
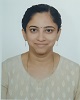
- Open Access
- Authors : L. P. Usha Sri , Col T A Aravind
- Paper ID : IJERTV9IS030467
- Volume & Issue : Volume 09, Issue 03 (March 2020)
- Published (First Online): 03-04-2020
- ISSN (Online) : 2278-0181
- Publisher Name : IJERT
- License:
This work is licensed under a Creative Commons Attribution 4.0 International License
Bio-Mechatronic Hand with SCP Actuator Muscle
Col T A Aravind
Dean, Faculty of Degree Engineering MCEME
Secunderabad, India
Mrs. L. P. Usha Sri
Assistant Professor, Faculty of Degree Engineering MCEME
Secunderabad, India
Abstract An Artificial hand is said to be the one which is capable of fulfilling all the necessary functionalities of a human hand. It can be wearable by the user which means that it can be perceived as part of the natural body and should replicate sensory-motor capabilities of the natural hand. However such an ideal Bionic prosthetics is still far from reality. This paper attempts a design and fabrication of a noble artificial hand based on a bio-mechatronic and cybernetic approach. The paper is aimed at providing natural sensory-motor co- ordination, by integrating bio-mimetic mechanism, force and position sensors, actuators and control and by interfacing the hand with the peripheral nervous system. This idea can be designed and fabricated as a first-hand prototype and aimed at increasing the grasping force of the hand while retaining the main positive characteristic of previous designs. The new hand architecture value will be based on under actuated mechanism comprising of DC Motor and Super coiled Polymer. The hand will have around 9 independent degree of freedom and aim to generate a grasping force of about 30 N. Commercially available prosthetic devices such as Otto Bock sensor hand as well as multifunctional hand designs are far from providing the grasping abilities of the human hand.
Keywords Bio-Mechatronic, Super Coiled Polymer, Robotics, Artificial muscle, Arduino, Electro Myography
-
INTRODUCTION
The field of Robotics is growing fast, in order to make the human life more efficient and easy.[19] There are various machines or robots designed for this purpose. The purpose of the field of robotics is served on the day it is successful in replacing the limbs and parts of human body. The real challenge lies in connecting artificial limbs to human brain. The robots thus manufactured in this particular field has to help the handicapped people facing problems like blindness, broken legs or arms, body part dislocation etc. A vast number of people today have disability issues due to misfortunes like accidents, war, natural calamity etc etc., Currently there are different technologies which give physically challenged people, the ability to move around and help them do their day to day tasks without the help of others. Apart from this category, there are number of people who are fully handicapped or have full-body paralysis , while their mind still work properly. The field of robotics comes to the rescue in such situations. This paper presents a novel design of a prosthetic hand which is controlled by human brain. This paper deals with the design and development of a Bio Mechatronic hand which is controlled by Electromyography(EMG) signals produced by the brain and measured at the forearm.[3] This paper presents a new way to
design and develop a Robotic Arm which will be controlled by human beings Muscle EMG waves[1]. Super Coiled Polymer(SCP) Actuator helps to provide the necessary control and flexibility for the hand. It has super coiled Nylon threads which acts like nerves in the human body very thin but highly efficient in carrying control signals from controller and the actuator. It acts like Artificial muscle which provides strength and also a vital connection between the individual parts. The design aspects were developed initially using CAD CAM. The design was later developed using a 3D printer so that robotic arm can be fitted on a handicap person comfortably.
-
ASPECTS IN DESIGNING A BIO-MECHATRONIC DEVICE
-
Motion Analysis and Mechanical Parameters of a human hand
The maximum velocity at which the closing and opening of finger is calculated by recording the maximum velocity at which human fingers could open and close[2]. The motion of each finger was considered and video uploaded in Tracker, which is a free video analysis and modelling tool. Position-time graphs for both the x and y axes were generated and analysed, The angular velocity and the revolutions per minute (rpm) were calculated using the following formulae:
Vmax= = rpm
. Motor is used to provide the necessary torque and power to move the fingers. To calculate the torque and power that the motor would have to supply in order to move the fingers, the maximum force that a finger could either exert or sustain was determined. The force was determined by hanging mass from fingers until it could no longer lift them. Force is derived from mass and acceleration due to gravity whereas Power is derived from Torque and Angular velocity. To increase the accuracy of the results, weighing scale was used, each finger was pushed down and Force was calculated. The following tabular column shows the result of the analysis. The data table for velocity, torque, power and force are given as TABLE I and TABLE II.To ensure that the robotic hand can sustain the forces it will potentially be subjected to, the materials it is made of should be strong enough. This means that the motors and actuators used must provide enough power and torque, but it also means that the plastic piece involved should be hard enough to hold together. Super
coiled polymers are chosen to sustain the necessary stress and strain. The stress involved with the robotic hands fingers are essentially of two types: compressional and shear. When the finger is horizontal, shear stress is at its maximum[4]. When the finger is vertical, compression stress is greatest. Therefore, the maximum stress occurs when the finger is at a 45 degree angle[22], where both types of stress are involved. The calculations on stress on each finger and at 45 degrees are individually calculated and summarized in TABLE III and TABLE IV.[14] [15]
-
Super Coiled Polymer
Super coiled polymers are built by combining nylon lines or nanotube threads or carbon nanotube yarns together to provide strength to the actuator part.[17]
TABLE I
DATA TABLE OF VELOCITY
Finger
Vxmax(m/s)
Vymax(m/s)
Vmax (m/s)
Radius (m)
(rad/s)
Rpm
Thumb
0.00527
0.0360
0.0364
0.116
0.314
3.00
Index
0.0608
0.124
0.138
0,0963
1.484
14.2
Middle
0.0626
0.0744
0.0972
0.107
0.908
8.67
Ring
0.0467
0.140
0.148
0.0631
2.35
22.4
Little
0.166
0.133
0.213
0.0811
2.63
25.11
TABLE II
DATA TABLE OF FORCE, TORQUE AND POWER
Finger
Force (N)
Radius (m)
Torque (Nm)
(rad/s)
Power (W)
Thumb
30
0.116
3.48
0.314
1.09
Index
25
0.0963
2.41
1.484
3.58
Middle
22
0.107
2.35
0.908
2.13
Ring
15
0.0631
0.947
2.35
2.23
Little
12
0.0811
0.973
2.63
2.56
TABLE III STRESS ON EACH FINGER
Finger
Area (sq.m)
Force (N)
Comp. stress (N/sq.m)
Shear stress (N/sq.m)
Thumb
0.0000531
30
56. 497
56 .497
Index
0.0000491
25
50. 916
50 .916
Middle
0.0000346
22
63 .583
63. 583
Ring
0.0000346
15
43. 352
43 .352
Little
0.0000284
12
42 .253
42 .253
TABLE IV
STRESS ON EACH FINGER AT 45 DEGREES[22]
Finger
Area (sq.m)
Force (N)
Comp.stress (N/sq.m)
Shear stress (N/sq.m)
Thumb
0.0000531
30
39 .949
39 .949
Index
0.0000491
25
36. 003
36 .003
Middle
0.0000346
22
44 .960
44 .960
Ring
0.0000346
15
30 .654
30 .654
Little
0.0000284
12
29 .877
29. 877
Polymer fibres are made up of flexible polymer chains. These chains are oriented in fiber direction. They are forced into helical configuration by twisting. Because of this
structure, high strength motions like bending and torsional motions can be realized easily.[12] With the help of a motor actuator, these polymers acts like artificial muscles to the robotic hand. Depending on the force required for the purpose, thicker SCP actuator or bundles or multiple actuators can be used in parallel[5].
-
Electromyography (EMG)
Electromyography (EMG) is a technique used to analyse muscles and nerves. It works by measuring small electrical signals generated in the muscles when they are in action, like moving a finger, clenching a fist, or lifting an arm.[13] This signals originate in the brain and travels through the muscles with the help of nerves. They produce action potential in the end. Action potential occurs due to chemical exchange between potassium and sodium ions.[6] They are usually detected in 0- 500 Hz range.
-
-
PROPOSED ARCHITECTURE
The design proposed in this paper involves using Myoware muscle sensor which is basically an EMG sensor which is Arduino compatible.[7][16] The design has two main circuits Transmitter Circuit and Receiver Circuit.
Fig.1. Transmitter Circuit
Fig.2. Receiver Circuit
The hardware part of the bionic arm is made with the help of 3D printing technology.[8] The most important part of 3D printing is using the right material for the design. Strength, Flexibility, Accuracy are the important parameters considered while going for 3D printing. The skeleton or the frame of the arm is designed using AutoCAD. Acrylonitrile butadiene
styrene (ABS) and Poly Lactic Acid (PLA) are used for printing. ABS is among the most common materials used. ABS is a very strong plastic and can be procured from non- proprietary sources also. PLA is a biodegradable material, which can be used in resin form for Digital Light Processing (DLP) and Stereo lithography. Movement of wrist and finger joints will be controlled by SCP connected to the servo motors (torque capacity 600gcm) fitted on the arm. For elbow movement, a linear actuator is used.
-
RESULTS
The arm is a Ultra-Torque Metal Gear which has 35kgcm Coreless Standard Servo Motors attached to it, as shown in fig 3. It consists of 36 individual 3D printed components. Its operating voltage is 6V to 8.4V, with the operating temperature range of -10°C to 50°C[23]. The bionic arm offers six degrees of freedom.[9] It can be controlled using myoelectric signals or through a joystick. The thumb, index finger and middle fingers can move independently whereas the ring finger and small finger move in tandem.[10] The elbow has 110o bending flexibility and wrist has 180o rotational freedom. EMG electrodes are placed either on the forearm or bicep of the user. The device is portable and has a battery life of more that 200 minutes. TABLE V gives the electrical specifications used for the design of current prototype and TABLE VI gives a few of the system properties.
TABLE V ELECTRICAL SPECIFICATIONS
Electrical Specifications:
7.2V
8.4V
Operating speed (at no load)
0.13sec/ 60°
0.10sec/60°
Running current (at no load)
250mA
300mA
Stall torque (at lock)
31kg.cm
35kg.cm
Stall current (at lock)
3.2A
3.5A
Idle current (at stopped)
4mA
5mA
TABLE VI SYSTEM PROPERTIES
System Weight
1.5 Kg
Tendons
Braided Tennis Gutting
Power Source
AC 230V, AC to DC &
DC to DC Converter
Microcontroller
Atmega 328,Atmega 2560
EMG Sensors
Muscle Sensor Kit V3
ServoVoltage Regulators
AP1117 5V output, maximum current 1A
Fig.3. 3D Printed frame of Bionic Arm
The fingers are able to move in a relatively smooth and natural way. Its fluidity in motion is dependent on many factors including friction between moving plastic components, servo control and the tendons. The fingers opens and closes exceptionally well. The movement of elbow is fair, as it is done through linear actuator. The servo controlling the wrist movement is also fairly good. The fingers are able to provide at least 300g of force each.[11] By increasing the speed of servo motors, bearing force on each finger can be increased. The limiting factor in finger force is not the torque of the servo motors but rather the strength of the printed 3D components. The 2- Axis joystick allows wrist rotation and elbow movement. It was possible to instruct the hand to close, rotate to a certain position, rotate back and then reopen. Proportional control of the fingers works through flexing the joint. However, this proportional control caused the fingers to start shaking when trying to close. This was due to noisy signals being used to control servo positions. AC supply was used to work most of the components. AC to DC converter is used to convert 230 Volt to 12 Volt. DC to DC converter was used to get the required voltage of various other parts, as shown in Fig 4
Fig.4. Bio Mechatronic Arm
-
CONCLUSION
In this paper, a design process for a novel 3D Bionic Arm which also uses SCP as artificial muscle, has been presented. The ultimate aim was to develop a low cost Bio Mechanical device with multiple degrees of freedom and multi-sensing capabilities, which is also low weight and noiseless in nature. The purpose has been served to a certain extent but still can be impoved in many aspects. One of the biggest limitation of this device is its lack of pressure feedback. Pressure sensors can be incorporated along with Advanced EMG Algorithms and processing. With future growth of the 3D printing industry, many advanced and robust prosthetic devices can be designed. This paper is just a small step towards developing nature-like devices which are controlled by human brain and can successfully replace a missing limb of an individual.
REFERENCES
-
P. Agnew, Functional effectiveness of a myoelectric prosthesis compared with a functional split hook prosthesis: a single subject experiment, Prost. & Orth. Int. 5 (1981), 9296.
-
S.-E. Baek, S.-H. Lee, J.-H. Chang, Design and control of robotic finger for prosthetic hands, Proc. Int. Conf .Intelligent Robots and Systems (1999), 113-117.
-
M. E. Cupo, S. J. Sheredos, Clinical Evaluation of a new, above elbow, body powered prosthetic arm: a final report, J.Rehab. Res. Dev. 35 (1998), 431-446.
-
R. Doshi, C. Yeh, M. LeBlanc, The design and development of a gloveless endoskeletal prosthetic hand, J. Rehab. Res. Dev.35 (1998), 388395.
-
Belter, Joseph T,M.S., B.S., J. L. Segil, Dollar, Aaron M, PhD, S.M., B.S. and R. F. Weir PhD. Mechanical design and performance specifications of anthropomorphic prosthetic hands: A review. Journal of Rehabilitation Research and Development 50(5), pp. 599-618. 2013.
-
D. H. Silcox, M. D. Rooks, R. R. Vogel, L. L. Fleming, Myoelectric Prostheses, J. Bone & Joint Surg., 75 (1993),1781 1789.
-
R. Vinet, Y. Lozach, N. Beaundry, G. Drouin, Design methodology for a multifunctional hand prosthesis, J. Rehab. Res. Dev. 32 (1995), 316324.
-
M. R. Cutkosky, Robotic Grasping and Fine Manipulation, Boston: Kluwer Academic Publishers, 1985.
-
Ashutosh Gupta, Emg Signal Analysis of Healthy and Neuropathic Individuals
-
A. G. Erdman, G. N. Sandor, Mechanism design. Prentice Hall International, Inc. Third edition (1997)
-
M. T. Mason, J. K. Salisbury, Robot hands and the mechanics of manipulation, Cambridge, MA: MIT Press, 1985.
-
WALKER, Jearl, 2014. Fundamentals of Physics, 10th Edition, Danvers, MA: John Wiley and Sons, 1368 p.
-
Dr. Scott Day. Important factors in Surface EMG measurement. Bortec Biomedical Ltd
. htm, 2015.
[15]. Wikimediafoundation .Stress(mechanics).http://en.wikipedia.org/wiki/stress_ (mechanics), 5 February 2015.
[16]. Arduino. Arduino reference. http://arduino.cc/en/reference/homepage, 2015Cabrillo. Tracker help. https://www.cabrillo.edu/~dbrown/tracker/help/frameset.html, 2015
-
Jun Zhang, Jun Sheng, Ciaran oneill, conor J.Walsh, Robert J.Wood, Jee-Hwan, Jaydev P.Desai, Michael c.Yip,
Robotic Artificial Muscles: Current Progress and Future Perspectives, IEEE Transaction, 2019
-
https://www.semanticscholar.org/paper/A-%E2%80%9C- Wearable-%E2%80%9D-Artificial-Hand-for-Prosthetics-and- Carrozza- Massa/3db3114a9bd4317d906c7e0edbe15192860da318
-
http://seminarabstracts1.blogspot.com/2007/10/120biomechatronic s.html
-
www.researchgate.net/publication/220806919_Design_and_Experi ments_on_a_Novel_Biomechatronic_Hand
-
http://www.journalijdr.com/oum-v01-mind-controlled-robotic- arm
-
https://www.vaniercollege.qc.ca/student-research- centre/files/2015/03/Biomech_final_report.pdf
-
https://robokits.co.in/motors/rc-servo-motors/ultra-torque-metal- gear-35kgcm-coreless-standard-servo-motor
-
www.academia.edu/39599212/3D_Printed_Myoelectric_Prostheti c_Arm_3D_Printed_Myoelectric_Prosthetic_Arm_i
-
Bio Mechatronic arm, Proj by Deg Students, Fac of Deg Engg, MCEME