
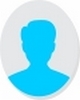
- Open Access
- Authors : Avinash N Bhat , Ashoka G U , Ajay H R
- Paper ID : IJERTV10IS060149
- Volume & Issue : Volume 10, Issue 06 (June 2021)
- Published (First Online): 19-06-2021
- ISSN (Online) : 2278-0181
- Publisher Name : IJERT
- License:
This work is licensed under a Creative Commons Attribution 4.0 International License
Autonomous Robot with Microcontroller for Plant Health Condition Analysis
Avinash N Bhat1, Ashoka G U2, Ajay H R3
1Research Scholar, Dept. of Mechanical Engineering, Bapuji Institute of Engineering and Technology, Karnataka, India
2Research Scholar, Dept. of Mechanical Engineering, Malnad College of Engineering, Karnataka, India
3Research Scholar, Dept. of Mechanical Engineering, Sri Venkateshwara College of Engineering, Karnataka, India
Abstract – India is an agricultural country and most of the people are farmers. Farmers are cultivating different types of crop. These crops affected by fungi, bacteria, viruses and many more. Identification of disease is very difficult for farmers at its early stage. There are number of diseases found in crop. Farmers cannot be determining accurate percentage of observed disease. Patterns of diseases are so many complexes that finding affected area is difficult. It is very difficult to monitor the plant diseases manually. It requires tremendous amount of work, expertise in the plan diseases, and also require the excessive processing time. Hence, image processing is used for the detection of plant diseases. Disease detection involves the steps like moving robot mannerly for image acquisition, image pre-processing, image segmentation, feature extraction and classification. [1, 2,3]
A vision-based row guidance method is presented to guide a robot platform which is designed independently to drive through the row crops in a field according to the design concept of open architecture. Then, the offset and heading angle of the robot platform are detected in real time to guide the platform on the basis of recognition of a crop row using machine vision. Essentially the aim of this project is creating a farming automation which is able to work on line following principle which indicates the plant health by observing color of their leaves. The automation will note encompassing environmental conditions like temperature, humidity, wetness etc, and it'll be displayed on alphanumeric display, in order that automation can decide health of the plant.
Here we are designing autonomous intelligent farming robot which indicates the plant health by observing the color of their leaves in terms of image processing which is done by raspberry pi and some limitation to plant height. The robot also notes the surrounding environmental conditions of the plant in terms of temperature and humidity so that the robot will decide about health of plat and will display on the LCD [4, 5]. The proposed system prototype is implemented by selecting arenas which considering agricultural field of any kind of crop.
Key Words: Open Architecture, Environmental Conditions, Health.
-
INTRODUCTION
Robot is a machine especially one programmable by a computer capable of carrying out a complex series of actions automatically. Robotics can be described as the current pinnacle of technical development. Robotics is a confluence science using the continuing advancements of mechanical engineering, material science, sensor fabrication, manufacturing techniques and advanced algorithm. The study and practice of robotics will expose a dabbler or professional to hundreds of different avenues of study. A journey of lifetime awaits in robotics. Robotics can be defined as the science or study of the technology primarily associated with the design, fabrication, theory, and application of robots. Crafters and researchers in robotics study more than just robotics. In
summary, robotics is the field related to science and technology primarily related to robotics. It stands tall by standing the accomplishments of many other fields of study.
The term comes from Czech word, robota, meaning forced labor ; the word root was first used to denote a fictional humanoid in earth 1920 by Karel Capek but it was Karels brother Josef Capek who was the words true inventor electronics evolved into the driving force of development with the advent of the first electronic autonomous robot created by William Grey Walter in Bristol, England in 1948.The first commercial, digital and programmable robot was built by George Devol in1954 and was named the Unimate. It was sold to general motors in 1961 where it was used to lift pieces of hot metal from die-casting.
1.1 AGRICULTURAL APPLICATION
From the start of human, humans are worked in the farms directly but from the start of 21st century many industries are worked to reduce this human labor by making robots and machines. Many industries developed machines for the specific task like picking, harvesting, weeding, pruning, planting, grafting, agricultural classification, etc. And they gradually appear advantages in agricultural production to increase productivity, improve application accuracy and enhance handling safety.
Robots are increasingly being used to sort, grade, package and even pick fruit and vegetables. For example, an autonomous wheeled robot has been developed to pick orange from orange-farm using vision to identify both fruit quality and as a means of navigation,onion harvesting machine is also been developed, corn picking machine and finally tomato plucking machine.
In this project, we are going to make a robot which uses vision based row guidance method to drive through the row crops. Ultimately, a unique system has been described for Plant & Food Research which makes use of a number of electrical and computer systems engineering theories. A prototype robotic arm has to be designed, developed and constructed, which should be integrated with motors, controllable using specific electronic components and custom computer software. A number of sensors are integrated into the robotic system including colour, proximity, temperature and humidity systems. The system required the use of vision, with custom algorithms being developed to identify plant growth rates. The entire system will have integrated into a fully automated package. This allowed the system to autonomously return to specified sites (i.e. individual plantlets) at set time intervals to identify subtle changes in growth rates and leaf colour. This provided the potential for plant nutrient levels and
the immediate environment to be routinely adjusted in response to continuous sensing resulting in optimized rapid growth with minimal human input. [6]
Leaf diseases on plant are the main element and having superior strength which appear as spots on the leaves. In case of severe infection, the leaf becomes completely covered by disease in terms of spots. Different type of leaf diseases on plant determines the quality, quantity, and stability of yield.
Figure 1.1: Leaf minor disease
Leaf miners are the larval stage of an insect family that feeds between the upper as well as lower part of leaves are heavily diseased and damaged due to insect on large amount in plants. It is common to find 6 or more maggots per leaf. So these heavily damage of leaf of plant can restrict plant growth, leads to reduced yields and loss of vigour, healthy plants can tolerate considerable injury.
Figure 1.2: Yellow spot disease
Pesticide use in plant diseases treatment increases the proportion of toxic level on agricultural products leads to a major contribution to ground water pollution or making water much more hazardous, also large amount of pesticide use leads to increase in production cost. This can be done by identifying the severity of disease and target the diseases places, with the diseases in plant not only reduce the yield but also making progressively worse condition of plant. Increase in appropriate quantity and concentratio of pesticide. The normal observation is generally used to decide diseases severity in the production practice but results are subjective and its impossible to measure the disease severity. As one of the trends of development on automation in coming days is that all kinds of agricultural robots have been researched and developed to perform number of task like harvesting, weeding, pruning, planting, grafting, agricultural classification, etc. They gradually appear advantages in agricultural production. Thus the improved accuracy on implementing this method in various sector and enhance handling safety.
-
LITRATURE REVIEW
-
Sanjukumar et. al. (2013) : The Soil moisture content based irrigation system was developed and successfully implemented along with flow sensor. Salient features of the system are: Closed loop automatic irrigation system, temperature and water usage monitoring. User can easily preset the levels of the Moisture and is regularly updated about current value of all Parameters on LCD display. In future, other important soil parameters namely soil pH, soil electrical conductivity will also be incorporated in the system.
-
Swarup et al (2013) : Smart sensors based monitoring system for agriculture have been used to increase the yield of plants by monitoring the environmental conditions (parameters) and thus providing the necessary information to the clients (farmers). The proposed system is mainly developed for the betterment of farmers. The use wireless sensor network over the wired one helps for deploying it in any type of environment for monitoring, making it flexible and robust. The use of FPGA element facilitates the system for Re-configurability and re- programmability according to different environmental conditions.
-
Gholap et al (2014): A system with high speed of operation for an advanced agriculture process which includes cultivation based on robotic platform. The robotic system is an electromechanical (conveys a sense that it has agency of its own) and artificial agent which is steered by DC motor which has four wheels. The farm is cultivated by the machine, depending on the crop considering particular rows & specific columns. The infrared sensor detects the obstacles in the path and it also senses turning position of vehicle at end of land. The seed block can be detected and solved using water pressure. The machine can be controlled remotely and solar panel is used to charge DC battery. Assembly language is used in programming the microcontrollers. The microcontroller is used to control and monitor the process of system motion of vehicle with the help of DC motor.
-
Kirankumar et al (2015) : The project would be considering an area where any of the crops that are grown, and finds a solution for a an agricultural system by different deployment techniques, the device will successfully help in growth of a plant by monitoring temperature, pesticides, humidity without human interference, these device can be implemented an in a half acre of land as a prototype model, the device if implemented in a large scale the overall cost can be brought down that is demonstrated using qualnet simulator. This device will go over the years, as sensors usually has large durability with frequent replace in batteries
-
Heldi et al (2014) : The objective of the study is to develop a system for monitoring the temperature in the greenhouse by placing multiple temperature sensors at several observation positions. The proposed system allows more representative and comprehensive observations for conducting an analysis of the temperature changes using wireless communication. In addition the temperature in greenhouse can be monitored optimally.
-
METHODOLOGY
Problem Identification & Research
Assessing the working principle
Conceptual Design
Material Selection & Fabrication of Chassis
Circuit Connection and Programming
Fig.4.2: Design of Chassis frame in CATIA
Field Testing of Robot
Conclusion
-
EXPERIMENTAL INVESTIGATION
-
The research processes of the Autonomous Robot for Plant Health detection are as follows:
-
It all started with a spark of an idea which we developed when discussing about the current problems related to agriculture. We first designed initial models in 2d to have a basic knowledge on how we could get into 3d models.
-
After the initial concept we properly designed the model using CATIA with near to the actual dimensions on how we wanted it to be. The design helped us understand the limitations which we were gonna face while fabricating. We planned the design and came into a conclusion that the robot should be able to enter in congested places and also be able detect plants which are grown in peculiar places.
Fig.4.1: Design of Chassis frame in CATIA
Fig.4.3: Design of Chassis frame in CATIA
-
Material selection before the fabrication was difficult part as we needed to concentrate on the weight of the complete device. So, we used aluminum frame which was sturdy enough to withstand any damage and also be able to get the work done without adding more weight.
ALUMINIUM EXTRUSION ROD: 2020 T Slot
Aluminum extrusion profiles are easier and faster to build assemblies. It is made up of Aluminum, is exactly 20x20mm square and has slots on all four sides. We can use T-nuts that slide into the slots to connect plates. Aluminum profile can be easily cut down with a hacksaw blade or Band-saw and assembled with some nuts, screws and plates to build a frame, then finish off with end-caps. Aluminium is a very light metal with a specific weight of 2.7 g/cm3 , about a third that of steel. Aluminium naturally generates a protective oxide coating and is highly corrosion resistant. Different types of surface treatment such as anodising, painting or lacquering can further improve this property. Aluminium is 100 percent recyclable with no downgrading of its qualities. The remelting of aluminium requires little energy: only about 5 percent of the energy required to produce the primary metal initially is needed in the recycling process.
ACRYLIC PLASTIC : Acrylics are polymers of Methyl Methacrylate (PMMA). Acrylic can be optically clear or cloudy, as in the case of impact modified Acrylics.
It is formable With a little heat, it's easy to shape and mould. Durable where it withstands Impact resistance all the time. Weatherable, Stands up to the elements longer than other plastic. Advantages of using the same are below
Excellent optical clarity, Excellent weatherability and resistance to sunlight, Rigid, with good impact strength
,Excellent dimensional stability and low mould shrinkage & Stretch forming increases bi-axial toughness Because of all
these excellent feature we are using Acrylic Plastic Sheets in order to cover Electronic Circuit and also for finishing purpose.
Fig.4.4: Acrylic plastic sheet
-
For the arm movement we used lead screw which acts as power screw. A lead screw also known as a power screw or translation screw is a screw used as a linkage in a machine, to translate turning motion into linear motion. Because of the large area of sliding contact between their male and female members, screw threads have larger frictional energy losses compared to other linkages. They are not typically used to carry high power, but more for intermittent use in low power actuator and positioner mechanisms.
Following Lead Screws are being used: 2 M10 300mm, 1 M10 250mm & 1 M10 420mm.
Fig.4.5: Lead Screw
GUIDE ROD: Guide rods Provides key performance benefits such as high load capacities, high speeds, and design compatibility. They are well suited for long travel applications, minimizing vibration and providing smooth and quiet travel over joined shafts. Following Guide Rods are being used: 4 D10 420mm, 2 D10 340mm & 1 D10 280mm.
Fig.4.6: Guide Rods
BARING (SCS10uu): SCS10uu bearing A bearing is a device that is used to enable rotational or linear movement, while reducing friction and handling stress. Resembling wheels, bearings literally enable devices to roll, which reduces the friction between the surface of the bearing and the surface it's rolling over. Specification: 7 SCS10uu 10mm(Dia).
Fig.4.7: SCS10uu Bearing
6. Final assembly of the robot was done and after all the connections we took it for test run to check all the joints were properly screwed and the battery connections was done correctly. There was some trail and error here and finally we were able to achieve what we wanted. The wheels were of plastic hence it needed some traction to travel in mud and sand. Hence we added rubber tyres to all the wheels and it was able to climb small to minor inclined surfaces without any issues.
Fig.4.8: Final Assembly 1
Fig.4.9: Final Assembly 2
-
Software requirements are as follows:-
Programming language: Embedded C Language
Proteus Design Software: The Proteus Design Suite is a software tool suite used for electronic design automation even only software itself the output can be checked by the software and also electronic prints for manufacturing printed circuit boards.
Fig.4.10: Programming in EMBEDDED-C
Fig.4.11: Programmed for Pattern Motion
-
Implementation of Plant Health Detection.
The robots are made which observe the leaf color based on RGB color standard and also investigates the chlorophyll a and Lipid contents to investigate the plant health. For this purpose, many color sensors and image processing technology is used. Automated farming robot required all system on robot, for that Raspberry Pi and PIC controller are used to perform robotic operation.
Fig.4.11: Block diagram of the system
5. TESTING
Figure 5.1: Humidity Output
-
Graph shows the humidity sensor readings at respective time period. X-axis shows the time (in minutes) and Y-axis represents Humidity (in %) from sensor. At the area of testing, humidity is varying between 43.5% to 45% during particular period time is recorded.
Figure 5.2 Moisture Output
-
Graph shows the moisture sensor readings at respective time period. X-axis shows the time (in minutes) and Y-axis represents Moisture (in %) from sensor. At the area of testing, moisture content of soil is readings during particular period time is recorded.
6. Weed cutting can be done easily by adding the ultrasonic sensor to calculate the distance and by changing it to cutting tool it can be cut.
Hence, there are many more applications in future with the multi-purpose chassis that we have designed and fabricated.
Figure 5.3: Temperature Output
-
Graph shows the temperature sensor readings at respective time period. X-axis shows the time (in minutes) and Y-axis represents temperature (in ) from sensor. At the area of testing, temperature readings during particular period time is recorded.
Figure 5.4: CO2 Output
Graph shows the Gas sensor (CO2) sensor readings at respective time period. X-axis shows the time (in minutes) and Y-axis represents CO2 (in ppm) from sensor. At the area of testing, CO2 readings during particular period time is recorded.
6. CONCLUSION AND FUTURE SCOPE
In the agriculture and horticulture sector there is a requirement of time, power and water management. Based on this main point of view we design the robot which will help in this point. Also for the farmer safety point of view it is perfect. By using this system, we can manage the time; also save the water and pesticide using sensing unit.
As the design of the robot is with the aluminum extrusion, alteration of the sizes is simple. And as we have used the three axis arm for the tool placement it would actually give precision for distances in the working volume of the robot.
Since the tool is replaceable it has lot of advantages such as
-
With the change of the tool it is possible to add a new feature and that can be a new project.
-
By changing the wheels and replacing by rack and pinion that would help the robot for line following in green house.
-
We can either add the extrusions for different dimension or can even be reduced for small plants.
-
We can use the tool as weed cutter, seeding crop tool, watering tool, pesticides tool, etc.
-
As in crop seeding we can also have many patters as required in the field by programming it in the required way.
-
7. FEATURES AND APPLICATIONS
-
Fully automated system thus reduces the human labor.
-
As we are making a fully autonomous robot which works on open architecture principle and done lot of work in farms so it reduces human labour. Saves time.
-
As we are using machines which works faster than human efforts which definitely saves the time.
-
More Accuracy.
-
The system observes different environmental conditions and take actions accordingly which humans cant do accurately.
-
Low Cost.
-
We are using sensors and drivers for making this system which are easily available in market and cheap which reduces the cost of system.
-
This system will provide surveillance on plant health.
-
For an infected plant, thus system will provide us the accurate knowledge about whether or not to carry on the cutting of plant leaves.
APPLICATIONS:
-
This system will provide surveillance on plant health.
-
It will have constant knowledge about moisture content in the soil.
-
The system also informs us at which time the amputating must be done.
-
It can be used for watering.
-
It also indicates the height of plant growth.
-
It continuously shows the surrounding temperature of plant.
-
This robot detects which disease the plant had undergone.
-
7. REFERENCES
-
Autonomous Farming Robot with Plant Health Indication using Image Processing by Prof. R.K. Moze, Nitin Gawade et al. (IJIRWEICE Volume 4 Issue 04 April 2016).
-
Intelligent Autonomous Farming Robot with Plant Disease Detection using Image Processing by D A Shaikh, Ghorale Akshay G et al. (IJARCCE Volume 5, Issue 04 April 2016).
-
Intelligent Farming Robot with Plant Health Detection using Image Processing and Sensing device by Wable A. A , Khapre G. P et al. (IJESE Volume 6, Issue 07,2016).
-
Autonomous Farming Robot with Plant Health Indication by Dhanasekar J, Sengottuvel P et al. (IJPAM Volume116, Issue 20, 2017).
-
Autonomous Farming Robot with Plant Health Indication by Madan Veer, Akash Chavan et al. (NCACIT 2016).
-
Autonomous Farming Robot with Plant Health Indication by Prof.Dr. Saurabh Mehta, Neha D. Kherade et al.(IJAERD Volume 4, Issue 03, March 2017).
-
Autonomous Farming Robot with Plant Health Indication by Prof. K.P.Fale, Bhure Amit P et al. (IJATES Volume 3,Issue 01, January 2015).