
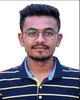
- Open Access
- Authors : Akshay Kerai , Mayur Gorasiya
- Paper ID : IJERTV11IS050298
- Volume & Issue : Volume 11, Issue 05 (May 2022)
- Published (First Online): 03-06-2022
- ISSN (Online) : 2278-0181
- Publisher Name : IJERT
- License:
This work is licensed under a Creative Commons Attribution 4.0 International License
An Experimental Study on Replacing of Crushed Aggregates with Reuseable Material in Layers of Pavement
Akshay Kerai
M.Tech construction management MIT-ADT UNIVERSITY
Loni kalbhor Pune, India
Mayur Gorasiya
-
Tech construction management MIT-ADT UNIVERSITY
Loni kalbhor Pune, India
Abstract The development of a country is dependent on the ability to connect various locations via a sufficient road network. Roads are the primary mode of transportation for both goods and people. They have an important role in raising a region's socioeconomic standards. Main focus of study is to examine the suitability of various non-traditional materials as a partial replacement for crushed aggregates in the granular sub-base of a pavement. To calculate the cost of granular sub base with and without the use of non-conventional materials.
Keywords- Pavement design, gsb layer, flexiable pavement, reuseable material, mix design
-
INTRODUCTION
Now days, natural resource depletion is a serious issue in the construction industry, and the road segment cannot be disregarded because the aggregate demand for road building is so high, and they consume so much energy. India is a large country with abundant natural resources; by utilizing these resources, construction costs can be decreased. The current research focuses on the use of locally available granular material in sub-base building. These materials should be able to provide a low-cost basis and sub-base for roads with low traffic volumes but high axle loads. The precision and method in which material properties are analyzed and employed in the analysis determine the quality of pavement design.
-
PROJECT REVIEW
-
Aim of study
Waste material is used in the GSB layer of pavement, lowering the overall cost of construction. Rejected coal aggregate and phosphate aggregate are examples of waste material.
-
Scope of the study
-
E-waste and river bed materials are considered alternative materials for burnt brick bats, low coal content coal rejected from power plants.
-
The main focus of this study is on the use of non- traditional materials in the pavement sub-base as a partial replacement for crushed aggregates.
-
The strength and durability of non-conventional materials will be determined through a number of tests.
-
-
-
REPLACEABLE MATERIAL WE USE IN STUDY
-
Coal aggregate was rejected by the power plant.
Material containing less than 40% fuel (pure coal) content is rejected because it includes less coal percent, and when fed into machinery, it causes damage to the mechanism.
Because this material is separated at thermal power
plants, the power plants must create a different arrangement of space to dump the material.
Because they have no means to use it and no other agency have power to remove it, heaps and heaps of it are lying about and land is being occupied.
F
i g
1 Rejected Coal
-
Fertilizer plant waste phosphate aggregate
Because of their high strength and hardness, aggregates made from basalt rock are utilised in building. Because there has been a scarcity of construction materials in recent years, artificial substitution of construction materials has become conceivable in whole or in part.
Phosphate production produces a significant amount of waste. However, particles of 16 mm to 40 mm are discarded since producing acid from this size aggregate is expensive.
Rejected phosphorous stone aggregates have the potential to be used in granular sub-base because of their hardness.
Fig 2 Rejected phosphorous stone aggregates
-
-
WORK METHODOLOGY
-
IDENTIFICATION OF PROBLEM
-
DEFINING AIM AND SCOPE OF THE STUDY
-
LITERATURE REVIEW
-
MATERIAL SELECTION
-
TESTING
-
AGGREGATE TESTING
-
SIEVE ANALYSIS
-
IMPACT VALUE
-
SPECIFIC GRAVITY
-
WATER ABSORPTION
-
ABRASION TEST
-
-
PAVEMENT MODEL
-
PERMEABILITY TEST
-
CBR TEST
-
-
-
RESULT ANALYSIS
-
PAVEMENT DESIGN
-
COST CALCULATION
-
CONCLUSION
Sr. No.
Proportion Mix Design
1
100 % Crushed aggregate
2
90% A + 10% RCA
3
80% A + 20% RCA
4
70% A + 30% RCA
5
90% A + 10% PA
6
80% A + 20% PA
7
70% A + 30% PA
-
-
MIX PROPORTION DESIGN
-
QUANTITY & COST CALCULATION
-
Thickness Design of Flexible Pavement as Per IRC: 37 2001 & IRC: 37 2012
Data for pavement design are given below and from that design of flexible pavement can be done. For Clay soil soak CBR value obtained from test results is 5.79%.
Data:
-
State Highway (2 Lane)
-
Design Traffic (A) = 1000 CVPD
-
Lane Distribution Factor (D) = 50 percent (Two Lane Single Carriageway Road)
-
Vehicle Damage Factor (F) = 4.5 (Plain Terrain)
-
Design Life (n) = 15 years
-
Annual Growth Rate (r) = 5 percent (Assumed)
-
Design Soak CBR = 5.79% (obtained) Design Calculations:
Cumulative no. of standard axle load
Now, for 5.79% CBR and 18 msa traffic, thickness design is calculated as per IRC: 37 2012, pg.26. After interpretation for 18 msa traffic Pavement composition is shown below.
-
Total Pavement Thickness for Clay Soil
-
-
Total Pavement Thickness = 640 mm
-
Pavement Composition
-
Granular Sub base (GSB-I) = 260 mm
-
Granular Base Course = 250 mm = 125 mm +125 mm
-
Dense Bound Macadam = 90 mm
-
Bituminous Course = 40 mm
BC
(40mm)
DBM (90mm)
GBC (250mm)
GSB (260mm)
Sub-grade
Fig 3 Composition of layers for Clay Soil
-
-
-
Material calculation
For present study purpose main focus area is GSB. GSB-I grading had been adopted during practical work. Hence, material quantity would be determined only for GSB layer. Out of two materials Phosphate aggregates found to be best material based on analysis of test results. Therefore quantity of normal aggregates and phosphate aggregates would be determined.
Unit weight of phosphate aggregate = 1762 kg/m3 Unit weight of crushed aggregate = 1570 kg/m3 Now, For 1 km, 2 lane stretch
Length = 1 km = 1000m Width = 7m (2 lane) Thickness = 260mm = 0.26m (Surface Course)
Volume = L * B * H
= 1000 * 7 * 0.26
= 1820 m3
Weight of coarse aggregate
= Volume * Unit weight of normal aggregate
= 1820 * 1570 kg/m3
= 2857400 kg say 2850 ton
Now best results were obtained in 70% crushed aggregates + 30% phosphate aggregate proportion. So we can replace phosphate aggregates by 30% in crushed aggregate.
If we adopt this proportion,
Weight of crushed aggregates required = 2000 ton Wight of phosphate aggregates required = 850 ton
-
Cost caluction
Initial cost is generally the major factor in deciding the type of the pavement design. Generally the construction cost is based on tender pricing. It is assumed that the initial cost reflects correct design and the best workmanship of required quality. Here the Rate is taken from NH Standard Data Book (Road & Bridge) 2017.
Table 1:- Material cost
Now, width = 7m & length = 1000 m
Quantity for GSB I = 0.260 * 7 * 1000 = 1820m3
-
GBC = 250 mm (125 mm WBM + 125 mm WMM)
Quantity for WBM = 0.125 * 7 * 1000 = 875m3 Quantity for WMM = 0.125 * 7 * 1000 = 875m3
-
Quantity for Prime Coat = 7* 1000 =
7000m2
-
Quantity for DBM = 0.090 * 7 * 1000 = 630 m3
Quantity for BC = 0.040 * 7* 1000 = 280m3
Item
QNo.
Item Name
Total Quantity
Unit
Rate Rs.
Total cost Rs.
u 1
GSB I
1820
Cum
989
1799980
a 2
WBM
875
Cum
1036
906500
n
t 3
WMM
875
Cum
1330
1163750
i 4
Prime Coat
7000
Sq. m
35
245000
t 5
DBM
630
Cum
7398
4660740
y 6
BC
280
Cum
8493
2378040
Total Amount Rs.
11154010
Table 3: Cost Analysis for Normal aggregate GSB layer
f
or pavement with composite mixture in GSB (1 km)
-
GSB = 260 mm (200 mm GSB I + 180 mm GSB II)
Now, width = 7m & length = 1000 m
Quantity for GSB I = 0.260 * 7 * 1000 = 1820m3
-
GBC = 250 mm (125 mm WBM + 125 mm WMM)
Material
Cost (In Rs)
Crushed aggregate
750 Rs. / 1 ton.
Phosphate aggregate
400 Rs. / 1 ton.
Quantity for WBM = 0.125 * 7 * 1000 = 875m3
Table 2:- Material quantity for 1 km, 2 lane road having 6% CBR
Material
Quantity
Normal mixture
Crushed aggregate = 2850 ton
Composite mixture
Crushed aggregate = 2000 ton Phosphate aggregate = 850 ton
Cost for normal mixture =2850*750 = INR 2137500/-
Cost for normal mixture = 2000*750 + 850*400 = INR 1840000/-
Hence,
Saving in material cost = 2137500 1840000 = INR 297500/Km.
Quantity for pavement with normal mixture in GSB (1 km)
-
GSB = 260 mm (200 mm GSB I + 180 mm GSB II)
Quantity for WMM = 0.125 * 7 * 1000 = 875m3
-
Quantity for Prime Coat = 7* 1000 = 7000m2
-
Quantity for DBM = 0.090 * 7 * 1000 = 630 m3
-
-
Quantity for BC = 0.040 * 7* 1000 = 280m3
Table 4: Cost Analysis for composite aggregate GSB layer
Item No.
Item Name
Total Quantity
Unit
Rate Rs.
Total cost Rs.
1
GSB I
1820
Cum
884
1608880
2
WBM
875
Cum
1036
906500
3
WMM
875
Cum
1330
1163750
4
Prime Coat
7000
Sq. m
35
245000
5
DBM
630
Cum
7398
4660740
6
BC
280
Cum
8493
2378040
Total Amount Rs.
10962910
Change in overall cost = INR 191100/-
-
-
CONCLUSION
-
Various experiments were carried out on various proportions, with the optimal proportion being 70 percent normal aggregate + 30 percent phosphate aggregates.
For the purposes of this study, the GSB-I grading system was adopted. The crushed aggregate, RCA, and PA gradation results are all within acceptable limits.
Because neither material is commonly used in construction, both materials had higher values in the form test than usual aggregates, although the values were judged to be within allowed limits.
The porosity of coal is higher than that of crushed aggregate. As a result, the inclusion of coal aggregate increases water absorption. There is no significant difference in specific gravity between RCA and PA.
Impact value and abrasion value increase as replacement % of coal aggregate increases, but as replacement percentage of coal aggregate increases, impact value and abrasion value decrease.
Because the GSB-I classification is for strength, it has a low permeability value. However, the minimum permeability value has been obtained for all proportions.
We may save INR 297500/- on material costs for a 1 km, two-lane road by replacing phosphate aggregates.
REFERENCES
[1] Sieve analysis and Shape test IS: 2386-Part 1-1963 [2] Specific gravity and water absorption test IS: 2386-Part 3-1963
[3] Aggregate impact test and Los Angeles abrasion test IS: 2386-Part 4-1963
[4] Highway Engineering by S.K.Khanna and C.E.G.Justo [5] Umesh Kamariya, Dr. L.B. Zala, Amit A. Amin, Utilization of Reclaimed Asphalt Pavement (RAP) Materials: A Synthesis Report, International Research Journal of Engineering and Technology (IRJET) 2018
Mr. Akshay Dinesh kerai, has completed his masters degree in M.Tech in construction project management from MIT-ADT Pune and he has an experience in project management field. |
Mr. Mayur Ravji Gorasiya, from Mankuva, Bhuj-Kutch has pursuing his masters degree in M.Tech in Construction Management from MIT-ADT Pune. |
AUTHOR PROFILE