
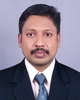
- Open Access
- Authors : Revathy A , Aliya Navas , Muhzeena A , Anoob Devarajan, Manu Varghese
- Paper ID : IJERTV11IS080068
- Volume & Issue : Volume 11, Issue 08 (August 2022)
- Published (First Online): 24-08-2022
- ISSN (Online) : 2278-0181
- Publisher Name : IJERT
- License:
This work is licensed under a Creative Commons Attribution 4.0 International License
Brick Manufacturing by Amalgamation of Sludge and Glass Powder
Revathy A1, Aliya Navas1, Muhzeena A1,Manu Varghese1,Anoob Devarajan2
1Students, Department of Civil Engineering MES Institute of Technology & Management, Chathannoor, Kollam, Kerala, India 2Associate professor , Department of Civil Engineering MES Institute of Technology & Management, Chathannoor, Kollam, Kerala, India
Abstract Waste may be defined as unwanted materials generated after the manufacturing process from industry, agriculture or from household activities. Waste causes many nuisances in environment. It creates many infectious diseases for living beings. The greatest solid waste disposal problems are from sludge generated by municipal wastewater treatment plants. Dewatered sludge is disposed off by land filling. However, it is not an appropriate solution due to land limitation. Fly ash is one of the major residues generated during combustion of coal in thermal power plants and the glass waste is a problematic threat to environment. The experimental study aimed to check the feasibility of using water treatment sludge, fly ash and glass powder in brick making that can be used as building material and analyse the effect of sludge and glass powder in brick in terms of compressive strength, water absorption, and efflorescence. In this study, the sludge from water treatment plant Punalur was collected and analysed. As a remedial measure, that is to reduce the wastage of land the clay is partially replaced with sludge, fly ash and glass powder in brick making. Then the various properties of the bricks are studied. The need for the study is to reduce the environment impact of disposal of the main two waste products i.e. water treatment plant sludge and glass powder. Clay bricks available in some regions have poor quality, low compressive strength, higher water absorption which have been compelling to develop better materials to counter these issues. So, the main objective of this study is the conservation of natural resources like clay and to check the feasibility of making brick from sludge and glass powder for a sustainable development.
KeywordsSludge,glasspowder,flyash,strength properties
-
INTRODUCTION
Wastes are the common environmental threat to India as well as to developing countries. Most of the municipalities dump the waste in land and water. The greatest solid waste disposal problems are sludge from municipal wastewater treatment plant and glass, an amorphous non degradable component in which provides hazardous properties to the landfill and fly ash a finely divided residue resulting from the combustion of powdered coal and collected by electronic precipitators in thermal power plants. Presently these materials are neither used in any of the activities. In India, the sludge is disposed by landfilling methods. Approximately 160 million tons of fly ash is produced by thermal power plants every year. However, the greatest proportion of the fly ash produced must be disposed off either by trucking to a dumping ground or by sluicing to an ash pond and the waste glass is being dumped directly which create environmental issues on global network. In todays environment the main objective is to manufacture the building materials without any impact to the environment. In this situation it is necessary to concentrate on reuse and recycle of waste materials. At the same time the waste material should
not affect the strength and should have low cost. The materials we used for experiment are sludge lagoon, fly ash of class F and glass powder.
Recycling the water treatment plant (WTP) sludge is usually an attempt to reduce its volume makes it stable, recover useful contents and facilitate its safe disposal without imposing burden to the environment. The sludge dry mass contains mainly high concentration of silica, aluminium or iron salts, with mixture of organic and inorganic materials and hydroxide precipitates. The mineralogical composition of the sludge is particularly close to that of clay . This fact encourages the use of WTP sludge to be a potential substitute for clay in brick making. Energy requirements for the developing countries in particular area get energy from coal. The disposal of the increasing amounts of thermal waste from coal-fired thermal power plants, this disposal of the thermal waste is called fly ash. It is a powdery substance obtained from the dust collectors in the electrical power plants that use coal as fuel. There are two basic type of fly ash. Class F and class C. Glass powder is a material consisting of numerous extremely fibres of glass. It is a light weight, extremely strong material. These are commonly used in the construction industries for high performance. Their characteristic is their high strength. Glass powder mainly consists of silica which is primarily constituent of sand. Some aluminium oxides and other metallic ions are there in various proportions to either ease the working operations or modify some properties.
A. Significance of study
Conservation of natural resources is the main use of this study.The use of the alternate materials can reduce the cost of construction materials .Environmental pollution can be reduced. .By making use of waste materials ,a light weight product is obtained.Utilisation of sludge ,flyash and glasspowder provides a better environment.
-
MATERIALS
-
Flyash
The greatest proportion of the fly ash produced from the coal burning power plants must be disposed off either by trucking to a dumping ground or by sluicing to an ash pond. In this case the result is a large waste area which is resistant to the growth of vegetation and has the potential for ground or surface water pollution due to the leaching of soluble materials from the fly ash.
-
Sludge
Fig 2.1 Flyash
Fig 2.3 Glasspowder
Silica, alumina, ferric oxide and lime constitute the major percentage of chemical components present in the sludge. Some heavy metals are also found in the sludge. Discharging waste treatment sludge into river, streams, ponds, lakes, drains etc. or landfilling the dewatered WTS is not environment friendly disposal option. Based on the characteristics, sustainable and profitable disposal through recycling and reuse have been reviewed. Utilization of WTS in brick making, in ceramics making, in the manufacture of cement and cementitious materials and as a substitute to building materials could provide safe disposal route. Reuse in wastewater treatment, in removal of heavy metals from aqueous solutions and in nutrient reduction from laden soils and runoffs are also some of the possible alternatives. It is required to explore suitable option for developing sustainable sludge management strategies under stringent environmental norms.
Fig 2.2 Sludge
-
Glasspowder
Glass powder is a waste material and it becomes granulated by sieving by means of sieves after they are crushed in the breaker and milled. Glass powder is proved to be economical and is considered as environmentally friendly construction material. Based on the experiment related to the water absorption (WA), firing shrinkage, compressive strength, and apparent porosity (AP) of fired clay bricks containing waste glass, it was shown that the waste glass powder can be used as a potential fluxing agent to help in lowering the firing temperatures of clay bricks.
-
Clay
Clay soil has very fine mineral particles and not much organic materials.It develops plasticity when in wet conditions.Clay minerals are composed of silica,alumina,magnesia or both and water.The clay buildng materials are stable and durable.Clays are the result of weathering.These are used in wide varieties of industries.These clays provides porosity,aeration and water retention.
-
-
EXPERIEMENTAL PROCEDURE
There are four steps involved in brick manufacturing process.They are preparation of brick earth,moulding of bricks,drying of bricks,burning of bricks.
In first step the soil is excavated and then laid on a levelled ground after removing impurities it is exposed to weather for few months. This is called process of weathering.Then it is blended with other materials to prepare good brick earth. Then mixed soil is tempered by being thoroughly broken up, watered.
Moulding of brick is done in many ways depending on the quality of the product to be made. They are hand moulding and machine moulding For hand moulding the tempered clay is forced into the mould in such a way that it fills the corners of mould. Extra clay is removed by wooden strike or frame with wire. Machines used for moulding is generally of two types. i) Plastic clay machines ii) Dry clay machines
In plastic clay machines the clay in plastic state is forced to rectangular openings of a size equal to length and breadth of a bricks and is then cut into strips of thickness of brick with wires in frame. In dry clay machines, dry clay is reduced to powder, filled dry into mould by machine and then subjected to high pressure to form hard and well-shaped bricks
Drying is usually done in placing the bricks in the shed with open sides so as to ensure free circulation of air The drying period is usually 7 to 14 days.
Burning is the most important step in manufacture of brick. Kilns are permanent structures consisting of many chambers. There are intermittent and continuous kilns. Moulded clay is stacked in the champers they are slowly dried and burned to high temperature and cooled.
-
Methodology
-
Materials collection
-
Materials testing
-
Mix design
-
Brick making
-
Tests to determine the properties of bricks
-
Analysis of results
-
-
Material Testing Dry sludge
-
Specific gravity test
Specific gravity is the ratio of the density of a substance to the density of a reference substance equivalently, it is the mass of the substance to the mass of the reference substance for the same given volume.The specific gravity of sludge passing through 4.75 mm IS sieve is found out by pycnometer.First step is to wash,dry and weigh the pycnometer(w1).Then place about 200-400g of dry sample in pycnometer.Weigh the bottle with dry sludge(w2).Add sufficient amount of water to cover the dry sludge,and mix thoroughly with glass rod and add more water and stir it.Fill the bottle with water with upto the calibration mark.Then clean the exterior surfaces of bottle pycnometer with dry cloth and weigh the bottle with contents(w3).Empty the bottle and clean it and fill it with distilled water upto the hole of conical cap and record its weight(w4) and then conduct the test times.
Table 3.1 specfic gravity test
Determination no.
1
2
3
w1 g
662
662
662
w2 g
962
962
962
w3 g
1656
1648
1656
w4 g
1522
1522
1522
Specific gravity,G
1.8
1.72
1.8
SPG = (w2 -w1) / (w2-w1)-(w3-w4)
= 1.8
-
Sieve analysis
A sieve analysis is a practice or procedure used to assess the particle size distribution of granular particles. The size distribution is often of critical importance to the way the material performs in use. Here determination of quantitative size distribution of particles of dry sludge to fine grain fraction is done by following steps.Take a suitable quantity of oven dried dry sludge. The mass of dry sludge sample required for each test depends on the maximum size of material. Clean the sieve to be used and record the weight of each sieve and the pan .Arrange the sieves to have the largest mesh sire at the top of the stack Pour carefully the soil sample into the top sieve and place lid over it. Place the sieve stack on the mechanical shaker, screw down the lid, and vibrate the dry sludge sample for 10min.Remove the stack and re-weigh each sieve and the bottom pan with the soil sample fraction retained on it.Initial mass of soil sample taken for analysis (kg) = 1.000kg
Table 3.2 sieve analysis
Sieve no.
Sludge retained
% sludge retained
Cumulative% reatined
%finer
4.75mm
10
1
1
99
2 mm
248
24.8
25.8
74.2
1 mm
248
24.8
50.6
49.4
600
microns
122
12.2
62.8
37.2
300
microns
192
19.2
82
18
150
microns
158
15.8
97.8
2.2
75 microns
22
2.2
100
0
Sieve opening in mm= 1mm
Weight of soil retained=248 g Percentage retained = (248/1000) x10
=24.8
Cumulative percentage retained = 1+24.8+24.8
= 50.6
Percentage finer = 100-50.6 = 49.4 The results obtained are as follows: Effective size = 0.18
Uniformity coefficient = 7.22 Coefficient of curvature = 1.69 Percentage of gravel = 100-99 = 1% Percentage of silt and clay = 0%
According to IS specification for well graded soil uniformity coefficient should be more than 4 and coefficient of curvature should be between 1 & 3
-
Hydrometer analysis
In the wet mechanical analysis or sedimentation analysis, soil fraction finer than 75 microns size is kept in suspension in liquid medium. The method for determining grain size distribution of such soils are based on Stokes law. It define the rate of free fall of sphere through liquid.
Fig.3.1 Hydrometer
Dry weight of particles put in 1000 ml suspension =50g
Volume of hydrometer (cc) = 79.4c3 Test temperature = 31 degree Celsius
Cross section area of sedimentation jar= 29.412c2 Viscosity at test temperature = 7.205 × 105/c2
Composite correction, c =3
Specific gravity of soil, G =2.65 Area x height= volume
A = V/HT =100/3.4 = 29.412c2
He = 11cm t = 2 min = 120s
= 7.805 × 105/cm2
G= 2.65
Dmm = 1200he/((G1) t) = 0.0223 mm
R =24.67 cm
Wd =50 g
G =2.65
N=(GR×100)/(d(G1)) =79.24%
% Of silt (0.075-0.002) = 41%
% Of clay (< 0.002mm) =37%
ClAY
1.Specific gravity
SPG= 2.78
Determination no.
1
2
3
w1 g
679
679
679
w2 g
854
858
880
w3 g
1602
1600
1598
w4 g
1488
1490
1486
Specific gravity
,G
2.87
2.59
2.89
Table 3.3 specific gravity test
Flyash
1.Specific gravity
Only kerosene which is free o water shall be used. At time of weighing, the temperature of the apparatus will not be allowed to exceed the specified temperature.All air bubbles can be eliminated in filling the apparatus and inserting the stopper. Weighing shall be done quickly after filling the apparatus and shall be accurate to 0.1mg..Precaution shall be taken to prevent expansion and overflow of contents resulting from heat of hand when wiping the surface of the apparatus.
Weight of specific gravity bottle, W1 = 226g Weight of bottle + fly ash, W2 = 283 g
Weight of bottle + fly ash + kerosene, W3 =470g Weight of bottle + kerosene, W4 = 439 g
SPG = 2.19
-
-
MIX DESIGN
The mix design for the present study was taken from literature review.The details of materials are given below in table 3.4.
Table 3.4 mix design
% of sludge
Clay (%)
Flyash (%)
Glass powder(%)
20
8
15
0.4
40
14
15
0.8
60
24
15
1
-
BRICK MANUFACTURING
The first step involved in brick manufacturing is the drying of sludge.Then mixing of raw materials used in brick making.The raw materials are sludge,flyash,glasspowder and clay.and add sufficient amount of water to attain plasticity.After this brick is made to its shape and size by using mouldings.Then dry the brick in air for about 24 hours and for about 1 week the brick should be dryed in presence of sunlight.After drying,the brick should be fired in a kiln at 900 degree celsius .Then natural cooling is taking place after firing and the brick ready for testing.
Fig 3.2 Air dryed brick
Fig 3.3 Burned sludge brick
-
-
RESULTS AND DISCUSSIONS
To study the possibility of using sludge from water treatment plant in brick making, air dried sludge from industry was mixed thoroughly with soil in proportion of 20%,40% and 60% Water was added to these soil sludge mixes to produce a homogeneous paste having enough consistency to mould it into the brick shape by hand. Bricks were fabricated from these pastes using mould and soft extrusion technologies as carried out in the brick making industry. The bricks were air dried under shade and burnt at 900°C in muffle furnace. The burnt bricks, so obtained, were subjected to standard tests viz., efflorescence test, water absorption test and compressive strength test as per I.S: 3495-1976 (Part I to IV). Each test was conducted and noted its values.
-
Absorption test
To find the amount of moisture content on bricks.Bricks are taken and weighted Then immersed in water for 24 hrs Weighed the wet brick and noted down its values Difference between dry and wet brick weights gives the amount of water absorption.
Fig 3.4 Brick immersed in water for absorption test
Water absorption (in %) = ( w 2 w 1) / w1×100 Weight of dry brick, w1= 2460 g
Weight of water absorbed brick, w2 = 2815 g
= (28152460)/2460×100
= 14.4
Average water absorption (in%) = 14.4 %
addition of glass powder and flyash increased the strength of brick.
3.Hardness Test
A sharp tool or fingernail was used to make scratch on brick.Resisted scratches against sharp things.There is no scratch impression on brick then it is hard brick.
-
Compressive Strength
When bricks are used as masonry units, especially in load bearing structures, they are meant to carry loads.The load carrying capacity is determined by compressive strength.It
4.Efflorescence Test
Fig 3.6 Hardness testing
depends on composition,method of brick manufacturing and
degree of firing..Take required no.of specimens from each composition..Measure the dimension of the specimen nearest to 1 mm.Place the specimen with flat face horizontal..Place two plywood sheet each of 5mm .Carefully center between plates of testing machine.Apply load axially at uniform rate till failure occurs.Note maximum load at which the specimen fails.No further increase in indicator reading.on machine.
Fig 3.5 Compressive strength testing of brick
Size of brick = 20 x 10 x 10 Failure load (N/mm2) = 250 x 103 Length = 20 cm
Breadth= 10 cm Area = lxb = 20 x103
Compressive strength =12.5 N/mm2
Compressive strength of the bricks will be affected by the addition of sludge, glass powder. The addition of sludge into the brick will reduce the quantity of material by burning and
Efflorescence is caused by alkalies present in bricks. Place the end of bricks in dish,depth of immersion in water being 25mm. Place the arrangement in warm ventilated room until all water in dish is absorbed by specimen and surplus water evaporates. Cover the dish containing brick with suitable glass cylinder.When water has been absorbed and brick appears to be dry. Place similar quantity of water in dish and allow it to evaporate. Examine the bricks for efflorescence.
The efflorescence of the specimen bricks was of slight for all the studied mixtures of sludge, glass powder and fly ash.
V.CONCLUSION
This project will enable reuse of three waste products, making them assets without any new environmental hazards. In fact, there is also an additional environmental benefit in preserving the clay resource and less damage by excavation and quarrying and reduction in the cost of land rehabilitation.
Three tests were performed on specimen bricks which are its compressive strength,water absorption,efflorescence and test result has been compared with the conventional bricks available in market.Compression test shows that by the increase in proportion of sludge, glasspowder and flyash content increased the compressive strength.Then the result was satisfactory for 60% sludge,24% clay,15% flyash,1% glasspowder.The strength of brick is 12.5N/mm2 and it is of class A.The water absorption for the brick is 14.4%. As the % of sludge increased, light weight product us obtained.
WTP sludge can be successfully used in brick manufacture combined with agricultural and industrial waste materials, which contain high silica content. The results are limited to the study conditions such as mixing proportions, firing temperatures, and manufacturing methods used in this study. sludge , fly ash and glass powder harm the environment in number of ways. Such as fly ash causes pulmonary diseases and sludge causes sewage sickness of land and glass powder contribute to environmental stressors through continuous
recreation and plays a significant role in both air and water pollution and also kills wildlife when not recycled. Since this project utilizes use of wastes in making of Brick which is not harmful in nature. Hence environmentally feasible. Since it utilizes major waste materials and obtains a lightweight product it is also economically feasible.
REFERENCES
[1] Sandeep Yadav, Suyash Agnihotri, Shivam Gupta (2014) Incorporation of stp sludge and flyash in brick manufacturing Journal of advancement in research and technology, 138 ISSN 2278-7763. [2] G.Reddy Babu,N. Venkataramana (2013) Durability of bricks cast with industrial sludge IOSR journal of mechanical and civil engineering,Vol.6(4), [3] Anyokara Nkolika Victoria(2013) Characterisation and performance evaluation of water works sludge as brick material International journal of engineering and applied science,Vol.3(3). [4] A.Pappu,M Saxena,S.R.Asolekar (2007) Solid waste generation in india and their recycling potential in buiding material Journal of building and environment.Vol.-42,pp.2311-2320. [5] J.Alleman, N.Berman (1984) Constructive sludge management : biobrick ASCE.Vol.-110(2).. [6] R.Srinivasan,K.Sathiya, mM,Palanisamy (2010) Experiementalinvestigation in developing low cost concrete from paper industry sludge Buletinul institutuli polytehnic ,vol-53..
[7] N.Sudharsan ,(2020) Feasibilty of using waste glass powder in flyash bricks International journal of advanced engineering technology, e- issn 0976-3945.