
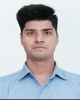
- Open Access
- Authors : Vishesh Bhatt , Gaurav Nakhat
- Paper ID : IJERTV10IS040079
- Volume & Issue : Volume 10, Issue 04 (April 2021)
- Published (First Online): 20-04-2021
- ISSN (Online) : 2278-0181
- Publisher Name : IJERT
- License:
This work is licensed under a Creative Commons Attribution 4.0 International License
Braking Calculation for a BAJA ATV
Vishesh Bhatt, Gaurav Nakhat
Amity School of Engineering & Technology
Abstract: An important factor in handling of every vehicle is its effective braking, making the vehicle easy and quick to stop with complete control of its essentials in the drivers hand. The safety being priority, braking values are computed using mathematical models. The evaluation is done by calculating the required braking torque and comparing it with the generated braking torque. This paper discusses the reverse calculation of the braking system and eventually calculates the required bore diameter of a caliper and hence apprise about most preferred caliper that should be used to have the most effective braking for a hydraulically operated braking system of a BAJA ATV. The related data is calculated and attained to extract average values for different design parameters to make the theoretical calculations as realistic as possible.
Index Terms: Braking system, Disc brakes, Calipers, Weight Transfer, Hydraulic braking, Pascals Law.
-
INTRODUCTION
This document gives a brief introduction to braking system and provides a calculation methodology to calculate and determine the rightful braking calipers for a BAJA ATV vehicle, to be stopped within a specified distance running at a specified speed.
The braking system is an essential device of a vehicle used to retard the vehicles speed and provide control over its motion. It enables the driver to press the pedal and control speed by decelerating the vehicle. Hence, enabling the driver to have a good control over the vehicles dynamics.
The braking system works on the principle of energy conservation converting the kinetic energy of the rotating disk in to heat energy, produced due to friction force between the pads and the disk. The frictional force produced by the pads on the disc all together should be enough to counter the rotation of the disc and bring it to stationary i.e.; to lock the tire within a specified distance. The force of compression on the brake pads are generated with the help of fluid pressure generated as a result of the force from the foot brake pedal.
The braking assembly and components are restricted with space complication of a compact BAJA vehicle, where all the components and assembly needs to be accommodated in a sound and functional manner without restraining any other component or the driver or any of its motion.
A passel of calculations hence need to be done in order to achieve the goal to lock the tires within the given distance keeping all the constraints in account.
-
BRAKING SYSTEM
-
Introduction to Braking System
The aim of the braking system is to provide a reliable and easy to operate system capable of locking the wheels, and provide continuous control over vehicles speed in all terrain.
The braking system consists of following components:
-
Master Cylinder:
It is a device comprising of two chambers, one chamber is the reservoir containing Brake fluid, which is the working fluid in the braking system and is responsible for compensating any fluid curtail in the brake lines or due to leakage, though rubber seals are used for preventing leakages. The other chamber of the master cylinder is the compression chamber, responsible for retaining pressure in the brake lines even when the brakes are released. As the pedal is pressed, the plunger connected to the pedal moves in opposing the piston return springs force to push the piston inside, creating a pressure in the fluid by pressing the fluid present inside the brake line. Eventually creating high pressure inside the calipers leading to compression of brake pads with very high force.
-
Brake Calipers:
It is an assembly consisting of brake pads and pistons. Basically there are two types of calipers floating type and fixed type.
In the Baja vehicle a fixed type brake caliper is used. A fluid inlet allows high pressure brake fluid to flow inside, creating a pressure inside the cylinder pushing the piston and the brake pads attached to it, eventually creating a high compression force pressing the brake pads against the rotor resulting in decreasing its speed or to stop the rotor.
-
Brake Rotor:
-
The brake rotor also known as the brake disc has an integral function of retarding of the wheel, by applying the braking torque on the wheel.
Disc brakes are widely used in the industry as they are better than drum brakes in heat dissipation and cooling down. The rotor is clamped in between the brake pads and they tolerate the compressive forces, from the caliper.
The major parameter that decides the size of the rotor is the size of the rim. In the current BAJA buggy as assumed for the discussion, the rims used are of 10 inch diameter, hence, after considering the clearances and mountings of the caliper, it was concluded that the diameter of the rotor to be made would be of 6 inches.
The material of the rotor selected is EN 34 due to its high corrosion resistivity and optimum heat dissipation.
-
Brake Pedal:
The brake and accelerator pedal are so designed and placed according to the spaces available after the respective clearances.
The pedals should be placed in a way that the driver should not face any hindrance in pressing them with full comfort.
The master cylinder should be placed such that it is well protected inside the roll cage.
The length of the brake pedal is decided according to the required ratio. A significant consideration while deciding the length of the pedal is the compact nature of the buggy, the area around the pedal is less, which is also covered by the steering column and the steering rack which is shielded hence consuming more space.
Therefore, the pedal should have an appropriate length according to the ratio required and should be mounted for unhindered swinging.
-
-
BRAKE CALCULATION
-
Introduction
The following calculations lay the foundation of selecting the rightful caliper for a BAJA vehicle to achieve precise braking and perfect handling of the vehicle. According to the BAJA specification the vehicle should come to a complete stall condition from a speed of 40km/hr or 11.11m/s, within a distance of 4.5m. The input parameters including the dimensions and specification of the vehicle are mentioned in Table I.
The rate of retardation (artd) can be calculated using the Third Equation of Motion (1). Taking the initial velocity u as 11 m/s, the final velocity v as 0 m/s, and the distance s as 4.5m within which the vehicle is tend to be stopped from a speed of 11 m/s.
v2 u2 = 2*a*s (1)
In (1) the acceleration term (a) will be replaced by the retardation (artd), and so the value of retardation using the (1) will be,
artd. = (11.11)2 / (2 * 4.5)
= 13.7146 m/s2
When the driver press the brake pedal, some pedal force (Fp) which on multiplication with the pedal ratio, act as an input to generate force inside the master cylinder (Fmc), this force causes to produced pressure on the braking fluid (Pbf) of the braking system. In (2) the force applied by the driver on the pedal (Fp) is taken as 300N and considering all the space constraints and drivers ease, the pedal is designed in a way to have a pedal ratio of 6 and so the force generated can be calculated as,
Fmc = Fp * pedal ratio (2)
= 300 * 6
= 1800 N
TABLE I INPUT PARAMETERS
Sr. No.
Value
Unit
1
Track Width
1.2192
m
2
Wheelbase
1.3716
m
3
Total Weight (including Drivers weight)
2109.15
N
4
Total mass (including drivers mass)
215
Kg
5
Height of C.G
0.4064
m
6
Diameter of Tyre (same for front and rear)
0.5842
m
7
Effective Brake Rotor Diameter
Front
0.12065
m
Rear
0.1905
m
8
Distance of Centre of Gravity
From front tyres centre
0.7112
m
From rear tyres centre
0.6604
m
9
Master cylinder bore diameter
0.015
m
10
Pedal Ratio
6.01
–
-
General Calculations
For the ATV moving at a speed of 40km/hr or 11.11 m/s and coming to a complete stop within a distance of 4.5 m.
This force generates pressure on the braking fluid inside the master cylinder, this pressure is transferred in the entire brake line to the calipers to hold and stall the wheels. The pressure generated in the brake line can be calculated as,
Pbf = Fmc / Abore (3)
= 1800 / (( * (0.015)2)/4) Pbf = 10191082.8025 Pa
In (3) the radius of the master cylinder outlet bore is taken as 0.015m and thus the area of the master cylinders outlet port (Abore) is calculated.
Please note, the area of the outlet port of the master cylinder is equivalent to the area of the brake line, thus the pressure on the brake fluid inside the brake line is taken equivalent to the value calculate through (3). For a different bore area of brake line and the outlet port, the pressure inside the brake line would be different and needs to be calculated for further calculations.
-
Static Load Calculations
The load or force applied on the ground by the vehicle due to its weight while being at static condition is calculated in order to understand the weight distribution of the vehicle and to further choose the braking calipers accordingly.
Fig.1 Force Distribution in the Vehicle
As shown in Fig.1 the weight of the Vehicle is divided into 2 parts, on the front axle tyres (Ff) and the rear axle tyres (Fr), and can be calculated using the Third law of Motion, for the vehicle mass (m) of 215 kg, using the following equation,
Ff + Fr = mg (4)
Now to calculate the force on the Rear axle wheels, we need to take moment about Ff, for a wheelbase (wb) of 1.3716 m and distance of Centre of Gravity from front tyre (x) of 0.7112 m,
Fr * wb = mg * x (5)
Fr = mg * x / wb
Fr = 215 * 9.81 * 0.7112 / 1.3716 Fr = 1093.6333 N
Fbr = (DFr mass * artd )/2 (10)
= (47.77 * 13.7146) /2
Fbr = 327.5732 N
F. Calculation for the Bore Diameter of calipers piston The calipers available in the market are differentiated on the basis of number of pistons and the bore diameter of each piston. If the required bore diameter is known it will become convenient to select the caliper to fulfill our requirements and to stop the vehicle in the required distance. The braking force (Fbf or Fbr) applied is used to produce braking torque (b) which acts on the wheels to stop the vehicle. In order to calculate the bore diameter is is necessary to calculate the braking torque required. So for a wheel radius (Rw) of 0.2921m, the braking torque (b) is calculated as;
For Front wheel,
Now using (3) the static load on the front tyres can also be calculated as,
Ff + Fr = mg (6)
Ff + 1093.63 = 2109.15
Ff = 1015.52 N
-
Dynamic Load Calculations
Dynamic loading condition of the wheels is examined in order to understand the actual load acting on the wheels at the time of braking, at the time of braking when the rotors are retarded or locked, the mass at the centre tends to move forward, thus adding a positive impact on the front load and reducing the load at the rear wheels. This depends upon the height of the point of centre of gravity (h), the static axle loading (Ff or Fr) and the wheel base (wb). The dynamic load (DFf) can be calculated for front wheels as,
DFf = Ff + (h mg) / wb (7)
= 1015.52 + (0.4064*2109.15)/1.3716
DFf = 1640.453 N
DFf mass = 167.22 Kg
And for the rear wheels the dynamic loading (DFr) is calculated as,
DFr = Fr – (h mg) / wb (8)
= 1093.633 (0.4064*2109.15)/1.3716
DFr = 468.696 N
DFr mass = 47.77 Kg
-
Brake Force Calculation
The brake force is the required force that the caliper needs to generate in order to lock the wheels or retard the vehicle in a desired manner to achieve the stopping goal. As already seen the dynamic loads on the rear and front wheels are different, so the brake forces are also different for each sets of wheels. Thus this force required on each wheel is calculated using the Second Law of Motion. The braking force at each front wheel (Fbf) can be calculated as,
Fbf = (DFf mass * artd )/2 (9)
= (167.22 * 13.7146) /2
Fbf = 1146.677 N
Similarly the brake force at each rear wheel (Fbr) can be calculated as,
bf = Fbf * Rw (11)
bf = 1146.677 * 0.2921
bf = 334.944 Nm
Similarly for Rear Wheel,
br = Fbr * Rw (12)
br = 327.5732 * 0.2921
br = 95.684 Nm
The braking torque applied on the wheel is equally applied on the braking rotor which is directly mounted on the wheels. Thus the braking force on the rotor (Fbrf or Fbrr) generated as a result of force applied by the piston (Fpf) via brake pads on the Braking rotor radius (Rrf or Rrr) can be calculated as;
For front wheel,
Fbrf = b / Rrf (13)
= 334.944 / 0.060325
= 5552.3249 N
For rear wheel,
Fbrr = b / Rrr (14)
= 334.944 / 0.09525
= 3516.4724 N
The braking force on the rotor (Fbrf or Fbrr) is applied by the brake calipers piston via brake pads. The force applied by the piston is equal to coefficient of friction (µr = 0.35) between the brake pad and the brake rotor multiplied by twice the force applied by the piston. Twice as floating caliper is considered in this case or a caliper with two operational braking pads is considered in this case. The force applied by each piston (Fpf or Fpr) can be calculated as, For front caliper,
Fbrf = 2Fpf * µr (15)
So, Fpf = Fbrf / (2* µr)
Fpf = 7931.8927 N
For rear caliper,
Fbrr = 2Fpr * µr (16)
So, Fpr = Fbrr / (2* µr)
Fpr = 5023.532 N
The bore of the caliper (df or dr) is calculated using the Pressure formula,
For front wheel,
2
2
Pbf = Fpf / Af piston = Fpf / ( * df / 4) (17)
So, df = 0.0314878 m
df = 31.4878 mm 31.5 mm
Similarly, for rear wheel,
2
2
Pbr = Fpr / Ar piston = Fpr / ( * dr / 4) (18)
So, dr = 0.025058 m
dr = 25.058 mm 25 mm
G. Brake Selection
The effective diameter of the piston of a brake caliper is calculated in the fore mentioned calculations. Thus a caliper of the calculated piston diameter is required for a circular operating piston caliper. However, it is not necessary that the calculated diameters piston caliper will be available in the mrket, thus, the area using the calculated diameter is to be calculated. This calculated area should be equal to the total effective area of n number of pistons of a caliper.
-
-
CONCLUSION
This paper presents the methodology to calculate for the selection of braking calipers for a BAJA ATV. The calculation process considered all the masses acting at the wheels and thus on the brakes both in static and dynamic conditions.
REFERENCES
-
Thomas D. Gillespie, Fundamentals of Vehicle Dynamics, Society of Automobile Engineers, Inc. 1992, pp. 45-57.
-
Kirpal Singh, Automobile Engineering Vol.1 , 14th ed., vol. 1Standard Publishers Distributors, 2017, pp.333-344.
AUTHORS PROFILE
Vishesh Bhatt, received B.Tech degree from Amity School of Engineering & Technology, Delhi, India, in 2019. He is currently working in the R&D department of a two wheeler manufacturer in India. His area of work includes 2 Wheeler components development and validation.
Gaurav Nakhat, currently in the final year of his B.Tech degree program from Amity School of Engineering & Technology, Delhi, India. He is an active member in the colleges Automobile society taking part in SAE BAJA India competition.