
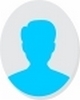
- Open Access
- Authors : Tejas Patil , Sudhakar Umale
- Paper ID : IJERTV11IS090036
- Volume & Issue : Volume 11, Issue 09 (September 2022)
- Published (First Online): 28-09-2022
- ISSN (Online) : 2278-0181
- Publisher Name : IJERT
- License:
This work is licensed under a Creative Commons Attribution 4.0 International License
CFD Analysis of Baffled Shell and Tube Heat Exchanger with Different Cross-Section of Tubes
Tejas Patil1
M. Tech. Scholar Mechanical Engineering Department Sardar Patel College of Engineering, Andheri (West)
Mumbai, Maharashtra, India
Sudhakar Umale2
Former Associate Professor Mechanical Engineering Department,
Sardar Patel College of Engineering, Andheri (West) Mumbai, Maharashtra, India
Abstract One of the industrial processes most widely used heat exchangers is the shell and tube unit. This study used a shell and tube heat exchanger with helical and double segmental baffles. By adjusting baffle spacing, baffle number, and tube cross-section shape, analysis is done on a shell and tube heat exchanger with ANSYS 2021 to determine the best heat transfer coefficient and minimal pressure loss. Tubes with various cross-sections, including circular, elliptical in the horizontal and vertical directions, and angled at 30°, 45°, and 60°, were also investigated. It has been found that the results are sensitive to the baffle type, baffle spacing, and cross- sectional tube shape.
With varying Reynolds numbers between 10000 and 40000, a shell and tube heat exchanger with double segmental and helical baffles was examined. The velocity of the fluid in the hot tube was maintained constant at 0.01 m/s. In contrast, Cold Shell fluid velocity changed according to Reynolds' number. The input temperature of cold and hot fluids was
-
K and 353.15 K, respectively. The arrangement of eight helical baffles in a vertical elliptical tube was discovered to have the highest overall heat transfer coefficient. As compared to other tube geometries, vertical elliptical tube geometry performs optimally with both double-segmental and helical baffles. Helical baffles demonstrate more heat transmission when compared to double-segmental baffles. Although helical and double-segmental baffles improve the performance of vertical elliptical tubes, they also exhibit the greatest pressure loss. Maximum pressure loss indicates that more pumping power is needed to keep the fluid moving at its current pace. Angled elliptical tubes are ideal for balancing heat transfer and pressure drop. They have a much lower pressure drop than other cross-section shapes of tubes and exhibit heat transfer that is close to that of vertical elliptical tubes.
Keywords Shell and tube heat exchanger, cross-sectional shape of tube, heat transfer, CFD analysis, Pressure drop.
-
INTRODUCTION
A shell with a bundle of tubes inside makes up this type of heat exchanger. The fluid inside these tubes is either heated or cooled. Heat exchange is possible because the second fluid flows over the tubes. High-pressure applications use Shell & tube heat exchangers because of their durable design [1]. Numerous variables, including the required heat transfer rate, the permitted pressure drop, the number of baffles, the distance between baffles, the type of fluid and its phase, temperature, density, viscosity, pressure, chemical composition, and various other thermodynamic properties, affect the type and size of the heat exchanger [2].
Single-segmental baffles are utilized in the most popular shell and tube heat exchanger type. In order to achieve a greater heat transfer coefficient, they are employed to direct the flow across the bundle, support the tubes for strength and rigidity, prevent tube vibration, prevent tube sagging, and structural support [5]. However, conventional Shell and Tube heat exchangers with segmental baffles suffer significant drawbacks like high-pressure drop and dead zones. Contrarily, double-segmental baffles have demonstrated fewer dead zones and vibrations than segmental baffles [6].
The optimal baffle spacing shell and tube heat exchanger have been the subject of numerous studies in the past [7]. The performance of the heat exchanger is affected by changes in the baffle spacing, where a reduction in the baffle spacing is brought on by an increase in the Nusselt number and friction factor [8].
The issues above with segmental baffles have been addressed by a number of investigations [69] [21]. Several configurations were suggested, including double segmental baffles, disk-and-donut layout, optimized spacing baffles, floral baffles, etc. [18] [19]. A new kind of baffle termed a "helical baffle" was introduced to make improvements [10] [17]. The fouling on the shell side can be reduced, and flow-induced vibration can be avoided with properly constructed continuous helical baffles. According to the findings, continuous helical baffles have a nearly 10% higher heat transfer coefficient than traditional segmental baffles with the same shell-side pressure drop [11].
As an additional method to enhance the efficiency of heat exchangers, researchers have recently examined the usage of various tube bundles. Researchers used elliptical tubes paired with helical baffles in a vertical shell tube heat exchanger. The modified baffle and tube arrangement achieved a 3035% increase in thermal performance [14]. Comparing tubes with different cross sections circular, elliptical with a 90° attack angle, and elliptical with a 0° attack angle was done. A combined model of a shell and tube heat exchanger with 90°-attack elliptical and circular tubes was shown [15] [20].
Fig. 1 Schematic diagram of Counterflow shell and tube heat exchanger [1]
This literature study demonstrates significant advancements in our knowledge of the shell and tube heat exchanger with elliptical tubes; this had some numerical analysis work and was primarily driven by experimental research. The goal of the current effort, which was to create a baffled shell and tube heat exchanger with angled elliptical tubes, was inspired by these literature evaluations.
-
METHODOLOGY
-
Geometrical modeling of shell and tube heat exchanger.
The shell and tube heat exchanger had been designed, rated, and sized. When designing the heat exchanger, two fluids were taken into account. In contrast to raw water (Cold fluid), which runs on the shell side, distillate water (Hot water) flows on the tube side. Consideration was given to single shell and single tube pass geometries. Because it had a simplistic construction and was simple to utilize baffles in, the E-type shell was selected for the experiment. Additionally, the tubes' dimensions were chosen as per the reference research papers. That then selected the Tube geometry, arrangement, and Pitch. Copper has high thermal conductivity and is used in various settings, from little household appliances to substantial industrial operations.
TABLE I. PARAMETERS OF HEAT EXCHANGER
Parameters
Values
Shell Diameter (Ds)
90 mm
Heat Exchanger Length
500 mm
No. of Tubes
07
No./ Turns of Baffles
04, 06, 08
The layout with the maximum tube density and staggered arrangement is a 30° triangular tube design. The outlet was designed with a height and diameter of 30 mm, shell, and tube inlet. The diameter of circular tubes was considered 20 mm. Since the perimeter of circular and elliptical tubes was the same, the diameter of elliptical tubes with a ratio of 1:2 can be calculated from the following equation,
ACircle = AEllipse (1)
AEllipse = 2 ×((a2+b2)/2) (2) Therefore, a = 6.32 mm and b = 12.64 mm.
-
(b)
(c) (d)
(e) (f)
Fig. 2. (a) Circular tubes (b Horizontal elliptical tubes (c) Vertical elliptical tubes (d) 30°Angled Elliptical tubes (e) 45°Angled Elliptical tubes (f) 60°Angled Elliptical tubes.
Different tube geometries utilized for the analysis are depicted in Figure 2. These include circular tubes, horizontal elliptical tubes, vertical elliptical tubes, 30° angled elliptical tubes, 45° angled elliptical tubes, and 60° angled elliptical tubes.
-
-
Boundary conditions.
Reynolds number was varied between 10000 and 40000, and a shell and tube heat exchanger with double segmental and helical baffles was examined. The velocity of the fluid in the hot tube was maintained constant at 0.01 m/s. In contrast, Cold Shell fluid velocity changes according to Reynolds' number. Cold fluid's input temperature is 300.15 K, whereas hot fluid's inlet temperature is 353.15 K. Fig. 3 and 4 illustrate, respectively, an isometric view of a shell and tube heat exchanger with double segmental baffles and helical baffles.
Fig. 3. Shell and Tube heat exchanger with Double segmental baffles (Isometric View)
-
Continuity equation:
+ + + = 0 (3)
t x y z
-
Conservation of momentum equation:
-
X-momentum equation:
2 2 2
( + + v + w ) = – P + + ( + + ) (4)
t x y z
x
2
2
2
-
Y-momentum equation:
2 2 2
( + + v + w ) = – P + + ( + + ) (5)
t x y z
y
2
2
2
-
Z-momentum equation:
2 2 2
( + + v + w ) = – P + + ( + + )
Fig. 4. Shell and Tube heat exchanger with Helical baffles (Isometric View)
t x y z
x
2
2
2
(6)
-
-
Conservation of energy equation:
2T
2T
2T q
1 T
T T T
-
-
Meshing model.
An ANSYS Fluent 19.0 meshing modular was used to mesh the Shell & tube heat exchanger with double segmental and helical baffles after 3D geometric modelling. To obtain the appropriate meshed quality, automatic meshing was carried out. Fluent with integrated meshing was employed because it produces effective results without sacrificing mesh quality. The polyhedral mesh was created by creating polygons around every node on the tetrahedral mesh, which is what is used in this application. Improved numerical stability results from polyhedral mesh since it enhances polyhedral mesh by creating polygons around every node on the tetrahedral mesh quality and minimizes skewness.
A minimum element size for meshing of 2.5 mm was selected with a polyhedral mesh type. The smooth transition achieved improved mesh elements for inlets and outlets. Using a transition ratio of 0.1, 3 layers, and a growth rate of 1.2 resulted in a fine mesh. There are 964720 and 1124970 nodes for shell and tube heat exchangers with double segmental baffles and helical baffle designs, respectively.
2 + 2 + 2 + k = ( t + u x + vy + wz) (7)
-
Turbulence Model (Standard k-e) equation:
The most popular model used in CFD analysis is the K- epsilon (k-) turbulence, model. To simulate the flow characteristics of turbulent flow situations, this model is
utilized. It is a two-equation model with two transport equations that offers a broad description of turbulence. On the scales in a fluid flow, from simple to complicated, it is also utilized to discover an alternative to the turbulent length described algebraically. Unlike the earlier turbulence model, the k- model does not concentrate on factors influencing kinetic energy. The fundamental presumption of this model is that a turbulent dynamic viscosity corresponds to shear stress to strain ratio that is constant in all fluid flow directions. Improved wall treatment for the realizable k- model is employed to improve outcomes.
The two model transport equations for k and in the realizable k- model is:
Partial () + ( ) = [( + ) ] + +
+
(8)
() + ( ) = [( + ) ] + 2
+
+
1
2 +
1 3
(9)
Fig. 5. Meshed cells of Shell & tube heat exchanger.
-
-
Mathematical modeling.
Mass momentum is used for mathematical modeling according to the different physical phenomena and the governing equations of energy conservation. Below are the governing equations that were employed:
-
Post-processing.
A simulation was run to check for convergence after applying the equations, boundary conditions, and other parameters. It requires convergence to arrive at a sound solution. Results for the temperature and pressure drop were obtained after convergence. Hybrid initialization was completed after giving inlet and boundary conditions, and iterations were carried out. Successful convergence of the solution was done. The effect of a change in Reynolds number on double-segmental and helical baffles were studied using contours. Temperature and pressure drop in hot fluids was examined and compared.
Fig. 6. Residual plot.
-
-
RESULTS AND DISCUSSION Reynold's number variation alters the shell fluid's velocity, increasing turbulence and disturbance. It results in a drop in pressure and a change in the temperature of the hot fluid at the output. Both the Shell and tube heat exchanger with double segmental baffles and helical baffles are investigated for these changes. In the figures, variations are compared and analyzed using contour plots.
-
Grid Independence Study.
In the current work, a mesh of a polyhedral mesh type is generated using ANSYS mesh software. Three cases with element sizes of 2 mm, 2.5 mm, and 3 mm were utilized in the current work's mesh independence test. There are 462070, 359496, and 291138 cells connected with these element sizes,
respectively. For the three different element sizes, all boundary conditions are maintained constant. In Figures 7 and 8, respectively, the results of mesh independence for temperature and pressure drop are displayed.
Fig. 7. Effect of Mesh density on Temperature drop
.
Fig. 8. Effect of Mesh density on Pressure drop
It has been found that the findings are mainly unaffected by the sizes of the elements. Temperature and pressure drop measurements made for elements with a 2 mm and 2.5 mm size are very similar to one another. A 2.5 mm element size is chosen for the remaining research to reduce time and still produce high-quality results.
-
Validation of Results.
No experimental model for validating data from software for the new types of tube configuration was discovered in the literature. However, the conventional shell and tube heat exchanger with circular tubes has been the subject of in-depth research. A relatively small difference of 5-8% is seen when comparing software results with experimental results [16]. Only the tube shape was altered in all of the heat exchangers that were the subject of this study, while other aspects, including the kind of fluid, governing equations, baffles, and flow type, remained constant. As a result, it can be said that the findings for the new instances in this research have a sufficient level of validity.
By altering the velocity of the shell fluid, parametric analysis was carried out to validate further the results acquired. The comparison of tube outlet temperature v/s variations in Reynolds number for various types of tube geometries is shown in Fig. 9. By comparing the results, it can be seen that for various tube geometries, the temperature drop follows a similar trajectory in terms of variation with Reynolds number. The aforementioned parametric comparisons and analyses lead to the cnclusion that the CFD model has a respectable level of precision.
Fig. 9. Tube outlet temperature v/s Reynolds number
-
Temperature Contour Plots.
-
Shell and tube heat exchanger with double segmental baffles
Fig. 10. Temperature Variation (Reynolds No.= 40000) (STHX-CT- 8×DSB)
Fig. 11. Temperature Variation (Reynolds No.= 40000) (STHX-VET- 8×DSB)
Fig. 12. Tube Outlet Temperature v/s No. of Baffles (STHX-DSB)
Figures 10 and 11 depict temperature variation across the shell and tube (eight double segmental baffles) with circular and Vertical elliptical tubes. The relationship between the number of double segmental baffles and the tube geometries and tube output temperature is shown in Fig. 12. Of all the tube geometries, it is discovered that circular tubes have the least temperature drop. At the hot fluid output of a Shell and Tube heat exchanger with eight
double segmental baffles, the lowest temperature is 314.12
K. (Vertical Elliptical tubes). The most significant temperature drop, 38.88 K, is recorded. The highest Reynold's Number, 40000, is observed to cause this temperature reduction. It demonstrates that Vertical Elliptical tubes perform the best among all the tube geometries.
-
Shell and tube heat exchanger with helical baffles.
Fig. 13. Temperature Variation (Reynolds No.= 40000) (STHX-CT- 8×HB)
Fig. 14. Temperature Variation (Reynolds No.= 40000) (STHX-VET- 8×HB)
Fig. 15. Tube Outlet Temperature v/s No. of Baffles (STHX-HB)
Figures 13 and 14 show temperature variation across the shell and tube (eight helical baffles) with circular and Vertical elliptical tubes. The impact of the number of helical baffles and the tube geometries on tube output temperature is shown in Fig. 15. Among all tube geometries, it has been found that circular tubes exhibit the lowest temperature drop. The hot fluid's minimum exit
temperature was 311.54 K. (Vertical Elliptical tubes) in a Shell and Tube heat exchanger with eight Helical baffles. The most significant temperature drop, 41.46 K, is noted. At the greatest Reynolds Number of 40000, this temperature reduction is seen. It demonstrates that Vertical Elliptical tubes perform the best among all the tube geometries. It indicates that, regardless of the type of baffle or the number of baffles, Vertical Elliptical tube geometry delivers the most significant temperature drop among all tube geometries. Following the vertical elliptical tubes, angled elliptical tubes work well.
-
Pressure Contour Plots.
-
Shell and tube heat exchanger with double segmental baffles
Fig. 16. Pressure drop (Reynolds Number = 40000) (STHX-CT-8 DSB)
Fig. 17. Pressure drop (Reynolds Number = 40000) (STHX-60°AET -8 DSB)
Fig. 18. Pressure Drop v/s No. of Baffles (STHX-DSB)
Figures 16 and 17 depict Pressure drops across the shell and tube (eight double segmental baffles) with circular, and 60° angled elliptical tubes. The impact of the number of double segmental baffles and tube geometries on pressure drop is shown in Fig. 18. Among all tube geometries, it has been found that circular tubes exhibit the highest pressure drop. In 60° Angled Elliptical tubes, a minimum pressure drop of 47.3 Pa is achieved with eight Double segmental baffles. The greatest Reynold's Number of 40000 is where this pressure reduction is seen. It demonstrates that 60° Angled Elliptical tubes perform the best among all tube geometries.
-
Shell and tube heat exchanger with helical baffles
Fig. 19. Pressure drop (Reynolds Number = 40000) (STHX-CT-8 HB)
Fig. 20. Pressure drop (Reynolds Number = 40000) (STHX-30°AET-8 HB)
Fig. 21. Pressure Drop v/s No. of Baffles (STHX-HB)
Figures 19 and 20 depict pressure drops across the shell and tube (eight helical baffles) with circular and 30° angled elliptical tubes. The impact of the number of helical baffles and tube geometries on pressure drop is shown in Fig. 21. Among all tube geometries, it has been found that vertical elliptical tubes exhibit the highest pressure drop. In 30° Angled elliptical tubes, the minimal pressure drop is achieved with eight helical baffles, 138.93 Pa. This pressure drop is seen at a Reynolds number of 40000, the highest. It demonstrates that 30° angled elliptical tubes perform best across all tube geometries. It shows that 60° Angled elliptical tube geometry performs best, giving the lowest pressure drop among all types of tube geometries with double segmental baffles. While with helical baffles, 30° Angled elliptical tube geometry performs best, giving lowest pressure drop.
-
-
Overall Heat Transfer Coefficient (U).
Several conductive and convective barriers' overall capacity to transfer heat is gauged by the overall heat transfer coefficient (U). It is based on the logarithmic mean temperature difference, total heat transfer area, and heat transfer rate.
Fig. 22. Overall heat transfer coefficient v/s Number of Baffles (STHX- DSB)
Fig. 23. Overall heat transfer coefficient v/s Number of Baffles (STHX- HB)
Fig. 22 and 23 depict how the total heat transfer coefficient is affected by the number of double-segmental baffles, helical baffles, and various tube shapes. The highest overall heat transfer coefficient among all tube geometries is found
in vertical elliptical tubes with double-segmental and helical baffles. The overall heat transfer coefficient increases along with the number of baffles. Maximum heat transfer has been seen with eight baffles because baffles add additional resistance and diversion to fluid flow, intensifying turbulence. The vertical elliptical tube configuration with eight helical baffles has the highest reported overall heat transfer coefficient, 36.547 KW/m2K.
-
-
CONCLUSION
By altering the orientation of the tube geometries, the variations in outlet tube temperature and shell side pressure drop were examined. The impact of helical and double segmental baffles on the same was investigated by varying the number of baffles.
The following results were obtained:
-
In comparison to all the other cases, the shell and tube heat exchanger with eight helical baffles and vertical elliptical tubes had the greatest temperature drop. Since an increase in Reynold's number causes an increase in turbulence, which enhances temperature drop, Reynold's number plays a significant role in temperature decline.
-
The STHX-VET and THE-AET configurations showed the most significant temperature drop. Due to the fluid's angle of attack as it falls from the shell into the tube surfaces, elliptical tubes in heat exchangers transfer heat more quickly than round tubes. Therefore, the temperature drop is strongly influenced by the various geometrical shapes of the tubes.
-
Comparing STHX-60°AET to all the other tube geometries revealed a minimum pressure drop of 47.3 Pa. STHX-60°AET produces pressure drops that are 17.4% lower than STHX-CT.
-
STHX-30°AET with eight helical baffles had the lowest pressure drop of 138.93 Pa among all the tube shapes. STHX-30°AET shows a 71.5% decrease in pressure, which is smaller than STHX-VET and 67% less than STHX-CT.
-
For any geometry of STHX, the least pressure drop is preferable to minimize energy loss. Different inclined elliptical tube shapes have demonstrated the least amount of pressure drop. As a result, the pressure drop on the shell side is greatly influenced by the cross- sectional surface of the tubes in the shell.
-
The vertical elliptical tube configuration with 8 helical baffles has the highest total heat transfer coefficient,
36.547 KW/m2K. Compared to other tube geometries, vertical elliptical tube geometry performs well with double-segmental and helical baffles. When compared to double-segmental baffles, helical baffles exhibit more excellent heat transfer.
-
Although they exhibit the most signficant pressure drop, vertical elliptical tubes work best when equipped with helical and double-segmental baffles. A maximum pressure drop indicates that more pumping power is needed to maintain the fluid's velocity. For these reasons, inclined elliptical tubes are the most excellent choice for balancing heat transfer and pressure drop. In comparison to other cross-section
shapes of tubes, they have heat transfer that is close to that of vertical elliptical tubes and have a very low- pressure drop.
-
-
REFERENCES
-
, 2010.
[3] https://www.southwestthermal.com/shell-tube-exchanger.html [4] http://www.thermex.co.uk/news/blog/605-why-counter-flow-heat- exchangers-are-more-efficient [5] Asif Ahmed, Imam Ul Ferdous and Sumon Saha, Comparison of Performance of Shell-and-Tube Heat Exchangers with Conventional Segmental Baffles and Continuous Helical Baffle, 7th BSME International Conference on Thermal Engineering, June 2017. [6] Pranita Bichkar, Ojas Dandgaval, Pranita Dalvi, Rhushabh Godase and Tapobrata Dey, Study of shell and tube heat exchanger with the effect of type of baffles, Elsevier, February 2018. [7] M. A. Zebua1 and H. Ambarita, A study on the effect of baffle spacing to the performance of a shell and tube heat exchanger, IOP Conf. Series: Journal of Physics: Conf. Series 1235, Year 2019. [8] Mustapha Mellal, Redouane Benzeguir, Djamel Sahel and Houari Ameur, Hydro-thermal shell-side performance evaluation of a shell and tube heat exchanger under different baffle arrangement and orientation, International Journal of Thermal Sciences 121 (2017). [9] Noor Afsar and Dr. Mohammad Ilias Inam, CFD Analysis of Shell and Tube Heat Exchanger with Different Baffle Orientation& Baffle Cut, International Conference on Mechanical, Industrial and Materials Engineering 2017.
[10] Lutcha, J and Nemcansky J, Performance improvement of tubular heat exchangers by helical baffles, Chemical Engineering Research and Design; (UK); Journal Volume: 68: A3 (1990) [11] B. Peng and Q. W. Wang, An Experimental Study of Shell-and- Tube Heat Exchangers with Continuous Helical Baffles, Journal of Heat Transfer Vol. 129 (2007) [12] Cong Dong, Ya-Ping Chen and Jia-Feng Wu, a Influence of baffle configurations on flow and heat transfer characteristics of trisection helical baffle heat exchangers, Energy conversion and management (2014). [13] Cong Dong, Ya-Ping Chen and Jia-Feng Wu, Flow and heat transfer performances of helical baffle heat exchangers with different baffle configurations, Applied thermal engineering 80 (2015) [14] Numerical investigation on performance comparison of non- Newtonian fluid flow in vertical heat exchangers combined helical baffle with elliptic and circular tubes, Z. He, et al. (2016) [15] Mohammad Reza Safarian, Farivar Fazelpour and Mehrzad Sham, Numerical study of shell and tube heat exchanger with different cross section tubes and combined tubes, International Journal of Energy and Environmental Engineering (2019). [16] Anas El Maakoul, Azzedine Laknizi, Said Saadeddine, Mustapha El Metoui, Abdelkabir Zaite, Mohamed Meziane, Abdelatif Ben Abdellah, Numerical comparison of shell-side performance for shell and tube heat exchangers with trefoil-hole, helical and segmental baffles, Applied thermal engineering 109 (2016) [17] Ashish Sahu and Amit Kumar, Comparative Analysis and Simulation of Helical & Segmented Baffles in Shell & Tube Heat Exchanger using CFD Method, International Research Journal of Engineering and Technology (IRJET) Volume: 05 Issue: 05 | May- 2018. [18] Li He and Peng Li, Numerical investigation on double tube-pass shell-and-tube heat exchangers with different baffle configurations, Applied thermal engineering 143 (2018). [19] Emad M.S. El-Said, M.M. Abou Al-Sood, Shell and tube heat exchanger with new segmental baffles configurations: A comparative experimental investigation, Applied thermal engineering 150 (2019). [20] Ali Akbar Abbasian Arani and Hamed Uosofvand, Double-pass shell-and-tube heat exchanger performance enhancement with new combined baffle and elliptical tube bundle arrangement, International journal of thermal sciences 167 (2021). [21] Erica Jacqueline Fernandes and Sachidananda Hassan Krishanmurthy, Design and analysis of shell and tube heat exchanger, Int. J. Simul. Multidisci. Des. Optim. 13, 15 (2022).