Figure no. 13 depicts that out of all the geometries least outlet temperature of the fluid and the least average bottom wall temperature are obtained for the Microchannel heat sink with double branching fins having a stem height of 0.6 mm.
The largest temperature drop is obtained for the Microchannel heat sink with double branching fins having a stem height of
AVG BASE TEMP. OF MCHS (K)
-
mm for a velocity of 1 m/s. For this case, the outlet temperature of the fluid noted is 295.89 K, and the average bottom wall temperature is 309.65 K. Similar effect of increasing the stem height of the branching fin is observed. The double branching fins contain extra branches contributing to an increase in surface area of the fin as well as Microchannel heat sink, more temperature drop occurs, therefore MCHS with double branching fins gives better results than the MCHS with branching fins for stem height 0.3 mm to 0.6 mm and for velocity 0.25 m/s to 1m/s.
Single branching
Double branching
330
325
320
315
310
305
300
326.68
322.32
317.24
314.084
314.89
311.12
309.65
311.27
0 . 2 5
0 . 5
0 . 7 5
1
VELOCITY (M/S)
Fig. 14. Temperature v/s Velocity for single and double branching fins
-
Pressure Contour Plots
-
-
Microchannel heat sink with single branching
fins:
Fig. 15. Pressure Variation for stem height = 0.6 mm (Velocity = 1 m/s)
Figure 15 depicts the pressure drop for the MCHS with single branching fins having a stem height of 0.6 mm is 1708.5 Pa; the pressure drops increase with an increase in the velocity of the cooling fluid and an increase in the stem height of the fin.
SINGLE BRANCHING FINS
1800
1600
1400
1200
1000
800
600
400
200
0
VELOCITY (m/s)
STEM HEIGHT = 0.3 mm STEM HEIGHT = 0.4 mm
STEM HEIGHT = 0.5 mm STEM HEIGHT = 0.6 mm
55599. 695.46376.538.31
97
23255.4246.2127.28.05
0.25 0.5
0.75
1
PRESSSURE DROP (Pa)
Fig. 16. Pressure drops v/s Velocity for single branching fins.
-
Microchannel heat sink with double branching
fins:
Fig. 17. Pressure Variation for stem height = 0.6 mm (Velocity = 1 m/s)
Figure 17 depicts the pressure drop for the MCHS with single branching fins with a stem height of 0.6 mm is 2001.23 Pa; the pressure drops increase with the velocity of the cooling fluid and an increase in the stem height of the fin. Also, the pressure drop for double branching fins is higher as the extra branches cause more obstruction to the cooling fluid.
DOUBLE BRANCHING FINS
VELOCITY (m/s)
STEM HEIGHT = 0.3 mm STEM HEIGHT = 0.4 mm
STEM HEIGHT = 0.5 mm STEM HEIGHT = 0.6 mm
1708.5
1625.7
1416419.34.9
956.00118
1110181.6601.5
2500
2000
1667.8
1811950.35.6
2001.23
1500
1139.74.71
12318310450.96.65
1000
500 28391.23292.0038.8094.8
0
0.25
67753729.69.69
918.39
.2
0.5
0.75
1
PRESSURE DROP (Pa)
Fig. 18. Pressure drops v/s Velocity for double branching fins.
Figures 5.17 and 5.18 indicate that the maximum pressure drop is obtained for double branching fins with a stem height of 0.6 mm for all the velocities. The highest pressure drop obtained was 2001.23 Pa at the velocity of 1 m/s. It shows that the higher the fluid velocity, the more the pressure drop. Increasing fin height raised the flow obstruction and caused pressure drop to increase. In addition, as we increase the branching f the fin, the pressure drop increases respectively as they contribute more obstruction to the flow.
-
CONCLUSION
For the velocity range of 0.25 – 1m/s at a constant heat flux of 500 kW/m2, two different fin designs (single branching and double branching) for a microchannel heat sink using water as the cooling fluid are examined. Based on the comparative analysis of the results, the following important findings have been reported:
-
Microchannel heat sink with double branching fins of stem height of 0.6 mm gives least bottom wall temperature of 309.65 K, which is 4.78% less when compared to a Microchannel heat sink with rectangular fins of the same height.
-
With increasing fin height and branching of the fin, solid- fluid interaction or net convective area increases. Hence, the heat transfer rate also increases; therefore, the fins stem height and branching enable heat transfer enhancement.
-
The double branching fins proved more effective than single branching fins for heat transfer for all the applied velocities and variation in stem heights. The highest heat transfer coefficient is obtained for the Microchannel heat sink with double branching fins of stem height of 0.6 mm, which is 8000.01 W/m2K.
-
Pressure drop rises with increasing fin height since longer fins create more obstruction in the flow path. Consequently, heat sinks of 0.3 mm and 0.6 mm stem height offer minimum and maximum pressure drop, respectively.
-
The double branching fins for all the stem heights 0.3 mm to 0.6 mm have higher pressure drops than single branching fins since the extra branching adds more obstruction.
-
-
REFERENCES
335351,
[4] C.Y. Zhao, T.J. Lu, Analysis of microchannel heat sinks for electronics cooling, Int. J. Heat Mass Transf. 45 (2002) 48574869. [5] D.B. Tuckerman, R.F.W. Pease, High-performance heat sinking for VLSI, IEEE Electron Device Lett. 2 (1981) 126129.
[6] S. Kandlikar, S. Garimellar, D. Li, S. Colin, M.R. King, Heat Transfer and Fluid Flow in Minichannels and Microchannels, Elsevier, 2005 [7] Y. Peles, A. Kosar, C. Mishra, et al., Forced convective heat transfer across a pin fin micro heat sink, Int. J. Heat Mass Transf. 48 (2005) 36153627. [8] V. Yadav, K. Baghel, R. Kumar, Numerical investigation of heat transfer in extended surface microchannels, Int. J. Heat Mass Transf. 93 (2016) 612622.
[9] B. Yazicioglu and H. Yuncu, Optimum fin spacing of rectangular fins on a vertical base in free convection heat transfer, Heat Mass Transfer, Vol. 44, Pp. 1121, 2007. [10] V. Karlapalem, S. Rath, S.K. Dash, Orientation effects on laminar natural convection heat transfer from branching-fins, Int. J. Therm. Sci. 142 (2019) 89105. [11] S. Huang, J. Zhao, L. Gong, X. Duan, Thermal performance and structure optimization for slotted microchannel heat sink, Appl. Therm. Eng. 115 (2017) 12661276. [12] Sakkarin Chingulpitak et Al.;Fluid flow and heat transfer characteristics of heat sinks with laterally perforated plate fins. (International Journal of Heat and Mass Transfer 2019) [13] Jiayi Zheng, Jing Wang, Taotao Chen, Yanshun Yu, Solidification performance of heat exchanger with tree- shaped fins.(Renewable Energy 2020) [14] Vidyadhar Karlapalem, Sukanta Kumar Dash, Design of perforated branching fins in laminar natural convection. (International Communications in Heat and Mass Transfer 2021) [15] Y. Chen, C. Zhang, M. Shi, Y. Yang, Thermal and hydrodynamic characteristics of constructal tree-shaped minichannel heat sink, AIChE J. 56 (8) (2010) 2018e2029. [16] D. Calamas, J. Baker, Tree-like branching fins: performance and natural convective heat transfer behavior, Int. J. Heat Mass Transf. 62 (2013) 350361 [17] H.Y. Zhang, D. Pinjala, T.N. Wong, K.C. Toh, Y.K. Joshi, Single-phase liquid cooled microchannel heat sink for electronic packages, Appl. Thermal Eng. 25 (2005) 14721487. [18] P. Xu, A.P. Sasmito, B. Yu, A.S. Mujumdar, Transport phenomena and properties in treelike networks, Appl. Mech. Rev. 68 (2016) 040802,https://doi.org/10.1115/ 1.4033966.
[19] ANSYS®, Academic Research Mechanical, Release 19.2, Help System, ANSYS Inc, Cannonsburg,PA, 2019. [20] K.T. Park, H.J. Kim, D.-K. Kim, Experimental study of natural convection from vertical cylinders with branched fins, Exp. Thermal Fluid Sci. 54 (2014) 2937, https://doi.org/10.1016/j.expthermflusci.2014.01.018 [21] Y. Alihosseini, M.Z. Targhi, M.M. Heyhat, N. Ghorbani, Effect of a micro heat sink geometric design on thermo-hydraulic performance: a review, Appl. Therm. Eng. 170 (2020) 114974. [22] O.O. Adewumi, T. Bello-Ochende, J.P. Meyer, Constructal design of combined microchannel and micro pin fins for electronic cooling, Int. J. Heat Mass Transf. 66 (2013) 315323. [23] P.S. Lee, S.V. Garimella, Thermally developing flow and heat transfer in rectangular microchannels of different aspect ratios, Int. J. Heat Mass Transf. 49 (2006) 30603067. [24] A. Bejan, M. Almogbel, Constructal T-shaped fins, Int.J. Heat Mass Transf. 43 (2000) 21012115
[25] S. Acharya, S.K. Dash, Natural convection heat transfer from a perforated hollow cylinder with inline and staggered holes, J. Heat Transf. 140 (2018). [26] M. Mesgarpour, A. Heydari, S. Saedodin, Comparison of free convection flow around an engineered porous fin with spherical connections and rigid fin under different positioning angles – an experimental and numerical analysis, Phys. Fluids 31 (2019). [27] N.S. Effendi, S.S.G.R. Putra, K.J. Kim, Prediction methods for natural convection around hollow hybrid fin heat sinks, Int. J. Therm. Sci. 126 (2018) 272280.