
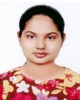
- Open Access
- Authors : Maria S Sebastian , Thahzin Rasha V R
- Paper ID : IJERTV10IS080082
- Volume & Issue : Volume 10, Issue 08 (August 2021)
- Published (First Online): 20-08-2021
- ISSN (Online) : 2278-0181
- Publisher Name : IJERT
- License:
This work is licensed under a Creative Commons Attribution 4.0 International License
An Investigation on Geopolymer Concrete with GGBFS and Fly Ash
Maria S Sebastian, Thahzin Rasha V R Students, Civil Engineering Department Sahrdaya College of Engineering and Technology Thrissur, India
AbstractThe conventional concrete used for the construction of large structures releases greenhouse gases leading to ozone layer depletion and global warming. An alternative solution to conventional concrete has been sought by many researchers. Geopolymer concrete is the one in which cement in conventional concrete is replaced by mineral admixtures such as fly ash, GGBFS, metakaolin, micro silica etc and chemical solutions acting together as a binder. In this paper, geopolymer concrete is made using ground granulated blast furnace slag (GGBFS) and fly ash in alkaline solutions (sodium silicate and sodium hydroxide) is compared with conventional concrete. The strength parameters investigated are (i) 7 days compressive strength (ii) 28 days compressive strength (iii) 28 days split tensile strength (iv) 28 days flexural strength. Workability and cost analysis of different cases of geopolymer concrete is also investigated.
KeywordsGeopolymer concrete; micro silica; ground granulated blast furnace slag; fly ash; alkaline solution
-
INTRODUCTION
The climatic change owing to global warming is a grave environmental dilemma having significant pessimistic impacts on all living beings of the world. The discharges of greenhouse gases such as CO2, methane, nitrous oxide, chlorofluorocarbons, hydrofluorocarbons, etc. from diverse sources into the atmosphere are accountable for this critical impasse. One such cause of the release of primary greenhouse gas – CO2 is the present production process for Ordinary Portland Cement (OPC). It was revealed that the world production of OPC had contributed almost 57% of the total CO2 emission into the ambience. Estimation is assessed that the production of one ton of OPC is answerable to the almost equal quantity of discharge of CO2 into the atmosphere. For the year 2014, the global utilization of OPC in the world was
3.7 billion metric tons. Likewise, one ton of cement production releases one ton of carbon dioxide into the atmosphere and consumes almost 4GJ of energy. This is a severe hazard to humanity across the world. Therefore, research efforts towards the search for eco-friendlier materials for construction are going on.[2] The present production process of OPC is not merely high temperature and highly energy-intensive for which it needs to swallow restricted natural coal resources for calcination of limestone but also a solemn threat to The environment. Hence, it is also a need of the hour to search for an alternative of conventional OPC- concrete which should be user and eco-friendly and can be developed by conserving natural resources at low temperature and a cost of merely slim energy and of course, cost-effective. Moreover, the conventional fine and coarse ingredients of
OPC concrete are also mined from limited natural resources hence the researches are essential for a type of concrete that can be developed by incorporating natural and industrial wastes to lower down environmental concerns.
Geopolymer is a novel inorganic binder produced by the polymerisation reaction between source materials (having higher silica and alumina content) of geological origin and alkaline solution in highly alkaline conditions at low temperatures and atmospheric pressure. Geopolymer concrete demonstrates excellent properties of resistance against sulphate, chloride, and acid attacks. In comparison with regular Portland cement concrete, it has strong prospective applications in the encapsulation of toxic solid waste and heavy metals. It functions as fire-resistant as it shows excellent high-temperature stability.
-
Polymerization
Polymerization is a procedure of responding monomer particles together in a substance response to shape polymer chains or three-dimensional systems. In substance mixes, polymerization happens through an assortment of response instruments that change in multifaceted nature because of practical gatherings introduce in responding compounds and their inalienable steric impacts. Polymerization, any procedure in which generally little particles, called monomers, consolidate chemically to deliver a vast chainlike or system atom, called a polymer. As a rule, no less than 100 monomer atoms must be consolidated to make an item that has certain remarkable physical properties, for example, versatility, high rigidity, or the capacity to frame filaments that separate polymers from substances made out of littler and easier particles frequently, a large number of monomer units are joined in a single molecule of a polymer.
-
Aim and Scope
The project aims to find a replacement for cement as cement manufacturing is one of the major contributors to air pollution. Cement industries release greenhouse gases into the atmosphere which causes global warming and other environmental problems. Industrial dust like fly ash, metakaolin, micro silica and GGBFS can be used to replace cement in concrete. This reduces the harmful industrial solid waste released into the environment and promotes sustainable development. The project helps to find out the constructions for which concrete can be replaced by geopolymer concrete depending on the workability and cost.
-
Fly Ash
-
-
MATERIALS
response since need enough initiations potential. In this way, its constantly utilized without withstanding sodium hydroxide to improve the alkalinity quality of examples. Along these
Fly ash is produced from the combustion of coal in electric utility or industrial boilers. There are four basic types of coal- fired boilers: pulverized coal (PC), stoker-fired or travelling grate, cyclone, and fluidized-bed combustion (FBC) boilers. The PC boiler is the most widely used, especially for large electric generating units. The other boilers are more common at industrial or cogeneration facilities. Fly ashes produced by FBC boilers are not considered in this document. Fly ash is captured from the flue gases using electrostatic precipitators (ESP) or in filter fabric collectors, commonly referred to as baghouses. The physical and chemical characteristics of fly ash vary among combustion methods, coal sources, and particle shape.[4]
-
Ground Granulated Blast Furnace Slag
Granulated Blast Furnace Slag is obtained by rapidly chilling (quenching) the molten ash from the furnace with the help of water. During this process, the slag gets fragmented and transformed into amorphous granules (glass), meeting the requirement of IS 12089:1987 (manufacturing specification for granulated slag used in Portland Slag Cement). The granulated slag is ground to desired fineness for producing GGBFS. It ensures higher durability of the structure and reduces the temperature rise and helps to avoid early-age thermal cracking and also improve workability. It is off-white and substantially lighter than Portland cement. Resultantly, it helps soften the visual impact of large structures such as bridges and retaining walls. [3]
-
Sodium Hydroxide
The most widely recognized soluble base activator utilized in the Geopolymer concrete is NaOH. As an activator, NaOH isn't that dynamic that as KOH particle. In any case, the particle of NaOH are small in size and accordingly, they can infiltrate inside the system with a simple exertion. Likewise, NaOH particles have a thickness of extremely high charge which offers extra zeolitic development vitality. The properties of the resultant glue f geopolymer concrete are liable to the centralization of NaOH arrangement. While framing folio high concentration of NaOH may help in synthetic disintegration however it opposes the development of ettringite and CH (carbon-hydrogen) bond. It has likewise been concentrated by the analysts that the high convergence of NaOH may give higher quality at early ages however for the matured examples it was discovered that the solid had poor morphology and non- consistency because of exorbitant OH particles. One of the upsides of utilizing NaOH as an activator is that the resultant Geopolymer concrete is increasingly crystalline and along these lines has more prominent soundness in unforgiving situations, for example, impervious to sulphates and acids.
-
Sodium Silicate
The point when at a high temperature of about 1100°C or more, sand is melded with sodium carbonate than Sodium silicate is shaped. A result of the above response is broken up with the high weight steam & semi-thick fluid is framed which are known as the water glass. The Sodium Silicate in its physical state can be found beneath. A Sodium silicate/water glass alone can't be utilized as an activator to start pozzolanic
lines, NaOH & Na2SiO3 are the most regular salt activator utilized in the Geopolymer solid creation. Financially, sodium silicates can be found in various evaluations and states, for example, powder structures/ fluid structures, however fluid structure has progressively propensities to start response. It is found from the overview that Na2SiO3 having SiO2 to Na2O mass proportion of 2.0 blended with NaOH activator 24 hours preceding use offers better outcomes.
-
-
SPECIFIC GRAVITY
Specific gravity is the ratio of the weight of the volume of any material to the weight of the water of the same volume at a certain temperature. Specific gravity is a value to calculate whether a material will sink or float in water. Each material has some specific gravity. Specific gravity is calculated to know the behaviour of the material and it usually ranges from 0.1 to
-
Specific gravity test is carried out for binder materials like cement, fly ash, GGBFS, micro silica etc using a specific gravity bottle.[4]
Specific gravity is given by the following equation:
(W2 W1) / (W2-W1) – (W3-W4) x 0.79 (1)
where,
W1 = Weight of bottle with stopper
W2 = Weight of bottle with stopper + Weight of material
W3 = Weight of bottle with stopper + Weight of material + Weight of kerosene
W4 = Weight of bottle with stopper + Weight of kerosene
-
Observation
-
Cement:
W1 = 30 g W2 = 45 g W3 = 83 g W4 = 70 g
Specific gravity = (45 30) / (45 -30) – (83-70) x 0.79
= 3.15
-
Fly Ash:
W1 = 30 g W2 = 38 g W3 = 76 g W4 = 70 g
Specific gravity = (38 30) / (38 -30) – (76-70) x 0.79
= 2.45
-
Ground granulated blast furnace slag:
-
-
W1 = 30 g W2 = 42 g W3 = 80 g W4 = 70 g
Specific gravity = (42 30) / (42 -30) – (80-70) x 0.79
= 2.92
-
-
MIX DESIGN
-
Mix Design for Conventional Concrete
The mix design of the geopolymer concrete is done in an entirely different manner compared to that of conventional concrete. In this project, the mix design of the geopolymer concrete is prepared.
-
Materials replacing cement: Quantity and fineness of material used to replace cement-like fly ash, GGBFS and micro-silica plays an important role in the activation process of geopolymer. It was already pointed out that the strength of geopolymer concrete increases with an increase in the quantity and fineness of the material. Similarly, higher fineness shows higher workability and strength with an early duration of heating in the case of fly ash. So, the main emphasis is given on the quantity and fineness of fly ash in the development of the mix proportioning procedure of geopolymer concrete.[6]
-
Alkaline activators: In the project, sodium-based alkaline activators are used. The combination of sodium hydroxide and sodium silicate solutions are used for the activation of geopolymer concrete. It is observed that the compressive strength of geopolymer concrete increases with an increase in the concentration of sodium hydroxide solution and or sodium silicate solution with increased viscosity of the fresh mix. An increase in the concentration of sodium hydroxide solution in terms of molarity (M) makes the concrete more brittle with increased compressive strength. Secondly, the cost of sodium hydroxide solid is high and preparation is very caustic. Similarly, to achieve the desired degree of workability, extra water is required which ultimately reduce the concentration of sodium hydroxide solution. So, the concentration of sodium hydroxide was maintained at 10 M while the concentration of sodium silicate solution (10 M) contains Na2O of 16.37 %, SiO2 of 34.35 % and H2O of 49.72
% is used as alkaline solutions.
-
Water: Water comes out from the mix during the polymerization process. The role of water in the geopolymer mix is to make workable concrete in a plastic state and do not contribute towards the strength in the hardened state. Similarly, the demand for water increases with an increase in the fineness of source material for the same degree of workability. So, the minimum quantity of water required to achieve the desired workability is selected based on the degree of workability, fineness of source material and grading of fine aggregate.
-
Aggregates: Aggregates are inert mineral materials used as filler in concrete which occupies 7085 % volume. So, in the preparation of geopolymer concrete, fine and coarse aggregates are mixed in such a way that it gives the least voids in the concrete mass. This was done by grading fine aggregate and selecting a suitable fine-to-total aggregate ratio. The workability of geopolymer concrete is also affected by the grading of fine aggregate similar to cement concrete.
-
Water to geopolymer binder ratio: Water-to- geopolymer binder ratio The ratio of total water (i.e. water present in solution and extra water if required) to the material involved in the polymerization process (i.e. fly ash and sodium silicate and sodium hydroxide solutions) plays an important role in the activation process.
-
Solution to fly ash ratio: As solution (i.e. sodium silicate + sodium hydroxide) to fly ash ratio increases, strength is also increased. But the rate of gain of strength is not much
significant beyond the solution to fly ash ratio of 0.35. Similarly, the mix was more and more viscous with higher ratios and unit cost also increases. So, in the present mix design method, the solution-to-fly ash ratio was maintained at 0.35.
-
Preparation of geopolymer concrete mixes: The preparation of geopolymer concrete is similar to that of cement concrete. Two types of coarse aggregates 12 mm and 20 mm, fine sand and source material (fly ash, GGBFS, micro silica) were mixed in the dry state. Then add prepared mixture solution of sodium hydroxide and sodium silicate along with extra water-based on water-to-geopolymer binder ratio and mix thoroughly for 34 min to give a homogeneous mix.
-
Six concrete cubes of side 150 mm, two cylinders of 300 mm height and 150 mm diameter and one beam of 100 mm x 100 mm x 500 mm are cast in three layers for each case. Each layer is well compacted by a tamping rod of diameter 12 mm. After compaction of concrete, the top surface was levelled by using a trowel. After 24 h of casting, all cubes were unmoulded and then placed at room temperature for curing. Fly ash geopolymer concrete is kept in an oven for thermal curing (heating) at 60o C. To avoid the sudden variation in temperature, the concrete cubes were allowed to cool down up to room temperature in an oven.
TABLE I. QUANTITIES WORKED OUT
Material
Quantit per meter cube
Source material for replacing cement
405.92 kg/m3
Fine sand
551.11 kg/m3
Coarse aggregate ( 12 mm )
1015.7 kg/m3
Coarse aggregate ( 20 mm )
276.74 kg/m3
Sodium silicate solution
100.75 kg/m3
Sodium hydroxide solution
40.89 kg/m3
Additional water
20 kg/m3
Sodium silicate concentration
10 M
Sodium hydroxide solution
10 M
( Sodium silicate + sodium hydroxide solution ) / Source material content
0.35
Total water content including solution / Source material
0.40
Sodium hydroxide solution / Sodium silicate solution
0.40
The geopolymer concrete in this project is prepared by using the ratio 1: 1.3: 3.1.[4]
-
-
CASES INVESTIGATED
28 days split tensile strength test, 28 days flexural tensile strength test and 7 and 28 days compressive strength test has to be conducted for all the trials. Therefore 3 cubes for 7 days, 3 cubes for 28 days, 2 cylinders for 28 days and 1 beam for 28 days are required. There are 9 specimens to be cast for each case. The volume of concrete to be prepared for each case is as follows;
Volume of 6 cubes = 6 x 0.150 x 0.150 x 0.150
= 0.02025 m3
Volume of 2 cylinders = 2 x x 0.075 x 0.075 x 0.300
= 0.0105975 m3
Volume of 1 cube = 1 x 0.010 x 0.010 x 0.050
= 0.005 m3
Total volume = 0.036 m3
Considering extra 2 % total volume = 0.03672 m3
-
Case 1:
Ordinary concrete
Cement = 405.92 kg/m3
Fine aggregate = 551.11 kg/m3 Coarse aggregate (12 mm) = 1015.7 kg/m3 Coarse aggregate (20 mm) = 276.74 kg/m3 Water = 160 kg/m3
Water cement ratio = 0.39
-
Case 2:
100 % replacement of cement by fly ash
Fly ash = 405.92 kg/m3
Sodium silicate solution = 100.75 kg/m3 Sodium hydroxide solution = 40.89 kg/m3 Fine aggregate = 551.11 kg/m3 Coarse aggregate (12 mm) = 1015.7 kg/m3 Coarse aggregate (20 mm) = 276.74 kg/m3 Water = 20 kg/m3
-
Case 3:
100 % replacement of cement by GGBFS
GGBFS = 405.92 kg/m3
Sodium silicate solution = 100.75 kg/m3 Sodium hydroxide solution = 40.89 kg/m3 Fine aggregate = 551.11 kg/m3 Coarse aggregate (12 mm) = 1015.7 kg/m3 Coarse aggregate (20 mm) = 276.74 kg/m3 Water = 20 kg/m3
VI EXPERIMENTATION
-
Workability
The slump test is carried out to determine the workability of concrete where the nominal maximum size of the aggregate does not exceed 38 mm. This test is used at a construction sites all over the world. It gives the idea of the water-cement ratio to be used for different works. Fresh unsupported concrete flows to the sides and the sinking in height takes place. The vertical settlement is known as a slump and is measured when supporting mould is removed. Concrete is said to be workable if it can be easily mixed, compacted and easily finished.
Slump Value:
Slump value indicates workability in the following manner.
-
0 25 mm slump:
Indicates low workability suitable for mass reinforcement
-
25 75 mm slump:
Indicates medium workability suitable for RCC work with less reinforcement.
-
75 150 mm slump:
Indicates high workability suitable for RCC work with heavy reinforcement.
Slump Cone:
The mould for the test specimen shall be in the form of a frustum of a cone having the following internal dimensions.
-
Bottom diameter (d1) = 200 mm
-
Top diameter (d2) = 100 mm
-
Height (h) = 300 mm Observations:
TABLE II. SLUMP VALUE OF THE DIFFERENT CASES
Sl. no.
Description of the case
Initial height of the slump (cm)
Final height of the slump (cm)
Slump Value (cm)
1
Normal concrete
30
27
3
2
100% Fly ash
30
23
7
3
100% GGBFS
30
25.5
4.5
Inference:
All the geopolymer concrete cases above have medium workability suitable for RCC work with less reinforcement.
-
-
-
Tests Conducted
-
Compressive strength test:
Compressive strength test is conducted at 7 days and 28 days in CTM (compression testing machine) on 150mm x 150mm x150mm size cubes.
Load /Area =P/A (2)
-
Split tensile strength test:
Split tensile strength is conducted at 28 days on 300mm long and 150 mm diameter cylinders in a compression testing machine(CTM). Split tensile strength is calculated using the given formula:
2P DL (3)
where,
P is the load
L is the length of the cylinder and D is the diameter of the cylinder.
-
Flexural strength test:
Flexural strength is conducted on a beam of depth 100 mm, width 100 mm and length 500 mm in ultimate tensile strength testing machine (UTM). Flexural tensile strength test is given by the following formula
(f) = ( M x y) / I (4)
M = (P x l )/4 (5)
I = (b x d3)/12 (6)
y = d/2 (7)
where,
M is the bending moment f is the bending stress
I is the moment of inertia
y is the distance to the extreme fibre P is the load
d is the depth of the beam b is the width of the beam
l is the total length of the beam
-
-
Results
-
Case 1: Normal Concrete
TABLE III. 7 DAYS COMPRESSIVE STRENGTH TEST
Sl.
No.
7 days compressive strength
Load (N)
Strength (N/mm2)
1
350 x 103
15.55
2
370 x 103
16.44
3
370 x 103
16.44
Average 7 days compressive strength = (15.55 + 16.44 + 16.44) / 3 = 16.14 N/mm2
TABLE IV. 28 DAYS COMPRESSIVE STRENGTH TEST
Sl.
No.
28 days compressive strength
Load (N)
Strength (N/mm2)
1
385 x 103
17.11
2
380 x 103
16.88
3
380 x 103
16.88
Average 28 days compressive strength = (17.11 + 16.88 + 16.88) / 3 = 16.96 N/mm2
TABLE V. 28 DAYS SPLIT TENSILE STRENGTH TEST
Sl.
No.
28 days split tensile strength
Load (N)
Strength (N/mm2)
1
455 x 103
6.51
2
460 x 103
6.44
Average 28 days split tensile strength = (6.51 + 6.44) / 2 = 6.47 N/mm2
TABLE VI. 28 DAYS FLEXURAL STRENGTH TEST
Sl.
No.
28 days flexural tensile strength
Load (N)
Strength (N/mm2)
1
10 x 103
7.5
M = (P x l) /4 = (10 x 103 x 500) /4 = 1250000 N mm
y = 100 / 2 = 50 mm
I = (b x d3) /12 = (100 x 1003) /12 = 8333333.33 mm4
28 days flexural strength (f) = (M x y) / I
<>= (1250000 x 50) / 8333333.33 = 7.5 N/mm2
-
Case 2: 100% Fly Ash Replacement of Cement
TABLE VII. 7 DAYS COMPRESSIVE STRENGTH TEST
Sl.
No.
7 days compressive strength
Load (N)
Strength (N/mm2)
1
310 x 103
13.77
2
310 x 103
13.77
3
310 x 103
13.77
Average 7 days compressive strength = (13.77 + 13.77 + 13.77) / 3 = 13.77 N/mm2
TABLE VIII. 28 DAYS COMPRESSIVE STRENGTH TEST
Sl.
No.
28 days compressive strength
Load (N)
Strength (N/mm2)
1
460 x 103
20.44
2
460 x 103
20.44
3
455 x 103
20.22
Average 28 days compressive strength = (20.44 + 20.44 + 20.22) / 3 = 20.37 N/mm2
TABLE IX. 28 DAYS SPLIT TENSILE STRENGTH TEST
Sl.
No.
28 days split tensile strength
Load (N)
Strength (N/mm2)
1
210 x 103
2.97
2
220 x 103
3.11
Average 28 days split tensile strength = (2.97 + 3.11) / 2 = 6.47 N/mm2
TABLE X. 28 DAYS FLEXURAL STRENGTH TEST
Sl.
No.
28 days flexural tensile strength
Load (N)
Strength (N/mm2)
1
5 x 103
3.75
M = (P x l) /4 = (5 x 103 x 500 )/4 = 625000 N mm
y = 100 / 2 = 50 mm
I = (b x d3) /12 = (100 x 1003) /12 = 8333333.33 mm4
28 days flexural strength (f) = (M x y) / I
= (625000 x 50) / 8333333.33 = 3.75 N/mm2
-
Case 3: 100% GGBFS Replacement of Cement
-
TABLE XI. 7 DAYS COMPRESSIVE STRENGTH TEST
Sl. No. |
7 days compressive strength |
|
Load (N) |
Strength (N/mm2) |
|
1 |
840 x 103 |
37.33 |
2 |
870 x 103 |
38.66 |
3 |
830 x 103 |
36.88 |
Average 7 days compressive strength = (37.33 + 38.66 + 36.88) / 3 = 37.63 N/mm2
TABLE XII. 28 DAYS COMPRESSIVE STRENGTH TEST
Sl. No. |
28 days compressive strength |
|
Load (N) |
Strength (N/mm2) |
|
1 |
950 x 103 |
42.22 |
2 |
960 x 103 |
42.66 |
3 |
980 x 103 |
43.55 |
Average 28 days compressive strength = (42.22 + 42.66 + 43.55) / 3 = 42.81 N/mm2
TABLE XIII. 28 DAYS SPLIT TENSILE STRENGTH TEST
Sl. No. |
28 days split tensile strength |
|
Load (N) |
Strength (N/mm2) |
|
1 |
750 x 103 |
10.61 |
2 |
760 x 103 |
10.75 |
Average 28 days split tensile strength = (10.61 + 10.75) / 2 =
10.68 N/mm2
TABLE XIV. 28 DAYS FLEXURAL STRENGTH TEST
Sl. No. |
28 days flexural tensile strength |
|
Load (N) |
Strength (N/mm2) |
|
1 |
15 x 103 |
11.25 |
M = (P x l) /4 = (10 x 103 x 500)/4 = 1875000 N mm
y = 100 / 2 = 50 mm
I = (b x d3) /12 = (100 x 1003) /12 = 8333333.33 mm4
28 days flexural strength (f) = (M x y) / I
= (1875000 x 50) / 8333333.33 = 11.25 N/mm2
VII COST ANALYSIS
Cost analysis is a summary of all the costs involved in doing particular work or unit work. In this project, case 1 (conventional concrete), case 2 (100% Fly ash) and case 3 (100% GGBFS) are cast. The mix design for M30 geopolymer concrete was derived and obtained a mix ratio of 1:1.3:3.1. NaOH solution (10 M) and Na2SiO3 solution (50.32%) are required in case 2 and case 3 for the polymerization reaction. Quantities of the materials required for 1 m3 in all the cases and their rates are required for the cost analysis. Cost of cement, fine aggregate and coarse aggregate (12mm and 20mm) are obtained from the Schedule of Rates 2012: Volume 1.[5] The rates of the materials like NaOH, Na2SiO3, GGBFS and fly ash etc are obtained from the commercial market value.
TABLE XV. COST OF MATERIALS
Sl. No. |
Material |
Rate (Rs.) |
Per |
1 |
Fine aggregate |
616 |
Cum |
2 |
Coarse aggregate (20 mm) |
942 |
Cum |
3 |
Coarse aggregate (12 mm) |
962 |
Cum |
4 |
Cement |
5940 |
Tonne |
5 |
GGBFS |
1950 |
Tonne |
6 |
Fly ash |
1700 |
Tonne |
7 |
Sodium hydroxide flakes |
28 |
Kg |
8 |
Sodium silicate solution |
8 |
Kg |
TABLE XVI. COST PER m3 OF CONCRETE
Sl. No. |
Cases |
Cost per m3 of concrete |
1 |
Conventional concrete |
3453.50 |
2 |
100% Fly ash |
2991.90 |
3 |
100% GGBFS |
3094.40 |
Experiments |
Results |
||
Case 1 |
Case 2 |
Case 3 |
|
7 days compressive strength test (N/mm2) |
16.14 |
13.77 |
37.63 |
28 days compressive strength test (N/mm2) |
16.96 |
20.22 |
42.81 |
28 days split tensile strength test (N/mm2) |
6.47 |
3.04 |
10.68 |
28 days flexural strength test (N/mm2) |
7.5 |
3.75 |
11.25 |
Workability (mm) |
30 |
70 |
45 |
Cost (Rs.) |
3453.5 |
2991.9 |
3094.4 |
Experiments |
Results |
||
Case 1 |
Case 2 |
Case 3 |
|
7 days compressive strength test (N/mm2) |
16.14 |
13.77 |
37.63 |
28 days compressive strength test (N/mm2) |
16.96 |
20.22 |
42.81 |
28 days split tensile strength test (N/mm2) |
6.47 |
3.04 |
10.68 |
28 days flexural strength test (N/mm2) |
3.75 |
11.25 |
|
Workability (mm) |
30 |
70 |
45 |
Cost (Rs.) |
3453.5 |
2991.9 |
3094.4 |
-
GRAPHICAL RESPRESENTATION OF RESULTS TABLE XVII. RESULTS
Specific gravity of materials
3.15
3.5
3
2.5
2
1.5
1
0.5
0
2.92
Specific gravity of materials
3.15
3.5
3
2.5
2
1.5
1
0.5
0
2.92
Cement
Flyash
Materials
GGBFS
Cement
Flyash
Materials
GGBFS
2.45
2.45
Workability
Workability
Specific Gravity
Specific Gravity
Fig 1. Graph showing specific gravity of materials
Workability – Slump in mm
70
80
70
60
50
40
30
20
10
0
45
Workability – Slump in mm
70
80
70
60
50
40
30
20
10
0
45
Conventional concrete
100 % flyash
Cases
100% GGBFS
Conventional concrete
100 % flyash
Cases
100% GGBFS
30
30
Fig 2. Graph showing workability
7 days compressive strength
7 days compressive strength
40
35
30
25
20
15
10
5
0
37.63
40
35
30
25
20
15
10
5
0
37.63
Conventional concrete
100 % flyash
Cases
100% GGBFS
Conventional concrete
100 % flyash
Cases
100% GGBFS
16.14
16.14
13.77
13.77
Strength
Strength
Fig 3. Graph showing 7 days compressive strength
Strength
Strength
Fig 4. Graph showing 28 days compressive strength
28 days split tensile strength
28 days split tensile strength
12
10
10.68
12
10
10.68
8
6.47
8
6.47
Conventional concrete
100 % flyash
Cases
100% GGBFS
Conventional concrete
100 % flyash
Cases
100% GGBFS
6
4
2
0
6
4
2
0
3.04
3.04
Fig 5. Graph showing 28 days split tensile strength
28 days flexural strength test
12 11.25
10
Strength
Strength
8 7.5
6
4 3.75
2
0
Conventional 100 % flyash 100% GGBFS concrete
Cases
Cost per m³ of concrete
Cost per m³ of concrete
Fig 6. Graph showing 28 days flexural strength
Cost per m³ of concrete
Cost per m³ of concrete
3500
3400
3300
3200
3100
3000
2900
2800
2700
3453.5
3094.4
3500
3400
3300
3200
3100
3000
2900
2800
2700
3453.5
3094.4
Conventional 100 % flyash 100% GGBFS concrete Cases
Conventional 100 % flyash 100% GGBFS concrete Cases
2991.9
2991.9
Fig 7. Graph showing cost analysis
-
CONCLUSION AND SCOPE FOR FUTURE WORKS
The concrete specimens were prepared in the ratio 1:1.3:3.1 for 7 and 28 days compressive strength, 28 days split tensile strength and 28 days flexural tensile strength. Cement was replaced by fly ash and GGBFS in the second and third case, respectively and NaOH / Na2SiO3 solutions were used for polymerization in the geopolymer concrete. The highest strength was obtained for 100% GGBFS geopolymer concrete. This shows considerably high strength compared to the 100% fly ash geopolymer concrete and normal cement concrete. The
specific gravity of GGBFS and fly ash were found using a specific gravity bottle. The specific gravity of fly ash and GGBFS were found to be 2.45 and 2.92 respectively. Workability of all three cases was found using slump test and the slump value was obtained between 25 75 mm that gives medium workability suitable for RCC work with less reinforcement. Cost analysis was carried out for all the cases and the highest cost was obtained for conventional concrete and the lowest cost was for fly ash-based geopolymer concrete. This also shows that GGBFS based geopolymer concrete is economical as well as gives high strength to be used in various construction works. The study shows that usage of GGBFS increases the strength of geopolymer concrete and this reduces the harmful industrial solid waste released into the environment and promotes sustainable development. GGBFS can be collected from various industries and can be taken to a concrete mix plant or for making ready mix concrete which promotes a sustainable infrastructure in the country. Similar studies can be conducted on other aluminosilicates such as rice husk ash, metakaolin etc. The durability of different cases of geopolymer concrete can also be studied to find out where it can be used. GPC roads, runways, pavement blocks, LTGS bricks, precast industries, automotive applications and aircraft interior and cabin interior applications can be constructed or manufactured or fabricated in the future based on various investigations.
REFERENCES
-
E. Rabiaa, R. A. S. Mohamed, W. H. Sofi and Taher A. Tawfik, 2020, Developing Geopolymer Concrete Properties by Using Nanomaterials and Steel Fibers, Hindawi Advances in Materials Science and Engineering, Volume 2020, pp 1-12, accessed 8 October 2020, ISSN: 5186091
-
Luhar Salmabanu and Luhar Ismail, 2020, Rubberized Geopolymer Concrete: Application of Taguchi Method for Various Factors, International Journal of Recent Technology and Engineering (IJRTE), Volume 8, Issue 5, pp 1167-1172, accessed 8 October 2020, ISSN: 2277-3878, DOI:10.35940/ijrte.E5679.018520
-
Luhar Salmabanu and Luhar Ismail, 2020, Parameters Impact on Compressive Strength of Slag Based Geopolymer Concrete, Advanced Research in Chemistry and Applied Science, Volume 2, Issue 1, pp 9-12, accessed 8 October 2020, ISSN: 2690-0769
-
IS 2720 (Part 3): Indian Standard Methods of Test for Soils Part 3: Determination of Specific Gravity (Bureau of Indian Standards, New Delhi)
-
Schedule of Rates 2012: Volume 1 (Government of Kerala, Public Works Department)